Comparing Time-Triggered Ethernet with Flexray: an Evaluation of Competing Approaches to Real-Time for In-Vehicle Networks
Total Page:16
File Type:pdf, Size:1020Kb
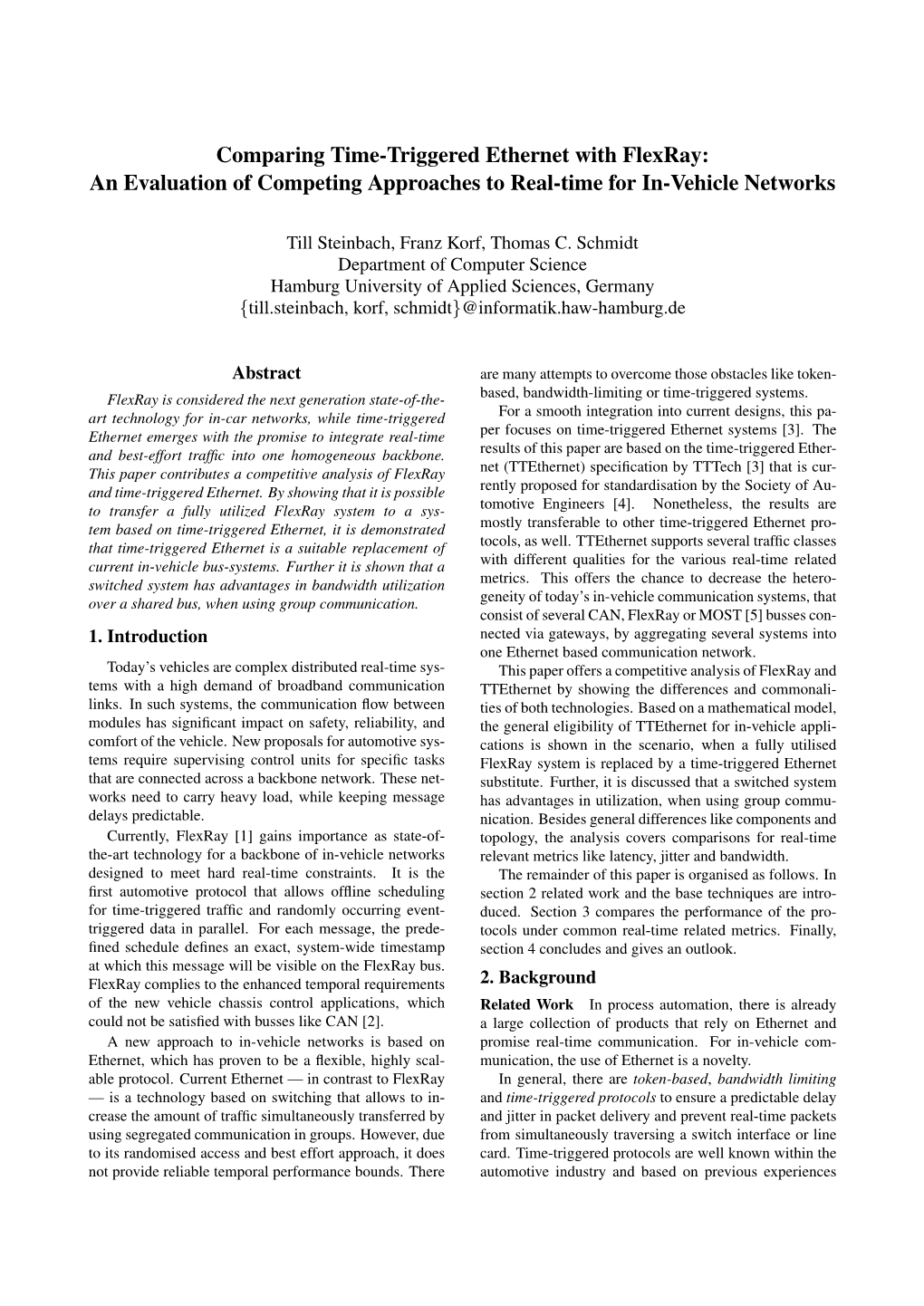
Load more
Recommended publications
-
Fnio Ethernet Specification
FnIO-S System FnIO Adapter SPECIFICATION Rev 3.02 NA-9286 (EtherCAT) Page 1 of 33 FnIO S–Series: NA-9286 EtherCAT Adapter FnIO-S System FnIO Adapter SPECIFICATION Rev 3.01 NA-9286 (EtherCAT) Page 2 of 33 DOCUMENT CHANGE SUMMARY REV. PAGES REMARKS DATE Editor N/A New Document Draft release 2012/6/13 Kim, HY 1.00 Release 2013/1/14 Kim, HY 2.00 Renamed NA-9186 → NA-9286 2013/8/7 Kim, HY 3.00 Image Update 2014/2/27 Kim, YM 3.01 Master fault action option is added (0x1100) 2016/10/6 DHLEE Register 0x1101 is removed 3.02 SDO list added 2017/5/25 DHLEE FnIO-S System FnIO Adapter SPECIFICATION Rev 3.01 NA-9286 (EtherCAT) Page 3 of 33 Table of Contents 1 FNBUS OVERVIEW.......................................................................................................................................4 1.1 FNBUS SYSTEM.................................................................................................................................................................4 1.2 FNBUS PIN DESCRIPTION...................................................................................................................................................5 2 ETHERCAT ADAPTER MODULE..............................................................................................................6 2.1 THE INTERFACE................................................................................................................................................................6 2.2 ENVIRONMENT SPECIFICATION............................................................................................................................................7 -
Benefits of a Standardized Diagnostic Framework
Benefits of a standardized diagnostic framework Hareesh Prakash Development Engineer The copying, distribution and utilization of this document as well as the communication of its contents to other without expressed authorization is prohibited. Offenders will be held liable for the payment of damages. All rights reserved in the event of the grant of a patent, utility model or ornamental design registration. Agenda DiagnosticsDiagnostics withwith standardsstandards –– Motivation Motivation ODXODX –– ODXplorer ODXplorer MCD-3MCD-3 ServerServer –– samMCD3 samMCD3 serverserver MVCI-D-PDU-APIMVCI-D-PDU-API –– HSX HSX samtecsamtec DiagnosticDiagnostic FrameworkFramework The copying, distribution and utilization of this document as well as the communication of its contents to other without expressed authorization is prohibited. ffenders will be held liable for the payment of damages. All rights reserved in the event of the grant of a patent, utility model or ornamental design registration. Diagnostics with Standards Motivation 2000 - 2009 New ACC Stop & Go ALC + Navigation Strategies, Heading Control Night Vision Process, AFS I + II X-AGS 1990 - 1999 Internet Tools, … Telematics Navigation system Online Services CD-Changer Bluetooth Bus system Car Office ACC Adaptive Cruise Control Complexity Local Hazard Warning Complexity 1980 - 1989 Airbags Integrated Safety Systems DSC Dynamic Stability Control Electronic Transmission control Break-By-Wire Adaptive Transmission Control Electronic air conditioning control Steer-By-Wire Anti-roll ASR i-Drive Xenon Lights ABS Fuel cells 1970 - 1979 BMW Assist Telephone LH RDS/TMC 2 Electronic Fuel Injection Seat heating Lane change ssistant Emergency calls Electronic Ignition … Personalization Servotronic Check Control Software Update … Idle speed regulator Force Feedback Pedal Central lock … Costs Source: [2] Hudi; [4] Reichert The copying, distribution and utilization of this document as well as the communication of its contents to other without expressed authorization is prohibited. -
Smartwire-DT Gateways – Canopen and PROFIBUS-DP
09/11 MN05013002Z-EN Manual replaces 06/09 AWB2723-1612en SmartWire-DT Gateways All brand and product names are trademarks or registered trademarks of the owner concerned. Emergency On Call Service Please call your local representative: http://www.eaton.com/moeller/aftersales or Hotline of the After Sales Service: +49 (0) 180 5 223822 (de, en) [email protected] Original Operating Instructions The German-language edition of this document is the original operating manual. Translation of the original operating manual ) All editions of this document other than those in German language are translations of 2 the original German manual. 1st edition 2009, edition date 02/09 2nd edition 2009, edition date 06/09 3rd edition 2010, edition date 03/10 4th edition 2010, edition date 06/10 5th edition 2011, edition date 03/11 6th edition 2011, edition date 09/11 See revision protocol in the “About this manual“ chapter © 2009 by Eaton Industries GmbH, 53105 Bonn Production: René Wiegand Translation: globaldocs GmbH All rights reserved, including those of the translation. Rückenbreite festlegen! (1 Blatt = 0,106 mm, gilt nur für XBS) g/m 80 bei Digitaldruck Eberwein für mm = 0,080 Blatt (1 No part of this manual may be reproduced in any form (printed, photocopy, microfilm or any other process) or processed, duplicated or distributed by means of electronic systems without written permission of Eaton Industries GmbH, Bonn. Subject to alteration without notice. Danger! Dangerous electrical voltage! Before commencing the installation • Disconnect the power supply of the • Suitable safety hardware and device. software measures should be • Ensure that devices cannot be implemented for the I/O interface accidentally restarted. -
AKD Scalability Brochure EN Revc
AKD SCALABLE PROGRAMMABILITY About Kollmorgen Kollmorgen is a leading provider of motion systems and components for machine builders. Through world-class knowledge in motion, industry-leading quality and deep expertise in linking and integrating standard and Application Centers Experience Scalable Programmability Micron™ Gearheads custom products, Kollmorgen delivers breakthrough Global Design & Manufacturing solutions that are unmatched in performance, reliability ™ Optimize Your Machine with the Leader Global Manufacturing and ease-of-use, giving machine builders an irrefutable with Advanced Kollmorgen Drive in Motion Control. marketplace advantage. For assistance with your application needs, Motion is at our core. We consistently maintain the highest standards contact us at: 540-633-3545, [email protected] or visit of quality, innovation and technology. We help you build in exceptional kollmorgen.com for a global contact list. motion performance, reliability and longevity, while considering cost AKM™ Servomotors and time-to-market challenges. Find Your Solution from the Broadest Range in the Industry Our breadth of products allows for a range of solutions—standard, modified orcustom. Stockholm Säro You can depend on our integrated, optimized components and hit the ground running in any application with ease. Fond du Lac Ratingen Kollmorgen Cartridge DDR™ Motors Marengo Lausanne Brno Milan Beijing Rely on Our Support and a Global Footprint to Help You Build a Differentiated Machine Radford Tianjin Santa Barbara Tokyo Nagoya With Kollmorgen, you’re getting great value and strength. We leverage a team of more than 1,800 Tijuana Shanghai employees, and over 60 years of application experience applied to selecting the optimum motion Hong Kong Mumbai components for your machine. -
AKD P-Standard Drive.Pdf
AKD SERVO DRIVES AKD SERVO AKD® Servo Drive Our AKD series is a complete range of Ethernet-based servo drives that are fast, feature-rich, flexible and integrate quickly and easily into any application. AKD ensures plug-and-play commissioning for instant, seamless access to everything in your machine. And, no matter what your application de- mands, AKD offers industry-leading servo performance, communication options, and power levels, all in a smaller footprint. This robust, technologically advanced family of drives delivers optimized performance when paired with our best-in-class components, producing higher quality results at greater speeds and more up- time. With Kollmorgen servo components, we can help you increase your machine’s OEE by 50%. 26 KOLLMORGEN AKD SERVO DRIVES AKD SERVO The Benefits of AKD Servo Drive • Optimized Performance in Seconds • Auto-tuning is one of the best and fastest in the industry • Automatically adjusts all gains, including observers • Immediate and adaptive response to dynamic loads • Precise control of all motor types • Compensation for stiff and compliant transmission and couplings • Greater Throughput and Accuracy • Up to 27-bit-resolution feedback yields unmatched precision and excellent repeatability • Very fast settling times result from a powerful dual processor system that executes industry-leading and patent pending servo algorithms with high resolution • Advanced servo techniques such as high-order observer and bi-quad filters yield industry-leading machine performance • Highest bandwidth torque-and-velocity -
— PROFIBUS-Adapter
— ABB MEASUREMENT & ANALYTICS | DATA SHEET PROFIBUS-Adapter — To find your local ABB contact visit: www.abb.com/contacts For more information visit: www.abb.com/measurement — We reserve the right to make technical changes or modify the contents of this document without prior notice. With regard to purchase orders, the agreed particulars shall prevail. ABB does not accept any responsibility whatsoever for potential errors or possible lack of information in this document. We reserve all rights in this document and in the subject matter and illustrations contained therein. Any reproduction, disclosure to third parties or utilization of its contents – in whole or in parts – is forbidden without prior written consent of ABB. © ABB 2019 3KXN631121R1001 10/63-6.31-EN Rev. G 05.2019 2 NDA121-NO PROFIBUS-ADAPTER | 10/63-6.31-EN REV. G NDA121-NO PROFIBUS-ADAPTER | 10/63-6.31-EN REV. G 7 — Measurement made easy — Profibus DP / PC Adapter • USB NDA121-NO PROFIBUS-ADAPTER | 10/63-6.31-EN REV. G 3 — NDA121-NO PROFIBUS DP / PC-USB adapter hange from one to two columns Adapter CommDTM Desktop PC’s as well as notebooks can be flexible connected The Device Type Manager CommDTM provides access to the in the field to a PROFIBUS® network via the adapter PROFIBUS® Master NDA121-NO. Within the FDT architecture, NDA121-NO. Thereby a parallel operation of up to 16 adapter the CommunicationDTM enables DeviceDTMs to connect to is possible. The adapter supports the Master functionality of their respective devices via PROFIBUS® DP/-V1. the PROFIBUS® Standards DP (class 1 and 2), DP-V1 (class 2). -
Master Simulators
Master simulators By using master simulators from HMS, you can set up and test slaves/adapters on PROFIBUS, PROFINET, CANopen, EtherNet/IP and DeviceNet without having a PLC in place. Simply connect to your computer and you have a very cost-efficient alternative to a PLC or PC-card. CANopen interface — powered by USB USB port on the PC RS-232 CANopen cable 9-pin D-Sub connector PROFIBUS interface Device under test Device under test DeviceNet interface USB (24V power supply required to connect and test a DeviceNet adapter —not included). DeviceNet cable with data and power lines Pluggable screw connector Ethernet cable with termination Device under test Device under test Available for: Test your device without an expensive PLC Key features Master simulators are ideal for test-wiring of inputs and ouputs • Easy-to-use test and diagnostics and reading and writing analog values. They are useful during tool. setup of slave/adapters in a network as well as during final • No programming required. inspection tests at the device manufacturer. • Auto-detects slaves/adapters Industrial Ethernet versions are software-only, while fieldbus (even when GSD/EDS file is not versions also include a converter interface which is used to available). connect the fieldbus cable to the PC. • Auto detection of I/O data size. No GSD/EDS files needed (not for EtherNet/IP) During setup and maintenance, there may not be GSD/EDS available making master simulators especially useful for this scenario. HMS provides a full 3 year product guarantee TECHNICAL SPECIFICATIONS Description Consists of a Windows-based Software only. -
Efficiently Triggering, Debugging and Decoding Low-Speed Serial Buses
Efficiently Triggering, Debugging and Decoding Low-Speed Serial Buses Hello, my name is Jerry Mark, I am a Product Marketing Engineer at Tektronix. The following presentation discusses aspects of embedded design techniques for “Efficiently Triggering, Debugging, and Decoding Low-Speed Serial Buses”. 1 Agenda Introduction – Parallel Interconnects – Transition from Parallel to Serial Buses – High-Speed versus Low-Speed Serial Data Buses Low-Speed Serial Data Buses – Challenges – Technology Reviews – Measurement Solutions Summary 2 In this presentation we will begin by taking a glance at the transition from parallel-to-serial data and the challenges this presents to engineers. Then we will briefly review some of the most widely used low-speed serial buses in industry today and some of their key characteristics. We will turn our attention to the key measurements on these buses. Subsequently, we will present by example how the low-speed serial solution from Tektronix addresses these challenges. 2 Parallel Interconnects Traditional way to connect digital devices used parallel buses Advantages – Simple point-to-point connections – All signals are transmitted in parallel, simultaneously – Easy to capture state of bus (if you have enough channels!) – Decoding the bus is relatively easy Disadvantages – Occupies a lot of circuit board space – All high-speed connections must be the same length – Many connections limit reliability – Connectors may be very large 3 Parallel buses present all of the bits in parallel, as shown in the logic analyzer display. A parallel connection between two ICs can be as simple as point-to-point circuit board traces for each of the data lines. If you can physically probe these lines, it is easy to display the bus state on a logic analyzer or mixed signal oscilloscope. -
The Role of CAN in the Age of Ethernet and IOT
iCC 2017 CAN in Automation The role of CAN in the age of Ethernet and IOT Christian Schlegel, HMS Industrial Networks CAN technology was developed in the 1980s and became available in 1987, just as other industrial fieldbus systems like PROFIBUS or INTERBUS entered the stage of industrial communication. Beside the fact that CAN is a success in the automotive industry and used in all types of cars today, it has also made its way in many other industrial areas. About 15 years ago, new technologies based on Ethernet started to emerge, with ap- pealing and sometimes outstanding features. Some six years ago Ethernet also started to find its way into automobiles. Today, other new communication technologies are showing up on the horizon driven by the omnipresent Industrial Internet of Things. But even now, 30 years after their introduction, these “classic” fieldbus technologies are still alive – with varying success. Since CAN was initially developed with a focus for use in automobiles, CAN has certain features that still make it the best choice for many applications in automobiles and industrial areas – even when compared to the newer technologies. This paper discusses why CAN is still a valid or even better choice for certain applica- tion areas than Ethernet-based technologies, not just focusing on the advanced fea- tures provided by the enhanced capabilities of CAN FD but also highlighting how these applications benefit from the features of “classic” CAN. Looking back into history … the requirement to transmit data between … when CAN was born these ECUs but also to connect sensors and actuators to them. -
AIT Presentation
Distributed Sensors & Connectivity as the answer to future grid requirements Karl-Heinz Mayer Director Engineering Innovation & Program Management AIT Industry Day – September 11th, 2015 © 2015 Eaton Corporation. All rights reserved. Power business – status quo • Electricity is still the backbone and driver of mankind‘s productivity – this seems not to be changed soon 2 © 2015 Eaton Corporation. All rights reserved. 2 Power business – status quo • Electricity is still the backbone and driver of mankind‘s productivity – this seems not to be changed soon • Climate changes are requesting less CO2 emission despite the worldwide increase of power demand Green Energy; programs for ISO 50001, LEED,…certifications 3 © 2015 Eaton Corporation. All rights reserved. 3 Power business – status quo • Electricity is still the backbone and driver of mankind‘s productivity – this seems not to be changed soon • Climate changes are requesting less CO2 emission despite the worldwide increase of power demand Green Energy; programs for ISO 50001, LEED,…certifications • Consumer – Prosumer transformation requests new system approaches Virtual power plants 4 © 2015 Eaton Corporation. All rights reserved. 4 Technology trends are lowering the hurdles to develop and connect more intelligent devices • Semiconductor component costs continue to decline • Functionality and power management performance improving • Pervasiveness of communications increasing • Cloud services and development tools are being used more and more…and their costs are dropping dramatically with scale 5 © 2015 Eaton Corporation. All rights reserved. 5 Future challenges 1. Growing Electricity 2. Electricity Peak 3. Increasing Variable 4. Increasing Demand & Ageing Management Energy Generation Integration of Electric Infrastruture Vehicle World Energy Consumption by fuel type, 1990-2040 - Source : EIA (2013) 6 © 2015 Eaton Corporation. -
Connect-And-Protect: Building a Trust-Based Internet of Things for Business-Critical Applications Table of Contents
WHITE PAPER CONNECT-AND-PROTECT: BUILDING A TRUST-BASED INTERNET OF THINGS FOR BUSINESS-CRITICAL APPLICATIONS TABLE OF CONTENTS THE INTERNET OF WHATEVER 3 LET’S GET PHYSICAL 8 TALK THE TALK 11 PROTECTED INTEREST 14 PICTURE ME ROLLING 23 DATA: THE NEW BACON 25 CONCLUSION 29 SOURCES 29 ABOUT ARUBA NETWORKS, INC. 30 WHITE PAPER CONNECT-AND-PROTECT: INTERNET OF THINGS THE INTERNET OF WHATEVER Today it’s almost impossible to read a technical journal, sometimes a daily paper, without some reference to the Internet of Things (IoT). The term IoT is now bandied about in so many different contexts that its meaning, and the power of the insights it represents, are often lost in the noise. Enabling a device to communicate with the outside world isn’t by itself very interesting. The value of the IoT comes from applications that can make meaning of what securely connected devices have to say – directly and/or inferentially in combination with other devices – and then act on them. Combining sensors and device with analytics can reveal untapped operational efficiencies, create end-to-end process feedback loops, and help streamline and optimize processes. Action can take many forms, from more efficiently managing a building or factory, controlling energy grids, or managing traffic patterns across a city. IoT has the potential to facilitate beneficial decision making that no one device could spur on its own. But that potential can only be realized if the integrity of the information collected from the devices is beyond reproach. Put another way, regardless of how data gathered from IoT are used, they’re only of value if they come from trusted sources and the integrity of the data is assured. -
Fieldbus Communication: Industry Requirements and Future Projection
MÄLARDALEN UNIVERSITY SCHOOL OF INNOVATION, DESIGN AND ENGINEERING VÄSTERÅS, SWEDEN Thesis for the Degree of Bachelor of Science in Engineering - Computer Network Engineering | 15.0 hp | DVA333 FIELDBUS COMMUNICATION: INDUSTRY REQUIREMENTS AND FUTURE PROJECTION Erik Viking Niklasson [email protected] Examiner: Mats Björkman Mälardalen University, Västerås, Sweden Supervisor: Elisabeth Uhlemann Mälardalen University, Västerås, Sweden 2019-09-04 Erik Viking Niklasson Fieldbus Communication: Industry Requirements and Future Projection Abstract Fieldbuses are defined as a family of communication media specified for industrial applications. They usually interconnect embedded systems. Embedded systems exist everywhere in the modern world, they are included in simple personal technology as well as the most advanced spaceships. They aid in producing a specific task, often with the purpose to generate a greater system functionality. These kinds of implementations put high demands on the communication media. For a medium to be applicable for use in embedded systems, it has to reach certain requirements. Systems in industry practice react on real-time events or depend on consistent timing. All kinds are time sensitive in their way. Failing to complete a task could lead to irritation in slow monitoring tasks, or catastrophic events in failing nuclear reactors. Fieldbuses are optimized for this usage. This thesis aims to research fieldbus theory and connect it to industry practice. Through interviews, requirements put on industry are explored and utilization of specific types of fieldbuses assessed. Based on the interviews, guidelines are put forward into what fieldbus techniques are relevant to study in preparation for future work in the field. A discussion is held, analysing trends in, and synergy between, state of the art and the state of practice.