Cranfield University A. J. Lamb Experimental Investigation
Total Page:16
File Type:pdf, Size:1020Kb
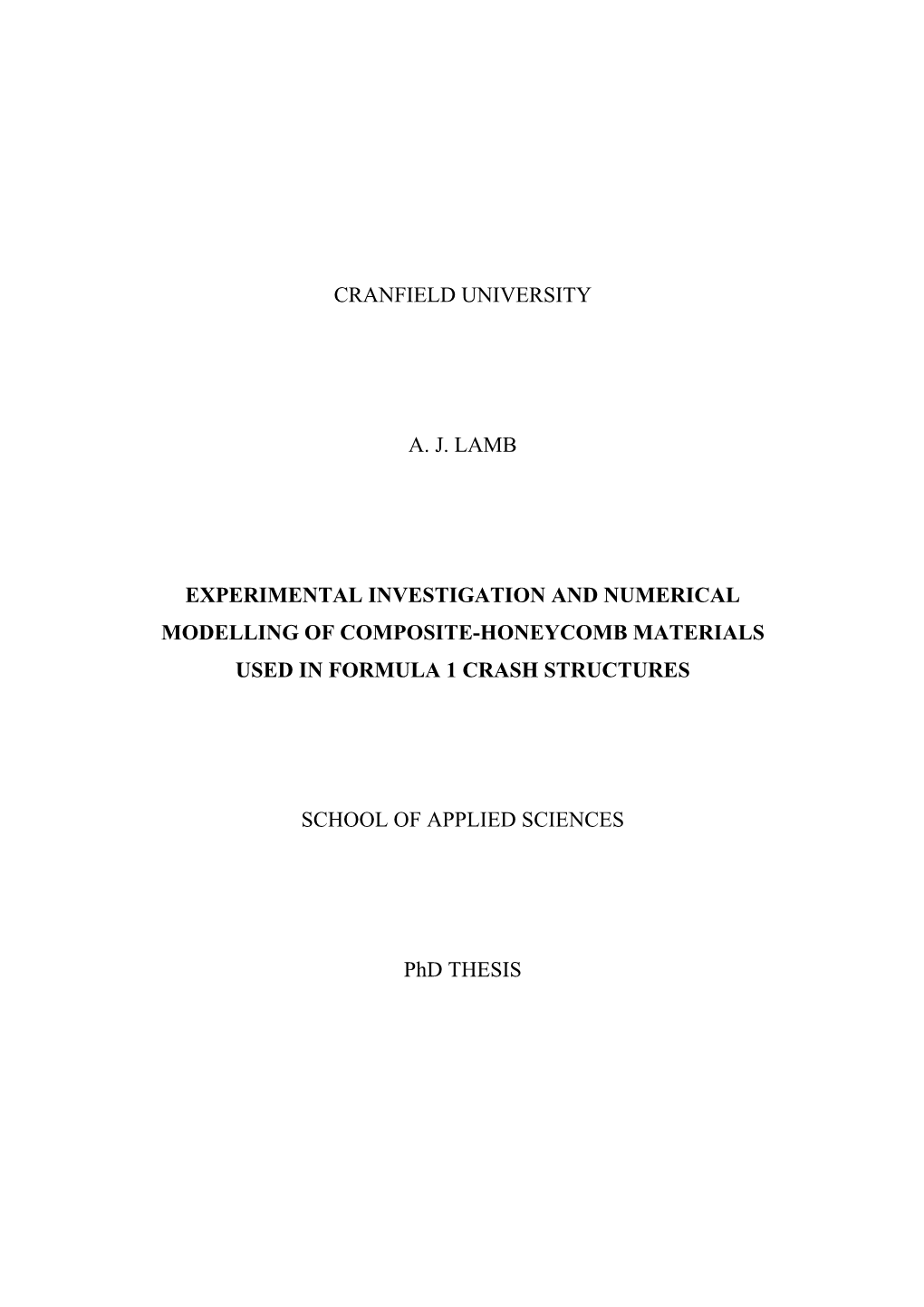
Load more
Recommended publications
-
Jornada De Paraguas En Wimbledon
10350893 07/03/2004 01:21 a.m. Page 2 2D |EL SIGLO DE DURANGO | SÁBADO 3 DE JULIO DE 2004 | DEPORTES POSICIONES A ritmo de samba Pilotos brasileños marcaron el rumbo en los entrenamientos. Pos. Piloto (País) Escudería/Motor Tiempo 1. Rubens Barrichello (BRA) Ferrari F2004 1:15:487 2. Michael Schumacher (ALE) Ferrari F2004 1:15.713 3. Marc Gené (ESP) Williams FW26 BMW 1:19.348 4. Timo Glock (ALE) Jordan EJ14 Ford 1:19.428 5. Giorgio Pantano (ITA) Jordan EJ14 Ford 1:19.466 6. Nick Heidfeld (ALE) Jordan EJ14 Ford 1:20.531 7. Gianmaría Bruni (ITA) Minardi PS04 Ford 1:21.203 8. Bas Leinders (BEL) Minardi PS04 Ford 1:22.267 9. Anthony Davidson (GBR) BAR 006 Honda 1:26.552 10. Cristiano Da Matta (BRA) Toyota TF104 1:26.757 11. Olivier Panis (FRA) Toyota TF104 1:27.449 12. Jenson Button (GBR) BAR 006 Honda 1:28.317 13. Ricardo Zonta (BRA) Toyota TF104 1:29.085 14. Christian Klien (AUT) Jaguar R5 Cosworth 1:29.626 15. Zsolt Baumgartner (HUN) Minardi PS04 1:29.877 El brasileño Cristiano da Matta, adelante del multicampeón Michael Schumacher durante las prácticas de ayer en Francia. (Reuters) 16. Takuma Sato (JAP) BAR 006 Honda 1:30.092 17. Bjorn Wirdheim (SUE) Jaguar R5 Cosworth 1:30.204 CLASIFICATORIO | BARRICHELLO Y DA MATTA LIDERAN PRÁCTICAS 18. Jarno Trulli (ITA) Renault R24 1:39.392 Felipe Massa (BRA) Sauber C23 Petronas Sin tiempo Fernando Alonso (ESP) Renault R24 Sin tiempo Giancarlo Fisichella (ITA) Sauber C23 Petronas Sin tiempo David Coulthard (GBR) McLaren Mercedes Sin tiempo Juan Pablo Montoya (COL) Williams FW26 BMW Sin tiempo Kimi Raikkonen (FIN) McLaren Mercedes Sin tiempo Los brasileños Mark Webber (AUS) Jaguar R5 Cosworth Sin tiempo SEGUNDO ENTRENAMIENTO 1. -
Club Racing Board Contents
EFFECTIVE FIRST DAY OF THE MONTH UNLESS OTHERWISE NOTED May 2012 CLUB RACING BOARD CONTENTS SCCA Club Racing Board Minutes | April 3, 2012 BOARD OF DIRECTORS NONE CLUB RACING 1 The Club Racing Board met by teleconference on April 3, 2012. Participating were CRB Minutes 1 Jim Wheeler, Chairman; Chris Albin, Fred Clark, Jim Drago, Peter Keane, Tom Start, Technical Bulletin 33 Mirl Swan, and Pam Richardson, secretary. Also participating were: Todd Butler and Court of Appeals 36 Richard Patullo, BoD liaisons; Terry Ozment, Vice President of Club Racing; Doug Time Trials Admin. Council None Gill, General Manager, Technical Services Department; and John Bauer, Technical Manager, Club Racing. Jerry Wannarka, Chairman of the BoD participated as a SOLO 40 guest. The following decisions were made: SEB Minutes 40 RALLY 43 SUGGESTED RULES FOR 2013 RallyCross 43 The following subjects will be referred to the Board of Directors for approval. Address RoadRally NONE all comments, both for and against, to the Club Racing Board. It is the BoD’s policy to LINKS 45 withhold voting on a rules change until there has been input from the membership on the presented rules. Member input is suggested and encouraged. Please send your comments via the form at http://www.crbscca.com/ or www.clubracingboard.com. GCR 1. #7214 (Terry Ozment) 15-year old licensing change Change Appendix C, GCR 2.6.G: G. A 15 year-old must complete his first SCCA driver school in a carnot classed in GT1, GT2, FA, FB, FS, ITR, STO, ASR, CSR, DSR, or T1. from one of the following classes: FV, FST, FF, SRF, SM, HP, T3, SSB, SSC, ITA, ITB or ITC. -
Alonso:“Tenemosque Ponerelr24patasarriba”
MUNDO DEPORTIVO · Sábado 19 de junio de 2004 POLIDEPORTIVO GP de EE.UU. de F-1 39 El español asegura que a su Renault le está faltando estabilidad y velocidad Alonso: “Tenemos que poner el R24 patas arriba” R. B. BARCELONA así nuevo para la carrera y ello ilusión, trabajar más. Lo que está puede ser una baza interesante. claro es que el sábado debe ser ernando Aloso quiso restar De todas formas el piloto espa- mejor... porque peor será muy difí- Fimportancia al hecho de no ñol se mostró pesimista. Habitual- cil”, afirmó. haber podido rodar en la se- mete, Alonso se muestra siempre Los problemas podrían venir de gunda sesión de ayer porque “no precavido en los pronósticos y la la falta de adaptación del Ren- afecta nada. Tal como estaba la 'rebaja' las expectativas anuncia- ault R24 a la pista, donde ni en pista y como iba el coche, no íba- das por sus jefes de fina. Pero ayer estabilidad ni en velocidad parece mos a sacar nada nuevo”. se mostró disgustado con esta pis- estar a la altura de careras anterio- Michael Schumacher se conformó con una posición discreta por preparar la carrera FOTO: REUTERS Ni siquiera el no haber podido ta “que puede ser divertidapara el res. “Tenemos poca adherencia y probar a fondo los neumáticos pa- público pero desde luego no para en las zonas bacheadas sufrimos de a nadie a estas alturas de tempo- que ha sidod enominador común ra elegir el tipo más adecuado le el piloto. Creo que va a ser un final mucho. -
HBH Catalog 2016 En.Pdf
The company of HBH was created in 2011 with the aim to help people who wish to do bodyweight training outdoors and indoors with equipment designed by us. We started as one of the first manufacture designing body weight training equipments to create wide sport fields in the urban areas. We are convinced that community building and recreational functions of city parks will prevail if they are furnished properly. We consulted professional athletes, when shaping our sports equipment in order to best meet the needs of people doing street workout, calisthenic or body weight trainings. With our multiple award winning products, exercises can be done using your own body weight, thus developing physical and mental endurance. www.hardbodyhang.com HBH BAR 00 1 OUTDOOR PULL UP BAR HBHbar SIZE: 1500x110x2300MM Combining the basic elements as you like, complex systems, so called the Sets or Parks, can be assembled for cities, sport clubs and private customers as well. Every request is 2 welcome! 14 M HBH BAR 002 HBH BAR 003 OUTDOOR VERTICAL LADDER OUTDOOR HORIZONTAL LADDER SIZE: 1500x110x2300MM SIZE: 1900x1500x2300MM 14 M2 22 M2 HBH BAR 004 HBH BAR 005 OUTDOOR PARALLEL BAR OUTDOOR PUSH UP BAR SIZE: 2500x650x1300MM SIZE: 4500x110x450MM 20 M2 22 M2 HBH BAR 006 HBH bar 007 EQUALIZER MINI BENCH SIZE: 750x750x600MM SIZE: 650x550x600MM 12 M2 6 M2 HBH bar 008 HBH bar 009 FLAT BENCH SLANT BENCH SIZE: 1500x550x600MM SIZE: 1400x550x1100MM 12 M2 12 M2 HBH ADD 00 1 HBH ADD 002 BIKE SHED INFO BOARD SIZE: 600x200x900MM SIZE: 1800x800x50MM 4 M2 2 M2 HBH BAR 0 10 HBH -
LISTE DES ENGAGES Première Page À Demander Auprès De Héléna Ou Jérémy De L'aco
LE MANS 2018 - 86 ème édition InfosCourse LISTE DES ENGAGES première page à demander auprès de Héléna ou Jérémy de l'ACO 1 REBELLION RACING InfosCourse Au Mans : 9 Part : 3 Vict + 2 Pod ; 1 Pole & 8°Pro-Cup 24h Spa /AudiR8 TOM’s,1 Vict + 4 Pod. LOTTERER André LMS WRT 08 à 09 A1 GP /Team D,, 4 MT F1 / Caterham Renault, 08 3°F.Nippon / TOMs, 4 pod. 17 AB /P.919 Hybrid Porsche Audi Joest (Fässler, Tre- FFSA GT /Audi R8BAC Team 3°SuperGT 500 /Lexus (Jani, Tandy) luyer) WRT , Vict Spa TOMs, 4 pod. 16 4° /Audi R18 Audi Joest 12 Vict & PP /Audi R18 e-tron 13 Vice-Chpion WECP1 /Audi 07 5°F.Nippon / TOMs , 1 vict + (Fässler, Treluyer) Audi Joest (Treluyer, Fäss- R18 A.S.Team Joest, 3 Vict 2 pod. 15 3° & MT /Audi R18 e-tron ler) 2° Silverstone & Bahrain, 6°Super GT500/ Lexus Toms, Audi Joest (Fässler, Tre- 11 Vict & MT /Audi R18 Audi 3°Austin 4 pod. luyer) Joest (Treluyer, Fässler) Vice-Chpion Japan SF / Team 06 Chpion Super GT500 /Lexus- 14 Vict & MT /Audi R18 e-tron 10 2° /Audi R15 Audi Joest Tom’s, 2 Vict Tom’s, 1 Vict +2 Pod. DEU Audi Joest (Fässler, Tre- (Fässler, Treluyer) 3°24h Spa/ Audi R8 3°F. Nippon /Tom’s , 2 vict luyer) 09 7° /Audi R10 Kolles (Charles 12 Chpion WEC P1 /Audi R18 e- 05 4°F.Nippon/Nakajima 2 vict 13 5° & MT /Audi R18 e-tron Jr Zwolsman, Karthikeyan) tron A. S. Team Joest, 3 Vict 17°Super GT500 / NSX 4° F. -
Bmmcmagazine Bmmc Magazine
BMMC MAGAZINE BMMCMAGAZINE SSouthouthM iMidlandsdlands Reg iRegiononJuly 20 14 July 2017 1 Contents 3 – Chairman’s Chatter 11 – Poker Stars Rally 4 – South Mids AGM 2017 12 – BMMC Regalia Order Form 5 – BMMC Auction 13 – 50 yrs of Marshalling 6 – Ignition Festival 15 – SMids Region Members of Motoring 10 – Weekend of Motoring 16 – National Directors 2 The Chairman’s Chatter…. Paul Harris - South Midlands Chairman .... Welcome to the Newsletter for the South Midlands Region I hope that those of you, who marshalled the GP at Silverstone recently for the first time, enjoyed the experience and will volunteer again next year. It is a meeting that you have to do at least once to say that you have done it. After all, it is the biggest race meeting that is held in the UK. To those of you for whom it was not the first time, I hope you got the same amount of enjoyment out of it as you did the first time. The region is holding a bar-b-que to celebrate the Club’s 60th Anniversary, at the Silverstone Recreation Club on Saturday 19th August, to which you are all invited. It is free to all members provided you show your BMMC membership card; any guests that you are welcome to bring will be charged. As you will see in another part of the newsletter the Region’s 50th Anniversary AGM and Dinner is to be held at Fox and Hounds at Whittlebury on Saturday 29th October. Please do make every effort to attend. Further details will follow. -
Board of Directors Contents
EFFECTIVE FIRST DAY OF THE MONTH UNLESS OTHERWISE NOTED November 2012 BOARD OF DIRECTORS CONTENTS SCCA Board of Directors Minutes | October 11-13, 2012 BOARD OF DIRECTORS 1 CLUB RACING 55 The SCCA National Board of Directors met at the National Office in Topeka, KS on CRB Minutes 55 Thursday, October 11, Friday, October 12 and Saturday, October 13. The following Technical Bulletin 62 directors participated: Jerry Wannarka, Chairman; Lisa Noble, Vice-Chairman; Dick Court of Appeals 64 Patullo, John Walsh, Bill Kephart, Todd Butler, Secretary; Bob Lybarger, Michael Time Trials Admin. Council 71 Lewis, Treasurer; R. David Jones, Robin Langlotz, Steve Harris and Brian McCarthy. Phil Creighton participated via conference call. SOLO 72 SEB Minutes 72 The following SCCA, Inc. staff participated in the meeting: Jeff Dahnert, President RALLY 76 and CEO; Richard Ehret, Vice President Finance; Howard Duncan, Vice President RallyCross 76 Rally/Solo & Special Projects; Terry Ozment, Vice President Club Racing; Eric Prill, RoadRally 78 Vice President Marketing and Communications; Colan Arnold, Vice President Member LINKS 80 & Region Services, and Aimee Thoennes, Executive Assistant. The following guests participated: Steve Hudson, SEB Chairman; Jim Wheeler, CRB Chairman; Dan Helman, Insurance Committee Chairman; Paul Pfanner, Founder / President / CEO / Executive Publisher of Racer Media & Marketing, Inc. ; Pasquale Trozzolo, Angelo Trozzolo and Jeff Madden, Trozzolo Communications Group; K. David Nokes, Chairman of the Stewards; Tom Campbell, President SCCA Pro Racing. The secretary acknowledges that these minutes may not appear in chronological order and that all participants were not present for the entire meeting. The meeting was called to order by Chairman Wannarka. -
Y Ferrari Quieren El Séptimo
10286505 08/03/2004 12:10 a.m. Page 1 Futbol: Directiva de Alacranes de Durango protestará mal arbitraje | Pág. 2 Lunes 8 de marzo de 2004 D PASE Procopio Franco irá a Atenas, tras finalizar en segundo lugar en el Maratón Lala 2004. MARATÓN 4 Editor: CÉSAR ACOSTA MALTOS Coeditor Gráfico: AXEL VÉLEZ AGUILAR [email protected] TÍTULO | EL TENISTA IBÉRICO VENCIÓ EN LA FINAL A SU COMPATRIOTA FERNANDO VERDASCO 6-3 Y 6-0 Moyá recupera cetro Jared Borgetti, la imagen de la impotencia. El Abierto Mexicano de Tenis se celebró Gol de Navia y gana en Acapulco y estuvo dotado con 652 el América a Santos mil dólares en premios TORREÓN, COAHUILA (AGENCIAS).- Águilas del Amé- ACAPULCO, GUERRERO (AGENCIAS).- rica obtuvo un importante triunfo de 1-0 sobre el Carlos Moyá ganó por segunda vez Santos Laguna de Torreón en su visita al Esta- el Abierto Mexicano de Tenis, tor- dio Corona, en partido de la fecha nueve. neo que se celebró en Acapulco y El gol de la victoria fue obra del chileno Rei- que estuvo dotado con 652 mil dó- naldo Navia, al minuto 22. Jared Borgetti tuvo el lares en premios, ello tras derrotar gol del empate, sin embargo, falló un penal que en la Gran Final a Fernando Ver- le regaló Abramo Lira, a los 81. dasco por un concluyente 6-3 y 6-0. Ivetta Benesova logró el título Con esta victoria, la primera como visitante en Con esta victoria, el jugador femenil del Abierto Mexicano. el torneo, América llegó a 15 unidades y es sublí- mallorquín logró el segundo título der del Grupo Dos, mientras que Santos se quedó de esta temporada, tras el obteni- MUSTER, LA REFERENCIA en el último sitio del mismo sector con diez puntos. -
2009 GCR.Indd
GCR - 556 9.1.10. Touring Category Specifications INTRODUCTION TCS These specifications are presented as an adjunct to your Factory Shop Manual. They are not meant to supersede the information that is in your manual that legitimately applies to your make, model, and year of car, with the exception of the following items. TIRE SIZES, RIM WIDTHS, SPRINGS, SWAY BAR(S), AND PERFORMANCE EQUIPMENT. In the case of the foregoing exceptions, the TCS will have priority. Voids or mistakes that may occur in the TCS do not allow you to change your vehicle to conform to the TCS. These specifications reflect the best information available at the time of publication. Any error found in this edition will be updated when reliable specifications are available from the factory/factory distributor or other sources recognized by SCCA, Inc. A model is defined as a unique car configuration which can be identified by means of decoding the Vehicle Identification Number. 9.1.10. TOURING CATEGORY These Specifications are part of the SCCA General Competition Rules (GCR), and all classified automobiles shall conform with the requirements of GCR Section 9 unless this Category is specifically exempted from said requirements. A. Purpose Touring Category Classes are intended to provide the Membership with the opportunity to compete in commonly-available, recently-produced automobiles in as near the legal, street-driven form of those automobiles as is practically and safely possible under racing circumstances. B. Intent Touring Category automobiles shall, at all times, be in com pliance with the specifications contained within their factory Shop/Service Manual(s) except as modified by these rules. -
Empresarios Ven Cercanas a Figuras De NBA En La LNBP Kareem Abdul Jabbar Mar Con Sus Respectivas Quintetas
10319705 09/05/2004 12:40 a.m. Page 5 DEPORTES | DOMINGO 9 DE MAYO DE 2004 | EL SIGLO DE DURANGO | 5D Mientras los aficionados xeneizes piden por él, Maradona no encuentra hospitalidad en las clínicas argentinas. (Reuters) Clínicas cierran sus El teutón Michael Schumacher está listo para conquistar el gran premio ibérico. (Agencias) FÓRMULA UNO | GRAN PREMIO DE ESPAÑA; IBÉRICO ALONSO EN OCTAVO puertas a Maradona BUENOS AIRES, ARGENTINA (AGENCIAS).- El médico personal de Diego Maradona, Alfredo Cahe, admitió el sábado que los centros de rehabili- Michael Schumacher, tación para la adicción a las drogas de Argen- tina no “aceptan” como paciente al ex futbolis- ta, que aún permanece internado en una clíni- ca de Buenos Aires a causa de un severo cua- dro cardiaco y respiratorio. De todos modos, Cahe sostuvo que para que sea trasladado de la Clínica Suizo Argen- de nuevo al frente tina a un centro de rehabilitación, “Diego tie- ne que estar de acuerdo”. El viernes, se conoció que cinco clínicas consul- El alemán PARRILLA tadas por los familiares de Maradona negaron la posibilidad de encargarse de la atención del ex ca- y Juan Pablo Caballo rampante gana largada pitán de la selección argentina. De nuevo el alemán Michael Schumacher encabezará la parrilla de salida. El director de la Clínica Suizo Argentina, Montoya arrancan Claudio Belocopit, informó que el ex jugador PRIMERA FILA 1:16.313 Honda 1:17.575 es un paciente “que se quiere ir”, aunque negó primero Michael Schumacher (GER) Ferrari Fernando Alonso (ESP) Renault OCTAVA FILA que haya “provocado destrozos en la habita- F2004 1:15.022 R24 1:16.422 Nick Heidfeld (GER) Jordan EJ14 ción”, tal como había trascendido. -
A Bordo E Em Terra Celebramos Portugalidade Contacte O Seu Agente De Viagens Ou A
A VOZ DE PORTUGAL, 7 de Abril de 2004 - Página GRELHADOS SOBRE CARVÃO Paulo F. Gonçalves Páscoa 2004 PFGPFG B.A., A.V.C. Seguros : > Doença grave > Hipoteca MAÎTRE CARROSSIER > Salário > Vida Consulte-me sem compromisso!!! 8261 BOUL. ST-LAURENT Prop. Elvis Soares (514) 389-0606 (514) 884-0522 Ano XLII • Nº 14 email: [email protected] WWW.AVOZDEPORTUGAL19.COM de junho 7de DE 2002 Abril de 2004 Apontamento Jean Lapierre em entrevista A Libertação de Gostava de ter voltado Jorge Ritto à política para defender ideias... É Uma Vergonha para o País Por Luís Tavares Bello Encontrámos recentemente Jean Lapierre, que é o candidato do Partido Liberal * A. Barqueiro do Canadá na circunscrição de Outremont e também o “braço direito” do Primeiro- ministro do Canadá Paul Martin na província do Quebeque. A generalidade dos portugueses, Desse encontro aqui deixamos a nossa troca de impressões. tanto os que residem no país, como VP – O Senhor já foi ministro, respondi sim. Respondi sim porque com os que se encontram fora, estão deputado, e mais recentemente a chegada de Paul Martin, de uma nova indignados pela decisão do Tribunal comunicador de grande êxito na equipa, de um novo programa, de um da Relação de Lisboa, que ordenou estacão televisiva TQS e na emissora novo tom, disse para mim mesmo que a libertação do Embaixador Jorge de radio CKAC. Usufruía pois até há valia a pena dar o salto para a política Ritto, em prisão preventiva desde pouco, de condições financeiras e senti que tinha o gosto de servir. Maio de 2003, por suspeitas de abuso seguramente mais interessantes e de VP- Todavia constato que ainda é sexual de crianças e lenocínio um trabalho com menos “stress”. -
Rtl: Formel I - Rennen 1992
Dr. Kathryn Boi Die Formel 1 als mediatisiertes Sportereignis: Organisation, Präsentation und Rezeption Quelle Bild: Mail Christian Danner vom 24.02.2013 Online-Anhang (Teil 1) Inhalt: 1. Übersicht der Fernsehübertragungen am Rennsonntag (1981 bis 2004) 2. Einschaltquoten RTL (1992 bis 2012) 3. Faktorisierte Zuschauerzahlen im Saisonverlauf 4. Fahrerstatistiken zu allen stichprobenrelevanten Rennen 5. Teamstatistiken zu allen stichprobenrelevanten Rennen 6. Zeiteinheiten und Rangdurchschnitte 7. Fahrerpositionen in der Moderatorenbeliebtheitsskala (Teil 1 und 2) 8. Durchschnittliche Kommentarzeiten der Fahrer pro Namensnennung 9. Ermittlung der Übertragungsschwerpunkte pro Zeitabschnitt 10. Detailbetrachtung der Rennausfälle 11. Komplettliste Einblendungsarten 12. Einblendungen in der Übertragungsrealität 13. Telefoninterview Christian Danner 14. Farbabbildungen 1 Übersicht der Fernsehübertragungen am Rennsonntag (1981 bis 2004) Übersicht Fernsehübertragungen Rennsonntag Renndaten Aufwärmtraining So Countdown Rennen Highlights Jahr Land Ort Datum stattgf. ORF ÖR RTL Eurosp. DSF ntv DF1 Premiere stattgf. RTL stattgf. ORF ÖR RTL Eurosp. DSF ntv DF1 Premiere stattgf. RTL 1980 Argentinien Buenos Aires 13.01.80 1 1980 Brasilien Interlagos 27.01.80 1 1980 Südafrika Kyalami 01.03.80 1 1980 USA-West Long Beach 30.03.80 1 1980 Belgien Zolder 04.05.80 1 1 1980 Monaco Monte Carlo 18.05.80 1 1 1980 Frankreich Le Castellet 29.06.80 1 1 1980 Großbritannien Brands Hatch 13.07.80 1 1 1980 Deutschland Hockenheim 10.08.80 1 1 1980 Österreich Österreichring