Ground Performance Testing of Cubesat ADCS Case Study on Delfi-N3xt Van Kleef, A.J.P. , Oving, B.A. , Verberne, C.J. , Haemmerli
Total Page:16
File Type:pdf, Size:1020Kb
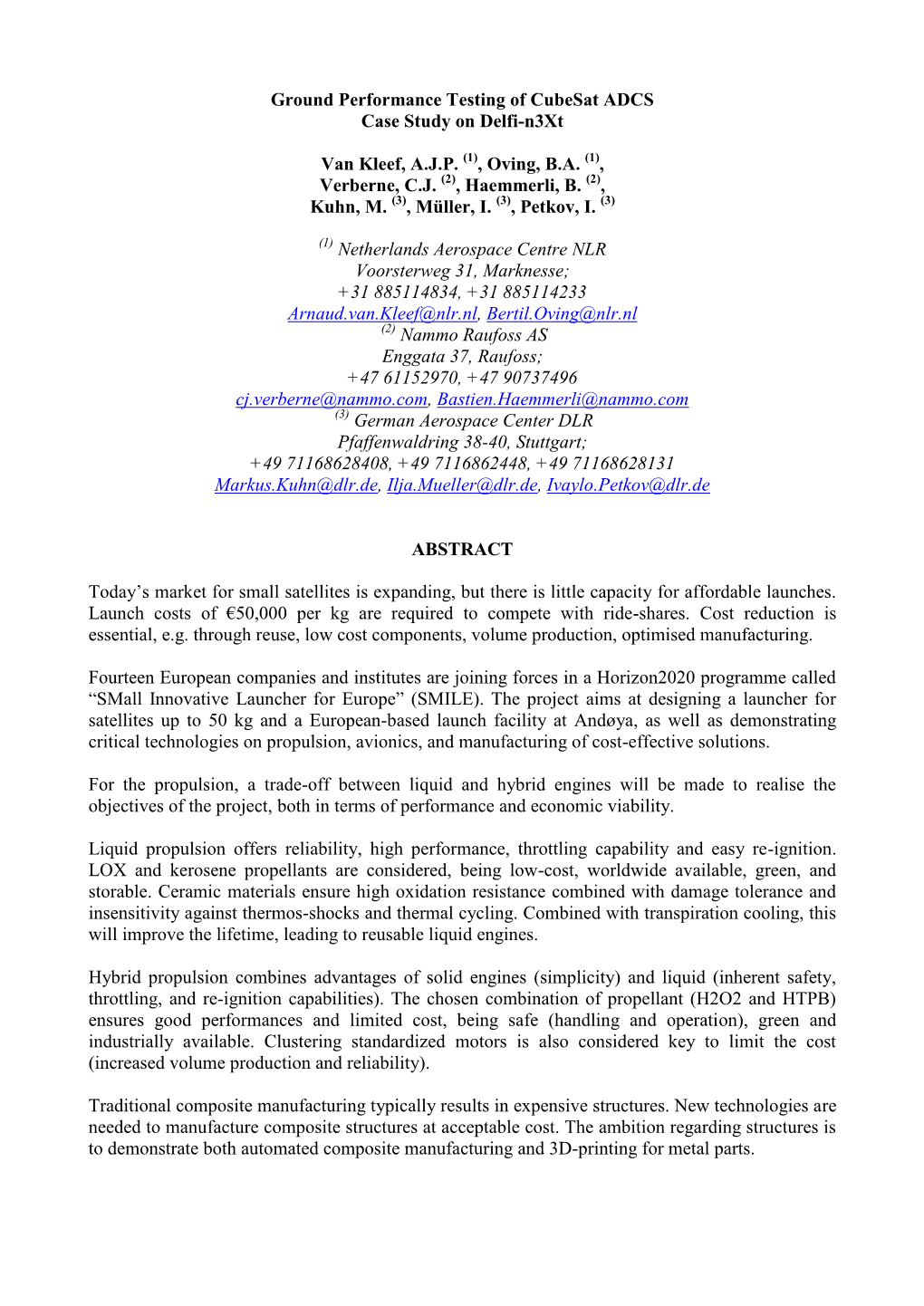
Load more
Recommended publications
-
Aerospace America
June 2016 Ambition: Europa NASA might find more than life in this moon’s ocean. It could find a new strategy for exploring other worlds. Page 22 Oklahoma’s Bridenstine on climate, term limits/8 20 years of Design/Build/Fly/30 Smart bombs for wildfires/38 A PUBLICATION OF THE AMERICAN INSTITUTE OF AERONAUTICS AND ASTRONAUTICS • COVER-0616ƒ.indd 1 5/19/16 1:18 PM 2O16 13 –17 JUNE 2016 WASHINGTON, D.C. AIAA AVIATION 2016 is the only aviation Exclusive Premier Sponsor event that covers the entire integrated spectrum of aviation business and technology. Confirmed Speakers Charles F. Michimasa Maj. Gen. Mike Delaney John S. Richard A. Clarke Bolden Jr. Fujino Joe Engle Langford Vice President, Chairman & CEO, Administrator, President & CEO, United States Air Airplane Chairman and Good Harbor NASA Honda Aircraft Force (Ret.) Development, Chief Executive Security Risk Company The Boeing Officer, Aurora Management, LLC Company Flight Sciences Corporation REGISTER TODAY! AIAA-AVIATION.ORG 16-1132 June 2016 DEPARTMENTS Page 16 EDITOR’S NOTEBOOK 2 Congress’s dynamic aerospace duo IN BRIEF 4 3D-printed drone; status change at Ames? smart repair manuals; Page 34 subscale aircraft CONVERSATION 8 Change agent for aerospace CASE STUDY 12 Preventing more MH370s ENGINEERING NOTEBOOK 16 Making a money saver OUT OF THE PAST 46 Page 4 CAREER OPPORTUNITIES 48 FEATURES AMBITION: EUROPA 22 Jupiter’s moon Europa could have life in the ocean under its shell. NASA came up with a step-by-step plan to find out. Then, along came a congressman from Texas. by Debra Werner Page 38 DESIGNING A WINNER 30 AIAA’s Design/Build/Fly contest gives college students a chance to pit their engineering smarts against international competitors in a remote-controlled aircraft flyoff. -
Technical Report on Different RLV Return Modes' Performances
Formation flight for in-Air Launcher 1st stage Capturing demonstration Technical Report on different RLV return modes’ Performances Deliverable D2.1 EC project number 821953 Research and Innovation action Space Research Topic: SPACE-16-TEC-2018 – Access to space FALCon Formation flight for in-Air Launcher 1st stage Capturing demonstration Technical Report on different RLV return modes’ Performances Deliverable Reference Number: D2.1 Due date of deliverable: 30th November 2019 Actual submission date (draft): 15th December 2019 Actual submission date (final version): 19th October 2020 Start date of FALCon project: 1st of March 2019 Duration: 36 months Organisation name of lead contractor for this deliverable: DLR Revision #: 2 Dissemination Level PU Public X PP Restricted to other programme participants (including the Commission Services) RE Restricted to a group specified by the consortium (including the Commission Services) CO Confidential, only for members of the consortium (including the Commission Services) APPROVAL Title issue revision Technical Report on different RLV return modes’ 2 1 performances Author(s) date Sven Stappert 19.10.2020 Madalin Simioana 21.07.2020 Martin Sippel Approved by Date Sven Stappert 19.10.2020 Martin Sippel FALCon D2.1: RLV Return Mode Performances vers. 19-Oct-20 Page i Contents List of Tables iii List of Figures iii Nomenclature vi 1 Executive Summary ......................................................................................... 1 1.1 Scope of the deliverable ............................................................................................ -
Disrupting Launch Systems
DISRUPTING LAUNCH SYSTEMS THE RISE OF SPACEX AND EUROPEAN ACCESS TO SPACE Thesis submitted to the International Space University in partial fulfillment of the requirements of the M. Sc. Degree in Space Studies August 2017 Thesis author: Paul Wohrer Thesis supervisor: Prof. Jean-Jacques Favier International Space University 1 Abstract The rise of SpaceX as a major launch provider has been the most surprising evolution of the launch sector during the past decade. It forced incumbent industrial actors to adapt their business model to face this new competitor. European actors are particularly threatened today, since European Autonomous Access to Space highly depends on the competitive edge of the Ariane launcher family. This study argues that the framework of analysis which best describes the events leading to the current situation is the theory of disruptive innovation. The study uses this framework to analyse the reusability technology promoted by new actors of the launch industry. The study argues that, while concurring with most analysis that the price advantage of reused launchers remains questionable, the most important advantage of this technology is the convenience it could confer to launch systems customers. The study offers two recommendations to European actors willing to maintain European Autonomous Access to Space. The first one aims at allocating resources toward a commercial exploitation of the Vega small launch system, to disrupt the growing market of small satellites and strengthen ties with Italian partners in the launcher program. The second aims at increasing the perception of European launchers as strategic assets, to avoid their commoditization. The recommendation entails developing an autonomous European capacity to launch astronauts into space, which could strengthen the ties between France and Germany as well as lead to a rationalization of the geo-return principle. -
Future Launchers Preparatory Programme”: the Reusability Option for Ariane Evolutions
DOI: 10.13009/EUCASS2019-971 8TH EUROPEAN CONFERENCE FOR AERONAUTICS AND SPACE SCIENCES (EUCASS) LAUNCH VEHICLES SYSTEM STUDIES IN THE “FUTURE LAUNCHERS PREPARATORY PROGRAMME”: THE REUSABILITY OPTION FOR ARIANE EVOLUTIONS. Olivier Gogdet(1), Jamila Mansouri(2), Jerome Breteau(3) , Antoine Patureau De Mirand(4), (5) Eric Louaas (1) Ariane Group (AG), 66, route de Verneuil, 78130 Les Mureaux (France) Email:[email protected] (2) European Space Agency (ESA), 52, rue Jacques Hillairet, 75012 Paris (France) Email:[email protected] (3) European Space Agency (ESA), 52, rue Jacques Hillairet, 75012 Paris (France) Email:[email protected] (4) Centre National d’Etudes Spatiales (CNES), 52, rue Jacques Hillairet, 75012 Paris Cedex (France) Email:[email protected] (5) Centre National d’Etudes Spatiales (CNES), 52, rue Jacques Hillairet, 75012 Paris Cedex (France) Email:[email protected] ABSTRACT: The European launchers shall answer the evolutions of the payloads and their mission profiles. Ariane 6 and Vega-C programmes are the next step “short term” answers. But Beyond that, the Future Launchers Preparatory Programme (FLPP) managed By ESA, prepares the future launcher system architectures and the enaBling technologies through demonstrators. Concerning the future of Ariane, and in front of the increasing competition pressure, the system and technology activities in FLPP/NEO shall prepare the options that will ensure sustainaBle competitiveness. Part of these activities, the in-flight reusaBle vehicle demonstration aims to contriBute to the following targets: • Ariane Recurring Cost decrease with a target of -50% compared to Ariane 6 Baseline • ReusaBility to reduce investment in production means (CAPEX) • Acquisition of the reusaBility key competences not availaBle in Europe The reusaBility option, for the future liquid Boosters and/or lower stage, is under evaluation through Ariane Group studies currently ongoing. -
Launch Vehicle First Stage Reusability a Study to Compare Different Recovery Optionslaunch Vehicle for Am
Launch Vehicle First Stage Reusability Launch Vehicle First Stage Reusability a study to compare different Technische Universiteit Delft recovery options for a reusable launch vehicle M. D. Rozemeijer Launch Vehicle First Stage Reusability a study to compare different recovery options for a reusable launch vehicle by M. D. Rozemeijer to obtain the degree of Master of Science at the Delft University of Technology, to be defended publicly on Tuesday December 1st, 2020 at 09:00. Student number: 4141733 Project duration: April 23, 2019 – December 1, 2020 Thesis committee: Ir. B. T. C. Zandbergen, TU Delft, supervisor Dr. A. Cervone, TU Delft Ir. M. C. Naeije, TU Delft An electronic version of this thesis is available at http://repository.tudelft.nl/. Preface This report concludes, and is the culmination of, my Master thesis to complete the master curriculum in the field of Aerospace Engineering. Besides this, it also, hopefully, answers part of the question on how to make access to space easier. I have been working in the field of entry descent and landing since the start of the Stratos III project in 2016. This is also the start of the ParSim tool, which is the base of my thesis tool. Back then it was only able to recover part of the Stratos III rocket. This tool expanded to encompass the demands for the other projects I have been working on within Delft Aerospace Rocket Engineering (DARE), which are Project Aether and the Supersonic Parachute Experiment Aboard Rexus (SPEAR) all within the Parachute Research Group. Besides the tool, working on these projects increased my knowledge of Entry, Descent and Landing tremendously. -
Paper: Is It Worth It? the Economics of Reusable Space Transportation
Presented at the 2016 International Training Symposium: www.iceaaonline.com/bristol2016 Is It Worth It? The Economics of Reusable Space Transportation ICEAA 2016 International Training Symposium Bristol, UK, October, 2016 Richard Webb KAR Enterprises Abstract Over the past several decades billions of dollars have been invested by governments and private companies in the pursuit of lower cost access to space through earth-to-orbit (ETO) space transportation systems. Much of that investment has been focused on the development and operation of various forms of reusable transportation systems. From the Space Shuttle to current efforts by private commercial companies, the overarching belief of those making such investments has been that reusing system elements will be cheaper than utilizing expendable systems that involve throwing away costly engines, avionics, and other hardware with each flight. However, the view that reusable systems are ultimately a “better” approach to providing ETO transportation is not held universally by major stakeholders within the space transportation industry. While the technical feasibility of at least some degree of reusability has been demonstrated, there continues to be a sometimes lively debate over the merits and drawbacks of reusable versus expendable systems from an economic perspective. In summary, is it worth it? Based on our many years of direct involvement with the business aspects of several expendable and reusable transportation systems, it appears to us that much of the discussion surrounding reusability is hindered by a failure to clearly define and understand the financial and other metrics by which the financial “goodness” of a reusable or expandable approach is measured. As stakeholders, the different users and suppliers of space transportation have a varied set of criteria for determining the relative economic viability of alternative strategies, including reusability. -
Intel International Science and Engineering Fair 2016 Program May 8 – 13, 2016 Phoenix, Arizona Intel International Science and Engineering Fair
THINK BEYOND Intel International Science and Engineering Fair 2016 Program May 8 – 13, 2016 Phoenix, Arizona Intel International Science and Engineering Fair About the Intel ISEF The Intel International Science and Engineering Fair (Intel ISEF), a program of Society for Science & the Public, is the world’s largest international pre-college science competition. The Intel ISEF is the premier science competition in the world and provides a forum for more than 1,750 high school students from more than 75 countries, regions and territories to showcase their independent research annually. Each year, millions of students worldwide compete in local science fairs; winners go on to participate in Intel ISEF-affiliated regional, state and national fairs to earn the opportunity to attend the Intel ISEF. Uniting these top young scientific minds, the Intel ISEF provides the opportunity to finalists to display their talent on an international stage, while enabling them to submit their work for judging by doctoral-level scientists. The Intel ISEF provides awards of nearly $4 million in prizes and scholarships annually. Intel International Science and Engineering Fair 2016 Intel International Science and Engineering Fair 2016 Greetings ..........................................................................................................2 Title Sponsor ..................................................................................................6 Gordon E. Moore Award ..........................................................................7 About -
Innovative Small Launcher
NLR-TP-2015-472 | November 2015 Innovative Small Launcher CUSTOMER: Netherlands Aerospace Centre NLR – Netherlands Aerospace Centre Netherlands Aerospace Centre The NLR is a leading international research centre for aerospace. Bolstered by its multidisciplinary expertise and unrivalled research facilities, NLR provides innovative and integral solutions for the complex challenges in the aerospace sector. The NLR’s activities span the full spectrum of Research Development Test & Evaluation (RDT & E). Given the NLR’s specialist knowledge and facilities, companies turn to the NLR for validation, verification, qualification, simulation and evaluation. The NLR thereby bridges the gap between research and practical applications, while working for both government and industry at home and abroad. The NLR stands for practical and innovative solutions, technical expertise and a long-term design vision. This allows the NLR’s cutting edge technology to find its way into successful aerospace programs of OEMs, including Airbus, Embraer and Pilatus. NLR contributes to (military) programs, such as ESA’s IXV re-entry vehicle, the F-35, the Apache helicopter, and European programs, including SESAR and Clean Sky 2. Founded in 1919, and employing some 650 people, the NLR achieved a turnover of 73 million euros in 2014, of which three-quarters derived from contract research, and the remaining from government funds. For more information visit: www.nlr.nl EXECUTIVE SUMMARY UNCLASSIFIED Innovative Small Launcher Problem area REPORT NUMBER The market for small satellites is expected to increase substantially in NLR-TP-2015-472 the coming years, but there is little capacity to launch them affordably. No operational dedicated launcher for small satellites exists today. -
NASA Mosaic of #Plutotime Photos
December 2015 2015 NASA mosaic of #PlutoTime photos A PUBLICATION OF THE AMERICAN INSTITUTE OF AERONAUTICS AND ASTRONAUTICS At this time of year, we count our blessings and give back to the people and organizations that have helped us grow in our profession. Please join the AIAA Foundation Board of Trustees and many AIAA members who have already donated to the AIAA Foundation. Your support is critical to our work of offering educational programs, conferences, scholarships and design competitions. Share your legacy and support and inspire tomorrow’s aerospace leaders by giving to the AIAA Foundation. www.aiaafoundation.org #AdvancingAerospace AIAA strongly believes in the importance of our educational programs and will match individual and corporate donations up to $1 million dollars (of unrestricted funds). The AIAA Foundation is a nonprofit, tax-exempt organization recognized under section 501(c)(3) of the United States Internal Revenue Code. All donations are tax deductible. December 2015 EDITOR’S NOTEBOOK 2 OUT OF THE PAST 72 CAREER OPPORTUNITIES 74 THE YEAR IN REVIEW The most important developments as described by AIAA’s Technical and Program Committees Adaptive Structures 6 Microgravity and Space Processes 61 Aeroacoustics 14 Missile Systems 62 Aerodynamic Decelerator Systems 26 Multidisciplinary Design Optimization 7 Aerodynamic Measurement Technology 15 Non-Deterministic Approaches 8 Aerospace Power Systems 50 Nuclear and Future Flight Propulsion 56 Aircraft Design 27 Plasmadynamics and Lasers 23 Aircraft Operations 28 Pressure -
A Systematic Comparison of Reusable First Stage Return Options
DOI: 10.13009/EUCASS2019-438 8TH EUROPEAN CONFERENCE FOR AERONAUTICS AND SPACE SCIENCES (EUCASS) A Systematic Comparison of Reusable First Stage Return Options Sven Stappert*, Jascha Wilken*, Leonid Bussler*, Martin Sippel* *German Aerospace Center (DLR), Institute of Space Systems, Robert-Hooke-Straße 7, 28359 Bremen [email protected], [email protected], [email protected], [email protected] Abstract The recent success of the emerging private space companies SpaceX and Blue Origin in landing, recovering and relaunching first stages have demonstrated the possibility of building reliable reusable launchers with low launch costs. Due to this risen interest in reusability, the project AKIRA was initiated by the German Aerospace Center (DLR) in 2017. This multidisciplinary project focuses on identifying and investigating key technologies for possible future reusable launch vehicles. Within this paper the focus is set on the comparison of different return options including vertical takeoff, vertical landing and vertical takeoff, horizontal landing on a technological and economic level. Abbreviations AoA Angle of Attack ASDS Autonomous Spaceport Droneship DRL Downrange Landing EC Economical Condition ELV Expendable Launch Vehicle FB Flyback GLOM Gross Lift-Off Mass IAC In-Air Capturing Isp Specific Impulse LFBB Liquid Fly-Back Booster LZ-1 Landing Zone 1 MECO Main Engine Cut-Off RLV Reusable Launch Vehicle RoRo Roll On, Roll Off (Ship) RTLS Return to Launch Site STS Space Transportation System TOSCA Trajectory Optimization and Simulation of Conventional and Advanced Spacecraft TRL Technology Readiness Level VTHL Vertical Takeoff, Horizontal Landing VTVL Vertical Takeoff, Vertical Landing 1. Introduction While reusability in space transportation can have a strong impact on the costs and thus competitiveness of space launchers, the historic Space Shuttle has also shown that this impact does not necessarily have to be positive if the refurbishment costs cannot be kept low. -
The Economics of Reusable Space Transportation ICEAA 2016 International Training Symposium Bristol, UK, October, 2016 Richard Webb KAR Enterprises Abstract
https://ntrs.nasa.gov/search.jsp?R=20160013370 2019-08-29T17:24:41+00:00Z View metadata, citation and similar papers at core.ac.uk brought to you by CORE provided by NASA Technical Reports Server Is It Worth It? The Economics of Reusable Space Transportation ICEAA 2016 International Training Symposium Bristol, UK, October, 2016 Richard Webb KAR Enterprises Abstract Over the past several decades billions of dollars have been invested by governments and private companies in the pursuit of lower cost access to space through earth-to-orbit (ETO) space transportation systems. Much of that investment has been focused on the development and operation of various forms of reusable transportation systems. From the Space Shuttle to current efforts by private commercial companies, the overarching belief of those making such investments has been that reusing system elements will be cheaper than utilizing expendable systems that involve throwing away costly engines, avionics, and other hardware with each flight. However, the view that reusable systems are ultimately a “better” approach to providing ETO transportation is not held universally by major stakeholders within the space transportation industry. While the technical feasibility of at least some degree of reusability has been demonstrated, there continues to be a sometimes lively debate over the merits and drawbacks of reusable versus expendable systems from an economic perspective. In summary, is it worth it? Based on our many years of direct involvement with the business aspects of several expendable and reusable transportation systems, it appears to us that much of the discussion surrounding reusability is hindered by a failure to clearly define and understand the financial and other metrics by which the financial “goodness” of a reusable or expandable approach is measured. -
Space Age Is Emerging
EQUITY RESEARCH | April 4, 2017 A new Space Age is emerging. Rocket launches are being privatized, the most ambitious satellite constellation ever is Noah Poponak, CFA being deployed, man is looking +1 212 357-0954 back to the Moon and to Mars, [email protected] and militaries are vying for the Goldman, Sachs & Co. ultimate high ground. In the latest in our Profiles in Matthew Porat +1 801 884-4174 Innovation series, we examine [email protected] where new industries are being Goldman, Sachs & Co. created, and where others are being disrupted in the latest race Michael Bishop +44(20)7552-4248 to harness the cosmos. We show [email protected] how technological advances and Goldman Sachs International necessity are creating a wave of opportunity as business and Chris Hallam governments invest in a new +44(20)7552-2958 [email protected] Space Economy. Goldman Sachs International Brett Feldman INSIDE: +1 212 902-8156 [email protected] Goldman, Sachs & Co. Private Company Ecosystem Heath P. Terry, CFA +1 212 357-1849 [email protected] Goldman, Sachs & Co. PROFILESIN INNOVATION The Next Investment Frontier Goldman Sachs does and seeks to do business with companies covered in its research reports. As a result, investors should be aware that the firm may have a conflict of interest that could affect the objectivity of this report. Investors should consider this report as only a single factor in making their investment decision. For Reg AC certification and other important disclosures, see the Disclosure Appendix, or go to www.gs.com/research/hedge.html.