Brighton Gasworks
Total Page:16
File Type:pdf, Size:1020Kb
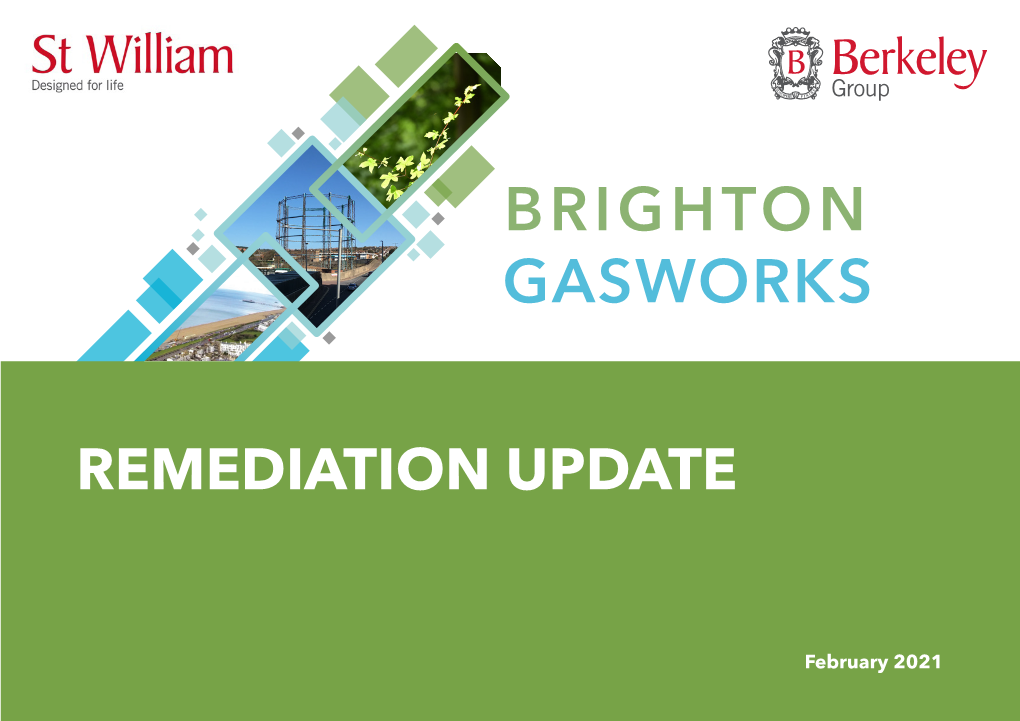
Load more
Recommended publications
-
Queens Park Area Bus Routes
ROUTE Queens Park l City Centre Tourist Attractions North Street/Old Steine for Theatre Seven Dials Royal, Royal Pavilion, Dow Ter n Jubilee Library, Brighton Pepper Pot race ad Ro Using the train Museum, Palace Pier, rk 18 a D P d Mon-Sat too - see page 15 y s a k n o e Brighton Station e R daytimes Sea Life Centre R e d u ld . e Q fi 18 sh Brighton Station for Waitrose re No F Queens rth 18 Churchill S . t. l Toy Museum P Park Square t 18 n o m e r g E Daily Brighton Old Steine Mondays to Saturdays route number 18 18 18 18 18 18 18 18 18 18 18 18 18 18 18 18 18 18 18 18 18 18 18 18 18 18 day code MF MF MF S MF S Pepper Pot, Queens Park Terrace 0604 0624 0644 0704 0724 0744 0804 0824 0844 0904 0916 31 46 01 16 1431 1446 1501 1516 1532 1548 Old Steine (stop U) 0609 0630 0650 0711 0731 0751 0811 0831 0851 0911 0923 38 53 08 23 1438 1453 1508 1523 1539 1555 Brighton Station= (stop E) 0615 0636 0656 0717 0738 0759 0819 0839 0850 0859 0919 0931 46 01 16 31 1446 1501 1516 1531 1547 1604 Seven Dials, Vernon Terrace t t t t t t t t t t t 0934 t 04 t 34 t 1504 t 1534 t t Waitrose, Western Road t t t t t t t t t t t 0937 t 07 t 37 t 1507 t 1537 t t opp Homelees House, Dyke Rd 0617 0638 0658 0719 0740 0801 0821 0841 0852 0901 0921 t 48 t 18 t 1448 t 1518 t 1549 1606 until Churchill Square (stop H) 0622 0643 0703 0724 0745 0806 0826 0846 0857 0906 0926 0941 then at 56 11 26 41 1456 1511 1526 1541 1557 1611 North Street (stop B) 0624 0645 0705 0726 0747 0808 0828 0848 0859 0908 0928 0944 59 14 29 44 1459 1514 1529 1544 1600 1614 Down Terrace, Stonehurst -
Social and Emotional Aspects of Learning (SEAL) Materials
BRIGHTON AND HOVE Moving On 2 A resource to support Year 6 and Year 7 students in developing social and emotional skills for transfer. Healthy Schools Team Hove Park Mansions Hove Park Villas Hove BN3 6HW Tel: 01273 293530 Fax: 01273 295392 E-mail: [email protected] The Healthy Schools Team will provide updates to this resource online Published May 2009 Preface The transfer from primary school to secondary school is a significant event involving many complex emotions. The move ought to be successful for all pupils and we should try to ensure that the process is as smooth as possible. In Brighton & Hove schools there is already much good practice supporting pupils in managing this significant change. The CYPT welcomes wholeheartedly this new resource, Moving On 2. It will provide schools with additional materials for use within the curriculum, ensuring that pupils feel that their primary level achievements are valued and acknowledged, and enabling them to build on those achievements at secondary level. Preface ThisThe transfer resource, from primary school which to secondar yhas school isbeen a significant developed event by Brighton & Hove teachers working with consultants from involving many complex emotions. The move ought to be successf u l for all pupils and we should try to ensure that the process is as smooth as possible. theIn Brighton Advisory & Hove schools Service,there is already much replaces good practice supportingthe Moving On booklet and instead provides a Year 6 unit of work that pupils in managing this significant change. links effective literacy planning to the Social and Emotional Aspects of Learning (SEAL) materials. -
University of Brighton Guide Brighton and Sussex Medical School (BSMS) B74
WWhenhen you have finished wwiith this prospectus please recycle it. Central contact details University of Brighton Mithras House Lewes Road Brighton BN2 4AT email [email protected] telephone (01273) 644644 fax (01273) 642607 international code (+441273) UCAS institutional codes University of Brighton (BRITN) B72 University of Brighton Hastings campus (BRITN) B72 campus code U University of Brighton Guide Brighton and Sussex Medical School (BSMS) B74 There’s more online... Please refer to the website, www.brighton.ac.uk/courses for up-to-date course information. www.brighton.ac.uk A–Z course finder 02–03 Choosing the University of Brighton 04–47 Great minds 04–05 Inspirational teaching 06–07 Career-focused 08–09 Enriching experiences 10–11 A brilliant place to live 12–13 Brighton 14–15 Falmer campus 16–17 Courses at Falmer 18–19 Grand Parade campus 20–21 Courses at Grand Parade 22–23 Moulsecoomb campus 24–25 Courses at Moulsecoomb 26–29 Eastbourne 30–31 Eastbourne campus 32–33 Courses at Eastbourne 34–35 Hastings 36–37 Hastings campus 38–39 Courses at Hastings 40–41 Support for you 42–45 Your Brighton experience 46–47 All about… 48–81 How to apply 50–51 Entry requirements 52–54 University of Brighton Compact 55 Types of course 56 International students 57–59 Money 60–68 Where to live 69–76 Open days 77 Timeline 78–79 General index 80 How to find us 81 www.brighton.ac.uk 01 A–Z COURSE FINDER Accounting and Finance BSc(Hons) M 26 Criminology and Sociology BA(Hons) F 19 Aeronautical Engineering BEng(Hons) M 28 Criminology and Substance -
NORTH PORTSLADE COMMUNITY NEWS Produced and Delivered Free by Volunteers to Over 6,000 Local Homes and Businesses Throughout Portslade Issue No
NORTH PORTSLADE COMMUNITY NEWS Produced and delivered free by volunteers to over 6,000 local homes and businesses throughout Portslade Issue No. 143 APRIL / MAY 2020 A Portslade & Mile Oak Covid-19 support group has been set up - look on Facebook for further details. Information boards now in place Following news that the ruins of Portslade Old Manor are to be resurrected as a local history focal point, with information boards being written by residents, John Shepherd from the Fresh Start Charity reports 10 boards have now been in ‐ stalled. When researching and writing about the varying stages in Portslade’s history ‐ from 1066 to the current day ‐ volunteers were supported by local historians, archaeologists and the University of Sussex. The boards are the first steps in ensuring the long‐term sur ‐ vival of the Manor grounds, which it’s hoped will be opened Timeline boards. to the public this year. John says the Charity is planning a se ‐ Volunteer site guardians have also been recruited to help ries of improvements which include essential repairs to the maintain the grounds and undertake basic historic preser ‐ stonework, better access and a general revamping of the site. vation. Portslade Families Activities Morning The Parish Centre, South Street, BN41 2LE Arts & crafts plus lots of other activities available Drinks and snacks provided £1 donation per child* suggested Wednesday 15 April, 10.30‐12.30 *children must be accompanied by a parent/carer at all times Portslade Community Forum Portslade Community Forum (PCF) will now be meeting every three months at 7.15pm at Lifelong learner Bernard hits 100! The Village Centre, Windlesham Close, Portslade. -
Princesscollection Welcome
PrincessCollection Welcome We are a specialist boutique British manufacturer of solid brass door and window products, including the original iconic Princess and Constable Collections, along with custom accessories for electrical applications and bathrooms. With a unique range of Collections dating back to architectural periods in the early 16th Century we offer a uniquely extensive range of Period, Heritage and Contemporary Door Furniture made from the purest Brass all hand worked, polished and finished on site... in England. We work with professional and private clients worldwide to create elegant door and window furniture products for royal palaces, super yachts, stately homes and high specification private residences. Here and on our website you can learn more about us, the work we do and how we can help you add those finishing touches of elegancee Our Timeline of Architectural Styles Welcome to our Collections architectural timeline! We are in a privileged position to be able to showcase to you our range of period, heritage, classic and contemporary Collections including the original iconic Princess and Constable Collections. All of our Collections make reference to a particular historical architectural style, helping you choose the right finishing touches to your home. Within our Collections you will find a number of product types so that you can add that luxury touch, not only to your doors! Louis XIV Louis XV Louis XVI Adam Constable Executive Style: Baroque & Rococo Style: Neoclassical Style: Victorian Style: Modern 1590-1725 1750-1880 1835-1901 1918-2000 Style: Ancient Greek Style: Georgian Style: Regency Style: Art Nouveau Style: Contemporary 1200BC-100AD 1720-1840 1810-1835 1890-1910 1980-now Coming Soon Meandros Burlington Governor Princess Liberty Bamboo 2 Princess Collection Style: Regency 1810-1835 A Brief History The Regency era circa 1795 to 1840 was noted in history for its elegance and achievements in the fine arts and architecture and some say excesses by the aristocracy. -
Brighton Energy Co-Op: an Innovation History
Brighton Energy Co-op: An Innovation History July 2012 Report prepared by Sabine Hielscher on behalf of the Community Innovation for Sustainable Energy research team July 2012 For further information please contact: Sabine Hielscher Research Fellow – The Sussex Energy Group SPRU – Science and Technology Policy Research University of Sussex, Freeman Centre Brighton, BN1 9QE Email: [email protected] Tel: +44 (0)1273 678165 www.grassrootsinnovations.org The Community Innovation for Sustainable Energy project is a partnership between the University of Sussex and the University of East Anglia. The project is funded by the UK Engineering and Physical Sciences Research Council (EPSRC) and the European Centre Laboratories for Energy Efficiency Research (ECLEER) of EdF Energ Brighton Energy Co-op Brighton Energy Co-op The Brighton Energy Co-op is a community renewable energy project based in Brighton & Hove. The Co-op currently consists of a chairman, Will Cottrell, two directors, Damian Tow and Ross Gilbert and three advisors, Danni Craker, Jeremy Leggett and John Smith. The Brighton Energy Co-op aims to run and finance renewable energy projects in Brighton & Hove whilst benefiting the local community and the environment. They want to enable people to invest money into renewable energy projects that provide a small financial return to its members but also deliver environmental and social benefits. In the process they aim to make the running of renewable projects more democratic. This innovation history traces the development of the Brighton Energy Co-op from its conception (i.e. the coming together of three people in June 2010) through its development phase, with its numerous setbacks and comebacks (e.g. -
Groundwater Flooding in Brighton & Hove
Section 19 Flood Investigations Report Groundwater Flooding in Brighton and Hove City (February 2014) May 2014 Revision Schedule Rev Date Details Author Checked and Approved by 1 April 2014 M Moran N Fearnley 2 May 2014 Following comments from the EA and M Moran N Fearnley Southern Water (6/05/2014) 3 June 2014 Following comments from Southern Water M Moran N Fearnley Contents 1. Introduction............................................................................................................... 1 2. Groundwater Flood History...................................................................................... 5 3. Groundwater Flood Event - February 2014............................................................. 7 4. Recommendations.................................................................................................... 13 Figures Figure 1 Geological bedrock map. (Environment Agency) ....................................................... 3 Figure 2 Topography and Areas Affected in Brighton and Hove City – February 2014 ............ 4 Figure 3 Groundwater Levels – 2000/2001 ............................................................................... 5 Figure 4 Flood Event 2000/2001 ............................................................................................... 6 Figure 5 Ditchling Road - Rainfall (mm) .................................................................................... 7 Figure 6 High Park Farm - Rainfall (mm).................................................................................. -
Brighton and Hove Food Strategy Action Plan 2018-2023 Brighton and Hove Food Strategy Action Plan – 2018-2023 2 in Collaboration With
Brighton and Hove Food Strategy Action Plan 2018-2023 Brighton and Hove Food Strategy Action Plan – 2018-2023 2 In collaboration with... Expert Panel Members • Brighton & Hove City Council • Department for Work and • NHS Brighton & Hove Clinical • University of Sussex* (including 26 departments) Pensions Commissioning Group* • UnLtd • Brighton & Hove City Council • Brighton & Hove Energy Services • Digital Brighton and Hove • Old Tree Brewery • Varndean College (BHCC) Cooperative (BHESCo) • Dorothy Stringer School • Paper Round* • Varndean School • • Brighton & Hove Connected Brighton & Hove Food Festival* • Downland Estate Farmers* • PigShare / SheepShare • Visit Brighton* • • Brighton & Hove Food Brighton & Hove Food • East Sussex Healthcare • Plastic Free Brighton • Western Sussex Hospitals Partnership (BHFP) Partnership NHS Trust* • Platf9rm NHS Foundation Trust* • • Brighton & Sussex University Brighton & Hove Impetus • FareShare Sussex* • Plumpton College* • Whitehawk Community Hospitals NHS Trust (BSUH) • Brighton & Hove Organic • Fin & Farm* • Possability People Food Project • Community Works Gardening Group • Florence Road Market • Refill Brighton & Hove • World Food Project • FareShare Sussex • Brighton & Sussex • Food Banks via Emergency • Restaurants Brighton • NHS Brighton & Hove Clinical Medical School Food Network (EFN) • National Supporting • Saddlescombe Farm* Commissioning Group (CCG) Brighton & Sussex University • Food Pioneers* Organisations Hospitals NHS Trust* • South Downs National Park* • Possability People • Fork -
The Public Consultation for Homes for Brighton & Hove in Portslade
Public Consultation July 2018 Portslade Industrial Site 01 Existing aerial photographs Welcome to the Public Consultation for Homes for Brighton & Hove in Portslade The former Belgrave Day Centre site in Portslade is one of the first sites that Homes for Brighton & Hove are planning to develop into affordable housing, with 50% of the homes Site available for rent and the remaining 50% as shared ownership. All the homes will be for working households living in the city, set at rates affordable to people working on the Living Wage. This site is owned by Brighton & Hove City Council and has been identified in the Joint Area Action Plan as a brownfield site intended to be developed as residential homes. The location is currently surrounded by industrial estates, but neighbouring sites on Wellington Road are also intended to be developed in the future and this site will help act as a catalyst for the regeneration and improvement of the area. It is also an area that is well served with local transport and community facilities. The potential of building homes here opens up public access through the site between North Street and Wellington Road, with attractive, planted areas. It will increase pedestrian Aerial View from north-east footfall around the location that is expected to help revitalise the southern end of Boundary Road. Site Project timeline Early Drop in Finalisation Planning Estimated Public Sessions of Design Submission Start on Site Consultation Autumn 2018 Autumn 2018 Summer 2019 Summer 2018 Design Development Public Consultation July 2018 Portslade Industrial Site 02 Site location, context and development history Historic maps Local context • Sustainable location Vale Park • Well connected Church of St. -
Community Engagement Framework?
Contents Introduction What is the Community Engagement Framework? What are the aims of the Community Engagement Framework? What is community engagement? Our commitment to community engagement Our standards for community engagement Our actions for improving community engagement How will the Community Engagement Framework be implemented & monitored? Contacts and Acknowledgements Information about the development of the Community Engagement Framework, and copies of the Framework and the accompanying consultation report are available on the 2020 Community Partnership website www.2020community.org/cef Introduction The Community Engagement Framework has been developed to be both a policy document and a practical resource. As a policy document it sets out the 2020 Community Partnership’s commitment to and understanding of community engagement in Brighton and Hove. As a practical resource it provides a clear definition of community engagement and importantly sets specific standards for community engagement that all Partners must adhere to. It identifies the first wave of priority actions that must be taken to improve community engagement in the city. As a policy document and a practical tool the Community Engagement Framework will help the 2020 Community Partnership achieve its vision for Brighton and Hove….. ‘of a dynamic city that improves and protects the environment, meets social needs and promotes sustainable economic success in an inclusive, just and harmonious way’ We are not starting from scratch. We recognise that good community engagement activity has and is happening in the city. However, this is the first time that as a group of public, private and community and voluntary organisations we have produced a common approach to community engagement. -
Of Sheep & Fish: an Historical Archaeology Project Proposal on the South Downs Between Brighton and Lewes, 1830--1942
Of Sheep & Fish A History of the South Downs between Lewes and Brighton An Historical-Archaeology Project Proposal by David Cuthbertson 4th June 2019 Photograph of Newmarket Farm c.1925. From a collection by Capt. Bertie Hubbard MacLaren, in Brighton Pavilion and Museums, HA930078. Title: Of Sheep & Fish: A History of the South Downs between Lewes and Brighton: An Historical Archaeology Project Proposal Authors: David Cuthbertson Derivation: Meetings of Peggy and David Cuthbertson with Desmond (Bob), Lucy and Sylvia Phipps at the Woodingdean Then and Now Event; the 2013 Newmarket Farm Dig project and correspondence with Mark Barratt, OASIS. Origination Date: 2010 Revisers: David Cuthbertson Date of last revision: 4th June 2019 Version: 0.51 Status: Draft Summary of Changes: Content planning, writing, layout & proof reading Circulation: Preliminary consultation with the East Sussex County Archaeologist and Sussex Archaeological Society Research Officer Then, East Sussex Historic Environment Record, OASIS; Finalised project document also to Brighton and Hove Archaeology Society, Brighton and Hove Royal Pavilion and Museums, East Sussex Record Office, Hodson family, Kingston Heritage Group, Natural England, Peter Mercer (Woodingdean historian), Phipps family, Society for Post-Medieval Archaeology, South Downs National Park Authority, Sussex Archaeological Society. Required Action: Feedback Approval: Provisional File Name/Location: OSF-0_51.pdf 1 Contents 1 Executive Summary3 2 Project Name4 3 Summary Description4 4 Background5 5 Research -
FOR CULTURAL RECOVERY Introduction
THE FOR CULTURAL RECOVERY Introduction In the middle of the storm, with livelihoods threatened and organisations at risk of collapse, Brighton & Hove’s cultural and creative sector came together. Over 100 creative workers: award-winning artists and those just starting out, leaders and frontline staff of organisations large and small, those freelance and those salaried, participated in 17 conversations over two weeks in September 2020. With generosity, solidarity and common purpose, they focussed on how one of the most vital sectors to Brighton & Hove’s economy and reputation might recover from the crisis and find more sustainable and inclusive ways to grow in the future. This is their plan... 2 | The ABCD for Cultural Recovery Context Creative/cultural industries generated More than At over Brighton’s performing arts sector Home to 13 £1.5bn 16,000 6,100 £329m of Arts Council England’s (ACE) in annual turnover employees in creative businesses companies based in Brighton & Hove turnover in 2018/19 National Portfolio Organisations The strength of Brighton & Hove as a creative city is well arts festival, Brighton Fringe) forming part of its regular Most of the city’s theatres, venues, and museums remain known. In 2019 a study from the University of Sussex1 events calendar. The city’s creative reputation encourages either closed or have re-opened with a much-reduced revealed that the creative and cultural industries in Greater employers and entrepreneurs to set up their businesses capacity. Events, festivals and exhibitions have been Brighton generated more than £1.5 billion in annual locally, and creatives at all stages of their careers are drawn cancelled and the resumption of large-scale gatherings is turnover.