Title of Your Paper
Total Page:16
File Type:pdf, Size:1020Kb
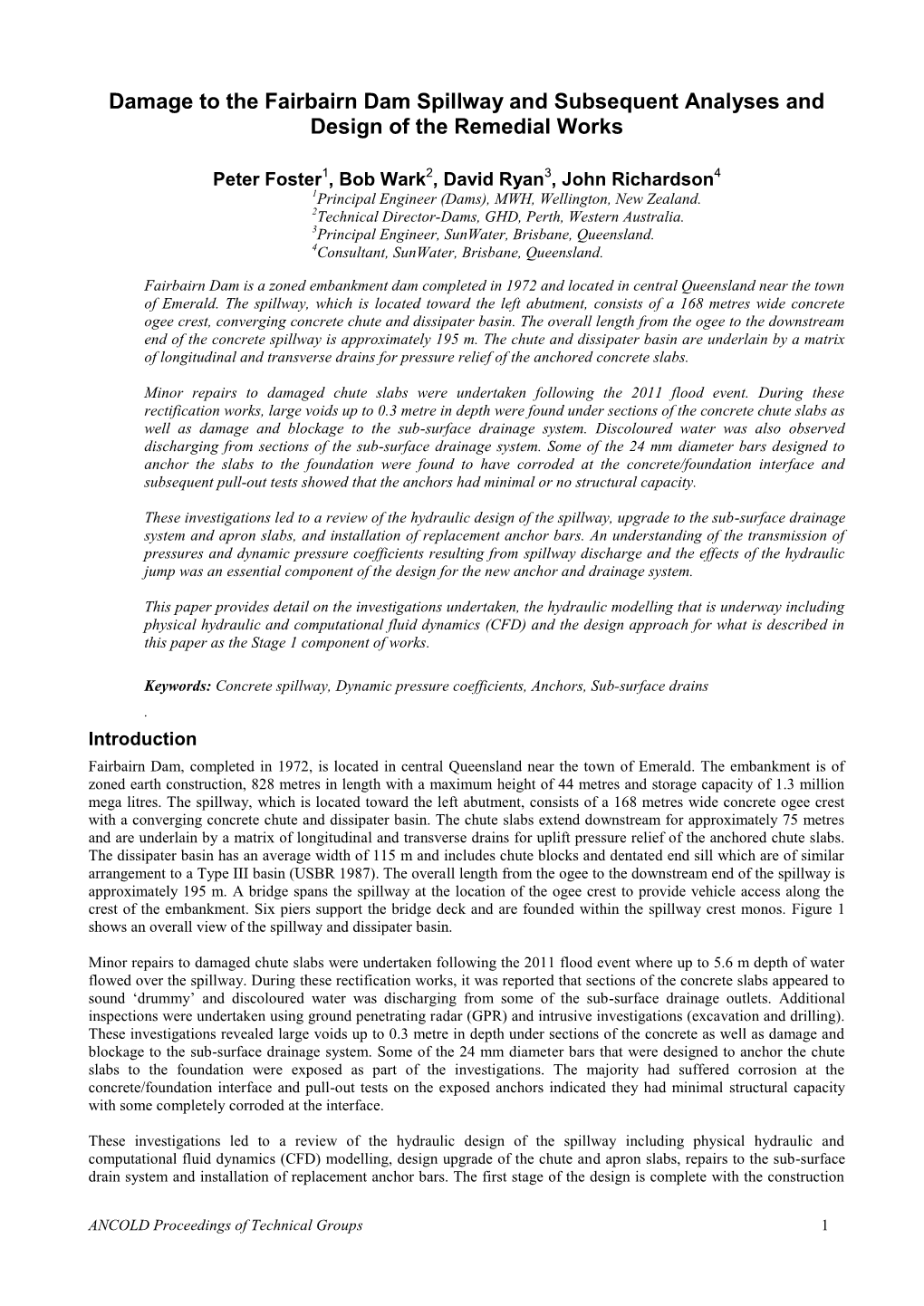
Load more
Recommended publications
-
Strategic Framework December 2019 CS9570 12/19
Department of Natural Resources, Mines and Energy Queensland bulk water opportunities statement Part A – Strategic framework December 2019 CS9570 12/19 Front cover image: Chinaman Creek Dam Back cover image: Copperlode Falls Dam © State of Queensland, 2019 The Queensland Government supports and encourages the dissemination and exchange of its information. The copyright in this publication is licensed under a Creative Commons Attribution 4.0 International (CC BY 4.0) licence. Under this licence you are free, without having to seek our permission, to use this publication in accordance with the licence terms. You must keep intact the copyright notice and attribute the State of Queensland as the source of the publication. For more information on this licence, visit https://creativecommons.org/licenses/by/4.0/. The information contained herein is subject to change without notice. The Queensland Government shall not be liable for technical or other errors or omissions contained herein. The reader/user accepts all risks and responsibility for losses, damages, costs and other consequences resulting directly or indirectly from using this information. Hinze Dam Queensland bulk water opportunities statement Contents Figures, insets and tables .....................................................................iv 1. Introduction .............................................................................1 1.1 Purpose 1 1.2 Context 1 1.3 Current scope 2 1.4 Objectives and principles 3 1.5 Objectives 3 1.6 Principles guiding Queensland Government investment 5 1.7 Summary of initiatives 9 2. Background and current considerations ....................................................11 2.1 History of bulk water in Queensland 11 2.2 Current policy environment 12 2.3 Planning complexity 13 2.4 Drivers of bulk water use 13 3. -
Apportionment of Dam Safety Upgrade Costs
Consultation paper Rural irrigation price review 2020–24: apportionment of dam safety upgrade costs October 2018 © Queensland Competition Authority 2018 The Queensland Competition Authority supports and encourages the dissemination and exchange of information. However, copyright protects this document. The Queensland Competition Authority has no objection to this material being reproduced, made available online or electronically but only if it is recognised as the owner of the copyright2 and this material remains unaltered. Queensland Competition Authority Contents SUBMISSIONS Closing date for submissions: 22 February 2019 Public involvement is an important element of the decision-making processes of the Queensland Competition Authority (QCA). Therefore submissions are invited from interested parties concerning it developing and applying an appropriate approach for apportioning dam safety upgrade capital expenditure as part of the review of irrigation prices for 2020–24. The QCA will take account of all submissions received within the stated timeframes. Submissions, comments or inquiries regarding this paper should be directed to: Queensland Competition Authority GPO Box 2257 Brisbane Q 4001 Tel (07) 3222 0555 Fax (07) 3222 0599 www.qca.org.au/submissions Confidentiality In the interests of transparency and to promote informed discussion and consultation, the QCA intends to make all submissions publicly available. However, if a person making a submission believes that information in the submission is confidential, that person should claim confidentiality in respect of the document (or the relevant part of the document) at the time the submission is given to the QCA and state the basis for the confidentiality claim. The assessment of confidentiality claims will be made by the QCA in accordance with the Queensland Competition Authority Act 1997, including an assessment of whether disclosure of the information would damage the person’s commercial activities and considerations of the public interest. -
KEY POINTS • on the 1 October 2010, Wivenhoe Dam Reached 100 Per Cent for the First Time Since 2001
Department of Environment and Resource Management - Parliamentary Briefing Note To Minister Robertson Prepared for Parliamentary sittings 5 -7 October 2010 WIVENHOE DAM SPILLING - the likelihood of Wivenhoe Dam spilling and safety KEY POINTS • On the 1 October 2010, Wivenhoe Dam reached 100 per cent for the first time since 2001. c • After the weekend's weather, the dam reached 101 per cent on Monday. • On Monday 4 October, Seqwater commenced controlled increased releases from Wivenhoe Dam through the hydro- electric plant in the dam wall. • Even with substantial rain, Wivenhoe Dam's flood capacity is equal to 3 times Sydney harbour - or - 1.45 million megalitres. • Releases from Somerset Dam into Wivenhoe Dam via the cone valves ceased over the weekend. • Seqwater has a Dam Safety Management Program and a Flood Control Centre. The program ensures that each of its dams is operated and maintained in a manner that is both safe and minimises the risks associated with a dam failure and flood events, including working with local councils and emergency services. Contact: Dan Spiller Approved: Mike Lyons, Director, SEQ Water Grid Comms Telephone: Approved: [Insert title of ADG or DOG] Date: 4 October 2010 Approved: Director-General CTS No. 17669/10 1 RESPONSE • On the 1 October 2010 Wivenhoe Dam reached 100 per cent for the first time since 2001. • After the weekend's weather, the dam reached 101 per cent on Monday 4 October 2010. • The trigger level for full gate releases for Wivenhoe Dam is 102.5 per cent. • Also on Monday 4 October, Seqwater commenced controlled C increased release from Wivenhoe Dam through the hydro- electric plant in the dam wall. -
CASE STUDIES Emerald
Attachment 1 CASE STUDIES CASE STUDY NO 1: THE BENEFITS OF WATER INFRASTRUCTURE DEVELOPMENT IN THE EMERALD AREA OF CENTRAL QUEENSLAND Emerald - pre Fairbairn Dam The Emerald District, when first settled in the 1860s, was predominantly a sheep and cattle area. This remained the case into the 1940s, although some small pockets of land were under irrigation. At that time, the population was less than 1,500 people. During the late 1940s and through the 1950s investigations into the feasibility of a dam on the Nogoa River upstream of Emerald were in progress. By 1966, the population of the town of Emerald itself had only grown to be a little more than 2,000 people. At this time, Central Queensland had only 9,000 hectares under irrigation compared with in excess of 120,000 hectares for the whole State. In addition, the value of production in Central Queensland was 12% of that for the State. For the nine year period from 1952/53 to 1961/62, the growth in the Gross National Product was only 25% in this region. This compared unfavourably with the 37% growth exhibited in South Queensland and the 70% growth for North Queensland. The Proposed Scheme A report on the proposed water infrastructure and irrigation scheme for the Emerald Area was presented to Parliament in early 1968. The scheme, as proposed then included: • the construction of Maraboon Dam (now Fairbairn Dam) to provide a supply of 147,600 megalitres/annum (120,000 acre feet/annum). This equated to a supply of about 95,940 megalitres/annum (65,000 acre feet/annum) delivered to the farms; • the construction of a channel supply system on both the right and left banks of the Nogoa River; and, • development of up to 130 farms with an area of not less than 182 hectares (450 acres) and an annual supply of 738 megalitres/annum (600 acre feet/annum). -
An Economic Assessment of the Value of Recreational Angling at Queensland Dams Involved in the Stocked Impoundment Permit Scheme
An economic assessment of the value of recreational angling at Queensland dams involved in the Stocked Impoundment Permit Scheme Daniel Gregg and John Rolfe Value of recreational angling in the Queensland SIP scheme Publication Date: 2013 Produced by: Environmental Economics Programme Centre for Environmental Management Location: CQUniversity Australia Bruce Highway North Rockhampton 4702 Contact Details: Professor John Rolfe +61 7 49232 2132 [email protected] www.cem.cqu.edu.au 1 Value of recreational angling in the Queensland SIP scheme Executive Summary Recreational fishing at Stocked Impoundment Permit (SIP) dams in Queensland generates economic impacts on regional economies and provides direct recreation benefits to users. As these benefits are not directly traded in markets, specialist non-market valuation techniques such as the Travel Cost Method are required to estimate values. Data for this study has been collected in two ways in 2012 and early 2013. First, an onsite survey has been conducted at six dams in Queensland, with 804 anglers interviewed in total on their trip and fishing experiences. Second, an online survey has been offered to all anglers purchasing a SIP licence, with 219 responses being collected. The data identifies that there are substantial visit rates across a number of dams in Queensland. For the 31 dams where data was available for this study, recreational anglers purchasing SIP licences have spent an estimated 272,305 days fishing at the dams, spending an average 2.43 days per trip on 2.15 trips per year to spend 4.36 days fishing per angler group. Within those dams there is substantial variation in total fishing effort, with Somerset, Tinaroo, Wivenhoe and North Pine Dam generating more than 20,000 visits per annum. -
To Whom It May Concern
To whom it may concern, I am a resident of Emerald in Central Queensland, who experienced the flooding in January, 2011 of our recently built 3 month old house. The house was built with the floor height approximately 0.5 meter above the flood levels that occurred in 2008 which was referred to as a ‘1 in100 year flood’. The resultant height of the January flood (all time record) meant that our house had approx. 100mm throughout the house. This amount of water might not seem a significant amount; however with modern houses that have gyprock walls and compressed fibre materials used in kitchens, a small amount of water can cause large degrees of damage. The final cost to our insurance company will be approx. $250,000 to repair our house, replace contents damaged and provide alternative accommodation for us while the house is being repaired as well as storage of our procession during this time. In the township of Emerald I know there are people I’ve personally met and most likely many more residents who experience similar levels of inundation through there houses that we did with varying amounts of damage and cost. We were lucky that firstly an insurance policy was in place and secondly the policy provided had adequate cover. So the cost to repair our house could be considered the ‘true cost’ to repair a house such as ours without us carrying over any flood effects which we could not afford to repair. If in Emerald there was conservatively 30 homes which experienced 100mm of water through their homes and incurred 50% of the cost of our house in repairs ($125,000) as we did, this equates to a considerable expense ($3,750,000). -
State of Queensland Agriculture Report June 2014
Case study Improved management practices The Queensland Government is committed to building • pest management a strong and sustainable agricultural industry; – Targeted chemical application which has been demonstrated through its ongoing (injecting rather than spraying) commitment to the Reef Water Quality Protection Plan – Reduced chemical use and other land management initiatives. Agricultural practices may impact the environment and natural • soil and water management resources that the industry depends on. However, – Reduced tillage improving agricultural practices may result in a two- fold benefit of improved environmental outcomes and – Longer crop cycles economic benefit over the long term. – Minimised traffic in wet season – Soil moisture monitoring Modelling of a typical cane farm near Cairns showed – Interrow vegetation that income increased by improving practices such as reducing tillage and nitrogen application and legume – Composting. fallow. Although analysis indicated a small reduction Capital outlay was needed for purchasing three in crop yield, financial returns were enhanced through harvesters and a slasher and to make changes to reduced tillage operations, increased efficiencies the irrigation and fertigation system. The farmer and inputs over a full crop cycle. Overall, operating considered it a worthwhile investment as it led to a with these improved practices provided important 20 per cent reduction in irrigation-related costs and economic benefits to a farmer at the plot level and improved soil and plant health. resulted in positive effects on profitability. Water monitoring equipment and a soil analysis was A 95 hectare banana farm that adopted improved also purchased, which resulted in a considerable practices after Severe Tropical Cyclone Larry in reduction in chemical (fertiliser and pesticide) costs. -
Stygofauna in Australian Groundwater Systems: Extent of Knowledge
From: Andrew Helps Sent: Friday, 14 May 2021 9:27 AM To: Amy Selvaraj (DELWP) Subject: Stygofauna Attachments: StygofaunaEP158350.pdf EXTERNAL SENDER: Links and attachments may be unsafe. Good morning Amy, Have any of the KALBAR consultants mentioned the Stygofauna in the Lindenow Groundwater ecosystem? As you would be aware Stygofauna are protected by the EPBC Act and the RAMSAR Convention and a competent environmental ecologist would be producing a paper Vis a Vis the impact of the Lindenow mining operations and the destruction of the Stygofauna habitat at Lindenow. There is an urgent need for KALBAR to retain a competent ecologist to write a report on the impact of flocculants on Stygofauna in the Lindenow sub surface aquifer. I would suggest that KALBAR use the team at Macquarie University to do this. Stygofauna have been the subject of a recent report (2015) funded by ACARP. Kindest Regards Andrew Helps 安德鲁 郝普斯 常务董事 Mobile UNEP Global Mercury Partnership Waste Management Partnership - designated expert Mercury added products and alternatives – designated expert Mercury Fate and Transport Group IMPORTANT PLEASE READ: This email may contain confidential and or proprietary information and may be protected by the rules of legal privilege. If you receive this email by mistake, or are not the intended recipient you must not use it or the information in any way. If this is the case, could you please inform the sender by return email or by telephoning and delete any such email from your computer. This email and any attachments, has been scanned for computer viruses but you should also perform your own scan. -
Emerald Regional Water Supply Security Assessment CS6824 05/17
Department of Energy and Water Supply Emerald regional water supply security assessment CS6824 05/17 This publication has been compiled by the Department of Energy and Water Supply. © State of Queensland, 2017. The Queensland Government supports and encourages the dissemination and exchange of its information. The copyright in this publication is licensed under a Creative Commons Attribution 4.0 International (CC BY 4.0) licence. Under this licence you are free, without having to seek our permission, to use this publication in accordance with the licence terms. You must keep intact the copyright notice and attribute the State of Queensland as the source of the publication. Note: Some content in this publication may have different licence terms as indicated. For more information on this licence, visit https://creativecommons.org/licenses/by/4.0/. The information contained herein is subject to change without notice. The Queensland Government shall not be liable for technical or other errors or omissions contained herein. The reader/user accepts all risks and responsibility for losses, damages, costs and other consequences resulting directly or indirectly from using this information. Introduction Emerald is a growing community of about 16 000 in the heart of Central Queensland—a region that continues to play a significant role in supporting Queensland’s economy. Extensive agricultural production (including cotton and citrus) dominates the area south and west of Emerald, and some of the state’s most productive coalmines lie to the north and east in the Bowen Basin. Emerald’s population is projected to grow from around 16 000 to about 25 000 by 2036 (Queensland Government Statistician’s Office). -
Queensland Bulk Water Opportunities Statement: Part B
Department of Regional Development, Manufacturing and Water Queensland bulk water opportunities statement Part B: 2019–20 Program update CS10120 2/21 Front cover image: Burdekin Falls Dam (image courtesy Sunwater) Back cover image: The Blackall Woolscour (image courtesy Tourism and Events Queensland) All images courtesy of Department of Regional Development, Manufacturing and Water, Tourism and Events Queensland, Sunwater, Seqwater and CSIRO This publication has been compiled by the Department of Regional Development, Manufacturing and Water © State of Queensland, 2021. The Queensland Government supports and encourages the dissemination and exchange of its information. The copyright in this publication is licensed under a Creative Commons Attribution 4.0 Australia (CC BY 4.0) licence. Under this licence you are free, without having to seek our permission, to use this publication in accordance with the licence terms. You must keep intact the copyright notice and attribute the State of Queensland as the source of the publication. Note: Some content in this publication may have different licence terms as indicated. For more information on this licence, visit http://creativecommons.org/licenses/by/4.0 The information contained herein is subject to change without notice. The Queensland Government shall not be liable for technical or other errors or omissions contained herein. The reader/user accepts all risks and responsibilities for losses, damages, costs and other consequences resulting directly or indirectly from using this information. The Queensland Government is committed to providing accessible services to Queenslanders from all culturally and linguistically diverse backgrounds. If you have difficulty in understanding this document, you can contact us within Australia on 13QGOV (13 74 68) and we will arrange an interpreter to effectively communicate the report to you. -
CASE STUDIES Emerald
Attachment 1 CASE STUDIES CASE STUDY NO 1: THE BENEFITS OF WATER INFRASTRUCTURE DEVELOPMENT IN THE EMERALD AREA OF CENTRAL QUEENSLAND Emerald - pre Fairbairn Dam The Emerald District, when first settled in the 1860s, was predominantly a sheep and cattle area. This remained the case into the 1940s, although some small pockets of land were under irrigation. At that time, the population was less than 1,500 people. During the late 1940s and through the 1950s investigations into the feasibility of a dam on the Nogoa River upstream of Emerald were in progress. By 1966, the population of the town of Emerald itself had only grown to be a little more than 2,000 people. At this time, Central Queensland had only 9,000 hectares under irrigation compared with in excess of 120,000 hectares for the whole State. In addition, the value of production in Central Queensland was 12% of that for the State. For the nine year period from 1952/53 to 1961/62, the growth in the Gross National Product was only 25% in this region. This compared unfavourably with the 37% growth exhibited in South Queensland and the 70% growth for North Queensland. The Proposed Scheme A report on the proposed water infrastructure and irrigation scheme for the Emerald Area was presented to Parliament in early 1968. The scheme, as proposed then included: • the construction of Maraboon Dam (now Fairbairn Dam) to provide a supply of 147,600 megalitres/annum (120,000 acre feet/annum). This equated to a supply of about 95,940 megalitres/annum (65,000 acre feet/annum) delivered to the farms; • the construction of a channel supply system on both the right and left banks of the Nogoa River; and, • development of up to 130 farms with an area of not less than 182 hectares (450 acres) and an annual supply of 738 megalitres/annum (600 acre feet/annum). -
Legend THIS MAP IS INDICATIVE ONLY
Bamaga Funnel traps with a rigid opening size of between 5 cm and 10 cm can also be used in these stocked impoundments: • Atkinsons Dam • Koombooloomba Dam • Baroon Pocket Dam • Lake Awonga • Beehive Dam • Lake Gregory Weipa • Bill Gunn Dam • Lake MacDonald Lockhart River (Lake Dyer) • Lenthalls Dam • Bjelke-Petersen Dam (Lake Lenthall) • Boondooma Dam • Leslie Dam • Borumba Dam • Maroon Dam • Burdekin Dam • Middle Creek Dam Coen Port Stewart Ebagoola (Lake Dalrymple) • Moogerah Dam Yarraden • Callide Dam • Mount Morgan Big Dam • Cania Dam • North Pine Dam • Connolly Dam • Peter Faust Dam • Cooby Dam • Ross River Dam Laura Cooktown • Coolmunda Dam • Sideling Creek Dam Lakeland • Cressbrook Dam (Lake Kurwongbah) Maramie • Eungella Dam • Somerset Dam Daintree • Ewen Maddock Dam • Storm King Dam Julatten • Fairbairn Dam • Teemburra Dam Cairns • Fred Haigh Dam • Theresa Creek Dam Mutchilba Atherton (Lake Monduran) • Tinaroo Dam Ravenshoe • Glenlyon Dam • Wivenhoe Dam • Gordonbrook Dam • Wuruma Dam Mount Garnet • Hinze Dam • Wyaralong Dam Mount Surprise • Kinchant Dam Greenvale Townsville Charters Towers Mount Isa Torrens Creek Hughenden Mackay Llanarth Winton Clermont Longreach Barcaldine Emerald Rockhampton Jericho Alpha Blackwater Gladstone Blackall Rolleston Biloela Taroom Gayndah Augathella Injune Wandoan Mitchell Roma Kingaroy Chinchilla Quinalow Crows Nest Brisbane Toowoomba Gatton Millmerran Allora Aratula Warwick Goondiwindi Stanthorpe Legend THIS MAP IS INDICATIVE ONLY. Great Dividing Range These datasets are licensed under the Creative