Standards for Modular Electronics
Total Page:16
File Type:pdf, Size:1020Kb
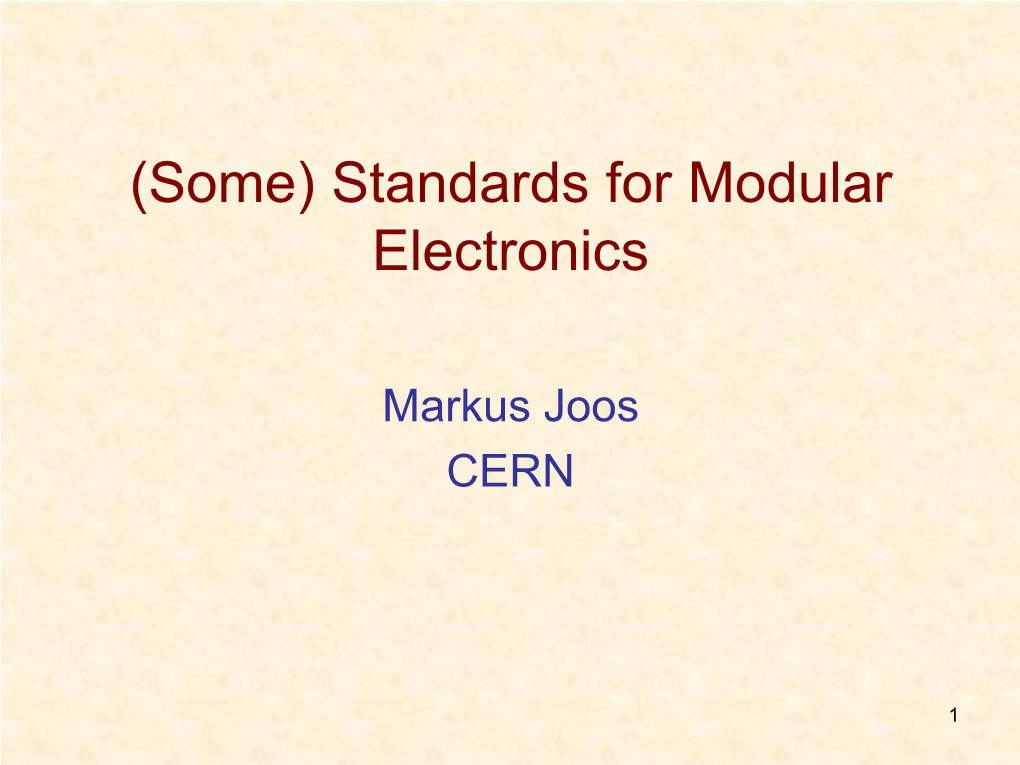
Load more
Recommended publications
-
Allgemeines Abkürzungsverzeichnis
Allgemeines Abkürzungsverzeichnis L. -
Compactpci Serial ...The Smart Solution
CompactPCI® Serial ... ... the Smart Solution © EKF •www. ekf.com CompactPCI® Serial Systems Designed for performance • 40 x PCI® Express • 8 x Gigabit Ethernet • 8 x SATA • 8 x USB3 CompactPCI® Serial - the Smart Solution www.ekf.com/s/serial.html © EKF •www. ekf.com CompactPCI® Serial Systems CPCI Serial backplanes for optimum throughput CompactPCI® Serial - the Smart Solution Sample Backplanes CompactPCI® Serial The CompactPCI® Serial system slot is located either most left or most right © EKF •www. ekf.com CompactPCI® Serial Systems Reverse order backplanes (system slot right aligned) for CPU cards with 4HP to 12HP front panel CompactPCI® Serial - the Smart Solution www.ekf.com/s/serial.html © EKF •www. ekf.com CompactPCI® Serial Systems CPCI® Serial BLUBRICK series - ultra rugged CompactPCI® Serial - the Smart Solution www.ekf.com/s/srs/srs1201/srs1201.html SRS-1201-BLUBRICK CompactPCI® Serial © EKF • www.ekf.com CompactPCI® Serial Systems CPCI Serial BluBoxx series - small and economic www.ekf.com/s/srs/srs3201/srs3201.html CompactPCI® Serial - the Smart Solution SRS-3201-BLUBOXX CompactPCI® Serial © EKF •www. ekf.com CompactPCI® Serial Systems CPCI Serial rugged system racks www.ekf.com/s/srs/srs4401/srs4401.html CompactPCI® Serial - the Smart Solution SRS-4401-SERIAL CompactPCI® Serial © EKF •www. ekf.com CompactPCI® Serial Systems CPCI® Serial racks 84HP CompactPCI® Serial - the Smart Solution www.ekf.com/s/srs/srs8401/srs8401.html SRS-8401-SERIAL CompactPCI® Serial © EKF •www. ekf.com Embedded Blue® CPCI® Serial boxed solutions • fixed & custom configuration CompactPCI® Serial - the Smart Solution www.ekf.com/b/bc200/bc200.html BC200 Embedded Blue® © EKF •www. -
From Camac to Wireless Sensor Networks and Time- Triggered Systems and Beyond: Evolution of Computer Interfaces for Data Acquisition and Control
Janusz Zalewski / International Journal of Computing, 15(2) 2016, 92-106 Print ISSN 1727-6209 [email protected] On-line ISSN 2312-5381 www.computingonline.net International Journal of Computing FROM CAMAC TO WIRELESS SENSOR NETWORKS AND TIME- TRIGGERED SYSTEMS AND BEYOND: EVOLUTION OF COMPUTER INTERFACES FOR DATA ACQUISITION AND CONTROL. PART I Janusz Zalewski Dept. of Software Engineering, Florida Gulf Coast University Fort Myers, FL 33965, USA [email protected], http://www.fgcu.edu/zalewski/ Abstract: The objective of this paper is to present a historical overview of design choices for data acquisition and control systems, from the first developments in CAMAC, through the evolution of their designs operating in VMEbus, Firewire and USB, to the latest developments concerning distributed systems using, in particular, wireless protocols and time-triggered architecture. First part of the overview is focused on connectivity aspects, including buses and interconnects, as well as their standardization. More sophisticated designs and a number of challenges are addressed in the second part, among them: bus performance, bus safety and security, and others. Copyright © Research Institute for Intelligent Computer Systems, 2016. All rights reserved. Keywords: Data Acquisition, Computer Control, CAMAC, Computer Buses, VMEbus, Firewire, USB. 1. INTRODUCTION which later became international standards adopted by IEC and IEEE [4]-[7]. The design and development of data acquisition The CAMAC standards played a significant role and control systems has been driven by applications. in developing data acquisition and control The earliest and most prominent of those were instrumentation not only for nuclear research, but applications in scientific experimentation, which also for research in general and for industry as well arose in the early sixties of the previous century, [8]. -
Putting Switched Fabric to Work for Software Radio
PUTTING SWITCHED FABRIC TO WORK FOR SOFTWARE RADIO Rodger H. Hosking (Pentek, Inc., Upper Saddle River, NJ, USA, [email protected]) ABSTRACT In order to take advantage of the wealth of high- volume, low-cost devices for mass-market electronics, and The most difficult problem for designers of high- to reap the same benefits of easier connectivity, even the performance, software radio systems is simply moving data most powerful high-end software radio RISC and DSP within the system because of data throughput limitations. processors from Freescale and Texas Instruments are now Driving this dilemma are processors with higher clock rates sporting gigabit serial interfaces. and wider buses, data converter products with higher sampling rates, more complex digital communication 2. GIGABIT SERIAL STANDARDS standards with increased bandwidths, disk storage devices with faster I/O rates, FPGAs and DSPs offering incredible The descriptive phrase “gigabit serial” covers a truly diverse computational rates, and system connections and network range of implementations and application spaces. Figure 1 links operating at higher speeds. shows most of the popular standards used in embedded Traditional system architectures relying on buses and systems suitable for software radio, along with how each parallel connections between system boards and mezzanines standard is normally deployed in a system. fall far short of delivering the required peak rates, and suffer even worse if they must be shared and arbitrated. New Standard Main Application strategies for solving these problems exploit gigabit serial Gigabit Ethernet Computer Networking links and switched fabric standards to create significantly FibreChannel Data Storage more powerful architectures ideally suited for embedded software radio systems. -
VXS Created in the First Place? VXS and VPX Are Both Based on the Same Multigig RT2 Connector Family
Frequently Asked Questions on 1. Why was VXS created in the first place? VXS and VPX are both based on the same MultiGig RT2 connector family. Mesh versions of VXS can match the slot-to-slot The VITA community needed a way to expand beyond the bandwidth of VPX. The primary advantage of VXS is the backward performance limitations of the solely parallel bus architectures compatibility with millions of existing VMEbus boards with the and incorporate serial fabrics. VXS offers backward compatibility edition of high-speed serial switch fabrics. to the VMEbus while adopting the use of serial signals such as Gigabit Ethernet, PCI Express, Serial RapidIO, and other fabrics. Each architecture has its own advantages that must be carefully considered. Designers should review factors such as A well-established ecosystem exists for VXS products. With more the ecosystem, architecture maturity/stability, pricing, power/ than 80 unique products offered in the market and deployed cooling requirements, I/O availability, bandwidth, and backwards throughout the world, the VXS architecture provides developers compatibility. with a logical extension and performance upgrade to their VME- based applications. 6. What’s the difference between VXS and VPX? 2. What are the general VXS features? VXS offers backwards compatibility for existing VME/VME64x • Backwards compatible to the VME/VME64x architecture. line cards for payload slots. VPX can offer compatibility through Enabling re-use of existing hardware and software. the use of hybrid backplanes with VME/VME64x slots. As VXS is • Uses high-speed Multi-Gig RT2 for P0 connector. based on a 0.8” pitch versus a typical 1.0” pitch for VPX, VXS offers • Switch card slot(s) in Star or Dual Star configurations. -
2013 State of the VITA Technology Industry
2013 State of the VITA Technology Industry September 2013 P.O. Box 19658 Fountain Hills, AZ 85269 480.837.7486 [email protected] www.vita.com This page intentially left blank for double sided printing. State of the VITA Technology Industry September 2013 by: Ray Alderman, Executive Director, VITA This report provides the reader with updates on the state of the VITA Technology industry in particular and of the board industry in general, from the perspective of Ray Alderman, the executive director of VITA. VITA is the trade association dedicated to fostering American National Standards Institute (ANSI) accredited, open system architectures in critical embedded system applications. The complete series of reports can be found at Market Reports. (www.vita.com) Introduction This issue of the “State of the VITA Technology Industry” recaps our current economic Contents conditions We will also take a close look at unmanned vehicles of all types Optical backplanes have been on the horizon for many years, new innovation keeps moving us Introduction . 1 so ever slowly forward, but we are quickly running out of runway There have been a few deals made in the mergers and acquisition department, and to wrap it up, we will close Business Conditions . 1 with “Alderman’s Business Rules ” Markets. 3 MIL/Aero 3 Business Conditions Telecom 7 Optical Developments. 8 The final numbers for Q1 2013 U S GDP growth1 came in at a disappointing 1 8% after two earlier estimates of 2 4% The final Q1 GDP was revised to 1 1% by the Bureau of Mergers and Acquisitions 10 Economic Analysis (the Bureau of Economic Analysis issues a preliminary GDP number, and revises it three times until the next quarter GDP estimate is announced) While this Changing Business Models 10 is not exciting, it beats the situation we have seen in China2 and Europe3 in Q1 Market Estimates . -
3U Compactpci Serial Communications Products
CommunicationsCommunications ProductsProducts 3U CompactPCI Serial Communications Products Model Name cPCI-3538 cPCI-3534 cPCI-3544 Plug & Play √ √ √ Serial Port Number 8 4 4 Max. Async Speed 115.2Kbps 115.2Kbps 115.2Kbps Isolation - On-board On-board RS-232C # of Ports 8 3 - RS-485 # of Ports - 1 Isolated 4 Isolated RS-422 # of Ports - 1 Isolated 4 Isolated Rear I/O Version √ √ √ Cable C825M / C809M C425M / C409M C425M / C409M Page No. 7-4 7-4 7-5 PCI-based Serial Communications Products 7 Model Name C588 C584 C518 C514 C422 C485 Plug & Play √ √ √ √ √ √ Serial Port Number 8 4 8 4 2 4 Max. Async Speed 115.2Kbps 115.2Kbps 115.2Kbps 115.2Kbps 115.2Kbps 115.2Kbps Isolation External External –– –– On-board On-board RS-232C # of Ports 8 4 7 3 - - RS-485 # of Ports - - 1 Isolated 1 Isolated 2 Isolated 4 Isolated RS-422 # of Ports - - 1 Isolated 1 Isolated 2 Isolated 4 Isolated Cable C825M / C809M C425M / C409M C825M / C809M C425M / C409M –– C425M / C409M Page No. 7-3 7-3 7-3 7-3 7-3 7-3 7-1 PCI-7841/cPCI-7841PCI-7841 Dual-port Isolated CAN Interface Cards Introduction 1 The PCI-7841/cPCI-7841 is a Controller Area Network (CAN) interface Software card. It supports a dual-port CAN's interface that can run independently or bridged at the same time. The built-in CAN controller of this card is Philips SJA1000, which provides bus arbitration and error detection with auto correction and re-transmission function. 2 GEME Series Controller Area Network The CAN (Controller Area Network), a serial bus system originally 3 developed by Bosch for use in automobiles, is increasingly being used DPAC for industry automation. -
ADLINK Technology, Inc
Enduring Performance ADLINK’s extensive rugged portfolio delivers power, flexibility, affordability, endurance and longevity CompactPCI | Enduring Performance In the most severe environments, CompactPCI shines brightest. Standard hardware is typically designed for home or office use, which means climate-controlled spaces and narrow operating temperature ranges. Outside of these parameters, failure can quickly go from possibility to reality. From the hottest places on Earth to the bleak expanse of outer space, CompactPCI endures where other solutions falter. Benefitting from decades of research and development, CompactPCI has emerged as an outstanding platform across a range of industries. The CompactPCI architecture perfectly suits mission-critical situations that demand resilience and high performance. ADLINK is dedicated to offering a robust portfolio of cost-effective, cutting-edge CompactPCI solutions for today’s applications and years into the future. P 1 At ADLINK, we strive to be at the forefront of innovation. Our commitment to building best-of-breed products for many demanding verticals makes us an industry leader. When we support a particular technology, we are fully committed investing resources and joining relevant industry consortia. As such, ADLINK is an executive member of the PCI Industrial Core™, Xeon®, and Atom® processors. ADLINK also owns and Computer Manufacturers Group (PICMG) consortium, which has full control of its manufacturing facilities, based in our initially introduced CompactPCI in 1999. By participating Asia headquarters. Incorporating top-tier hardware into our in PICMG, we are able to contribute expertise that guides own manufacturing capabilities lets ADLINK create products future CompactPCI development and helps us position the with exceptional life spans. -
HARTMANN ELEKTRONIK Innovationen Aus Erfahrung Innovations Bases on Experience
System platforms 03 Komfortlösungen CPCI, VME, VPX Comfort solutions CPCI, VME, VPX Inhalt Contents Einführung 4 Introduction 4 Systemplattformen System platforms PXI 4 HE, 63 TE 6 PXI 4 U, 63 HP 6 CompactPCI ® CompactPCI ® • CPCI 3 HE, 30 TE 7 • CPCI 3 U, 30 HP 7 • CPCI 3,5 HE, 42 TE 8 • CPCI 3,5 U, 42 HP 8 • CPCI 3 HE, 84 TE 9 • CPCI 3 U, 84 HP 9 • CPCI 6 HE, 84 TE 10 • CPCI 6 U, 84 HP 10 • CPCI 4 HE, 63 TE 11 • CPCI 4 U, 63 HP 11 • CPCI 1 HE, 84 TE 12 • CPCI 1 U, 84 HP 12 • CPCI 2 HE, 84 TE 14 • CPCI 2 U, 84 HP 14 • CPCI 4 HE, 84 TE 16 • CPCI 4 U, 84 HP 16 CompactPCI ® 2.16 CompactPCI ® 2.16 • CPCI 2.16 4 HE, 84 TE 18 • CPCI 2.16 4 U, 84 HP 18 • CPCI 2.16 10 HE, 84 TE 19 • CPCI 2.16 10 U, 84 HP 19 VME64x VME64x • VME64x 1 HE, 84 TE 20 • VME64x 1 U, 84 HP 20 • VME64x 2 HE, 84 TE 22 • VME64x 2 U, 84 HP 22 • VME64x 4 HE, 84 TE 24 • VME64x 4 U, 84 HP 24 • VME64x 7 HE, 84 TE 26 • VME64x 7 U, 84 HP 26 VME 7 HE, 84 TE 28 VME 7 U, 84 HP 28 VXS 11 HE, 84 TE 29 VXS 11 U, 84 HP 29 VPX 4 HE, 84 TE 30 VPX 4 U, 84 HP 30 Baugruppenträger Subracks Open Frame 32 Open Frame 32 CompactPCI ® CompactPCI ® • CPCI 3 HE, 30 TE 34 • CPCI 3 U, 30 HP 34 • CPCI 3 HE, 84 TE 35 • CPCI 3 U, 84 HP 35 • CPCI 6 HE, 84 TE 37 • CPCI 6 U, 84 HP 37 VME64x VME64x • VME64x 3 HE, 84 TE 38 • VME64x 3 U, 84 HP 38 • VME64x 6 HE, 84 TE 39 • VME64x 6 U, 84 HP 39 Baugruppenträgerzubehör Accessories for subracks Zubehör 41 Accessories 41 Shelfmanager 42 Shelf manager 42 Netzteile 50 Power supplies 50 Lüfterschublade 1 HE, 84 TE 52 Fan tray 1 U, 84 HP 52 Kundenspezifi sche Lösungen 53 Customized Solutions 53 Die passenden Bausteine für Ihren Erfolg Exactly the right modules for your success 4 HARTMANN ELEKTRONIK Innovationen aus Erfahrung Innovations bases on experience Hartmann Elektronik ist ein Hartmann Elektronik is a langjähriger Partner der Embedded longstanding partner of the Industrie und verfügt über embedded industry and has a variety eine Vielzahl unterschiedlicher of different backplanes. -
20G022-00 E1 User Manual
20G022-00 E2 – 2014-04-10 User Manual G22 – 3U CompactPCI® Serial Intel® Core™ i7 CPU Board Configuration example G22 - 3U CompactPCI® Serial Intel® Core™ i7 CPU Board G22 - 3U CompactPCI® Serial Intel® Core™ i7 CPU Board The G22 is a versatile 4HP/3U single-board computer supporting a multitude of modern serial interfaces according to the CompactPCI® Serial standard. It is thus perfectly suited for data-intensive applications which require high computing- power. The CPU card is equipped with the Intel® third-generation Core i7 processor running at up to 3.3 GHz maximum turbo frequency and offering the latest multi- core processor architecture from Intel® with full 64-bit support. The processor frequency can be stepped down via the BIOS to lower power consumption and make the board more suitable for high temperatures. The G22 supports the Intel® Active Management technology which makes it possible to access the board via the network even when it is in soft-off or standby state. For system security, a Trusted Platform Module is available on request. The memory configuration of the G22 includes a state-of-the-art fast DDR3 DRAM which is soldered to the board to guarantee optimum shock and vibration resistance. An mSATA disk connected via a SATA channel and a microSD™ card device which is connected via a USB interface offer nearly unlimited space for user applications. The board delivers an excellent graphics performance. Two DisplayPort® interfaces are accessible at the board front. Using an external adapter two HDMI or two DVI ports can also be realized. -
User Guide SC3-LARGO • Compactpci ® Serial CPU Card 5Th Generation Intel® Core™ Processor (Broadwell H)
User Guide SC3-LARGO • CompactPCI ® Serial CPU Card 5th Generation Intel® Core™ Processor (Broadwell H) Document No. 7951 • Edition 20 • 3rd April 2019 User Guide • SC3-LARGO • CompactPCI® Serial CPU Board • Intel® CoreTM 5xxx Processor Contents About this Manual........................................................... 5 Edition History......................................................... 5 Related Documents..................................................... 6 Nomenclature......................................................... 6 Trade Marks .......................................................... 6 Legal Disclaimer - Liability Exclusion ......................................... 6 Standards............................................................ 7 Overview............................................................. 8 Technical Features .......................................................... 10 Feature Summary ..................................................... 10 Power Requirements................................................... 15 Block Diagram........................................................ 16 Top View Component Assembly .......................................... 17 Bottom View Component Assembly........................................ 18 Front Panel Connectors ................................................. 19 Front Panel Switches & Indicators ......................................... 19 On-Board Connectors & Sockets .......................................... 20 Pin Headers......................................................... -
Embedded Modules Industrial Pcs • Systems & Customization
Embedded modules l Industrial PCs • Systems & Customization Our membership PC/104 Consortium is an international organization of The OPC Foundation is dedicated to ensuring interoperabil - PC/104 products manufacturers that maintains the PC/104 ity in automation by creating and maintaining open speci - specifications, disseminates PC/104 technology, and pro - fications that standardize the communication of acquired motes the welfare of its members. process data, alarm and event records, historical data, and Executive Member batch data to multi-vendor enterprise systems and be - tween production. PICMG (PCI Industrial Computer Manufacturers Group) is a consortium of companies who collaboratively develop The EtherCAT Technology Group (ETG) is the forum in open specifications for high performance telecommunica - which key user companies from various industries and tions and industrial computing applications. leading automation suppliers join forces to support, pro - Associate Member mote and advance the EtherCAT technology. EtherCAT Technology Group aims to ensure the compatibility of EtherCAT implementations by defining functional require - Intel ® Embedded and Communications Alliance (Intel ® ments, conformance tests as well as certification proce - ECA) is a community of developers and solution providers dures. committed to the design and implementation of modular systems based on Intel technologies in the area of com - StackPC – New Standard of Embedded Stackable Systems munication and embedded applications. Design. The StackPC Specification defines new approach to stackable systems design and development. The spec - CAN in Automation (CiA) is the international users’ and ification includes all valuable heritage of PC/104 standards manufacturers’ organization that develops and supports along with the new features of StackPC connector. The CAN-based higher-layer protocols.