Synthesis of Disc Brake Squeal Quieting Experience
Total Page:16
File Type:pdf, Size:1020Kb
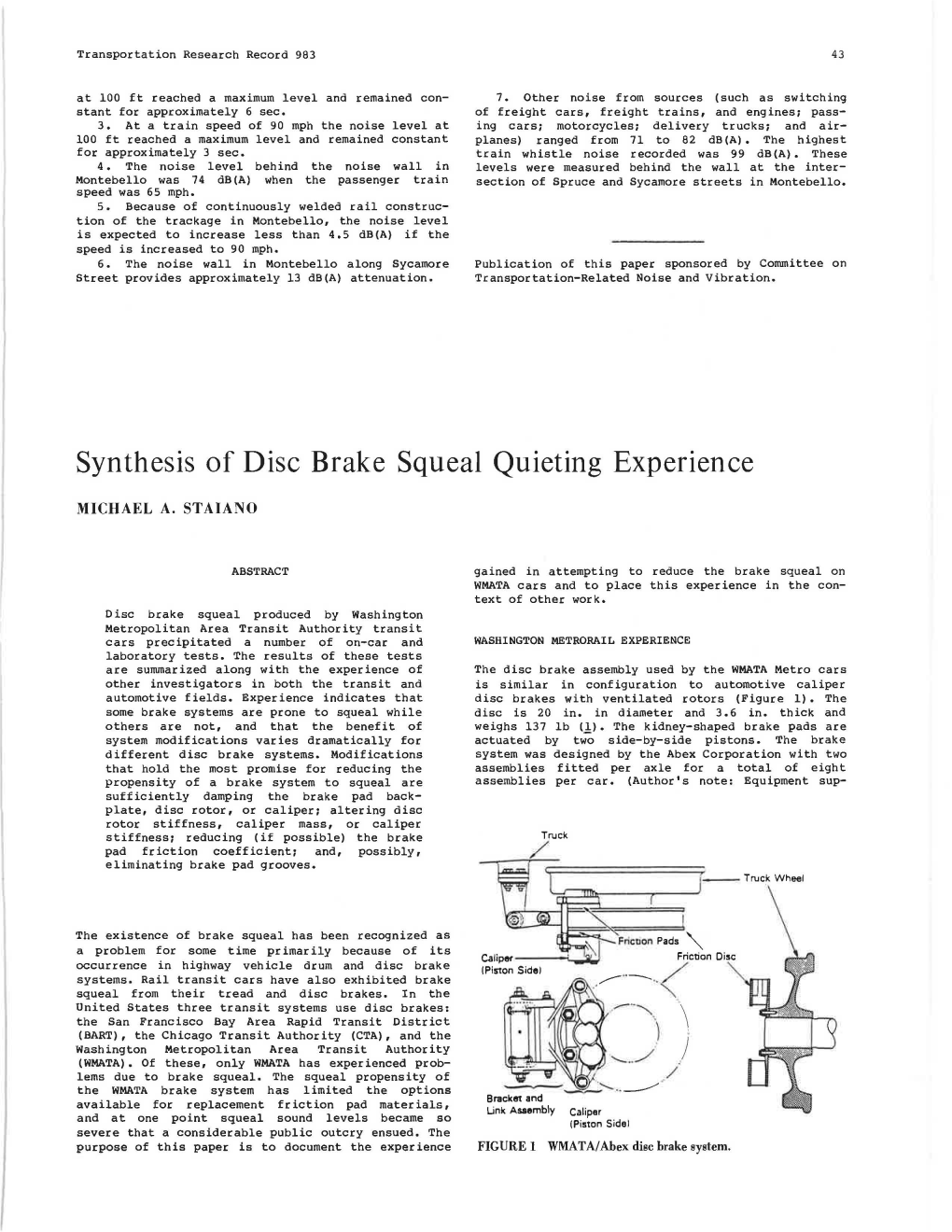
Load more
Recommended publications
-
10B-FY2020-Budget-Adoption-FINALIZED.Pdf
Report by Finance and Capital Committee (B) 03-28-2019 Washington Metropolitan Area Transit Authority Board Action/Information Summary MEAD Number: Resolution: Action Information 202068 Yes No TITLE: Adopt FY2020 Operating Budget and FY2020-2025 CIP PRESENTATION SUMMARY: Staff will review feedback received from the public and equity analysis on the FY2020 Proposed Budget and request approval of the Public Outreach and Input Report, FY2020 Operating Budget and FY2020-2025 Capital Improvement Program (CIP). PURPOSE: The purpose of this item is to seek Board acceptance and approval of the Public Outreach and Input Report and Title VI equity analysis, and the FY2020 Operating Budget and FY2020-2025 CIP. DESCRIPTION: Budget Priorities: Keeping Metro Safe, Reliable and Affordable The budget is built upon the General Manager/CEO's Keeping Metro Safe, Reliable and Affordable (KMSRA) strategic plan. Metro is making major progress to achieve the goals of this plan by ramping up to average capital investment of $1.5 billion annually, establishing a dedicated capital trust fund exclusive to capital investment, and limiting jurisdictional annual capital funding growth to three percent. Metro continues to encourage the U.S. Congress to reauthorize the Passenger Rail Investment and Improvement Act (PRIIA) beyond FY2020, which provides $150 million in annual federal funds matched by $150 million from the District of Columbia, State of Maryland, and Commonwealth of Virginia. In order to establish a sustainable operating model, Metro is limiting jurisdictional operating subsidy growth to three percent and deploying innovative competitive contracting. The items on the KMSRA agenda that remain to be completed include restructuring retirement benefits and creating a Rainy Day Fund. -
Gmf-Icsp-Wsw-2012
Agenda ICSP/GMF Meeting 9 am - 12pm October 9, 2011 Newseum, Knight Conference Center 555 Pennsylvania Avenue, NW, 6th Street Entrance, The Freedom Forum Entrance, Washington, DC 20001 Co Chairs: Mary Saunders NIST, ICSP and Mary McKiel, EPA, GMF ICSP Closed Session – Federal Government Only 9:05-10:15 ICSP Closed Door Meeting – see ICSP meeting agenda for call in information ICSP/GMF Joint Session – Open to All Teleconference Call In: 1-866-469-3239 or 1-650-429-3300 Host access code (Scott): 25558273 Attendee access code: 25515125 10:30 Welcome- Co-Chairs: Mary Saunders NIST, ICSP and Mary McKiel, EPA, GMF 10:35 Remarks – Joe Bhatia, ANSI 10:40 Self introductions – All 10:45 Incorporation by Reference issues before PHMSA – Tim Klein, DOT 10:55 Discussion of Standards Incorporated by Reference Database – Fran Schrotter, ANSI 11:15 Discussion of NAESB ‘Green Button’ smart meter standard success story- Dave Wollman, NIST 11:35 ISO General Assembly Update – Mary McKiel, EPA 11:45 Current legislative activities of potential interest to the standardization community – Scott Cooper, ANSI 11:50-noon Other Business, Next Meeting Adjourn Directions to the Newseum Newseum 555 Pennsylvania Ave, NW 6th Street Entrance Washington, DC 20001 Metro Accessible Archives/Navy Memorial-Penn Quarter Station • • Take the Green or Yellow Line to the Archives/Navy Memorial-Penn Quarter Metro Station. Exit the station, turn left and walk toward Pennsylvania Avenue. Turn left onto Pennsylvania Avenue, walk toward the Capitol and cross Seventh Street. Walk one block to the Newseum, located at the corner of Pennsylvania Avenue and Sixth Street. -
Proposed Judiciary Square Historic District
GOVERNMENT OF THE DISTRICT OF COLUMBIA HISTORIC PRESERVATION OFFICE HISTORIC PRESERVATION REVIEW BOARD APPLICATION FOR HISTORIC LANDMARK OR HISTORIC DISTRICT DESIGNATION New Designation _X_ Amendment of a previous designation __ Please summarize any amendment(s) Property name Judiciary Square Historic District If any part of the interior is being nominated, it must be specifically identified and described in the narrative statements. Address Roughly bounded by Constitution and Pennsylvania Avenues, N.W. and C Street, N.W. to the south, 6th Street to the west, G Street to the north, and 3rd and 4th Streets N.W to the east. See Boundary Description section for details. Square and lot number(s) Various Affected Advisory Neighborhood Commission 2C Date of construction 1791-1968 Date of major alteration(s) Various Architect(s) Pierre Charles L’Enfant, George Hadield, Montgomery C. Meigs, Elliott Woods, Nathan C. Wyeth, Gilbert S. Underwood, Louis Justement Architectural style(s) Various Original use Various Property owner Various Legal address of property owner Various NAME OF APPLICANT(S) DC Preservation League If the applicant is an organization, it must submit evidence that among its purposes is the promotion of historic preservation in the District of Columbia. A copy of its charter, articles of incorporation, or by-laws, setting forth such purpose, will satisfy this requirement. Address/Telephone of applicant(s) 1221 Connecticut Avenue, NW, Washington, DC 20036 Name and title of authorized representative Rebecca Miller, Executive Director Signature of representative _______ _____ Date ____10/25/2018______ Name and telephone of author of application DC Preservation League, 202.783.5144 Office of Planning, 801 North Capitol Street, NE, Suite 3000, Washington, D.C. -
Reagan National
Monday, October 11th Honor Guard Teams / Motors / Support Staff Arrive Tuesday, October 12th Early Arrival Day (Reagan National Airport) for Survivors, 9 AM to 6 PM Colorado Survivor / Peace Officer Reception, 5 PM to 8 PM * * Wednesday, October 13th Official Arrival Day (Reagan National Airport) for Survivors, 9 AM to 6 PM C.O.P.S. 3rd Annual Blue Honor Gala, 6:30 PM Thursday, October 14th C.O.P.S. Blue Family Brunch at Hilton Alexandria Mark Center ***Colorado Peace Officer Group Photo 7th St NW & Indiana Ave NW, 5:15 PM*** NLEOMF Candlelight Vigil on the National Mall, 6 PM Friday, October 15th C.O.P.S. Survivors’ Conference & Kids Programs C.O.P.S. Picnic on the Patio Steve Young Honor Guard / Pipe Band Competition CANCELLED 27th Annual Emerald Society Memorial March, 5 PM Saturday, October 16th National Peace Officers’ Memorial Service (West Front Lawn US Capitol) 12 PM Stand Watch for the Fallen, 2 PM to Midnight at Memorial Sunday, October 17th 30th Anniversary Commemoration at Memorial, 9 AM to 10:30 AM Produced by Danny Veith - Colorado Fallen Hero Foundation - 720.373.6512 - [email protected] Page 1 of 18 Never before has this annual guide been distributed just 8-weeks before Police Week. This guide was delayed to insure Police Week events were not cancelled (as occurred in May of 2019), postponed (as occurred last May), all while monitoring District of Columbia health orders (for example, an order by the Mayor’s Office on July 29, 2021 to resume indoor mask use). Because of the pandemic, this is the first time National Police Week will occur outside the week encompassing May 15th. -
National Gallery
West Building East Building Main Floor 1 – 13 13th- to 16th-Century Italian 35 – 35A, 15th- to 16th-Century 53 – 56 18th- and Early 19th-Century Tower 2 Modern and Paintings and Sculptures 38 – 41A Netherlandish and German French Paintings and Sculptures Contemporary Art Paintings and Sculptures 17 – 28 16th-Century Italian, French, and 57 – 59, 61 British Paintings and Sculptures Roof Special Exhibitions Terrace Spanish Paintings, Sculptures, 42 – 51 17th-Century Dutch and Flemish 60 – 60B, American Paintings and Sculptures Roof Terrace and Decorative Arts Paintings 62 – 71 Tower 3 Tower 2 Tower 1 Public Space 29 – 34, 17th- to 18th-Century Italian, 52 18th- and 19th-Century Spanish 80 – 93 19th-Century French Paintings 36 – 37 Spanish, and French Paintings and French Paintings Closed to the Public 72 – 79 Special Exhibitions Roof Terrace Tower 3 Tower 1 Tower Level 19 18 17 20 21 24 12 23 13 25 22 Sculpture Garden 26 27 11 28 10 19 9 18 6 Tower 2 17 5 3 Lobby A 20 8 2 31 24 West 21 7 23 Garden 12 4 29 13 80 32 25 Court22 Lobby B 1 79 30 11 91 Sculpture Garden 26 27 10 81 78 33 28 45 9 92 90 87 82 37 46 6 88 86 75 Tower 2 38 5 93 76 43 48 3 83 77 34 Lobby A 44 8 51 50C 2 89 31 36 West 47 7 85 74 Tower 1 39 Garden 49 4 Rotunda 84 73 Tower 3 35 29 42 50B 80 32 35A Court Lobby B 50 1 79 30 40 50A 91 78 41 52 92 90 87 Lobby C East81 82 33 41A 45 Information Founders 56 75 72 37 46 Room 88 86 Garden 76 38 48 Room 53 93 57 77 34 43 89 58 83Court Lobby D Terrace Café 36 44 47 51 50C 54 74 Tower 1 39 55 85 73 Tower 3 Upper Level 35 42 49 50B -
The D.C. Freeway Revolt and the Coming of Metro Part 6 a New Administration Takes Over
The D.C. Freeway Revolt and the Coming of Metro Part 6 A New Administration Takes Over Table of Contents The New Administration Gets to Work .......................................................................................... 2 Transition in the District ................................................................................................................. 7 Waiting for Secretary Volpe ......................................................................................................... 10 Secretary Volpe Gets Involved ..................................................................................................... 15 Trying to Break the Logjam .......................................................................................................... 21 Backstage Negotiation .................................................................................................................. 24 The Nixon Administration Gets Involved ..................................................................................... 36 Advancing Metro .......................................................................................................................... 42 How To Break An Impasse ........................................................................................................... 48 Regrouping After a Loss ............................................................................................................... 65 Imminent Compromise ................................................................................................................ -
East Building
West Building East Building Main Floor Ground Floor Modern and 1 – 13 13th- to 16th- 52 18th- and 19th- G1 – G9, G21 19th- and 20th- G22 – G34 Special Exhibitions Contemporary Art Century Italian Century Spanish Century Sculptures G42 – G43 American Special Exhibitions 17 – 28 16th-Century Italian, 53 – 56 18th- and Early G11 – G13A 17th- and 18th- Decorative Arts and French, and Spanish 19th-Century Century Sculptures Paintings Roof Terrace French and Decorative Arts 29 – 34, 36 – 37 17th- to 18th- Public Space Public Space Century Italian, 57 – 59, 61 British G10, G14 – 19 Medieval, Spanish, and French Renaissance, Closed to the Public Closed to the Public 60 – 60B, 62 – 71 American and Baroque 35 – 35A, 38 – 41A 15th- to Sculptures and Tower 2 Temporarily Closed 16th-Century 80 – 93 19th-Century Decorative Arts Visit nga.gov/renovation Netherlandish and French Roof German Terrace Accessible Path to Concourse 72 – 79 Special Exhibitions and West Building 42 – 51 17th-Century Dutch and Flemish Tower 1 Tower 19 18 17 20 21 24 12 23 13 25 22 26 27 11 28 10 9 6 Main Floor Tower 2 5 3 Lobby A 8 2 31 West 7 Garden 4 29 1 80 32 Court Lobby B 91 79 30 90 81 78 33 45 92 87 82 37 46 88 86 75 38 48 93 76 34 43 Rotunda 89 83 77 36 44 47 51 50C 74 39 85 73 Tower 1 35 42 49 50B 84 35A 50 40 41 50A 52 41A Information Lobby C East 72 Room Founders 56 Room 53 57 Garden 54 58 Court Lobby D Terrace Café 55 59 71 Upper Level Pavilion 60 69A Café 61 67 70 63 60A 68 69 9TH STREET 65 Fountain / Ice Rink 62 66 60B G14 64 G10 G13A G15 G9 G16 G13 G12 G11A Tower -
WMATA Escalator Canopy Program - 8043 Phase 4 Various Locations NCPC MAP FILE NUMBER Washington, DC 00:00(40.00)44875
Executive Director’s Recommendation Commission Meeting: March 7, 2019 PROJECT NCPC FILE NUMBER WMATA Escalator Canopy Program - 8043 Phase 4 Various Locations NCPC MAP FILE NUMBER Washington, DC 00:00(40.00)44875 SUBMITTED BY APPLICANT’S REQUEST Washington Metropolitan Area Transit Approval of comments on concept Authority design REVIEW AUTHORITY PROPOSED ACTION D.C. Code § 9-1107.01, Washington Approval of comments on concept Metropolitan Area Transit Authority Compact design ACTION ITEM TYPE Staff Presentation PROJECT SUMMARY The Washington Metropolitan Area Transit Authority (WMATA) is seeking comments on concept designs for Phase IV of the installation of exterior canopies at five Metrorail stations that are located on National Park Service (NPS) sites. The five sites are (1) Archives-Navy Memorial-Penn Quarter, (2) Arlington Cemetery (both north and south entrance locations), (3) Judiciary Square North, (4) Smithsonian (north entrance), and (5) U Street/African-American Civil War Memorial (east entrance). WMATA’s objectives for the canopy program are to comply with current building codes, improve escalator reliability, protect Metro patrons from rain, ice, and snow, and provide design excellence that reflects the dignity and elegance appropriate for an entrance to the Metrorail system of the Nation’s Capital. KEY INFORMATION • The prototype canopy design was selected in July 2001, created by Lourie & Chenowith, and approved by the U.S. Commission of Fine Arts (CFA) and the National Capital Planning Commission (NCPC). The District of Columbia, Maryland, and Virginia State Historic Preservation Officers determined that the prototype canopy did not result in adverse effects on historic properties. • The WMATA prototype canopy design was approved by the NCPC on December 4, 2003, for use at all exterior uncovered Metrorail entrances, with the exception of eight that the Commission requested be individually submitted and reviewed. -
Campus Antiwar Network Plans for Counter-Inauguration Protests on January 20, 2005
CAMPUS ANTIWAR NETWORK PLANS FOR COUNTER-INAUGURATION PROTESTS ON JANUARY 20, 2005 [See note below on subway closings] On January 20, 2005 students and youth will protest the inauguration of George W. Bush in locations all over the country. As Bush takes the oath of office for his second presidential term on January 20, 2005, thousands of people will protest Bush’s war and right-wing agenda. As he rides his limousine down Pennsylvania Avenue, he and the world will hear our message: “Bush is not our President.” The Campus Antiwar Network will participate in the counter-inaugural activities in both Washington DC and San Francisco, and urges everyone who can to come out to make this big, visible and loud. We will join thousands of others to send a message against the continuing war on the Iraqi and Palestinian people, and to demand money for schools and jobs not war and military recruitment in our schools. Washington DC: The DC Anti-War Network (DAWN) has called for a permitted anti-war rally and march from Malcolm X Park to the parade route. Since the Inaugural parade doesn’t start till 2:30, this DC area coalition is hoping that the march can be an exciting way to kick off the day by marching through the city. CAN folks who are getting into town before 11:15 AM will meet up at the park and join the march, and go from the march to the parade route. ANSWER has gotten a protest permit for 4th St and Pennsylvania Ave. This is the start of the parade route, where there is a lot of open space. -
D.C. Freeway Revolt and the Coming of Metro Part 4 Battling the Revolt
D.C. Freeway Revolt and the Coming of Metro Part 4 Battling the Revolt Table of Contents Unfinished Business ........................................................................................................................ 3 President Johnson Intervenes .......................................................................................................... 7 Revisiting Home Rule ..................................................................................................................... 9 Revenue Bill .................................................................................................................................. 14 Interstate Compact ........................................................................................................................ 15 North-Central Freeway .................................................................................................................. 19 The Arthur D. Little Report .......................................................................................................... 21 Reaction to the Little Report ......................................................................................................... 25 The Doxiadis Plan for the Georgetown Waterfront ...................................................................... 30 Policy Advisory Committee Acts.................................................................................................. 36 About Tunnels .............................................................................................................................. -
Arts Section Association of College and Research Libraries American
ArtsGuide, Washington Arts Section Association of College and Research Libraries American Library Association Annual Conference June 24-29, 2010 Introduction Welcome to the ACRL Arts Section’s ArtsGuide Washington D.C.! This selective guide to cultural attractions and events has been created for attendees of the 2010 ALA Annual Conference in D.C. As home to many of our nation’s cultural heritage treasures and world-reknowned arts institutions, there’s no shortage of opportunities for arts-related activity in Washington D.C. We hope our guide will help you find all of the places you’ve heard of before...and maybe some that you haven’t! This Artsguide also includes a supplement (pgs. 19-34) that provides locations, descriptions, and brief histories of some of the many D.C.-area monuments discussed in the ACRL Arts Section program: How We Memorialize: The Art and Politics of Memorialization Sunday, June 27, 1:30 - 3:30 pm REN (Renaissance Washington) - Congressional Hall A/B Map of sites listed in this guide See what’s close to you or plot your course by car, foot, or public transportation using the Google map version of this guide: http://tinyurl.com/artsguide-dc Where to search for arts and entertainment • The Washington Post’s Going Out Guide: http://www.washingtonpost.com/gog/dc- events.html • The Smithsonian provides a comprehensive calendar that covers events at all of the Smithsonian institutions: http://www.si.edu/events/ This guide has been prepared by: Editor: Caroline Caviness (Rutgers University) Contributors: Rachel Martin Cole (The Art Institute of Chicago), Kim Detterbeck (Frostburg State University), Jenna Rinalducci (George Mason University), Angela Weaver (University of Washington) *Efforts were made to gather the most up to date information for performance dates, but please be sure to confirm by checking the venue web sites provided. -
LCT for 70 Ave Park H L4 D2 Q St UM TB15 34 F4 F6 Nolte Q T St R G H 88
Dunoon Rd D a A O pg 89M J1 d G v lk Z13 Su R 70 H e Fo Dall 22 O ill Grosvenor Ln 46 96 L8 Leafy Denn ve C2 ia Dr C M is A Ave Z29 er C Center ls 6 y 89 Bel Baltimore r C4 20 v S R2 81 J5 Montg House ’ Tucker w Eccleston St Imperial D 21 a Powder Mill Rd Y 81 89M J7 k X R5 Y 46 4 Kent St 9 22 R E 83 u H St P Renfrew Rd 22 83 m J9 Dexter Ave Dublin Dr 19 20 E G UM a Sunnyside Ave n 7 Devere R Riggs Rd 89 70 o Capitol Q1 Four Dr 10 20 83X S 89M H t Vie 22 M t 86 g w 5 r O n Q2 O i A McKenney D 22 24 E IKEA s r v e Q4 e Corners 20 D G J1 n e Hills v G v Dr 495 e o n 20 T J2 Fleming K A Park Y5 r r 22 e E TB17 G D v N Baltimore Washington y Dallas Ave a 22 McGovern J3 Park f Y7 t k th 650 C 87 a s oc es O e Y8 e Br Cr N 70 185 4 L r M I 89 o Fo 19 193 Y9 F rest Z2 Z6 R 89M Forest Glen: r 8 8 Glen P 81 Cherry Hill 30 e 7 D Rd C2 r v 7 Z8 Z9 D Road Community B30 r 5 n 83 A 7 8 o C4 Beaver Dam Rd D r 8 Z11 Z13 t Park G P Forest e 19 h C8 UM Cherry Hill Rd College 30 o ut Kensington 19 g k m o c Z29 9 i H Old Georgetown Rd k Cedar Ln i a 19 K6 o Glen L Park 86 s t Cabin D 30 H d c o 21 22 E 20 Seven ill R Rock e Park Market TB17 Whitley n br 7 8 y Springs Village Creek 34 n 495 24 Place Edgewood Rd 30 e Oakview Dr Park Ter J5 o 8 Holy S M n t Pi Apartments Singleton Dr Park C l 20 sgah Ln 81 o i 83 UM 201 Mormon Temple t J5 Cross g Merwood J7 S o UM 81 81 83 Greenbelt Ryland Dr Hospital 8 Northwest C8 National C Park Dr UM 30 Maplewood Sligo 83 47th J9 r Ln Ave y ve e 20 K6 Kiernan Dr A Rec Area J5 e Frankli S UM Greenbelt w 30 n t d Paint k