Engineering Alloys
Total Page:16
File Type:pdf, Size:1020Kb
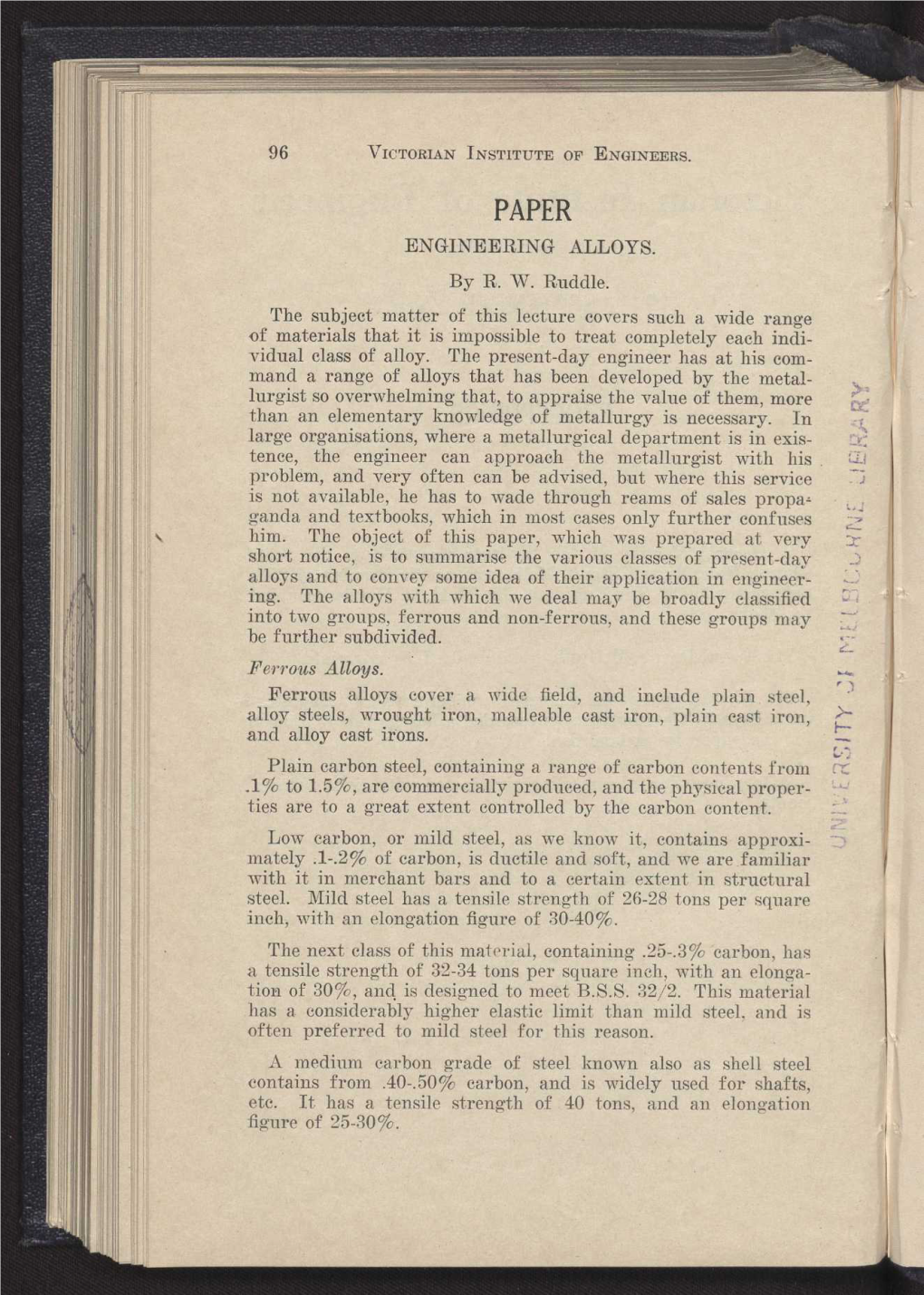
Load more
Recommended publications
-
Hiduminium Technical Data
HIDUMINIUM TECHNICAL DATA HIGH DUTY ALLOYS LTD SLOUGH F oreword Extensive research carried out in recent years, com bined with an increasing demand for " H ID UM IN IUM " high tensile aluminium alloys, has necessitated the revision and increase of the series of data sheets pre viously issued by the Company. As before, our aim is to place before designers and constructors the fullest possible particulars regarding the physical and mechanical properties of " H ID U M IN IU M ," which will enable them to select the materials most suitable for their requirements and to adapt their designs in accordance with the outstanding character istics of this range of alloys. " HIDUMINIUM" is produced under conditions of strict scientific control and progressive inspection and a staff of expert Metallurgists, Research W orkers and Technicians is always ready to give advice on all problems connected with the use of these alloys. Fresh data, as it is revealed by further research, will be issued on additional sheets. This will ensure that all information contained in this volume is up-to-date and may thus be referred to at all times with complete confidence. HIGH DUTY ALLOYS LIMITED 3 CONTENTS Page Index to Specifications 6-9 Hiduminium 15 10-11 Hiduminium 23 12-13 Hiduminium 33 14-15 Hiduminium 35 16-17 H iduminium 40 & 42 18-19 Hiduminium 45 20-21 Hiduminium R.R. 50 22-23 Hiduminium R.R. 53 24-26 Hiduminium R.R. 53.C 27-29 Hiduminium R.R. 56 30-32 H iduminium R.R. 59 33-35 Hiduminium 72 36-37 Hiduminium R.R. -
850°C. Sp. Gray. 3.75 ; S. Ht. .068. Obtained in the Pure State
126 NEWNES PRACTICAL MECHANICS December, 1939 greenish -yellow appearance. In English cent. ; tin, 2.5 per cent. ; zinc, 7.1 per cent. per alloys recently introduced in America. standard gold the silver is replaced by Sometimes about .5per cent. of alu- Typical composition :silver,70.44 per copper. minium is also added. cent.; copper, 28.90 per cent. ; beryllium, Autogenous Soldering. -The uniting of twoBearings Metals. -See Anti -friction Metals. .87 per cent. Used as a resistance -wire pieces of metal together simply by meltingBell Metal. -A type of bronze or copper -tin. material. their edges by means of a blowlamp or alloy containing from 12 to 24 per cent.BessemerSteel. -Steel manufactured by other source of heat. The word " auto- of tin.Technically known as Hard the Bessemer process (the invention of geneous " means " self -generated." Bronze." Sir Henry Bessemer in1856). In the The lead linings of chemical and acidBeryllium. -Formerly named " Gluoinum." Bessemer process, the molten " pig " iron tanks are usually autogenously soldered Metallic element. Chemical symbol, Be ; is run into a receptacle known as a because the presence of any dissimilar At. No. 4 ; At. Wt. 9 ; M.P. 962°C. ; Sp. " converter," in which a blast of air is metal at the joints would set up electro- Gray. 2.1; Sp. Ht. .397. passed through it.Impurities are thus lytic actions which might attain serious Chief ore :Beryl, 3BeO.A1203.6SiO2. burned out of the molten metal. proportions. Occurs also in gems, such as emerald. BibraAlloy. -Composition :Bismuth, 8 Avional.-A Swiss aluminium alloy. Com- Name of the metal derived from its parts; tin, 9 parts; lead, 38 to 40 parts. -
Brazing Compilation of Literature References from 1973 to 1978
OCTOBER 1979 BRAZING COMPILATION OF LITERATURE REFERENCES FROM 1973 TO 1978. BY J.C. RÖMER N et hf^rlfi rids E norqy R o soa re h \ oundation ECN does not assume any liability with respect to the use of, or for damages resulting from the use of any information, apparatus, method or process disclosed in this document. Netherlands Energy Research Foundation ECN P.O. Box 1 1755 ZG Petf.n(NH) The Netherlands Telephone (0)2246 - 62».. Telex 57211 ECN-7* OCTOBER 1979 BRAZING COMPILATION OF LITERATURE REFERENCES FROM 1973 T01978. BY J.C. ROMER -2- ABSTRACT This report is a compilation of published literature on high temperature brazing covering the period 1973-1978. The references are listed alphabetically with regard to the base material or combination of base materials to be brazed. Trade names are treated as base materials. The report contains approximately 1500 references, of which 300 are to patents. KEYWORDS BRAZING BRAZING ALLOYS FILLER METALS JOINING - 3 CONTENTS ABSTRACT 1. ALUMINIUM 2. ALUMINIUM (FLVXLESS) 3. ALUMINIUM - BERYLLIUM 4. ALUMINIUM/BORON COMPOSITES 5. ALUMINIUM - COPPER 5.1. Aluminium - graphite 5.2. Aluminium - nickel alloys 5.3. Aluminium - niobium 5.4. Aluminium ~ molyldenum 5.5. Aluminium - stainless steel 5.6. Aluminium - steels 5.7. Aluminium - tantalum 5.8. Aluminium - titanium 5.9. Aluminium - tungsten 6. BERYLLIUM 7. BORONNITRIDE• 8. BRASS 8.1. Brass - aluminium 8.2. Brass - steels 9. BRONZE 9.1. Bronze - stainless steels 10. CERAMICS 10.1. Ceramics - metal - 4 - CERMETS 61 11.1. Cermets - stainless steels 62 COBALT 63 COPPER ALLOYS 64 13.1. Copper alloys - brass 68 13.2. -
Metallurgical Abstracts (General and Non-Ferrous)
METALLURGICAL ABSTRACTS (GENERAL AND NON-FERROUS) Volume 2 1935 Part 13 I —PROPERTIES OF METALS (Continued from pp. 553-568.) Refined Aluminium. Robert GaDeau (Metallurgist (Suppt. to Engineer), 1936, 11, 94-96).—Summary of a paper presenteD to the Congrès Inter nationale Des Mines, De la Métallurgie, et De la Géologie Appliquée, Paris. See Met. Abs., this vol., pp. 365 anD 497.—R. G. _ On the Softening and Recrystallization of Pure Aluminium. ------ (A lu minium, 1935, 17, 575-576).—A review of recent work of Calvet anD his collaborators ; see Met. Abs., this vol., pp. 453, 454. A. R. P. *Some Optical Observations on the Protective Films on Aluminium in Nitric, Chromic, and Sulphuric Acids. L. TronstaD anD T. HbverstaD (Trans. Faraday Soc., 1934, 30, 362-366).—The optical properties of natural films on aluminium were measureD in various solutions anD their change with time of immersion observeD. Little change occurs in such films in chromic aciD solutions with or without chloriDe ; the films are not protective in concentrateD sulphuric aciD, anD in concentrateD nitric aciD the protective films are alternately DissolveD anD re-formeD. The mean thickness of natural films on aluminium is 100 p. or more than 10 times as thick as those on iron.—A. R. P. *Light from [Burning] Aluminium and Aluminium-Magnésium [Alloy], J. A. M. van Liempt anD J. A. De VrienD (Bee. trav. chim., 1935, 54, 239-244). „ . —S. G. ’"Investigations Relating to Electrophotophoresis Exhibited by Antimony Gisela Isser anD AlfreD Lustig (Z . Physik, 1935, 94, 760-769).—UnchargeD submicroscopic particles subjecteD to an electric fielD in an intense beam of light are founD to move either in the Direction of, or against, the fielD. -
The Tensile and Creep Behavior of Mg–Zn Alloys with and Without Y and Zr As Ternary Elements
J Mater Sci (2007) 42:3675–3684 DOI 10.1007/s10853-006-1352-5 The tensile and creep behavior of Mg–Zn Alloys with and without Y and Zr as ternary elements C. J. Boehlert Received: 28 July 2005 / Accepted: 28 February 2006 / Published online: 30 January 2007 Ó Springer Science+Business Media, LLC 2007 Abstract Tensile–creep experiments were conducted effects on the tensile properties and creep behavior in the temperature range 100–200 °C and stress range are discussed in comparison to other Mg-based alloy 20–83 MPa for a series of magnesium–zinc–yttrium systems. (Mg-Zn-Y) and mangnesium-zinc–zirconium (Mg-Zn- Zr) alloys ranging from 0 to 5.4 wt% Zn, 0 to 3 wt% Y, and 0 to 0.6 wt.% Zr. The greatest tensile– creep resistance was exhibited by an Mg–4.1Zn–0.2Y alloy. The room-temperature yield strength increased Introduction with increasing Y content for Mg–1.6–2.0Zn alloys. The greatest tensile strength and elongation was In order to improve the creep strength of magnesium exhibited by Mg–5.4Zn–0.6Zr. This alloy also exhibited (Mg) alloys, rare earth and/or alkaline earth elements the finest grain size and the poorest creep resistance. in small quantities have been effectively used as alloy The measured creep exponents and activation energies additions [1–14]. For example, the creep rate of suggested that the creep mechanisms were dependent Mg–8wt.%Y1 has been observed to be four orders of on stress. For applied stresses greater than 40 MPa, the magnitude lower than AZ91 at 277 °C in the stress creep exponents were between 4 and 8. -
Aircraft Metallurgy (According to the Syllabus Prescribed by Director General of Civil Aviation, Govt
L.N.V.M. Society Group of Institutes, Palam Extn., Part-1, Sec.-7, Dwarka, New Delhi - 45 1 Aircraft Metallurgy (According to the Syllabus Prescribed by Director General of Civil Aviation, Govt. of India) 2 Aircraft Metallurgy L.N.V.M. Society Group of Institutes, Palam Extn., Part-1, Sec.-7, Dwarka, New Delhi - 45 3 CONTENTS 1. FERROUS METALS : PRODUCTION OF STEELS AND ALLOY STEELS 1 2. NON-FERROUS METALS AND IT’S ALLOYS 12 3. NICKEL ALLOYS 19 4. COPPER AND ITS ALLOYS 29 5. WROUGH ALUMINIUM ALLOYS 36 6. MAGNESIUM ALLOYS 43 7. HEAT TREATMENT OF NON-FERROUS METALS AND ALLOYS 58 8. IDENTIFICATION OF METALS 65 9. MECHANICAL TESTING OF METALS 67 10. CORROSION : REMOVAL AND RECTIFICATION 77 11. CORROSION : METHODS OF PROTECTION 82 12. NDE : OIL AND CHALK PROCESSES 86 13. NDE : PENETRANT DYE PROCESSES 88 14. NDE : MAGNETIC FLAW DETECTION 93 15. NDE : FLUORESCENT PENETRANT PROCESSES 98 16. NDE : ENDOSCOPE INSPECTIONS 103 17. NDE : ULTRASONIC FLAW DETECTION AND THICKNESS MEASUREMENT 107 18. NDE : RADIOLOGICAL EXAMINATION OF AIRCRAFT STRUCTURE 111 19. NDE : EDDY CURRENT METHODS 114 20. ADVANCED COMPOSITES MATERIALS 118 L.N.V.M. Society Group of Institutes, Palam Extn., Part-1, Sec.-7, Dwarka, New Delhi - 45 1 UNIT - I FERROUS METAL: PRODUCTION OF STEELS AND ALLOYS STEELS STEEL Steel basically differs from cast iron in the amount of carbon content contained by it. It is not only the quantity of carbon which makes the difference but also the form in which it is present. In steel the amount of carbon present is upto 1.5 percent and it is completely in the combined form. -
Isinox Metaltec Private Limited
+91-8042974287 Isinox Metaltec Private Limited https://www.indiamart.com/isinoxalloys/ Isinox Metaltec Private Limited is one of the renowned names occupied in manufacturing and exporting an inclusive collection of products comprising Aluminium Alloy Wire and Copper Cladding Wire. About Us Incepted in the year 2013, Isinox Metaltec Private Limited is one of the excellent business organization effortlessly engrossed in manufacturing and exporting a range of products which include Aluminium Alloy Wire and Copper Cladding Wire. Made in adherence with the prevailing market set standards, we guarantee that only optimal-class material and different modern tools and machines are used in their improvement procedure. In compliance with the trends and advancements taking place in the market, these are especially applauded. Underneath the path of our mentor Mr. Ravi Bansal, we have finished massive popularity and credibility of our customers. For more information, please visit https://www.indiamart.com/isinoxalloys/profile.html ALUMINIUM ALLOY WIRES P r o d u c t s 5052 Aluminium Alloy Wire Aluminum Alloy Wire Aluminum Alloy TIG Welding 5056 Aluminium Alloy Wire Wire ALUMINUM WELDING WIRE P r o d u c t s Aluminium Alloy Wire for 5052 Aluminum Alloy Wire Water-Bottle Carrier 1050 Aluminum Wire 2011 Aluminium Alloy Wire ALUMINIUM ALLOY WIRE P r o d u c t s 1060 1080 1085 High Quality Aluminium Alloy Wire For Aluminum Wire Used In Refrigerator Grilles Aluminium Alloy Wire For 1120 Aluminium Alloy Wire Clothes Pegs ALUMINUM WIRE P r o d u c t s 5154 -
Thermomechanical Processing of Mg-Li-Al Ultralight Alloys Rezawana Islam
University of North Dakota UND Scholarly Commons Theses and Dissertations Theses, Dissertations, and Senior Projects January 2019 Thermomechanical Processing Of Mg-Li-Al Ultralight Alloys Rezawana Islam Follow this and additional works at: https://commons.und.edu/theses Recommended Citation Islam, Rezawana, "Thermomechanical Processing Of Mg-Li-Al Ultralight Alloys" (2019). Theses and Dissertations. 2462. https://commons.und.edu/theses/2462 This Thesis is brought to you for free and open access by the Theses, Dissertations, and Senior Projects at UND Scholarly Commons. It has been accepted for inclusion in Theses and Dissertations by an authorized administrator of UND Scholarly Commons. For more information, please contact [email protected]. THERMOMECHANICAL PROCESSING OF Mg-Li-Al ULTRALIGHT ALLOYS by Rezawana Islam Bachelor of Science, Military Institute of Science and Technology A Thesis Submitted to the Graduate Facility of the University of North Dakota in partial fulfillment of the requirements for the degree of Master of Science Grand Forks, North Dakota May 2019 i Copyright 2019 Rezawana Islam ii PERMISSION Title Thermomechanical processing of Mg-Li-Al ultralight alloys. Department Mechanical Engineering Degree Master of Science In presenting this thesis in partial fulfillment of the requirements for a graduate degree from the University of North Dakota, I agree that the library of this University shall make it freely available for inspection. I further agree that permission for extensive copying for scholarly purposes may be granted by the professor who supervised my thesis work or, in her (or his) absence, by the Chairperson of the department or the Dean of the School of Graduate Studies. -
Alloys for Aeronautic Applications: State of the Art and Perspectives
metals Review Alloys for Aeronautic Applications: State of the Art and Perspectives Antonio Gloria 1, Roberto Montanari 2,*, Maria Richetta 2 and Alessandra Varone 2 1 Institute of Polymers, Composites and Biomaterials, National Research Council of Italy, V.le J.F. Kennedy 54-Mostra d’Oltremare Pad. 20, 80125 Naples, Italy; [email protected] 2 Department of Industrial Engineering, University of Rome “Tor Vergata”, 00133 Rome, Italy; [email protected] (M.R.); [email protected] (A.V.) * Correspondence: [email protected]; Tel.: +39-06-7259-7182 Received: 16 May 2019; Accepted: 4 June 2019; Published: 6 June 2019 Abstract: In recent years, a great effort has been devoted to developing a new generation of materials for aeronautic applications. The driving force behind this effort is the reduction of costs, by extending the service life of aircraft parts (structural and engine components) and increasing fuel efficiency, load capacity and flight range. The present paper examines the most important classes of metallic materials including Al alloys, Ti alloys, Mg alloys, steels, Ni superalloys and metal matrix composites (MMC), with the scope to provide an overview of recent advancements and to highlight current problems and perspectives related to metals for aeronautics. Keywords: alloys; aeronautic applications; mechanical properties; corrosion resistance 1. Introduction The strong competition in the industrial aeronautic sector pushes towards the production of aircrafts with reduced operating costs, namely, extended service life, better fuel efficiency, increased payload and flight range. From this perspective, the development of new materials and/or materials with improved characteristics is one of the key factors; the principal targets are weight reduction and service life extension of aircraft components and structures [1]. -
The Phase Composition and Mechanical Properties of the Novel Precipitation-Strengthening Al-Cu-Er-Mn-Zr Alloy
applied sciences Article The Phase Composition and Mechanical Properties of the Novel Precipitation-Strengthening Al-Cu-Er-Mn-Zr Alloy Sayed Amer 1,2, Olga Yakovtseva 1 , Irina Loginova 1, Svetlana Medvedeva 1, Alexey Prosviryakov 1 , Andrey Bazlov 1,3, Ruslan Barkov 1 and Andrey Pozdniakov 1,* 1 Department of Physical Metallurgy of Non-Ferrous Metals, National University of Science and Technology MISiS, 119049 Moscow, Russian; [email protected] (S.A.); [email protected] (O.Y.); [email protected] (I.L.); [email protected] (S.M.); [email protected] (A.P.); [email protected] (A.B.); [email protected] (R.B.) 2 Faculty of Engineering, Metallurgy and Petroleum Engineering Department, Al-Azhar University, Mining, Cairo 11371, Egypt 3 7/9 Universitetskaya nab, St.Petersburg State University, 199034 St. Petersburg, Russia * Correspondence: [email protected]; Tel.: +7-(495)-638-44-80 Received: 4 July 2020; Accepted: 1 August 2020; Published: 3 August 2020 Abstract: The microstructure, phase composition, and mechanical properties during heat treatment and rolling of the novel Al-5.0Cu-3.2Er-0.9Mn-0.3Zr alloy were evaluated. A new quaternary (Al,Cu,Mn,Er) phase with possible composition Al25Cu4Mn2Er was found in the as-cast alloy. Al20Cu2Mn3 and Al3(Zr,Er) phases were nucleated during homogenization, and θ”(Al2Cu) precipitates were nucleated during aging. The metastable disc shaped θ”(Al2Cu) precipitates with a thickness of 5 nm and diameter of 100–200 nm were nucleated mostly on the Al3(Zr,Er) phase precipitates with a diameter of 35 nm. The hardness Vickers (HV) peak was found after the annealing of a rolled alloy at 150 ◦C due to strengthening by θ”(A2Cu) precipitates, which have a larger effect in materials hardness than do the softening processes. -
Application of a State Variable Description of Inelastic Deformation to Geological Materials
APPLICATION OF A STATE VARIABLE DESCRIPTION OF INELASTIC DEFORMATION TO GEOLOGICAL MATERIALS A thesis submitted for the degree of Doctor of Philosophy (University of London) and for the Diploma of University College by Stephen John Covey-Crump Department of Geological Sciences, University College London, Gower Street, London, WC1E 6BT ProQuest Number: 10630768 All rights reserved INFORMATION TO ALL USERS The quality of this reproduction is dependent upon the quality of the copy submitted. In the unlikely event that the author did not send a com plete manuscript and there are missing pages, these will be noted. Also, if material had to be removed, a note will indicate the deletion. uest ProQuest 10630768 Published by ProQuest LLC(2017). Copyright of the Dissertation is held by the Author. All rights reserved. This work is protected against unauthorized copying under Title 17, United States C ode Microform Edition © ProQuest LLC. ProQuest LLC. 789 East Eisenhower Parkway P.O. Box 1346 Ann Arbor, Ml 48106- 1346 2 ABSTRACT The work reported in this thesis is an investigation of the potential for employing non steady-state constitutive relations to describe the inelastic deformation properties of rock forming minerals. Attempts to determine generally applicable constitutive equations for inelastic deformation are complicated by the severe path dependence of the deformation response and by the wide range of mechanisms by which that deformation is accomplished. In the geological literature it has been normal practice to circumvent these problems by approximating the deformation as occurring at steady-state. This presents difficulties for the description of deformation by inherently transient mechanisms, for the description of small strain deformation, and for the reliability of extrapolating laboratory mechanical properties to geological deformation conditions. -
Guide to High Performance Alloys
Table of Contents Alloy Guide 3 The Alloys of Materion Brush Performance Alloys 4 Chemical Composition 6 Alloy Products 6 Physical Properties 8 Product Guide 10 Strip and Wire Temper Designations 11 Strip 12 Strip Product Specifications 13 Spring Bend Limits of Strip Alloys 19 Wire 20 Rod, Bar, Tube and Plate Temper Designations 22 Rod and Bar 22 Tube 26 Plate and Rolled Bar 29 MoldMAX® and PROtherm™ Plastic Tooling Alloys 31 ToughMet® and Alloy 25 Oilfield Products 32 Alloy 25 Drill String Temper (25 DST) 33 BrushCAST® Casting Ingot & Master Alloys 34 Forged and Extruded Finished Components 36 Cast Shapes 37 Recommended Replacements for Discontinued Alloys 38 Materion Brush Performance Alloys Value-Added Services 39 Custom Fabrication Capabilities 40 Customer Technical Service 40 Other Services 42 Processing and Fabrication Guide 43 Heat Treating Fundamentals 44 Forming of Strip 47 Cleaning and Finishing 50 Joining 51 Machining 53 Hardness 56 Microstructures 57 Other Attributes and Application Engineering Data 59 Fatigue Strength 60 Stress Relaxation Resistance 62 Corrosion Resistance 64 Magnetic Properties 67 Galling Resistance 68 Bearing Properties 69 Friction & Wear Properties 69 Resilience and Toughness 70 Elevated Temperature Properties 71 Cryogenic Properties 72 Other Attributes 72 Your Supplier 73 Company and Corporate History 74 Materion Corporate Profile 75 Brush Performance Alloys Mining & Manufacturing 77 Product Distribution 78 Customer Service 79 Quality 80 Health and Safety, Environment and Recycling 81 Alloy Guide The copper and nickel alloys commonly supplied in wrought product form are highlighted in this section. Wrought products are those in which final shape is achieved by working rather than by casting.