(CNC)Milling Machine 1Mr
Total Page:16
File Type:pdf, Size:1020Kb
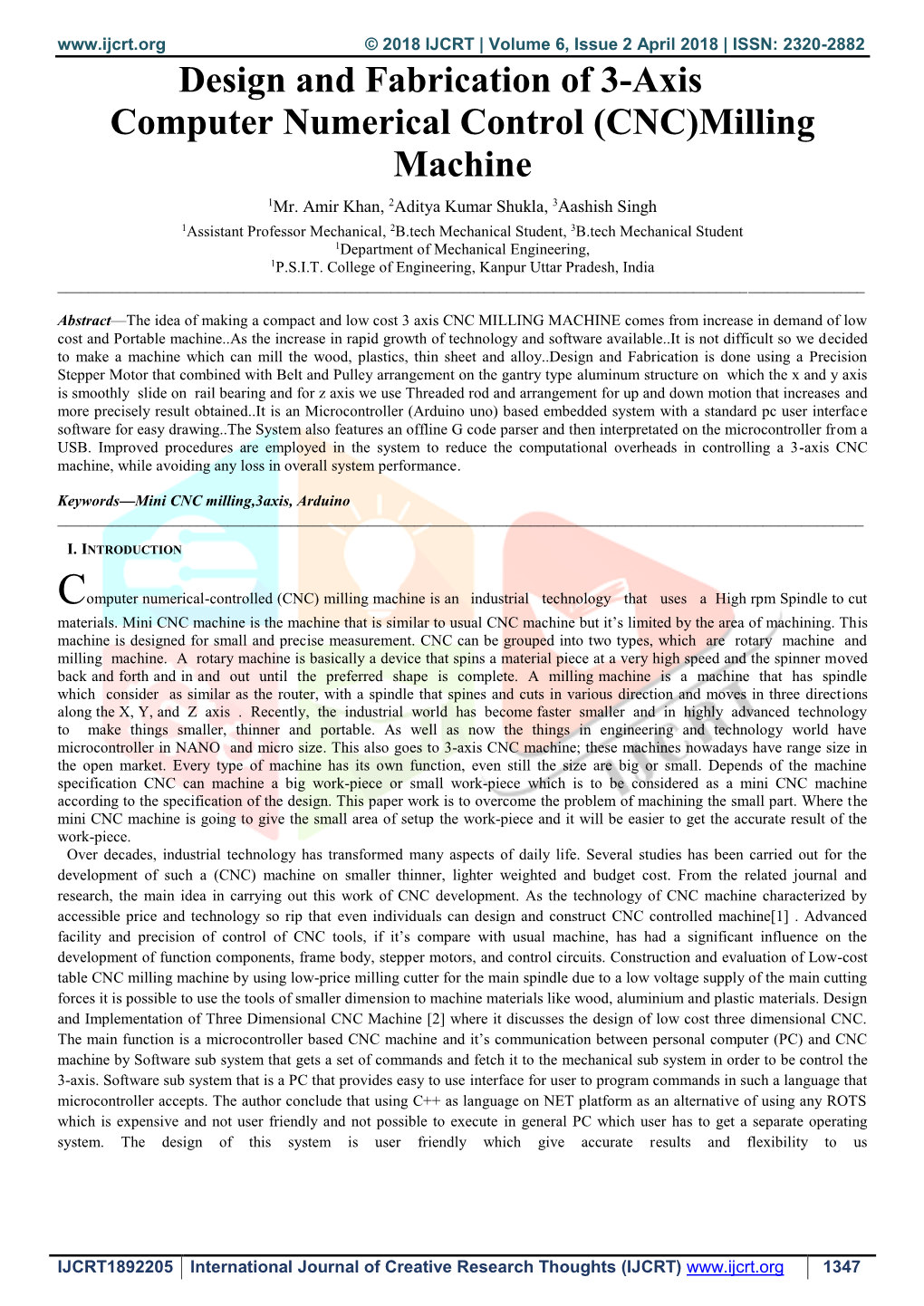
Load more
Recommended publications
-
Wood Engraving Using 3 Axis CNC Machine Ms.Disha D.Devardekar1, Ms.Aishwarya J.Gudale2
Wood Engraving Using 3 Axis CNC Machine Ms.Disha D.Devardekar1, Ms.Aishwarya J.Gudale2, Ms.Rutuja R.Karande3, 1,2,3Department of Electronics & Telecommunication Engineering, Bharati Vidyapeeth’s College of Engineering Kolhapur (India) ABSTRACT This machine can be used for Cutting, Engraving and Marking on wood, acrylic and PCB objects. Design picture that have been made on the PC sent to the microcontroller using serial communication then CNC perform execution on object according to point coordinates. Drill spindles will create patterns on objects automatically according to the design drawings. After testing, the CNC machine can be used for cutting, engraving and marking on wood, acrylic and PCB to 2D or 3D objects with 98.5% of carving accuracy and 100% of depth accuracy.Though there are several models for plotter, this plotter is designed in economical way. Main advantage of this plotter is we can replace the tool based on any application such as engraving machine, laser cutting machine, painting any surface and drawing purposes.Increase in the rapid growth of Technology significantly increased the usage and utilization of CNC systems in industries but at considerable expensive.The idea on fabrication of low cost CNC Router came forward to reduce the cost and complexity in CNC systems.Inspiring from this CNC technology and revolutionary change in the world of digital electronics &Microcontroller, we are presenting here an idea of “ 3 Axis CNC Machine For Wood Engraving Based On CNC Controller.” Keywords: CNC, Cutting, Engraving, Marking, Microcontroller. I.INTRODUCTION Working with automatic electrical and mechanical equipment demands precise, accuracy, speed, consistency and flexibility. -
Making Things Move DIY Mechanisms for Inventors, Hobbyists, and Artists
Making Things Move DIY Mechanisms for Inventors, Hobbyists, and Artists Dustyn Roberts New York Chicago San Francisco Lisbon London Madrid Mexico City Milan New Delhi San Juan Seoul Singapore Sydney Toronto Copyright © 2011 by The McGraw-Hill Companies. All rights reserved. Except as permitted under the United States Copyright Act of 1976, no part of this publication may be reproduced or distributed in any form or by any means, or stored in a database or retrieval system, without the prior written permission of the publisher. ISBN: 978-0-07-174168-2 MHID: 0-07-174168-2 The material in this eBook also appears in the print version of this title: ISBN: 978-0-07-174167-5, MHID: 0-07-174167-4. All trademarks are trademarks of their respective owners. Rather than put a trademark symbol after every occurrence of a trade- marked name, we use names in an editorial fashion only, and to the benefi t of the trademark owner, with no intention of infringe- ment of the trademark. Where such designations appear in this book, they have been printed with initial caps. McGraw-Hill eBooks are available at special quantity discounts to use as premiums and sales promotions, or for use in corporate training programs. To contact a representative please e-mail us at [email protected]. Information has been obtained by McGraw-Hill from sources believed to be reliable. However, because of the possibility of hu- man or mechanical error by our sources, McGraw-Hill, or others, McGraw-Hill does not guarantee the accuracy, adequacy, or completeness of any information and is not responsible for any errors or omissions or the results obtained from the use of such information. -
Setting up the Hardware and Software for a 3D Printer
Setting up the Hardware and Software for a 3D Printer Caroline Kerbelis Application Note March 28th 2014 Design Team 8 ECE 480 Abstract The purpose of team 8’s project is to design, fabricate, simulate, test and demonstrate a specialty printer that will be used to produce tactile graphics and maps for visually impaired students at MSU. Ideally this printer will produce durable images and be more feasible than current specialty printers available commercially. Extensive knowledge of 3D printer hardware and software and how they both interacted with each other is essential to the success of the project. 1 Table of Contents Abstract………………………..…………………….…………………………….1 Key Words.…………………...……………………….…………….…………….3 Introduction………………………………………………………………………..3 Hardware…………………………………………………………….…………….4 Software……………………………….…………………………………………..5 CAD Tools…………………….…………………………….………………5 CAM Tools…….…………………………………….….….……….……….6 Firmware……………………...……………………….…………….…………….7 Temperature Measurement…….…………………………….………………8 Conclusion..…………………...……………………….…………….…………….9 References..…………………...……………………….…………….…………...10 2 Introduction 3D printing, also known as additive manufacturing, is a process consisting of making a solid three-dimensional object from a digital model. This form of printing is achieved by using an additive process, where successive layers of material are added to a surface in different shapes to create a particular object, figure or graphic. The image is created using a Computer-Aided Design program (CAD) and then saving this file as a STereoLithography (STL) file. The file is then transferred to a g-code generator program which converts the file containing the image into a set of instructions/language that the printer understands. The 3D printer then used Computer Aided Manufacturing (CAM) software that reads the file and send electronic signals to control uses an extruder and motors that move along a x, y, and z axis to extrude a filament onto a surface creating the object through sequential layering. -
Programy Pro Obsluhu CNC
2021/01/14 06:54 1/11 CNC CNC CNC stroj není CNC strojař. Myslet za tebe nebude. Co nedělat: Neodpojovat motory když je k jednotce připojený napájení Nezapínat řídící jednotku když nejsou připojený motory Pokud arduino neblika po pripojeni k USB, tak nepripojuj napajeni motoru. Je tam asi zkrat. Nepřipojovat napájení motorů, pokud arduino nemá 5V z USB. Netočit manuálně s motorem moc rychle (generuje napětí?) Nešahat na žádný kontakty na arduinu Nenajizdet do kraju, zatim nejsou nainstalovany koncovy spinace Nenamoč drevotriskovy desky na CNC Nezapomeň vynulovat souřadnice před posláním G-kódu do stroje Neposílej do stroje G-kód, kterej sis předtim pořádně neprohlídnul/nevyzkoušel ve vzduchu (rozměry, rychlosti, atd…) Neutahuj při upínání šrouby do insertů moc hluboko nebo velkou silou. Neutahuj je ani proti šikmejm plochám! Nenastavuj nic na VFD invertoru vretena!! Da se tak spalit invertor i s motorem. Neutahuj klestinu vretene moc velkou silou (cim delsi klic tim snazsi je to prehnat). Vreteno pak ztrati presnost a je po srande. Klestinu vzdycky nejdriv zacvakni do matky, nez do ni das frezu, nebo nez ji zacnes sroubovat do vretene. Nenapínej řemeny silou. Šroub napínáku je velkej převod, takže bez námahy řemen přetrhne. Frezy skladuj tak, aby se nemohly otresama mlatit o sebe (treba v jedny krabici nebo v pytli). Jsou krehky a vzajemne se ostipou a ztupi. Programy pro obsluhu CNC Moje soucasny workflow 2D: LibreCAD → export do formatu DXF → bCNC → UGS-platform 3D: OpenSCAD → export do formatu STL → Kiri:Moto → UGS-platform PCB: gEDA/PCB -
Kustannustehokkaat Cad, Fem Ja Cam -Ohjelmat Tutkimus Saatavilla Olevista Ohjelmista Tammikuussa 2018
OULUN YLIOPISTON KERTTU SAALASTI INSTITUUTIN JULKAISUJA 6/2018 Kustannustehokkaat Cad, Fem ja Cam -ohjelmat Tutkimus saatavilla olevista ohjelmista tammikuussa 2018 Terho Iso-Junno Tulevaisuuden tuotantoteknologiat FMT-tutkimusryhmä Terho Iso-Junno KUSTANNUSTEHOKKAAT CAD, FEM JA CAM -OHJELMAT Tutkimus saatavilla olevista ohjelmista tammikuussa 2018 OULUN YLIOPISTO Kerttu Saalasti Instituutin julkaisuja Tulevaisuuden tuotantoteknologiat (FMT) -tutkimusryhmä ISBN 978-952-62-2018-5 (painettu) ISBN 978-952-62-2019-2 (elektroninen) ISSN 2489-3501 (painettu) Terho Iso-Junno Kustannustehokkaat CAD, FEM ja CAM -ohjelmat. Tutkimus saatavilla olevista ohjelmista tammikuussa 2018. Oulun yliopiston Kerttu Saalasti Instituutti, Tulevaisuuden tuotantoteknologiat (FMT) -tutkimusryhmä Oulun yliopiston Kerttu Saalasti Instituutin julkaisuja 6/2018 Nivala Tiivistelmä Nykyaikaisessa tuotteen suunnittelussa ja valmistuksessa tietokoneohjelmat ovat avainasemassa olevia työkaluja. Kaupallisten ohjelmien lisenssihinnat voivat nousta korkeiksi ja olla hankinnan esteenä etenkin aloittelevilla yrityksillä. Tässä tutkimuk- sessa on kartoitettu kustannuksiltaan edullisia CAD, FEM ja CAM -ohjelmia, joita voisi käyttää yritystoiminnassa. CAD-ohjelmien puolella perinteisille 2D CAD-ohjelmille löytyy useita hyviä vaih- toehtoja. LibreCAD ja QCAD ovat helppokäyttöisiä ohjelmia perustason piirtämiseen. Solid Edge 2D Drafting on erittäin monipuolinen täysiverinen 2D CAD, joka perustuu parametriseen piirtämiseen. 3D CAD-ohjelmien puolella tarjonta on tasoltaan vaihtelevaa. -
Fabrication of Low Cost 3-Axis Cnc Router
International Journal of Engineering Science Invention ISSN (Online): 2319 – 6734, ISSN (Print): 2319 – 6726 www.ijesi.org Volume 3 Issue 6ǁ June 2014 ǁ PP.01-10 Fabrication of Low Cost 3-Axis Cnc Router Dr.B.Jayachandraiah1, O.Vamsi Krishna2, P.Abdullah Khan3, R.Ananda Reddy4 Prof of M.E &Vice-Principal1, B.Tech, Mechatronics Engineering2, B.Tech, Mechatronics Engineering3, B.Tech, Mechatronics Engineering4 Department of Mechanical Engineering SriKalahateeswara Institute of Technology, Srikalahasti,A.P, India ABSTRACT : Increase in the rapid growth of Technology significantly increased the usage and utilization of CNC systems in industries but at considerable expensive. The idea on fabrication of low cost CNC Router came forward to reduce the cost and complexity in CNC systems. This paper discusses the development of a low cost CNC router which is capable of 3-axis simultaneous interpolated operation. The lower cost is achieved by incorporating the features of a standard PC interface with micro-controller based CNC system in an Arduino based embedded system. The system also features an offline G-Code parser and then interpreted on the micro- controller from a USB. Improved procedures are employed in the system to reduce the computational overheads in controlling a 3-axis CNC machine, while avoiding any loss in overall system performance. I. INTRODUCTION: In modern CNC systems, end-to-end component design is highly automated using computer-aided design (CAD) and computer-aided manufacturing (CAM) programs. The programs produce a computer file that is interpreted to extract the commands needed to operate a particular machine via a post processor, and then loaded into the CNC machines for production. -
Troubleshooting Your Thing-O-Matic
10/24/12 2:11 PM Troubleshooting Your Thing-O-Matic This troubleshooting page is for the MakerBot Thing-O-Matic. For help with The Replicator, go to The Replicator Troubleshooting page on MakerBot.com Table of Contents This troubleshooting page is for the MakerBot Thing-O-Matic. For help with The Replicator, go to The Replicator Troubleshooting page on MakerBot.com Basic Rules TESTING Here is the basic method for testing your bot to make sure that you're OK to print. ASSEMBLY Read the instructions. Sanding parts. X/Y Axes Alignment Tape your nuts! ELECTRONICS/FIRMWARE "I'm having trouble connecting to my Motherboard. I continue to get the 'Null version reported!' error." Connect to the Internet while using ReplicatorG right before updating board firmware Calibrate your Stepper Driver Boards "My Thermocouple / Heater Board Thermistor reads '1024'" No matter what I do, I cannot get my Power Supply Unit to turn on! SOFTWARE / REPLICATORG "Where do I get the software I need to run my bot/slice my models?" "What software can I use to create models?" Where can I get models? "I'm uploading a model to my SD card — why is this taking so long?" "My copy of ReplicatorG is not behaving as described elsewhere in the wiki — cannot generate G-code or gives file access errors." PRINTING I just started my first print, and my toolhead started printing above the platform! One of my Thing-O-Matic's X, Y, or Z axes is moving twice as far as I want it to! My model will not stick to the platform The corners of the raft curl up, or the part curls. -
Opensource 3D Printing
4D Minus 1D Printer Assembly and Maintenance Manual Opensource 3D Printing Iain Letourneau Nathaniel Hupman Mathias Gossen 1 Table of Contents Preparation Section 1 Page 3 Z-Stage Section 2 Page 15 X and Y-Stage Section3 Page 20 Stepstruder (MK7) Section 4 Page 41 Safety Cutoff Section 5 Page 75 Body Section 6 Page 87 Electronics Installation Section 7 Page 122 Update the Firmware Section 8 Page 155 Quick-Start Guide Section 9 Page 162 Proper Belt Tensioning Section 10 Page 183 Testing Your Bot Section 11 Page 185 How to Print Section 12 Page 197 Maintenance and Upkeep Section 13 Page 210 Fine Tuning & Calibration Section 14 Page 212 How to Print Raftlessly Section 15 Page 226 Troubleshooting your Thingomatic Section 16 Page 229 2 Section 1 Preparation Before we start building, we need to do a few things to make the process go a bit more smoothly. Follow the instructions on this page closely, because this will make the whole process easier. Documentation First step: read the documentation, so nothing is unexpected. Read it all the way through, from beginning to end, before you start putting anything together. Then, go ahead and start following the instructions on this page, followed by each of the other build steps. Software First off, we’ll gather and install the software and drivers required for the Thing-O-Matic to work with your computer. Kit Contents Open box and separate contents into piles. Make sure that you keep everything well-organized; there’s nothing worse than losing a small but essential part! Tools Most of the tools needed for assembling a MakerBot Thing-O-Matic are included with the kit, but there are a few other common tools you’ll need. -
Um Modelador 3D Paramétrico Para CAD Yorik Van Havre
F r e e C A D Um modelador 3D paramétrico para CAD Yorik van Havre FISL 13, julho de 2012 ● Tuitem com #FreeCAD ● Interrompam quando quiserem ● PDF desta palestra disponível em http://yorik.uncreated.net ● Esta apresentação é vergonhosamente copiada de uma palestra de Ryan Gordon Yorik van Havre ● Arquiteto (de verdade, daqueles que fazem prédios), artista 3D, desenvolvedor do FreeCAD ● http://yorik.uncreated.net ● [email protected] ● @yorikvanhavre FreeCAD ● Plataforma para CAD (Desenho Assistido por Computador) ● Totalmente aberta (licença LGPL) ● Multiplataforma (Windows, Mac, Linux, BSD) ● http://free-cad.sourceforge.net A interface: http://free-cad.sourceforge.net A problemática do CAD: ● Refém de 4 ou 5 mega-empresas ● Tecnologias e conceitos evoluem muito rapidamente ● Setor muito pequeno ● Quase nenhum padrão aberto O propósito do CAD (e do FreeCAD) é poder fabricar os modelos: ● via CNC, ● impressão 3D, ● por equipe de pedreiros Precisamos de dimensões exatas, e noção de volume (diferente dos modelos para games ou animação). O que era CAD 15 anos atrás: O que é CAD hoje: O que é CAD hoje: O que é CAD hoje: O que é CAD hoje: ● Não é mais desenho, é modelagem ● Nos raros casos onde ainda precisa de desenhos, estes são produzidos automaticamente ● Os modelos servem para muitas outras coisas antes da fabricação, como cálculos ou simulações. Fabricação direta ( CNC): Impressão 3D: Simulações: Geração automática de desenhos: FreeCAD, o projeto: ● Iniciado em 2002 por 2 engenheiros alemães, Jürgen Riegel e Werner Mayer ● Hoje: 10 a 15 desenvolvedores, 3 a 4 commits por dia, comunidade ativa e entusiasta, primeiros passos no mundo profissional FreeCAD, o projeto: FreeCAD: psi13art.. -
A Practical Approach to the Design and Implementation of a Low Cost 3D Printer Using Open Source Technologies
Scientific Bulletin of the „Petru Maior” University of Tîrgu Mureş Vol. 14 (XXXI) no. 2, 2017 ISSN-L 1841-9267 (Print), ISSN 2285-438X (Online), ISSN 2286-3184 (CD-ROM) A PRACTICAL APPROACH TO THE DESIGN AND IMPLEMENTATION OF A LOW COST 3D PRINTER USING OPEN SOURCE TECHNOLOGIES Stelian-Emilian OLTEAN “Petru Maior” University of Tîrgu-Mureș, Romania Nicolae Iorga Street, no.1, 540088 Tîrgu-Mureș, Romania [email protected] Abstract The process of manufacturing parts with additive technologies has seen tremendous growth in recent years, and the emergence of more 3D open source printers has led to complex and personalized shapes at a lower price. For these reasons, 3D printers that form parts by extruding a filament of molten plastic are becoming standard equipment in many laboratories and workshops. In this context, the paper aims to present some theoretical aspects about the implementation and testing of a low cost 3D printer using open source technologies, the description of its main components and the stages to be taken from the 3D modelling of an object to the proper printing. Key words: 3D printing, additive manufacturing, rapid prototyping, open source technologies 1. Introduction range from $1,000 to $500,000, or even more In order to meet the technical demands of correlated with printing output and quality. Among customers who need products of complex shapes, but the most successful industrial printers are Objet made in a smaller number of items with a lower Eden260VS, ProJet 3500 HDMax, Objet260 production costs, mini CNC (Computer Numerical Connex3, EOSINT P 760 [11,12]. -
1 from Drawing to CNC: Overview
1 From Drawing to CNC: overview Gcode Motor Step motors CAD CAM interpreter driver (mill, lathe...) LinuxCNC = Emc2 or GRBL Arduino board FreeCAD HeeksCNC LibreCAD FreeCAD (*) HeeksCAD (*) FreeCAD CAM is currently being developed, will probably be very performant when ready HeeksCNC is working fine, but development is stagnating (state 5.2017) 2 SOFTWARE: CAD FreeCAD 2D, 3D, Free, Open Source https://freecadweb.org/ LibreCAD Free, Open Source http://librecad.org/cms/home.html HeeksCAD 2D, 3D, Free for Linux, Open source https://sites.google.com/site/heekscad/home Inkscape CAM FreeCAD Path module (under development!) https://freecadweb.org/ HeeksCAD / HeeksCNC included in HeeksCAD https://sites.google.com/site/heekscad/home BlenderCAM http://blendercam.blogspot.lu/ dxf2gcode can be integrated in LinuxCNC https://sourceforge.net/projects/dxf2gcode/ pyCAM (sleeping??) http://pycam.sourceforge.net/ CAMBAM (free up to 1000 lines G code) CAMmill not really documented http://cambam.info/ PCB CAM pcb2gcode converts gerber files to gcode https://sourceforge.net/projects/pcb2gcode/ FlatCAM converts gerber files to gcode http://flatcam.org/ CAM CAMotics Allows simulation of what the Gcode does http://www.camotics.org/ Simulation Info about other simulators: https://www.shapeoko.com/wiki/index.php/Previewing_G-Code G code LinuxCNC Real time operating system for CNC (on PC) http://linuxcnc.org/ interpreter GRBL - Arduino Arduino with GRBL Firmware https://github.com/grbl/grbl/wiki My favorites are marked in bold. All the software listed is free and Open Source and available for Linux 3 CAD FreeCAD Is for 2D and 3D drawing, is under heavy development and very promising. There are a lot of good tutorials to be found. -
Fabrication of Low Cost CNC Engraving Machine
6 IV April 2018 http://doi.org/10.22214/ijraset.2018.4794 International Journal for Research in Applied Science & Engineering Technology (IJRASET) ISSN: 2321-9653; IC Value: 45.98; SJ Impact Factor: 6.887 Volume 6 Issue IV, April 2018- Available at www.ijraset.com Fabrication of Low Cost CNC Engraving Machine Dhairya R. Patel1, Chirag B. Prajapati2, Porwal Sarthak R.3, Prajapati Swapnil V4, Krunal Parikh5 1, 2, 3, 4, 5Department of Mechanical Engineering Indus Institute of Technology and Engineering, Rancharda, Gujarat, India. Abstract: When the name of CNC comes up the first thing that comes in our minds is that high degree of surface finish can be achieved but also at a higher cost. Most of the conventional CNC machines available in the market are very costly. But there is an alternative available to us in the market. Micro-controllers, nowadays are becoming very famous because at a reasonable cost we can achieve a remarkable similarity in the working and operation as in comparison to the big sized controllers. Micro- controller namely the Arduino and GRBL coupled system can operate the tool with such intricacy that we can even sometimes not achieve with the conventional CNC machine. There is one more advantage of this kind of desktop CNC that very small work pieces can be machined which sometimes is not possible on larger size CNC. I. INTRODUCTION In the modern CNC machines, all the work is carried in integration to the computers hence it is a fully computer integrated mechanism. In order to achieve a computer integrated manufacturing various software are required which work in integration with the machine and the computer.