DEVELOPMENT of SMART PAINTING MACHINE USING IMAGE PROCESSING Atif Saeed Faculty, Department of Mechatronics Engineering, SZABIST, (Pakistan)
Total Page:16
File Type:pdf, Size:1020Kb
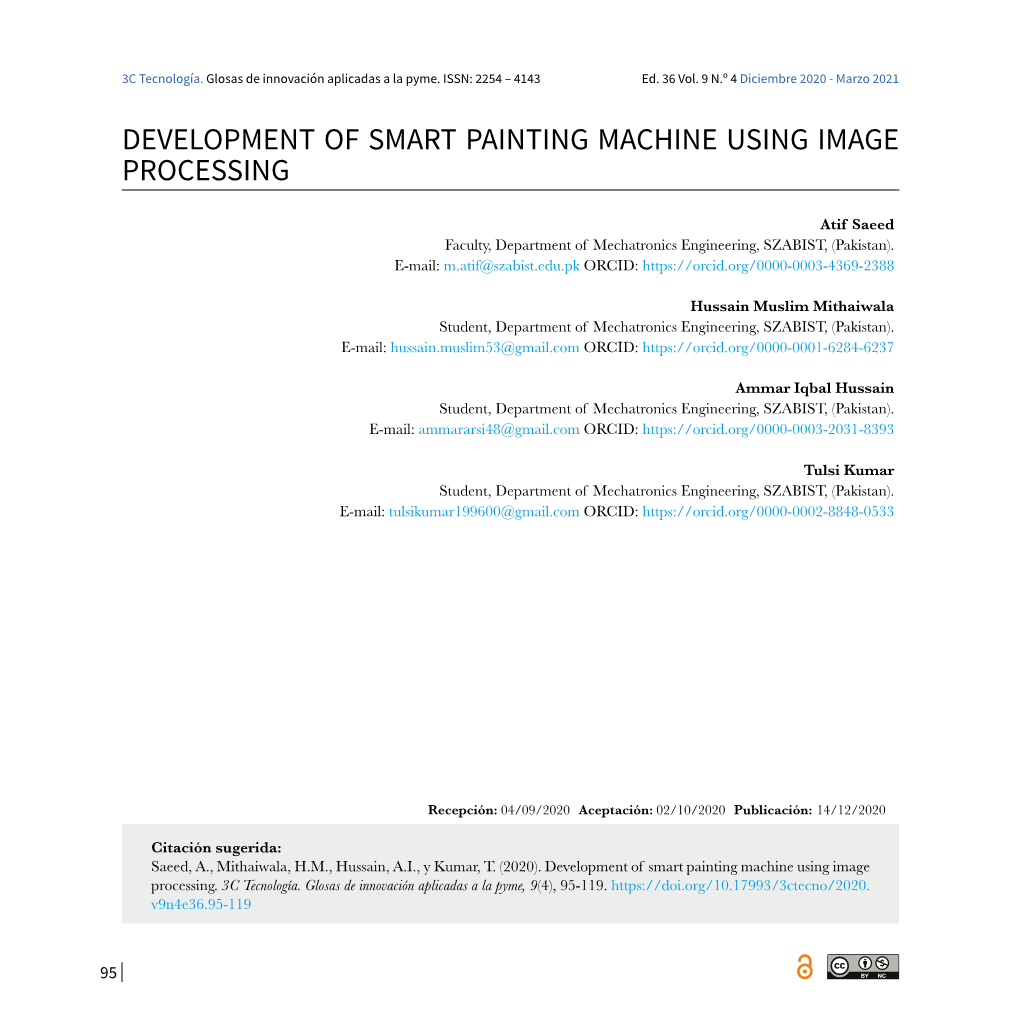
Load more
Recommended publications
-
Six DOF Spray Painting Robot Analysis
ISSN (Print) : 2320 – 3765 ISSN (Online) : 2278 – 8875 International Journal of Advanced Research in Electrical, Electronics and Instrumentation Engineering (An ISO 3297: 2007 Certified Organization) Vol. 4, Issue 9, September 2015 Six DOF Spray Painting Robot Analysis Om Prakash Gujela1, Vidhatri Gujela2, Dev Prakash Gujela3 Asst. Professor, Dept. of Electrical Engineering, SHIATS, Allahabad, India1 Asst. Professor, Dept. of Electrical & Electronics Engineering, HMFA Memorial Institute of Engineering & Technology, Allahabad, India2 External Assessor, TUV SUD South Asia, Delhi, India3 ABSTRACT: Today, different kinds of robots are being used in many fields. Especially in industries, robots are essential. One application in the industries is spray painting task which is no more suitable for human workers because it have large effect on health. Also the spray painting is a challenging task and need significant skill. Thus, spray painting robot are using wider and wider. This paper represents the analysis of a spray painting robot. Calculations and analysis are made to get the position and orientation of end effector. Also the spray painting patch and angles of each joint are calculated in this analysis. Position and orientation of end effector are analysed by forward kinematic. The angles of each joint are find out by inverse kinematic. Denavit- Hartenberg (D-H) methods are used in forward and inverse kinematic. Spray painting patch is generated by finding the equation of the surface of regular shape work-piece. Measurement and observation of robot are made on SolidWorks software. In this analysis, the calculation is quite complex and containing many variables even in an element of a matrix. Such kind of long equations are simplified by using MATLAB software. -
A Century of ABB Review
W ABB 2 |14 review en 100 years of ABB Review 7 40 years in robotics 24 60 years of HVDC 33 Boundaries of knowledge 68 The corporate technical journal A century of ABB Review Dear Reader, Technological innovation has been the cornerstone of ABB’s success since the founding of our predecessor companies in the late 19th century. Today, we invest $1.5 billion each year in R&D and we have 8,500 technologists focused on power and automation innova- tions around the world. For 100 years, ABB Review has been keeping our shareholders, customers and employees informed about our innovative solutions and achievements in the areas of power and auto- mation. Just like ABB, ABB Review is continually innovating in terms of content and design. The next phase of ABB Review will be to strengthen its pres- ence online to meet the oppor - tunities and demands of the digital world, for instance through more interactive communication. We are proud to share our centenary issue with you. Ulrich Spiesshofer Chief Executive Officer ABB Group 2 ABB review 2|14 Contents 7 100 years of ABB Review Centenary Looking back on a century in print 21 Editors’ picks celebration Treasures from the archives 24 Rise of the robot Perpetual Celebrating 40 years of industrial robotics at ABB 33 60 years of HVDC Pioneering ABB’s road from pioneer to market leader 42 Pumping efficiency Knowledge to A 100 MW converter for the Grimsel 2 pumped storage plant power 48 Unit of power Cutting-edge motor design redefines power density 54 Multitalented ACS800 power electronics can do more than rotate a motor 58 Hot spot Power A new infrared sensor measures temperature in generator circuit breakers is knowledge 65 At a higher level A medium-voltage-level UPS for complete power protection 68 Boundaries of knowledge Knowledge of boundary conditions is crucial for reliable simulations 74 Pushing the limits Turbine simulation for next-generation turbochargers Contents 3 Editorial 100 years of ABB Review Dear Reader, History often holds the key to understanding taking up the IRB 6’s anthropomorphic the present. -
Automated Systems Training at M-TEC
AUTOMATED SYSTEMS TRAINING AT THE M-TEC Macomb Community College’s Michigan Technical Education Center (M-TEC) is the College’s headquarters for its engineering and advanced technology workforce and continuing education team. The M-TEC is a 40,600-square-foot facility providing education and training in advanced integrated manufacturing, automated systems and robotics. We work across multiple industry sectors and in collaboration with employers to develop and deliver customized solutions addressing the technical talent pipeline at every level of an organization or industry sector. A $2.6 million investment by the Department of Labor, Michigan’s Community College Skilled Trades Equipment Program and the College has funded a major upgrade of the facility, advancing its capabilities in advanced integrated manufacturing, automated systems and robotics. M-TEC offers training on the latest industry-specific equipment in body- shop, paint, general assembly and powertrain. These Open Enrollment courses provide a way for companies to get the in-demand training they require in the most cost effective way. This is just a small part of what we do. There are many more training courses available so if you don’t see what you need, please ask! We specialize in customized training that meets your specific need. Equipment Summary FANUC Robot Cells with Weld Controllers FANUC Robotics Paint Cell FANUC Robot Cell with Nordson Sealant System FANUC Fenceless CERT Carts with iRVision ABB Portable Robotic Work Cells with RFID and Conveyor Siemens S7/TIA -
Development of Autonomous Wall Painting Robot Using Raspberry Pi and Image Processing
Special Issue - 2020 International Journal of Engineering Research & Technology (IJERT) ISSN: 2278-0181 IETE – 2020 Conference Proceedings Development of Autonomous Wall Painting Robot using Raspberry Pi and Image Processing Nayana C G Mamatha D Assistant Professor, Dept. of TCE, GSSSIETW Dept. of TCE, GSSSIETW, Mysuru Mysuru Nandini M Nandini S Dept. of TCE, GSSSIETW Dept. of TCE, GSSSIETW Mysuru Mysuru Abstract-This paper describes development of Automatic Wall II. PROBLEM STATEMENT Painting Robot prototype which helps to achieve low cost Painting is often tedious, repetitive work, as well as painting equipment. It would offer the opportunity to reduce being time-consuming work which in turn costs money. or eliminate human exposure to difficult and hazardous Also, workers risk exposure to harmful toxins. In addition environments, which would solve most of the problems to the fact that manual painting, paint guns depend mostly connected with safety when many activities occur at the same time.The system performs the painting process by the use of on human precision, when compared to automated spraying image captured by the pi camera. The painting area is lacks consistency. Manual wall painting is repetitive, time- calculated and information is transferred to the spray gun. consuming, physically exhaustive, and dangerous [1] [2]. The painting is done using bound box. Raspberry pi module Spray painting robot is an important advanced paint will control the base DC motors and the actuator. The production equipment, which is widely used in the paint actuator while extending and retracting raises the scissor lift production line of automotive and other products at home and lowers it, respectively. -
Spray Painting Robots
SHOWCASE:Robotic Painting Spray Painting Robots Robots for a variety of coating applications are featured on the following pages . Four Robots in One The New Technol- ogy Hydraulic (NTH) finishing system has 360.deg capability with six degrees of arm freedom for a work envelope that allows one robot to do the work of four. The work envelope features a complete overlapping torus with a majar diam- eter of 206 ft. The system covers a 32-ft radius, and the trans- porter has vertical motion to 6.5 ft. Payload is 10 Ibs at ful1 speed, ful1 accel- eration and ful1 accu- racy. Main-axis speed is 90 deg per sec and main-axis acceleration is 150 to 220 The NTH robot has a remote station for deg per sec. programming without downtime. S~UJ-ce: Kremlin, Inc., Addison, Illinois. For more data circle 270 on Postpaid Card 120 PRODUCTS FINISHING JIJNE, 1992 Quality and Consistency Model EE 10 all-electric paint- ing robot is Factory-Mutual ap- proved for spray painting. Pay- load is 22 Ib, and the robot operates at speeds to 6.5 ft per sec. Repeatability is kO.02 inch, providing for a consistent qual- ity finish. Sour-ce: Kawasaki Robotics, Farmington Hills, Michigan. For. morc data circle 271 011 Postpuid CUTd Painting a Variety The P-155 six-axis, electric paint robot for automotive and non-automotive coating appli- cation applies primers, topcoats, underbody deadener, anti-chip, camouflage and other paint materials. The P-155 retains the wrist and outer arm of the company’s P- 150 robot along with the cast- aluminum construction, AC servo drive, precision ground and hardened gears and sealed construction. -
D8.2 Stakeholder Analysis and Mapping
REMODEL - Robotic tEchnologies for the Manipulation of cOmplex DeformablE Linear objects Deliverable 8.2 – STAKEHOLDER ANALYSIS AND MAPPING ___________________________________________________________________ Version 2020-10-31 Project acronym: REMODEL Project title: Robotic tEchnologies for the Manipulation of cOmplex DeformablE Linear Grant Agreement No.: 870133 ObjectsTopic: DT-FOF-12-2019 Call Identifier: H2020-NMBP-TR-IND-2018-2020 Type of Action: RIA Project duration: 48 months Project start date: 01/11/2019 Work Package: WP8 – Communication/Dissemination, Exploitation and Knowledge Management Lead Beneficiary: TECNALIA Authors: All partners Dissemination level: Public Delivery date: 31/10/2020 Project website address: https://REMODEL-project.eu Table of Contents 1 Executive Summary ....................................................................................................... 3 2 Introduction ..................................................................................................................... 4 3 Market analysis............................................................................................................... 5 1 Market sectors ............................................................................................................ 5 3.1 Sectorial applications ................................................................................................ 8 3.1.1 Automotive .................................................................................................................. 9 3.1.2 -
FANUC Robotics SYSTEM R-30Ia and R-30Ib Controller KAREL
FANUC Robotics SYSTEM R-30iAandR-30iB Controller KAREL Reference Manual MARRC75KR07091E Rev D Applies to Version 7.50 and higher © 2012 FANUC Robotics America Corporation About This Manual This manual can be used with controllers labeled R-30iAorR-J3iC. If you have a controller labeled R-J3iC,youshouldreadR-30iAasR-J3iC throughout this manual. Copyrights and Trademarks This new publication contains proprietary information of FANUC Robotics America Corporation, furnished for customer use only. No other uses are authorized without the express written permission of FANUC Robotics America Corporation. FANUC Robotics America Corporation 3900 W. Hamlin Road Rochester Hills, MI 48309-3253 The descriptions and specifications contained in this manual were in effect at the time this manual was approved. FANUC Robotics America Corporation, hereinafter referred to as FANUC Robotics, reserves the right to discontinue models at any time or to change specifications or design without notice and without incurring obligations. FANUC Robotics manuals present descriptions, specifications, drawings, schematics, bills of material, parts, connections and/or procedures for installing, disassembling, connecting, operating and programming FANUC Robotics’ products and/or systems. Such systems consist of robots, extended axes, robot controllers, application software, the KAREL® programming language, INSIGHT® vision equipment, and special tools. FANUC Robotics recommends that only persons who have been trained in one or more approved FANUC Robotics Training Course(s) be permitted to install, operate, use, perform procedures on, repair, and/or maintain FANUC Robotics’ products and/or systems and their respective components. Approved training necessitates that the courses selected be relevant to the type of system installed and application performed at the customer site. -
Design of Automated Image Injecting and Painting Robot
International Journal of Research and Review www.ijrrjournal.com E-ISSN: 2349-9788; P-ISSN: 2454-2237 Original Research Article Design Of Automated Image Injecting And Painting Robot S. Kalaimagal1, A. Arun Raja2 1II Year, M.E Embedded Systems Technologies 2Assistant Professor, M.E Embedded Systems Technologies, Sri Ramakrishna Engineering College, Coimbatore, India Corresponding Author: S. Kalaimagal Received: 27/04/2015 Revised: 14/05/2015 Accepted: 16/05/2015 ABSTRACT Wall painting is a repetitive, exhausting and hazardous process which makes it an ideal case for automation. There is a strong need for a mobile robot that can move to paint interior walls of residential buildings. In this paper, the conceptual design of an autonomous wall painting robot is described consisting of an arm that scans the walls. IR sensors are attached to the mobile platform and used to maintain a certain distance from the facing wall and to avoid collision with side walls. When settled on adjusted distance from the wall, the controller starts the painting process autonomously. The design objective is to satisfy the criteria of simplicity, low weight, low cost. Keywords: Construction, Wall Painting Robot, spray Painting, Building Automation, Safety. I. INTRODUCTION growing rapidly. But the labors in the Construction paint robots are still construction industry are not sufficient. This in use today but are of inferior quality and insufficient labor in the construction safety to the latest electronic offerings. The industry is because of the difficulty in the newest robots are accurate and deliver work. This automatic wall painting robot is results with uniform film builds and exact not designed using complicated components. -
Parks, Recreation and Greenways Master Plan
Vision Holly Springs Comprehensive Plan Chapter 3: Parks, Recreation and Greenways Master Plan Adopted: March 16, 2021 Holly Springs Parks, Recreation, and Greenway Trails Master Plan CHAPTER # - NAME TOWN OF HOLLY SPRINGS PARKS, RECREATION, AND GREENWAYS MASTER PLAN March 2021 ACKNOWLEDGMENTS Department of Parks and Recreation Additional members from other committees LeeAnn Plumer, CPRP - Parks and Recreation Director Van Crandall, Planning Board Matt Beard, AICP – Park Planner Joe Fuller, Tree Advisory Committee Adam Huffman - Assistant Director Julia Janosko, Tree Advisory Committee Tay Abebe, Mayor’s Youth Advisory Board Administration Faatimah Bell, Mayor’s Youth Advisory Board Randy Harrington - Town Manager J. Scott Chase - Assistant Town Manager Consultant Team Daniel Weeks - Assistant Town Manager McAdams Company, Design Lead Mayor and Town Council Rachel Cotter, RLA - Project Manager Dick Sears - Mayor Shweta Nanaker, RLA - Landscape Architect Dan Berry - Mayor Pro-Tem Garrett Jenkins - Designer + Graphics Specialist Christine Kelly - Councilmember Erich Melville - Greenway Planner Pete Villadsen - Councilmember Shaun McGrath - Councilmember PROS Consulting Dr. Aaron Wolff - Councilmember Leon Younger, President Steering Committee ETC Institute Jason Morado, President Recreation Advisory Committee Members Susan Smith, Chairperson Molly Sapienza, Vice-Chairperson Elizabeth Stone, Secretary H. Val Atkinson Stephen Brauer Christopher Cook Alice Reese Len Lloyd Jason Guetgemann Pete Villadsen, Town Council Representative Christine -
When and Why to Select Painting Robot
WHEN AND WHY TO SELECT PAINTING ROBOT If a company is seriously considering a robot for its painting operation, there are two questions to answer. Is a paint robot truly the right automation choice for the application? If so, how would a robot impact the painting system's overall design and operation? Spray painting methods are categorized into the three most common types: Manual. A human operator with a spray gun.Hard Automation. Spray guns affixed to stationary gun arms or systems such as reciprocators, spinning guns or two- or three-axis positioners.Robot. Generally a six- axis programmable device capable of complex arm and wrist motion. Many times a robot is suggested as the answer to a painting problem; however, this often happens without sufficient analysis of application requirements. Although robots are now faster, more flexible and easier to program, they are not the only or best solution for every application. Sometimes users are so fascinated with a robot that they do not examine whether their parts can be painted more quickly and inexpensively with a less exotic technique. Part Shape. Complex parts with recesses, curved surfaces and picture-frame-like qualities are great candidates for a robot. Others, such as flat sheet panels or those having simple geometry are handled easily with less expensive mechanisms. If keeping the spray gun normal to the part surface requires a great deal of articulation, then a robot is a consideration. Part Variety. The variety of part shapes and sizes bears greatly on how best to paint them. A low-volume job shop where no two painted parts are the same would be a poor location for a robot. -
Motion Planning of Multi-Robot System for Airplane Stripping Rawan Kalawoun
Motion planning of multi-robot system for airplane stripping Rawan Kalawoun To cite this version: Rawan Kalawoun. Motion planning of multi-robot system for airplane stripping. Robotics [cs.RO]. Université Clermont Auvergne, 2019. English. NNT : 2019CLFAC008. tel-02284448 HAL Id: tel-02284448 https://tel.archives-ouvertes.fr/tel-02284448 Submitted on 11 Sep 2019 HAL is a multi-disciplinary open access L’archive ouverte pluridisciplinaire HAL, est archive for the deposit and dissemination of sci- destinée au dépôt et à la diffusion de documents entific research documents, whether they are pub- scientifiques de niveau recherche, publiés ou non, lished or not. The documents may come from émanant des établissements d’enseignement et de teaching and research institutions in France or recherche français ou étrangers, des laboratoires abroad, or from public or private research centers. publics ou privés. Ecole´ doctorale no70: Sciences pour l’ingenieur´ THESE` pour obtenir le grade de docteur delivr´ e´ par l’ Universite´ Clermont Auvergne Specialit´ e´ doctorale “Electronique´ et Systemes”` present´ ee´ et soutenue publiquement par Rawan KALAWOUN le 26 Avril 2019 Motion planning of multi-robot system for airplane stripping Jury Nacim Ramdani, Professeur des universites,´ PRISME (Bourges) Rapporteur Philippe Fraisse, Professeur des universites,´ LIRMM (Montpellier) Rapporteur Fabrice Le Bars, Maˆıtre de conferences,´ Lab-STICC (Brest) Examinateur Ouiddad Labbani-Igbida, Professeur des universites,´ XLIM (Limoges) Examinatrice Youcef Mezouar, Professeur des universites,´ Institut Pascal (Aubiere)` Directeur Sebastien´ Lengagne, Maˆıtre de conferences,´ Institut Pascal (Aubiere)` Encadrant Universite´ Clermont Auvergne - SIGMA Clermont Institut Pascal, UMR 6602 CNRS/UCA/SIGMA Clermont, F-63171 Aubiere,` France Abstract This PHD is a part of a French project named AEROSTRIP, (a partnership between Pascal Institute, Sigma, SAPPI, and Air-France industries), it is funded by the French Government through the FUI Program (20th call). -
Painting Powerpac
ABB Robotics Operating manual Painting PowerPac Trace back information: Workspace RW 5-15-01 version a4 (not checked in) Published 2013-04-01 at 11:06:15 Skribenta version 1184 Operating manual Painting PowerPac Document ID: 3HNA019758-001 Revision: G © Copyright 2008-2013 ABB. All rights reserved. The information in this manual is subject to change without notice and should not be construed as a commitment by ABB. ABB assumes no responsibility for any errors that may appear in this manual. Except as may be expressly stated anywhere in this manual, nothing herein shall be construed as any kind of guarantee or warranty by ABB for losses, damages to persons or property, fitness for a specific purpose or the like. In no event shall ABB be liable for incidental or consequential damages arising from use of this manual and products described herein. This manual and parts thereof must not be reproduced or copied without ABB's written permission. Additional copies of this manual may be obtained from ABB. The original language for this publication is English. Any other languages that are supplied have been translated from English. © Copyright 2008-2013 ABB. All rights reserved. ABB AS, Robotics Discrete Automation and Motion N-4349 BRYNE Norway Table of contents Table of contents Overview .......................................................................................................................................... 7 Product documentation, M2004 ......................................................................................................