(10) Patent No.: US 8545646 B1
Total Page:16
File Type:pdf, Size:1020Kb
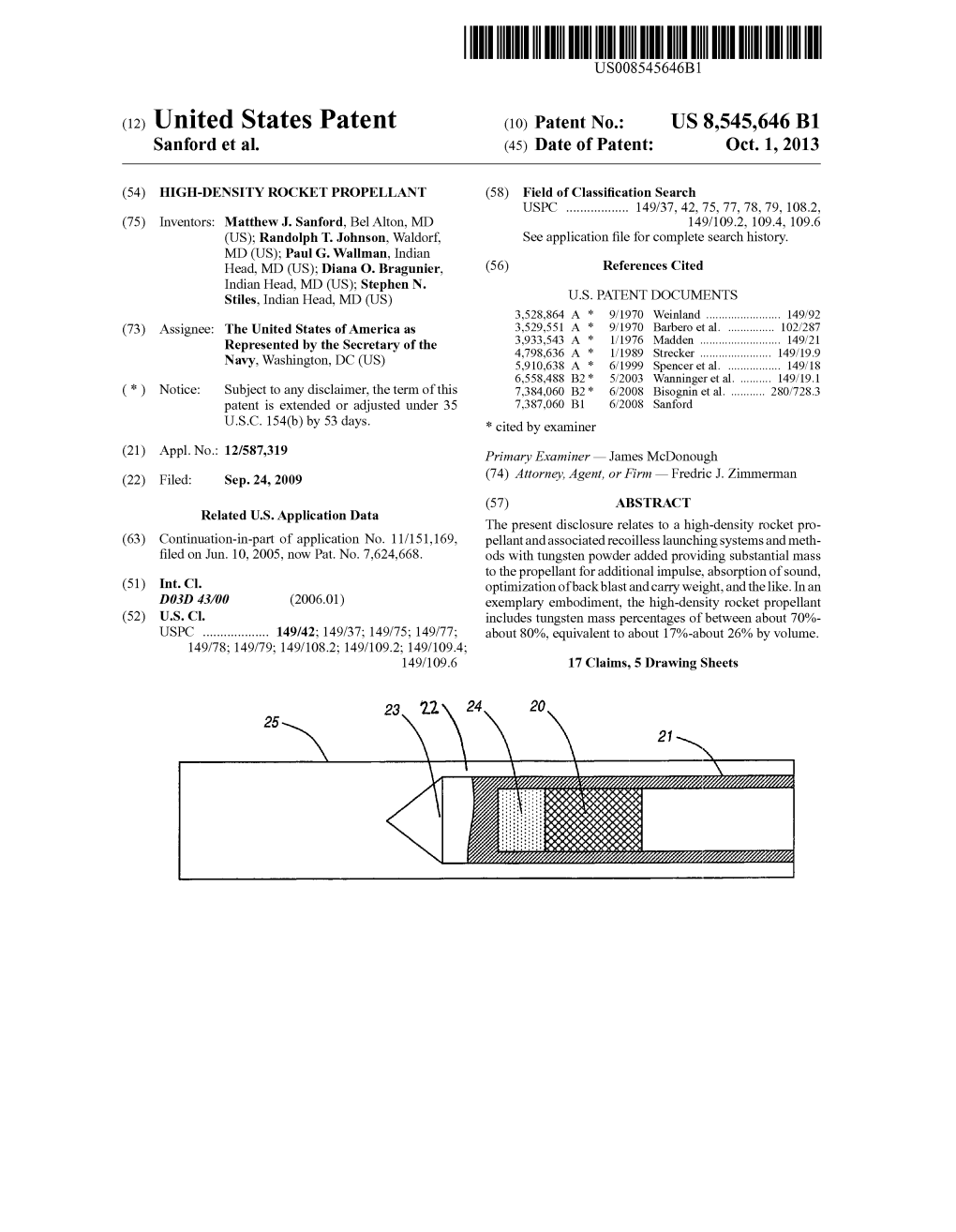
Load more
Recommended publications
-
Standards in Weapons Training (Special Operations Forces)
Department of the Army Pamphlet 350–39 Training Standards in Weapons Training (Special Operations Forces) Headquarters Department of the Army Washington, DC 3 July 1997 UNCLASSIFIED SUMMARY of CHANGE DA PAM 350–39 Standards in Weapons Training (Special Operations Forces) This revision-- o Deletes requirements for M72A2 light antitank weapon (LAW) (Chap 2). o Deletes requirements for ranger antiarmor-antipersonnel weapon system (RAAWS) (Chap 2). o Deletes requirements for Stinger crews (Chap 2). o Deletes requirements for mine warfare (Chap 2). o Deletes requirements for MGXX warfare (Chap 2). o Deletes requirements for CAR15 warfare (Chap 2). o Deletes requirements for Combat Training Center (CTC) (Chap 2). o Adds requirements for rocket propelled grenades (RPG) (Chap 3). o Adds requirements for close-quarters combat (CQC) (Chap 3). o Adds requirements for recoilless rifles (RCRL) 84-mm and 90-mm (Chap 3). o Adds requirements for Stinger crews (Chap 3). o Adds requirements for mortars 107-mm (Chap 3). Headquarters *Department of the Army Department of the Army Pamphlet 350–39 Washington, DC 3 July 1997 Training Standards in Weapons Training (Special Operations Forces) procedures for planning, resourcing, and exe- of Staff for Operations and Plans may dele- cuting training. It includes weapons qualifica- gate this authority, in writing, to a division tion standards, suggested training programs, chief within the proponent agency or a field and ammunition requirements for the attain- operating agency in the grade of colonel or ment and sustainment of weapons proficien- the civilian equivalent. c y . T h e p r o g r a m s i n c o r p o r a t e t r a i n i n g devices and simulators. -
Military Guide to Terrorism in the Twenty-First Century
US Army TRADOC TRADOC G2 Handbook No. 1 AA MilitaryMilitary GuideGuide toto TerrorismTerrorism in the Twenty-First Century US Army Training and Doctrine Command TRADOC G2 TRADOC Intelligence Support Activity - Threats Fort Leavenworth, Kansas 15 August 2007 DISTRIBUTION RESTRICTION: Approved for Public Release; Distribution Unlimited. 1 Summary of Change U.S. Army TRADOC G2 Handbook No. 1 (Version 5.0) A Military Guide to Terrorism in the Twenty-First Century Specifically, this handbook dated 15 August 2007 • Provides an information update since the DCSINT Handbook No. 1, A Military Guide to Terrorism in the Twenty-First Century, publication dated 10 August 2006 (Version 4.0). • References the U.S. Department of State, Office of the Coordinator for Counterterrorism, Country Reports on Terrorism 2006 dated April 2007. • References the National Counterterrorism Center (NCTC), Reports on Terrorist Incidents - 2006, dated 30 April 2007. • Deletes Appendix A, Terrorist Threat to Combatant Commands. By country assessments are available in U.S. Department of State, Office of the Coordinator for Counterterrorism, Country Reports on Terrorism 2006 dated April 2007. • Deletes Appendix C, Terrorist Operations and Tactics. These topics are covered in chapter 4 of the 2007 handbook. Emerging patterns and trends are addressed in chapter 5 of the 2007 handbook. • Deletes Appendix F, Weapons of Mass Destruction. See TRADOC G2 Handbook No.1.04. • Refers to updated 2007 Supplemental TRADOC G2 Handbook No.1.01, Terror Operations: Case Studies in Terror, dated 25 July 2007. • Refers to Supplemental DCSINT Handbook No. 1.02, Critical Infrastructure Threats and Terrorism, dated 10 August 2006. • Refers to Supplemental DCSINT Handbook No. -
U.S. Army Board Study Guide Version 5.3 – 02 June, 2008
U.S. Army Board Study Guide Version 5.3 – 02 June, 2008 Prepared by ArmyStudyGuide.com "Soldiers helping Soldiers since 1999" Check for updates at: http://www.ArmyStudyGuide.com Sponsored by: Your Future. Your Terms. You’ve served your country, now let DeVry University serve you. Whether you want to build off of the skills you honed in the military, or launch a new career completely, DeVry’s accelerated, year-round programs can help you make school a reality. Flexible, online programs plus more than 80 campus locations nationwide make studying more manageable, even while you serve. You may even be eligible for tuition assistance or other military benefits. Learn more today. Degree Programs Accounting, Business Administration Computer Information Systems Electronics Engineering Technology Plus Many More... Visit www.DeVry.edu today! Or call 877-496-9050 *DeVry University is accredited by The Higher Learning Commission of the North Central Association, www.ncahlc.org. Keller Graduate School of Management is included in this accreditation. Program availability varies by location Financial Assistance is available to those who qualify. In New York, DeVry University and its Keller Graduate School of Management operate as DeVry College of New York © 2008 DeVry University. All rights reserved U.S. Army Board Study Guide Table of Contents Army Programs ............................................................................................................................................. 5 ASAP - Army Substance Abuse Program............................................................................................... -
USMC Range Safety Pocket Guide V2.4
USMC Range Safety Pocket Guide Version 2.4 This portable guide provides references to MCO 3570.1C and DA PAM 385-63. It is not intended for use as a sole source of information for the MCO 3570.1C and/or DA PAM 385-63. For further information, consult the full versions of MCO 3570.1C and DA PAM 385-63. Surface Danger Zone templates included in this guide are shown at a scale of 1:25,000 and 1:50,000 and are for reference only. Range & Training Area Management Branch Training and Education Command 2300A Louis Rd. Quantico, VA 22134-5001 Send questions and comments to: [email protected] https://rtam.tecom.usmc.mil USMC Range Safety Pocket Guide Version 2.4 Table of Contents Summary ............................................................................................................................ 1 Purpose of this Pocket Guide ............................................................................................. 1 Excerpts from MCO 3570.1C, 30 January 2012 .................................................................. 1 Applicability ........................................................................................................................ 1 General .............................................................................................................................. 2 Other Military Services and/or agencies ............................................................................. 2 Danger Zones.................................................................................................................... -
Worldwide Equipment Guide
WORLDWIDE EQUIPMENT GUIDE TRADOC DCSINT Threat Support Directorate DISTRIBUTION RESTRICTION: Approved for public release; distribution unlimited. Worldwide Equipment Guide Sep 2001 TABLE OF CONTENTS Page Page Memorandum, 24 Sep 2001 ...................................... *i V-150................................................................. 2-12 Introduction ............................................................ *vii VTT-323 ......................................................... 2-12.1 Table: Units of Measure........................................... ix WZ 551........................................................... 2-12.2 Errata Notes................................................................ x YW 531A/531C/Type 63 Vehicle Series........... 2-13 Supplement Page Changes.................................... *xiii YW 531H/Type 85 Vehicle Series ................... 2-14 1. INFANTRY WEAPONS ................................... 1-1 Infantry Fighting Vehicles AMX-10P IFV................................................... 2-15 Small Arms BMD-1 Airborne Fighting Vehicle.................... 2-17 AK-74 5.45-mm Assault Rifle ............................. 1-3 BMD-3 Airborne Fighting Vehicle.................... 2-19 RPK-74 5.45-mm Light Machinegun................... 1-4 BMP-1 IFV..................................................... 2-20.1 AK-47 7.62-mm Assault Rifle .......................... 1-4.1 BMP-1P IFV...................................................... 2-21 Sniper Rifles..................................................... -
Army Developing Soldier Wearable Battery
!"#$%&'( *'2:'()%KTLL%%%U%%%%IJ&V@W%XX0%7J$%L !"#$%&'(()%*$%+,-.//0%(.1(.,.2#32"%#4.%5(6)%7'#382'/%9:'(;0%<'#=4.,%43,%>(32"%/'2.%?8(%#'(".#,%;:(32"%#4.%@A%='(-32.%('2".%B:'/3>='#382%.C.2#%8?%#4.%5(6)D,%E.,#%F'((38(% G861.#3#3820%4./;%82%H8(#%&..0%I'$0%J=#$%KL$%H8(%68(.%32?8(6'#382%'-8:#%#4.%@A%'2;%8#4.(%<.'182,0%,..%1'".%MN$%OP48#8%-)%!1=$%I.2.,,'%Q.(2'2;.RS !"#$"%&'"()*'+", !"()<7$9"='>%"5)$%&", " " -.$/.+0"1233"4"5)6'+$787$9"%&'":)+;' "?'@+/.+0"1233"4"A%)+7'B":+)<".+)/$6"%&'"C+<0 D$67.$."=.%7)$.E"F/.+6"A)E67'+B" 8?%E'##.()%50%K2;%E'##'/3820%LNT#4% ?7'E6"C+%7EE'+0"G'97<'$%H":7+'"%&'" 5III"&)J7%8'+".%"(.<K"C%%'+@/+0" -)7$%"5.$'/*'+"L+.7$7$9"('$%'+"7$" =.2#('/%+2;3'2'0%78C$%A$%Y4.%+2;3'2'% 9:'(;%3,%82.%8?%#4.%>(,#%,#'#.,%#8%-.% 7BB/'6"%&'B'"$'J"K7';'BM"?)+"<)+'" 7$:)+<.%7)$".@)/%"%&'"5IIINB"$'J" 1(8Z.=#3/.0%,..%1'".%MT$%OP48#8%-)% !"#$%*842%G(8,-)S !"#$"%&'()** )&*+,'&( !"#$%#$& ! !"#$%$&#' ( " )*+,-./.(!01(234 ( !" # 5/6(7,&"#.(8&9:-%(;/<$=>/ $% ?#@-#%,A(B8C(9&./,#$D-%$&# $& !$#$(,&:&%(%-E/'(&#(?FG' ( $' 8&9:-%(H/<$=>/' ( $( !"##$%&%$'()%#*+,-. !" &' CI4J(8&9:-%K*,&H/# &) /0&1%,2%)$3.#%'(,")-.(4+.#%, !" &( 4/-*&#'("*+,-./' ( '% LA'%/9'(%/=<#&>&+$/' ( '' )#9-##/.('A'%/9' ( )$ F#/,+A(-#.(+,//#(%/=<#&>&+$/' *+,-J((./01234-56/7530882/-59,++:2,; !" !"#"$%"&'"()*&+,-).)-/0+12/&&3&&456()"1%&2*7*8)$"&&&3&&&9:;;&<"##"1%5$&!*.)%&=>/&?&@5A&B;&&3&&&+16)$7-5$?&C+&&999D90BEDD&&&3& FGDBH&ID90DJGD&&&3&&!4K&&BB90DJGD&&&3&&L*A&&FGDBH&&ID90JB;M&&&3&&&N--OPQQ>>>R*12/R2)6Q%56()"1% !"#"$%" &"!'()(*+','+- !"#$%&'()*+ (.&-)/.0!1*+'0$ ,-.-$/012$3*4*5)6# !"#$"%&$'()*(%+"(,$-'( -
NSIAD-84-57 Department of the Army's Competitive Test And
*s*,’ ,I , UNITED STATES GENERAL ACCOUNTING OFFICE WASHINGTON, D.C. 20542 NATIONAL @tcUnlw *MO INTLRNATIONAL ACPAIRS DIVIIION FEWUARY 14. 1984 B-213544 The Honorable Warren B. Rudman United States Senate Subject: Department of the Army’s Competitive Test and Evaluation of Alternative Light Antiarmor Weapons (GAO/NSIAD-84-57) Dear Senator Rudman: We have reviewed the Army’s competitive test and evaluation of alternative light antiarmor weapons (LAWS) as requested in your letter of February 16, 1983. The test began on April 5, 1983, and was completed on July 27, 1983. Six types of LAWS were tested. After evaluating the test results and the price proposals provided by the weapon system’s contractors, the Army, on September 28, 1983, informed the Congress that it had selected a weapon developed in Sweden, the AT-4, for further testing. The Marine Corps, which is also seeking a light antiarmor weapon, chose the same weapon. The Army also submitted a report to the Congress containing the detailed test results. We (1) were on site throughout the full test cycle observ- ing the tests, (2) verified the recorded test results, and (3) reviewed the source selection data that the Army and Marine Corps used to select the winner. In our opinion, the test and evaluation were conducted objectively and the report provided to the Congress accurately reflected the test results. In selecting the AT-4 as the winner, the Army and Marine Corps have committed themselves only to further test the weapon, but not necessarily to procure it. They plan to perform a limited test of 36 AT-48, including 24 to be modified for defi- ciencies revealed in the portability test, before proceeding with a development and operational test of 1,000 rounds. -
SOCOM Shoulder Fired Weapons
SOCOM Shoulder Fired Weapons • HEAVY – JAVELIN •MEDIUM – MAAWS – FADW (AT4CS HP/RS) •LIGHT – LAW/LAW-CS USSOCOM SHOULDER FIRED WEAPON SYSTEMS OVERVIEW CURRENT NEAR TERM LONG TERM MULTI-ROLE ANTI- ARMOR MAAWS IR ANTI-PERSONNEL WEAPON LIGHTEN M3 GUN SYSTEM (MAAWS) CONFINED SPACE MAAWS ROUNDS: UPGRADED WARHEADS HE 441 HEAT 551 MULTI-TARGET HEDP 502 WARHEAD ADM 401 SMOKE 469 ILLUM 545 Technology Transfer AT4CS AT4CS AT4 AT4CS-RS NATO Multi-Target M72 LAW CS M72 A7 LAW With Improved Fuze MULTI-ROLE ANTI-ARMOR ANTI-PERSONNEL USER PAYOFF WEAPON SYSTEM (MAAWS) AMMUNITION CAPABILITIES HIGH EXPLOSIVE LIGHT ARMORED VEHICLES, • REUSABLE 22 POUND, 42 INCH 700M ANTI-TANK (HEAT) BRICK/CONCRETE WALLS LAUNCHER HIGH EXPLOSIVE EARTH & TIMBER BUNKERS, • FULL FAMILY OF AMMUNITION DUAL PURPOSE (HEDP) 500M SOFT STRUCTURES, WALLS TH • FIELDED TO 75 RR 1990, PERSONEL IN OPEN AND HIGH EXPLOSIVE (HE) 1000M NAVSPECWARCOM 1997 DEFILADE, SOFT VEHICLES CLOSE RANGE AREA AREA DETERRANT 100M SOCOM Work – Horse System MUNITION (ADM) PERSONNEL TARGETS OBSCURE AND SMOKE 1000M MARK TARGETS ILLUMINATION 1700M ILLUMINATE TARGETS ACQUISITION SUMMARY • USSOCOM PROGRAM • NDI SYSTEM FROM BOFORS, SWEDEN • EVOLUTIONARY SYSTEM UPGRADES TO ENHANCE SAFETY AND CAPABILITY • ACAT IV SYSTEM MANAGER AT RDECOM- ARDEC LEADS JOINT SERVICE IPT (ARMY/NAVY/SOCOM/OSD) CONTINUOUS SYSTEM UPGRADES MAAWS SYSTEM STATUS (EVOLUTIONARY ACQUISITION) WARHEAD EVALUATION ITEM (DODIC) FUZE MATERIAL STATUS M3 RECOILLESS RIFLE COMPLETE 553B SUBCALIBER ADAPTER COMPLETE 7.62mm TRAINING ROUND COMPLETE BACKBLAST -
Small Arms for Urban Combat
Small Arms for Urban Combat This page intentionally left blank Small Arms for Urban Combat A Review of Modern Handguns, Submachine Guns, Personal Defense Weapons, Carbines, Assault Rifles, Sniper Rifles, Anti-Materiel Rifles, Machine Guns, Combat Shotguns, Grenade Launchers and Other Weapons Systems RUSSELL C. TILSTRA McFarland & Company, Inc., Publishers Jefferson, North Carolina, and London LIBRARY OF CONGRESS CATALOGUING-IN-PUBLICATION DATA Tilstra, Russell C., ¡968– Small arms for urban combat : a review of modern handguns, submachine guns, personal defense weapons, carbines, assault rifles, sniper rifles, anti-materiel rifles, machine guns, combat shotguns, grenade launchers and other weapons systems / Russell C. Tilstra. p. cm. Includes bibliographical references and index. ISBN 978-0-7864-6523-1 softcover : acid free paper 1. Firearms. 2. Urban warfare—Equipment and supplies. I. Title. UD380.T55 2012 623.4'4—dc23 2011046889 BRITISH LIBRARY CATALOGUING DATA ARE AVAILABLE © 2012 Russell C. Tilstra. All rights reserved No part of this book may be reproduced or transmitted in any form or by any means, electronic or mechanical, including photocopying or recording, or by any information storage and retrieval system, without permission in writing from the publisher. Front cover design by David K. Landis (Shake It Loose Graphics) Manufactured in the United States of America McFarland & Company, Inc., Publishers Box 611, Jefferson, North Carolina 28640 www.mcfarlandpub.com To my wife and children for their love and support. Thanks for putting up with me. This page intentionally left blank Table of Contents Acronyms and Abbreviations . viii Preface . 1 Introduction . 3 1. Handguns . 9 2. Submachine Guns . 33 3. -
Reliable Intel Mission
Reliable Intel Mission The SEALs’ missions were varied, but a booby traps and foot falls in the pitch black exfiltrated toward a predetermined extrac- typical mission included seven SEALs op- of the night. tion point. Often this involved pursuing erating as a self-contained unit. The team enemy troops, so Claymore anti-personnel With their objective in sight, be it a included a medic, an M60 machine-gunner mines, grenades, and M60 firepower were communist leader or a demolition target, (or two), a radio man, and the rest of the used to help break contact. If all else failed, the patrol carefully and silently deployed squad. Typically a South Vietnamese inter- a quick call to the Seawolves would bring to cover all approaches and visual enemy pretor joined the patrol, making eight. All in a pair of gunships to intervene and tie contacts. Enemy pickets and scouts were wore camouflaged uniforms and painted up the enemy so the SEALs could reach neutralised with silenced pistols and knives. exposed skin in earth colours to help them their extraction vehicle, usually a boat or Then, they would unleash hell so quickly blend in with the jungle. helicopter. and fiercely that sometimes twenty enemy would be dead before they could fire back INSERTION in return. RELIABLE INTEL MISSION Patrols were inserted away from their target The following mission takes you on patrol and moved in, slowly and silently, to keep EXTRACTION with a SEAL squad. You’re deep behind the element of surprise. Point men were enemy lines with a mission to complete. -
Product Manager Excalibur Product Manager Mortars Systems
M1117 armored security vehicle tar weapon systems include the 60 mm, 81 mm and 120 mm mortars and related equipment. Fire-control systems, used to calculate mortar missions, include new, improved systems like the mortar fire-con- trol system-heavy (MFCS-H) and the light- weight handheld mortar ballistic com- puter (LHMBC). The M224 60 mm mortar weapon sys- tem is a lightweight, high-angle-of-fire, smooth-bore, manportable, muzzle-loaded mortar with improved rate-of-fire capabili- ties. The M224 consists of the following components: M225 cannon (tube), M170 bipod assembly, M7 baseplate, M8 auxil- tillery combat observation lasing teams Product Manager Excalibur iary baseplate and the M64A1 sight unit. (COLTs) in both heavy and Infantry brigade The Product Manager Excalibur (PM Ex- The M224 fires the complete family of 60 combat teams, the Armored Knight will calibur) is developing Excalibur, a preci- mm ammunition, such as high explosive, combine the proven armored security vehi- sion, autonomously guided, long-range ar- smoke, illumination, infrared illumination cle with the M707 Knight mission equip- tillery system. and practice cartridges. With ranges from ment package. The XM982 Excalibur is a 155 mm preci- 70 meters to 3,500 meters, the M224 meets The resultant M1200 Armored Knight sion-guided artillery round with extended lethality, range and weight requirements will provide COLTs with increased armor range. Already being fielded to warfight- for light forces without an additional trans- protection, payload and agility. Textron ers and successfully employed in combat portation requirement. Marine and Land Systems is presently un- operations, Excalibur uses GPS precision- The M252 81 mm mortar system is a der contract with the U.S. -
BICC Brief 7
brief 7 The New Field of Micro- Disarmament: Addressing the Proliferation and Buildup of Small Arms and Light Weapons september 96 brief 7 Contents Zusammenfassung German Summary 4 Abstract 5 About the Authors Background and Purpose 6 History, Definition and Evolution of Edward J. Laurance is Professor the Concept of Micro-Disarmament 7 of International Studies at the Monterey Institute of Typology of Light Weapons 10 International Studies in California. He has a Ph.D. in Internaional Production and Methods of Relations from the University of Accumulating Light Weapons 14 Pennsylvania. He has been consultant to the United Nations Negative Effects of Small Arms and Centre for Disarmament Affairs Light Weapons 16 since 1991, working on the UN Register of Conventional Arms Micro-Disarmament in Practice: and with the current UN Experts Situation and Scenarios 19 Panel on Small Arms. Policies, Tools and Instruments 24 Sarah Meek is program manager at the Program for Arms Control, Multilateral Action for Disarmament and Conversion, Micro-Disarmament 29 Monterey. An earlier version of this study Appendices was prepared by the Program for Arms Control, Disarmament and I. Current Projects on Light Weapons 31 Conversion, Monterey Institute of International Studies, and the II. Excerpt from Supplement to Bonn International Center for An Agenda for Peace 35 Conversion on behalf of the Foreign Office of the Federal III. Guidelines for Republic of Germany. International Arms Transfers in the Context of General Assembly Appendix I is based on BASIC's Resolution 46/36 H of listing of projects of light December 1991 37 weapons. Appendix VII is reproduced from Michael Klare IV.