Magneto Rheological Damper Requirements Document
Total Page:16
File Type:pdf, Size:1020Kb
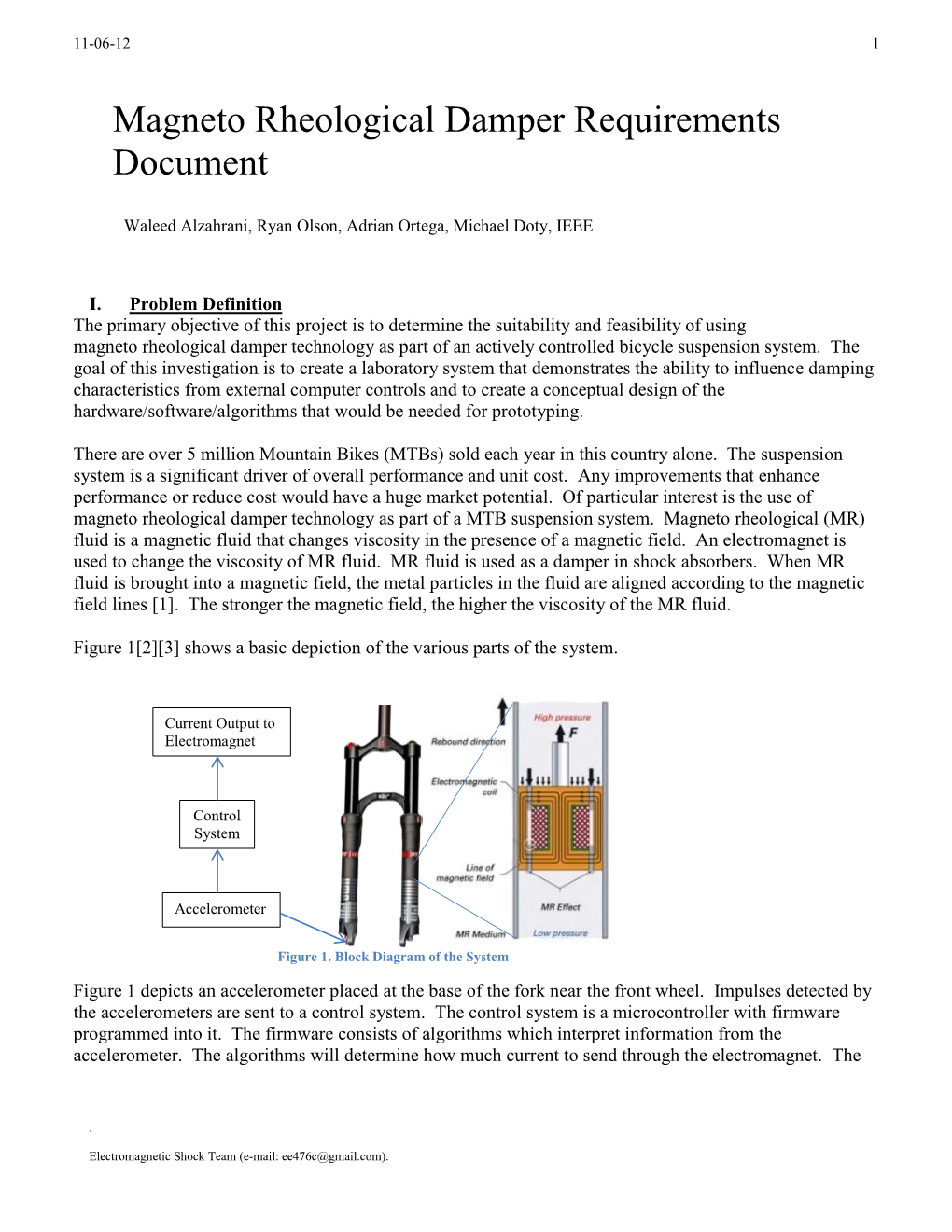
Load more
Recommended publications
-
Instructions for M-Xxxx-Xxxx
M-9602-M Spring and Stabilizer Bar Kit w/ MagneRide Calibration NO PART OF THIS DOCUMENT MAY BE REPRODUCED WITHOUT PRIOR AGREEMENT AND WRITTEN PERMISSION OF FORD PERFORMANCE PARTS Please visit www. performanceparts.ford.com for the most current instruction and warranty information. PLEASE READ ALL OF THE FOLLOWING INSTRUCTIONS CAREFULLY PRIOR TO INSTALLATION. AT ANY TIME YOU DO NOT UNDERSTAND THE INSTRUCTIONS, PLEASE CALL THE FORD PERFORMANCE TECHLINE AT 1-800-367-3788 M-9602-M is designed for 2018+ Mustangs equipped with MagneRide and includes a unique MagneRide calibration that is loaded with the included Procal voucher and software. Please reference the instruction tab on the Procal and make sure you use version 3.9+ Kit Includes: Front Stabilizer Bar Front Springs Rear Stabilizer Bar Rear Springs MagneRide Tuning Calibration Front Stabilizer Bar Removal NOTICE: Suspension fasteners are critical parts that affect the performance of vital components and systems. Failure of these fasteners may result in major service expense. Use the same or equivalent parts if replacement is necessary. Do not use a replacement part of lesser quality or substitute design. Tighten fasteners as specified. 1. Remove all 4 wheels and tires and set aside. 2. On both sides. 1. NOTE: The stabilizer bar links are designed with low friction ball joints that have a low breakaway torque. NOTE: Use the hex-holding feature to prevent the ball stud from turning while removing the stabilizer bar link nut. Remove and the front stabilizer bar link lower nut. 2. Position aside the front stabilizer bar link. Factory Ford shop manuals are available from Helm Publications, 1-800-782-4356 Techline 1-800-367-3788 Page 1 of 41 IS-1850-0631 M-9602-M Spring and Stabilizer Bar Kit w/ MagneRide Calibration NO PART OF THIS DOCUMENT MAY BE REPRODUCED WITHOUT PRIOR AGREEMENT AND WRITTEN PERMISSION OF FORD PERFORMANCE PARTS 4. -
Product Information Sheet Steering and Suspension System Trainer
Product Information Sheet Steering and Suspension System Trainer This real component trainer provides the instructor with a . Remove, inspect, and install coil springs and spring working light vehicle steering and suspension system for insulators. group or whole-class demonstration. Inspect, replace, and adjust track rod ends, track rod sleeves, and clamps. This includes all the individual components of the system . Remove, inspect, and install upper and lower wishbones, presented on a moveable, steel frame so that each bushes, shafts, and rebound bumpers. component can be clearly identified. Remove, inspect, and install hub carrier assemblies. Inspect, remove, and replace dampers. The system comprises front wheel assemblies, MacPherson strut and coil spring assemblies, road wheels and power Items Included: steering rack. Trainer (right-hand and left-hand drive options available) . The trainer can also be used in conjunction with our Other Items Required: optional cloud-based software, which offers online practical tasks as well as interactive theory presentations, . Automotive workshop tools investigations, and assessments, which link directly to the . AC supply outlet (110V/230V options available) practical activities carried out using this resource. General Information: Trainer Enables Demonstrations of the Following: Trainer Dimensions (W x D x H): . Introduce the steering and suspension system trainer. 1750 x 1250 x 1500 mm / 69 x 49 x 59 inches . Inspect steering shaft universal joint, flexible coupling, Packed Volume: Approx. 3.67m3 / 130ft3 collapsible column, lock cylinder mechanism, and Packed Weight: Approx. 360kg / 795lb steering wheel. Packed Dimensions (W x D x H): . Disassemble, inspect, and reassemble rack and pinion 1904 x 1244 x 1550 mm / 75 x 49 x 62 inches steering gear. -
Active Suspension Control of Electric Vehicle with In-Wheel Motors
University of Wollongong Research Online University of Wollongong Thesis Collection 2017+ University of Wollongong Thesis Collections 2018 Active suspension control of electric vehicle with in-wheel motors Xinxin Shao University of Wollongong Follow this and additional works at: https://ro.uow.edu.au/theses1 University of Wollongong Copyright Warning You may print or download ONE copy of this document for the purpose of your own research or study. The University does not authorise you to copy, communicate or otherwise make available electronically to any other person any copyright material contained on this site. You are reminded of the following: This work is copyright. Apart from any use permitted under the Copyright Act 1968, no part of this work may be reproduced by any process, nor may any other exclusive right be exercised, without the permission of the author. Copyright owners are entitled to take legal action against persons who infringe their copyright. A reproduction of material that is protected by copyright may be a copyright infringement. A court may impose penalties and award damages in relation to offences and infringements relating to copyright material. Higher penalties may apply, and higher damages may be awarded, for offences and infringements involving the conversion of material into digital or electronic form. Unless otherwise indicated, the views expressed in this thesis are those of the author and do not necessarily represent the views of the University of Wollongong. Recommended Citation Shao, Xinxin, Active suspension control of electric vehicle with in-wheel motors, Doctor of Philosophy thesis, School of Electrical, Computer and Telecommunications Engineering, University of Wollongong, 2018. -
You Auto Know New for 2018
You Auto Know 2018 Mustang Key Mustang Messages Mustang is designed to appeal to current enthusiasts as well as a new generation of drivers. Impressive features include its sleek design, advanced technology and performance, with two powerful engines and features like MagneRide Damping System Two engines, including the 5.0L Ti-VCT V8 and a 2.3L EcoBoost An all-new 10-speed automatic transmission Available Active Valve Performance Exhaust provides throaty Mustang sound or more aggressive rumble with the flip of a switch Available 12-inch LCD digital instrument cluster for customizable performance Impressive array of standard and available advanced technology features, including: ‒ SYNC Connect powered by FordPass and Wi-Fi® hotspot ‒ Light-emitting diode (LED) headlamps and foglamps ‒ Pre-collision Assist with Pedestrian Detection Several packages allow owners to add unique style to their Mustang Key Mustang Features 5.0L Ti-VCT V8 and 2.3L EcoBoost engines Active Valve Performace Exhaust 12" LCD digital instrument cluster Selectable drive modes MagneRide Damping System Launch control Innovative driver-assist technologies GT and EcoBoost Performance Packages NOTE: For product features, please see Models & Packages and/or the Dealer Ordering Guide for availability. New for 2018 New for 2018 2018 Mustang Features Performance/Handling Revised 2.3L EcoBoost and more powerful 5.0L Ti-VCT V8 All-new dual fuel delivery system, combines port fuel and direct injection to the 5.0 Ti-VCT V8 All-new 10-speed SelectShift automatic transmission Active -
Ride Control Defined
RIDE CONTROL DEFINED According to Newton's First Law, a moving body will continue moving in a straight line until it is acted upon by another force. Newton's Second Law states that for each action there is an equal and opposite reaction. In the case of the automobile, whether the disturbing force is in the form of a wind-gust, an incline in the roadway, or the cornering forces produced by tires, the force causing the action and the force resisting the action will always be in balance. Many things affect vehicles in motion. Weight distribution, speed, road conditions and wind are some factors that affect how vehicles travel down the highway. Under all these variables however, the vehicle suspension system including the shocks, struts and springs must be in good condition. Worn suspension components may reduce the stability of the vehicle and reduce driver control. They may also accelerate wear on other suspension components. Replacing worn or inadequate shocks and struts will help maintain good ride control as they: Control spring and suspension movement Provide consistent handling and braking Prevent premature tire wear Help keep the tires in contact with the road Maintain dynamic wheel alignment Control vehicle bounce, roll, sway, dive and acceleration squat Reduce wear on other vehicle systems Promote even and balanced tire and brake wear Reduce driver fatigue Suspension concepts and components have changed and will continue to change dramatically, but the basic objective remains the same: 1. Provide steering stability with good handling characteristics 2. Maximize passenger comfort Achieving these objectives under all variables of a vehicle in motion is called ride control 1 BASIC TERMINOLOGY To begin this training program, you need to possess some very basic information. -
Review on Active Suspension System
SHS Web of Conferences 49, 02008 (2018) https://doi.org/10.1051/shsconf/20184902008 ICES 2018 Review on active suspension system 2 Aizuddin Fahmi Mohd Riduan1, Noreffendy Tamaldin , Ajat Sudrajat3, and Fauzi Ahmad4 1,2,4Centre for Advanced Research on Energy, Universiti Teknikal Malaysia Melaka, Hang Tuah Jaya, 76100 Durian Tunggal, Melaka Malaysia. 1,2,4Faculty of Mechanical Engineering, Universiti Teknikal Malaysia Melaka, Hang Tuah Jaya, 76100 Durian Tunggal, Melaka, Malaysia. 3Engineering Physics, Faculty of Science and Technology, Universitas Nasional-Jakarta JL. Sawo Manila, Pasar Minggu, Jakarta 12520, Indonesia. Abstract. For the past decade, active suspension systems had made up most of research area concerning vehicle dynamics. For this review, recent studies on automobile active suspensions systems were examined. Several vehicular suspension types were also described to compare amongst them. From published investigations by previous researchers, various automotive suspensions in terms of cost, weight, structure, reliability, ride comfortability, dynamic and handling performance were exhibited and compared. After careful examination, it was concluded that electromagnetic active suspensions should be the general direction of vehicle suspension designs due to its energy regeneration, high bandwidth, simpler structure, flexible and accurate force control, better handling performance as well as drive characteristics. Keywords: Active Suspension, Handling Performance, Dynamic Performance 1 Introduction Vehicle suspension main task -
Design and Development of Multi-Link Suspension Suspension System
ISSN: 2455-2631 © June 2019 IJSDR | Volume 4, Issue 6 Design and Development of Multi-Link Suspension Suspension System 1Piyush Parida, 2Vaibhav Itkikar, 3Harshal Patil, 4Sandip Patil 1,2,3,4UG Students Mechanical Engineering Department G.H. Raisoni College of Engineering and Management, Chas, Ahmednagar, India Abstract: In order to provide a comfortable ride to the passengers and avoid additional stresses in motor car frame, the car should neither bounce or roll or sway the passengers when cornering nor pitch when accelerating. For this purpose the virtual prototype of suspension systems were built in software MSC ADAMS/CAR and suspensions for military truck were analyzed keeping in mind the optimization of suspension parameters. As there is tremendous development in Suspension Technology, Multi-Link suspension system are considered better independent suspension system among all other independent suspension system. Its simple design and construction makes it way more convenient to install and serve its purpose. As there is vast growth in Agriculture, farming becoming more and more advanced in terms of technology and in that transport vehicles play important role in making agriculture more productive. We saw different scenario where agriculture transport vehicles collapsing because of their conventional suspension system fails to stabalize the loaded vehicle on different road conditions. We tried to see the improvement in performance of vehicle in stabalizing itself by using Multi- Link suspension system. Keywords: Suspension, links, vibrations, Multi body dynamic analysis (MBD) 1. INTRODUCTION In heavy transport vehicle field existing dependent suspension system unit is used. If some have that is leaf spring suspension. In all cases Leaf spring design for full load condition. -
Automotive Service Modern Auto Tech Study Guide Chapter 67 & 69 Pages 1280 1346 Suspension & Steering 32 Points Automotive Service 1
Automotive Service Modern Auto Tech Study Guide Chapter 67 & 69 Pages 1280 1346 Suspension & Steering 32 Points Automotive Service 1. The ____________________ system allows a vehicle’s tires & wheels to move up and down as they roll. Steering Suspension Brake Automotive Service 2. Suspension can be grouped into 2 broad categories: _________________ & ________________. Independent & Nonindependent Coil Springs & Air Springs Active & Passive Automotive Service 3. The perfect suspension system balances understeer and oversteer, resulting in ______________ steering. Tight Neutral Loose Automotive Service 4. Compressing springs is known as ________. As springs extend, they are said to ________. Jounce, Rebound Bounce, Resound Dribble, Rebound Automotive Service 5. Springs can be one of 4 types: A. _________, B. __________, C. _________________ ______, & D. _______. Coil Leaf Air Torsion Bar Automotive Service 6. ______________ weight is all of the weight supported by the springs. __________________ weight is all of the weight not supported by the springs. The more sprung weight, the better the vehicle will ride. Spring, Unspring Sprang, Unsprang Sprung, Unsprung Automotive Service 7. Control arms are connected to the steering knuckles with pivoting joints called ___________ joints. Automotive Service Automotive Service 8. __________ ______________ limit spring oscillations (jounce & rebound), but don’t effect ride height Slack Absorbers Shock Absorbers Shock Restorers Automotive Service 9. ______ shocks are filled with low pressure nitrogen gas to prevent fluid aeration (bubble formation). Gas Water Air Automotive Service 10. Options on shock absorbers include the ___________________________ feature & adjustable stiffness. SelfLeveling SelfIgniting SelfEnergizing Automotive Service Automotive Service Automotive Service 11. A ______ assembly consists of a shock, coil spring & an upper damper/pivot bearing. -
Semi-Active Suspension
KYB TECHNICAL REVIEW No. 55 OCT. 2017 Glossary Semi-active Suspension Included in “The technical term used in Development of Externally-Mounted Shock Absorber with Adjustable Solenoid Damping Force” P. 25 ITO Naoki KYB TECHNICAL REVIEW editor 1 Semi-active Suspension Skyhook damper Cs (imaginary) Acceleration Speed Semi-active suspension is a type of automotive suspension systems that controls the damping force of the shock absorber in response to input from the continuously varying road surfaces. It is intended to approximately Cp: Damping coefcient of implement the active suspension (to be described later) passive damper with a damping force adjustable shock absorber Cs: Damping coefcient of Skyhook damper (hereinafter “SA”). Fcont: Controlling force M2: Sprung mass Semi-active suspension may be implemented by several M1: Unsprung mass types of control methodologies. A generally known typical K2: Suspension spring constant K1: Tire spring constant technology is Skyhook control. X0: Road surface variation X1: Unsprung variation Fig. 1 shows a Skyhook control model. An imaginary X2: Sprung variation damper (= Skyhook damper) hung from an aerial height with its end fi xed there is implemented by generating a Fig. 1 Skyhook control model force of the sprung (vehicle body) speed multiplied by the damping coeffi cient sC . A passive (= uncontrolled) damper 4th quadrant 1st quadrant (Cp), which is installed in parallel with the Skyhook damper (Cs), provides a force equivalent to the SOFT damping force of the damping force adjustable SA. When this damper model is given a random input from the road surface, the relationship between the required Contraction Expansion combined damping forces of the Skyhook and passive dampers, and the relative speed (piston speed) between the sprung and unsprung components (including tires) is Relative speed (m/s) shown in Fig. -
Steeda S550 Mustang Magneride Dual Rate Ultimate Handling
Steeda S550 Mustang MagneRide Dual Rate Ultimate Handling Lowering Springs Instructions for 555-8243 • A qualified technician should be used if you are not confident with removing and installing the vehicles front struts & springs. • A suspension coil spring compressor must be used to allow for replacement of the mount and/or coil spring. • Caution: Coil springs store a tremendous amount of energy. 1 Failure to properly remove and install the springs can lead to severe injury. • The vehicle will require an alignment following installation. • Refer to a service manual for fastener torque specifications and make sure to torque suspension components at curb. Front Spring Installation 1. Lift the car, by the chassis, on a vehicle lift or with a jack, and supported by jack stands, to work on the front suspension of the car. 2 2. Remove the front wheels. 3. Remove the ABS harness from the strut. 4. Disconnect the sway bar end link from the strut. 5. Remove the four bolts securing the brake caliper to the spindle and the spindle to the strut. See image 2. 6. Disconnect the MagneRide plug on the bottom of the strut. Remove 7. From under the hood, remove the 3 nuts securing the strut to the strut tower. The strut can now be removed. 8. Using a coil spring compressor, compress the front spring until there is no tension on the upper strut mount. Once the spring is safely secured, remove the nut holding down the upper strut mount. Then, separate the strut from the spring and the upper strut mount. -
Adaptive Semi-Active Suspension and Cruise Control Through LPV Technique
applied sciences Article Adaptive Semi-Active Suspension and Cruise Control through LPV Technique Hakan Basargan 1 , András Mihály 2, Péter Gáspár 2,* and Olivier Sename 3 1 Department of Control for Transportation and Vehicle Systems, Budapest University of Technology and Economics, M˝uegyetemrkp. 3, H-1111 Budapest, Hungary; [email protected] 2 Systems and Control Laboratory, Institute for Computer Science and Control, Kende u. 13-17, H-1111 Budapest, Hungary; [email protected] 3 GIPSA-lab, INPG, Université Grenoble Alpes, 11 Rue des Mathématiques, 38000 Grenoble, France; [email protected] * Correspondence: [email protected]; Tel.: +36-1-279-6171 Abstract: Several studies exist on topics of semi-active suspension and vehicle cruise control systems in the literature, while many of them just consider actual road distortions and terrain characteristics, these systems are not adaptive and their subsystems designed separately. This study introduces a new method where the integration of look-ahead road data in the control of the adaptive semi-active suspension, where it is possible to the trade-off between comfort and stability orientation. This trade-off is designed by the decision layer, where the controller is modified based on prehistorical passive suspension simulations, vehicle velocity and road data, while the behavior of the controller can be modified by the use of a dedicated scheduling variable. The adaptive semi-active suspension control is designed by using Linear Parameter Varying (LPV) framework. In addition to this, it proposes designing the vehicle velocity for the cruise controller by considering energy efficiency and comfort together. -
Vince Taliano
Cadillac & LaSalle Club Potomac Region Caddie Chronicle June 2016 DIRECTOR’S MESSAGE BY VINCE TALIANO 2016 OFFICERS: Thanks to the following Potomac Region REGIONAL DIRECTOR members who participated in the 12th Annual NEWSLETTER EDITOR National Memorial Day Parade in Washington, WEBSITE MANAGER VINCE TALIANO DC: Pete Sanders (1935 Ford convertible), ASSISTANT REGIONAL DIRECTOR Byron & Alida Alsop (1936 Cadillac Series 85 CAR SHOW COORDINATOR DAN RUBY V-12 convertible sedan), Harry Scott (1937 NATIONAL DIRECTOR Cadillac Series 75 convertible sedan), Daniel NEWSLETTER COLUMNIST Jobe (unable to attend but sent his 1946 JACK MCCLOW Cadillac Series 62 convertible) and Randy Denchfield (1976 SECRETARY ASSOCIATE NEWSLETTER EDITOR Cadillac Eldorado convertible). SANDY KEMPER TREASURER Congratulations to the members who won awards at the 2016 HARRY SCOTT ACTIVITIES DIRECTOR AACA Eastern Spring Meet in Vineland, New Jersey. The list NEWSLETTER COLUMNIST includes Randy Denchfield who won a 1st Senior Award in Class R. SCOT MINESINGER 19C for his 1935 LaSalle 50 Convertible R/S and Jerry Gordon MEMBERSHIP DIRECTORS CENTRAL VA REGION LIAISONS who won a Repeat Preservation in Class 27D for his 1961 Cadillac NEWSLETTER COLUMNISTS Sedan DeVille. Franklin Gage received a driver participation CHUCK & DEBBIE PIEL award for one of his Chevys. OTHER KEY POSITIONS: SUMMER PICNIC HOST J. ROGER BENTLEY The 2016 Grand National is over! But AUTOMOBILIA AUCTIONEER one of the largest GNs ever is fast GEORGE BOXLEY approaching. Ronnie Hux, Meet NEWSLETTER COLUMNIST RITA BIAL-BOXLEY Chairman, reports that the Potomac NEWSLETTER COLUMNIST Region and Valley Forge Regions are CHRIS CUMMINGS making progress daily to finalize all PHOTOGRAPHER RANDY EDISON of the exciting plans for the 2017 GN AUTOMOBILIA AUCTIONEER at the Hilton Hotel in Tyson's Corner.