Technological Evolution of Concrete: from Ancient Times to Ultra High-Performance Concrete
Total Page:16
File Type:pdf, Size:1020Kb
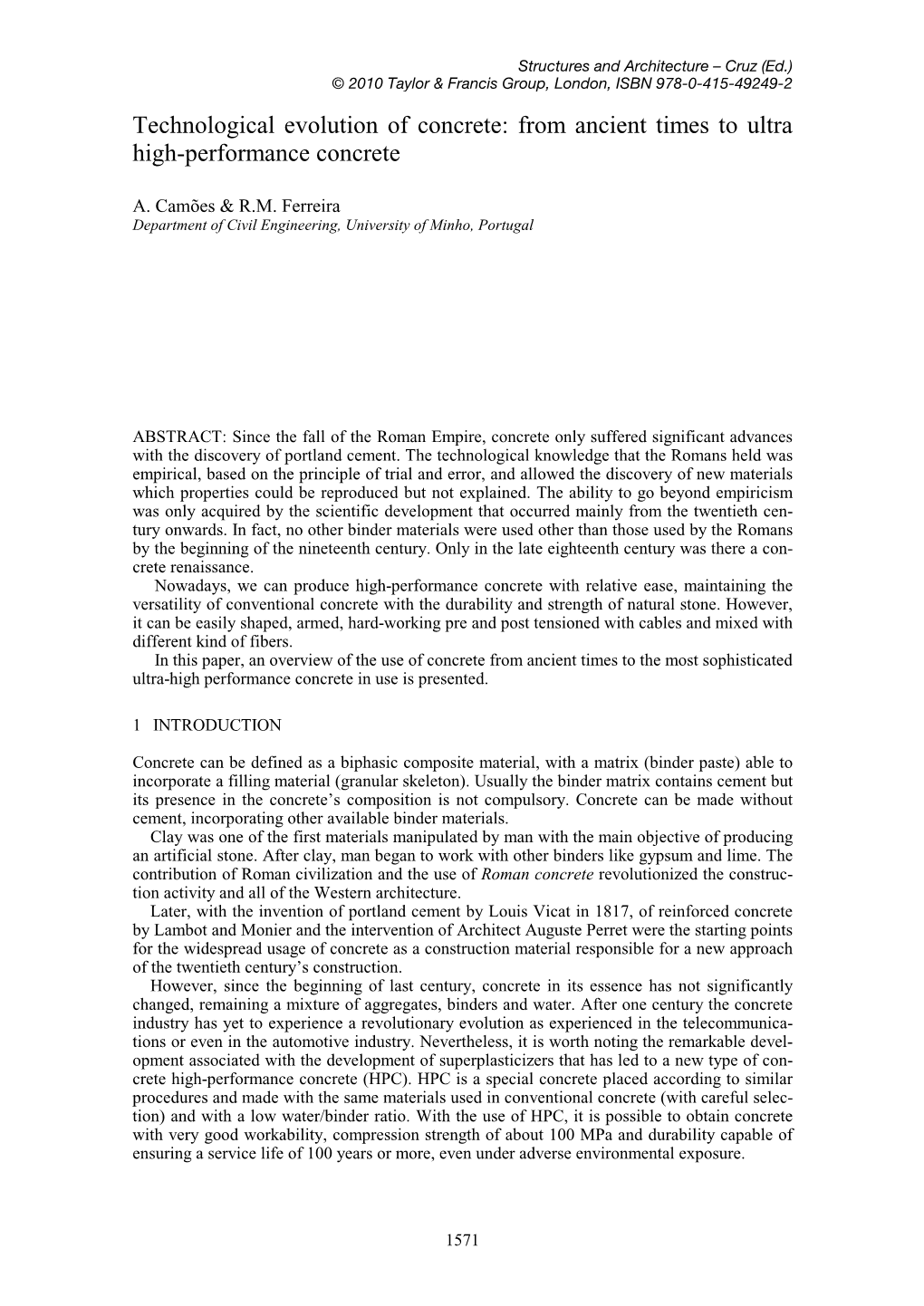
Load more
Recommended publications
-
Experimental Investigation on Nano Concrete with Nano Silica and M-Sand
International Research Journal of Engineering and Technology (IRJET) e-ISSN: 2395-0056 Volume: 06 Issue: 03 | Mar 2019 www.irjet.net p-ISSN: 2395-0072 EXPERIMENTAL INVESTIGATION ON NANO CONCRETE WITH NANO SILICA AND M-SAND Mohan Raj.B1, Sugila Devi.G2 1PG Student, Nadar Saraswathi College of Engineering and Technology, Theni, Tamilnadu, India. 2Assistant Professor, Nadar Saraswathi College of Engineering and Technology, Theni, Tamilnadu, India. ---------------------------------------------------------------------***--------------------------------------------------------------------- Abstract - The influence of Nano-Silica on various material is Nano Silica (NS). The advancement made by the properties of concrete is obtained by replacing the cement study of concrete at Nano scale has proved the Nano silica is with various percentages of Nano-Silica. Nano-Silica is used as much better than silica fume used in conventional concrete. a partial replacement for cement in the range of 3%, 3.5%, Now, the researchers are capitalizing on nanotechnology to and 10% for M20 mix. Specimens are casted using Nano-Silica innovate a new generation of concrete materials that concrete. Laboratory tests conducted to determine the overcome the above drawbacks and trying to achieve the compressive strength, split tensile and flexural strength of sustainable concrete structures. Evolution of materials is Nano-Silica concrete at the age of 7, 14 and 28 days. Results need of the day for improved or better performance for indicate that the concrete, by using Nano-Silica powder, was special engineering applications and modifying the bulk able to increase its compressive strength. However, the density state of materials in terms of composition or microstructure is reduce compared to standard mix of concrete. -
In This Study, Marcello Mogetta Examines the Origins and Early Dissemina- Tion of Concrete Technology in Roman Republican Architecture
Cambridge University Press 978-1-108-84568-7 — The Origins of Concrete Construction in Roman Architecture Marcello Mogetta Frontmatter More Information THE ORIGINS OF CONCRETE CONSTRUCTION IN ROMAN ARCHITECTURE In this study, Marcello Mogetta examines the origins and early dissemina- tion of concrete technology in Roman Republican architecture. Framing the genesis of innovative building processes and techniques within the context of Rome’s early expansion, he traces technological change in monumental construction in long-established urban centers and new Roman colonial cites founded in the 2nd century BCE in central Italy. Mogetta weaves together excavation data from both public monu- ments and private domestic architecture that previously have been studied in isolation. Highlighting the organization of the building industry, he also explores the political motivations and cultural aspirations of patrons of monumental architecture, reconstructing how they negotiated economic and logistical constraints by drawing from both local traditions and long- distance networks. By incorporating the available scientific evidence into the development of concrete technology, Mogetta also demonstrates the contributions of anonymous builders and contractors, shining a light on their ability to exploit locally available resources. marcello mogetta is a Mediterranean archaeologist whose research focuses on early Roman urbanism in Italy. He conducts primary fieldwork at the sites of Gabii (Gabii Project) and Pompeii (Venus Pompeiana Project), for which he has received multiple grants from the National Endowment for the Humanities, the Loeb Classical Library Foundation, the AIA, and the Social Sciences and Humanities Research Council. He coordinates the CaLC-Rome Project, an international collaboration that applies 3D mod- eling and surface analysis to the life cycle of ceramic vessels from the Esquiline necropolis in Rome. -
Vermiculite Concrete Introduction Vermiculite Concrete Is a Low Density Non-Structural Construction Product
Vermiculite Concrete Introduction Vermiculite concrete is a low density non-structural construction product. It is insulating (both thermally and acoustically) and intrinsically fire resistant. It is normally made simply by mixing exfoliated vermiculite as the aggregate, with cement and water, plus additives such as plasticisers if required. The ratio of exfoliated vermiculite aggregate to cement and the vermiculite grade can be varied to the properties such as strength and insulation as required for the concrete. The applications for vermiculite concrete are however, all non-structural. Vermiculite concretes can also be produced containing other lightweight aggregates, such as expanded perlite, to give differing physical properties. Normally the type of cement used in these mixes is Ordinary Portland Cement (O.P.C), although a higher initial strength may be obtained using Rapid Hardening Portland Cement (R.H.P.C). For high temperature refractory applications, high alumina (luminate in the USA) cements may be used with great success to manufacture lightweight in-situ cast insulation mixes and back up insulation products. However, these applications are beyond the scope of this specific application note. Applications for Vermiculite Concrete The principal applications for vermiculite concrete are for in-situ site mixed applications such as: • Floor and roof screeds • Void filling insulation mixes around chimneys, back boilers and fire backs • Blocks and slabs • Swimming pool bases [see separate application note for this application] Vermiculite concrete can be easily cut, sawed, nailed or screwed. The lower density vermiculite concrete screeds are usually covered with a denser topping mix of 4:1 or 5:1 sand to cement mix to a minimum depth of 25mm (1 inch); the screed and denser more load distributing topping should ideally be laid monolithically to prevent dis-bonding and shear fracturing between the screed and the topping. -
Alkali-Silica Reactivity: an Overview of Research
SHRP-C-342 Alkali-Silica Reactivity: An Overview of Research Richard Helmuth Construction Technology Laboratories, Inc. With contributions by: David Stark Construction Technology Laboratories, Inc. Sidney Diamond Purdue University Micheline Moranville-Regourd Ecole Normale Superieure de Cachan Strategic Highway Research Program National Research Council Washington, DC 1993 Publication No. SHRP-C-342 ISBN 0-30cL05602-0 Contract C-202 Product No. 2010 Program Manager: Don M. Harriott Project Maxtager: Inam Jawed Program AIea Secretary: Carina Hreib Copyeditor: Katharyn L. Bine Brosseau May 1993 key words: additives aggregate alkali-silica reaction cracking expansion portland cement concrete standards Strategic Highway Research Program 2101 Consti!ution Avenue N.W. Washington, DC 20418 (202) 334-3774 The publicat:Lon of this report does not necessarily indicate approval or endorsement by the National Academy of Sciences, the United States Government, or the American Association of State Highway and Transportation Officials or its member states of the findings, opinions, conclusions, or recommendations either inferred or specifically expressed herein. ©1993 National Academy of Sciences 1.5M/NAP/593 Acknowledgments The research described herein was supported by the Strategic Highway Research Program (SHRP). SHRP is a unit of the National Research Council that was authorized by section 128 of the Surface Transportation and Uniform Relocation Assistance Act of 1987. This document has been written as a product of Strategic Highway Research Program (SHRP) Contract SHRP-87-C-202, "Eliminating or Minimizing Alkali-Silica Reactivity." The prime contractor for this project is Construction Technology Laboratories, with Purdue University, and Ecole Normale Superieure de Cachan, as subcontractors. Fundamental studies were initiated in Task A. -
The Effects of Alkali-Silica Reaction on the Mechanical Properties of Concretes with Three Different Types of Reactive Aggregate
Technical Paper Okpin Na* DOI: 10.1002/suco.201400062 Yunping Xi Edward Ou Victor E. Saouma The effects of alkali-silica reaction on the mechanical properties of concretes with three different types of reactive aggregate This paper investigates the degradation of the mechanical prop- environment, the product of ASR is expansive, which is erties of concretes made with three types of aggregate affected detrimental to concrete structures [1, 2]. by alkali-silica reaction (ASR). Three standard testing methods ASR is a chemical reaction between the reactive – ASTM C289, JASS 5N T-603 and ASTM C1260 – were used to silica in the aggregate and the alkalis (Na2O and K2O) in identify the reactivity of ASR of the three aggregates selected. Portland cement. This chemical reaction produces alkali- The test results show that all three aggregates are potentially silica gel swelling with the absorption of the moisture deleterious. A new acceleration method based on JASS 5N T-603 from the surrounding cement paste. The expansive gel and ASTM C1260 was proposed for concrete specimens. In the can cause cracking in the concrete. Therefore, the neces- acceleration method, cylindrical concrete specimens were used, sary conditions for the expansive ASR gel to form in the additional alkali material was added to the concrete mixture and concrete are a sufficiently high alkali concentration in the the specimens were stored under conditions similar to ASTM cement, high moisture content in the concrete and reac- C1260. The preconditioned concrete specimens were then used tive aggregates. for evaluating the mechanical properties of the ASR-affected In order to control or prevent the occurrence of concrete in terms of strength and stiffness. -
Reinforced Concrete Failure Mechanisms
Reinforced Concrete Failure Mechanisms Best Practices in Dam and Levee Safety Risk Analyses Part E – Concrete Structures Chapter E-2 Last modified June 2017, Presented July 2019 Reinforced Concrete Failure Mechanisms OUTLINE: • Types of Structures • Spillway Piers • Navigation Lock Walls • Floodwalls • Slabs • Buttresses • Factors influencing strength and stability of reinforced concrete sections • National code requirements in the context of risk • Considerations when determining risk analysis failure probabilities based on structural analysis results • Typical event tree of the progression of failure 2 Reinforced Concrete Failure Mechanisms OBJECTIVES: • Get a broad overview of potential failure modes for different kinds of reinforced concrete structures • Understand the mechanisms that affect reinforced concrete failures • Understand how to construct an event tree to represent reinforced concrete failures • Understand how to estimate event probabilities and probability of breach Reinforced Concrete Failure Mechanisms SUMMARY OF KEY CONCEPTS: • Significant uncertainty for reinforced concrete failure mechanisms under seismic loading due to limited case histories • Concrete and reinforcement material properties can be determined with confidence for dams and floodwalls. • Type and duration of loading is important to understand – consider both static and earthquake loading • Ductile and Brittle Failure mechanisms • Seismic reinforcement details have changed dramatically over the past few decades; older concrete hydraulic structures may be -
Portland Cement Concrete
B Highway Materials Engineering Course PARTICIPANT WORKBOOK Portland Cement Concrete MODULE G Ti Table of Contents About This Workbook .................................................................................................................. 2 Course Overview .......................................................................................................................... 3 Introduction ................................................................................................................................. 3 Module G Overview ..................................................................................................................... 4 Module Goals ............................................................................................................................... 5 Learning Outcomes ...................................................................................................................... 5 ILT Instruction Icons ..................................................................................................................... 9 Module G Lesson 8 Review ..................................................................................................... G8-1 Module G Lesson 9 Basic Mix Design and Proportioning ....................................................... G9-1 Module G Lesson 10 Reinforcing and Corrosion ..................................................................G10-1 Module G Lesson 11 Hot Topics ...........................................................................................G11-1 -
Portland Cement User's Guide == Steps == # Plan Your Concrete
Portland Cement User’s guide == Steps == # Plan your concrete project carefully. There is a set sequence of steps you must take to be successful, and following them will save you a lot of problems later on. # Purchase or gather the raw materials for your concrete. You will need Portland type I or II cement, masonry or builder's sand or other clean sand, and if you want, as a filler, gravel or crushed limestone. The Portland cement usually comes in one cubic foot bags, weighing in at about 96 pounds each, so you may need help handling them, as well as a truck to haul it. # Build a mixing box, or get a good, sturdy wheel barrow to mix the materials in. If it is a large project, rent a concrete mixer to do the hardest part of the work for you. We have mixed as much as 6 or 8 cubic feet with a mason's hoe and shovel, in a large plastic tub, so not having the best equipment shouldn't stop you from trying it. # Allow yourself time to complete the whole process when you begin. If the concrete is a large "finished" slab, start early in the morning and gather all the help you can. # Build the form you are placing the concrete in, brace it off securely, level and plumb it up, and then carefully measure the dimensions to determine the volume in cubic feet. This is done by multiplying width X length X height in feet. An example would be 5 ft. X 2 ft. -
Components of Concrete Desirable Properties of Concrete
Components of Concrete Concrete is made up of two components, aggregates and paste. Aggregates are generally classified into two groups, fine and coarse, and occupy about 60 to 80 percent of the volume of concrete. The paste is composed of cement, water, and entrained air and ordinarily constitutes 20 to 40 percent of the total volume. In properly made concrete, the aggregate should consist of particles having adequate strength and weather resistance and should not contain materials having injurious effects. A well graded aggregate with low void content is desired for efficient use of paste. Each aggregate particle is completely coated with paste, and the space between the aggregate particles is completely filled with paste. The quality of the concrete is greatly dependent upon the quality of paste, which in turn, is dependent upon the ratio of water to cement content used, and the extent of curing. The cement and water combine chemically in a reaction, called hydration, which takes place very rapidly at first and then more and more slowly for a long period of time in favorable moisture conditions. More water is used in mixing concrete than is required for complete hydration of the cement. This is required to make the concrete plastic and more workable; however, as the paste is thinned with water, its quality is lowered, it has less strength, and it is less resistant to weather. For quality concrete, a proper proportion of water to cement is essential. Desirable Properties of Concrete Durability: Ability of hardened concrete to resist -
A Computational Study of the Shear Behavior of Reinforced Concrete Beams Affected from Alkali–Silica Reactivity Damage
materials Article A Computational Study of the Shear Behavior of Reinforced Concrete Beams Affected from Alkali–Silica Reactivity Damage Bora Gencturk 1,* , Hadi Aryan 1, Mohammad Hanifehzadeh 1, Clotilde Chambreuil 2 and Jianqiang Wei 3 1 Sonny Astani Department of Civil and Environmental Engineering, University of Southern California, 3620 S. Vermont Avenue, KAP 210, Los Angeles, CA 90089-2531, USA; [email protected] (H.A.); [email protected] (M.H.) 2 LMT—Laboratoire de Mécanique et Technologie, University Paris-Saclay, ENS Paris-Saclay, CNRS, 91190 Gif-sur-Yvette, France; [email protected] 3 Department of Civil and Environmental Engineering, University of Massachusetts, Lowell, MA 01854-5104, USA; [email protected] * Correspondence: [email protected]; Tel.: +1-(213)-821-1036; Fax: +1-(213)-744-1426 Abstract: In this study, an investigation of the shear behavior of full-scale reinforced concrete (RC) beams affected from alkali–silica reactivity damage is presented. A detailed finite element model (FEM) was developed and validated with data obtained from the experiments using several metrics, including a force–deformation curve, rebar strains, and crack maps and width. The validated FEM was used in a parametric study to investigate the potential impact of alkali–silica reactivity (ASR) degradation on the shear capacity of the beam. Degradations of concrete mechanical properties were correlated with ASR expansion using material test data and implemented in the FEM for Citation: Gencturk, B.; Aryan, H.; different expansions. The finite element (FE) analysis provided a better understanding of the failure Hanifehzadeh, M.; Chambreuil, C.; mechanism of ASR-affected RC beam and degradation in the capacity as a function of the ASR Wei, J. -
How to Make Concrete More Sustainable Harald Justnes1
Journal of Advanced Concrete Technology Vol. 13, 147-154, March 2015 / Copyright © 2015 Japan Concrete Institute 147 Scientific paper How to Make Concrete More Sustainable Harald Justnes1 A selected paper of ICCS13, Tokyo 2013. Received 12 November 2013, accepted 16 February 2015 doi:10.3151/jact.13.147 Abstract Production of cement is ranking 3rd in causes of man-made carbon dioxide emissions world-wide. Thus, in order to make concrete more sustainable one may work along one or more of the following routes; 1) Replacing cement in con- crete with larger amounts of supplementary cementing materials (SCMs) than usual, 2) Replacing cement in concrete with combinations of SCMs leading to synergic reactions enhancing strength, 3) Producing leaner concrete with less cement per cubic meter utilizing plasticizers and 4) Making concrete with local aggregate susceptible to alkali silica reaction (ASR) by using cement replacements, thus avoiding long transport of non-reactive aggregate. 1 Introduction SCMs, also uncommon ones like calcined marl 2. Replacing cement in concrete with combinations of The cement industry world-wide is calculated to bring SCMs leading to synergic reactions enhancing about 5-8% of the total global anthropogenic carbon strength dioxide (CO2) emissions. The general estimate is about 3. Producing leaner concrete with less cement per cubic 1 tonne of CO2 emission per tonne clinker produced, if meter utilizing plasticizers. fossil fuel is used and no measures are taken to reduce it. 4. Making concrete with local aggregate susceptible to The 3rd rank is not because cement is such a bad mate- alkali silica reaction (ASR) by using cement re- rial with respect to CO2 emissions, but owing to the fact placements, thus avoiding long transport of non- that it is so widely used to construct the infrastructure reactive aggregate and buildings of modern society as we know it. -
Formwork.Pdf
Formwork INTRODUCTION ............................................................................................................................................................ 3 DESIGN REQUIREMENTS ............................................................................................................................................... 4 FACTORS RELATING TO FORMWORK ........................................................................................................................... 6 HIGH WALL FORMWORK .......................................................................................................................................... 6 Timber Framed Formwork. ....................................................................................................................................... 7 SHEATHING ............................................................................................................................................................... 8 WALL TYING SYSTEMS .............................................................................................................................................. 8 CONSTRUCTION JOINTS ............................................................................................................................................ 9 SLIPFORM ............................................................................................................................................................... 10 CLIMBING OR JUMP FORMS ..................................................................................................................................