Ageing/ Degradation of Paper
Total Page:16
File Type:pdf, Size:1020Kb
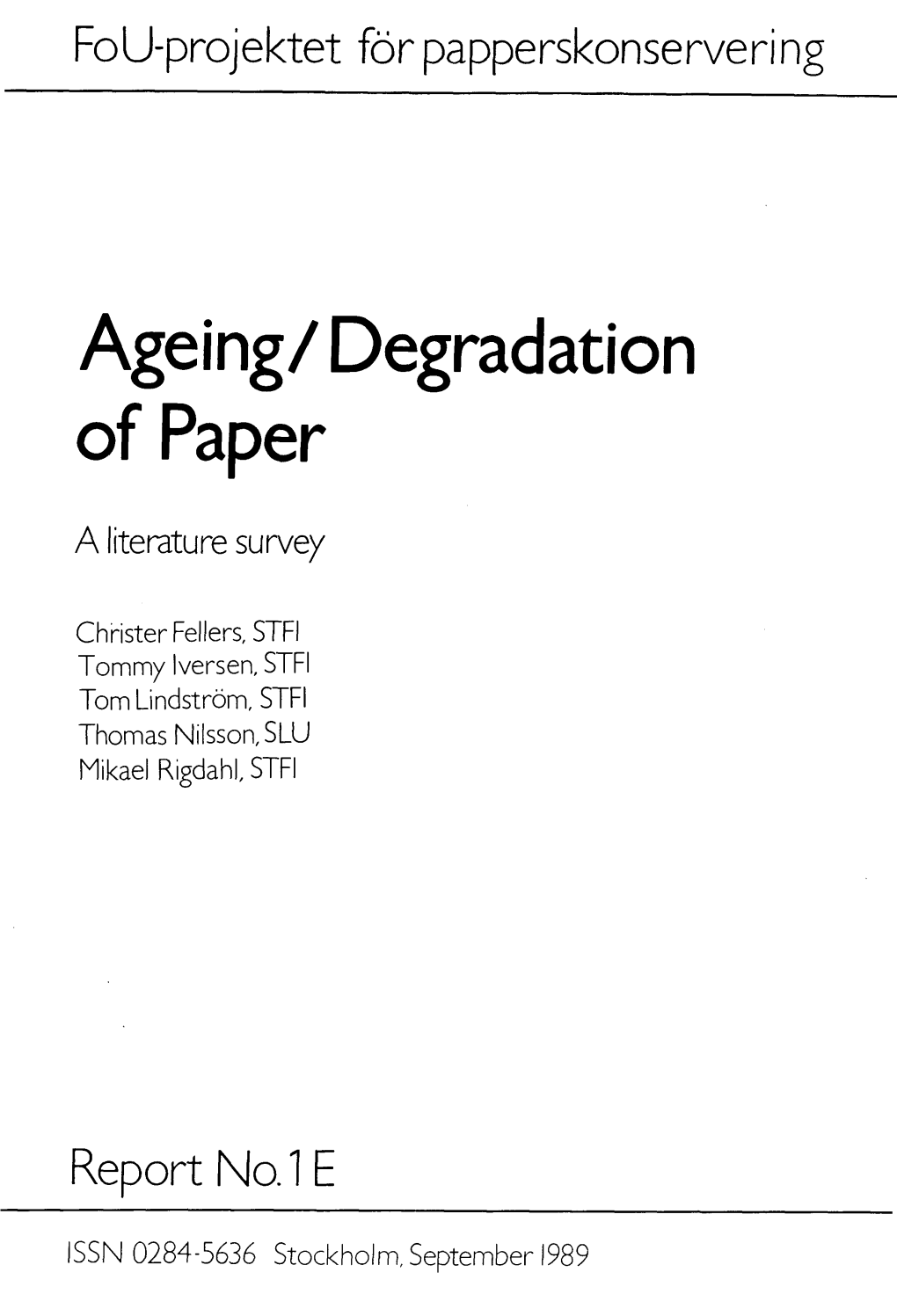
Load more
Recommended publications
-
Assessing Preservation Needs: a Self-Survey Guide, by the Northeast Document Conservation Center
ASSESSING PRESERVATION NEEDS ASSESSING PRESERVATION NEEDS A SELF-SURVEY GUIDE Beth Patkus Northeast Document Conservation Center Andover, Massachusetts 2003 The Institute of Museum and Library Services, a federal agency that fosters innovation, leadership, and a lifetime of learning, supported the publication of this book, Assessing Preservation Needs: A Self-Survey Guide, by the Northeast Document Conservation Center. The National Endowment for the Humanities, an independent grant-making agency of the federal government, provides substantial funding to support field service activities, including publications, at the Northeast Document Conservation Center. Library of Congress Cataloging Number ISBN No. 0-9634685-5-3 Copyright © 2003 by Northeast Document Conservation Center. All rights reserved. No part of this publication may be reproduced or transmitted for commercial purposes in any form or media, or stored by any means in any storage retrieval system, without prior written permission of the Northeast Document Conservation Center, 100 Brickstone Square, Andover, MA 01810. This publication is printed on paper that meets the requirements of American National Standard for Information Sciences—Permanence of Paper for Printed Library Materials, ANSI Z39.48-1992 (R1997). CONTENTS PREFACE ................................................................................................................................. ix INTRODUCTION.................................................................................................................... -
Australian/New Zealand Standard
AS/NZS 1301.423rp:1997 Australian/New Zealand Standard Methods of test for pulp and paper Method 423rp: Folding strength of paper—Kohler-Molin method This is a free 7 page sample. Access the full version online. AS/NZS 1301.423rp:1997 This Joint Australian/New Zealand Standard was prepared by Joint Technical Committee PK/19, Methods of Test for Pulp and Paper. It was approved on behalf of the Council of Standards Australia on 1 August 1997 and on behalf of the Council of Standards New Zealand on 7 July 1997. It was published on 5 September 1997. The following interests are represented on Committee PK/19: Australian Government Analytical Laboratories Australian Government Publishing Service CSIRO —Division of Forestry and Forest Products National Association of Forest Industries New Zealand Forest Research Institute New Zealand Pulp and Paper Industry Association Printing and Allied Trades Employers Federation of Australia Pulp and Paper Manufacturers Federation of Australia The Technical Association of the Australian and New Zealand Pulp and Paper Industry (APPITA) Additional interests participating in preparation of Standard: Paper manufacturers Pulp manufacturers Research interests Manufacturers of paper testing instruments Suppliers of paper testing instruments Review of Standards. To keep abreast of progress in industry, Joint Australian/ New Zealand Standards are subject to periodic review and are kept up to date by the issue of amendments or new editions as necessary. It is important therefore that Standards users ensure that they are in possession of the latest edition, and any amendments thereto. Full details of all Joint Standards and related publications will be found in the Standards This is a free 7 page sample. -
JCAC33 Boruvka
The Development of Foxing Stains on Samples of Book Paper after Accelerated Ageing Natalie Boruvka Journal of the Canadian Association for Conservation (J. CAC), Volume 33 © Canadian Association for Conservation, 2008 This article: © Natalie Boruvka, 2008. Reproduced with the permission of Natalie Boruvka. J.CAC is a peer reviewed journal published annually by the Canadian Association for Conservation of Cultural Property (CAC), PO Box 87028, 332 Bank Street, Ottawa, Ontario K2P 1X0, Canada; Tel.: (613) 231-3977; Fax: (613) 231- 4406; E-mail: [email protected]; Web site: http://www.cac-accr.ca/. The views expressed in this publication are those of the individual authors, and are not necessarily those of the editors or of CAC. Journal de l'Association canadienne pour la conservation et la restauration (J. ACCR), Volume 33 © l'Association canadienne pour la conservation et la restauration, 2008 Cet article : © Natalie Boruvka, 2008. Reproduit avec la permission de Natalie Boruvka. Le J.ACCR est un journal révisé par des pairs qui est publié annuellement par l'Association canadienne pour la conservation et la restauration des biens culturels (ACCR), BP 87028, 332, rue Bank, Ottawa (Ontario) K2P 1X0, Canada; Téléphone : (613) 231-3977; Télécopieur : (613) 231-4406; Adresse électronique : [email protected]; Site Web : http://www.cac-accr.ca. Les opinions exprimées dans la présente publication sont celles des auteurs et ne reflètent pas nécessairement celles de la rédaction ou de l'ACCR. 38 The Development of Foxing Stains on Samples of Book Paper after Accelerated Ageing Natalie Boruvka Queen's University, Art Conservation Program, 15 Bader Lane, Kingston, ON K7L 3N6, Canada; [email protected] The term foxing is used to describe red-brown spots that develop on some paper objects over time. -
Characterization and Evaluation of Datura Stramonium Stalks As an Alternative Non Wood Raw Material for Paper Production Using Soda Pulping
Published by : International Journal of Engineering Research & Technology (IJERT) http://www.ijert.org ISSN: 2278-0181 Vol. 5 Issue 11, November-2016 Characterization and Evaluation of Datura Stramonium Stalks as an Alternative Non Wood Raw Material for Paper Production using Soda Pulping Sartaj Ahmad Ganie1*, Shoukat Ara1, Mohammad Aneesul Mehmood1 Saakshy Agarwal2, R.K. Jain2 1Division of Environmental Sciences, 2Kumarappa National Handmade Paper Institute, Shere-Kashmir University of Agricultural Sciences & Jaipur 302029, Rajasthan, India. Technology of Kashmir, Shalimar, 190025, India Abstract - The study was carried out to evaluate Datura stalks narcotic effects or to treat asthma [7]. In the Hindu religion, as an alternative raw material for paper production. The the seed of Datura stramonium is believed to be associated proximate analysis of Datura stalks, black and wash liquor with the God Shiva, which can promote on religious analysis and strength properties of paper was characterized. occasions, such as Shivaratri and Swasthani Puja [8]. The results revealed that Ash, Lignin, Hot water solubility, Datura stramonium is native to deserts of the North 10% NaOH solubility, Alcohol-benzene solubility and American Southwest, Central and South America, Europe, Holocellulose content of Datura stalks were of the order of Asia, and Africa. It is mainly distributed in the Himalaya 9.57, 15.81, 15.9, 57.9, 11.75 and 62.51 per cent respectively. region from Kashmir to Sikkim up to 2700 m, in the hilly The values of black liquor include pH, Total solids, Chemical oxygen demand and color were 8.66, 4.68%, 81342 ppm and district of central and south India [9] 66203 PCU respectively, while as for wash liquor the World demand for paper and paperboard is respective values were 8.34, 0.95%, 35739 ppm and 21702 estimated to grow from 300 million tons to over 490 PCU. -
Conservation of Coated and Specialty Papers
RELACT HISTORY, TECHNOLOGY, AND TREATMENT OF SPECIALTY PAPERS FOUND IN ARCHIVES, LIBRARIES AND MUSEUMS: TRACING AND PIGMENT-COATED PAPERS By Dianne van der Reyden (Revised from the following publications: Pigment-coated papers I & II: history and technology / van der Reyden, Dianne; Mosier, Erika; Baker, Mary , In: Triennial meeting (10th), Washington, DC, 22-27 August 1993: preprints / Paris: ICOM , 1993, and Effects of aging and solvent treatments on some properties of contemporary tracing papers / van der Reyden, Dianne; Hofmann, Christa; Baker, Mary, In: Journal of the American Institute for Conservation, 1993) ABSTRACT Museums, libraries, and archives contain large collections of pigment-coated and tracing papers. These papers are produced by specially formulated compositions and manufacturing procedures that make them particularly vulnerable to damage as well as reactive to solvents used in conservation treatments. In order to evaluate the effects of solvents on such papers, several research projects were designed to consider the variables of paper composition, properties, and aging, as well as type of solvent and technique of solvent application. This paper summarizes findings for materials characterization, degradative effects of aging, and some effects of solvents used for stain reduction, and humidification and flattening, of pigment-coated and modern tracing papers. Pigment-coated papers have been used, virtually since the beginning of papermaking history, for their special properties of gloss and brightness. These properties, however, may render coated papers more susceptible to certain types of damage (surface marring, embedded grime, and stains) and more reactive to certain conservation treatments. Several research projects have been undertaken to characterize paper coating compositions (by SEM/EDS and FTIR) and appearance properties (by SEM imaging of surface structure and quantitative measurements of color and gloss) in order to evaluate changes that might occur following application of solvents used in conservation treatments. -
Sustainable Raw Material in Paper Industries Accepted: 30-10-2017
Journal of Pharmacognosy and Phytochemistry 2017; 6(6): 2096-2100 E-ISSN: 2278-4136 P-ISSN: 2349-8234 Paper making potential of Amaranthus hybridus stalks; JPP 2017; 6(6): 2096-2100 Received: 29-09-2017 Sustainable raw material in paper industries Accepted: 30-10-2017 Sartaj A Ganie Sartaj A Ganie, Shoukat Ara, Saakshy Agarwal, Mohamad Aneesul Division of Environmental Sciences, Shere-Kashmir Mehmood, Imtiyaz Murtaza Giri and Shakeel A Mir University of Agricultural Sciences & Technology of Abstract Kashmir, Shalimar, Jammu and Stalks of non-wood herbaceous species Amaranthus hybridus was investigated by soda pulping to Kashmir, India investigate the future of Amaranthus hybridus species stalks as a auspicious renewable cradle in pulp and Shoukat Ara paper industry, which is profusely accessible in Kashmir (India) along road sides, foot paths, wastelands, Division of Environmental pastures, hilly areas as unwanted weed. In the opportunity of current study, the element characterization Sciences, Shere-Kashmir of Amaranthus hybridus stalk dust, chemical characterization of liquor analysis and paper properties were University of Agricultural carried out. The elemental analysis of test species bared that Ash%, Lignin%, Hot water solubility%, Sciences & Technology of 10% NaOH solubility, Alcohol-benzene solubility% and Holocellulose % content were detected in the Kashmir, Shalimar, Jammu and array of 11.03, 17.55, 20.25, 40.40, 6.64 and 62.41 respectively. Liquors obtained after digestion of test Kashmir, India species results what is called as black liquor and the chemical analysis of the liquor includes pH, total solids, chemical oxygen demand and color which were chronicled 8.84, 6.82%, 226240 ppm and 115505 Saakshy Agarwal PCU respectively and for wash liquor the corresponding values were recorded 8.45, 1.90%, 113100 Kumarappa National Handmade ppm and 31684 PCU. -
Full Article
INTERNATIONAL JOURNAL OF CONSERVATION SCIENCE ISSN: 2067-533X Volume 7, Issue 4, October-December 2016: 1023-1030 www.ijcs.uaic.ro EXPERIMENTAL STUDY ON THE CLEANING OF FOXING SPOTS ON THE OLD PAPER MANUSCRIPTS USING NATURAL PRODUCTS Nadia Zaki SHABAN1, Sawsan Said DAROUISH2, Taha Ayman SALAH*3 1 Biochemistry Department, Faculty of Science, Alexandria University, Alexandria, Egypt 2 Conservation Department, Faculty of Archaeology, Cairo University, Cairo, Egypt 3 Conservation Department, Faculty of Archaeology, Aswan University, Egypt. Abstract Many manuscripts and historical books contain a form of deterioration known as foxing or fox spots, a brownish stain which has the effect of altering aesthetic and visual appeal. The aim of this work is to study the role of the extracts of Water Cantaloupe (CE) and Water melon (WE) separately as natural products in removing foxing spots in various modern and old papers. Old papers and three types of modern papers made from cotton, linen and a mixture of cotton, linen and wood (1:1:1) were used for this purpose. Each type was divided into two groups, one of them was infected with foxing and the other was left as control (uninfected). Infected papers were treated with CE, WE and 2% sodium hypochlorite (as a traditional chemical bleaching) separately. Fourier Transform Infrared Spectroscopy (FTIR), Atomic Absorption Spectroscopy, Scanning Electron Microscopy equipped with Energy-Dispersive X-ray spectroscopy (SEM-EDX) in addition to some optical and mechanical properties were carried out to evaluate the Cantaloupe Extracts (CE) and Water Melon Extracts (WE) use in removing foxing stains compared to sodium hypochlorite. The results showed that CE removed foxing in different studied papers at pH = 7.4. -
Effect of Different Locations on the Morphological, Chemical, Pulping and Papermaking Properties of Trema Orientalis (Nalita)
Bioresource Technology 101 (2010) 1892–1898 Contents lists available at ScienceDirect Bioresource Technology journal homepage: www.elsevier.com/locate/biortech Effect of different locations on the morphological, chemical, pulping and papermaking properties of Trema orientalis (Nalita) M. Sarwar Jahan a,b,*, Nasima Chowdhury a, Yonghao Ni b a Pulp and Paper Research Division, BCSIR Laboratories, Dr. Qudrat-E-Khuda Road, Dhaka 1205, Bangladesh b Pulp and Paper Research Centre, University of New Brunswick, Fredericton, Canada article info abstract Article history: The chemical compositions and fiber morphology of stem and branch samples from Trema orientalis at Received 24 August 2009 three different sites planted in Bangladesh were determined and their pulping, bleaching and the result- Received in revised form 1 October 2009 ing pulp properties were investigated. A large difference between the stem and branch samples was Accepted 13 October 2009 observed. The stem samples have consistently higher a-cellulose and lower lignin content, and longer Available online 14 November 2009 fibers than the branch samples in all sites. T. orientalis from the Dhaka and Rajbari region had higher a-cellulose content and longer fiber length, resulting in higher pulp yield and better papermaking prop- Keyword: erties. The T. orientalis pulp from Rajbari region also showed the best bleachability. Trema orientalis, Variation of wood Ó 2009 Elsevier Ltd. All rights reserved. properties Stem and branch Pulping and bleaching 1. Introduction sely to those of Malaysian-grown mangium and other fast-grow- ing plantation species, including the traditionally-used pulpwood The increased demand for wood and fiber and declining avail- of the Philippines. -
The Aging of Archival Storage Boxes As Indicated by Ph
DOCUMENT RESUME ED 424 868 IR 057 234 AUTHOR Nawalaniec, Theresa M. TITLE The Aging of Archival Storage Boxes as Indicated by pH. PUB DATE 1998-04-00 NOTE 29p.; Master's Research Paper, Kent State University. PUB TYPE Dissertations/Theses (040) EDRS PRICE MF01/PCO2 Plus Postage. DESCRIPTORS Academic Libraries; Acids; *Age; *Archives; Change; *Chemical Analysis; Correlation; Higher Education; *Information Storage; Tables (Data) IDENTIFIERS Acid Free Paper; *pH ABSTRACT In order to determine if the pH of archival storage boxes decreases over time, experimental research was performed by sampling 25 Hollinger, one cubic foot, archival storage boxes from the Kent State University (Ohio) Archives. Boxes chosen for testing were new,5, 10, 15, and 20 years old. Each box was tested for pH value using pH pens and a cold extraction method, both in duplicate, to see if there was a relationship between pH value and age of archival box. Most of the 10 to 20-year-old boxes increased in acidity in comparison to their original pH values. A few of the 10 to 20-year-old boxes were still acid-free. All new and 5-year-old boxes were found to be acid-free. The average cold extraction pH value is 9.4 for new boxes, 9.0 for 5-year-old boxes, 6.5 for 10-year-old boxes, 6.9 for 15-year-old boxes, and 6.5 for 20-year-old boxes. A correlation was done using the cold extraction pH results from the 10 to 20-year-old boxes, which produced an r-value of -0.436, showing a negative correlation between time (age of storage box) and pH value. -
Ref. 676.03 SMO 2Nd
INDEX Refer to Chapter Refer to Chapter Refer to Chapter A test 14 acid pretreatment 10 acetate 4 acidproof brick 8 abaca 3 acetate laminating 18 acid pulping 8 abatement 20 acetate pulp 4 acid rain 21 odor 21 acetic acid 4 acid-refined tall oil 6 pollution 20 acetic anhydride 4 acid-resistant 14 abatement device 21 acetone 4 acid size 5 abietic acid 6 acetylated starch 5 acid-stable size 5 abrasion 24 acetyl radical 4 acid sulfite process 8 abrasion debarker I acetylating agent 4 acid tower 8 abrasion resistance 14 acid(s) 4, 8 acid treatment 10 abrasion test 14 abietic 6 acidulating 4 abrasive 7 acetic 4 acidulating agent 4 abrasive backing papers 16 accumulator 8 acidulation 6 abrasiveness 14 carbonic 20 acoustical board 16 abrasive segment 7 Caro's 10 acoustical testing 14 abrasivity (of mineral fillers) 13 cooking 8 acoustic leak detector 9 absorbency 11,14 digester 8 acre-foot 20 relative II fatty 6 acrylamide resins 5 water II formamidine sulfinic 10 acrylic binders 17 absorbent 14,24 formic 4 acrylic fiber 3 absorbent capacity II glucuronic 4 activatable chemical 9 absorbent grades 16 humic 20 activated carbon 20 absorption 5 hydroxy 4 activated sludge 20 capillary 13 hypochlorous 10 activated sludge loading 20 ink 14 lignosulfonic 8 activated sludge process 20 light 14 linoleic 6 activation 4 mechanical 13 mineral 4 surface II tensile energy 14 oleic 6 activation energy 8 vapor 13 pectic 4 Arrhenius 4 absorption coefficient 14 peracetic 10 activator 5 accelerated aging 14 raw 8 active alkali 8 accelerated aging test 14 resin -
Deterioration and Microbiological Evaluation of Information Bearing Paper in a Nigerian University
Annual Research & Review in Biology 26(2): 1-9, 2018; Article no.ARRB.39280 ISSN: 2347-565X, NLM ID: 101632869 Deterioration and Microbiological Evaluation of Information Bearing Paper in a Nigerian University 1* 1 F. Ayoade and S. D. Amona 1Department of Biological Sciences, College of Natural Sciences, Redeemer’s University, PMB 230, Ede, Osun State, Nigeria. Authors’ contributions This work was carried out in collaboration between both authors. Author FA designed the study, performed laboratory and statistical analyses, wrote the protocol and wrote the first draft of the manuscript. Author SA managed the sample collection and laboratory analyses of the study. Both authors read and approved the final manuscript. Article Information DOI: 10.9734/ARRB/2018/39280 Editor(s): (1) George Perry, Dean and Professor of Biology, University of Texas at San Antonio, USA. Reviewers: (1) Yassellis J. R. Ruiz, Universidad de Carabobo, Venezuela. (2) Modupe Elizabeth Ojewumi, Covenant University, Nigeria. Complete Peer review History: http://www.sciencedomain.org/review-history/24455 Received 1st December 2017 th Original Research Article Accepted 7 February 2018 Published 4th May 2018 ABSTRACT Using a completely randomized block design and Redeemer’s University as a case study, air samples at the University library, clinic and registry were evaluated for microorganisms that are capable of causing paper deterioration and the physical environments were assessed for ability to predispose paper to bio-deterioration. Using the sterile swab stick, microbial samples were collected from randomly selected books and documents exhibiting signs of deterioration such as brown discolouration (foxing) and, specific codes were assigned for tracking purposes. -
Tensile Strength Increases Slightly to a Maximum at 30-35% Relative Humidity and Then Decreases Quite Rapidly at Higher Relative Humidities
S~h Cess /Iraininq fProoramme on "Calibration & Testing Methods" at CPPRI, Saharanpur July 22 - 26, 2006 Sponsored by Development Council For Pulp Ministry of commerce & Industry Paper & Allied Industry Govt. of India Sixth Cess Training Programme on Calibration & Testing Methods At CPPRI , Saharanpur July 22- 26, 2006 Organised by cPatfm ~ uci CPLdLut ~ ?ll:~ CENTRAL PULP & PAPER RESEARCH INSTITUTE AN ISO 9001 :2000 INSTITUTION In pursuit of cleaner production, resource conservation & quality excellence m~ ~~ .m Cl>ldl\Jl 3I<?XRrnoIRmroI Central Pulp & Paper Research Institute AN ISO 9001 :2~00 INSTITUTION Accred.ited by~ •• : ~ Mcm~of~ n /11pursuit of cleaner production, resource conservation & qllali~l' excellence IAF MLA for ,. ~ An autonomous organisation registered under societies Act under the administrative QMS * ~ control of the Ministry of Commerce & Industry (Govt. of India) c' Dr. A. G. KULKARNI Director PREFACE Under the present scenario of trade liberalization in the country, Indian paper Industry is required to be globally competitive. There is a need to explore innovative means to reduce costs while improving environmental performance, safety and efficiency of mills and ultimately of quality of products. Today, quality of the end product has become one of the most important factors. Evaluation of quality is closely linked with the proper calibration of the testing equipments/ instruments. In Europe, organizations/ institutes like Finish Pulp & Paper Research Institute, Helsinki & PIRA in UK, etc. have been providing calibration service to the pulp and paper mills in their countries for quite long time. The calibration service helps the pulp and paper mills to check the performance of the testing equipments/ instruments so that the desired quality parameters of the raw materials and end products are ensured.