A Review on the Beneficiation Methods of Borate Minerals
Total Page:16
File Type:pdf, Size:1020Kb
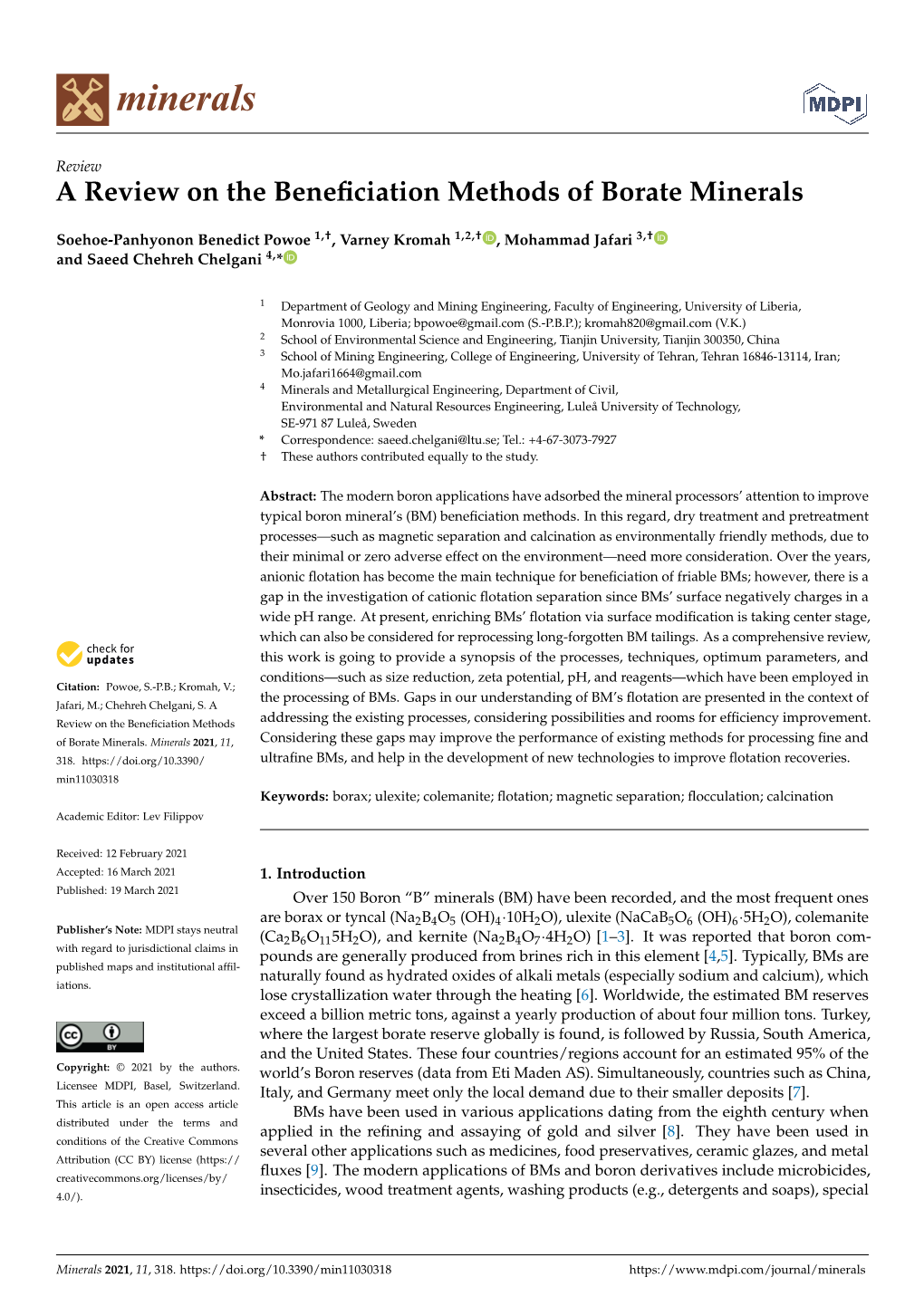
Load more
Recommended publications
-
Midterm 2 Examination Key
GLY4200C Name 90 points October 26, 2011 16 took exam - Numbers to the left of the question number in red are the number of incorrect responses. Instructor comments are in blue. Florida Atlantic University MINERALOGY -- MIDTERM 2 EXAMINATION KEY True-False - Print the letter T or F in the blank to indicate if each of the following statements is true or false. Illegible answers are wrong. (1 point each) 0 T 1. All mathematical groups, including crystallographic point and space groups, must contain an identity operation. 2 F 2. All pyramidal forms are closed. 11 F 3. As nuclei grow, their surface area/volume ratio increases. 1 F 4. Growth twins are always penetration twins. 2 T 5. Low-spin Fe3+ is smaller than high-spin Fe3+. 0 T 6.As pressure increases, minerals transform to denser structures, with atoms packed more closely together 1 T 7. Although silicon normally has CN = IV, in the lower mantle the pressures are so great that the CN of silicon is VI. 2 F 8. If two ions have the same charge, the larger ion will enter a crystal structure preferentially. 2 T 9. Crystal classes are defined by the thirty-two possible point groups. 11 F 10. Possible symmetry operations include rotation axes, mirror planes, and an inversion center. What is wrong with this statement? 0 T 11. Faces composed of all anions or all cations are very high energy. They attract ions of opposite sign, grow rapidly, and may grow themselves out of existence. 1 T 12. The calculation of the zone axis is done using the same method as a vector cross- product. -
Rocks and Minerals in This Station-Based Event
Gary Vorwald NYS Rock & Mineral Supervisor Paul J. Gelinas JHS [email protected] Event Description Participants will demonstrate their knowledge of rocks and minerals in this station-based event. A team of up to 2 Approximate time: 40 – 50 Minutes Event Parameters Each team may bring: one magnifying glass One 3-ring binder (1 inch) containing information in any form from any source Materials MUST be 3-hole punched and inserted into the rings (sheet protectors allowed) The Competition Station Event: 15-24 stations with samples & questions Equal time intervals will be allotted for each station. When the signal is given, participants will begin work at their initial station. Participants may not move to the next station until prompted to do so, may not skip stations, nor return to any previously-visited station Mineral and Rock Stations The Competition HCl will not be provided, nor may it be brought to, or be used during the competition. Written descriptions as to how a specimen might react were it to be tested with HCl may be provided. The Competition Identification will be limited to specimens appearing on the Official Science Olympiad Rock and Mineral List (see www.soinc.org) Other rocks or minerals may be used to illustrate key concepts. Tournament Directors may include up to five additional specimens important to their own state. If additional specimens are to be included, all teams must be notified no later than 3 weeks prior to the competition. 2017 Rock & Mineral List Available at: https://www. soinc.org Students should place list in front of notebook Minerals are organized by mineral family Consists of: 59 Minerals 7 Metamorphic Rocks 10 Igneous Rocks 17 Sedimentary Rocks (or varieties) Minerals Native Elements 31. -
Economic Diversification Plan for East Kern County
FEBRUARY 2017 ECONOMIC DIVERSIFICATION PLAN EAST KERN COUNTY, CA KERN COUNTY ACKNOWLEDGEMENTS TIP Strategies would like to thank the many individuals who participated in the creation of this Economic Diversification Plan. We are especially grateful to the members of the East Kern Economic Alliance who contributed their time and input throughout this planning process. Their expertise helped us gain a deep understanding of the region’s range of assets and opportunities. We are also thankful for the US Department of Defense Office of Economic Adjustment for their visionary investments and support which helped make this project a reality. We also want to thank the leadership and staff of Kern County and the Kern EDC for their essential support, guidance, and feedback during the development of this plan. EAST KERN ECONOMIC ALLIANCE KEY STAKEHOLDERS Richard Chapman, President & CEO Jennifer Wood, Mayor Gary Parsons, Economic Kern Economic Development California City Development Manager Corporation City of Ridgecrest Karina Drees, CEO and General Bill Deaver, Michelle Vance, Economic Manager Edwards Community Alliance Development Coordinator Mojave Air & Spaceport City of Tehachapi Kimberly Maevers, President Kelly Bearden, Director Ryan Rush, Field Representative Greater Antelope Valley Economic CSU-Bakersfield SBDC Kern County Board of Supervisors, Alliance 2nd District KERN COUNTY PROJECT TEAM Supervisor Zach Scrivner, Chairman of the Kern County Board of Supervisors & 2nd District Supervisor Teresa Hitchcock, Assistant County Administrative -
A Multi-Methodological Study of Kurnakovite: a Potential B-Rich 2 Aggregate 3 4 G
1 A multi-methodological study of kurnakovite: a potential B-rich 2 aggregate 3 4 G. Diego Gatta1, Alessandro Guastoni2, Paolo Lotti1, Giorgio Guastella3, 5 Oscar Fabelo4 and Maria Teresa Fernandez-Diaz4 6 7 1Dipartimento di Scienze della Terra, Università degli Studi di Milano, 8 Via Botticelli 23, I-20133 Milano, Italy 9 2Dipartmento di Geoscienze, Università degli Studi di Padova, 10 Via G. Gradenigo 6, I-35131, Padova, Italy 11 3Agenzia delle Dogane e dei Monopoli, Direzione Regionale per la Lombardia, 12 Laboratorio e Servizi Chimici, Via Marco Bruto 14, I-20138 Milan, Italy 13 4Institut Laue-Langevin, 71 Avenue des Martyrs, F-38000 Grenoble, France 14 15 16 Abstract 17 The crystal structure and crystal chemistry of kurnakovite from Kramer Deposit (Kern 18 County, California), ideally MgB3O3(OH)5·5H2O, was investigated by single-crystal neutron 19 diffraction (data collected at 293 and 20 K) and by a series of analytical techniques aimed to determine 20 its chemical composition. The concentration of more than 50 elements was measured. The empirical 21 formula of the sample used in this study is: Mg0.99(Si0.01B3.00)Σ3.01O.3.00(OH)5·4.98H2O. The fraction 22 of rare earth elements (REE) and other minor elements is, overall, insignificant. Even the fluorine 23 content, as potential OH-group substituent, is insignificant (i.e., ~ 0.008 wt%). The neutron structure 24 model obtained in this study, based on intensity data collected at 293 and 20 K, shows that the 25 structure of kurnakovite contains: [BO2(OH)]-groups in planar-triangular coordination (with the B- 2 26 ions in sp electronic configuration), [BO2(OH)2]-groups in tetrahedral coordination (with the B-ions 3 27 in sp electronic configuration), and Mg(OH)2(H2O)4-octahedra, connected in (neutral) 28 Mg(H2O)4B3O3(OH)5 units forming infinite chains running along [001]. -
Inyoite Cab3o3(OH)5 • 4H2O C 2001-2005 Mineral Data Publishing, Version 1
Inyoite CaB3O3(OH)5 • 4H2O c 2001-2005 Mineral Data Publishing, version 1 Crystal Data: Monoclinic. Point Group: 2/m. Typically as crystals, short prismatic along [001], tabular on {001}, exhibiting prominent {110} and {001} and a dozen other minor forms, to 2.5 cm; in cockscomb aggregates of pseudorhombohedral crystals; also coarse spherulitic, granular. Physical Properties: Cleavage: {001}, good; {010}, distinct. Fracture: Irregular. Tenacity: Brittle. Hardness = 2 D(meas.) = 1.875 D(calc.) = 1.87 Soluble in H2O. Optical Properties: Transparent, translucent on dehydration. Color: Colorless, white on dehydration. Luster: Vitreous. Optical Class: Biaxial (–). Orientation: Y = b; X ∧ c =37◦; Z ∧ c = –53◦. Dispersion: r< v, slight. α = 1.490–1.495 β = 1.501–1.505 γ = 1.516–1.520 2V(meas.) = 70◦–86◦ Cell Data: Space Group: P 21/a. a = 10.621(1)) b = 12.066(1) c = 8.408(1) β = 114◦1.2◦ Z=4 X-ray Powder Pattern: Monte Azul mine, Argentina. 7.67 (100), 2.526 (25), 3.368 (22), 1.968 (22), 2.547 (21), 3.450 (20), 2.799 (19) Chemistry: (1) (2) B2O3 37.44 37.62 CaO 20.42 20.20 + H2O 9.46 − H2O 32.46 H2O 42.18 rem. 0.55 Total 100.33 100.00 • (1) Hillsborough, Canada; remnant is gypsum. (2) CaB3O3(OH)5 4H2O. Occurrence: Along fractures and nodular in sedimentary borate deposits; may be authigenic in playa sediments. Association: Meyerhofferite, colemanite, priceite, hydroboracite, ulexite, gypsum. Distribution: In the USA, in California, from an adit on Mount Blanco, Furnace Creek district, Death Valley, Inyo Co., and in the Kramer borate deposit, Boron, Kern Co. -
Ulexite Nacab5o6(OH)6 • 5H2O C 2001-2005 Mineral Data Publishing, Version 1 Crystal Data: Triclinic
Ulexite NaCaB5O6(OH)6 • 5H2O c 2001-2005 Mineral Data Publishing, version 1 Crystal Data: Triclinic. Point Group: 1. Rare as measurable crystals, which may have many forms; typically elongated to acicular along [001], to 5 cm, then forming fibrous cottonball-like masses; in compact parallel fibrous veins, and radiating and compact nodular groups. Twinning: Polysynthetic on {010} and {100}; possibly also on {340}, {230}, and others. Physical Properties: Cleavage: On {010}, perfect; on {110}, good; on {110}, poor. Fracture: Uneven across fiber groups. Tenacity: Brittle. Hardness = 2.5 D(meas.) = 1.955 D(calc.) = 1.955 Slightly soluble in H2O; parallel fibrous masses can act as fiber optical light pipes; may fluoresce yellow, greenish yellow, cream, white under SW and LW UV. Optical Properties: Transparent to opaque. Color: Colorless; white in aggregates, gray if included with clays. Luster: Vitreous; silky or satiny in fibrous aggregates. Optical Class: Biaxial (+). Orientation: X (11.5◦,81◦); Y (100◦,21.5◦); Z (107◦,70◦) [with c (0◦,0◦) and b∗ (0◦,90◦) using (φ,ρ)]. α = 1.491–1.496 β = 1.504–1.506 γ = 1.519–1.520 2V(meas.) = 73◦–78◦ Cell Data: Space Group: P 1. a = 8.816(3) b = 12.870(7) c = 6.678(1) α =90.36(2)◦ β = 109.05(2)◦ γ = 104.98(4)◦ Z=2 X-ray Powder Pattern: Jenifer mine, Boron, California, USA. 12.2 (100), 7.75 (80), 6.00 (30), 4.16 (30), 8.03 (15), 4.33 (15), 3.10 (15b) Chemistry: (1) (2) B2O3 43.07 42.95 CaO 13.92 13.84 Na2O 7.78 7.65 H2O 35.34 35.56 Total 100.11 100.00 • (1) Suckow mine, Boron, California, USA. -
THE MAIN-GROUP ELEMENTS Atomic Properties
THE MAIN-GROUP ELEMENTS Atomic Properties Properties of elements is based valence-shell electron configurations. Five atomic properties: 1. atomic radius 2. ionization energy 3. electron affinity 4. electronegativity 5. polarizability Atomic Size Adding more valence levels increases the distance from the electrons to the nucleus, it also decrease the effect the nucleus has on the outer electrons. decreases across a period Effective Nuclear Force increases down a group Valence levels Ionization Energy Ionization energy: the energy required to remove the most loosely held electron from an atom in the gaseous state. Size of Atom Ionization Energy Smaller size Higher ionization energy Electron Affinity The electron affinity is a release of energy to form an anion. Ionization Energy Electron Affinity Atoms with higher effective nuclear charges release more energy. Electronegativity Electronegativity is the tendency of an atom to attract electrons to itself. Ionization Energy Electronegativity Atoms with a greater effective nuclear charge have a stronger pull on bonding electrons. Large differences in electronegativity typically form ionic bonds and small differences from covalent bonds. Polarizability Polarizability is the ease an atoms electron cloud can be distorted. Size of Atom Polarizability Electron-rich, heavier atoms are easily polarized. High polarizing power atom-are small sized, highly charged atoms. Bonding Trends Elements in period 2 strictly follow the octet rule; carbon forms four bonds. Elements in Period 3 and higher periods exceed the octet. They reach higher oxidation states because they can access empty d-orbitals. Also, larger atoms can simply make more bonds to more neighbors . Group 1A: Alkali Metals The chemical properties of alkali metals are striking similar. -
Origin of the Kramer Borax Deposit, Boron, CA
A 50 year retrospective 1 OUTLINE 1. A brief history of borax 2. Kramer borax deposit a) Setting and Discovery b) Mineralogy of sedimentary borates c) Stratigraphy and Lithology d) Petrography and implications for geologic setting e) Solubility studies and modeling lake characteristics f) Comparable modern analogues 3. New evidence a) Turkish and Argentinian deposits b) Boron isotopic studies 4. Broader questions – Source water controls (thermal springs), B-As-Sb association, igneous-metamorphic controls on boron in thermal waters 2 Why give this talk? 1. Old (but rusty) material to me, new to most of you 2. Desire to see if ideas have changed in the past 50+ years. 3. Citation of my work even today suggests I did something right. 4. Wish to compare Kramer work with evidence from newer borate deposits in Turkey and South America 5. A wish to evaluate these ideas in light of new evidence using tools that weren’t available in 1964 6. A chance to ponder broader questions about boron’s geochemical cycle. 7. Work done so long ago that if you ask penetrating questions I can always plead a “senior moment” 3 What was unique about my research on the Kramer deposits? • Used a combination of geological tools (Field AND lab work – rare in 1964) • Stratigraphy, Petrography, and XRD based mineralogy • Experimental solubility studies of effects of other salts on Na-borate solubilities • Field studies of other possible borate environments (Borax Lake, Teels and Columbus Marsh, NV, Death Valley, Searles Lake) • Benefits of discussions with an all-star support team with similar interests (Mary Clark, Blair Jones, G.I. -
Bulletin of the Geological Society of Greece
Bulletin of the Geological Society of Greece Vol. 40, 2007 A PRELIMINARY STUDY OF THE COLEMANITE- RICH TUFF LAYER FROM THE SOURIDES AREA, KARLOVASSI BASIN, SAMOS ISLAND, HELLAS Kantiranis N. Aristotle University of Thessaloniki, Faculty of Sciences, School of Geology, Department of Min eralogy-Petrology-Economic Geology Filippidis A. Aristotle University of Thessaloniki, Faculty of Sciences, School of Geology, Department of Min eralogy-Petrology-Economic Geology Stamatakis M. National and Kapodistrian University of Athens, Faculty of Geology and Geoenvironment, Department of Economic Geology and Geochemistry Tzamos E. Aristotle University of Thessaloniki, Faculty of Sciences, School of Geology, Department of Min eralogy-Petrology-Economic Geology Drakoulis A. Aristotle University of Thessaloniki, Faculty of Sciences, School of Geology, Department of Min eralogy-Petrology-Economic Geology https://doi.org/10.12681/bgsg.16717 Copyright © 2018 N. Kantiranis, A. Filippidis, M. Stamatakis, E. Tzamos, A. Drakoulis To cite this article: http://epublishing.ekt.gr | e-Publisher: EKT | Downloaded at 20/02/2020 23:19:58 | Kantiranis, N., Filippidis, A., Stamatakis, M., Tzamos, E., & Drakoulis, A. (2007). A PRELIMINARY STUDY OF THE COLEMANITE-RICH TUFF LAYER FROM THE SOURIDES AREA, KARLOVASSI BASIN, SAMOS ISLAND, HELLAS. Bulletin of the Geological Society of Greece, 40(2), 769-774. doi:https://doi.org/10.12681/bgsg.16717 http://epublishing.ekt.gr | e-Publisher: EKT | Downloaded at 20/02/2020 23:19:58 | Δελτίο της Ελληνικής Γεωλογικής Εταιρίας τομ. -
Temperature and Relative Humidity (RH) Using Saturated Salt Solutions
THERMODYNAMICS OF 1:2 SODIUM BORATE MINERALS By LAURA SUZANNE RUHL A THESIS PRESENTED TO THE GRADUATE SCHOOL OF THE UNIVERSITY OF FLORIDA IN PARTIAL FULFILLMENT OF THE REQUIREMENTS FOR THE DEGREE OF MASTER OF SCIENCE UNIVERSITY OF FLORIDA 2008 1 © 2008 Laura Suzanne Ruhl 2 To my family, who have kept my inquisitive spirit and thirst for knowledge alive, always encouraging me, and giving me strength. 3 ACKNOWLEDGMENTS First and foremost, I thank the chair of my committee, Phil Neuhoff, for all of his time and all of the knowledge he has bestowed upon me throughout my time as his student. I would also like to thank my committee members, Ellen Martin and Guerry McClellan, for their time and support in my academic endeavors. I thank Jie Wang and Gökce Atalan for their help in the lab, for many scientific discussions and support. I also thank Derrick Newkirk for his unending encouragement and support. Major thanks go to my parents and siblings for always being there to help in any endeavor and their never-ending support and love. Lastly, I appreciate all of the never-ending encouragement from my friends and family. The National Science Foundation funded this project. 4 TABLE OF CONTENTS page ACKNOWLEDGMENTS ...............................................................................................................4 LIST OF TABLES...........................................................................................................................6 LIST OF FIGURES .........................................................................................................................7 -
United States Patent Office
2,983,577 United States Patent Office Patented May 9, 1961 2 Thus, contrary to the teachings of the prior art, I have found that kernite can be prepared synthetically from 2.983,577 borax providing certain conditions are maintained. First, an aqueous solution must be used which contains at least METHOD OF PRODUCING SODUMTETRA 28.0% by weight of borax, and secondly, the temperature BoRATE TETRAHYDRATE of the borax solution must be at a temperature of at least Vincent Morgan, Boron, Calif., assignor to United States 57.59 C. Borax & Chemical Corporation, Los Angeles, Calify As stated, kernite must be crystallized from solutions a corporation of Nevada containing at least 28% NaBO-10H2O. This means No Drawing. Filed Apr. 15, 1958, Ser. No. 728,545 i., v 10 that kernite can be crystallized from a 28% solution up to and including a 100% solution of the 10 mol borax. 2 Claims. (C. 23-59). If 10 mol borax is dissolved in its own water of hydra tion this solution can be used for the crystallization of kernite. This invention relates as indicated to a method for 15 According to the process of the present invention the producing sodium tetraborate tetrahydrate and has more 4 mol hydrate of sodium tetraborate may be prepared particular reference to a method for synthetically pro by first forming the 5 mole hydrate and then redissolving ducing kernite (NaBO'4H2O) from water solution at the 5 mole, hydrate in a solution saturated with respect atmospheric pressure. to the 5 mol hydrate and then crystallizing out the 4 mol The mineral kernite (NaBO'4H2O) is known to be 20 hydrate, or it may be crystallized directly from aqueous naturally occurring, and at one time was the major borate solution without having the 5 mol present at any time. -
Alphabetical List
LIST L - MINERALS - ALPHABETICAL LIST Specific mineral Group name Specific mineral Group name acanthite sulfides asbolite oxides accessory minerals astrophyllite chain silicates actinolite clinoamphibole atacamite chlorides adamite arsenates augite clinopyroxene adularia alkali feldspar austinite arsenates aegirine clinopyroxene autunite phosphates aegirine-augite clinopyroxene awaruite alloys aenigmatite aenigmatite group axinite group sorosilicates aeschynite niobates azurite carbonates agate silica minerals babingtonite rhodonite group aikinite sulfides baddeleyite oxides akaganeite oxides barbosalite phosphates akermanite melilite group barite sulfates alabandite sulfides barium feldspar feldspar group alabaster barium silicates silicates albite plagioclase barylite sorosilicates alexandrite oxides bassanite sulfates allanite epidote group bastnaesite carbonates and fluorides alloclasite sulfides bavenite chain silicates allophane clay minerals bayerite oxides almandine garnet group beidellite clay minerals alpha quartz silica minerals beraunite phosphates alstonite carbonates berndtite sulfides altaite tellurides berryite sulfosalts alum sulfates berthierine serpentine group aluminum hydroxides oxides bertrandite sorosilicates aluminum oxides oxides beryl ring silicates alumohydrocalcite carbonates betafite niobates and tantalates alunite sulfates betekhtinite sulfides amazonite alkali feldspar beudantite arsenates and sulfates amber organic minerals bideauxite chlorides and fluorides amblygonite phosphates biotite mica group amethyst