Dr. Sumbul Halim Khan
Total Page:16
File Type:pdf, Size:1020Kb
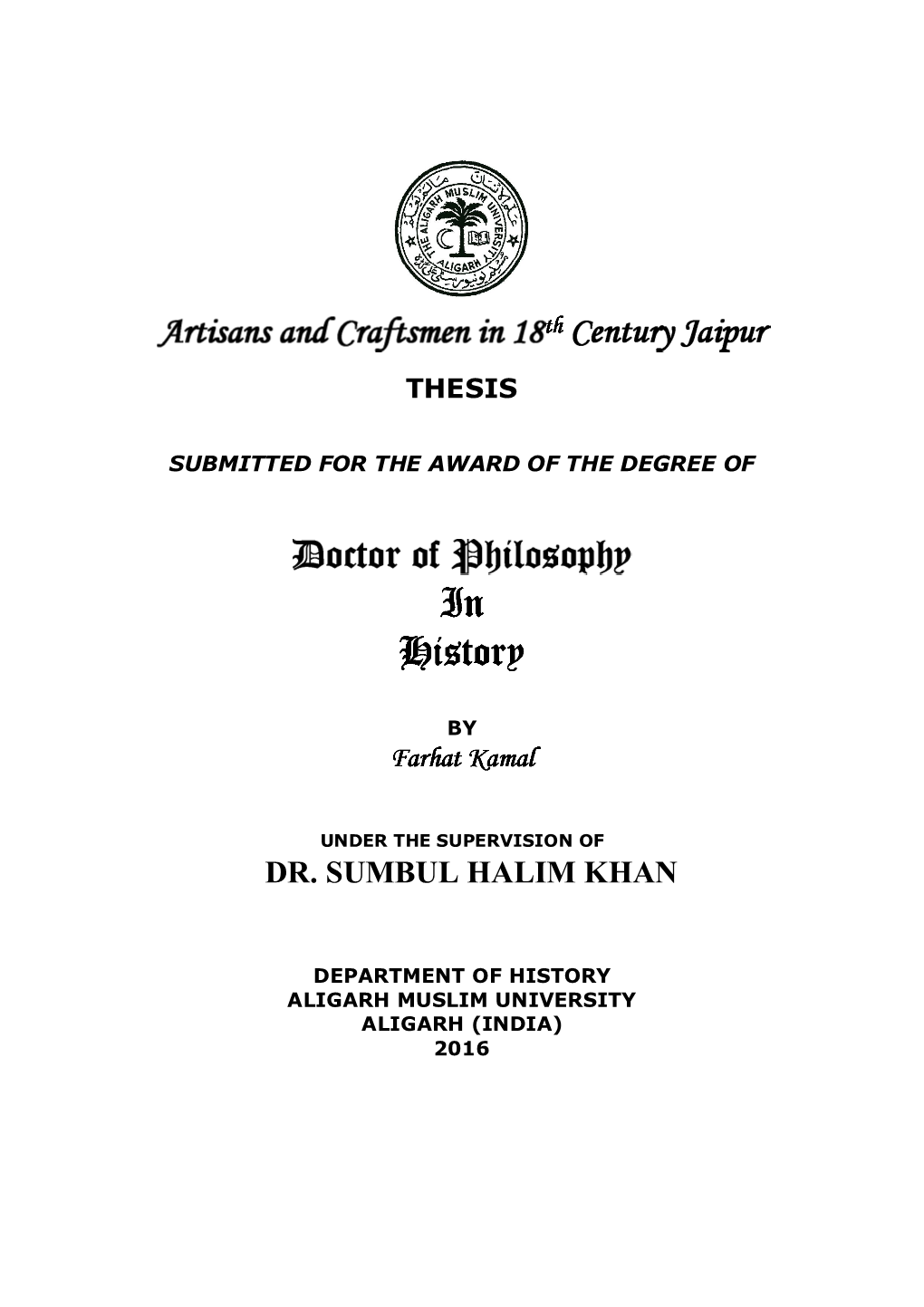
Load more
Recommended publications
-
In the Name of Krishna: the Cultural Landscape of a North Indian Pilgrimage Town
In the Name of Krishna: The Cultural Landscape of a North Indian Pilgrimage Town A DISSERTATION SUBMITTED TO THE FACULTY OF THE GRADUATE SCHOOL OF THE UNIVERSITY OF MINNESOTA BY Sugata Ray IN PARTIAL FULFILLMENT OF THE REQUIREMENTS FOR THE DEGREE OF DOCTOR OF PHILOSOPHY Frederick M. Asher, Advisor April 2012 © Sugata Ray 2012 Acknowledgements They say writing a dissertation is a lonely and arduous task. But, I am fortunate to have found friends, colleagues, and mentors who have inspired me to make this laborious task far from arduous. It was Frederick M. Asher, my advisor, who inspired me to turn to places where art historians do not usually venture. The temple city of Khajuraho is not just the exquisite 11th-century temples at the site. Rather, the 11th-century temples are part of a larger visuality that extends to contemporary civic monuments in the city center, Rick suggested in the first class that I took with him. I learnt to move across time and space. To understand modern Vrindavan, one would have to look at its Mughal past; to understand temple architecture, one would have to look for rebellions in the colonial archive. Catherine B. Asher gave me the gift of the Mughal world – a world that I only barely knew before I met her. Today, I speak of the Islamicate world of colonial Vrindavan. Cathy walked me through Mughal mosques, tombs, and gardens on many cold wintry days in Minneapolis and on a hot summer day in Sasaram, Bihar. The Islamicate Krishna in my dissertation thus came into being. -
Part 05.Indd
PART MISCELLANEOUS 5 TOPICS Awards and Honours Y NATIONAL AWARDS NATIONAL COMMUNAL Mohd. Hanif Khan Shastri and the HARMONY AWARDS 2009 Center for Human Rights and Social (announced in January 2010) Welfare, Rajasthan MOORTI DEVI AWARD Union law Minister Verrappa Moily KOYA NATIONAL JOURNALISM A G Noorani and NDTV Group AWARD 2009 Editor Barkha Dutt. LAL BAHADUR SHASTRI Sunil Mittal AWARD 2009 KALINGA PRIZE (UNESCO’S) Renowned scientist Yash Pal jointly with Prof Trinh Xuan Thuan of Vietnam RAJIV GANDHI NATIONAL GAIL (India) for the large scale QUALITY AWARD manufacturing industries category OLOF PLAME PRIZE 2009 Carsten Jensen NAYUDAMMA AWARD 2009 V. K. Saraswat MALCOLM ADISESHIAH Dr C.P. Chandrasekhar of Centre AWARD 2009 for Economic Studies and Planning, School of Social Sciences, Jawaharlal Nehru University, New Delhi. INDU SHARMA KATHA SAMMAN Mr Mohan Rana and Mr Bhagwan AWARD 2009 Dass Morwal PHALKE RATAN AWARD 2009 Actor Manoj Kumar SHANTI SWARUP BHATNAGAR Charusita Chakravarti – IIT Delhi, AWARDS 2008-2009 Santosh G. Honavar – L.V. Prasad Eye Institute; S.K. Satheesh –Indian Institute of Science; Amitabh Joshi and Bhaskar Shah – Biological Science; Giridhar Madras and Jayant Ramaswamy Harsita – Eengineering Science; R. Gopakumar and A. Dhar- Physical Science; Narayanswamy Jayraman – Chemical Science, and Verapally Suresh – Mathematical Science. NATIONAL MINORITY RIGHTS MM Tirmizi, advocate – Gujarat AWARD 2009 High Court 55th Filmfare Awards Best Actor (Male) Amitabh Bachchan–Paa; (Female) Vidya Balan–Paa Best Film 3 Idiots; Best Director Rajkumar Hirani–3 Idiots; Best Story Abhijat Joshi, Rajkumar Hirani–3 Idiots Best Actor in a Supporting Role (Male) Boman Irani–3 Idiots; (Female) Kalki Koechlin–Dev D Best Screenplay Rajkumar Hirani, Vidhu Vinod Chopra, Abhijat Joshi–3 Idiots; Best Choreography Bosco-Caesar–Chor Bazaari Love Aaj Kal Best Dialogue Rajkumar Hirani, Vidhu Vinod Chopra–3 idiots Best Cinematography Rajeev Rai–Dev D Life- time Achievement Award Shashi Kapoor–Khayyam R D Burman Music Award Amit Tivedi. -
List of Empanelled Artist
INDIAN COUNCIL FOR CULTURAL RELATIONS EMPANELMENT ARTISTS S.No. Name of Artist/Group State Date of Genre Contact Details Year of Current Last Cooling off Social Media Presence Birth Empanelment Category/ Sponsorsred Over Level by ICCR Yes/No 1 Ananda Shankar Jayant Telangana 27-09-1961 Bharatanatyam Tel: +91-40-23548384 2007 Outstanding Yes https://www.youtube.com/watch?v=vwH8YJH4iVY Cell: +91-9848016039 September 2004- https://www.youtube.com/watch?v=Vrts4yX0NOQ [email protected] San Jose, Panama, https://www.youtube.com/watch?v=YDwKHb4F4tk [email protected] Tegucigalpa, https://www.youtube.com/watch?v=SIh4lOqFa7o Guatemala City, https://www.youtube.com/watch?v=MiOhl5brqYc Quito & Argentina https://www.youtube.com/watch?v=COv7medCkW8 2 Bali Vyjayantimala Tamilnadu 13-08-1936 Bharatanatyam Tel: +91-44-24993433 Outstanding No Yes https://www.youtube.com/watch?v=wbT7vkbpkx4 +91-44-24992667 https://www.youtube.com/watch?v=zKvILzX5mX4 [email protected] https://www.youtube.com/watch?v=kyQAisJKlVs https://www.youtube.com/watch?v=q6S7GLiZtYQ https://www.youtube.com/watch?v=WBPKiWdEtHI 3 Sucheta Bhide Maharashtra 06-12-1948 Bharatanatyam Cell: +91-8605953615 Outstanding 24 June – 18 July, Yes https://www.youtube.com/watch?v=WTj_D-q-oGM suchetachapekar@hotmail 2015 Brazil (TG) https://www.youtube.com/watch?v=UOhzx_npilY .com https://www.youtube.com/watch?v=SgXsRIOFIQ0 https://www.youtube.com/watch?v=lSepFLNVelI 4 C.V.Chandershekar Tamilnadu 12-05-1935 Bharatanatyam Tel: +91-44- 24522797 1998 Outstanding 13 – 17 July 2017- No https://www.youtube.com/watch?v=Ec4OrzIwnWQ -
Administration of India Under the Mughul Emperors
Course: B.A History Honors Semester: B.A. 4th semester Code: 410 Topic:Administration of India under the Mughul Emperors Prepared by: Dr Sangeeta Saxena, Assistant Professor Department: History, Patna Women's College, Patna E mail: [email protected] Administration of India under the Mughul Emperors Content: 1 Central Administration of India under the Mughul emperors 2. Provincial Administration and local administration 3.. Military administration. 4. Financial Administration 5. Law and Justice. The Central Administration: Mughul emperors brought about certain fundamental changes in the administrative structure in India. Babur, the founder of the Mughul empire, assumed the title of Padshah (emperor) which was continued by his successors. It meant that the Mughul emperors did not accept the Khalifa even as their nominal overlord. Thus, the Mughul emperors were completely free from even the nominal authority of any foreign power or individual. Akbar enhanced further the power and prestige of the emperor. He declared himself the arbiter in case of difference of opinions regarding Islamic laws. The Mughul rule was also not theocratic. Except Aurangzeb no other Mughul emperor attempted to carry his administration on principles of Islam. The Mughul rule was not a police state as well. The emperors accepted two primary duties for themselves—Jahanbani (protection of the state) and Jahangiri (extension of the empire). Besides, they tried to create those conditions which were conducive to economic and cultural progress of their subjects. Another novelty of the Mughuls was that they began the policy of religious toleration. Babur and Humayun were no bigots while Akbar pursued the policy of equal respect to all religions. -
History) (M.A.History)
Directorate of Distance Education J.R.N. Rajasthan Vidyapeeth University Pratap Nagar, Udaipur Course Structure & Syllabus For MASTER OF ARTS (HISTORY) (M.A.HISTORY) 1 COURSE STRUCTURE SECOND YEAR: (FINAL) Code Course Title Credits MAHIS16 Historical Method and Historiography 7 MAHIS17 History of India (1526 to 1707) 7 MAHIS18 History of the Wodeyars of Mysore (1500 to 1956) 7 MAHIS19 History of Freedom Movement in India (1885-1947_ 7 MAHIS20 History of United States of America (1765-1990) 7 2 SYLLABUS (FINAL YEAR) MAHIS16: Historical Method and Historiography BLOCK 1: UNIT 1: Meaning and Definitions – Nature and Scope of History 1.0 Objectives 1.1 Introduction 1.2 Meaning and Definition 1.3 Nature of History 1.4 Scope of History 1.5 Let us sum up 1.6 Self Assessment Questions 1.7 Selected Bibliography UNIT 2: Subject Matter of History and kinds of History 2.0 Objectives 2.1 Introduction 2.2 Subject Matter of History 2.3 Kinds of History 2.4 Let us sum up 2.5 Self Assessment Questions 2.6 Books for further study UNIT 3: Purpose (Aims) and uses of History 3.0 Objectives 3.1 Introduction 3.2 Purpose (Aims) of History 3.3 Uses of History 3.4 Let us sum up 3.5 Self Assessment questions 3.6 Bibliography 3 UNIT 4: History and the relations with social science and other sciences 4.0 Objectives 4.1 Introduction 4.2 History and its relations with social sciences 4.2.1 History and Geography 4.2.2 History and political science 4.2.3 History and Economics 4.2.4 History and Sociology 4.2.5 History and Psychology 4.2.6 History and Ethics 4.2.7 History -
University of Mumbai Department of Music Sample of MCQ Question Paper for Students M.Mus Part 2 Paper -V Course Name – Music
University of Mumbai Department of Music Sample of MCQ Question Paper for Students M.mus part 2 paper -V Course Name – Music Education Paper/Subject Code_________ Student’s Seat No._____ Instrructions; 1. All the Questions are Compulsory Total Marks – 50 2. All Questions Carry Equal Marks 1. Name the artist from Kirana Gharana among the following a. Sangmeshwar Gurav b. Mallikarjun Mansoor c. Krishnarao Shankar Pandit d. Faiyyaz Khan 2. Name the student of Ustad Allauddin Khan a. Ust. Aliakbar Khan b. Kishore Kumar c. Gayatri Chitre d. MAnik Varma 3. Name disciple of Ust. Alladiya Khan among the following a. Kesarbai b. Hirabai c. Begam Akhtar d. Parveen Sultana 4. Where the Indira Kala Vishwavidyalay is Located? a. Pune b. Mumbai c. Khairagadh d. Nagpur 5. Among following who is awarded with Padmavibhushan? a. Pt. Rakesh Chaurasia b. Pt. Jasraj c. Pt. Mukund Lath d. Sumitra Guha 6. Who was the Guru of Kumar Gandharva? a. Saraswati Rane b. B.R. Deodhar c. Kagalkar buwa d. Bhaskarbuwa Bakhale 7. Who had written book on Aesthetics of Indian Music? a. Sudheer Nayak b. Manjiri Sinha c. Rama Deodhar d. Ashok D. Ranade 8. Among the following which is a performing art? a. Natya b. Pottery c. Poetry d. Sculpture 9. Who was titled as Swarbhaskar ? a. Prabhakar Karekar b. Vinay Mishra c. Rajan Sajan Mishra d. Bhimsen Joshi 10. Who was the only direct disciple of Kesarbai Kerkar? a. Dhondutai Kulkarni b. Parmeshwar Hegade c. Pahadi Sanyal d. Jaimala Shiledar 11. Name the famous stage actor-singer a. Saleel Choudhari b. -
Khanan: - Khan-I- Khanan Means Khan Among the Khans Or the Greatest Khan
Chapter 04 Akbar Class: 12th Khan-i- Khanan: - Khan-i- Khanan means Khan among the Khans or the greatest Khan. Akbar had bestowed this title upon his teacher and guardian Bairam Khan who had served him during the first four crucial years of his reign i.e. 1556-1569 A. D. Qanungo: - ‘Qanungo’ were local revenue officers who were conversant with the measurement of land, actual produce, state of cultivation and local prices etc. They were always ready to supply the government with useful information. Kirori: - Kirori were the revenue officials appointed by Akbar to collect revenue. They were responsible for the collection of a crore dams or Rs. 250,000. That is why they were called Kirors. They also checked their facts and figures supplied by the Qanungo. Bigha: - A ‘Bigha’ was a measurement of land used for fixing the state’s demand in the produce. The size and the kind of land held by a peasant was recorded in ‘bighas’. The revenue payable was fixed on the basis of average produce thereupon. Zabti: - The system of measurement and assessment of revenue based on actual size of the holding and the type of productivity was called Zabti. This system, which was first introduced by Raja Todar Mal under Sher Shah Suri was later on adopted by Akbar with some modifications. Dahsala: - 'Dahsala' was the system of revenue assessment based on figures of the last ten years. It was introduced by Akbar in 1580 A.D. It was calculated on the average produce and prices of different crops during the last ten years. -
Central Administration of Akbar
Central Administration of Akbar The mughal rule is distinguished by the establishment of a stable government and other social and cultural activities. The arts of life flourished. It was an age of profound change, seemingly not very apparent on the surface but it definitely shaped and molded the socio economic life of our country. Since Akbar was anxious to evolve a national culture and a national outlook, he encouraged and initiated policies in religious, political and cultural spheres which were calculated to broaden the outlook of his contemporaries and infuse in them the consciousness of belonging to one culture. Akbar prided himself unjustly upon being the author of most of his measures by saying that he was grateful to God that he had found no capable minister, otherwise people would have given the minister the credit for the emperor’s measures, yet there is ample evidence to show that Akbar benefited greatly from the council of able administrators.1 He conceded that a monarch should not himself undertake duties that may be performed by his subjects, he did not do to this for reasons of administrative efficiency, but because “the errors of others it is his part to remedy, but his own lapses, who may correct ?2 The Mughal’s were able to create the such position and functions of the emperor in the popular mind, an image which stands out clearly not only in historical and either literature of the period but also in folklore which exists even today in form of popular stories narrated in the villages of the areas that constituted the Mughal’s vast dominions when his power had not declined .The emperor was looked upon as the father of people whose function it was to protect the weak and average the persecuted. -
Mgt-7 31.03.2021
FORM NO. MGT-7 Annual Return [Pursuant to sub-Section(1) of section 92 of the Companies Act, 2013 and sub-rule (1) of (other than OPCs and Small rule 11of the Companies (Management and Companies) Administration) Rules, 2014] Form language English Hindi Refer the instruction kit for filing the form. I. REGISTRATION AND OTHER DETAILS (i) * Corporate Identification Number (CIN) of the company Pre-fill Global Location Number (GLN) of the company * Permanent Account Number (PAN) of the company (ii) (a) Name of the company (b) Registered office address (c) *e-mail ID of the company (d) *Telephone number with STD code (e) Website (iii) Date of Incorporation (iv) Type of the Company Category of the Company Sub-category of the Company (v) Whether company is having share capital Yes No (vi) *Whether shares listed on recognized Stock Exchange(s) Yes No Page 1 of 19 (a) Details of stock exchanges where shares are listed S. No. Stock Exchange Name Code 1 2 (b) CIN of the Registrar and Transfer Agent Pre-fill Name of the Registrar and Transfer Agent Registered office address of the Registrar and Transfer Agents (vii) *Financial year From date 01/04/2020 (DD/MM/YYYY) To date 31/03/2021 (DD/MM/YYYY) (viii) *Whether Annual general meeting (AGM) held Yes No (a) If yes, date of AGM 29/09/2021 (b) Due date of AGM 30/09/2021 (c) Whether any extension for AGM granted Yes No II. PRINCIPAL BUSINESS ACTIVITIES OF THE COMPANY *Number of business activities 1 S.No Main Description of Main Activity group Business Description of Business Activity % of turnover Activity Activity of the group code Code company G G2 III. -
MUGHAL EMPIRE Mughal Administration
M A HISTORY SEM-2 HY222 INDIAN HISTORY-2 MODULE-5 MUGHAL EMPIRE Mughal Administration Sources of information The Ain-I-Akbari of Abul Fazl Tabqat-I-Akbari of Nizam-ud-din Official handbooks or Dastur-ul-Amals Mundtakhab-ul-Tavarikh of Badauni Iqbal Namah of Muhammad Khan Foreign accounts and factory records Padshah Namah of Abdul Hamid Lahauri MUGHAL ADMINISTRATION • The history of the Mughals from 1526-1707 • Colorful and Splendid • Brought about immense Prestige • Beautification of Delhi • Development of administrative apparatus • Started purely as a military state but gradually gained the acceptance of the people • National Character under Akbar but reversed by Aurangzeeb Nature of Government • It was a military rule and was necessarily a centralised despotism • To the Muslims King was the head of government and religion • To the non-Muslims King was only their temporal head • Success of administration depended upon the personality of the King • Mughals were indebted to Shershah and the Persin rulers for administration Central Government • The King was the pivot of all administrative machinery • The power of the King depended upon the strength of the army under his command • There was no accepted law of succession • The rulers did not recognised any Khalifa as a superior overlord • The Kings except a few were hardworking in nature Central Government • Ministers are • Vakil or Prime Minister-important Vakils under Akbar were Bairam Khan and Sadullah Khan • Diva-I-Ala or Finance Minister-Muzafar Khan,Todarmal and Shah Manzur • -
SRNO FOLIO NO NAME Shares As on March 31, 2017 1 0000019 K VISWANATHAN 20 2 0000231 BHARAT MULCHAND CHOKSEY 212 3 0000234 PRAN K
GOODYEAR INDIA LIMITED Registered Office: Mathura Road, Ballabgarh (Dist. Faridabad) - 121 004, Haryana, Corporate Office: 1st Floor, ABW Elegance Tower, Plot no. 8, Commercial Centre Jasola – 110 025, New Delhi, India CIN: L25111HR1961PLC008578 Email – [email protected],Website –www.goodyear.co.in Details of Shareholders and Equity Shares due for transfer to IEPF Suspense Account in respect of which Dividends have been unpaid/unclaimed since financial year ended December 31, 2008 Shares as on SRNO FOLIO_NO NAME March 31, 2017 1 0000019 K VISWANATHAN 20 2 0000231 BHARAT MULCHAND CHOKSEY 212 3 0000234 PRAN KRISHANA MUKHERJEE 20 4 0000258 ULLAL VARADARAJA NAYAK 64 5 0000271 SACHINDRA NATH BASU 578 6 0000490 RAJENDRA KISHORE BAIJAL 2 7 0000623 KUNDAN LAL KOHLI 318 8 0000702 JAGDISH PRASHAD PANNALAL AND CO PVT LTD 190 9 0000716 CLIVE STREET NOMINEES PVT LTD 176 10 0000750 MOTI LOKUMAL JHANGIANI 70 11 0000759 BANTVAL SIVA RAO 560 12 0000800 MOHINDRA NATH 145 13 0000829 MOHAN LAL LATH 36 14 0000916 AMAR KRISHNA PODDER 26 15 0001010 PRAPHULLA KUMAR SEN 286 16 0001059 SOHAN LAL BERRY 2 17 0001091 SITA BHAGAT 10 18 0001106 SATYA PAL 22 19 0001218 BABOO HAYATH SAHAB 140 20 0001260 JETHALAL GOKALDAS UDESHI 9 21 0001273 SURATH CHANDRA ROY 72 22 0001274 VIDYA PRAKASH SARNA 78 23 0001297 KISHORI LAL AGARWALA 56 24 0001319 NIHAL DEVI AHUJA 8 25 0001349 HIRA LAL ARORA 56 26 0001351 ROSHAN LAL ARORA 28 27 0001358 JANAK AWASTI 46 28 0001359 GULAMALI MOHMED BABVANI 18 29 0001369 NANAK CHAND RAI BAHADUR 144 30 0001454 SATHANALA BHULOKAMU -
Annual Report 1990 .. 91
SANGEET NAT~AKADEMI . ANNUAL REPORT 1990 ..91 Emblem; Akademi A wards 1990. Contents Appendices INTRODUCTION 0 2 Appendix I : MEMORANDUM OF ASSOCIATION (EXCERPTS) 0 53 ORGANIZATIONAL SET-UP 05 AKADEMI FELLOWSHIPS/ AWARDS Appendix II : CALENDAR OF 19900 6 EVENTS 0 54 Appendix III : GENERAL COUNCIL, FESTIVALS 0 10 EXECUTIVE BOARD, AND THE ASSISTANCE TO YOUNG THEATRE COMMITTEES OF THE WORKERS 0 28 AKADEMID 55 PROMOTION AND PRESERVATION Appendix IV: NEW AUDIO/ VIDEO OF RARE FORMS OF TRADITIONAL RECORDINGS 0 57 PERFORMING ARTS 0 32 Appendix V : BOOKS IN PRINT 0 63 CULTURAL EXCHANGE Appendix VI : GRANTS TO PROGRAMMES 0 33 INSTITUTIONS 1990-91 064 PUBLICATIONS 0 37 Appendix VII: DISCRETIONARY DOCUMENTATION / GRANTS 1990-91 071 DISSEMINATION 0 38 Appendix VIll : CONSOLIDATED MUSEUM OF MUSICAL BALANCE SHEET 1990-91 0 72 INSTRUMENTS 0 39 Appendix IX : CONSOLIDATED FINANCIAL ASSISTANCE TO SCHEDULE OF FIXED CULTURAL INSTITUTIONS 0 41 ASSETS 1990-91 0 74 LIBRARY AND LISTENING Appendix X : PROVIDENT FUND ROOMD41 BALANCE SHEET 1990-91 078 BUDGET AND ACCOUNTS 0 41 Appendix Xl : CONSOLIDATED INCOME & EXPENDITURE IN MEMORIAM 0 42 ACCOUNT 1990-91 KA THAK KENDRA: DELHI 0 44 (NON-PLAN & PLAN) 0 80 JA WAHARLAL NEHRU MANIPUR Appendix XII : CONSOLIDATED DANCE ACADEMY: IMPHAL 0 50 INCOME & EXPENDITURE ACCOUNT 1990-91 (NON-PLAN) 0 86 Appendix Xlll : CONSOLIDATED INCOME & EXPENDITURE ACCOUNT 1990-91 (PLAN) 0 88 Appendix XIV : CONSOLIDATED RECEIPTS & PAYMENTS ACCOUNT 1990-91 (NON-PLAN & PLAN) 0 94 Appendix XV : CONSOLIDATED RECEIPTS & PAYMENTS ACCOUNT 1990-91 (NON-PLAN) 0 104 Appendix XVI : CONSOLIDATED RECEIPTS & PAYMENTS ACCOUNT 1990-91 (PLAN) 0 110 Introduction Apart from the ongoing schemes and programmes, the Sangeet Natak Akademi-the period was marked by two major National Academy of Music, international festivals presented Dance, and Drama-was founded by the Akademi in association in 1953 for the furtherance of with the Indian Council for the performing arts of India, a Cultural Relations.