An Immersed Tunnel, Better Than a Long Span Bridge?
Total Page:16
File Type:pdf, Size:1020Kb
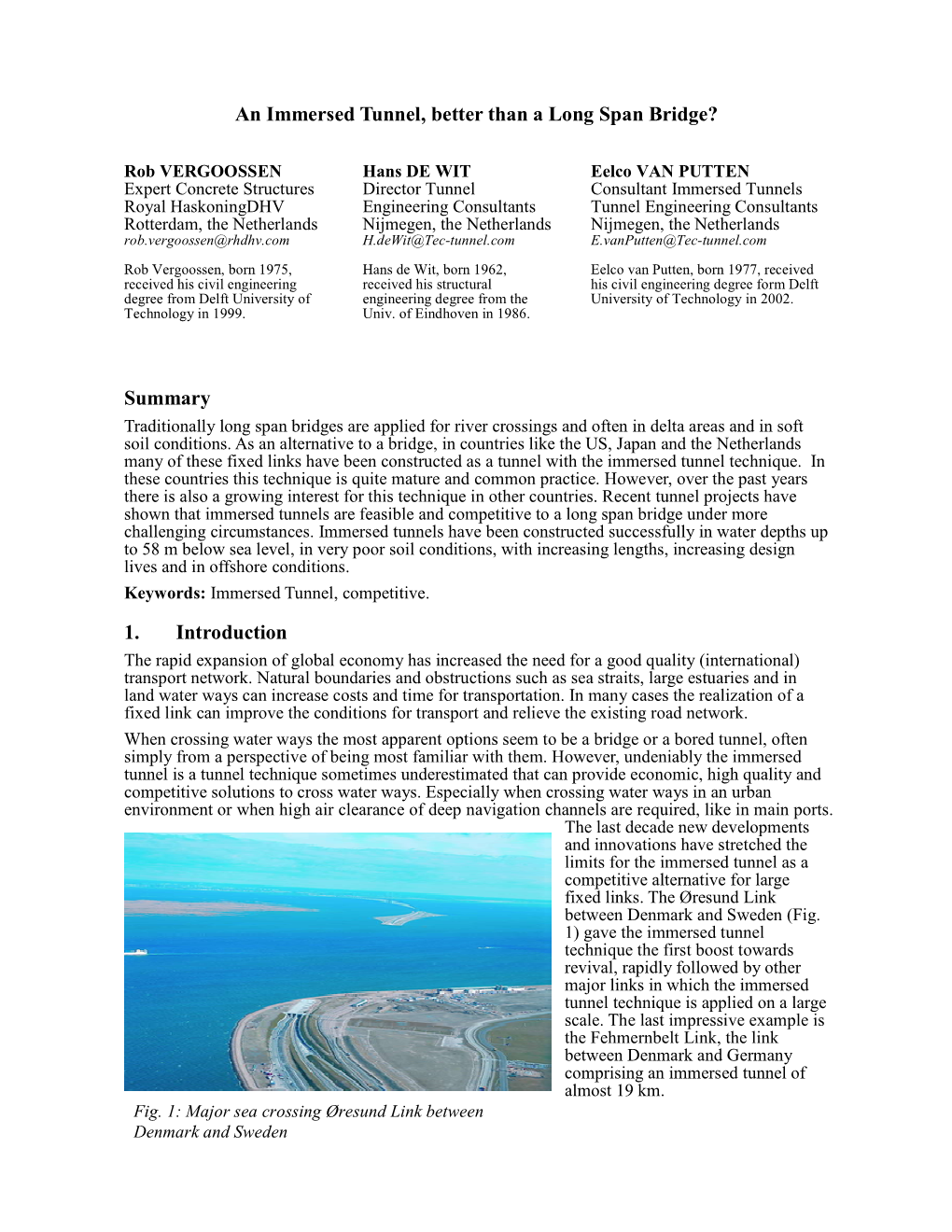
Load more
Recommended publications
-
Marmaray Project - Turkey
MARMARAY PROJECT - TURKEY Istanbul is a city where historical and cultural values must be preserved and at the same time modern railway facilities have to be installed to decrease the environmental impact of public transportation and increase the capacity, reliability and comfort of the railway systems. The Project provides an upgrading of the commuter rail system in Istanbul, connecting Halkalı on the European side to the Asian side with an uninterrupted, modern, high-capacity commuter rail system. Railway tracks in both sides of Istanbul Strait will be connected to each other through a railway tunnel connection under the Istanbul Strait. The line goes underground at Yedikule, continues through the Yenikapı and Sirkeci new underground stations, passes under the Istanbul Strait, connects to the Üsküdar new underground station and emerges at Sögütlüçesme. The entire upgraded and new railway system will be approximately 76 km long. The main structures and systems; include the immersed tube tunnel, bored tunnels, cut-and-cover tunnels, at - grade structures, three new underground stations, 37 surface stations (renovation and upgrading), operations control centre, yards, workshops, maintenance facilities, upgrading of existing tracks including a new third track on ground, completely new electrical and mechanical systems and procurement of modern railway vehicles. The idea of a railway tunnel under the Istanbul Strait was first raised in 1860. However, where the tunnel under the Istanbul Strait crosses the deepest parts of the Strait, the old-fashioned techniques would not allow the tunnel to be on or under the seabed, and therefore the design indicated a "floating" type of tunnel placed on pillars constructed on the seabed. -
Arcadius 8; (Column
index INDEX 319 Arcadius 8; (column of) 184 Balat 213–14 Archaeological Museum 93ff Baldwin, Count of Flanders 15 Argonauts, myth of 259, 263, 276 Balıklı Kilisesi 197–98 Major references, in cases where many are listed, are given in bold. Numbers in italics Armenian, Armenians 25, 189, 192, Balkapanı Han 132 are picture references. 193, 241–42, 258, 278; (Cemetery) Baltalimanı 258 268; (Patriarchate) 192 Balyan family of architects 34, 161, 193; Arnavutköy 255 (burial place of) 268 A Alexander, emperor 67 Arsenal (see Tersane) Balyan, Karabet 34, 247 Abdülaziz, sultan 23, 72, 215, 251; Alexander the Great 7; (sculptures of) 96 Ashkenazi Synagogue 228 Balyan, Kirkor 34, 234 (burial place of) 117 Alexander Sarcophagus 94, 95 Astronomer, office of 42 Balyan, Nikoğos 34, 246, 247, 249, Abdülhamit I, sultan 23, 118; (burial Alexius I, emperor 13, 282 At Meydanı (see Hippodrome) 252, 255, 274, 275 place of) 43 Alexius II, emperor 14 Atatürk 24, 42, 146, 237, 248; Balyan, Sarkis 34, 83, 247, 258, 272, Abdülhamit II, sultan 23, 251, 252, Alexius III, emperor 14 (Cultural Centre) 242; (Museum) 243; 267 278; (burial place of) 117 Alexius IV, emperor 15 (statue of) 103 Bank, Ottoman 227 Abdülmecit I, sultan 71, 93, 161, 164, Alexius V, emperor 15 Atik Ali Pasha 171; (mosque of) 119 Barbarossa, pirate and admiral 152, 247; (burial place of) 162 Ali Pasha of Çorlu, külliye of 119–20 Atik Mustafa Paşa Camii 216 250, 250; (burial place of) 250; Abdülmecit II, last caliph 24 Ali Sufi, calligrapher 157, 158 Atik Sinan, architect 130, 155, 212; (ensign -
Exports: the Heart of Nep
How to Export to 2018 Turkey This report includes all the information related to trade basics and detailed data regarding export from Brazil to Turkey. This report is for information purposes only and Tumer Eng. will not be liable to any direct, indirect, incidental, special, consequential or exemplary damages, including but not limited to, damages for loss of profits, goodwill, use, data, or other intangible losses. Ver:1.0 2018 1 Contents 1 Why Turkey.................................................................................................................................... 12 1.1 General Information .............................................................................................................. 12 1.2 Geography ............................................................................................................................. 13 1.2.1 Distances ....................................................................................................................... 18 1.2.2 Climate of Turkey .......................................................................................................... 19 1.2.2.1 Air temperature changes until now .......................................................................... 20 1.2.2.2 Precipitation changes until now ................................................................................ 21 1.2.2.3 Air temperature changes in the 21st century ........................................................... 21 1.2.2.4 Precipitation changes in the 21st century ................................................................ -
L-G-0008366837-0017086142.Pdf
Nuh Bilgin Hanifi Copur Cemal Balci TBM Excavation in Difficult Ground Conditions TBM Excavation in Difficult Ground Conditions Case Studies from Turkey Nuh Bilgin Hanifi Copur Cemal Balci Prof. Dr. Nuh Bilgin Prof. Dr. Hanifi Copur Prof. Dr. Cemal Balci Istanbul Technical University Faculty of Mines, Mining Engineering Department 34469 Maslak/Istanbul Turkey Cover: Methane Explosion in the Pressure Chamber of a Tunnel Boring Machine Photo: Bilgin/Copur Library of Congress Card No.: applied for British Library Cataloguing-in-Publication Data A catalogue record for this book is available from the British Library. Bibliographic information published by the Deutsche Nationalbibliothek The Deutsche Nationalbibliothek lists this publication in the Deutsche Nationalbibliografie; detailed bibliographic data are available on the Internet at <http://dnb.d-nb.de>. © 2016 Wilhelm Ernst & Sohn, Verlag für Architektur und technische Wissenschaften GmbH & Co. KG, Rotherstraße 21, 10245 Berlin, Germany All rights reserved (including those of translation into other languages). No part of this book may be reproduced in any form – by photoprinting, microfilm, or any other means – nor transmitted or translated into a machine language without written permission from the publishers. Registered names, trademarks, etc. used in this book, even when not specifically marked as such, are not to be considered unprotected by law. Coverdesign: Sonja Frank, Berlin Production Management: pp030 – Produktionsbüro Heike Praetor, Berlin Typesetting: Reemers Publishing Services -
TBM FACT Sheet (Lgrev).Pub
Chesapeake Bay Bridge-Tunnel Parallel Thimble Shoal Tunnel Project For more contest information, visit www.cbbt.com/TBMNamingContest/ For more project information, visit www.cbbt.com/parallelthimbleshoaltunnel/ Tunnel Boring Machine To Cape Charles, VA PROJECT DESCRIPTION The Chesapeake Bay Bridge-Tunnel is a 17.6 mile bridge and tunnel complex that spans the lower Chesapeake Bay and connects Virginia’s Eastern Shore with the mainland in Virginia #2 Island Proposed Beach. The Parallel Thimble Shoal Tunnel project will involve the construction of a two-lane bored tunnel from the CBBT’s southernmost island (#1 Island) under Thimble Shoal Channel to #2 Island. This will be the FIRST bored roadway tunnel in the Hampton Roads region as well as the Commonwealth. Not only did this bored tunnel solution offer a less expensive Parallel Existing Thimble Thimble Shoal Shoal Tunnel price tag, but it will have less environmental impact than the traditional immersed tube tunnel construction and will have less impact on the ship traffic that sails Thimble Shoal Channel. Tunnel When complete, this tunnel, which runs parallel to the existing tunnel, will carry southbound traffic headed towards Virginia’s mainland. CONTRACTOR: Chesapeake Tunnel Joint Venture COST: $755,987,318 Hydraulic Rams What is a Tunnel Boring Machine (TBM)? Rotating Arm A TBM is a machine used to excavate tunnels. This machine operates #1 Island like a giant drill, but one that builds as it drills. Here’s how it works: The large rotating cutter head scrapes away soil under the bay bottom. The soil is removed from the machine via a large conveyor system and hauled away. -
A. Minutes from the November 19, 2020 HRTPO Board Meeting
ITEM #7: APPROVAL OF CONSENT ITEMS [Action Requested] A. Minutes from the November 19, 2020 HRTPO Board Meeting Minutes from the November 19, 2020 HRTPO Board meeting are attached. Attachment 7-A RECOMMENDED ACTION: Approve the minutes. B. HRTPO Financial Statement The Statement of Revenues and Expenditures for the activities of November 2020 is attached. This statement reflects the financial status of the HRTPO as a whole. Attachment 7-B RECOMMENDED ACTION: Accept the HRTPO Financial Statement. HRTPO Board Meeting │ January 21, 2021│ Agenda Hampton Roads Transportation Planning Organization Board Summary Minutes of November 19, 2020 Pursuant to the declared state of emergency in the Commonwealth of Virginia in response to the COVID-19 pandemic and to protect the public health and safety of the Board members, staff, and the general public, the HRTPO Board Meeting was held electronically via Zoom with the following in attendance: HRTPO Voting Members in Attendance: Donnie Tuck, Chair (HA) Douglas Pons (WM) Rick West, Vice-Chair (CH) Thomas Shepperd (YK) Frank Rabil (FR) Delegate Stephen Heretick (GA)* Phillip Bazzani (GL) Delegate Jeion Ward (GA) Michael Hipple (JC) William Harrell (HRT) David Jenkins (NN Alternate) Zach Trogdon (WATA) Kenneth Alexander (NO)* Christopher Hall (VDOT) Herbert Green (PQ Alternate) Jennifer DeBruhl (DRPT Alternate)* John Rowe, Jr. (PO) Cathie Vick (VPA Alternate)* Robert Dyer (VB) HRTPO Nonvoting Members in Attendance: Christopher Price (CH) J. Randall Wheeler (PQ)* Amanda Jarratt (FR) Michael Johnson (SH) J. Brent Fedors (GL) Albert Moor (SU) Mary Bunting (HA) Patrick Duhaney (VB)* Randy Keaton (IW) Andrew Trivette (WM)* Scott Stevens (JC)* Neil Morgan (YK) Cynthia Rohlf (NN) Terry Danaher (CAC) Larry “Chip” Filer (NO)* Jenifer Spratley (PAA) HRTPO Executive Director: Robert A. -
Civil Engineering
Civil Engineering Volume 170 Issue CE2 May 2017 ■ Stabilising Lyme Regis – a strategic approach ■ Planning and procuring the Shatin–Central cross-harbour rail tunnel, Hong Kong ■ Innovative uses of thermal imaging in civil engineering ■ Sustainable post-earthquake reconstruction in Pakistan www.civilengineering-ice.com ISSN 0965 089 X Call for Papers Cities of the future Proceedings of the Institution of Civil Engineers Civil Engineering SPECIAL ISSUE Editors: Philippe Bouillard, Université Libre de Bruxelles, Brussels, Belgium and Priti Parikh, University College London, London, UK Civil Engineering is planning a special issue for Why publish with ICE? 2018 on cities of the future. Access to ICE membership – ICE Publishing, as the publishing arm of ICE, is the only publisher The 21st century has seen a rapid increase in population with over 50% of the that brings you direct access to ICE’s worldwide world’s population living in cities. According to report from the Organisation membership of 80 000. for Economic Co-operation and Development, the urban population will Visibility – we also have thousands of readers increase from less than 1 billion in 1950 to roughly 6 billion by 2050 to who are not members of ICE, from corporations, around 9 billion people by end of this century. Rapid urbanisation has brought to governments, to universities. Our journals in pressures and challenges for the built environment, infrastructure and are included in major engineering indexes and resource allocation in cities. There is a need to rethink engineering design and resources. strategies for future cities. This can be achieved by going beyond the physical appearance and by Quality – our journals’ reputation for quality focusing on different representations, properties and impact factors of the is unsurpassed, ensuring that the originality, urban system. -
I-64/Hampton Roads Bridge-Tunnel (HRBT) – Project Update
Hampton Roads Bridge Tunnel Expansion: Project Development Update May 17, 2018 James S. Utterback HRBT Project Director Virginia Department of Transportation 5/17/2018 Ten Hampton Roads Tunnels Chesapeake Channel Tunnel (1964) Hampton Roads Bridge-Tunnel (1957 & 1976) Thimble Shoal Tunnel (1964) Monitor-Merrimac Memorial Bridge- Tunnel (1992) Midtown Tunnel Downtown (1962 & 2016) Tunnel (1952 & 1987) 5/17/2018 3 • • • 5/17/2018 1950 Future tunnel #11 at Thimble Shoal will be bored tunnel Thimble Shoal will Future tunnel#11at 1 tunnel is concrete-box immersed tube 9 tunnels immersed tubes are steel-shell Downtown Tunnel #1 1955 Hampton Roads #1 1960 Midtown Tunnel #1 1965 Thimble Shoal #1 & Chesapeake #1 1970 of Tunneling 65 Years in Hampton Roads 1975 Hampton Roads #2 1980 1985 Downtown Tunnel #2 1990 Monitor-Merrimac 1995 2000 2005 2010 1976 2015 Midtown Tunnel #2 4 2020 HRBT Expansion - Scope of Work . Between Settlers Landing in Hampton and I-564 in Norfolk . Improvements in I- 64 including the construction of a new 4 lane HRBT tunnel . New 4 lane HRBT tunnel will serve Eastbound traffic . 2 existing HRBT tunnels will serve Westbound traffic Proposed Tunnel Alignment (Hampton Side) 6 5/17/2018 Proposed Tunnel Alignment (Norfolk Side) 5/17/2018 7 Proposed Lane Configuration for Tunnel and Approach Bridges 2+1+1 concept in each direction: • 2 free General Purpose lanes • 1 full-time HOT lane • 1 peak-hour HOT lane on left shoulder 5/17/2018 8 Tunnel Considerations Landside work has risks but is largely conventional Tunnel work is less -
The Effect of Wave Passage on Immersed Tube Tunnels - Busan Geoje Fixed Link in South Korea
IABSE SYMPOSIUM WEIMAR 2007 The effect of wave passage on immersed tube tunnels - Busan Geoje Fixed Link in South Korea Ronald HEIJMANS Peter JACKSON Dr. Thomas KASPER Civil Engineer Geotechnical Engineer Civil Engineer ARCADIS Infra, Cowi Cowi Amersfoort, The Netherlands Copenhagen, Denmark Copenhagen, Denmark [email protected] [email protected] [email protected] Guido MEINHARDT Jean SCHMITT Dr. Hessel VOORTMAN Geotechnical Engineer Project Engineer-in-charge Hydraulic Engineer ARCADIS Infra Ingerop ARCADIS Infra, Amersfoort, The Netherlands Paris, France Amersfoort, The Netherlands [email protected] [email protected] [email protected] Summary A special feature of the Busan-Geoje Fixed Link in South Korea is the foundation of an immersed tube tunnel in a trench of soft marine clay. The tunnel is subject to wave loads due to 9.2 meter high hurricane waves which jeopardize the stability of the tunnel. Analytical analyses, scale model tests and numerical analyses have been made to investigate this problem. This paper gives an overview of the analyses, performed from schematization of the non-linear waves to pressure variations at seabed, modelling of the wave induced groundwater flow and its effects on the tunnel buried in the seabed. This is followed by a discussion of the results and consequences for the design of the tunnel. Keywords: immersed tube tunnel; wave effect; numerical modelling, non-linear waves 1. Introduction 1.1 Introduction of the project The Busan Geoje Fixed Link consists of an 8.2 km long motorway with two large cable stayed bridges and a 3.3 km long immersed tube tunnel as main structures. -
Dynamic Analysis of an Immersed Tunnel in Izmir
Dynamic analysis of an immersed tunnel in Izmir Análisis dinámico de un túnel sumergido en Izmir Isfendiyar Egeli (Main Author) Usak University, Civil Engineering Department Bir Eylul Campus, 64000, Usak (Turkey) İ[email protected] Cagdas Gurbuz (Corresponding Author) Graduate Research Student, Izmir Institute of Technology Urla Campus, 35430, Izmir (Turkey) [email protected] Manuscript Code: 885 Date of Acceptance/Reception: 17.04.2018/27.01.2017 DOI: 10.7764/RDLC.17.1.103 Abstract The original design of the planned Izmir Bay Immersed Tube Tunnel, considered it to be a continuous subsea tunnel for the whole length of about 7.6 km. But this was later changed into having 2 shorter tubes of 2.7 km long each connected thru’ a 2.2 km long artificial island created in the middle of the bay from the excess dredged material, a concept which also reduces costs and increases efficiency. This island will serve as a venue for the 2025 Expo Exhibition, which Izmir city will apply to organize in the future. Reason for the research study was to provide a preliminary design, using a dynamic analysis, during the current pre-feasibility stage, of the immersed tunnel to show whether it can be built across the Izmir Bay. This paper takes into account the new alignment and presents the results of a 2-D dynamic analysis conducted of the prefabricated 100m long tunnel elements, sitting within a backfilled dredged ditch, dug after the recommended ground improvement was carried out. Analyses considered staged construction and the results showed that: Tunnel units and its surrounding soils inside the dredged ditch act together to provide a better earthquake response with a damping effect of the earthquake force; Tunnel units do not float to the sea surface, but continued to stay inside the dredged ditch and applied positive stresses to the foundations during the design earthquakes. -
Marmaray Tunnel Under the Sea: Public Safety, Cellular and GSMR Coverage in the Marmaray Tunnel
Cobham Wireless Case Study Marmaray tunnel Under the sea: public safety, cellular and GSMR Coverage in the Marmaray Tunnel Overview The project involved providing public safety, cellular and GSM-R connectivity for the Marmaray underground tunnel, a 13.6km long section of the Marmaray rail project. The tunnel connects Europe to Asia via an undersea tunnel crossing the Bosphorus strait. It is of significant strategic importance to Turkey, so a solution was required which would deliver reliable connectivity to the rail operator, the emergency services and commuters. Challenge Undersea tunnels are a challenging environment to provide coverage. Users of the network should The Challenge also not experience loss of communication while The Marmaray tunnel is a 13.6km long undersea tunnel, with three underground entering or exiting the tunnel, which provides an stations along the route. The tunnel connects Europe to Asia via the Bosphorus strait. additional challenge. A solution was required that would be capable of providing consistent and The project required providing public safety services and critical communications to the reliable public safety, cellular and GSM-R emergency services (police, fire service and ambulance service). connectivity throughout the tunnel. With such a critical project, it was also important Cellular connectivity was also required to connect rail passengers using three Turkish that the deployment was completed in time for operator networks, and GSM-R connectivity needed to be provided for the rail operator. the official opening of the tunnel. Therefore, a system was needed that could accommodate multiple radio technologies such as TETRA, UHF and VHF analogue (later migrated to VHF APCO), GSM, UMTS and The Tech GSM-R. -
HRBT EXPANSION Magazine
HRBT EXPANSION Spring 2020 HRBT EXPANSION Magazine IN THIS ISSUE Project Project Tunnel Boring Community Overview Timeline Approach Outreach 5 6 12 14 ABOUT THE PROJECT TEAM HRBT Message from Jim Utterback EXPANSION As the largest project in VDOT history, the HRBT Expansion Secretary of Transportation Project Financing TABLE OF Project is the long-awaited improvement to a major CONTENTS chokepoint in Hampton Roads. We’ve assembled a world- Shannon Valentine Project Team ........................... 3 class team of experts in bridge and tunnel construction. Project Overview ................ 4-5 We are currently working in the design phase with construction anticipated in Summer 2020. In the meantime, Project Timeline ..................6-7 VDOT Executive Committee the team is working on utility relocations and other Commonwealth History Of The Tunnels ......8-9 preparation activities to support construction. While much Stephen Brich: Commissioner Transportation Board Staff Spotlight ..................... 10 of the work (tunnel) will be happening underwater, there is Robert Cary: Deputy Commissioner still a lot of marine works and interstate widening as part Barton Thrasher: Chief Engineer Economic Impact .................. 11 of the project. By 2021, construction will be well underway, Boring Tunnels ..................12-13 so please drive safely and be mindful of crews working HRBT Project Management $3.8 Billion Project is Community Outreach ......14-15 along the interstate. We are committed to delivering 100% Funded James Utterback: Project