June 1, 1965 R
Total Page:16
File Type:pdf, Size:1020Kb
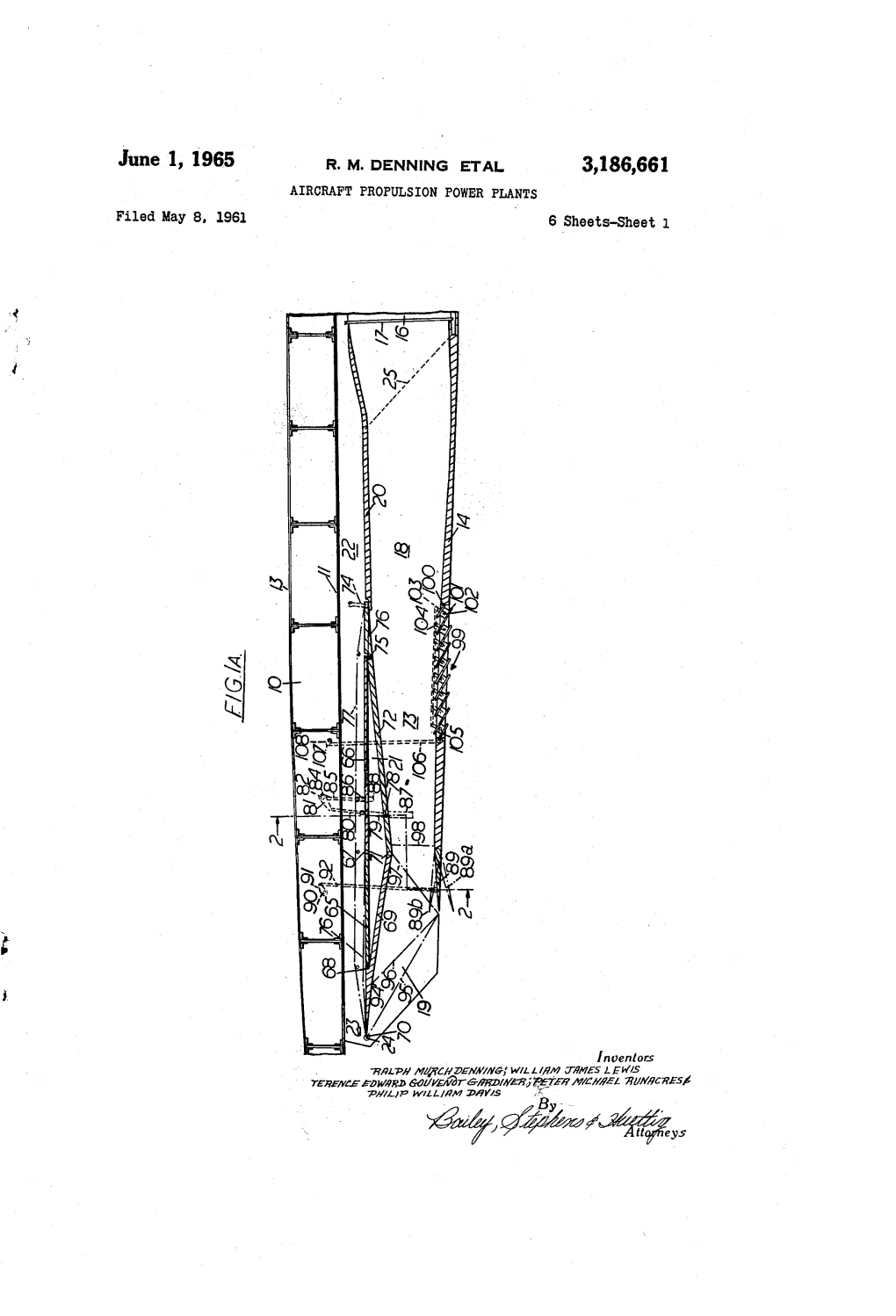
Load more
Recommended publications
-
Aviation Machinist's Mate 3 & 2
NONRESIDENT TRAINING COURSE Aviation Machinist’s Mate 3 & 2 NAVEDTRA 14008 DISTRIBUTION STATEMENT A: Approved for public release; distribution is unlimited. PREFACE About this course: This is a self-study course. By studying this course, you can improve your professional/military knowledge, as well as prepare for the Navywide advancement-in-rate examination. It contains subject matter about day- to-day occupational knowledge and skill requirements and includes text, tables, and illustrations to help you understand the information. An additional important feature of this course is its reference to useful information in other publications. The well-prepared Sailor will take the time to look up the additional information. History of the course: • Sep 1991: Original edition released. Prepared by ADCS(AW) Terence A. Post. • Jan 2004: Administrative update released. Technical content was not reviewed or revised. Published by NAVAL EDUCATION AND TRAINING PROFESSIONAL DEVELOPMENT AND TECHNOLOGY CENTER TABLE OF CONTENTS CHAPTER PAGE 1. Jet Engine Theory and Design ............................................................................... 1-1 2. Tools and Hardware ............................................................................................... 2-1 3. Aviation Support Equipment.................................................................................. 3-1 4. Jet Aircraft Fuel and Fuel Systems ........................................................................ 4-1 5. Jet Aircraft Engine Lubrication Systems .............................................................. -
SP2016-3124855 a Generic Thermodynamic Assessment Of
SP2016-3124855 A Generic Thermodynamic Assessment of Reusable High-Speed Vehicles V. Fernandez Villace, J. Steelant ESA-ESTEC, Section of Aerothermodynamics and Propulsion Analysis Keplerlaan 1, 2200 AG Noordwijk, The Netherlands Email: [email protected], [email protected] ABSTRACT Lifting based vehicles for either space transportation or sustained hypersonic cruise are exposed to high thermal loads during the atmospheric trajectory. The thermal protection system has therefore to efficiently manage the thermal load that penetrates the aeroshell in order to guarantee a satisfactory mission performance. In the present study, the thermal endurance of a LH2-fuelled Mach 8 hypersonic cruiser is assured by soaking the thermal load across the aeroshell into the on-board tank system. The so-produced boil-off acts as a coolant for other aircraft subsystems, like the cabin environmental control system. Further, in order to avoid over-board dumping of the vaporized fuel, a boil-off compression system is proposed to inject the fuel into the propulsion plant. The numerical approach comprised a detailed model of the airframe, where the heat transfer across the interfacing areas between the different subsystems, namely tanks, cabin, propulsion plant and the aeroshell, was resolved based on one-dimensional engineering models. This methodology allowed the evaluation of the complete mission cycle, from the apron, through taxiing and airborne phases and back to apron. 1. INTRODUCTION 2. PRELIMINARY EVALUATION The thermal management of cruising high-speed One of the purposes of the present study was to aircraft plays a very important role. These vehicles design a thermodynamic cycle able to balance the are submitted to high heat loads originating from the airframe thermal and mechanical loads. -
Conceptual Design for a Supersonic Advanced Military Trainer
Conceptual Design for a Supersonic Advanced Military Trainer A project presented to The Faculty of the Department of Aerospace Engineering San José State University In partial fulfillment of the requirements for the degree Master of Science in Aerospace Engineering by Royd A. Johansen May 2019 approved by Dr. Nikos Mourtos Faculty Advisor © 2019 Royd A. Johansen ALL RIGHTS RESERVED ABSTRACT CONCEPTUAL DESIGN FOR A SUPERSONIC ADVANCED MILITARY TRAINER by Royd A. Johansen The conceptual aircraft design project is based off the T-X program requirements for an advanced military trainer (AMT). The design process focused on a top-level design aspect, that followed the classic aircraft design process developed by J. Roskam’s Airplane Design. The design process covered: configuration selection, weight sizing, performance sizing, fuselage design, wing design, empennage design, landing-gear design, Class I weight and balance, static longitudinal and directional stability, subsonic drag polars, supersonic area rule applied to supersonic drag polars, V-n diagrams, Class II weight and balance, moments and products of inertia, and cost estimation. Throughout the process other materials and references are consulted to verify or develop a better understanding of the concepts in the Airplane Design series. ACKNOWLEDGEMENTS I would like to express my deep gratitude to Dr. Nikos Mourtos for his support throughout this project and his invaluable academic advisement throughout my undergraduate and graduate studies. I would also like to thank Professor Gonzalo Mendoza for introducing Aircraft Design to me as an undergraduate and for providing additional insights throughout my graduate studies. My thanks are also extended to Professor Jeanine Hunter for helping me develop my theoretical foundation in Dynamics, Flight Mechanics, and Aircraft Stability and Control. -
Validation and Parametric Study of Supersonic Air Intake Master’S Thesis in Applied Mechanics
Validation and Parametric Study of Supersonic Air Intake Master's thesis in Applied Mechanics JAKOB EKERMO Department of Mechanics and Maritime Sciences CHALMERS UNIVERSITY OF TECHNOLOGY G¨oteborg, Sweden 2018 MASTER'S THESIS IN APPLIED MECHANICS Validation and Parametric Study of Supersonic Air Intake JAKOB EKERMO Department of Mechanics and Maritime Sciences Division of Fluid Dynamics CHALMERS UNIVERSITY OF TECHNOLOGY G¨oteborg, Sweden 2018 Validation and Parametric Study of Supersonic Air Intake JAKOB EKERMO c JAKOB EKERMO, 2018 Master's thesis 2018:18 Department of Mechanics and Maritime Sciences Division of Fluid Dynamics Chalmers University of Technology SE-412 96 G¨oteborg Sweden Telephone: +46 (0)31-772 1000 Cover: Illustration of complex shock wave patterns residing in the intake for a simulation in the supercritical operating range. Chalmers Reproservice G¨oteborg, Sweden 2018 Validation and Parametric Study of Supersonic Air Intake Master's thesis in Applied Mechanics JAKOB EKERMO Department of Mechanics and Maritime Sciences Division of Fluid Dynamics Chalmers University of Technology Abstract The current study was carried out on behalf of GKN Aerospace as a Master's thesis at Chalmers University of Technology. The Department of Propulsion Engineering at this company wished to develop a deeper understanding into the performance of supersonic engine intakes and to relate this to the influential physical notions and geometry alterations. The ultimate objective was to obtain a CFD model to study the effects of key variations of geometrical and physical parameters on the aerodynamic performance. This model was initially to be validated on a model scale against the results of wind tunnel tests. -
The F-14 Tomcat Story Free
FREE THE F-14 TOMCAT STORY PDF Tony Holmes | 128 pages | 29 Apr 2010 | The History Press Ltd | 9780752449852 | English | Stroud, United Kingdom Tales | F Tomcat You need JavaScript enabled to view it. Everything is welcome about the first flight, the th or th trap, cruise The F-14 Tomcat Story, accident reports, squadron celebrations - whatever you want to go public anonymously with. The birth of the Tomcat logo began in the early '70's by a request from Norm Gandia former No. He asked me to draw. The F Tomcat Association P. Written by Paul Pompier FAs flying vs. Member Login. Remember Me. Featured Products. He asked me to draw Another Tomcat Tale. Written by Jerry "KarateJoe" Watson. The Birth of the Tomcat Logo. Written by Jim Rodriguez. The story of FA, Aircraft No. Written by William Barto. The day I shot myself down. Written by Pete Purvis. My most tense moment in the 26 years of flying Fs. Written by Dale Snodgrass. Crash landing a crippled Tomcat. Written by Anonymous. Written by David Baranek. The F-14 Tomcat Story by the Jolly Rogers. Eject on a familiarization hop. F The F-14 Tomcat Story Air-to-Air Victories. I hope there is a place Written by Paul Pompier. FAs flying vs. German F-4Fs. Written by Hubert Peitzmeier. Written by Bob Norris. The Last of the Jolly. Written by Bob Frantz. Sports Writer Earns The F-14 Tomcat Story Callsign. Written by Rick Reilly. Sunset Glows on the Tomcat. Written by Ward Carroll. Written by Dave Baranek. Zone 5 Afterburner Photo off the Coast of Vietnam. -
BRINGING HISTORY to LIFE Sseeeeee Ppagesaaggeess 332-33!2 333!
MayMMaay 2017200117 BRINGING HISTORY TO LIFE SSeeeeee PPagesaaggeess 332-33!2 333! 1:16 Scale Russian T-72 MBT from Trumpeter See Page 25 for complete details. Over 140 NEW Kits and Accessories Inside These Pages! PLASTIC MODELODELOD ELE L KITS KKITKI T S • MODEL ACCESSORIES SeeS bback cover for full details. BOOKS & MAGAZINES • PAINTS & TOOLS • GIFTS & COLLECTIBLES OrderO Today at WWW.SQUADRON.COM or call 1-877-414-0434 DearDFid Friends We are excited to share with you an improved flyer this month, designed with you in mind. Better images, improved merchandis- ing, and increased focus on accessories to elevate your kit building experience has been the focus of the enhancements. Remember, our monthly flyer is only the tip of the iceberg of the great modeling products we offer. We have so much more listed and available on our website at www.Squadron.com. Be sure to check it daily for new items and deals. There is always some- thing exciting happening at Squadron.com! Featured products this month include the latest new release from Squadron Signal Publications: (SS10249) UH-1 Huey In Action. Written by acclaimed military author David Doyle, this book is a tribute to one of the most recognized workhorses of the Vietnam War. The Huey remains in service today after 65 with the U.S. military and our Allies. The book is illustrated with more than 220 curated photos and supplemented by numerous line illustrations. True Details is launching a new premium accessory line which takes advantage of the huge strides made in the 3-D printing field. -
Design and Evaluation of High Speed Intakes
Design and Evaluation of High Speed Intakes T Cain Gas Dynamics Ltd., 2 Clockhouse Road, Farnborough, GU14 7QY Hampshire, UK [email protected] ABSTRACT The lecture provides a brief tour of some historic supersonic intakes beginning with Trommsdorff's missiles and ending with Concorde and the SR-71. The features that enable the intake to provide the right mass flow at the right total pressure while complying with constraints imposed by the vehicle and its mission, are analysed. The tour is combined with an introduction to tailoring compressive flow fields by exploitation of one and two dimensional flow elements. The lecture is essentially the same as one given a year earlier entitled “Ramjet Intakes”. 1 INTRODUCTION This lecture approaches the problem of intake design from a slightly unusual perspective, here we are less concerned with intakes in general, and far more concerned with the details of selected intakes. The approach is based on the belief that it is easier to extrapolate and expand from a detailed small study, than to imagine or reinvent what has not been revealed in a general overview. Should a less focused introduction be preferred, there are good references that are free to download. Reference [1] is a fine example, summarising what was known about intakes in 1964, which is practically everything known about them today. It is not that work done after that time is redundant, but since the ground work was complete, later intake studies tend to be either learning exercises for the individuals involved, or are focussed on an application and remain unpublished for commercial and/or military reasons. -
Concorde Magazine
Mach 2 Concorde magazine Going to extremes Test flights with G-AXDN Luxury purchase Buying a Concorde Concorde Watch News from Manchester and Duxford Issue 30 May 2021 Mach 2 May 2021 Introduction For this issue we look back at Concorde’s early years in the 1970s – including an important part of the test flight programme, and the entry of the production air- craft into British Airways’ fleet. Former BA flight engineerDavid Macdonald gives us an insight into the extraordinary task of buying and test-flying new Concordes for British Airways. Concorde avionics engineer John Dunlevy was in- volved in the test flights carried out by the British pre- production aircraft G-AXDN to test vital systems such as the digital air intake control system. He recalls his role in the test flight programmes that formed the bulk of G-AXDN’s work. Lastly, in Concorde Watch, we hear from Heritage Concorde about the maintenance and refurbishment work that they have done on Concordes G-BOAC and G-AXDN to make these aircraft ready for viewing as the museums open to visitors once again. In this issue 2 Introduction 12 Breaking the ice John Dunlevy 3 Buying a Concorde 15 Concorde Watch David Macdonald 8 Feature: Going to extremes Editor: Katie John 9 Joining the digital age Cover: Concorde G-AXDN appears on display at Farnborough, while painted with the test markings for John Dunlevy the ice trials later that year. Photo: The Peter Keating Collection © A Flying History Ltd aflyinghistory.com 2 Mach 2 May 2021 Buying a Concorde For many of us, purchasing a Concorde is the stuff of dreams. -
Specification AIR 7-3" in April 1953
CANADA AVIATION AND SPACE MUSEUM AIRCRAFT AVRO CANADA CF-105 ARROW RCAF SERIAL 25206 (NOSE SECTION & COMPONENTS ONLY) Introduction The CF-105 Arrow was a delta-winged interceptor aircraft, designed and built by A.V. Roe (Avro) Canada as the culmination of a series of design studies that originally began in 1953. The Arrow is considered by many to have been one of the most advanced technological achievements by the Canadian aviation industry. The CF-105 design was capable of near-Mach 2 speeds at altitudes in excess of 15,250 meters (50,000 feet) and it was intended to serve as the Royal Canadian Air Force’s (RCAF) primary interceptor in the 1960s and beyond. However, in February 1959, in the midst of its flight test program, the development of the CF-105 Arrow (including all of its associated programs, such as the Orenda Iroquois jet engines, Astra fire control system and missile armament systems) was abruptly cancelled before a scheduled final project review had taken place, sparking an intense and often bitter political debate. The controversy engendered by this cancellation, and the subsequent destruction of all of aircraft then in production, still remains a topic for debate amongst historians, politicians, authors and aircraft enthusiasts. This decision not only resulted in the termination of the aircraft program but also led to the demise of Avro Canada. Background Prior to 1939, as “war clouds” loomed on the horizon, the Canadian government encouraged a number of "shadow factories" to be set up in order to produce British aircraft designs in relative safety. -
Numerical Investigation of a Generic Scramjet Configuration
Numerical Investigation of a Generic Scramjet Configuration Numerische Analyse einer generischen Scramjet-Konfiguration Von der Fakultät Maschinenwesen der Technischen Universität Dresden zur Erlangung des akademischen Grades Doktoringenieur (Dr.-Ing.) angenommene Dissertation von Dipl.-Ing. Sebastian Karl geboren am 31. März 1974 in Dresden Tag der Einreichung: 23. August 2010 Tag der Verteidigung: 7. Februar 2011 Gutachter: Prof. (em.) Dr.-Ing. R. Grundmann Technische Universität Dresden Prof. Dr. ir. Johan Steelant European Space Research and Technology Centre (ESA-ESTEC) Kurzfassung Staustrahlantriebe, bei denen sich die Strömung im gesamten Triebwerksbereich im Überschall befindet (supersonic combustion ramjets, scramjets), stellen ein - zumindest theoretisch - effektives Antriebessystem für den Hyperschallflug im Machzahlbereich von M > 5 dar. Die Strömung wird durch die Diffusorwirkung des Treibwerkseinlaufs komprimiert. Um das Temperaturniveau am Brennkammereintritt und die Druckverluste im Einlauf zu begrenzen, arbeiten Scramjets mit einer Brennkammereintrittsgeschwindigkeit im Überschallbereich. Nachdem der Strömung in der Brennkammer durch Verbrennung von Treibstoff Energie zugeführt wurde, erfolgt die Expansion in der Schubdüse. Durch die Verwendung der Umgebungsluft als Oxidationsmittel erreichen Scramjet-Triebwerke einen hohen spezifischen Impuls. Die Auslegung und der Entwurf von luftatmenden Hyperschallantrieben sind in der Praxis mit Schwierigkeiten verbunden. Der Einsatz von Bodenversuchsanlagen ist auf kleinskalige -
Concorde Flight Testing David Contributing Editor: Nigel Ferris Macdonald and Pete Comport
Mach 2 Concorde magazine Performance reviews Certification flight tests Into the unknown Concorde visits Greenland Issue 12 October 2017 Mach 2 October 2017 Introduction This month we offer a detailed insight into two major aspects of Concorde operations. In our first article, British Airways Flight Engineer David Mac- donald and Fleet Shift Manager Pete Comport go through the procedure for Concorde certification flights – an essential requirement to keep the air- craft airworthy. Charter flights were another impor- tant part of Concorde services, and also required special management; Philip Cairns describes his experience of taking care of Concorde on her inau- gural charter flight to Greenland. We also have news of recent visits to Concorde museums. Katie John reports on a highly produc- tive meeting between Concorde preservation groups at Duxford, and Nigel Ferris gives us an insight into the final preparations at the Aerospace Bristol museum. In this issue 2 Introduction Editor: Katie John 3 Concorde flight testing David Contributing editor: Nigel Ferris MacDonald and Pete Comport 10 Concorde memories Philip Cairns Cover: Concorde G-BOAF in the new Aerospace 12 Concorde Watch Bristol hangar at Filton. Photo: Nigel Ferris 2 Mach 2 October 2017 Concorde flight testing Pete Comport in conversation with David Macdonald In order to maintain Concorde’s airworthiness, the aircraft had to undergo regular certification tests. Here, former British Airways Flight Engineer David Macdonald and Fleet Shift Manager Pete Comport talk us through each stage of this complex, meticulously planned process. All commercial aircraft need to have Manager in the right-hand seat – flight time was only 3.5 hours). -
About Supersonic Flight and Mach 3 Flying
American Journal of Engineering and Applied Sciences Review About Supersonic Flight and Mach 3 Flying Relly Victoria Virgil Petrescu ARoTMM-IFToMM, Bucharest Polytechnic University, Bucharest, (CE) Romania Article history Abstract: Aerospace-BAC Concorde was a supersonic passenger aircraft. Received: 13-08-2020 It was the result of a government treaty between the French and British Revised: 22-08-2020 governments, combining the efforts of Aerospace and British Aircraft Accepted: 28-08-2020 Corporation. With only 20 aircraft built in total, the cost of the development phase was a major economic failure. In addition, Air France Email: [email protected] and British Airways were subsidized by the government to buy the aircraft. Of the commercial supersonic aircraft, Concorde was the most successful, with the Tupolev Tu-144 being the other aircraft. The Tu-144 had a higher top speed, but the consumption was higher and the autonomy was lower than the Concorde. Flying for the first time in 1969, Concorde began its commercial service in 1976 and continued for 27 years. It operated transatlantic flights from Heathrow, London (British Airways) and Charles de Gaulle, Paris (Air France) to JFK, New York and Dulles, Washington; flying at record speeds, it travels these distances in less than half the time of other planes. Concorde also set other records, including the official FAI world record "Westbound Around the World" and "Eastbound Around the World" at speed. Following the sole accident on 25 July 2000, the economic effects following the events of 11 September 2001 and other factors, the flights ceased on 24 October 2003.