"Ice Patented Jan
Total Page:16
File Type:pdf, Size:1020Kb
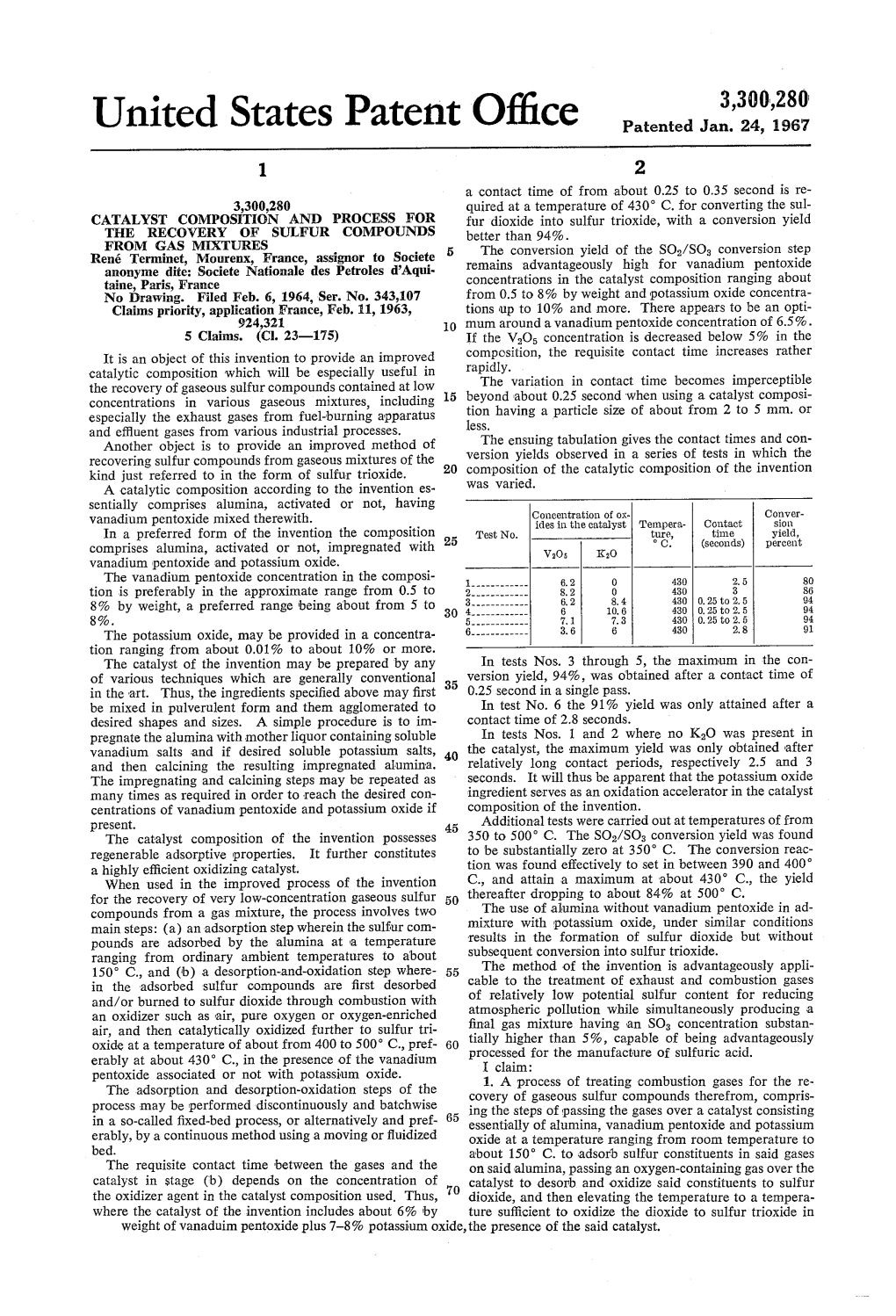
Load more
Recommended publications
-
Decontamination of Indoor and Outdoor Materials with Aqueous Chlorine Dioxide Solutions
EPA 600/R-12/516 | May 2012 | www.epa.gov/ord Decontamination of Indoor and Outdoor Materials with Aqueous Chlorine Dioxide Solutions Office of Research and Development National Homeland Security Research Center EPA/600/R/12/516 May 2012 Decontamination of Indoor and Outdoor Materials with Aqueous Chlorine Dioxide Solutions U.S. Environmental Protection Agency Research Triangle Park, NC 27711 ii Disclaimer The U.S. Environmental Protection Agency (EPA), through its Office of Research and Development’s (ORD) National Homeland Security Research Center (NHSRC), funded, directed and managed this work through Contract Number EP-C-10-001 with Battelle. This report has been peer and administratively reviewed and has been approved for publication as an EPA document. Mention of trade names or commercial products does not constitute endorsement or recommendation for use of a specific product. Questions concerning this document or its application should be addressed to: Joseph Wood National Homeland Security Research Center Office of Research and Development U.S. Environmental Protection Agency Mail Code E343-06 Research Triangle Park, NC 27711 919-541-5029 iii Foreword Following the events of September 11, 2001, addressing the critical needs related to homeland security became a clear requirement with respect to EPA’s mission to protect human health and the environment. Presidential Directives further emphasized EPA as the primary federal agency responsible for the country’s water supplies and for decontamination following a chemical, biological, and/or radiological (CBR) attack. To support EPA’s mission to assist in and lead response and recovery activities associated with CBR incidents of national significance, the National Homeland Security Research Center (NHSRC) was established to conduct research and deliver products that improve the capability of the Agency and other federal, state, and local agencies to carry out their homeland security responsibilities. -
United States Patent 19 11 3,904.425 Young Et Al
United States Patent 19 11 3,904.425 Young et al. (45) Sept. 9, 1975 54) ABSORPTIVE GLASS Primary Examiner-Harvey E. Behrend 75 Inventors: Robert W. Young, Woodstock, Attorney, Agent, or Firm-William C. Nealon; H. R. Conn.; Robert E. Graf, Southbridge, Berkenstock, Jr. Mass. W EXEMPLARY CLAIM 73) Assignee: American Optical Corporation, 1. A glass material having a calculated oxide composi Southbridge, Mass. tion comprising 22 Filed: June 12, 1964 21 Appl. No.: 374,811 Percent by Weight Silicon Dioxidc (SiO) 5.9 Sodium Oxide (NaO) 6.5 (52) U.S. Cl...................................... 106/52; 106/50 Potassium Oxide (KO) 6.8 (51 l Int. Cl........................................... CO3C 13/00 Calcium Oxide (CaO) 6.5 58) Field of Search................................. 106/50, 52 Antimony Trioxide (SbO) 0.4 Aluminum Oxide (AO) 4. Zinc Oxide (ZnO) 2.2 56) References Cited Titanium Dioxidc (TiO) 0.4 Manganese Dioxide (MnO) 23.4 UNITED STATES PATENTS Chromium Oxide (CrO) O.S 2,676,09 4/1954 Barnes ct al.......................... 106752 Tct O).() 2,776,900 l/1957 Duncan et al........................ 106/52 2,898,219 8/1959 Duncan ct al........................ 106/52 2,902,377 9, 1959 Duncan............ ... 106/52 a 100 micron thickness of said glass material having 3,146,2O 8/1964 Upton et al.... ... 106/52 an optical density greater than 0.25 at least for light 3,20386 8/1965 Bull et al.............................. 1 O6/52 from 0.4 to 0.6 microns wavelength. FOREIGN PATENTS OR APPLICATIONS 6 4,357 21 1961 Canada................................. 106/52 6 Claims, No Drawings 3,904,425 2 ABSORPTIVE GLASS als should have optical densities at least as high as 0.25 The field of this invention is that of glass composi in sample thickness as small as 100 microns at least for tions and the invention relates more particularly to light of wavelengths between 0.4 and 0.6 microns. -
BALANCE I: IONIZE (Dissociate) D: DELETE SPECTATOR IONS D: DECOMPOSE Y: YES – YOU DID IT!!
PREDICTING REACTIONS Chapter One | 1 Chapter 1 AP PREDICTING REACTIONS1 NOTE: we will cover this chapter throughout the year. A. Points 15 % of Free Response or 7.5% of final grade Each rxn worth 5 pts for a total of 15 pts possible. Three points for the unbalanced net ionic equation (total nine points). 1 pt reactants, 2 pts products One point for the balanced equation (I am assuming that if the net ionic is wrong, but the equation is balanced correctly, i.e. “internally consistence” then the students will get this point). One point for answering a question about the reaction. Possibilities include: indications of chemical reaction oxidizing agent oxidation number color of solid product general chemistry interest simple stoichiometry Points are deducted for including incorrect species, omitting species or including spectator ions. You don’t need to include states, but I like to include (s) and (g) so I won’t be tempted to dissociate incorrectly! B. Instructions For each of the following three reactions, in part (i) write a BALANCED equation and in part (ii) answer the question about the reaction. In part (i), coefficients should be in the lowest whole numbers. In all cases, a reaction occurs. Assume that solutions are aqueous unless otherwise indicated. Represent substances in solution as ions if the substances are extensively ionized. Omit formulas for any ions or molecules that are unchanged by the reaction. Example: (i) A strip of magnesium is added to a solution of silver nitrate. (ii) Which substance is the oxidizing agent? + 2+ (i) Mg + 2 Ag Mg + 2 Ag (ii) The Ag+ is the oxidizing agent. -
Chemical Formula of Binary Ionic Compounds – Sheet 1 the Combining Power Or Valency of Silver Is Always 1
Chemical Formula of Binary Ionic Compounds – Sheet 1 The combining power or valency of silver is always 1. All other transition metals are 2 unless otherwise indicated. No. Binary compound Formula No. Binary compound Formula 1 potassium fluoride 26 calcium sulfide 2 calcium chloride 27 lithium bromide 3 barium bromide 28 nickel sulfide 4 silver sulfide 29 zinc phosphide 5 aluminium iodide 30 barium iodide 6 potassium iodide 31 caesium chloride 7 lead(IV) oxide 32 copper bromide 8 zinc nitride 33 sodium nitride 9 silver iodide 34 silver chloride 10 barium fluoride 35 sodium hydride 11 lead(II) iodide 36 potassium nitride 12 silver fluoride 37 cobalt chloride 13 sodium sulfide 38 magnesium sulfide 14 sodium bromide 39 potassium chloride 15 calcium oxide 40 calcium bromide 16 zinc fluoride 41 iron(III) oxide 17 strontium phosphide 42 aluminium fluoride 18 barium sulfide 43 magnesium bromide 19 aluminium oxide 44 iron(III) chloride 20 aluminium chloride 45 barium nitride 21 aluminium sulfide 46 sodium fluoride 22 lead(II) oxide 47 lithium fluoride 23 barium chloride 48 lithium iodide 24 copper chloride 49 lithium hydride 25 barium phosphide 50 potassium oxide “Aluminum” and “cesium” are commonly used alternative spellings for "aluminium" and "caesium that are used in the US. May be freely copied for educational use. ©www.chemicalformula.org Chemical Formula of Binary Ionic Compounds – Sheet 2 The combining power or valency of silver is always 1. All other transition metals are 2 unless otherwise indicated. No. Binary compound Formula No. -
UNITED STATES PATENT OFFICE 2,278,867 LEAD-FREE GLAZE of LOW MATURNG TEMPERATURE for USE in DECORATING CERAMCWARE Alden J
Patented Apr. 7, 1942 2,278,867 UNITED STATES PATENT OFFICE 2,278,867 LEAD-FREE GLAZE OF LOW MATURNG TEMPERATURE FOR USE IN DECORATING CERAMCWARE Alden J. Deyrup, Elizabeth, N.J., assignor to E. ... " du Pont de Nemours & Company, Wilmington, Del, a corporation of Delaware No Drawing. Application May 1, 1940, Seria No. 332,732 9 Claims. (C. 106-48) This invention relates to certain improved lead temperature of glaze firing, being utilized. The free glazes or fluxes of the type suitable for use temperature employed in the overglazing fire to in art-glazing or Overglazing ceramic ware. More mature the overglaze is usually 700 to 800' C., particularly, this invention relates to certain new which is of course considérably.lower than the and improved flux compositions free from leadi 5 temperature range in which the glazes used to Oxide which, when used for the artglazing or coat the bisque are fired. At this overglaze fir Overglazing of chinaware and pottery, are capa ing temperature the colored decorative coating ble of melting at fairly low maturing tempera matures and vitrifles, and the ware is thus coat tures to a superior decorative coating of high ed with a colored decorative surface having a resistance to both the action of chemical agents 10 high degree of glossiness. such as acids and alkalies, and to mechanical Bisque ware is sometimes decorated by plac abrasion. ing on the surface of the ware, without prelimi In the manufacture of china and pottery a narily coating the surface of the bisque with a clay mixture is customarily formed into the de vitrified glaze, a mixture of pigment and low sired shape and then fired at a high tempera 15 melting flux which can be matured to a good ture, one within the range 1250 to 1400° C. -
REACH - Registration, Evaluation, Authorisation and Restriction of Chemical Substances
REACH - Registration, Evaluation, Authorisation and Restriction of Chemical Substances TERRITORY European Union RESTRICTION SUBJECT Human Health and Environment Protection against adverse effects of chemical substances The European Commission elaborated a Directive (EC 1907/2006) known as REACH with the aim to ensure Human Health and Environment Protection against adverse effects of chemical substances. The Directive imposes - to all companies conducting business with chemical substances - to adopt compulsorily “a special chemical substances work regime”. (REACH is valid from 1st of July 2007.) Producers, importers and follow-up users of chemical substances and/or substances contained in preparations and in items must, in compliance with the Directive, ask for their registration at the European Chemical Agency as of 1st of June 2008. The obligation to register in relation with chemical composition is mainly related to chemical substances and preparations made of them, but not according to the article 7, the paragraph 1 of the REACH Directive to final products, i.e. items which can be considered – under standard or reasonable foreseeable conditions of use – as completely safe. Preciosa does not supply either chemical substances or chemical preparations or mixtures on the market. The products that we supply are final products that meet the above mentioned requirements. This means that they are not subject to the REACH registration. Preciosa guarantees to the customer that all products of Preciosa are in conformity with requirements specified in COMMISSION REGULATION (EU) No 217/2016 of 16 February 2016 amending Regulation (EC) No 1907/2006 of the European Parliament and of the Council on the Registration, Evaluation, Authorisation and Restriction of Chemicals (REACH) as regards Annex XVII. -
Safety Data Sheet
SAFETY DATA SHEET Creation Date 24-Nov-2010 Revision Date 17-Jun-2021 Revision Number 4 SECTION 1: IDENTIFICATION OF THE SUBSTANCE/MIXTURE AND OF THE COMPANY/UNDERTAKING 1.1. Product identifier Product Description: Potassium tetraborate tetrahydrate Cat No. : 39435 Synonyms Potassium biborate tetrahydrate CAS-No 12045-78-2 Molecular Formula B4 K2 O7 . 4 H2 O Reach Registration Number - 1.2. Relevant identified uses of the substance or mixture and uses advised against Recommended Use Laboratory chemicals. Uses advised against No Information available 1.3. Details of the supplier of the safety data sheet Company Alfa Aesar . Avocado Research Chemicals, Ltd. Shore Road Port of Heysham Industrial Park Heysham, Lancashire LA3 2XY United Kingdom Office Tel: +44 (0) 1524 850506 Office Fax: +44 (0) 1524 850608 E-mail address [email protected] www.alfa.com Product Safety Department 1.4. Emergency telephone number Call Carechem 24 at +44 (0) 1865 407333 (English only); +44 (0) 1235 239670 (Multi-language) SECTION 2: HAZARDS IDENTIFICATION 2.1. Classification of the substance or mixture CLP Classification - Regulation (EC) No 1272/2008 Physical hazards Based on available data, the classification criteria are not met Health hazards ______________________________________________________________________________________________ ALFAA39435 Page 1 / 10 SAFETY DATA SHEET Potassium tetraborate tetrahydrate Revision Date 17-Jun-2021 ______________________________________________________________________________________________ Reproductive Toxicity Category 2 (H361d) Environmental hazards Based on available data, the classification criteria are not met Full text of Hazard Statements: see section 16 2.2. Label elements Signal Word Warning Hazard Statements H361d - Suspected of damaging the unborn child Precautionary Statements P201 - Obtain special instructions before use P280 - Wear protective gloves/protective clothing/eye protection/face protection P308 + P313 - IF exposed or concerned: Get medical advice/attention Additional EU labelling Restricted to professional users 2.3. -
Chemical Names and CAS Numbers Final
Chemical Abstract Chemical Formula Chemical Name Service (CAS) Number C3H8O 1‐propanol C4H7BrO2 2‐bromobutyric acid 80‐58‐0 GeH3COOH 2‐germaacetic acid C4H10 2‐methylpropane 75‐28‐5 C3H8O 2‐propanol 67‐63‐0 C6H10O3 4‐acetylbutyric acid 448671 C4H7BrO2 4‐bromobutyric acid 2623‐87‐2 CH3CHO acetaldehyde CH3CONH2 acetamide C8H9NO2 acetaminophen 103‐90‐2 − C2H3O2 acetate ion − CH3COO acetate ion C2H4O2 acetic acid 64‐19‐7 CH3COOH acetic acid (CH3)2CO acetone CH3COCl acetyl chloride C2H2 acetylene 74‐86‐2 HCCH acetylene C9H8O4 acetylsalicylic acid 50‐78‐2 H2C(CH)CN acrylonitrile C3H7NO2 Ala C3H7NO2 alanine 56‐41‐7 NaAlSi3O3 albite AlSb aluminium antimonide 25152‐52‐7 AlAs aluminium arsenide 22831‐42‐1 AlBO2 aluminium borate 61279‐70‐7 AlBO aluminium boron oxide 12041‐48‐4 AlBr3 aluminium bromide 7727‐15‐3 AlBr3•6H2O aluminium bromide hexahydrate 2149397 AlCl4Cs aluminium caesium tetrachloride 17992‐03‐9 AlCl3 aluminium chloride (anhydrous) 7446‐70‐0 AlCl3•6H2O aluminium chloride hexahydrate 7784‐13‐6 AlClO aluminium chloride oxide 13596‐11‐7 AlB2 aluminium diboride 12041‐50‐8 AlF2 aluminium difluoride 13569‐23‐8 AlF2O aluminium difluoride oxide 38344‐66‐0 AlB12 aluminium dodecaboride 12041‐54‐2 Al2F6 aluminium fluoride 17949‐86‐9 AlF3 aluminium fluoride 7784‐18‐1 Al(CHO2)3 aluminium formate 7360‐53‐4 1 of 75 Chemical Abstract Chemical Formula Chemical Name Service (CAS) Number Al(OH)3 aluminium hydroxide 21645‐51‐2 Al2I6 aluminium iodide 18898‐35‐6 AlI3 aluminium iodide 7784‐23‐8 AlBr aluminium monobromide 22359‐97‐3 AlCl aluminium monochloride -
Chemistry Study Materials for Class 10 (NCERT Based Revision of Chapter -03) Ganesh Kumar Date:- 24/11/2020
Chemistry Study Materials for Class 10 (NCERT Based Revision of Chapter -03) Ganesh Kumar Date:- 24/11/2020 METALS AND NON-METALS REACTION OF METALS WITH WATER: Metals form respective metal hydroxide and hydrogen gas when react with water. Metal + Water → Metal hydroxide + Hydrogen Most of the metals do not react with water. However, alkali metals react vigorously with water. Examples: Reaction of sodium metal with water: Sodium metal forms sodium hydroxide and liberates hydrogen gas along with lot of heat when reacts with water. Na + H2O → NaOH + H2 Reaction of aluminium metal with water: Reaction of aluminium metal with cold water is too slow to come into notice. But when steam is passed over aluminium metal; aluminium oxide and hydrogen gas are produced. 2Al + 3H2O → Al2O3 + 2H2 Reaction of zinc metal with water: Zinc metal produces zinc oxide and hydrogen gas when steam is passed over it. Zinc does not react with cold water. Zn + H2O → ZnO + H2 Reaction of Iron with water: Reaction of iron with cold water is very slow and come into notice after a long time. Iron forms rust (iron oxide) when reacts with moisture present in atmosphere. Iron oxide and hydrogen gas are formed by passing of steam over iron metal. 3Fe + 4H2O → Fe3O4 + 4H2 Reaction of potassium metal with water: Potassium metal forms potassium hydroxide and liberates hydrogen gas along with lot of heat when reacts with water. K + H2O → KOH + H2 Reaction of calcium metal with water: Calcium forms calcium hydroxide along with hydrogen gas and heat when reacts with water. Ca + 2H2O → Ca(OH)2 + H2 Reaction of magnesium metal with water: Magnesium metal reacts with water slowly and forms magnesium hydroxide and hydrogen gas. -
United States Patent Office Patented Sept
3,275,406 United States Patent Office Patented Sept. 27, 1966 1. 2 3,275,406 used at the high reaction temperatures and granules of CONVERSION OF SO TO SO WITH A CATALYST Smaller pore size are used at the lower reaction tempera OF SELECTED, POROSTY te. Robert Krempff, Paris, France, assignor to Compagnie de The novel catalysts which are used in the novel process Saint-Gobain, Neuilly-sur-Seine, Seine, France are a porous silica-vanadium oxide-potassium oxide cata No Drawing. Original application Aug. 16, 1962, Ser. lyst having at least a 60% of pores of radius in the range No. 217,288, now Patent No. 3,216,953, dated Nov. 9, of about 1000 and 3000 A., and a porous silica-vanadium 1965. Divided and this application Nov. 5, 1964, Ser. oxide-potassium oxide catalyst having at least 60% of No. 409,298 pores of radius in the range between about 50 and 500 A. 6 Claims. (C. 23-175) The granules of this invention can produce at high speeds This is a division of application Serial No. 217,288, O of reaction even at temperatures below 400 C. when the filed August 16, 1962, now Patent No. 3,216,953. temperature of the said conversion reaction falls to this This invention relates to the manufacture of SO3 by temperature range. the catalytic oxidation of SO on vanadium-potassium The novel method of preparing a catalyst comprises silica catalysts. The invention also relates to the manu 15 depositing vanadium oxide and potassium oxide on finely facture of novel catalysts for this process. -
Unit 9 Chemical Equations and Reactions Balancing Equations Notes
Unit 9 Chemical Equations and Reactions What is a Chemical Equation? A Chemical Equation is a written representation of the process that occurs in a chemical reaction. A chemical equation is written with the Reactants on the left side of an arrow and the Products of the chemical reaction on the right side of the equation. The head of the arrow typically points toward the right or toward the product side of the equation, although reactions may indicate equilibrium with the reaction proceeding in both directions simultaneously. The elements in an equation are denoted using their symbols. __ Coefficients ___ next to the symbols indicate the ____ stoichiometric ____ numbers. Subscripts are used to indicate the number of atoms of an element present in a chemical species. An example of a chemical equation may be seen in the combustion of methane: CH 4 + 2 O 2 → CO 2 + 2 H 2O Balancing Equations Notes An equation for a chemical reaction in which the number of atoms for each element in the reaction and the total charge are the same for both the reactants and the products. In other words, the mass and the charge are balanced on both sides of the reaction. Symbol Meaning + used to separate one reactant or product from another used to separate the reactants from the products - it is pronounced "yields" or "produces" when the equation is read used when the reaction can proceed in both directions - this is called an equilibrium arrow and will be used later in the course (g) indicates that the substance is in a gaseous state an alternative way of representing a substance in a gaseous state (s) indicates that the substance is in a solid state an alternative way of representing a substance in a solid state indicates that the substance is dissolved in water - the aq comes (aq) from aqueous (l) Identifies a phase state as pure liquid indicates that heat is applied to make the reaction proceed 1 Use coefficients to make sure the number of atoms is the same on both sides of the equation. -
Write the Following Chemical Equations and Balance Using Coefficients. 1
Write the following chemical equations and balance using coefficients. 1. Liquid mercury reacts with liquid bromine to produce solid mercury (II) Bromide Hg (l) + Br2 (l) → HgBr2 (s) balanced 2. Solid calcium carbonate decomposes upon heating to produce solid calcium oxide and carbon dioxide gas. CaCO3 (s) → CaO (s) + CO2 (g) balanced 3. Solid calcium will react with liquid water to produce aqueous calcium hydroxide and hydrogen gas. Ca (s) + 2H2O (l) →Ca(OH)2 (aq) + H2 (g) 4. Butane gas (C4H10) will react with oxygen gas to produce carbon dioxide gas and water vapor. 2 C4H10 (g) + 13 O2 (g) → 8 CO2 (g) + 10 H2O (g) 5. Solid aluminum will react with oxygen gas to produce solid aluminum oxide. 4Al (s) + 3O2 (g) → 2Al2O3 (s) 6. Aluminum metal is oxidized by oxygen (from the air) to form aluminum oxide. 4 Al (s) + 3O2 → 2 Al2O3 7. Sodium oxide reacts with carbon dioxide to form sodium carbonate. Na2O + CO2 → Na2 CO3 8. Calcium metal reacts with water to form calcium hydroxide and hydrogen gas. Ca (s) + 2H2O → Ca (OH)2 + H2 (g) 9. Potassium nitrate decomposes to form potassium nitrite and oxygen. 2 KNO3 (s) → 2 KNO2 (s) + O2 (g) 10. Barium metal reacts with Iron (III) sulfate to produce barium sulfate and iron metal. 3 Ba (s) + Fe2(SO4)3 → 3 BaSO4 + 2 Fe (s) 11. Barium chloride reacts with sodium sulfate to produce barium sulfate and sodium chloride. BaCl2 (aq) + Na2SO4 (aq) → BaSO4 (s) + 2 NaCl (aq) 7 Types of Chemical Reactions Directions (a) Write and balance the given equation.