Ellipsoidal Model of the Rise of a Taylor Bubble in a Round Tube
Total Page:16
File Type:pdf, Size:1020Kb
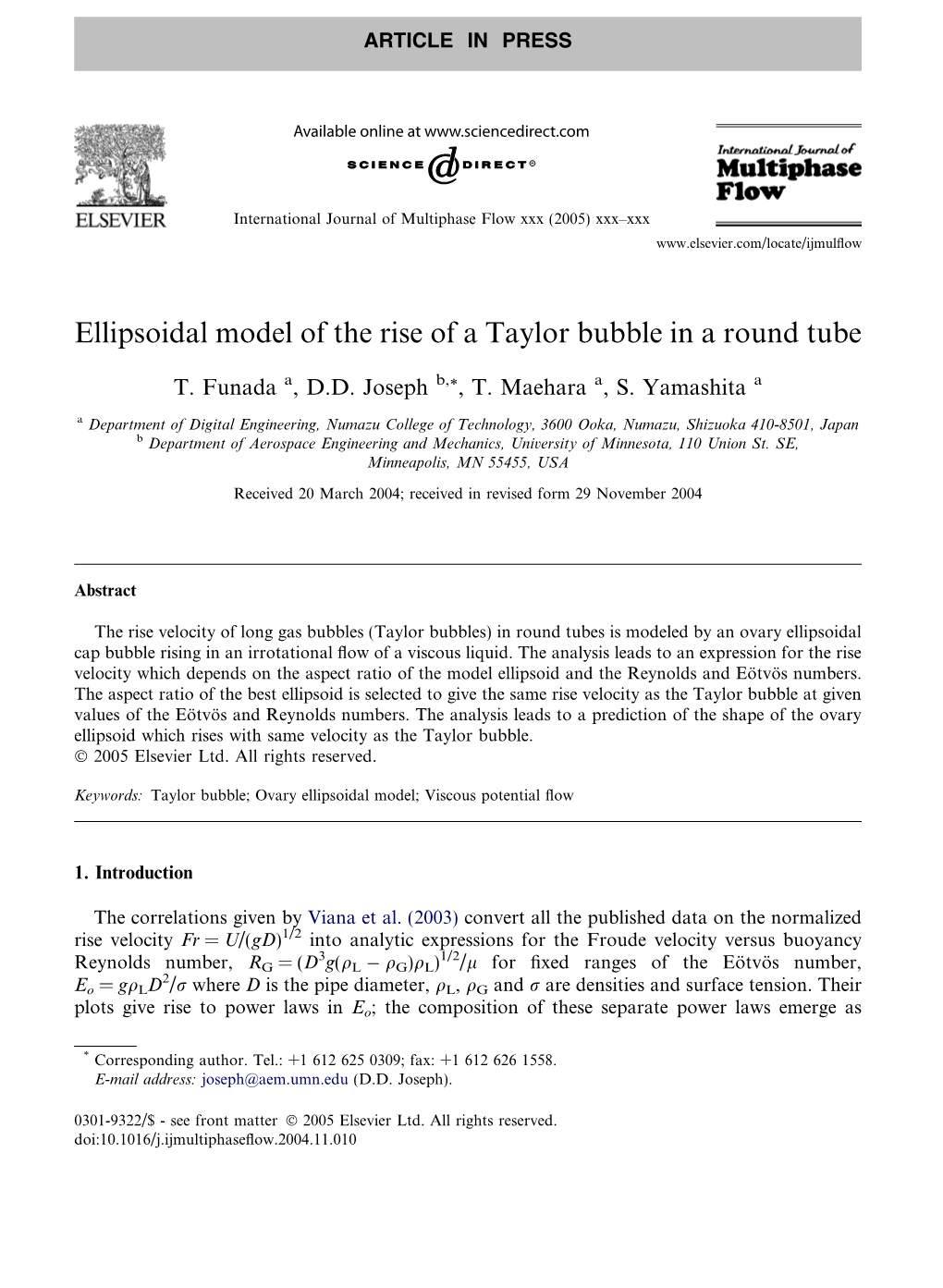
Load more
Recommended publications
-
Intrinsic Volumes and Polar Sets in Spherical Space
1 INTRINSIC VOLUMES AND POLAR SETS IN SPHERICAL SPACE FUCHANG GAO, DANIEL HUG, ROLF SCHNEIDER Abstract. For a convex body of given volume in spherical space, the total invariant measure of hitting great subspheres becomes minimal, equivalently the volume of the polar body becomes maximal, if and only if the body is a spherical cap. This result can be considered as a spherical counterpart of two Euclidean inequalities, the Urysohn inequality connecting mean width and volume, and the Blaschke-Santal´oinequality for the volumes of polar convex bodies. Two proofs are given; the first one can be adapted to hyperbolic space. MSC 2000: 52A40 (primary); 52A55, 52A22 (secondary) Keywords: spherical convexity, Urysohn inequality, Blaschke- Santal´oinequality, intrinsic volume, quermassintegral, polar convex bodies, two-point symmetrization In the classical geometry of convex bodies in Euclidean space, the intrinsic volumes (or quermassintegrals) play a central role. These functionals have counterparts in spherical and hyperbolic geometry, and it is a challenge for a geometer to find analogues in these spaces for the known results about Euclidean intrinsic volumes. In the present paper, we prove one such result, an inequality of isoperimetric type in spherical (or hyperbolic) space, which can be considered as a counterpart to the Urysohn inequality and is, in the spherical case, also related to the Blaschke-Santal´oinequality. Before stating the result (at the beginning of Section 2), we want to recall and collect the basic facts about intrinsic volumes in Euclidean space, describe their noneuclidean counterparts, and state those open problems about the latter which we consider to be of particular interest. -
17 Measure Concentration for the Sphere
17 Measure Concentration for the Sphere In today’s lecture, we will prove the measure concentration theorem for the sphere. Recall that this was one of the vital steps in the analysis of the Arora-Rao-Vazirani approximation algorithm for sparsest cut. Most of the material in today’s lecture is adapted from Matousek’s book [Mat02, chapter 14] and Keith Ball’s lecture notes on convex geometry [Bal97]. n n−1 Notation: We will use the notation Bn to denote the ball of unit radius in R and S n to denote the sphere of unit radius in R . Let µ denote the normalized measure on the unit sphere (i.e., for any measurable set S ⊆ Sn−1, µ(A) denotes the ratio of the surface area of µ to the entire surface area of the sphere Sn−1). Recall that the n-dimensional volume of a ball n n n of radius r in R is given by the formula Vol(Bn) · r = vn · r where πn/2 vn = n Γ 2 + 1 Z ∞ where Γ(x) = tx−1e−tdt 0 n−1 The surface area of the unit sphere S is nvn. Theorem 17.1 (Measure Concentration for the Sphere Sn−1) Let A ⊆ Sn−1 be a mea- n−1 surable subset of the unit sphere S such that µ(A) = 1/2. Let Aδ denote the δ-neighborhood n−1 n−1 of A in S . i.e., Aδ = {x ∈ S |∃z ∈ A, ||x − z||2 ≤ δ}. Then, −nδ2/2 µ(Aδ) ≥ 1 − 2e . Thus, the above theorem states that if A is any set of measure 0.5, taking a step of even √ O (1/ n) around A covers almost 99% of the entire sphere. -
Spherical Cap Packing Asymptotics and Rank-Extreme Detection Kai Zhang
IEEE TRANSACTIONS ON INFORMATION THEORY 1 Spherical Cap Packing Asymptotics and Rank-Extreme Detection Kai Zhang Abstract—We study the spherical cap packing problem with a observations can be written as probabilistic approach. Such probabilistic considerations result Pn ¯ ¯ in an asymptotic sharp universal uniform bound on the maximal i=1(Xi − X)(Yi − Y ) Cb(X; Y ) = q q inner product between any set of unit vectors and a stochastically Pn (X − X¯)2 Pn (Y − Y¯ )2 independent uniformly distributed unit vector. When the set of i=1 i i=1 i unit vectors are themselves independently uniformly distributed, (I.1) we further develop the extreme value distribution limit of where Xi’s and Yi’s are the n independent and identically the maximal inner product, which characterizes its uncertainty distributed (i.i.d.) observations of X and Y respectively, around the bound. and X¯ and Y¯ are the sample means of X and Y As applications of the above asymptotic results, we derive (1) respectively. The sample correlation coefficient possesses an asymptotic sharp universal uniform bound on the maximal spurious correlation, as well as its uniform convergence in important statistical properties and was carefully studied distribution when the explanatory variables are independently in the classical case when the number of variables is Gaussian distributed; and (2) an asymptotic sharp universal small compared to the number of observations. How- bound on the maximum norm of a low-rank elliptically dis- ever, the situation has dramatically changed in the new tributed vector, as well as related limiting distributions. With high-dimensional paradigm [1, 2] as the large number these results, we develop a fast detection method for a low-rank structure in high-dimensional Gaussian data without using the of variables in the data leads to the failure of many spectrum information. -
14-Geometry.Pdf
14. Geometry Po-Shen Loh CMU Putnam Seminar, Fall 2020 1 Classical results Archimedes' Principle. Let a sphere of radius 1 be inscribed inside a cylinder of radius 1 and height 2. Then for any two planes parallel to the base of the cylinder, the cylindrical strip that they cut out of the cylinder has surface area equal to that of the strip that they cut out of the sphere. 2 Problems 1. Two circles C1 and C2 intersect at A and B. C1 has radius 1. L denotes the arc AB of C2 which lies inside C1. L divides C1 into two parts of equal area. Show L has length greater than 2. p 2. Show that if X is a square of side 1 and X = A [ B, thenp A or B has diameter at least 5=2. Show that we can find A and B both having diameter at most 5=2. The diameter of a set is the maximum (strictly speaking, the supremum) of all distances between pairs of points in the set. 3. Let S be a spherical cap with distance taken along great circles. Show that we cannot find a distance preserving map from S to the plane. 4. Let k be a positive real and let P1;P2;:::;Pn be points in the plane. What is the locus of P such that P 2 PPi = k? State in geometric terms the conditions on k for such points P to exist. 5. Let S be a set of n points in the plane such that the greatest distance between two points of S is 1. -
1 Appendices 1 A1. Calculation of the Height of a Spherical Cap 2 A2. Surface Area of a Spherical Rectangle 3 A3. Calculation Of
1 Appendices 2 A1. Calculation of the height of a spherical cap 3 A2. Surface area of a spherical rectangle 4 A3. Calculation of fields of vision and lateral surface angles of cropped detectors (cameras) 5 A4. Non-uniformly distributed approach directions: derivation of equations 10 and 11 6 A5. Step-by-step guide to using the density estimation formula 7 1 8 A1. Calculation of the height of a spherical cap 9 The top section of an acoustic – i.e. conical – detection zone is a spherical cap. The surface area 10 of this cap is determined by the radius of the corresponding sphere (here, given by the cone’s slant 11 height s) and the cap’s height h. The following trigonometric calculations yield the formula for h that is 12 used in equation 5 of the main text (cf. Figure S1 for notation): 휙 14 퐴퐶 = 푠 cos and 퐴퐵 = 퐴퐷 = 푠 2 13 As such, 휙 15 ℎ = 퐷퐶 = 퐴퐷 − 퐴퐶 = 푠 (1 − cos ) (푆1.1) 2 16 17 Figure S1. Cross section of an acoustic detection zone, showing the measurements needed to calculate 18 the height h of the spherical cap (shaded region). The detector is located at the vertex A, which is also the center 19 of the sphere of radius s that the spherical cap is a part of. The angle 흓 is the opening angle of the detector. See 20 text for calculations. 21 2 22 A2. Surface area of a spherical rectangle 23 The top section of a camera-trap’s detection zone is a spherical rectangle whose surface area 24 can be calculated by considering the proportion of the surface area of the sphere of radius s that it 25 covers. -
Lie Sphere Geometry in Lattice Cosmology
Classical and Quantum Gravity PAPER • OPEN ACCESS Lie sphere geometry in lattice cosmology To cite this article: Michael Fennen and Domenico Giulini 2020 Class. Quantum Grav. 37 065007 View the article online for updates and enhancements. This content was downloaded from IP address 131.169.5.251 on 26/02/2020 at 00:24 IOP Classical and Quantum Gravity Class. Quantum Grav. Classical and Quantum Gravity Class. Quantum Grav. 37 (2020) 065007 (30pp) https://doi.org/10.1088/1361-6382/ab6a20 37 2020 © 2020 IOP Publishing Ltd Lie sphere geometry in lattice cosmology CQGRDG Michael Fennen1 and Domenico Giulini1,2 1 Center for Applied Space Technology and Microgravity, University of Bremen, 065007 Bremen, Germany 2 Institute for Theoretical Physics, Leibniz University of Hannover, Hannover, Germany M Fennen and D Giulini E-mail: [email protected] Received 23 September 2019, revised 18 December 2019 Lie sphere geometry in lattice cosmology Accepted for publication 10 January 2020 Published 18 February 2020 Printed in the UK Abstract In this paper we propose to use Lie sphere geometry as a new tool to CQG systematically construct time-symmetric initial data for a wide variety of generalised black-hole configurations in lattice cosmology. These configurations are iteratively constructed analytically and may have any 10.1088/1361-6382/ab6a20 degree of geometric irregularity. We show that for negligible amounts of dust these solutions are similar to the swiss-cheese models at the moment Paper of maximal expansion. As Lie sphere geometry has so far not received much attention in cosmology, we will devote a large part of this paper to explain its geometric background in a language familiar to general relativists. -
Chapter 4 Surfaces
Chapter 4 Surfaces In this chapter we turn to surfaces in general. We discuss the following topics. Describing surfaces with equations and parametric descriptions. ² Some constructions of surfaces: surfaces of revolution and ruled surfaces. ² Tangent planes to surfaces. ² Surface area of surfaces. ² Curvature of surfaces. ² Figure 4.1: In this design for the 1972 Olympic Games in Munich, Germany, Frei Otto illustrates the role of surfaces in modern architecture. (Photo: Wim Huisman) 91 92 Surfaces 4.1 Describing general surfaces 4.1.1 After degree 2 surfaces, we could proceed to degree 3, but instead we turn to surfaces in general. We highlight some important aspects of these surfaces and ways to construct them. 4.1.2 Surfaces given as graphs of functions Suppose f : R2 R is a di®erentiable function, then the graph of f consisting of all points of the form!(x; y; f(x; y)) is a surface in 3{space with a smooth appearance due to the di®erentiability of f. Since we are not tied to degree 1 or 2 expressions for f, the resulting surfaces may have all sorts of fascinating shapes. The description as a graph can 1 1 0.5 0.5 0 0 2 2 -0.5 -0.5 -1 -1 0 -6 0 -2 -4 -2 0 -2 0 -2 2 2 Figure 4.2: Two `sinusoidal' graphs: the graphs of sin(xy) and sin(x). be seen as a special case of a parametric description: x = u y = v z = f(u; v); where u and v are the parameters. -
Polydisperse Spherical Cap Packings
Mathematisches Forschungsinstitut Oberwolfach Report No. 40/2012 DOI: 10.4171/OWR/2012/40 Optimal and Near Optimal Configurations on Lattices and Manifolds Organised by Christine Bachoc, Bordeaux Peter Grabner, Graz Edward B. Saff, Nashville Achill Sch¨urmann, Rostock 19th August – 25th August 2012 Abstract. Optimal configurations of points arise in many contexts, for ex- ample classical ground states for interacting particle systems, Euclidean pack- ings of convex bodies, as well as minimal discrete and continuous energy problems for general kernels. Relevant questions in this area include the understanding of asymptotic optimal configurations, of lattice and periodic configurations, the development of algorithmic constructions of near optimal configurations, and the application of methods in convex optimization such as linear and semidefinite programming. Mathematics Subject Classification (2000): 11K41, 52C17, 11H31. Introduction by the Organisers The workshop Optimal and Near Optimal Configurations on Lattices and Mani- folds, organised by Christine Bachoc (Bordeaux), Peter Grabner (Graz), Ed Saff (Nashville) and Achill Sch¨urmann (Rostock), was held 19 August –25 August 2012. This meeting has gathered 27 participants from various areas of mathemat- ics, mostly Approximation Theory, Optimization, Number Theory and Discrete Geometry. Bringing together mathematicians with a variety of expertise on opti- mal configurations on lattices and manifolds was one of the aims of this workshop and was indeed fully achieved. A broad range of topics have been covered during the talks, especially minimal energy configurations, best packings in Euclidean 2430 Oberwolfach Report 40/2012 space or on other spaces, spherical designs, Euclidean lattices and linear and semi- definite programming methods. Theoretical as well as computational issues have been addressed. -
Volume and Area Ratios with Geogebra Libuse Samkova
10 North American GeoGebra Journal (ISSN: 2162-3856) Vol. 2, No. 1, 2013 Volume and area ratios with GeoGebra Libuse Samkova Abstract: This article was motivated by student work in a biological laboratory where a question 1 was asked regarding the liquid level corresponding to 5 of the volume of a laboratory flask. In this article, we use GeoGebra to explore such questions, analyzing volume and area ratios for containers of various shapes. We present various dynamic GeoGebra models including one of the experiment which initiated the article. Keywords: GeoGebra, modeling, algebraic proof, physics 1. INTRODUCTION moment, the volume of the liquid in the cylindrical por- 1 tion of the flask). Note that 5 of the ball volume does not 1 This article was motivated by student work in a biological correspond to 5 of the ball height. laboratory during the demonstration of a candle experi- The volume of a ball with radius r is given by a formula ment similar to that suggested illustrated in Fig. 1. 4 3 3 pr . The liquid in the ball reaches an unknown height h, and its volume equals the volume of the shaded re- gion shown in Fig. 2 (which we refer to as a spherical cap). Fig 1: An illustration of a candle experiment (Gallástegui 2011). The student experimenter ended the presentation by stat- Fig 2: Front views of the liquid in the ball (left), and of ing that “the liquid in the flask occupies 20% of the flask the spherical cap (right). volume,” and the audience nodded in agreement. Is it re- 1 A basic volume formula for a spherical cap with height h ally so easy to determine 5 of the flask volume? Con- sider the following steps required to complete the calcula- and base radius a is given by tion. -
Exact Calculation of the Overlap Volume of Spheres and Mesh Elements
Exact calculation of the overlap volume of spheres and mesh elements Severin Strobla,∗, Arno Formellab, Thorsten Poschel¨ a aInstitute for Multiscale Simulation, Friedrich-Alexander-Universit¨atErlangen-N¨urnberg, N¨agelsbachstr. 49 b, 91052 Erlangen, Germany bDepartment of Computer Science, Universidade de Vigo, Ourense, Spain Abstract An algorithm for the exact calculation of the overlap volume of a sphere and a tetrahedron, wedge, or hexahedron is described. The method can be used to determine the exact local solid fractions for a system of spherical, non- overlapping particles contained in a complex mesh, a question of significant relevance for the numerical solution of many fluid-solid interaction problems. While challenging due to the limited machine precision, a numerically robust version of the calculation maintaining high computational efficiency is devised. The method is evaluated with respect to the numerical precision and computational cost. It is shown that the exact calculation is only limited by the machine precision and can be applied to a wide range of size ratios, contrary to previously published methods. Eliminating this constraint enables the usage of meshes with higher resolution near the system boundaries for coupled CFD–DEM simulations. The numerical robustness is further illustrated by applying the method to highly deformed mesh elements. The full source code of the reference implementation is made available under an open-source license. Keywords: overlap volume, local solid fraction, numerical robustness, sphere-mesh overlap 1. Introduction Spherical objects are still the most commonly used primitives in a wide range of numerical simulations. Despite their alleged simplicity, particle methods often rely on spherical particles benefiting from an efficient contact detection and the availability of physically realistic force models with a relatively low numerical cost. -
Analytical Calculation of the Solid Angle Subtended by an Arbitrarily Positioned Ellipsoid Eric Heitz
Analytical calculation of the solid angle subtended by an arbitrarily positioned ellipsoid Eric Heitz To cite this version: Eric Heitz. Analytical calculation of the solid angle subtended by an arbitrarily positioned ellip- soid. Nuclear Instruments and Methods in Physics Research Section A: Accelerators, Spectrometers, Detectors and Associated Equipment, Elsevier, 2017. hal-01402302v3 HAL Id: hal-01402302 https://hal.archives-ouvertes.fr/hal-01402302v3 Submitted on 5 Feb 2017 HAL is a multi-disciplinary open access L’archive ouverte pluridisciplinaire HAL, est archive for the deposit and dissemination of sci- destinée au dépôt et à la diffusion de documents entific research documents, whether they are pub- scientifiques de niveau recherche, publiés ou non, lished or not. The documents may come from émanant des établissements d’enseignement et de teaching and research institutions in France or recherche français ou étrangers, des laboratoires abroad, or from public or private research centers. publics ou privés. Analytical calculation of the solid angle subtended by an arbitrarily positioned ellipsoid Eric Heitz Unity Technologies Abstract We present a geometric method for computing an ellipse that subtends the same solid-angle domain as an arbitrarily positioned ellipsoid. With this method we can extend existing analytical solid-angle calculations of ellipses to ellipsoids. Our idea consists of applying a linear transformation on the ellipsoid such that it is transformed into a sphere from which a disk that covers the same solid-angle domain can be computed. We demonstrate that by applying the inverse linear transformation on this disk we obtain an ellipse that subtends the same solid-angle domain as the ellipsoid. -
Math.PR] 9 Aug 2016 Rprisascae Ihaconfiguration a with Associated Properties Upr Fteewnsh¨Dne Nttt Nven,Weepart Where B Vienna, E
RANDOM POINT SETS ON THE SPHERE — HOLE RADII, COVERING, AND SEPARATION J. S. BRAUCHART, A. B. REZNIKOV, E. B. SAFF, I. H. SLOAN, Y. G. WANG AND R. S. WOMERSLEY Abstract. Geometric properties of N random points distributed independently and uni- formly on the unit sphere Sd Rd+1 with respect to surface area measure are obtained and several related conjectures are⊂ posed. In particular, we derive asymptotics (as N ) for the expected moments of the radii of spherical caps associated with the facets→ of the∞ convex hull of N random points on Sd. We provide conjectures for the asymptotic distri- bution of the scaled radii of these spherical caps and the expected value of the largest of these radii (the covering radius). Numerical evidence is included to support these conjec- tures. Furthermore, utilizing the extreme law for pairwise angles of Cai et al., we derive precise asymptotics for the expected separation of random points on Sd. 1. Introduction This paper is concerned with geometric properties of random points distributed inde- pendently and uniformly on the unit sphere Sd Rd+1. The two most common geometric ⊂ d properties associated with a configuration XN = x1,..., xN of distinct points on S are the covering radius (also known as fill radius or mesh{ norm),} d α(XN ) := α(XN ; S ) := max min arccos(y, xj), y Sd 1 j N ∈ ≤ ≤ d which is the largest geodesic distance from a point in S to the nearest point in XN (or the geodesic radius of the largest spherical cap that contains no points from XN ), and the separation distance ϑ(XN ) := min arccos(xj, xk), arXiv:1512.07470v2 [math.PR] 9 Aug 2016 1 j,k N ≤j=k≤ 6 Date: August 10, 2016.