Wool & Weaving Education Pack
Total Page:16
File Type:pdf, Size:1020Kb
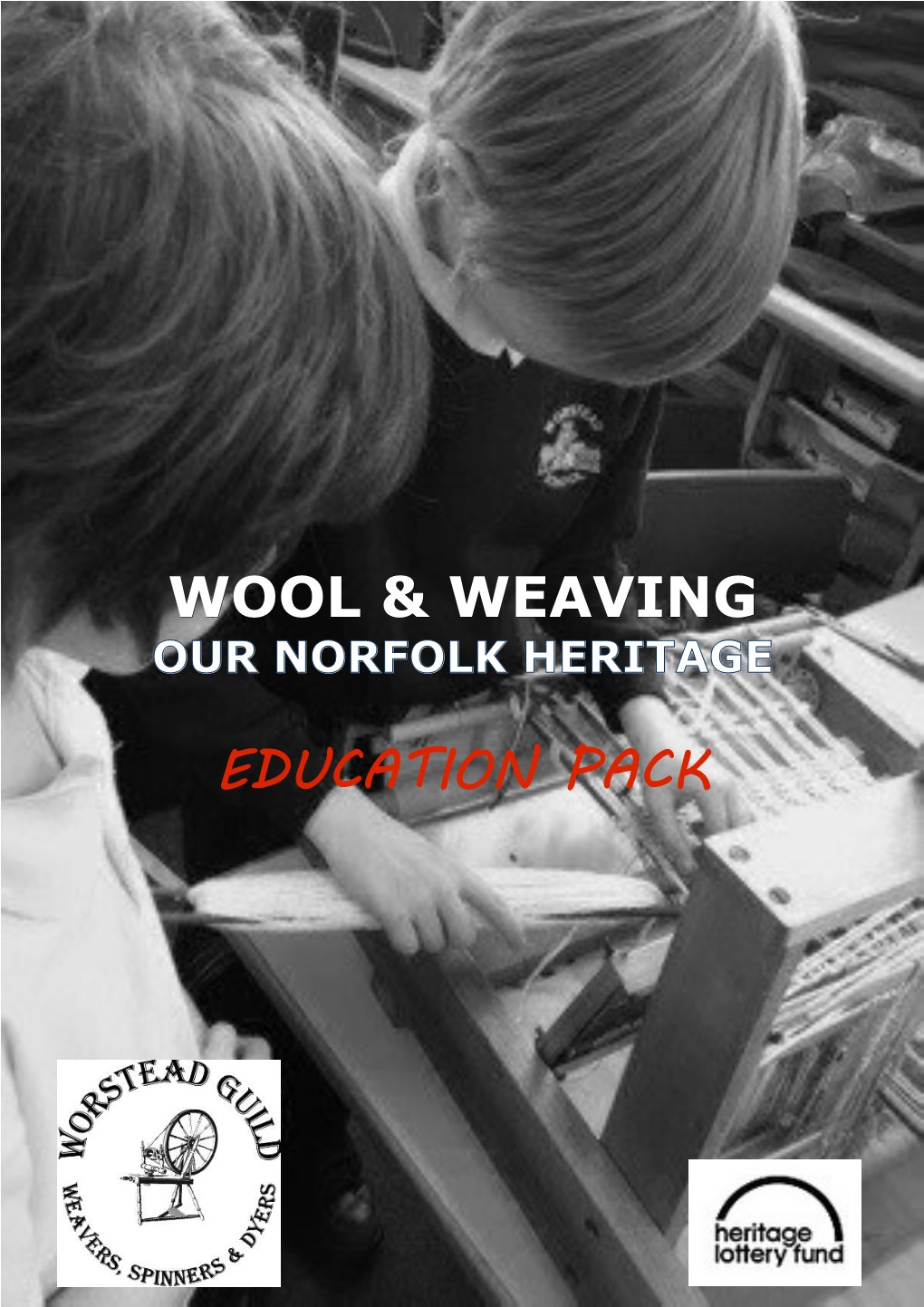
Load more
Recommended publications
-
The Rhetoric of the Saints in Middle English Bibiical Drama by Chester N. Scoville a Thesis Submitted in Conformity with The
The Rhetoric of the Saints in Middle English BibIical Drama by Chester N. Scoville A thesis submitted in conformity with the requirements for the degree of Doctor of Philosophy Graduate Department of English University of Toronto O Copyright by Chester N. Scoville (2000) National Library Bibiiotheque nationale l*l ,,na& du Canada Acquisitions and Acquisitions et Bibliographie Services services bibliographiques 395 Wellington Street 395, rwW~gtm OttawaON KlAûîU4 OtÈewaûN K1AW canada canada The author has granted a non- L'auteur a accordé une licence non exclusive licence allowing the exclusive permettant à la National Library of Canada to Bibliothèque nationale du Canada de reproduce, loan, distribute or sel1 reproduire, prêter, distribuer ou copies of this thesis in microform, vendre des copies de cette thèse sous paper or electronic formats. la forme de microfiche/nlm, de reproduction sur papier ou sur format électronique. The author retains ownership of the L'auteur conserve la propriété du copyright in this thesis. Neither the droit d'auteur qui protège cette thèse. thesis nor substantial extracts fiom it Ni la thèse ni des extraits substantiels may be printed or otheMrise de celle-ci ne doivent être imprimés reproduced without the author's ou autrement reproduits sans son permission. autorisation. Abstract of Thesis for the Degree of Doctor of Philosophy 2000 Department of English, University of Toronto The Rhetoric of the Saints in Middle English Biblical Dnma by Chester N. Scovilie Much past criticism of character in Middle English drarna has fallen into one of two rougtily defined positions: either that early drama was to be valued as an example of burgeoning realism as dernonstrated by its villains and rascals, or that it was didactic and stylized, meant primarily to teach doctrine to the faithfùl. -
Tartan As a Popular Commodity, C.1770-1830. Scottish Historical Review, 95(2), Pp
Tuckett, S. (2016) Reassessing the romance: tartan as a popular commodity, c.1770-1830. Scottish Historical Review, 95(2), pp. 182-202. (doi:10.3366/shr.2016.0295) This is the author’s final accepted version. There may be differences between this version and the published version. You are advised to consult the publisher’s version if you wish to cite from it. http://eprints.gla.ac.uk/112412/ Deposited on: 22 September 2016 Enlighten – Research publications by members of the University of Glasgow http://eprints.gla.ac.uk SALLY TUCKETT Reassessing the Romance: Tartan as a Popular Commodity, c.1770-1830 ABSTRACT Through examining the surviving records of tartan manufacturers, William Wilson & Son of Bannockburn, this article looks at the production and use of tartan in the late eighteenth and early nineteenth centuries. While it does not deny the importance of the various meanings and interpretations attached to tartan since the mid-eighteenth century, this article contends that more practical reasons for tartan’s popularity—primarily its functional and aesthetic qualities—merit greater attention. Along with evidence from contemporary newspapers and fashion manuals, this article focuses on evidence from the production and popular consumption of tartan at the turn of the nineteenth century, including its incorporation into fashionable dress and its use beyond the social elite. This article seeks to demonstrate the contemporary understanding of tartan as an attractive and useful commodity. Since the mid-eighteenth century tartan has been subjected to many varied and often confusing interpretations: it has been used as a symbol of loyalty and rebellion, as representing a fading Highland culture and heritage, as a visual reminder of the might of the British Empire, as a marker of social status, and even as a means of highlighting racial difference. -
Dress and Cultural Difference in Early Modern Europe European History Yearbook Jahrbuch Für Europäische Geschichte
Dress and Cultural Difference in Early Modern Europe European History Yearbook Jahrbuch für Europäische Geschichte Edited by Johannes Paulmann in cooperation with Markus Friedrich and Nick Stargardt Volume 20 Dress and Cultural Difference in Early Modern Europe Edited by Cornelia Aust, Denise Klein, and Thomas Weller Edited at Leibniz-Institut für Europäische Geschichte by Johannes Paulmann in cooperation with Markus Friedrich and Nick Stargardt Founding Editor: Heinz Duchhardt ISBN 978-3-11-063204-0 e-ISBN (PDF) 978-3-11-063594-2 e-ISBN (EPUB) 978-3-11-063238-5 ISSN 1616-6485 This work is licensed under a Creative Commons Attribution-NonCommercial-NoDerivatives 04. International License. For details go to http://creativecommons.org/licenses/by-nc-nd/4.0/. Library of Congress Control Number:2019944682 Bibliographic information published by the Deutsche Nationalbibliothek The Deutsche Nationalbibliothek lists this publication in the Deutsche Nationalbibliografie; detailed bibliographic data are available on the Internet at http://dnb.dnb.de. © 2019 Walter de Gruyter GmbH, Berlin/Boston The book is published in open access at www.degruyter.com. Typesetting: Integra Software Services Pvt. Ltd. Printing and Binding: CPI books GmbH, Leck Cover image: Eustaţie Altini: Portrait of a woman, 1813–1815 © National Museum of Art, Bucharest www.degruyter.com Contents Cornelia Aust, Denise Klein, and Thomas Weller Introduction 1 Gabriel Guarino “The Antipathy between French and Spaniards”: Dress, Gender, and Identity in the Court Society of Early Modern -
Historic Furnishings Assessment, Morristown National Historical Park, Morristown, New Jersey
~~e, ~ t..toS2.t.?B (Y\D\L • [)qf- 331 I J3d-~(l.S National Park Service -- ~~· U.S. Department of the Interior Historic Furnishings Assessment Morristown National Historical Park, Morristown, New Jersey Decemb r 2 ATTENTION: Portions of this scanned document are illegible due to the poor quality of the source document. HISTORIC FURNISHINGS ASSESSMENT Ford Mansion and Wic·k House Morristown National Historical Park Morristown, New Jersey by Laurel A. Racine Senior Curator ..J Northeast Museum Services Center National Park Service December 2003 Introduction Morristown National Historical Park has two furnished historic houses: The Ford Mansion, otherwise known as Washington's Headquarters, at the edge of Morristown proper, and the Wick House in Jockey Hollow about six miles south. The following report is a Historic Furnishings Assessment based on a one-week site visit (November 2001) to Morristown National Historical Park (MORR) and a review of the available resources including National Park Service (NPS) reports, manuscript collections, photographs, relevant secondary sources, and other paper-based materials. The goal of the assessment is to identify avenues for making the Ford Mansion and Wick House more accurate and compelling installations in order to increase the public's understanding of the historic events that took place there. The assessment begins with overall issues at the park including staffing, interpretation, and a potential new exhibition on historic preservation at the Museum. The assessment then addresses the houses individually. For each house the researcher briefly outlines the history of the site, discusses previous research and planning efforts, analyzes the history of room use and furnishings, describes current use and conditions, indicates extant research materials, outlines treatment options, lists the sources consulted, and recommends sourc.es for future consultation. -
YOUNIQUE TOUCH Pressed Powder Foundation
Fact Sheet YOUNIQUE TOUCH Pressed Powder Foundation New shades. New formula. Meet your match. We’ve got you covered with YOUNIQUE TOUCH pressed powder foundation. Our new formula goes on silky smooth to create a flawless, airbrushed finish with buildable, medium-to-full coverage. With brand-new shade options (in addition to our classic shades of TOUCH MINERAL pressed powder foundation), we’re sure you’ll be able to find your perfect match. TELL ME MORE APPLICATION TIPS USE WITH • Smooth and easy application with 1. Swirl the YOUNIQUE™ powder • Included foundation sponge a velvety soft feel puff brush or YOUNIQUE™ • YOUNIQUE™ • Shine control with matte finish powder/concealer brush in powder/concealer brush or • New skin-flattering shades: product, tapping away excess. YOUNIQUE™ powder • Crepe • Damask You can also swipe foundation puff brush • Camlet • Dupioni onto the included • TOUCH MINERAL skin • Poplin • Twill foundation sponge. perfecting concealer • Jacquard • Sable 2. Apply from center of face • Tweed • Percale towards outer edges. • Gingham • Brocade 3. Continue to build for • Voile desired coverage. Price for 8 g / 0.28 oz: $32 USD | $39 CAD | $46 AUD | $45 NZD | £25 GBP | $560 MXN | 34,50 € EUR | HK$248 ABOUT YOUNIQUE Nature + Love + Science. Since its inception in 2012, Younique has been committed to developing beauty products that combine innovative science with the best ingredients nature has to offer. Younique, famous for its best-selling MOODSTRUCK 3D FIBER LASHES+™ lash enhancer, is the first direct-selling company to pioneer the social media-based business model. Founded by a brother-sister team—Derek Maxfield and Melanie Huscroft—Younique offers women the opportunity to look and feel great while helping advance the brand’s mission to uplift, empower, and validate women around the world. -
Historic Costuming Presented by Jill Harrison
Historic Southern Indiana Interpretation Workshop, March 2-4, 1998 Historic Costuming Presented By Jill Harrison IMPRESSIONS Each of us makes an impression before ever saying a word. We size up visitors all the time, anticipating behavior from their age, clothing, and demeanor. What do they think of interpreters, disguised as we are in the threads of another time? While stressing the importance of historically accurate costuming (outfits) and accoutrements for first- person interpreters, there are many reasons compromises are made - perhaps a tight budget or lack of skilled construction personnel. Items such as shoes and eyeglasses are usually a sticking point when assembling a truly accurate outfit. It has been suggested that when visitors spot inaccurate details, interpreter credibility is downgraded and visitors launch into a frame of mind to find other inaccuracies. This may be true of visitors who are historical reenactors, buffs, or other interpreters. Most visitors, though, lack the heightened awareness to recognize the difference between authentic period detailing and the less-than-perfect substitutions. But everyone will notice a wristwatch, sunglasses, or tennis shoes. We have a responsibility to the public not to misrepresent the past; otherwise we are not preserving history but instead creating our own fiction and calling it the truth. Realistically, the appearance of the interpreter, our information base, our techniques, and our environment all affect the first-person experience. Historically accurate costuming perfection is laudable and reinforces academic credence. The minute details can be a springboard to important educational concepts; but the outfit is not the linchpin on which successful interpretation hangs. -
Week 3 the Woollen & Worsted Industries to 1780
Week 3 Dr Frances Richardson frances.richardson@conted. The woollen & ox.ac.uk https://open.conted.ox.ac.uk /series/manufactures- worsted industries industrial-revolution to 1780 Week 2 takeaways • Proto-industrialization theories give us some useful concepts for studying specific pre-factory manufacturing industries • More a framework than a predictive model • Artisan systems did not necessarily develop into putting-out systems • Proto-industry contained the seeds of its own demise • Although factory industrialization often grew out of proto-industry in the same area, some areas de-industrialized and industry spread to new areas • Other factors needed to explain changes, including marketing, industrial relations, and local politics Week 3 outline • Processes in woollen and worsted hand manufacture • Outline history – changing fashions, home demand and exports Wool comber • Organization of the industry in the West Country, Norwich and Yorkshire • How organisation and marketing affected success • How well different regions responded to changing fashion and demand Woollen cloth • Used carded, short-staple wool • Traditional from medieval period, predominated in Tudor exports • Types of cloth - broadcloth, kersey (lighter, less heavily fulled) • Export cloth high and medium quality – limited demand growth • Wool was sorted, willeyed, carded, spun, woven, fulled, finished – could involve raising nap, shearing, pressing, dyeing Broadcloth suit, 1705, VAM Worsted • Used combed, long-staple wool Lincoln longwool sheep • More suited to the Saxony -
Big Timber Pioneer | Thursday, November 12, 2020
PIONEERTHE BIG TIMBER WWW.BIGTIMBERPIONEER.NET $1 THURSDAY, NOVEMBER 12, 2020 | VOL. 132 NO. 6 Local marine returns home after nearly five years of active duty By G.Q. Hansen month security detail in the rugged Pioneer Staff Writer battle-scarred region of Afghani- stan, the graveyard of empires. losing five years of “It gave me a new perspective active duty and making just how good we have it,” he said. his way around the “People think everything sucks but globe, corporal Ian Gar- it could always be worse.” cia finally returned When asked what Afghanistan Chome to Big Timber late last month. was like, he said with a smile, After spanning the continents, “hot.” grasping cultures and christened in The base he would be stationed faraway customs, Garcia, of 1st at was attacked prior to his arrival Batallion, 7th Marines, has jour- and he mentioned there was antici- neyed home with a Navy and pation, that the troops were expect- Marine Corps. Achievement Medal ing something again. to his name. “You settle into a rhythm after a After he graduated from Sweet while and realize the bombs going Grass County High School, Garcia off, ‘alright that’s normal,’” he said. remembered lightheartedly coach- His company was tasked with ing his last Little Herder football providing security detail for mili- game before he left a few days lat- tary advisors to Afghan forces and er for the employ of the Comman- instructing soldiers within the dant, for God and Country, in the province. A duty that seemed frus- United States Marine Corps. -
Modernism for the Future: an International Conference
Modernism for the Future: An International Conference Conference Proceedings September 12–13, 2018, Kaunas, Lithuania European Year of Cultural Heritage 2018 Modernism for the Future 1 Organizers Kaunas – European Capital of Culture 2022 Lithuanian National Commission for UNESCO International Scientific Committee Edward Denison (The Bartlett School of Architecture, UCL) Marija Drėmaitė (Vilnius University) Giedrė Jankevičiūtė (Lithuanian Institute for Culture Research) Vaidas Petrulis (Kaunas University of Technology) Viltė Migonytė-Petrulienė (Vytautas Magnus University) Renata Kepežinskienė (Lithuanian National Commision for UNESCO) Vladimir Šlapeta (Brno University of Technology) Proceedings Editor: Vaidas Petrulis Language editor: George Vaitkunas Designer: Vytis Gruzdys Kaunas – European Capital of Culture 2022 kaunas2022.eu Kaunas, 2019 Copyright according to Creative Commons license CC BY-NC-ND, unless otherwise stated Terms on creativecommons.org/licenses/by-nc-nd/2.0/ ISBN 978-609-96109-0-0 2 Modernism for the Future 3 Contents INTRODUCTION 6 Approaches for the Conservation of 20th Century Architectural Heritage 140 Vaidas Petrulis (The Madrid Document): A Good Example to be Followed Fernando Espinosa de los Monteros OPENING SESSION SESSION IV – Artistic interpretations of Modernism Self-Realization of the Newly Liberated: Architecture in the Baltic States 10 Between the World Wars Why Do We Need to Decentre Modernism? Art History and 150 Mart Kalm Avant-Garde Art from the Periphery Partha Mitter SESSION I – National Modernisms -
A Household Inventory, 1581 Author(S): Albert J
A Household Inventory, 1581 Author(s): Albert J. Schmidt Source: Proceedings of the American Philosophical Society, Vol. 101, No. 5 (Oct. 31, 1957), pp. 459-480 Published by: American Philosophical Society Stable URL: https://www.jstor.org/stable/985201 Accessed: 26-07-2020 17:49 UTC JSTOR is a not-for-profit service that helps scholars, researchers, and students discover, use, and build upon a wide range of content in a trusted digital archive. We use information technology and tools to increase productivity and facilitate new forms of scholarship. For more information about JSTOR, please contact [email protected]. Your use of the JSTOR archive indicates your acceptance of the Terms & Conditions of Use, available at https://about.jstor.org/terms American Philosophical Society is collaborating with JSTOR to digitize, preserve and extend access to Proceedings of the American Philosophical Society This content downloaded from 129.2.19.103 on Sun, 26 Jul 2020 17:49:49 UTC All use subject to https://about.jstor.org/terms A HOUSEHOLD INVENTORY, 1581 ALBERT J. SCHMIDT Associate Professor of History, Coe College ONE of the most valuable sources for the died in May, 1581, he was about fifty-eight years biographer, Shakespearian scholar, and social old. Twice married,4 he had outlived both his historian of the sixteenth century is the house- spouses. He had by his first wife three children, hold inventory. The inventory was simply an two girls and a boy, all of whom were still under account of the goods, chattels, and lands found age at the time of his death. -
Coverage That's Blendable, Light, and Totally on Point
Fact Sheet YOUNIQUE TOUCH Loose Powder Foundation Coverage that’s blendable, light, and totally on point. Our YOUNIQUE TOUCH loose powder foundation is an innovative and easy way to get seamless coverage with an incredibly soft feel. Just buff your way to the coverage you want for that perfect no-makeup makeup look. This weightless foundation is buildable but never cakey or heavy—you’re left with natural-looking radiance and a smooth finish. YOUNIQUE TOUCH loose powder foundation looks flawless on its own or paired with any of our other foundations for a polished, matte finish. This dreamy powder foundation is definitely a match made in heaven. TELL ME MORE APPLICATION TIPS USE WITH • Weightless, buildable coverage 1. Gently press the YOUNIQUE™ • YOUNIQUE™ that never feels cakey or heavy powder/concealer brush into the powder/concealer brush • Comes in a range of beautiful YOUNIQUE TOUCH loose • YOUNIQUE™ powder puff shades: powder foundation mesh sifter. brush • Crepe • Damask 2. Tap away the excess and then • TOUCH MINERAL skin • Camlet • Dupioni buff the powder onto skin in perfecting concealer • Poplin • Twill circular motions until desired • Jacquard • Sable coverage is achieved. • Tweed • Percale • Gingham • Brocade • Voile Price for 9 g / 0.32 oz: $32 USD | $39 CAD | $46 AUD | $45 NZD | £25 GBP | $560 MXN | 34,50 € EUR | HK$248 ABOUT YOUNIQUE Nature + Love + Science. Since its inception in 2012, Younique has been committed to developing beauty products that combine innovative science with the best ingredients nature has to offer. Younique, famous for its best-selling MOODSTRUCK 3D FIBER LASHES+™ lash enhancer, is the first direct-selling company to pioneer the social media-based business model. -
Inns and Innkeeping in North Hertfordshire: 1660
INNS AND INNKEEPING IN NORTH HERTFORDSHIRE: 1660 - 1815 Annika McQueen Wolfson College Faculty of Architecture and History of Art Department of Building History University of Cambridge The full version of this dissertation was submitted for the degree of Master of Studies in Building History in May 2019. A copy is held by the Architecture and History of Art Library, University of Cambridge. This is a redacted version in adherence to copyright regulations. © Annika McQueen, 2019 1 Editorial Conventions In direct quotations from contemporary sources, the original spelling and capitalisation has been retained. Modern punctuation has been inserted in the case of lists. Old Style dating in contemporary sources has been addressed by the use of a slash date separator where the New Style dating equivalent is uncertain e.g. 1684/5. Currency is in pounds (£), shillings (s) and pence (d): there were 12 old pence to the shilling, 20 shillings or 240 old pence to the pound. Unless otherwise attributed, all drawings and photographs are the work of the author. Measurements in drawings by the author are in metres. This dissertation contains plans and drawings which are best viewed digitally. ii Acknowledgements I would like to express my thanks to the following individuals: • Dr Adam Menuge at the Department of Building History, University of Cambridge for his support and encouragement during my studies in his role as Course Director, and for his helpful guidance and comments on early drafts of this dissertation as my Supervisor. • Dr Debbie Pullinger at Wolfson College, Cambridge for her support and encouragement as College Tutor to part-time students.