Buoyancy and Load Exchange for Transport Airships
Total Page:16
File Type:pdf, Size:1020Kb
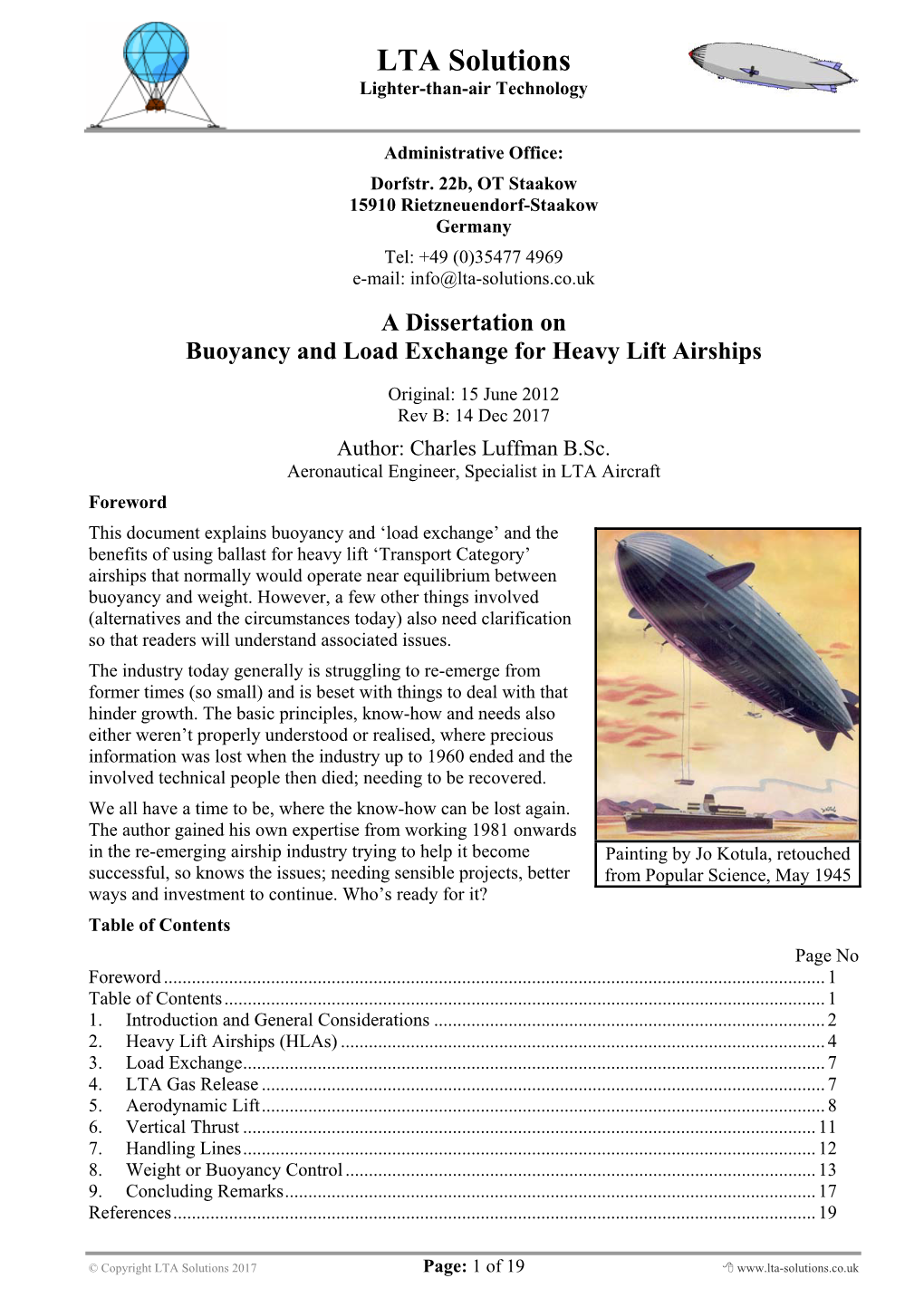
Load more
Recommended publications
-
A01 the Most Important Industrial Gases – Applications and Properties
A01 The most important industrial gases – Applications and properties Gas overview (table) Name Property / hazards Delivery form / hazards Liquefied Inert / non- Oxidising/fire Dissolved (in Cryogenically Combustible Gaseous under pres- Solid flammable intensifying solvent) liquefied sure Acetylene X X Argon X X X Helium X X X Carbon dioxide X X X X Oxygen X X X Nitrogen X X X Hydrogen X X X Propane (bu- X X tane) Acetylene (C2H2) Properties / manufacture Acetylene is a colourless, non-toxic fuel gas with a faint odour that is slightly lighter than air (relative density = 0.91). Acetylene is transported and stored in pressurised gas cylinders with a porous filling, dissolved in acetone. The cylinder must therefore be stored upright. It is produced from calcium carbide in acetylene generators or by the petrochemical sector. Main applications Multi-purpose fuel gas (autogenous welding and cutting process), chemical synthe- ses, etc. Safety Under unfavourable conditions, the energy-rich acetylene molecule can decompose without the involvement of oxygen, thereby releasing energy. This self- Shoulder decomposition can be initiated when an acetylene cylinder is exposed to high levels colour “oxide red” of heat or by flashback in the cylinder. The start of decomposition can be detected RAL 3009 by the generation of heat in the cylinder. Acetylene forms explosive mixtures with air. Ignition range in air: 2.3 - 82 % Self-ignition temperature in air: 305 °C A01 The most important industrial gases IGS-TS-A01-17-d Page 1 of 4 Argon (Ar) Properties / manufacture Argon is a colourless, odourless, non-combustible gas, extremely inert noble gas and heavier than air (relative density = 1.78). -
Colonization of Venus
Conference on Human Space Exploration, Space Technology & Applications International Forum, Albuquerque, NM, Feb. 2-6 2003. Colonization of Venus Geoffrey A. Landis NASA Glenn Research Center mailstop 302-1 21000 Brook Park Road Cleveland, OH 44135 21 6-433-2238 geofrq.landis@grc. nasa.gov ABSTRACT Although the surface of Venus is an extremely hostile environment, at about 50 kilometers above the surface the atmosphere of Venus is the most earthlike environment (other than Earth itself) in the solar system. It is proposed here that in the near term, human exploration of Venus could take place from aerostat vehicles in the atmosphere, and that in the long term, permanent settlements could be made in the form of cities designed to float at about fifty kilometer altitude in the atmosphere of Venus. INTRODUCTION Since Gerard K. O'Neill [1974, 19761 first did a detailed analysis of the concept of a self-sufficient space colony, the concept of a human colony that is not located on the surface of a planet has been a major topic of discussion in the space community. There are many possible economic justifications for such a space colony, including use as living quarters for a factory producing industrial products (such as solar power satellites) in space, and as a staging point for asteroid mining [Lewis 19971. However, while the concept has focussed on the idea of colonies in free space, there are several disadvantages in colonizing empty space. Space is short on most of the raw materials needed to sustain human life, and most particularly in the elements oxygen, hydrogen, carbon, and nitrogen. -
2013 News Archive
Sep 4, 2013 America’s Challenge Teams Prepare for Cross-Country Adventure Eighteenth Race Set for October 5 Launch Experienced and formidable. That describes the field for the Albuquerque International Balloon Fiesta’s 18th America’s Challenge distance race for gas balloons. The ten members of the five teams have a combined 110 years of experience flying in the America’s Challenge, along with dozens of competitive years in the other great distance race, the Coupe Aéronautique Gordon Bennett. Three of the five teams include former America’s Challenge winners. The object of the America’s Challenge is to fly the greatest distance from Albuquerque while competing within the event rules. The balloonists often stay aloft more than two days and must use the winds aloft and weather systems to their best advantage to gain the greatest distance. Flights of more than 1,000 miles are not unusual, and the winners sometimes travel as far as Canada and the U.S. East Coast. This year’s competitors are: • Mark Sullivan and Cheri White, USA: Last year Sullivan, from Albuquerque, and White, from Austin, TX, flew to Beauville, North Carolina to win their second America’s Challenge (their first was in 2008). Their winning 2012 flight of 2,623 km (1,626 miles) ended just short of the East Coast and was the fourth longest in the history of the race. The team has finished as high as third in the Coupe Gordon Bennett (2009). Mark Sullivan, a multiple-award-winning competitor in both hot air and gas balloons and the American delegate to the world ballooning federation, is the founder of the America’s Challenge. -
Atmospheric Planetary Probes And
SPECIAL ISSUE PAPER 1 Atmospheric planetary probes and balloons in the solar system A Coustenis1∗, D Atkinson2, T Balint3, P Beauchamp3, S Atreya4, J-P Lebreton5, J Lunine6, D Matson3,CErd5,KReh3, T R Spilker3, J Elliott3, J Hall3, and N Strange3 1LESIA, Observatoire de Paris-Meudon, Meudon Cedex, France 2Department Electrical & Computer Engineering, University of Idaho, Moscow, ID, USA 3Jet Propulsion Laboratory, California Institute of Technology, Pasadena, CA, USA 4University of Michigan, Ann Arbor, MI, USA 5ESA/ESTEC, AG Noordwijk, The Netherlands 6Dipartment di Fisica, University degli Studi di Roma, Rome, Italy The manuscript was received on 28 January 2010 and was accepted after revision for publication on 5 November 2010. DOI: 10.1177/09544100JAERO802 Abstract: A primary motivation for in situ probe and balloon missions in the solar system is to progressively constrain models of its origin and evolution. Specifically, understanding the origin and evolution of multiple planetary atmospheres within our solar system would provide a basis for comparative studies that lead to a better understanding of the origin and evolution of our Q1 own solar system as well as extra-solar planetary systems. Hereafter, the authors discuss in situ exploration science drivers, mission architectures, and technologies associated with probes at Venus, the giant planets and Titan. Q2 Keywords: 1 INTRODUCTION provide significant design challenge, thus translating to high mission complexity, risk, and cost. Since the beginning of the space age in 1957, the This article focuses on the exploration of planetary United States, European countries, and the Soviet bodies with sizable atmospheres, using entry probes Union have sent dozens of spacecraft, including and aerial mobility systems, namely balloons. -
Rest of the Solar System” As We Have Covered It in MMM Through the Years
As The Moon, Mars, and Asteroids each have their own dedicated theme issues, this one is about the “rest of the Solar System” as we have covered it in MMM through the years. Not yet having ventured beyond the Moon, and not yet having begun to develop and use space resources, these articles are speculative, but we trust, well-grounded and eventually feasible. Included are articles about the inner “terrestrial” planets: Mercury and Venus. As the gas giants Jupiter, Saturn, Uranus, and Neptune are not in general human targets in themselves, most articles about destinations in the outer system deal with major satellites: Jupiter’s Io, Europa, Ganymede, and Callisto. Saturn’s Titan and Iapetus, Neptune’s Triton. We also include past articles on “Space Settlements.” Europa with its ice-covered global ocean has fascinated many - will we one day have a base there? Will some of our descendants one day live in space, not on planetary surfaces? Or, above Venus’ clouds? CHRONOLOGICAL INDEX; MMM THEMES: OUR SOLAR SYSTEM MMM # 11 - Space Oases & Lunar Culture: Space Settlement Quiz Space Oases: Part 1 First Locations; Part 2: Internal Bearings Part 3: the Moon, and Diferent Drums MMM #12 Space Oases Pioneers Quiz; Space Oases Part 4: Static Design Traps Space Oases Part 5: A Biodynamic Masterplan: The Triple Helix MMM #13 Space Oases Artificial Gravity Quiz Space Oases Part 6: Baby Steps with Artificial Gravity MMM #37 Should the Sun have a Name? MMM #56 Naming the Seas of Space MMM #57 Space Colonies: Re-dreaming and Redrafting the Vision: Xities in -
Are Airships Making a Comeback? Nicolas Raymond
Mike Follows Are airships making a comeback? Nicolas Raymond Hot air balloons over When hot air balloons are propelled through the Quebec, Canada air rather than just being pushed along by the wind they are known as airships or dirigibles. The heyday of airships came to an abrupt end when the Hindenburg crashed dramatically in 1937. But, as Mike Follows explains, modern airships may Key words have a role in the future. density According to Archimedes’ Principle, any object forces immersed in a fluid receives an upthrust equal to the weight of the fluid it displaces. This can be Newton’s laws applied to lighter-than-air balloons: a balloon aircraft will descend if its weight exceeds that of the air displaced and rise if its weight is less. We can also think of this in terms of density. A balloon will rise if its overall density (balloon + air inside) is less than the density of the surrounding air. In hot-air balloons, the volume is constant and the density of air is varied by changing its temperature. Heating the air inside the envelope using the open flame from a burner in the gondola suspended beneath causes the air to expand and escape out through the bottom of the envelope. The top of the balloon usually has a vent of some sort, enabling the pilot to release hot air to slow an ascent. Colder, denser air will enter through the hole at the bottom of the envelope. Burning gas to give a hot air balloon greater lift 16 Catalyst February 2015 www.catalyststudent.org.uk Airships of the past airships. -
To What Extent Does Modern Technology Address the Problems of Past
To what extent does modern technology address the problems of past airships? Ansel Sterling Barnes Today, we have numerous technologies we take for granted: electricity, easy internet access, wireless communications, vast networks of highways crossing the continents, and flights crisscrossing the globe. Flight, though, is special because it captures man’s imagination. Humankind has dreamed of flight since Paleolithic times, and has achieved it with heavier-than-air craft such as airplanes and helicopters. Both of these are very useful and have many applications, but for certain jobs, these aircraft are not the ideal option because they are loud and waste energy. Luckily, there is an alternative to energy hogs like airplanes or helicopters, a lighter-than-air craft that predates both: airships! Airships do not generate their own lift through sheer power like heavier-than-air craft. They are airborne submarines of a sort that use a different lift source: gas. They don’t need to use the force of moving air to lift them from the ground, so they require very little energy to lift off or to fly. Unfortunately, there were problems with past airships; problems that were the reason for the decline of airships after World War II: cost, pilot skill, vulnerability to weather, complex systems control, materials, size, power source, and lifting gas. This begs the question: To what extent does modern technology address the problems of past airships? With today’s technology, said problems can be managed. Most people know lighter-than-air craft by one name or another: hot air balloons, blimps, dirigibles, zeppelins, etc. -
Gas Division Newsletter
GAS DIVISIONH NEWSLETTER Official Publication of the BFA Gas Division Volume 1, Issue 2 Copyright Peter Cuneo & Barbara Fricke, 2000 Summer 2000 DANVILLE by Barbara Fricke The invitation went out for the National Gas Balloon Race to be held with the Oldsmobile Balloon Classic Illinois in Danville, Illinois. It would be a BFA sanctioned 3-part task race instead of a distance race. Ten balloons would compete. The pilots and co-pilots who registered, according to the rally's web site ( www.balloonclassic.org ), were: Troy Bradley and Bruce Hale Rusty Elwell and Don Weeks Barbara Fricke, Ray Bair and Danni Suskin Jim Hershend and Jack Holland David Levin and George Ibach Bert Padelt and Jack Edling Johnny Petrehn and Sam Parks The first briefing was on Thursday evening. Shane Robinson, Paul Morlock and Charles Page Not much said, since weather was the main concern Stan Wereschuk and Ron Martin and the weatherman was unavailable. The flags in Randy Woods and Ted Stanley front of the hotel were almost straight out. Friday morning resulted in the only pictures taken relating to gas ballooning. The organizers had arranged for many helpers with the big mound of sand. Friday's noon briefing was positive about an evening flight. The 7:00 pm briefing put the flight on hold. The later briefing called the Friday flight off – too windy. It would have been a "Denver" windy inflation and a flight towards, if not over, Lake Erie with sunrise while over the lake. Saturday's noon briefing tried to be positive, while the weather channel was forecasting evening thundershowers. -
Airships for Planetary Exploration
NASA/CR—2004-213345 Airships for Planetary Exploration Anthony Colozza Analex Corporation, Brook Park, Ohio November 2004 The NASA STI Program Office . in Profile Since its founding, NASA has been dedicated to • CONFERENCE PUBLICATION. Collected the advancement of aeronautics and space papers from scientific and technical science. The NASA Scientific and Technical conferences, symposia, seminars, or other Information (STI) Program Office plays a key part meetings sponsored or cosponsored by in helping NASA maintain this important role. NASA. The NASA STI Program Office is operated by • SPECIAL PUBLICATION. Scientific, Langley Research Center, the Lead Center for technical, or historical information from NASA’s scientific and technical information. The NASA programs, projects, and missions, NASA STI Program Office provides access to the often concerned with subjects having NASA STI Database, the largest collection of substantial public interest. aeronautical and space science STI in the world. The Program Office is also NASA’s institutional • TECHNICAL TRANSLATION. English- mechanism for disseminating the results of its language translations of foreign scientific research and development activities. These results and technical material pertinent to NASA’s are published by NASA in the NASA STI Report mission. Series, which includes the following report types: Specialized services that complement the STI • TECHNICAL PUBLICATION. Reports of Program Office’s diverse offerings include completed research or a major significant creating custom thesauri, building customized phase of research that present the results of databases, organizing and publishing research NASA programs and include extensive data results . even providing videos. or theoretical analysis. Includes compilations of significant scientific and technical data and For more information about the NASA STI information deemed to be of continuing Program Office, see the following: reference value. -
A Comparison of Platforms for the Aerial Exploration of Titan
https://ntrs.nasa.gov/search.jsp?R=20050237895 2019-08-29T21:01:10+00:00Z View metadata, citation and similar papers at core.ac.uk brought to you by CORE provided by NASA Technical Reports Server A Comparison of Platforms for the Aerial Exploration of Titan Henry S. Wright1, Joseph F. Gasbarre2, and Dr. Joel S. Levine3 NASA Langley Research Center, Hampton, VA 23666 Exploration of Titan, envisioned as a follow-on to the highly successful Cassini-Huygens mission, is described in this paper. A mission blending measurements from a dedicated orbiter and an in-situ aerial explorer is discussed. Summary description of the science rationale and the mission architecture, including the orbiter, is provided. The mission has been sized to ensure it can be accommodated on an existing expendable heavy-lift launch vehicle. A launch to Titan in 2018 with a 6-year time of flight to Titan using a combination of Solar Electric Propulsion and aeroassist (direct entry and aerocapture) forms the basic mission architecture. A detailed assessment of different platforms for aerial exploration of Titan has been performed. A rationale for the selection of the airship as the baseline platform is provided. Detailed description of the airship, its subsystems, and its operational strategies are provided. Nomenclature cm = centimeter kg = kilogram km = kilometer m = meter mm = millimeter nm = nanometer s = second TRL = Technology Readiness Level W = Watts I. Introduction NE of the fundamental questions in all of science concerns the origin and evolution of life and the occurrence O of life beyond Earth. In the search for life in the Solar System, Titan holds a very unique position. -
Low-Cost Options for Airborne Delivery of Contraband Into North Korea
C O R P O R A T I O N Low-Cost Options for Airborne Delivery of Contraband into North Korea Richard Mason SUMMARY ■ For a number of years, various activist groups in Key findings South Korea have used hydrogen balloons to carry information and political, religious, and humanitarian materials across the border into • Modeling suggests that when balloons are North Korea. In the past, going back to the Korean War, the South launched under favorable wind conditions, Korean government itself used to launch propaganda balloons. For they can potentially penetrate deep into reasons of diplomacy, however, the South Korean government gave North Korea. up sending balloons in 2005, leaving private individuals and nongov- • Based on anecdotal reports, the balloons ernmental organizations (NGOs) in South Korea to fly their own. do not fly far across the border very often. The North Korean government strongly resents the balloons and in • It may be that the balloons are “saturating” October 2014 opened fire on one of them with an anti-aircraft gun, the border area with leaflets but not fulfill- causing South Korean forces to return fire when anti-aircraft bullets ing their full potential to reach larger areas landed inside South Korea. of the country. The NGOs’ balloon delivery techniques have evolved over time • Activist groups can probably improve their and are continuing to evolve—several NGOs have made an overt success rate by choosing launch conditions point of seeking new technological means to pursue their missions. more judiciously, with the aid of high-alti- In 2015, one organization announced that it would begin using tude wind forecasts. -
The Venus Sweet Spot: Floating Home
Science Fact The Venus Sweet Spot: Floating Home John J. Vester Venus hosts the most human-friendly environment in the Solar System, after Earth. Once the dar - ling of scientists and science-fiction writers alike, the surface of Venus has become a monu - mental disappointment as a vacation spot. With surface temperatures around 800 degrees F and atmospheric pressure of 90 bar, there will be no leisurely strolls along the rim of Artemis Coro - na in the foreseeable future. But we could live very near there in comfort, with readily available tech today, through buoy - ancy. The idea of living among the clouds of Venus in floating cities has been . well . float - ing around since at least the early ’70s, when the Russians, capitalizing on the success of their early, pioneering Venera surface probes, set forth detailed plans for great, complex habitats afloat in the so-called “sweet spot” of Venus. The Venus atmosphere is incredibly dense, but like all planetary atmospheres, it thins out to nothing with enough altitude. At one point along this diminishing spectrum, at about thirty miles above the hellish surface, the atmosphere almost exactly matches Earth’s in terms of tem - perature and pressure. And, what’s more, due to the high concentration of C O2, breathable air becomes a lifting gas. Much has been made of this opportunity (by Geoffrey Landis and others), and the internet is rife with lamentations that Venus has been for too long ignored, especially after the Venera and Magellan missions gave us so much bad news about the surface.