Diving Technologies and Techniques for the 21St Century
Total Page:16
File Type:pdf, Size:1020Kb
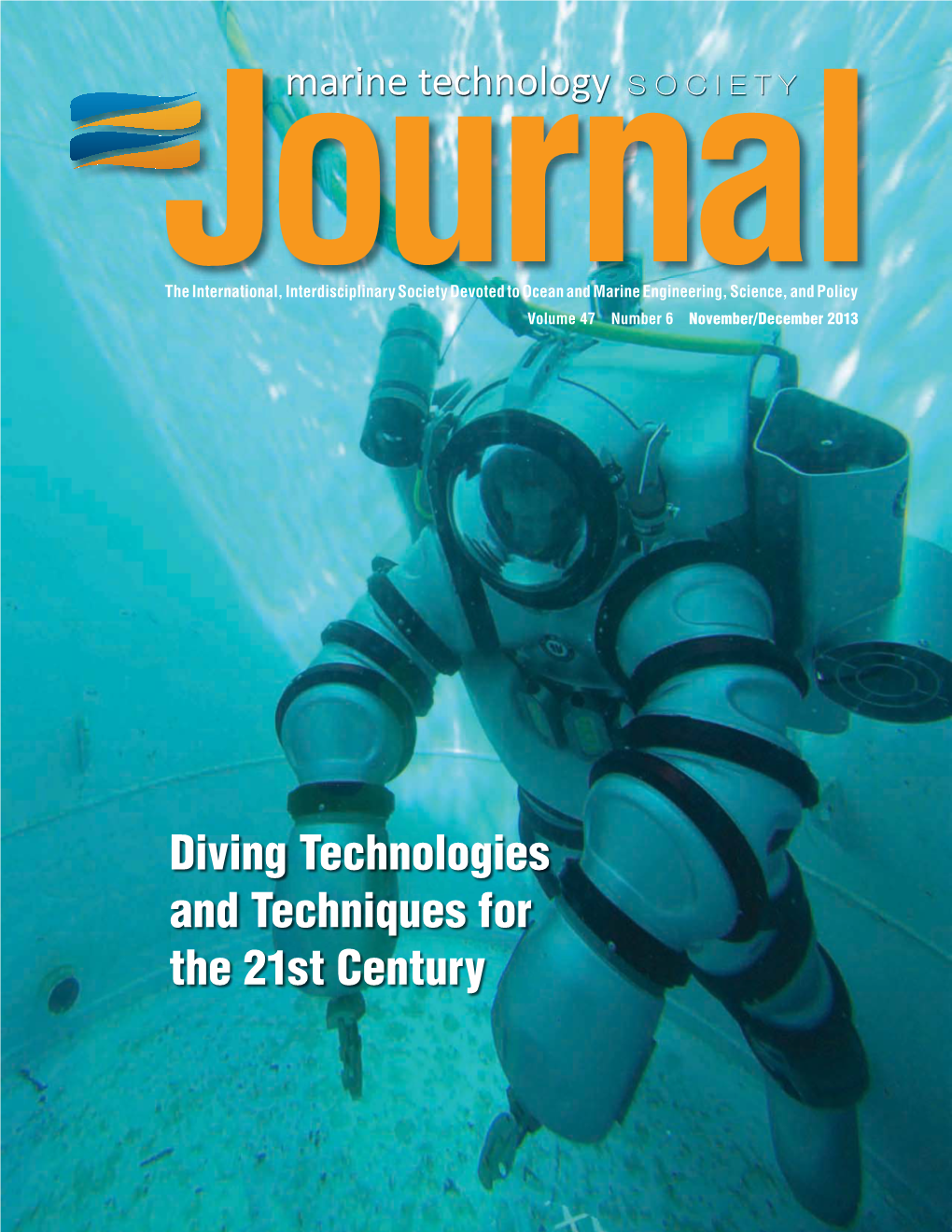
Load more
Recommended publications
-
Rebreather' Helps Navy Divers Beneath the Waves 31 May 2018, by Warren Duffie Jr
Deep breath: New 'rebreather' helps navy divers beneath the waves 31 May 2018, by Warren Duffie Jr. Panama City. The technology is sponsored by the Office of Naval Research Global (ONR Global) TechSolutions program. TechSolutions is ONR Global's rapid- response science and technology program that develops prototype technologies to address problems voiced by Sailors and Marines, usually within 12 months. "This rebreather system is an awesome opportunity to enhance the capabilities of Navy divers and accelerate their deployments," said ONR Command Master Chief Matt Matteson, who heads up TechSolutions. A US Navy diver gives the okay sign following his dive using the Office of Naval Research Global Navy diving missions include underwater rescues, TechSolutions-sponsored MK29 Mixed Gas Rebreather explosive ordnance disposal, ship hull system, which was developed at the Naval Surface maintenance, recovery of sunken equipment, and Warfare Center, Panama City Division. The new system salvage of vessels and aircraft. will conserve helium, which is a valuable natural resource, accelerate the deployment of Navy divers, and increase safety. Credit: U.S. Navy photo by John F. Beneath the waves, Navy divers breathe a careful Williams/Released mixture of oxygen and nitrogen. Below 150 feet, however, nitrogen becomes toxic—leading to nitrogen narcosis, a drowsy state that can dull mental sharpness severely and jeopardize safe The muscular U.S. Navy diver hoisted a 60-pound return to the surface. life-support regulator onto his back, then donned a 30-pound metal helmet. The solution is to replace nitrogen with helium. However, helium is expensive and hard to obtain Fellow divers connected his diving suit to an because of recent worldwide shortages. -
How to Make Solo Rebreather Diving Safer
technical So,what’s Say that you dive on your own with wrong about a rebreather and wait for the reactions. matters bringing a Rubiks cube You’ll hear some nasty comments about along on a dive? you being an accident waiting to happen Discussions about diving never did a solo dive. The other 92 percent have done at least a few Column by are very often boring— solo dives, with 33 percent doing Cedric Verdier always the same stories mostly solo diving. about numerous sharks Of course, a poll only represents dangerously close, strong the opinion of a few individuals current ripping a mask off who want to answer the questions. It cannot be considered as the “big or friendly dolphins play- picture” of the entire rebreather ing during a deco stop. diver community. Nevertheless, it We heard them so many shows that some rebreather divers times. keep on diving solo, even if the perceived risk is so high… So, if you want to have some Why people don’t dive fun, simply say that you dive on solo with a rebreather? your own with a rebreather and Simply because that’s one wait for the reactions. You’ll hear of the most basic rules some nasty comments about one learns during the you being an accident waiting Open Water Diver to happen, and some people course: “Never dive will clearly show you their option alone”. It’s so famous about your mental health. that it’s almost a dogma. And it sounds Why? Because everybody so logical? knows that CCR Solo diving is the most stupid thing to do on Earth 1. -
Anastasi 2032
Shashwat Goel & Ankita Phulia Anastasi 2032 Table of Contents Section Page Number 0 Introduction 2 1 Basic Requirements 4 2 Structural Design 15 3 Operations 31 4 Human Factors 54 5 Business 65 6 Bibliography 80 Fletchel Constructors 1 Shashwat Goel & Ankita Phulia Anastasi 2032 0 Introduction What is an underwater base doing in a space settlement design competition? Today, large-scale space habitation, and the opportunity to take advantage of the vast resources and possibilities of outer space, remains more in the realm of speculation than reality. We have experienced fifteen years of continuous space habitation and construction, with another seven years scheduled. Yet we have still not been able to take major steps towards commercial and industrial space development, which is usually the most-cited reason for establishing orbital colonies. This is mainly due to the prohibitively high cost, even today. In this situation, we cannot easily afford the luxury of testing how such systems could eventually work in space. This leaves us looking for analogous situations. While some scientists have sought this in the mountains of Hawaii, this does not tell the full story. We are unable to properly fathom or test how a large-scale industrial and tourism operation, as it is expected will eventually exist on-orbit, on Earth. This led us to the idea of building an oceanic base. The ocean is, in many ways, similar to free space. Large swathes of it remain unexplored. There are unrealised commercial opportunities. There are hostile yet exciting environments. Creating basic life support and pressure-containing structures are challenging. -
Notes on Diving in Ancient Egypt
A Brief History of Underwater Enterprise and Exploration The incentives to risk one’s life underwater from the earliest records of diving: 1) Subsistence and general aquatic harvest 2) Commerce/salvage 3) Warfare A sponge diver about to take the plunge, Classical Greece ca. 500 BCE The beginnings: subsistence in Ancient Egypt: skin divers netting fish in the Nile th Tomb of Djar, 11 Dynasty (ca. 2000 BCE) ‘Pull out well! (It is) a Happy day! Measure you, measure you, for you, good great fishes’ Text and image from the tomb of Ankhtifi (ca. 2100 BCE) The beginnings: other kinds of aquatic/underwater harvest: mother of pearl (left) and sponge diving (right) Mesopotamia (southern Iraq, ca. 2500 BCE) Classical Greece (ca. 500 BCE) The so-called ‘Standard of Ur’: a mosaic of lapis lazuli A sponge diver about to take the (from the exotic region of Afghanistan) and mother of plunge with a knife and a sack, the pearl (from the exotic source of a seabed), deposited in jar was also deposited in an elite tomb an elite tomb in Mesopotamia The beginnings: in search of exotic and high value things (things difficult to access/procure) Epic of Gilgamesh (composed in Mesopotamia no later than ca. 2100 BCE) records a heroic dive after a ‘plant of immortality’ on the seabed ‘He tied heavy stones *to his feet+ They pulled him down into the deep [and he saw the plant] He took the plant though it pricked his hands He cut the heavy stones from his feet The sea cast him up upon the shore’ The value of mother of pearl and sea sponge resides, in part, in the process of procuring them The beginnings: salvaging lost cargoes (lost valuable things) Scyllias and his daughter Hydna: the first professional divers known by name, famed for salvaging huge volumes of gold and silver (tribute and booty) from a Persian fleet in the Aegean that lost many ships in a storm (ca. -
History of Scuba Diving About 500 BC: (Informa on Originally From
History of Scuba Diving nature", that would have taken advantage of this technique to sink ships and even commit murders. Some drawings, however, showed different kinds of snorkels and an air tank (to be carried on the breast) that presumably should have no external connecons. Other drawings showed a complete immersion kit, with a plunger suit which included a sort of About 500 BC: (Informaon originally from mask with a box for air. The project was so Herodotus): During a naval campaign the detailed that it included a urine collector, too. Greek Scyllis was taken aboard ship as prisoner by the Persian King Xerxes I. When Scyllis learned that Xerxes was to aack a Greek flolla, he seized a knife and jumped overboard. The Persians could not find him in the water and presumed he had drowned. Scyllis surfaced at night and made his way among all the ships in Xerxes's fleet, cung each ship loose from its moorings; he used a hollow reed as snorkel to remain unobserved. Then he swam nine miles (15 kilometers) to rejoin the Greeks off Cape Artemisium. 15th century: Leonardo da Vinci made the first known menon of air tanks in Italy: he 1772: Sieur Freminet tried to build a scuba wrote in his Atlanc Codex (Biblioteca device out of a barrel, but died from lack of Ambrosiana, Milan) that systems were used oxygen aer 20 minutes, as he merely at that me to arficially breathe under recycled the exhaled air untreated. water, but he did not explain them in detail due to what he described as "bad human 1776: David Brushnell invented the Turtle, first submarine to aack another ship. -
DNVGL-OS-E402 Diving Systems
OFFSHORE STANDARDS DNVGL-OS-E402 Edition January 2017 Diving systems The content of this service document is the subject of intellectual property rights reserved by DNV GL AS ("DNV GL"). The user accepts that it is prohibited by anyone else but DNV GL and/or its licensees to offer and/or perform classification, certification and/or verification services, including the issuance of certificates and/or declarations of conformity, wholly or partly, on the basis of and/or pursuant to this document whether free of charge or chargeable, without DNV GL's prior written consent. DNV GL is not responsible for the consequences arising from any use of this document by others. The electronic pdf version of this document, available free of charge from http://www.dnvgl.com, is the officially binding version. DNV GL AS FOREWORD DNV GL offshore standards contain technical requirements, principles and acceptance criteria related to classification of offshore units. © DNV GL AS January 2017 Any comments may be sent by e-mail to [email protected] This service document has been prepared based on available knowledge, technology and/or information at the time of issuance of this document. The use of this document by others than DNV GL is at the user's sole risk. DNV GL does not accept any liability or responsibility for loss or damages resulting from any use of this document. CHANGES – CURRENT This document supersedes DNV-OS-E402 Offshore standard for Diving systems, October 2010 and DNV-DS- E403 Standard for Surface Diving Systems, July 2012 Changes in this document are highlighted in red colour. -
Chemical Tank Testing of Modified Commercial Diving Helmets And
CHEMICAL TANK TESTING OF MODIFIED COMMERCIAL DMNG HEL\1 ETS AND DRESS by James Nash Test Engineer Mason & Hanger-Silas Mason Co., Inc. USEPA - Oil &: Hazardous Materials Simulation Environmental Test Tank Leonardo, New Jersey On37 Contract No. 6&-3-30.56 Test Director: J. Morgan Wells, Jr., P~O. Diving Program Office National Ocearuc and Atmo.sphenc Administration Rockville, Maryland 208j2 ft, ns e•;a•ta £r! . UGID \1 Project Ofiicer Richard P. Traver, P.E. Oil and Hazardous Materials Spills Branch Municipal Environmental Research Laboratory Edison, New Jersey 08837 MUNICIPAL ENVIRONMENTAL RESEARCH LABORATORY OFACE OF RESEARCH AND DEVELOPMENT U.S. ENVIROl\'MENTAL PROTECTION AGENCY CINCINNAn, OHIO 4.5268 • DISCLAIMER This report has been reviewed by the Oil c5c Hazardous Materials Spills Branch, U.S. Environmental Protection Agency7 and approved for draft review. Approval does not signify the contents necessarily reflect the views and poUcies of the U.S. Environmental Protection Agency, nor does mention of trade names, commercial products or companies conStinne endorsement or recommendation for use. ll FOREWORD 'The U.S. Environmental Protection Agency was created because of increasing public and government concern a.boot the dangers of pollution to the health and welfare of the American people. Noxious air, foul water, and spoiled land are tragic testimonies to the deterioration of our natural environment. The complexity of that environment and the interplay of its components require a concentrated and integrat<ed attack on the problem. Research afld development is that necessary first step in problem solution; it involves def'ming the proble~ measuring its impact, and seatdilng for solutions. -
Spacesuits Have Been Created, but We Want to Go Further
Science and Innovation A Boeing/Teaching Channel Partnership EXTREME BIOSUITS Student Handbook Science and Innovation Extreme Biosuits Student Handbook Engineering Design Process Step 1 Identify the Need or Problem Describe the engineering design challenge to be solved. Include the limits and constraints, customer description, and an explanation of why solving this challenge is important. Step 2 Research Criteria and Constraints Research how others have solved this or similar problems, and discover what materials have been used. Be sure to thoroughly research the limitations and design requirements for success. Step 3 Brainstorm Possible Solutions Use your knowledge and creativity to generate as many solutions as possible. During this brainstorming stage, do not reject any ideas. Step 4 Select the Best Solution Each team member presents their solution ideas to the team. Team members annotate how each solution does or does not meet each design requirement. The team then agrees on a solution, or combination of solutions, that best meets the design requirements. Step 5 Construct a Prototype Develop an operating version of the solution. Step 6 Test Test your solution. Annotate the results from each test to share with your team. Step 7 Present Results Present the results from each test to the team. Step 8 Redesign Determine a redesign to address failure points and/or design improvements. The design process involves multiple iterations and redesigns. Redesign is based on the data from your tests, your team discussions as to the next steps to improve the design, and the engineering design process Steps 1 through 7. Once your team is confident of a prototype solution, you present the results to the client. -
Mark V Diving Helmet
Historical Diver, Number 5, 1995 Item Type monograph Publisher Historical Diving Society U.S.A. Download date 06/10/2021 19:38:35 Link to Item http://hdl.handle.net/1834/30848 IDSTORI DIVER The Offical Publication of the Historical Diving Society U.S.A. Number 5 Summer 1995 "Constant and incessant jerking and pulling on the signal line or pipe, by the Diver, signifies that he must be instantly pulled up .... " THE WORLDS FIRST DIVING MANUAL Messrs. C.A. and John Deane 1836 "c:lf[{[J a:tk o{ eadz. u.adn l;t thi:1- don't di£ wllfzoul fz.a1Jin5 Co't'towe.J, dofen, pwu!.hau:d O'l made a hefmd a{ :toorh, to gfimju.e (o'r. !JOU'tul{ thl:1 new wo'l.fJ''. 'Wifl'iam 'Bube, "'Beneath 'J,opic dlw;" 1928 HISTORICAL DIVING SOCIETY HISTORICAL DIVER MAGAZINE USA The official publication of the HDSUSA A PUBLIC BENEFIT NON-PROFIT CORPORATION HISTORICAL DIVER is published three times a year C/0 2022 CLIFF DRIVE #119 by the Historical Diving Society USA, a Non-Profit SANTA BARBARA, CALIFORNIA 93109 U.S.A. Corporation, C/0 2022 Cliff Drive #119 Santa Barbara, (805) 963-6610 California 93109 USA. Copyright© 1995 all rights re FAX (805) 962-3810 served Historical Diving Society USA Tel. (805) 963- e-mail HDSUSA@ AOL.COM 6610 Fax (805) 962-3810 EDITORS: Leslie Leaney and Andy Lentz. Advisory Board HISTORICAL DIVER is compiled by Lisa Glen Ryan, Art Bachrach, Ph.D. J. Thomas Millington, M.D. Leslie Leaney, and Andy Lentz. -
Idstorical Diver
Historical Diver, Number 3, 1994 Item Type monograph Publisher Historical Diving Society U.S.A. Download date 09/10/2021 13:15:37 Link to Item http://hdl.handle.net/1834/30846 IDSTORICAL DIVER Number 3 Summer 1994 The Official Publication of the Historical Diving Society U.S.A As you will by now know, the Society has relocated to Santa Barbara, California and this move, along with various other Society developments has delayed the publication of the Spring '94 issue of HISTORICAL DIVER. By way of catching up, we have produced a Summer double issue and have the good fortune to be able to publish with a color cover. Coinciding with the Santa Barbara relocation is the appointment, by the Board of Directors, of the first members of the HDS USA Advisory Board. This distinguished group of senior diving professionals, with extensive backgrounds in diving medicine, technical development, commercial, military and sports diving, bring in excess of 300 years of diving experience to the Society. Most of their biographies are the size of town phone directories, and have had to be severely edited for publication. We are honored and gratefulfortheir willing offers of service, and hope that we have done their biographies justice. Details start on page 4. The recently introduced, Founding Benefactor class of membership has proven to be very popular with over half of the thirty available memberships already taken. An opportunity still exists to acquire one of these unique memberships and details of it's benefits are noted on page 9. On the international front, the ongoing formation of the HDS USA as a nonprofit corporation has, by law, changed the conditions that govern our relationship with the HDS in UK. -
ATMOSPHERIC DIVING SUITS Kyznecov RR, Egorov IB
УДК 004.9 ATMOSPHERIC DIVING SUITS Kyznecov R.R., Egorov I.B., Scientific adviser: senior teacher Labusheva T.M. Siberian Federal University In our lives, information technology is found almost in everything - in smart stoves and in supercomputers. And atmospheric diving suits are not an exception. The report is dedicated to them. It will show the way they are connected to our future profession and what they can do. The most important periods of the atmospheric diving suit evolution are given below: LETHBRIDGE 1715 (UK) The first recorded attempt at protecting a diver in a rigid armor was done by John Lethbridge of Devonshire. It happened in England in 1715. The oak suit offered by him had a viewing port and holes for the diver’s arms. Water was kept out of the suit by greased leather cuffs which sealed around the operator’s arms. The device was said to have made many working dives to 60ft/18m. Lethbridge’s device probably performed as claimed. It is known from the painstaking work of Belgian expert, Robert Stenuit. Working under the protection of Comex with assistance from Comex’s founder, Henri Delauze, Stenuit imitated and operated as the "Lethbridge Engine," using only materials and techniques available in day time. JIM In 1960s an English company called DHB was interested very mush in Atmospheric Diving Suits. With the help of the government it started to perfect the Peress Tritonia suit from 1930 that it found out by coincidence and luck. After performing some tests with the old suit it became obvious that the joints had to be designed again. -
The Return of the Lama
Historical Diver, Volume 9, Issue 1 [Number 26], 2001 Item Type monograph Publisher Historical Diving Society U.S.A. Download date 09/10/2021 02:39:45 Link to Item http://hdl.handle.net/1834/30868 The Official Publication of The Historical Diving Societies of South East Asia & Pacific, Canada, Germany, Mexico and the U.S.A. Volume 9 Issue 1 Winter 2001 The Return of the Lama • Hugh Bradner's Wet Suit • Kenny Knott • Lowell Thomas Awards • • Antibes Diving History Seminar • Divair Regulator • E.R. Cross Files • • Anderson's Tales • ADCI, NOGI and DEMA Awards • Bud Swain • HISTORICAL DIVING SOCIETY USA A PUBLIC BENEFIT NONPROFIT CORPORATION 340 S KELLOGG AVE STE E, GOLETACA 93117, U.S.A. PHONE: 805-692-0072 FAX: 805-692-0042 e-mail: [email protected] or HTTP:I/www.hds.org/ ADVISORY BOARD FOUNDING BENEFACTORS Dr. Sylvia Earle Prof. Hans Hass Art Bachrach, Ph.D. Leslie Leaney Dr. Peter B. Bennett Lotte Hass Antonio Badias-Alonso Robert & Caroline Leaney Dick Bonin Dick Long Roger Bankston Andy Lentz Ernest H. Brooks II J. Thomas Millington, M.D. Ernie Brooks II A.L. "Scrap" Lundy Scott Carpenter Bob & Bill Meistrell Ken & Susan Brown Jim Mabry Wayne Brusate Andrew R. Mrozinski Jean-Michel Cousteau Bev Morgan P.K. Chandran Dr. Phil Nuytten E.R. Cross (1913-2000) Phil Nuytten Steve Chaparro Ronald E. Owen Henri Delauze Sir John Rawlins John Rice Churchill Torrance Parker Andre Galerne Andreas B. Rechnitzer, Ph.D. Raymond I. Dawson, Jr. Alese & Morton Pechter Lad Handelman Robert Stenuit Jesse & Brenda Dean Bob Ratcliffe Les Ashton Smith Diving Systems International Lee Selisky Skip & Jane Dunham Robert D.