Welding of Thermoplastic Materials Using Co2 Laser
Total Page:16
File Type:pdf, Size:1020Kb
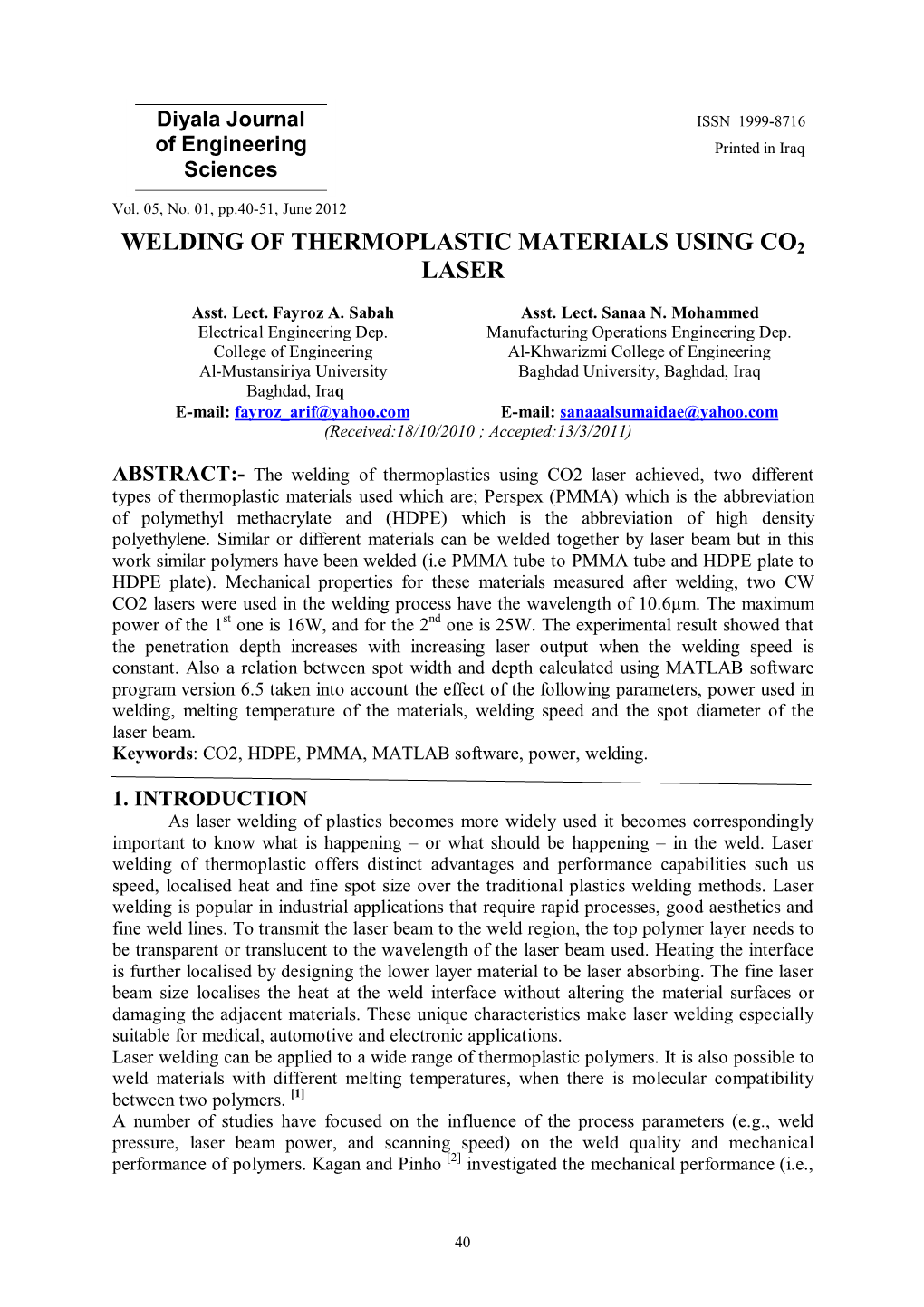
Load more
Recommended publications
-
Welding of Plastics: Fundamentals and New Developments
REVIEW ARTICLE D. Grewell*, A. Benatar Agricultural and Biosystems Eingineering, Iowa State University, Ames, IA, USA Welding of Plastics: Fundamentals and New Developments serves as the material that joins the parts and transmits the load This paper provides a general introduction to welding funda- through the joint. In welding or fusion bonding, heat is used to mentals (section 2) followed by sections on a few selected melt or soften the polymer at the interface to enable polymer welding processes that have had significant developments or intermolecular diffusion across the interface and chain entan- improvements over the last few years. The processes that are glements to give the joint strength. Each of these categories is discussed are friction welding (section 3), hot plate welding comprised of a variety of joining methods that can be used in (section 4), ultrasonic welding (section 5), laser/IR welding a wide range of applications. This paper is devoted to welding (section 6), RF welding (section 7) and hot gas/extrusion weld- processes only. Accordingly, only thermoplastics are consid- ing (section 8). ered, because thermosets cannot be welded without the addi- tion of tie-layers such as thermoplastics layers. Greater details on welding processes can be found in several monographs [1 to 4]. 1 Introduction to Joining Welding processes are often categorized and identified by the heating method that is used. All processes can be divided Despite designers’ goals of molding single component pro- into two general categories: internal heating and external heat- ducts, there are many products too complex to mold as a single ing, see Fig. -
A Review of Welding Technologies for Thermoplastic Composites in Aerospace Applications
doi: 10.5028/jatm.2012.04033912 A Review of Welding Technologies for Thermoplastic Composites in Aerospace Applications Anahi Pereira da Costa1, Edson Cocchieri Botelho1,*, Michelle Leali Costa2, Nilson Eiji Narita3, José Ricardo Tarpani4 1 Universidade Estadual Paulista Júlio de Mesquita Filho– Guaratinguetá/SP – Brazil 2 Instituto de Aeronáutica e Espaço – São José dos Campos/SP, Brazil 3 EMBRAER– São José dos Campos/SP, Brazil 4 Universidade de São Paulo – São Carlos/SP, Brazil Abstract: Reinforced thermoplastic structural detail parts and assemblies are being developed to be included in current aeronautic programs. Thermoplastic composite technology intends to achieve improved properties and low cost processes. Welding of detail parts permits to obtain assemblies with weight reduction and cost saving. Currently, joining composite materials is a matter of intense research because traditional joining technologies are not directly transfer- able to composite structures. Fusion bonding and the use of thermoplastic as hot melt adhesives offer an alternative to mechanical fastening and thermosetting adhesive bonding. Fusion bonding technology, which originated from the thermoplastic polymer industry, has gained a new interest with the introduction of thermoplastic matrix composites, which are currently regarded as candidate for primary aircraft structures. This paper reviewed the state of the art of the welding technologies devised to aerospace industry, including the ¿elds that Universidade Estadual Paulista -~lio de Mesquita Filho and -
Weldability of Linear Vibration Welded Dissimilar Amorphous Thermoplastics for Automotive External Lighting Applications
University of Windsor Scholarship at UWindsor Electronic Theses and Dissertations Theses, Dissertations, and Major Papers 10-30-2020 Weldability of Linear Vibration Welded Dissimilar Amorphous Thermoplastics for Automotive External Lighting Applications Stephen Daniel Austin Passador University of Windsor Follow this and additional works at: https://scholar.uwindsor.ca/etd Recommended Citation Passador, Stephen Daniel Austin, "Weldability of Linear Vibration Welded Dissimilar Amorphous Thermoplastics for Automotive External Lighting Applications" (2020). Electronic Theses and Dissertations. 8465. https://scholar.uwindsor.ca/etd/8465 This online database contains the full-text of PhD dissertations and Masters’ theses of University of Windsor students from 1954 forward. These documents are made available for personal study and research purposes only, in accordance with the Canadian Copyright Act and the Creative Commons license—CC BY-NC-ND (Attribution, Non-Commercial, No Derivative Works). Under this license, works must always be attributed to the copyright holder (original author), cannot be used for any commercial purposes, and may not be altered. Any other use would require the permission of the copyright holder. Students may inquire about withdrawing their dissertation and/or thesis from this database. For additional inquiries, please contact the repository administrator via email ([email protected]) or by telephone at 519-253-3000ext. 3208. Weldability of Linear Vibration Welded Dissimilar Amorphous Thermoplastics for Automotive -
Plastics and Composites Welding Handbook
CARL HANSER VERLAG David Grewell, Avraham Benatar, Joon B. Park Plastics and Composites Welding Handbook 3-446-19534-3 www.hanser.de 1.4 Goals of the Handbook 7 External heating methods rely on convection and/or conduction to heat the weld surface. These processes include: hot tool, hot gas, extrusion, implant induction, and implant resist- ance welding. Plastic and Composite Welding Processes External Internal Heating Heating Heated Tool Chapter 3 Mechanical Electromagnetic Hot Gas Ultrasonic Radio Frequency Chapter 4 Chapter 8 Chapter 11 Extrusion Vibration Infrared and Laser Chapter 5 Chapter 9 Chapter 12 Implant Induction Spin Microwave Chapter 6 Chapter 10 Chapter 13 Implant Resistance Chapter 7 Figure 1.6 Classification of plastic and composites welding processes Internal mechanical heating methods rely on the conversion of mechanical energy into heat through surface friction and intermolecular friction. These processes include: ultrasonic, vibration, and spin welding. Internal electromagnetic heating methods rely on the absorption and conversion of electro- magnetic radiation into heat. These processes include: infrared, laser, radio frequency, and microwave welding. 1.4 Goals of the Handbook This handbook was developed to provide the user with a resource for information about all welding methods. Each chapter was developed by experts in the field with a wide breadth of information dealing with all the welding aspects including materials, process phenome- nology, equipment, and joint design. The authors also included many application examples 2.4 Pressing 19 Figure 2.9 Schematic of two surfaces in contact To consider the deformation of one asperity, it is possible to expand the faying surface as shown in Fig. -
Approvals and Standards 3Rd Party Control and Standards Double Containment Piping System General Information Connection System L
Index Material Properties General properties page 103 - 107 Material Properties Specific properties page 108 - 110 Applications page 111 Pressure curves and component operating pressures page 112 - 123 Creep modulus curves page 124 - 128 Permissible buckling pressures page 129 - 132 Behaviour at abrasive fluids page 133 Chemical resistancy page 134 - 136 Installation Guidelines Transport, Handling, Storage page 137 Installation Guidelines General installation guidelines page 138 Machining page 139 Calculation Guidelines System of units page 140 SDR, Component operating pressure page 141 Operating pressure for water dangerous media page 142 Wall thickness, External pressure, necessary stiffening for page 143 - 145 pipes with buckling strain Pipe cross section, Determination of the hydraulic pressure page 146 - 149 Calculation Guidelines loss Flow Nomogramm page 150 Dog bone load page 151 Support distances, Support distance at fixed piping page 152 - 158 systems, Change in length, Minimum straight length Buried piping systems page 159 - 160 Connection Methods General standard, Application limits page 161 - 162 Connection Methods Heating element butt welding, pressure test page 163 - 173 Non-contact butt welding (IR-welding) page 174 Heating element socket welding page 175 - 178 Electrofusion welding page 179 - 184 Hot gas welding page 185 - 188 Extrusion welding page 189 - 191 Detachable joints page 192 Double Containment Piping System General Information page 193 - 194 Connection System page 195 - 197 Double Containment Piping Leakage Detection System page 198 Installation page 199 - 201 Approvals and Standards 3rd party control and standards page 202 - 203 German page 1 - 102 Approvals and Standards Material Properties General properties of PE Advantages of PE (Polyehylene) Material Properties z UV-resistance (black PE) Material Properties As a result of continuous development of PE z Flexibility molding materials, the efficiency of PE pipes and z Low specific weight of app. -
Infrared Welding
Infrared Welding Content Process description 1. Introduction 2. Process 3. Advantages of infrared heating up 4. Infrared radiator units (IR) 4.1 Short - wave radiator 4.2 Bat - wing radiator 4.3 Metal - foil radiator 5. KLN infrared welding machine technologie 5.1 Vibration welding machines with integrated pre-heating 5.1.1 The LVW Program 5.2 Hotplate welding machines - infrared machines 6. Summary KLN Ultraschall AG page 1 02/2014 Infrared Welding Process description 1. Introduction For welding by means of infrared technology short-wave (0,78-2 µm) as well as medium-wave (2-4 µm) infrared radiation of the spectrum can be used. This depends particularly on the radiation absorption capacity of the respective polymer material. The more precisely the radiator is adapted to the absorption capacity of the polymer material, the higher is the degree of efficiency, that means the conversion into warmth. Short waves are absorbed in deeper layers of the material, whereas medium waves heat it up more at the surface. Additives like carbon black lead to absorption of the largest part of energy at the surface. Since in most cases short-waves have a higher capacity (Watt/cm radiator length) and medium-wave metal-foil radiators are absorbed at the surface, the material surface can be impaired thermally. The parameters, capacity, radiation time and distance must be adjusted and optimized accordingly. The nearer the radiation source is positioned at the spot to be heated up and the better the ray is focussed, the faster the material will be heated up. 2. Process The welding process is very similar to that of hot plate welding (please see picture). -
Plastic Pipes in the Industry: the Right Choice! Legal Details / Editor
Plastic Pipes in the Industry: The right choice! Legal details / Editor: Kunststoffrohrverband e.V. Kennedyallee 1-5 53175 Bonn Germany Phone: +49-(0)2 28 / 9 14 77-0 Fax: +49-(0)2 28 / 9 14 77-19 e-mail: [email protected] Web: http://www.krv.de oder http://www.wipo.krv.de 2 Contents Introduction Page 4 General requirements for piping systems in the chemical process Page 5 industry (CPI) The chemical resistance of plastic pipes Page 6 Standardization / Quality assurance / Approval Page 7 Sustainability Page 8 Materials Page 10 Jointing techniques Page 15 Special Requirements of Plastics Page 18 Versatile piping concept Page 19 Examples of applications Page 20 Quo vadis industrial piping? Page 24 The Kunststoffrohrverband e.V. Page 25 Members of industrial pipes group Page 26 3 Einleitung Seit nunmehr 60 Jahren bestimmen Kunst- stoffe unseren Alltag. Ein modernes Auto ist ohne Kunststoff undenkbar, Verpa- ckungsfolien schützen unsere Nahrungs- mittel, Kunststoffrohre transportieren Gas und Wasser. Hochleistungsfolien versie- geln Deponien und feinste Kunststofffasern Introduction sind die Basis für moderne Sport- und During the last 60 years plastics have changed our lives High performance geomembranes secure durable sealing of Funktionskleidung. more than we could ever have imagined. A modern car con- landfills and plastic fibres represent the basis for modern structed without any plastics is unthinkable, packaging films sportswear respectively functional clothing. prevent our food from spoiling and gas as well as water are conveyed through plastic pipes. Bild: BMW Amaturentafel Bild: High Voltage Kabel Wesentliche Bedeutung haben die Kunststoffe für die chemische Industrie. Vor ca. 60Jahren wurden die ersten Kunststoffrohre in Frankfurt bei der Fa. -
INFORMATION to USERS This Manuscript Has Been Reproduced
INFORMATION TO USERS This manuscript has been reproduced from the microfilm master. UMI films the text directly from the original or copy submitted. Thus, some thesis and dissertation copies are in typewriter face, while others may be from any type of computer printer. The quality of this reproduction is dependent upon the quality of the copy submitted. Broken or indistinct print, colored or poor quality illustrations and photographs, print bleed through, substandard margins, and improper alignment can adversely affect reproduction. In the unlikely event that the author did not send UMI a complete manuscript and there are missing pages, these will be noted. Also, if unauthorized copyright material had to be removed, a note will indicate the deletion. Oversize materials (e.g., maps, drawings, charts) are reproduced by sectioning the original, beginning at the upper left-hand comer and continuing from left to right in equal sections with small overlaps. Each original is also photographed in one exposure and is included in reduced form at the back of the book. Photographs included in the original manuscript have been reproduced xerographically in this copy. Higher quality 6" x 9" black and white photographic prints are available for any photographs or illustrations appearing in this copy for an additional charge. Contact UMI directly to order. A Bell & Howell Information Company 300 North Z eeb Road. Ann Arbor. Ml 48106-1346 USA 313.'761-4700 800/521-0600 INFRARED HEATING AND WELDING OF THERMOPLASTICS AND COMPOSITES DISSERTATION Presented in Partial Fulfillment of the Requirements for the Degree Doctor of Philosophy in the Graduate School of the Ohio State University By Yang Shiau Chen, B.S., M.S. -
Bonding of Thermoplastic Material – a Literature Review
International Research Journal of Engineering and Technology (IRJET) e-ISSN: 2395-0056 Volume: 05 Issue: 05 | May-2018 www.irjet.net p-ISSN: 2395-0072 BONDING OF THERMOPLASTIC MATERIAL – A LITERATURE REVIEW Pravinkumar R. Meda1, Pritesh R Patel2 1Mechanical Department, Babaria Institute of Technology (005), Varnama-Vadodara, Gujarat, India. 2Asst. prof, Mechanical Department, Babaria Institute of Technology (005), Varnama-Vadodara, Gujarat, India. -------------------------------------------------------------------------------***--------------------------------------------------------------------------- Abstract - The paper provides a general information related to Fusion bonding or welding of Thermoplastic materials along with various processes carried out for bonding. The various welding techniques and the corresponding manufacturing methodologies, the required equipment, the effects of processing parameters on weld performance and quality, In many welding process techniques are applying we can join thermoplastics material Joining of thermoplastic composites is an important step in the manufacturing of aerospace thermoplastic composite structures. Joining of thermoplastic composites can be categorized into mechanical fastening, adhesive bonding, solvent bonding, co-consolidation, and fusion bonding or welding. Fusion bonding or welding has great potential for the joining, assembly, and repair of thermoplastic composite components. The process of fusion-bonding involves heating and melting the polymer on the bond surfaces of the components. -
And Deteriorating Environments on Polypropylene by Infrared Microscopy
QUANTIFYING THE EFFECTS OF PROCESSING AND DETERIORATING ENVIRONMENTS ON POLYPROPYLENE BY INFRARED MICROSCOPY Vom Fachbereich Chemie der Technischen Universität Darmstadt zur Erlangung des akademischen Grades eines Doctor rerum naturalium (Dr. rer. nat.) genehmigte Dissertation vorgelegt von M. Sc. Subin Damodaran aus Kerala, India Referent: Professor Dr. Matthias Rehahn Korreferent: Professor Dr. Markus Busch Tag der Einreichung: 30.03.2016 Tag der mündlichen Prüfung: 23.05.2016 Darmstadt 2016 D 17 Diese Arbeit wurde unter der Leitung von Herrn Professor Dr. Matthias Rehahn in der Zeit von Januar 2012 bis November 2014 am Fraunhofer LBF (ehemals Deutsches Kunststoff-Institut, DKI) durchgeführt. ii Publication List Journal articles 1. S. Damodaran, T. Schuster, K. Rode, A. Sanoria, R. Brüll, N. Stöhr. Measuring the orientation of chains in polypropylene welds by infrared microscopy: A tool to understand the impact of thermo-mechanical treatment and processing. Polymer (2015) 60, 125-136. 2. S. Damodaran, T. Schuster, K. Rode, A. Sanoria, R. Brüll, M. Wenzel, M. Bastian. Monitoring the effect of chlorine on the ageing of polypropylene pipes by infrared microscopy. Polym. Degrad. Stab. (2015) 111, 7-19. 3. T. Schuster, S. Damodaran, K. Rode, F. Malz, R. Brüll, B. Gerets, M. Wenzel, M. Bastian. Quantification of highly oriented nucleating agent in PP-R by IR-microscopy, polarised light microscopy, differential scanning calorimetry and nuclear magnetic resonance spectroscopy. Polymer (2014) 44, 1724-1736. 4. S. Damodaran, T. Schuster, K. Rode, A. Sanoria, R. Brüll, M. Wenzel, M. Bastian. Influence of the morphology of polypropylene on deterioration with chlorinated water. 2015 (in preparation) Poster presentations 1. Effect of Chlorinated hot water on Pipes Alpha and Beta Polypropylene. -
Forward to Better Understanding of Optical
BASF Corporation FORWARD TO BETTER UNDERSTANDING OF OPTICAL CHARACTERIZATION AND DEVELOPMENT OF COLORED POLYAMIDES FOR THE INFRA-RED/LASER WELDING: PART I – EFFICIENCY OF POLYAMIDES FOR INFRA-RED WELDING Abstract localized thermoplastic(s) melting and subsequent welding of the parts: The influence of a wide range of the infrared (IR) wavelengths (from 830 to 1,064 nm) on the optical • Non-contact laser welding (NCLW). properties of welded thermoplastics was evaluated for • Through-transmission laser welding (TTLW). unfilled, filled and reinforced polyamide 6, 66 and amorphous grades. Presented results and developed By heat generation, melt layers and inter-phase recommendations will help, designers, technologists and formation, LW methods may be classified into the materials scientists in welded parts design, materials following groups: selection and new materials development for various laser welding (LW) applications. • Scanning (moving) of the laser beam along the weld contour [1-5]; Introduction • Simultaneous heat generation by the family of laser beams, delivered by fiber-optic at the contour of the Infrared/laser through-transmission welding weld [6,9]. (TTLW) is an innovative method of joining technology for various thermoplastics. While many development and Analysis of the differences of these LW methods research programs were oriented towards optimization of is very important for clear understanding of the mechanical performance of the weld and evaluation of requirements for material(s) selection and parts design. absorption characteristics [1, 5-6], only a few studies [2-3, 7-8] concentrated on: Non-Contact Laser Welding (NCLW) • Characterization of transmittance and absorption of NCLW is typically used for joining rigid colored polymers and plastics; thermoplastics. -
Redalyc.A Review of Welding Technologies for Thermoplastic
Journal of Aerospace Technology and Management ISSN: 1984-9648 [email protected] Instituto de Aeronáutica e Espaço Brasil Pereira da Costa, Anahi; Cocchieri Botelho, Edson; Leali Costa, Michelle; Eiji Narita, Nilson; Tarpani, José Ricardo A Review of Welding Technologies for Thermoplastic Composites in Aerospace Applications Journal of Aerospace Technology and Management, vol. 4, núm. 3, julio-septiembre, 2012, pp. 255-265 Instituto de Aeronáutica e Espaço São Paulo, Brasil Available in: http://www.redalyc.org/articulo.oa?id=309426159002 How to cite Complete issue Scientific Information System More information about this article Network of Scientific Journals from Latin America, the Caribbean, Spain and Portugal Journal's homepage in redalyc.org Non-profit academic project, developed under the open access initiative doi: 10.5028/jatm.2012.04033912 A Review of Welding Technologies for Thermoplastic Composites in Aerospace Applications Anahi Pereira da Costa1, Edson Cocchieri Botelho1,*, Michelle Leali Costa2, Nilson Eiji Narita3, José Ricardo Tarpani4 1 Universidade Estadual Paulista Júlio de Mesquita Filho– Guaratinguetá/SP – Brazil 2 Instituto de Aeronáutica e Espaço – São José dos Campos/SP, Brazil 3 EMBRAER– São José dos Campos/SP, Brazil 4 Universidade de São Paulo – São Carlos/SP, Brazil Abstract: Reinforced thermoplastic structural detail parts and assemblies are being developed to be included in current aeronautic programs. Thermoplastic composite technology intends to achieve improved properties and low cost processes. Welding of detail parts permits to obtain assemblies with weight reduction and cost saving. Currently, joining composite materials is a matter of intense research because traditional joining technologies are not directly transfer- able to composite structures.