Casting Techniques of Cannonballs from the Akko 1 Shipwreck: Archaeometallurgical Investigation
Total Page:16
File Type:pdf, Size:1020Kb
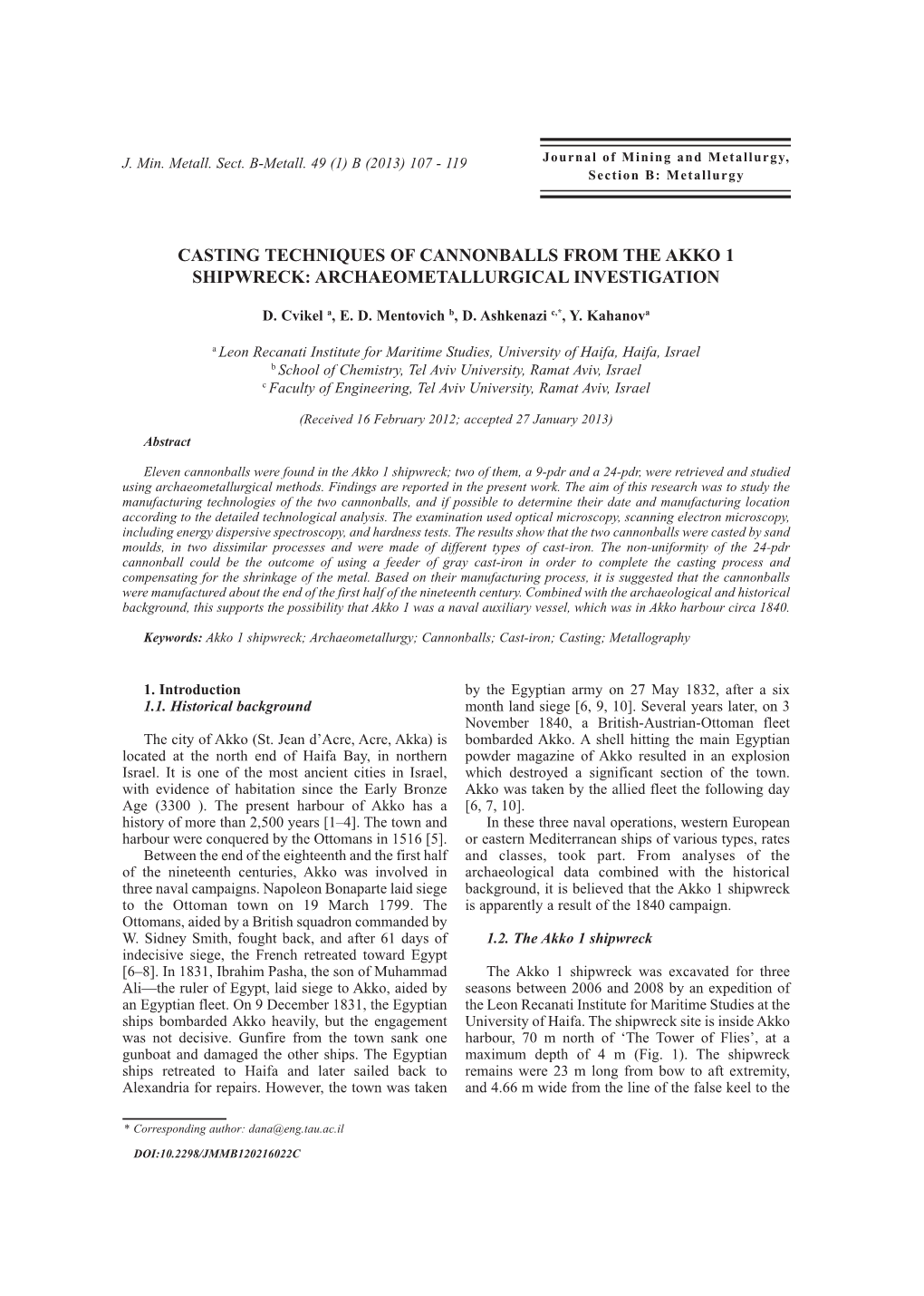
Load more
Recommended publications
-
Artillery Through the Ages, by Albert Manucy 1
Artillery Through the Ages, by Albert Manucy 1 Artillery Through the Ages, by Albert Manucy The Project Gutenberg EBook of Artillery Through the Ages, by Albert Manucy This eBook is for the use of anyone anywhere at no cost and with almost no restrictions whatsoever. You may copy it, give it away or re-use it under the terms of the Project Gutenberg License included with this eBook or online at www.gutenberg.org Title: Artillery Through the Ages A Short Illustrated History of Cannon, Emphasizing Types Used in America Author: Albert Manucy Release Date: January 30, 2007 [EBook #20483] Language: English Artillery Through the Ages, by Albert Manucy 2 Character set encoding: ISO-8859-1 *** START OF THIS PROJECT GUTENBERG EBOOK ARTILLERY THROUGH THE AGES *** Produced by Juliet Sutherland, Christine P. Travers and the Online Distributed Proofreading Team at http://www.pgdp.net ARTILLERY THROUGH THE AGES A Short Illustrated History of Cannon, Emphasizing Types Used in America UNITED STATES DEPARTMENT OF THE INTERIOR Fred A. Seaton, Secretary NATIONAL PARK SERVICE Conrad L. Wirth, Director For sale by the Superintendent of Documents U. S. Government Printing Office Washington 25, D. C. -- Price 35 cents (Cover) FRENCH 12-POUNDER FIELD GUN (1700-1750) ARTILLERY THROUGH THE AGES A Short Illustrated History of Cannon, Emphasizing Types Used in America Artillery Through the Ages, by Albert Manucy 3 by ALBERT MANUCY Historian Southeastern National Monuments Drawings by Author Technical Review by Harold L. Peterson National Park Service Interpretive Series History No. 3 UNITED STATES GOVERNMENT PRINTING OFFICE WASHINGTON: 1949 (Reprint 1956) Many of the types of cannon described in this booklet may be seen in areas of the National Park System throughout the country. -
Archeological Findings of the Battle of Apache Pass, Fort Bowie National Historic Site Non-Sensitive Version
National Park Service U.S. Department of the Interior Resource Stewardship and Science Archeological Findings of the Battle of Apache Pass, Fort Bowie National Historic Site Non-Sensitive Version Natural Resource Report NPS/FOBO/NRR—2016/1361 ON THIS PAGE Photograph (looking southeast) of Section K, Southeast First Fort Hill, where many cannonball fragments were recorded. Photograph courtesy National Park Service. ON THE COVER Top photograph, taken by William Bell, shows Apache Pass and the battle site in 1867 (courtesy of William A. Bell Photographs Collection, #10027488, History Colorado). Center photograph shows the breastworks as digitized from close range photogrammatic orthophoto (courtesy NPS SOAR Office). Lower photograph shows intact cannonball found in Section A. Photograph courtesy National Park Service. Archeological Findings of the Battle of Apache Pass, Fort Bowie National Historic Site Non-sensitive Version Natural Resource Report NPS/FOBO/NRR—2016/1361 Larry Ludwig National Park Service Fort Bowie National Historic Site 3327 Old Fort Bowie Road Bowie, AZ 85605 December 2016 U.S. Department of the Interior National Park Service Natural Resource Stewardship and Science Fort Collins, Colorado The National Park Service, Natural Resource Stewardship and Science office in Fort Collins, Colorado, publishes a range of reports that address natural resource topics. These reports are of interest and applicability to a broad audience in the National Park Service and others in natural resource management, including scientists, conservation and environmental constituencies, and the public. The Natural Resource Report Series is used to disseminate comprehensive information and analysis about natural resources and related topics concerning lands managed by the National Park Service. -
Three Rivers, the James, the Potomac, the Hudson, a Retrospect of Peace and War, by Joseph Pearson Farley
Library of Congress Three rivers, the James, the Potomac, the Hudson, a retrospect of peace and war, by Joseph Pearson Farley 4864 274 6 “ Benny Havens' Nest. West Point THREE RIVERS The James, The Potomac The Hudson A RETROSPECT OF PEACE AND WAR By JOSEPH PEARSON FARLEY, U. S. A. LC NEW YORK AND WASHINGTON THE NEALE PUBLISHING COMPANY 1910 F227 .F23 Copyright, 1910 THE NEALE PUBLISHING COMPANY LC In memory of my classmates, those who wore the blue and those who wore the gray You are doing, my friends, what your children could not do, for if you had gone to your grave cherishing the bitterness of conflict, their filial piety would have led them to cherish the same bitter and resentful feeling for generation after generation. You alone, you who fought, you who passed the weary days in the trenches, you who had the supreme exaltation of life at stake, you alone can render that supreme sacrifice to your country of a gentle and kindly spirit, receiving your former enemies to renewed friendship and binding Three rivers, the James, the Potomac, the Hudson, a retrospect of peace and war, by Joseph Pearson Farley http://www.loc.gov/ resource/lhbcb.02665 Library of Congress together all parts of the country for which you both fought.—( From Speech of Senator Elihu Root, to Federal and Confederate Veterans at Utica, N. Y. ) ILLUSTRATIONS Benny Havens' Nest—West Point Frontispiece FACING PAGE The De Russy House—Fortress Monroe 13 Brentwood—Residence First Mayor of Washington, D. C., 1818 93 West Point Light Battery—1860 108 Clearing the Road for -
Historic Firearms and Early Militaria: Day 2 November 2, 2016 — Lots 630 - 1484
Historic Firearms and Early Militaria: Day 2 November 2, 2016 — Lots 630 - 1484 Cowan’s Auctions Auction Exhibition Bid 6270 Este Avenue Lots 1 - 623 October 31, 2016 In person, by phone, absentee Cincinnati, OH 45232 November 1, 2016 12 to 5 pm or live online at bidsquare.com 513.871.1670 10 am November 1, 2016 Fax 513.871.8670 Lots 630 - 1484 8 to 10 am November 2, 2016 November 2, 2016 cowans.com 10 am 8 to 10 am Phone and Absentee Bidding 513.871.1670 or visit cowans.com Buyer’s Premium 15% Cowan's Auctions, Inc. DAY TWO - Historic Firearms and Militaria November 2, 2016 Auction begins at 10:00 AM **Please note - all lots marked with asterisks(*) require a Federal Firearms License or a Form 4473 to be completed and background check performed. Successful buyers will not be permitted to leave with the firearm without submitting a FFL or completing the Form 4473. No exceptions. Thank you for your cooperation. Lot Item Title Low Estimate High Estimate 630 Flintlock Yeager Rifle $1,000 $1,500 631 French Flintlock Trade Rifle $700 $1,000 632 Brass Fouled Anchor Flask by N.P. Ames Co $800 $1,200 633 Combination Sword And Flintlock Pistol $1,000 $1,500 634 Hand Held Flintlock Pistol $750 $1,000 635 Pair Of Iron Mounted Blunderbuss Pistols $1,000 $1,500 636 Pair Of Flintlock Blunderbuss Pistols By Alex Thompson $1,500 $2,500 637 Iron Mounted Four Shot Flintlock Pistol $1,500 $2,500 638 Flintlock Powder Tester $1,000 $1,500 639 Flintlock Powder Tester $1,000 $1,500 640 Middle-Eastern Flintlock Blunderbuss Gunbutt Pistol $750 $1,000 641 Middle-Eastern -
Deeds That Won the Empire
DEEDS THAT WON THE EMPIRE • • • II In our balls is hung Armoury of the invincible Knights of old: We must be free or die, who speak the tongue That Shakespeare spoke; the faith and morals hold Which Milton held. In everything we are sprung Of earth's first blood, have titles manifold." -WORDSWORTH. " Fair is our lot-O goodly is our heritage (Humble ye, my people, and be fearful in your mirth II, For the Lord our God Most High, He hath made the deep as dry, He hath smote for us a pathway to the ends of the earth." -KIPLING WELLI;\lGTO;\l Afl~r a .h1.illt/ttg' loy JOHN SJMPSOtf DEEDS THAT ~~1'i!. THE EMPIRE HISTORIC BATTLE SCENES BY THE REV. W. H. FITCHETT ("VEDETTE") WITH PORTRAITS AND PLANS SECOND EDITION LONDON SMITH, ELDER, & CO., IS WATERLOO PLACE 1897 \'f\VLt . l-~ c7 .7,- ~J 7 Printed by BALLANTYNB. HANSON &> Co. At the Ballantyne Pre.. PREFACE HE tales here told are written, not to glorify war, T but to nourish patriotism. They represent an effort to renew in popular memory the great traditions of the Imperial race to which we belong. The history of the Empire of which we are subjects -the story of the struggles and sufferings by which it has been built up-is the best legacy which the past has bequeathed to us. But it is a treasure strangely neglected. The State makes primary education its anxious care, yet it does not make its own history a vital part of that edu~ation. -
Manufacture and Transportation of Gunpowder In
THE MANUFACTURE AND TRANSPORTATION OF GUNPOWDER IN THE OTTOMAN EMPIRE: 1400-1800 by Cameron Rubaloff Nelson A thesis submitted to the faculty of The University of Utah in partial fulfillment of the requirements for the degree of Master of Arts in Middle East Studies/History Department of Languages and Literature The University of Utah August 2010 Copyright © Cameron Rubaloff Nelson 2010 All Rights Reserved The University of Utah Graduate School STATEMENT OF THESIS APPROVAL The thesis of Cameron Nelson has been approved by the following supervisory committee members: Peter Von Sivers , Chair 5-6-2010 Date Approved Peter Sluglett , Member 5-6-2010 bate Approved Ed Davies , Member 5-6-2010 bate Approved and by Fernando Rubio , Chair of the Department of Department of Languages and Literature and by Charles A. Wight, Dean of The Graduate School. ABSTRACT This thesis attempts to analyze the reasons for the Ottoman Empire’s successful expansion in the 1400s-1800s and its ultimate decline in the 1800s-1900s through the perspective of its national gunpowder factories and gunpowder transportation capabilities. Ultimately, all premodern firearms were only as powerful as the gunpowder they used, and a recurrent problem for all gunpowder armies was the unreliability of their powder. Such unreliability became the primary cause for the loss of a battle or an entire campaign. In comparison with their rivals to the west and to the east, the Ottomans displayed an unparalleled aptitude for the manufacture and transport of gunpowder. The abundance of natural resources, such as high quality saltpeter, sulfur, and the right kind of trees for producing charcoal, when combined with the Ottomans’ highly sophisticated state-run gunpowder works and excellent transportation network, was a major factor in their stunning successes between the 1450s and 1700s. -
National Park Service
National Park Service Manual of Instruction for the Safe Use of Reproduction Nineteenth Century Artillery in Historic Weapons Demonstrations 1 2 TABLE OF CONTENTS Page Part I: Introduction 1 Part II: Artillery Nomenclature 2 Part III: Artillery Inspection and Maintenance 8 Part IV: Artillery Drill 15 Part V: Artillery Misfires Procedures 49 Part VI: Artillery Laboratory 59 Part VII: Artillery Demonstration Critique 68 Part VIII: Artillery Competency Examination 70 Appendix A - Manual of the Piece from Instruction for Field Artillery (1860) 74 Appendix B - Commands for Battery Firing 89 Appendix C - Drill Manual for the Model 1841 Mountain Howitzer 92 Appendix D - Drill for the 30-Pounder Parrott Rifle 106 Bibliography 109 3 PART I - INTRODUCTION The four primary causes of accidents in historic weapons demonstrations using artillery are: 1. Rapid Firing 2. Poorly Maintained or Improper Equipment 3. Improper Drill 4. Improper Ammunition This manual sets forth the procedures that must be followed by persons demonstrating 19th century field artillery to the public in areas administered by the National Park Service. It also provides instruction on proper maintenance, inspection and repair procedures. This manual must be used in conjunction with Director’s Orders, DO-6, Historic Weapons Demonstration Safety Standards and the Historic Weapons Program Manual. Once an individual has completed training based on this manual. He/she will be able to perform historic weapons demonstrations that meet all NPS regulations and avoid all four of the primary causes of artillery accidents. This manual addresses basic nomenclature, equipment maintenance, ammunition manufacture, and drill. For additional interpretive information see the 19th Century Historic Weapons Reference Manual. -
Gunpowder and Ammunition, Their Origin and Progress
GUNPOWDER AND AMMUNITION THEIR ORIGIN AND PROGRESS BY LIEUT.-COLONEL HENRY W. L. HIME* * (LATE) ROYAL ARTILLERY LONGMANS, GREEN, AND CO. 39 PATERNOSTER ROW, LONDON NEW YORK AND BOMBAY 1904 All rights reserved Digitized by G o o g le Digitized by 1 1 0 8 3 8 SEP 3 0 1907 LRK ■ H 5 1 CONTENTS PART I THE ORIGIN OF GUNPOWDER CHAP. PAGB I. I ntroduction ..............................................................3 II. Sa l t p e t r e .....................................................................12 III. T he Gr e e k s ..................................................................... 29 IV. M arcus Gh s c u s ..................................................... 57 V. T he A r a b s ..................................................................... 90 VX T he H i n d u s ...................................................................105 VTI. T he C hinese................................................................... 124 VTII. F riar Baco n ................................................................... 141 PART II THE PROGRESS OF AMMUNITION IX. A nalytical T able op A mmunition • . .165 X. Hand A mmunition:— F ire-Arrows and F ire-Pikes . .168 H and G r e n a d e s ................................................. 169 XI. W ar R o c k e t s ....................................................172 XII. G unpowder . 177 Digitized by G o o g le VI CONTENTS CHAP. PAGE XIII. Shock P rojectiles:— D arts, & c..................................................................199 Round Sh o t .......................................................... 200 Case ........ 207 Sh r a p n e l .......................................................... 208 XIV. I gneous P rojectiles:— Hot Sh o t .......................................................... 217 I ncendiary F i r e b a l l s ........................................ 217 I ncendiary Sh e l l ................................................. 220 C a r c a s s e s .......................................................... 224 E xplosive F i r e b a l l s ....................................... -
The Mountain Howitzer at Big Hole National Battlefield: a Technical and Historical Report
The Mountain Howitzer at Big Hole National Battlefield: A Technical and Historical Report Mark T. Fiege Park Tech./Interp. Summer 1984 NATIONAL BA T MENLO CO HOLE 19761 NdANA THE MODEL 1841 BRONZE TWELVE POUND : MOUNTAIN HOWITZER Nineteenth century , artillery came in three types: mortars, guns, and howitzers. A mortar was fat and short--the diameter of the bore exceeded its length--and fired projectiles at high trajectories. A gun had a long, rifled barrel, and fired projectiles at high velocity and at a low, or flat, trajectory. A howitzer (from the Ge 1111 an haubitze, foLmerly haufnitze, which originated in the Czech word houfnice, or "catapult") was shorter and lighter than a gun of the same caliber, qualities which made it ideal for field and mountain use, where mobility was important. It had a smoothbore and fired shells at low velocity over a shorter range and higher trajectory than a gun, over obstacles that a gun could not reach. At the end of the bore the howitzer had a chamber of smaller diameter. (1) A howitzer was a lightpieceVhichfired- ,,arelatively large and heavy projectile. The weapon underwent less stress and a weaker recoil if the powder charge behind the projectile was made as small as possible. The chamber confined the reduced powder charge and made the gasses from the explosion at ignition more compressed and thus more efficient in propelling the projectile out of the bore--without the chamber, the howitzer would not have.ibeen as powerful. (2) In t the 1860s . mosttcannonwere:made of either iron, or in the case of mountain howitzers and other artillery, bronze. -
Historically Accurate: the Naval Gun Sights And
HISTORICALLY ACCURATE: THE NAVAL GUN SIGHTS AND PERCUSSION LOCKS RECOVERED FROM THE CONFEDERATE IRONCLAD RAM CSS GEORGIA A Thesis by MIGUEL GUTIERREZ Submitted to the Office of Graduate and Professional Studies of Texas A&M University in partial fulfillment of the requirements for the degree of MASTER OF SCIENCE Chair of Committee, Donny Hamilton Co-Chair of Committee, Kevin Crisman Committee Member, Joseph Dawson III Head of Department, Cynthia Werner August 2017 Major Subject: Maritime Archaeology and Conservation Copyright 2017 Miguel Gutierrez ABSTRACT Construction for a 19th-century Confederate ironclad ram known as CSS Georgia began in March 1862 after the Ladies Gunboat Association of Savannah, Georgia raised the necessary funds. However, Georgia never saw action and spent most of its career moored on the Savannah River. The Confederates intentionally sunk Georgia as General William T. Sherman’s troops approached Savannah in 1864 to prevent its capture by Union forces. It spent the next 150 years at the bottom of the channel. The U.S. Army Corps of Engineers Savannah District, in partnership with Panamerican Consultants, Inc., the Conservation Research Laboratory (CRL) at Texas A&M University, and the U.S. Naval History and Heritage Command, organized the recovery of thousands of artifacts and sent many of them to the CRL for subsequent conservation. This vast collection of artifacts includes a set of brass naval instruments known as gun sights. Their use enhanced the accuracy of guns during engagements at sea. Additionally, Georgia yielded brass percussion locks that facilitated the instantaneous discharge of naval guns. They represent one of the largest archaeologically recovered collections of naval gun sights and percussion locks from this era. -
The Last Smoothbores; the Development of John A. Dahlgren's
Washington Navy Yard, circa 1850. U.S. Naval Institute photo. TEE NAVAL PRACTICE BATTGRP AT TEE DRITED MATES NAVY YIIHD. WaSEIRf3'FON. 5. 0.--UIlil the smin there?.?.% rinpiu)-r%l Ilir Clr $1 War. it in ginmlral-lr Lt'i: nane Lovh r mnrr Cmlrpc~8 AT I'silht,u8; lrxi?sli!i 81 i) ~.nehcci:.~~I~~~b~lffff~~l~~ Lb* 0l1li. 14 ..-., ~8; r I ri rill $,.,I (liln, Li.r(lech olpuntm~t.P,~L,D~o$II+.~ ai~isi,,redur% tarla. Itl.~ruonlibs ~~~,ix,,,r~,,.,~~rIOraiir, nr,>ni.'r,,ril i,..:i.bL . .,, .. irl ..,I (i,,.iilrlliuircoa *r ~b*na- ,Iv,-. ~unboa~ airti, ilore urvn p Irii:uxu&ol lit. PNL~S(~C Is+~I SL ili~NYIY Yard st L-a&ustmn dluulai gudnerr ior tltk sermlr. d en1 our lupn tr Naval practice battery at the Washington Navy Yard. National Archives photo. Reprinted from the American Society of Arms Collectors Bulletin 57:12-36 Additional articles available at http://americansocietyofarmscollectors.org/resources/articles/ The Last Smoothbores The Development of John A. Dahlgren's Heavy Cast-Iron Ordnance For the United States Navy in an Era of Transition, 1848-1865 Robert J. Schneller, Jr. On his fortieth birthday, November 13, 1849, Lieu- tenant John Adolphus Bernard Dahlgren barely escaped death. He was working with a 32-pounder gun when, suddenly, it blew up. He wrote in his journal: I said, "Fire." An unusual explosion took place instantly. The battery was filled with smoke, and a great crash of timber was heard. Behind me I heard the ground ploughed up, and of the things that fell, something grazed my heels, which afterwards proved to be a part of the breeching, a piece weighing two thousand pounds. -
WEAPONRY from the MACHAULT an 18Th-Century French Frigate
WEAPONRY from the MACHAULT An 18th-century French Frigate Douglas Bryce Parks Pares Canada Canada Cover: One of the solid cast-iron 12-livre French cannonballs recovered from the wreck of the Machault. (Photo by G. Lupien.) WEAPONRY from the MACHAULT An 18th-century French Frigate Douglas Bryce Studies in Archaeology Architecture and History National Historic Parks and Sites Branch Parks Canada Environment Canada 1984 ©Minister of Supply and Services Canada 1984. Available in Canada through authorized bookstore agents and other bookstores, or by mail from the Canadian Government Publishing Centre, Supply and Services Canada, Hull, Quebec, Canada K1A 0S9. La traduction francaise s'intitule L'armement du Uachaalt, une fregate francaise du XVUfS siecle (n° de catalogue R61-2/9-20F). En vente au Canada par l'entremise de nos agents libraires agrees et autres librairies, ou par la poste au Centre d'edition du gouvernement du Canada, Approvisionnements et Services Canada, Hull, Quebec, Canada K1A 0S9. Price Canada: $5.10 Price other countries: $6.10 Price subject to change without notice. Catalogue No.: R61-2/9-20E ISBN: 0-660-11708-8 ISSN: 0821-1027 Published under the authority of the Minister of the Environment, Ottawa, 1984. Editing and design: 3ean Brathwaite The opinions expressed in this report are those of the author and not necessarily those of Environment Canada. Parks Canada publishes the results of its research in archaeology, architecture and history. A list of titles is available from Research Publications, Parks Canada, 1600 Liverpool Court, Ottawa, Ontario, K1A 1G2. Contents 5 Abstract Part Two 7 Introduction Ordnance, Ordnance Accessories and Ammunition 41 Introduction Part One 43 Guns and Carriages Small Arms 49 Ordnance Accessories 11 Introduction 51 Ammunition 13 Muskets 51 Powder 13 Fusils grenadiers 51 Projectiles 15 French Military/Marine Muskets 59 Canvas Bags 19 British Long Land Pattern Muskets 61 Conclusions 23 French Model 1733-34 Cavalry or Marine 63 Appendix A.