Efficient Hydraulic Pumps, Motors and Transformers for Hydraulic Hybrid Systems in Mobile Machinery
Total Page:16
File Type:pdf, Size:1020Kb
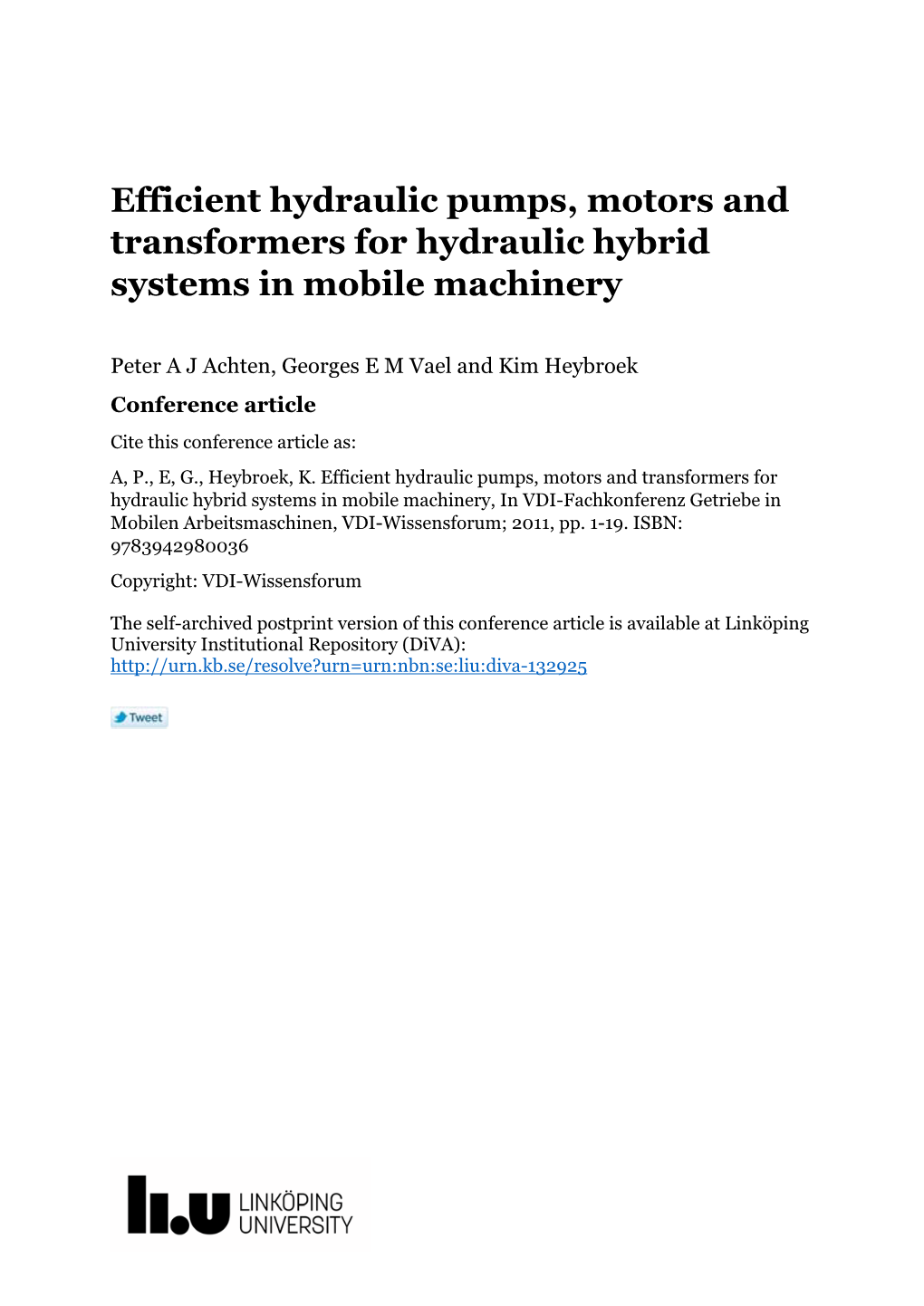
Load more
Recommended publications
-
Hydraulic Motors Catalog
HYDRAULIC MOTORS CATALOG DESIGN MANUFACTURE INTEGRATE 1 877 382-2850 EAGLE-HYDRAULIC.COM 1 OEM HYDRAULIC CYLINDERS 2 STANDARD HYDRAULIC CYLINDERS HYDRAULIC POWER UNITS -AC 3 -DC HYDRAULIC COMPONENTS -Pumps 4 -Motors 5 SYSTEM INTEGRATION 6 NEW: NOVAPEAK TABLE OF CONTENTS EBMM 4 EBMP/ EBMPH/ EBMPW/ EOZ 12 EBMR/ EBMRS/ EBMRWN/ EBMR-BK01/ EOK 39 EBMH 65 EBMSY 75 EBMT/ EBMTE/ EBMTJ/ EBMTS 99 EBMV 123 EBMK2 134 EBMK6 152 EBME2 167 EBMJ 182 EBMER-2/ EBMER-3/ EBMER-4 187 EGM02 GEARMOTOR HIGH SPEED 214 SPEED SENSOR 216 VALVES (CROSSOVER RELIEF/ SWITCH/ OVERCENTER/ COUNTERBALANCE) 217 HYDRAULIC BRAKES EBK10 / EBK2 226 LIMITED WARRANTY 238 HYDRAULIC PRODUCT SAFETY 240 FLUID POWER FORMULAS 241 COMPARISON TABLE 244 EBMM SERIES EBMM series motor is a small volume, economical type, which is designed with shaft distribution flow, which adapts the Gerotor gear set design and provides a compact volume, high power and low weight. FEATURES • Advanced manufacturing devices for the Gerotor gear set, which provide small volume, high efficiency and long life. • Shaft seal can bear high pressure and can be used in parallel or in series. • Advanced construction design, high power and low weight. • Speed sensor available on request. • Internal construction: no bearing, no bushing EBMM - Flange F - Rear Port Max. Inlet Pressure Continuous PSI (bar) 2538 (175) EBMM8-50 Intermittent PSI (bar) 3263 (225) EBMM EBMM EBMM EBMM EBMM EBMM 8 12.5 20 32 40 50 Geometric displacement in3/rev (cm3/rev.) 0.5 (8.2) 0.79 (12.9) 1.21 (19.9) 1.93 (31.6) 2.43 (39.8) 3.07 (50.3) EBMM Continuous (rpm) 1950 1550 1000 630 500 400 Max. -
A Review of Biological Fluid Power Systems and Their Potential Bionic Applications
The University of Manchester Research A review of biological fluid power systems and their potential bionic applications DOI: 10.1007/s42235-019-0031-6 Document Version Accepted author manuscript Link to publication record in Manchester Research Explorer Citation for published version (APA): Liu, C., Wang, Y., Ren, L., & Ren, L. (2019). A review of biological fluid power systems and their potential bionic applications. Journal of Bionic Engineering. https://doi.org/10.1007/s42235-019-0031-6 Published in: Journal of Bionic Engineering Citing this paper Please note that where the full-text provided on Manchester Research Explorer is the Author Accepted Manuscript or Proof version this may differ from the final Published version. If citing, it is advised that you check and use the publisher's definitive version. General rights Copyright and moral rights for the publications made accessible in the Research Explorer are retained by the authors and/or other copyright owners and it is a condition of accessing publications that users recognise and abide by the legal requirements associated with these rights. Takedown policy If you believe that this document breaches copyright please refer to the University of Manchester’s Takedown Procedures [http://man.ac.uk/04Y6Bo] or contact [email protected] providing relevant details, so we can investigate your claim. Download date:04. Oct. 2021 A review of biological fluid power systems and their potential bionic applications Chunbao Liu1,2, Yingjie Wang 1,2, Luquan Ren 2, Lei Ren2,3 1 School of Mechanical and Aerospace Engineering, Jilin University, Changchun 130022, China 2 Key Laboratory of Bionic Engineering, Ministry of Education, Jilin University, Changchun 130022, China 3 School of Mechanical, Aerospace and Civil Engineering, University of Manchester, Manchester M13 9PL, UK Abstract Nature has always inspired human achievements in industry, and biomimetics is increasingly being applied in fluid power technology. -
What Is Hydraulic and Pneumatic System
Module-01 : INTRODUCTION TO HYDRAULIC AND PNEUMATIC SYSTEMS Lecture-01 : What is Hydraulic and Pneumatic System: Fluid power systems use fluids to transmit power and motion. Both liquids and gases are called fluids. Hence both these types of fluids are used in fluid power technology. Under liquids mostly mineral oil with suitable additives are used instead of plain water - (which, however, is used also in some cases) and under gases usually atmospheric air is used after cleaning it suitably. However, synthetic fluids with additives and other gasses are also used for specific purposes, such as fire resistance or the fluid itself is the product- milk as an example. That is the state of art behind these two modern technologies of industrial oil-hydraulics and pneumatics. Fluid power technology actually has a long history behind it. From early days of civilization mankind could feel the existence of power in the water currents of rivers and streams, in ocean waves and in the flowing breeze and in the turbulent storms. Early men could even harness some of these natural sources of energy. Wind energy, for example, was utilized in sailing boats and water current to drive water wheels. Hydroelectric power generation still uses the same idea, of course now-a- days in a much more efficient way. Fluid power technology in its earliest forms mostly took advantage of the motion of fluids or scientifically speaking of its kinetic energy. But the present day oil hydraulics mostly depends on the pressure-energy of the fluids rather than its velocity and in some cases it is even called as hydrostatic transmission of power. -
Introduction to Hydraulic Actuators
Introduction to hydraulic actuators By - Kamalesh 16-11-2012 History and definition Inventor Joseph Bramah of England invented Hydraulic press and was issued a patent on this press in 1795. Pressurized hydraulic fluid used to transfer energy from flow and pressure to drive hydraulic machinery. 01 Principle of hydraulic system Pascal's law is the basis of hydraulic drive systems. 02 Basic hydraulic system Hydraulic jack 03 Hydraulic actuators 1. Hydraulic motors 2. Hydraulic cylinders 04 Hydraulic motors A hydraulic motor is a mechanical actuator that converts hydraulic pressure and flow into torque and angular displacement (rotation). 05 Hydraulic cylinders A Hydraulic cylinder (also called a linear hydraulic motor) is a mechanical actuator that is used to give a unidirectional force through a unidirectional stroke. Single acting vs. double acting 1. Single acting cylinders are economical and the simplest design. Hydraulic fluid enters through a port at one end of the cylinder, which extend the rod by means of area difference. An external force returns or gravity returns the piston rod. 2. Double acting cylinders have a port at each end, supplied with hydraulic fluid for both the retraction and extension. 06 Components of a hydraulic cylinder 1. Cylinder barrel 2. Cylinder base or cap 3. Cylinder head 4. Piston 5. Piston rod 6. Seal gland 7. Seals (nitrile rubber, Polyurethane or Fluorocarbon Viton) 07 Cylinder designs Telescopic cylinder These are multistage cylinders which can fit in the smaller dimensions of machine. Plunger cylinder An hydraulic cylinder without a piston or with a piston without seals is called a plunger cylinder. -
Electro-Hydraulic Servo System
Mechanical Engineering Department Mechatronics Engineering Program Bachelor Thesis Graduation Project Electro-Hydraulic Servo System Project Team Ashraf Issa Project Supervisor Eng. Hussein Amro Hebron- Palestine June, 2012 Palestine Polytechnic University Hebron-Palestine College of Engineering and Technology Department of Mechanical Engineering Electro-Hydraulic Servo System Project team Ashraf Issa According to the directions of the project supervisor and by the agreement of all examination committee members, this project is presented to the department of Mechanical Engineering at College of Engineering and Technology, for partial fulfillment Bachelor of engineering degree requirements. Supervisor Signature Supervisor Signature Committee Member Signature Department Head Signature II Abstract This project concerns of building an electro-hydraulic servo system model to be used in the industrial hydraulics lab to achieve the controlling of a hydraulic flow and pressure using a hydraulic servo valves, understanding the internal construction and the operational principles of servo hydraulic valves, understanding the mathematical model of a simple hydraulic system using hydraulic servo valve. The mathematical model for the built system was constructed and the simulation for linear mathematical model was done, and showed that the instability of the system and large steady state error. So indeed the system need an external controller to be designed. III Dedication To Our Beloved Palestine To my parents and family. To the souls that i love and can't see. To all my friends. To Palestine Polytechnic University. To all my teachers. May ALLAH Bless you. And for you i dedicate this project IV Acknowledgments I could not forget my family, who stood beside me, with their support, love and care for my whole life; they were with me with their bodies and souls, and helped me to accomplish this project. -
Energy Storage Techniques for Hydraulic Wind Power Systems
3rd International Conference on Renewable Energy Research and Applications Milwakuee, USA 19-22 Oct 2014 Energy Storage Techniques for Hydraulic Wind Power Systems Masoud Vaezi, Afshin Izadian, Senior Member, IEEE Energy Systems and Power Electronics Laboratory Purdue School of Engineering and Technology, IUPUI Indianapolis, IN, USA [email protected] Abstract__ Hydraulic wind power transfer systems allow transfer can be controlled by distributing the flow between the collecting of energy from multiple wind turbines into one hydraulic motors [12,13]. generation unit. They bring the advantage of eliminating the The new wind energy harvesting technique for hydraulic gearbox as a heavy and costly component. The hydraulically wind power systems should incorporate power generation connected wind turbines provide variety of energy storing equipment of individual towers in a central power generation capabilities to mitigate the intermittent nature of wind power. This paper presents an approach to make wind power become a unit. By introducing the new generation of wind turbines, more reliable source on both energy and capacity by using energy instead of utilizing the bulky electro-mechanical components, storage devices, and investigates methods for wind energy a hydraulic pump is accommodated is the wind tower. The electrical energy storage. The survey elaborates on three function of this hydraulic pump is to pressurize a fluid through different methods named “Battery-based Energy Storage”, a circuit which passes the hydraulic motor coupled with Pumped Storage Method, and “Compressed Air Energy Storage generator at ground level. This approach will provide several (CAES)”. benefits over the conventional systems such as increased life span, better reliability, and less maintenance requirement Keywords-Renewable Energy; Energy Storage; Wind Power systems; Hydraulic Transfer System. -
Hydraulic Servo Systems : Dynamic Properties and Control
Hydraulic Servo Systems Dynamic Properties and Control by Closed loop stiffness for a Karlposition-Erik servo Rydberg with velocity feedback s2 2 K h s 1 K s K K qi K 2 K vfv f sav A K FL vfv h vfv h p qi S Kvfv 1 K fv Ksav c X K V A p ce t p 2 1 s Ap 4eKce s s2 2 Steady state loop gain [1/s] 1 h s 1 2 2 Ap Kvv Kvfv h Kvfv h Kqi 1 Sc Kvv Kvfv Kvv Ksav K f K V Ap Kvfv ce 1 t s K K (without velocity feedback) K-E Rydberg 4eKce Feedbacks in Electro-Hydraulicvv v Servo Systems 7 For the same amplitude margin, Kv must have the same value in the system with and without velocity feedback. Velocity feedback increases the steady state stiffness with the factor Kvfv.FL K æ V ö ce ç1+ t s÷ Karl-Erik Rydberg, Linköping University, Sweden 2 ç 21 ÷ Ap è 4be K ce ø Threshold Saturation - . u i i imax Kqi 1 xp xp c K r v 1 1 + + sav s + s2 2d ei Ap 1+ + h s + 1 s - - n wv 2 w wh h Velocity feedback Kfv Position feedback Closed loop stiffness for a position servoK fwith velocityFigure 12: A feedbacklinear valve controlled position servo with velocity feedback Am = 6 dB If the bandwidth of the valve is relatively high and threshold and saturation is neglected With velocity feedback, K = 20 1/s, K = 9.0 the velocity feedbackvv will givevfv the effect on the hydraulic resonance frequency and damping as shown in Figure 13. -
Hydraulic Tools
R HYDRAULIC TOOLS UTILITIES NETWORK MAINTENANCE RESCUE AND CIVIL PROTECTION ROAD MAINTENANCE UNDERWATER WORKS HYDRAULIC GENERATORS AND COMPRESSORS HYDRAULIC PRODUCTS DESIGN ON CUSTOMER SPECIFICATIONS The production of DOA Srl is in constant evolution, DOA Srl reserves the right to make modifications or change configuration, characteristics and functions of products at any time without previous notice or obligations on products already sold. R INDEX POWER PACKS 6 HYDRAULIC GROUP FOR RAILROAD CAR CARRIERS 17 POWER PACK WITH REMOTE CONTROL NIGTH DEFENDER TOWER LIGHT 20 HYDROBOX 18 BREAKERS 24 HAMMER DRILL 27 DISC SAW 28 GRINDER 29 CORE DRILLS 30 VENTILATORS - ASPIRATORS 32 WATER PUMPS 38 MAGNETIC MEMBRANE 48 HYDRAULIC MOTOR FOR HOT TAPPING EQUIPMENT 50 HYDRAULIC MOTOR FOR WATER NETWORK GATES 51 PIPE COMPRESSING TOOLS 52 RECIPROCATING SAW 57 HYDRAULIC GENERATORS 58 HYDRAULIC WELDERS 61 HYDRAULIC COMPRESSORS 62 FLOW PRESSURE CONTROL VALVES 63 MAINTENANCE ACCESSORIES 64 3 R WHY HYDRAULIC TOOLS POWER & PRODUCTIVITY The power to weight ratio of hydraulic tools is unbeatable! A comparative test will immediately demonstrate this advantage that means increased productivity and less fatigue for the operators. TRANSPORTABILITY & ECONOMY The group power pack/tool is very compact and easy to transport, the fuel consumption of power packs is largely less then the one of air compressor, the power pack is lighter and can easily be transported by the smallest vehicles , can be positioned on job site occupying minimal space and without troubling operations and traffic, it does not have the typical problems associated with air compressors such as needs of bra- kes, lighting, car plates, hooks, lifting , parking etc A BETTER WAY TO WORK IN TOTAL SAFETY No other equipment either electric, gasoline, or pneumatic can solve together all the problems related to the urban maintenance of underground pipes. -
Planning and Operating Hydraulic Power Units to Provide Greater Energy Efficiency Build It In
Energy Efficiency White Paper Planning and operating hydraulic power units to provide greater energy efficiency Build it in. Potential solution for reducing energy consumption and digitalization of data for smart power management Marco Bison, Manager Mechatronic Technologies White Paper WP040005EN Effective April 2016 Introduction Reducing energy consumption is a stated objective of the Euro- pean Union. In 2007, EU Member States agreed to cut primary energy consumption by 20 per cent by 2020. Increasing energy efficiency is an important aspect in supporting this effort. This measure not only reduces energy costs, but also helps achieve a higher level of supply security and protects the climate. Every consumer sector offers considerable potential for energy savings across Europe. Industry plays a key role in this. For instance, in Germany almost 30 per cent of total final energy consumption is accounted for by the manufacturing sector1. The initiatives launched by the EU in this area also include the Ecodesign Direc- tive 2009/125/EC, which stipulates the ecodesign requirements for energy-related products. However, the motivation for companies to improve the energy ef- ficiency of their production processes should not only be driven by the need to fulfill political objectives. This is because increasing en- ergy efficiency also produces tangible cost reductions, while also boosting competitiveness and making an important contribution to protecting the environment. Using a hydraulically powered machine as an example, this white- paper will highlight how, by combining the right components, its energy efficiency can be significantly increased. Depending on the application, energy savings of up to 70 per cent can be achieved, which creates value and rapid return on investment (ROI) for the end user. -
Review of Fluid and Control Technology of Hydraulic Wind Turbines
Front. Mech. Eng. 2017, 12(3): 312–320 DOI 10.1007/s11465-017-0433-2 REVIEW ARTICLE Maolin CAI, Yixuan WANG, Zongxia JIAO, Yan SHI Review of fluid and control technology of hydraulic wind turbines © The Author(s) 2017. This article is published with open access at link.springer.com and journal.hep.com.cn Abstract This study examines the development of the the maintenance of wind turbines [12]. The research and fluid and control technology of hydraulic wind turbines. development of hydraulic wind turbines has been carried The current state of hydraulic wind turbines as a new out in many countries. technology is described, and its basic fluid model and typical control method are expounded by comparing various study results. Finally, the advantages of hydraulic 2 Development of hydraulic wind turbines wind turbines are enumerated. Hydraulic wind turbines are expected to become the main development direction of Figure 1 shows the main drive system of a typical wind turbines. hydraulic wind turbine, which mainly consists of a wind turbine, a fixed-quantity pump and variable hydraulic Keywords wind turbine, hydraulic system, fluid model, motor system, a synchronous generator, the control system control technology of the power generator. A wind turbine transforms wind energy into mechanical energy, which is in turn converted into hydraulic energy by the movement of the pump. After 1 Introduction the staircase energy is transferred, hydraulic energy is transferred to the variable motor to create mechanical Modern wind turbines typically adopt either a doubly fed energy. The variable motor drives the excited synchronous induction generator whose main drive is a step-up gearbox, generator to convert hydraulic energy into electrical or a multi-level permanent-magnet synchronous generator energy. -
Hydraulic Power Supply and Motors Concept and Theory
Hydraulic Power Supply and Motors Concept and Theory Graco, Inc. P.O. Box 1441 Minneapolis, MN 55440-1441 ©1996 Graco Inc. Form No. 321-046 1/96 Rev 2 SL Training 11/14 Hydraulic Systems Component Identification and Function A typical hydraulic fluid handling system, shown in Figure 1, is one in which the power supply, or power pack, provides hydraulic fluid at a given pressure and flow to operate differential hydraulic motors. These motors, in turn, drive fluid displacement pumps that deliver fluid at a given pressure and flow for a specific application. This module will discuss in detail only these parts of the hydraulic system - the hydraulic power supply and differential hydraulic motors. Fluid displacement pumps and application equipment are covered in other training modules. Hydraulic motor Application tool Fluid Power displacement supply pump 05867 Figure 1 Hydraulic Fluid Handling System Figure 2 shows the basic components of a hydraulic power supply. Their functions are: The reservoir stores and cools hydraulic oil and provides the mounting surface for other power supply components. It contains: Clean-out doors and a fluid drain port that are used for cleaning and maintenance. A filler breather port/cap that is used to fill the reservoir for with oil. The reservoir must breathe to atmosphere for proper operation. A low level/high temperature sensor that detects a low hydraulic oil level in the reservoir or a high oil temperature condition. A hydraulic oil level/temperature indicator that provides a visual check for oil level and temperature during operation. The hydraulic pump provides hydraulic oil to all hydraulic motors in the system. -
Hydropower Hydraulic System
+91-8048588602 Hydropower Hydraulic System https://www.indiamart.com/hydropowerhydraulicsystem/ Incepted in the year 1990, Hydro Power Hydraulic System commenced its operation as a reliable and competent Wholesale Trader of Hydraulic Vane Pump, Hydraulic Piston Pumps, Hydraulic Accumulator, etc. About Us Incepted in the year 1990, Hydro Power Hydraulic System commenced its operation as a reliable and competent Wholesale Trader of Hydraulic Vane Pump, Hydraulic Piston Pumps, Hydraulic Accumulator, etc. Along with this we are also Service Provider of AMC Service and Pump Repairing Services. Offered range of products is widely used and demanded across many industries. We provide these products to make our clients competent in the market place. Our culture is derived by growth of our products and customer base while making client satisfied with the quality and solutions we offer. Based on our focused endeavors and product innovation, we have been admired by our clients. Today, our organization is providing one stop shop for all relevant needs. Furthermore, state-of-the-art infrastructure, advance technology and quality material give our engineers means to design and produce offered range of products. Our produce is subjected to rigorous quality testing to ensure their high performance and quality which customers want. Our skilled professionals are expert in giving ideal product solution to the client according to their need and budget. With the help of strong distribution network, we are successful in delivering our products on time. Our