Investigation on Electromagnetic Launching for Single Stage Coilgun Hany M
Total Page:16
File Type:pdf, Size:1020Kb
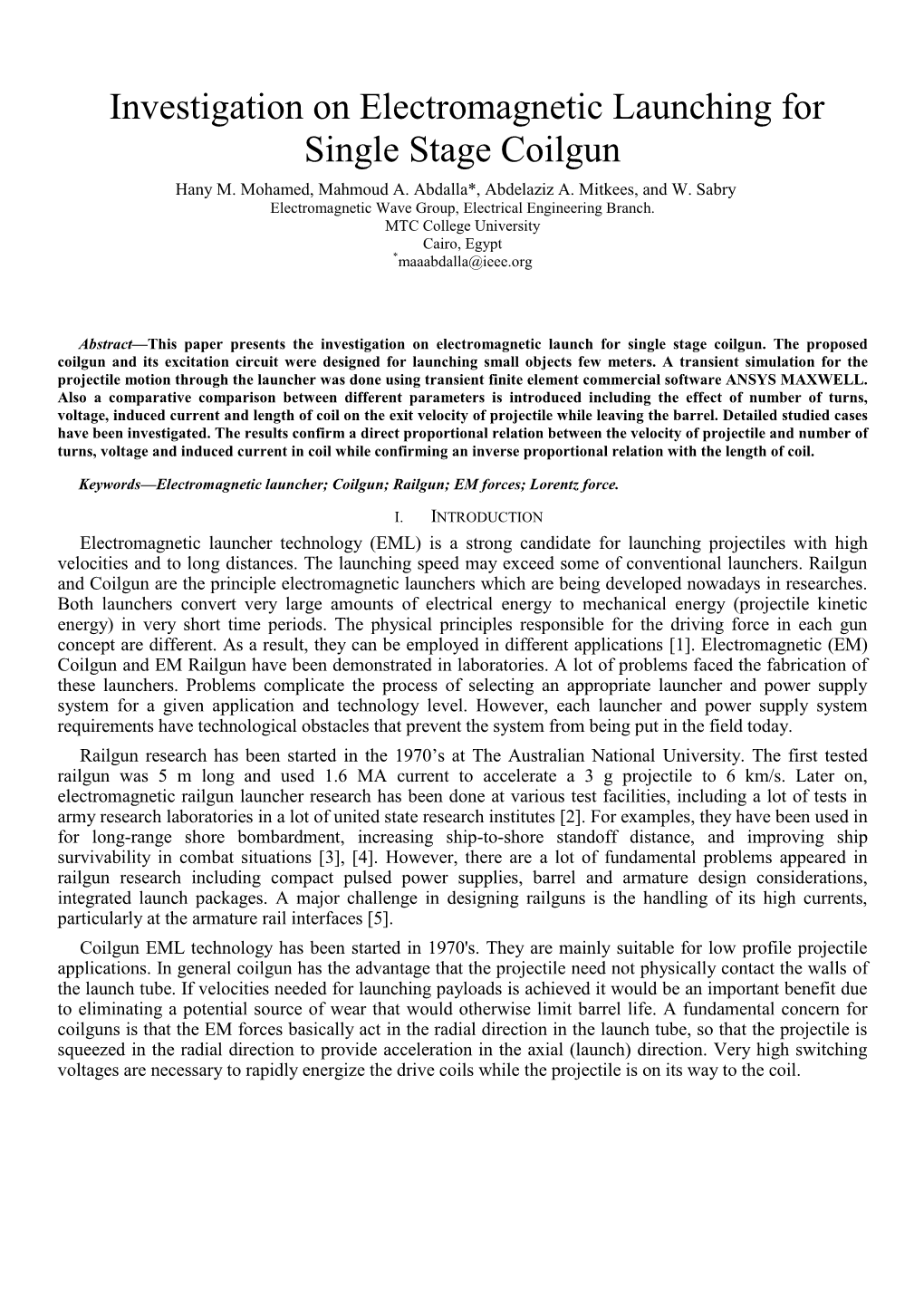
Load more
Recommended publications
-
Overlapped Electromagnetic Coilgun for Low Speed Projectiles
ISSN (Print) 1226-1750 ISSN (Online) 2233-6656 Journal of Magnetics 20(3), 322-329 (2015) http://dx.doi.org/10.4283/JMAG.2015.20.3.322 Overlapped Electromagnetic Coilgun for Low Speed Projectiles Hany M. Mohamed1, Mahmoud A. Abdalla2*, Abdelazez Mitkees, and Waheed Sabery Electrical Engineering Branch, MTC College, Cairo, Egypt [email protected] [email protected] (Received 20 February 2015, Received in final form 16 June 2015, Accepted 16 June 2015) This paper presents a new overlapped coilgun configuration to launch medium weight projectiles. The proposed configuration consists of a two-stage coilgun with overlapped coil covers with spacing between them. The theoretical operation of a multi-stage coilgun is introduced, and a transient simulation was conducted for projectile motion through the launcher by using a commercial transient finite element software, ANSOFT MAXWELL. The excitation circuit design for each coilgun is reported, and the results indicate that the overlapped configuration increased the exit velocity relative to a non-overlapped configuration. Different configurations in terms of the optimum length and switching time were attempted for the proposed structure, and all of these cases exhibited an increase in the exit velocity. The exit velocity tends to increase by 27.2% relative to that of a non-overlapped coilgun of the same length. Keywords : electromagnetic launch, excitation circuit, lorentz force, overlapped coilgun 1. Introduction is not easy to obtain the main performance parameters and optimize the design [3]. Electromagnetic (EM) launch technology is a strong Sandia National Laboratories has succeeded in coilgun candidate to launch objects with high velocities over long design and operations by developing four guns with distances. -
Axial-Flux Permanent-Magnet Dual-Rotor Generator for a Counter-Rotating Wind Turbine
energies Article Axial-Flux Permanent-Magnet Dual-Rotor Generator for a Counter-Rotating Wind Turbine Filip Kutt *,† , Krzysztof Blecharz † and Dariusz Karkosi ´nski † Faculty of Electrical and Control Engineering, Gda´nskUniversity of Technology, 80-233 Gda´nsk,Poland; [email protected] (K.B.); [email protected] (D.K.) * Correspondence: fi[email protected]; Tel.: +48-58-347-19-39 † These authors contributed equally to this work. Received: 31 March 2020; Accepted: 26 May 2020; Published: 2 June 2020 Abstract: Coaxial counter-rotating propellers have been widely applied in ships and helicopters for improving the propulsion efficiency and offsetting system reactive torques. Lately, the counter-rotating concept has been introduced into the wind turbine design. Distributed wind power generation systems often require a novel approach in generator design. In this paper, prototype development of axial-flux generator with a counter-rotating field and armature is presented. The design process was composed of three main steps: analytical calculation, FEM simulation and prototype experimental measurements. The key aspect in the prototype development was the mechanical construction of two rotating components of the generator. Sturdy construction was achieved using two points of contact between both rotors via the placement of the bearing between the inner and outer rotor. The experimental analysis of the prototype generator has been conducted in the laboratory at the dynamometer test stand equipped with a torque sensor. The general premise for the development of such a machine was an investigation into the possibility of developing a dual rotor wind turbine. The proposed solution had to meet certain criteria such as relatively simple construction of the generator and the direct coupling between the generator and the wind turbines. -
Electromagnetic Flyer Plate Technology and Development of a Novel Current Distribution Sensor
Electromagnetic Flyer Plate Technology and Development of a Novel Current Distribution Sensor A doctoral thesis by Kaashif A. M. Omar (MPhys. Physics with Astrophysics, University of Leicester, 2007) Submitted in partial fulfilment of the requirements for the award of the degree of Doctor of Philosophy of Loughborough University November 2014 To the School of Electronic, Electrical and Systems Engineering, Loughborough University, Loughborough, UK © British Crown Owned Copyright 2014/AWE Acknowledgements With the grace and blessing of Allah (SWT), I have been able to complete this work, and I hope to continue in the pursuit of knowledge as is commanded by him… Completing this research project and writing up this thesis has been full of ups and downs and it has been a very long journey, I can vaguely recall a young(er) single scientist who began this work not knowing where it would lead to; now, I am happily married to my wife Humna, having just celebrated our first wedding anniversary, and about to start the next big chapter in my life, which is to become a father… On that note I would like to take this opportunity to firstly thank my father, Mr Abdul Majid Omar and my mother, Mrs Shenaz A M Omar; who have always encouraged me to push myself and instilled within me the confidence that I can achieve anything I put my mind to. Without their constant support I would never have even been able to complete my first degree In physics with Astrophysics at Leicester University, let alone have the opportunity to complete a PhD. -
2016-09-27-2-Generator-Basics
Generator Basics Basic Power Generation • Generator Arrangement • Main Components • Circuit – Generator with a PMG – Generator without a PMG – Brush type –AREP •PMG Rotor • Exciter Stator • Exciter Rotor • Main Rotor • Main Stator • Laminations • VPI Generator Arrangement • Most modern, larger generators have a stationary armature (stator) with a rotating current-carrying conductor (rotor or revolving field). Armature coils Revolving field coils Main Electrical Components: Cutaway Main Electrical Components: Diagram Circuit: Generator with a PMG • As the PMG rotor rotates, it produces AC voltage in the PMG stator. • The regulator rectifies this voltage and applies DC to the exciter stator. • A three-phase AC voltage appears at the exciter rotor and is in turn rectified by the rotating rectifiers. • The DC voltage appears in the main revolving field and induces a higher AC voltage in the main stator. • This voltage is sensed by the regulator, compared to a reference level, and output voltage is adjusted accordingly. Circuit: Generator without a PMG • As the revolving field rotates, residual magnetism in it produces a small ac voltage in the main stator. • The regulator rectifies this voltage and applies dc to the exciter stator. • A three-phase AC voltage appears at the exciter rotor and is in turn rectified by the rotating rectifiers. • The magnetic field from the rotor induces a higher voltage in the main stator. • This voltage is sensed by the regulator, compared to a reference level, and output voltage is adjusted accordingly. Circuit: Brush Type (Static) • DC voltage is fed External Stator (armature) directly to the main Source revolving field through slip rings. -
Electromagnetic Launcher: Review of Various Structures
Published by : International Journal of Engineering Research & Technology (IJERT) http://www.ijert.org ISSN: 2278-0181 Vol. 9 Issue 09, September-2020 Electromagnetic Launcher : Review of Various Structures Siddhi Santosh Reelkar Prof. Dr. U. V. Patil Department of Electrical Engineering, Department of Electrical Engineering, Government College of Engineering, Government College of Engineering, Karad Karad Prof. Dr. V. V. Khatavkar Department of Electrical Engineering, P.E.S. Modern college of Engineering, Pune Hrishikesh Mehta Utkarsh Alset Aethertec Innovative Solutions, Aethertec Innovative Solutions, Bavdhan, Pune Bavdhan, Pune Abstract— A theoretic review of electromagnetic coil-gun This paper is mainly focusing the basic principle of launcher and its types are illustrated in this paper. In recent electromagnetic coil-gun launcher, inductance and resistance years conventional launchers like steam launchers, chemical calculations, construction and modeling concept of different launchers are replaced by electromagnetic launchers with coil-gun launcher. auxiliary benefits. The electromagnetic launchers like rail- gun and coil-gun elevated with multi pole field structure delivers II. WORKING PRINCIPLE great muzzle velocity and huge repulse force in limited time. Rail gun has two parallel rails from which object is launched. Various types of coil-gun electromagnetic launchers are When current passes through the rails to the object it compared in this paper for its structures and characteristics. The paper focuses on the basic formulae for calculating the produces arc. Because of high current pulse it has more values of inductance and resistance of electromagnetic contact friction losses [4]. Compare to the rail-gun launcher, launchers. Coil-gun launchers have no contact friction losses as there is no electrical contact between coils and object. -
Unit VI Superconductivity JIT Nashik Contents
Unit VI Superconductivity JIT Nashik Contents 1 Superconductivity 1 1.1 Classification ............................................. 1 1.2 Elementary properties of superconductors ............................... 2 1.2.1 Zero electrical DC resistance ................................. 2 1.2.2 Superconducting phase transition ............................... 3 1.2.3 Meissner effect ........................................ 3 1.2.4 London moment ....................................... 4 1.3 History of superconductivity ...................................... 4 1.3.1 London theory ........................................ 5 1.3.2 Conventional theories (1950s) ................................ 5 1.3.3 Further history ........................................ 5 1.4 High-temperature superconductivity .................................. 6 1.5 Applications .............................................. 6 1.6 Nobel Prizes for superconductivity .................................. 7 1.7 See also ................................................ 7 1.8 References ............................................... 8 1.9 Further reading ............................................ 10 1.10 External links ............................................. 10 2 Meissner effect 11 2.1 Explanation .............................................. 11 2.2 Perfect diamagnetism ......................................... 12 2.3 Consequences ............................................. 12 2.4 Paradigm for the Higgs mechanism .................................. 12 2.5 See also ............................................... -
Modelling and Optimisation of a Robocup MSL Coilgun
Modelling and Optimisation of a RoboCup MSL coilgun V. Gies, T. Soriano, C. Albert, and N. Prouteau Universit´ede Toulon, Avenue de l'Universit´e,83130 La Garde, France [email protected] Home page : http://rct.univ-tln.fr Abstract. This paper focuses on the modelling and optimization of a RoboCup Middle Size League (MSL) coil-gun. A mechatronic model coupling electrical, mechanical and electromagnetic models is proposed. This model is used for optimizing an indirect coil-gun used on limited size robots at the RoboCup for kicking real soccer balls. Applied to a well defined existing coil gun [6], we show that optimizing the initial position of the plunger and the length of a plunger extension leads to increase the ball speed by 30% compared to the results presented in a previous study. Keywords: Coil Gun, Electro Magnetic Launcher, Mechatronics, Modelling, RoboCup 1 Introduction An electromagnetic launcher (EML) is a system using electricity for propelling a projectile [5]. A coil gun is a type of EML, having only the ability to launch magnetic objects (such as iron rods) by converting electrical energy into kinetic energy using a coil [1]. Launching non-magnetic objects cannot be done directly using coil guns because they are not affected by magnetic field but can be done using an "indirect coil gun", having a magnetic plunger accelerated by a coil, propelling an non-magnetic object by continuous contact or elastic shock. Both these propelling techniques can be combined in a multi-phase EML. Optimization of this type of launcher is the purpose of this work. -
Why the Exlar T-LAM™ Servo Motors Have Become the New Standard of Comparison for Maximum Torque Density and Power Efficiency
Why the Exlar T-LAM™ Servo Motors have Become the New Standard of Comparison for Maximum Torque Density and Power Efficiency By Richard Welch Jr. - Consulting Engineer November 3, 2008 Introduction According to the U.S. Department of Energy (DOE) 63-65% of a typical manufacturing plant’s monthly electric bill goes to pay for all the electricity consumed by the electric motors operating in the plant. Hence, with a steady rise in electricity cost along with constant pressure to lower manufacturing cost, if you ask plant managers to describe the three most important words associated with electric motors they quickly respond by saying its “efficiency”, “efficiency” and “efficiency”. As you can see, no matter how you arrange these three words “efficiency” is always at the top of your list. Furthermore, systems and design engineers who build equipment used in manufacturing plants constantly search for electric motors that provide the “most bang for least buck”. Therefore, producing electric motors that have the highest obtainable torque density (i.e., continuous torque output per motor volume) along with maximum power efficiency has become a real challenge for all motor manufacturers. To meet this challenge for both high torque density and maximum power efficiency, Exlar has developed its T-LAM™ stator that’s now being used in all SLM and SLG brushless DC servo motors and in all GSX and GSM rotary actuators [1]. Hence, the focus of this paper is to show you graphically why the T-LAM servo motor has become the new standard of comparison for torque density and power efficiency. -
Electromagnetic Coil Gun Launcher System
ISSN(Online): 2319-8753 ISSN (Print) : 2347-6710 International Journal of Innovative Research in Science, Engineering and Technology (A High Impact Factor, Monthly, Peer Reviewed Journal) Visit: www.ijirset.com Vol. 8, Issue 3, March 2019 Electromagnetic Coil Gun Launcher System Prof. Yogesh Fatangde1 Swapnil Biradar2, Aniket Bahmne3, Suraj Yadav4, Ajay Yadav5 Department of Mechanical Engineering, RMD Sinhgad Technical Campus, Savitribai Phule Pune University, Pune, Maharashtra, India1 ABSTRACT: In our present time, a study was undertaken to determine if ground based electromagnetic acceleration system could provide a useful reduction in launching cost with current large chemical boosters, while increasing launch safety and reliability. An electromagnetic launcher (EML) system accelerates and launches a projectile by converting electric energy into kinetic energy. An EML system launches projectile by converting electric energy into kinetic energy. There are two types of EML system under development: rail gun and coil gun. A coil gun launches the projectile by magnetic force of electromagnetic coil. A higher velocity needs multiple stages of system, which make coil gun EML system longer. As a result installation cost is very high and it required large installation site for EML. So, we present coil gun EML system with new structure and arrangement for multiple electromagnetic coils to reduce the length of system KEYWORDS: EML, coil gun, Electromagnetic launcher, suck back effect I. INTRODUCTION In chemical launcher systems such as firearms and satellite launchers, chemical explosive energy is converted into mechanical dynamic energy. The system must be redesigned and remanufactured if the target velocity of the projectile is changed. In addition, such systems are not eco-friendly. -
ON Semiconductor Is
ON Semiconductor Is Now To learn more about onsemi™, please visit our website at www.onsemi.com onsemi and and other names, marks, and brands are registered and/or common law trademarks of Semiconductor Components Industries, LLC dba “onsemi” or its affiliates and/or subsidiaries in the United States and/or other countries. onsemi owns the rights to a number of patents, trademarks, copyrights, trade secrets, and other intellectual property. A listing of onsemi product/patent coverage may be accessed at www.onsemi.com/site/pdf/Patent-Marking.pdf. onsemi reserves the right to make changes at any time to any products or information herein, without notice. The information herein is provided “as-is” and onsemi makes no warranty, representation or guarantee regarding the accuracy of the information, product features, availability, functionality, or suitability of its products for any particular purpose, nor does onsemi assume any liability arising out of the application or use of any product or circuit, and specifically disclaims any and all liability, including without limitation special, consequential or incidental damages. Buyer is responsible for its products and applications using onsemi products, including compliance with all laws, regulations and safety requirements or standards, regardless of any support or applications information provided by onsemi. “Typical” parameters which may be provided in onsemi data sheets and/ or specifications can and do vary in different applications and actual performance may vary over time. All operating parameters, including “Typicals” must be validated for each customer application by customer’s technical experts. onsemi does not convey any license under any of its intellectual property rights nor the rights of others. -
Tradeoff Between Efficiency and Melting for a High
1 Tradeoff between Efficiency and Melting for a High-Performance Electromagnetic Rail Gun William C. McCorkle and Thomas B. Bahder Army Aviation and Missile Research, Development, and Engineering Center, Redstone Arsenal, AL 35898 USA Email: [email protected] Abstract— We estimate the temperature distribution in the and the historical lack of understanding of the reasons for the rails of an electromagnetic rail gun (EMG) due to the confinement low endurance of the gun rails in service, sometimes limited to of the current in a narrow surface layer resulting from the skin one shot at maximum energies before replacement is needed. effect. In order to obtain analytic results, we assume a simple geometry for the rails, an electromagnetic skin effect boundary For high-performance EMGs, in order to increase the arma- edge that propagates with the accelerating armature, and a ture velocity while keeping the length of the rails fixed, the current carrying channel controlled by magnetic field diffusion current pulse during firing must be shorter and have a higher into the rails. We compute the temperature distribution in the average amplitude, causing a stronger skin effect in the rails, rails at the time that the armature leaves the rails. For the range which leads to an increase in Joule heating of the rails. In this of exit velocities, from 1500 m/s to 5000 m/s, we find the highest temperatures are near the gun breech. After a single gun firing, paper, we show that the EMG efficiency is higher at higher the temperature reaches the melting temperature of the metal velocity, but there is increased melting of the rails, leading to rails in a layer of finite thickness near the surface of the rails, a tradeoff between efficiency of the EMG and melting of the for rails made of copper or tantalum. -
Compulsator Design for Electromagnetic Railgun System
COMPULSATOR DESIGN FOR ELECTROMAGNETIC RAILGUN SYSTEM By Bryan Bennett Senior Project Electrical Engineering Department Cal Poly State University, San Luis Obispo June, 2012 ABSTRACT This project designed, fabricated, and partially tested a compensated pulsed alternator (compulsator) to power an electromagnetic rail gun (EMRG) in a multidisciplinary team. The EMRG team includes two master’s AERO students, two senior EE students, and three senior ME students. Design of the compulsator began with research through conference and research papers. This design was changed throughout the project as system analysis and component testing exposed unforeseen system limitations. While original specifications were not met, all fabricated components but one, the stator, were completed using Cal Poly’s facilities and the project’s limited available budget. Experimental verification of calculations and system modeling were not obtained because the compulsator was fully assembled at the time of this writing, but the necessary measurements and testing procedures have been outlined. i TABLE OF CONTENTS Abstract……………………………………………………………………………………………i Table of Contents…………………………………………………………………………………ii List of Figures…………………………………………………………………………………….iii List of Tables……………………………………………………………………………………..iv Acknowledgements……………………………………………………………………………….v Introduction……………………………………………………………………………………….1 Background………………………………………………………………………………………..3 Requirements……………………………………………………………………………………...6 Design……………………………………………………………………………………..………7 Total System Design……………………………………………………………...……….7