Estimation of Bogie Performance Criteria Through On-Board Condition Monitoring
Total Page:16
File Type:pdf, Size:1020Kb
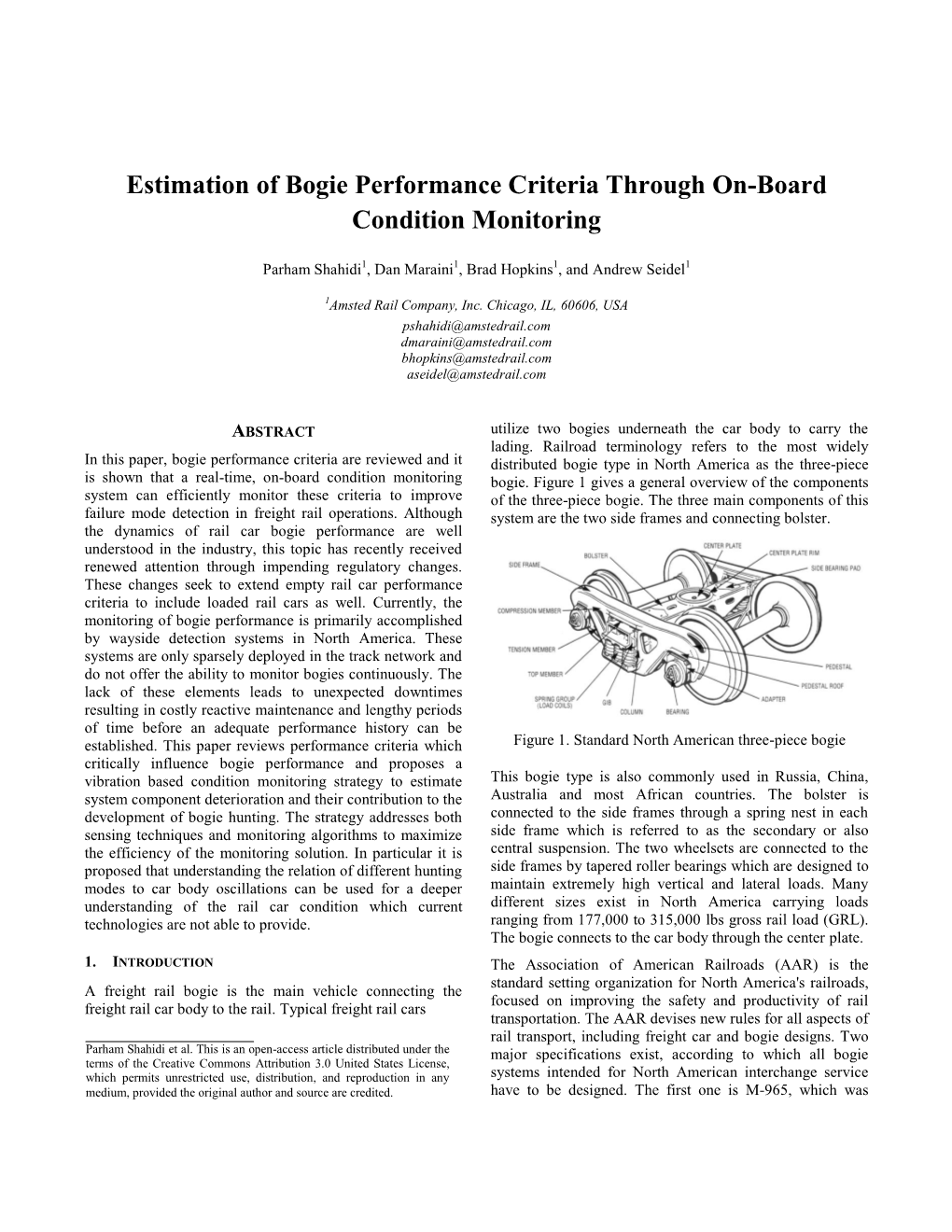
Load more
Recommended publications
-
Assessing Steam Locomotive Dynamics and Running Safety by Computer Simulation
TRANSPORT PROBLEMS 2015 PROBLEMY TRANSPORTU Volume 10 Special Edition steam locomotive; balancing; reciprocating; hammer blow; rolling stock and track interaction Dāvis BUŠS Institute of Transportation, Riga Technical University Indriķa iela 8a, Rīga, LV-1004, Latvia Corresponding author. E-mail: [email protected] ASSESSING STEAM LOCOMOTIVE DYNAMICS AND RUNNING SAFETY BY COMPUTER SIMULATION Summary. Steam locomotives are preserved on heritage railways and also occasionally used on mainline heritage trips, but since they are only partially balanced reciprocating piston engines, damage is made to the railway track by dynamic impact, also known as hammer blow. While causing a faster deterioration to the track on heritage railways, the steam locomotive may also cause deterioration to busy mainline tracks or tracks used by high speed trains. This raises the question whether heritage operations on mainline can be done safely and without influencing the operation of the railways. If the details of the dynamic interaction of the steam locomotive's components are examined with computerised calculations they show differences with the previous theories as the smaller components cannot be disregarded in some vibration modes. A particular narrow gauge steam locomotive Gr-319 was analyzed and it was found, that the locomotive exhibits large dynamic forces on the track, much larger than those given by design data, and the safety of the ride is impaired. Large unbalanced vibrations were found, affecting not only the fatigue resistance of the locomotive, but also influencing the crew and passengers in the train consist. Developed model and simulations were used to check several possible parameter variations of the locomotive, but the problems were found to be in the original design such that no serious improvements can be done in the space available for the running gear and therefore the running speed of the locomotive should be limited to reduce its impact upon the track. -
Car Body and Bogie Connection Modification for Track Curves Passability Improvement
MATEC Web of Conferences 157, 03009 (2018) https://doi.org/10.1051/matecconf/201815703009 MMS 2017 Car body and bogie connection modification for track curves passability improvement Vladimír Hauser1,*, la . Nozhenko1, Kara Kravchenko1, Mária Loulová1, Juraj Gerlici1, Tomáš Lack1 1University of Ţilina, Faculty of Mechanical Engineering, Department of Transport and Handling Machines, Univerzitná 1, 010 26 Ţilina, Slovak Republic Abstract. For Tram cars, it is often necessary to operate in cities on strongly curved track, which is followed by an increased effect of the vehicle on the track. Especially, this increased effect occurs in spiral transition curves situated between direct and arc sections or between two arc sections of different radius. In such case, increased guiding forces, creep in the rail - wheel contact, wear and noise generation can be observed. Exactly with the aim to reduce these undesirable effects we designed a tram bogie with steered wheelsets. This paper deals with a modification of its coupling to vehicle body in order to improve vehicle dynamics in transition curves. Proposed innovative construction of this coupling unit is registered by authors under Utility Model Nr. u201609015 and Utility Model Nr. u201703246. Description of the proposed way for a vehicle to pass through curved track with regard to bogie-body coupling and wheelset steering mechanisms with usage of multibody computing software is given in this paper. Keywords: bogie to vehicle body coupling, track transition curves, tramcar throughput improvement 1 Introduction The way a vehicle passes a track arc depends on many factors. The most important of these include the bogie wheelbase, the distance of pivot pins, the way the car body is mounted on the bogie, the design of the wheelset guiding in the bogie, the track gauge and the width of the track free channel with which the geometry of the wheel and rail profiles is directly related. -
Calculated Estimation of Railway Wheels Equivalent Conicity Influence on Critical Speed of Railway Passenger Car
MATEC Web of Conferences 157, 03006 (2018) https://doi.org/10.1051/matecconf/201815703006 MMS 2017 Calculated estimation of railway wheels equivalent conicity influence on critical speed of railway passenger car Juraj Gerlici1,*, Rostyslav Domin2, Ganna Cherniak2, Tomáš Lack1 1University of Žilina, Faculty of Mechanical Engineering, Department of Transport and Handling Machines, 010 26 Žilina, Slovak Republic 2Volodymyr Dahl East Ukrainian National University, Department of Rail Transport, 93400 Sewerodonetsk, Ukraine Abstract. The article presents the results of determining the equivalent conicity characterizing the geometric interaction of wheels and rails on 1520 mm track. The cases of interactions of rails and wheelsets, wheels of which have different profiles, are considered. The computer model of the motion speed of the passenger car is developed. According to the results of computer simulation, critical speeds for the bogie moving through the tracks of indented gauge are received. Based on the results of the simulation analysis, the significant dependence of the value of the equivalent conicity on the critical speed is confirmed. The necessity of considering the limit values of equivalent conicity in tests of high-speed rolling stock is emphasized. Keywords: railway wheels, equivalent conicity, critical speed, passenger vehicle 1 Introduction The increase of speed of passenger trains up to 160-200 km/h brings new technological level on the Ukrainian railways. Cars of high-speed trains must fully comply with international requirements, both in the level of comfort, and in terms of safety. In this regard, the task of ensuring the stability of motion of the high-speed rolling stock must be resolved as a matter of priority. -
The Evolution of the Steam Locomotive, 1803 to 1898 (1899)
> g s J> ° "^ Q as : F7 lA-dh-**^) THE EVOLUTION OF THE STEAM LOCOMOTIVE (1803 to 1898.) BY Q. A. SEKON, Editor of the "Railway Magazine" and "Hallway Year Book, Author of "A History of the Great Western Railway," *•., 4*. SECOND EDITION (Enlarged). £on&on THE RAILWAY PUBLISHING CO., Ltd., 79 and 80, Temple Chambers, Temple Avenue, E.C. 1899. T3 in PKEFACE TO SECOND EDITION. When, ten days ago, the first copy of the " Evolution of the Steam Locomotive" was ready for sale, I did not expect to be called upon to write a preface for a new edition before 240 hours had expired. The author cannot but be gratified to know that the whole of the extremely large first edition was exhausted practically upon publication, and since many would-be readers are still unsupplied, the demand for another edition is pressing. Under these circumstances but slight modifications have been made in the original text, although additional particulars and illustrations have been inserted in the new edition. The new matter relates to the locomotives of the North Staffordshire, London., Tilbury, and Southend, Great Western, and London and North Western Railways. I sincerely thank the many correspondents who, in the few days that have elapsed since the publication: of the "Evolution of the , Steam Locomotive," have so readily assured me of - their hearty appreciation of the book. rj .;! G. A. SEKON. -! January, 1899. PREFACE TO FIRST EDITION. In connection with the marvellous growth of our railway system there is nothing of so paramount importance and interest as the evolution of the locomotive steam engine. -
1976 Technical Documentation Locomotive Truck Hunting M.Pdf
TECHNICAL DOCUMENTATION LOCOMOTIVE TRUCK HUNTING MODEL V. K. Garg OHO G. C. Martin P. W. Hartmann J. G. Tolomei mnnnn irnational Government-Industry 04 - Locomotives ch Program on Track Train Dynamics R-219 TE C H N IC A L DOCUMENTATION rnn nnn LOCOMOTIVE TRUCK HUNTING MODEL V. K. Garg G. C. Martin P. W. Hartmann a a J. G. Tolomei dD 11 TT|[inr i3^1 i i H§ic§ An International Government-Industry Research Program on Track Train Dynamics Chairman L. A. Peterson J. L. Cann Director Vice President Office of Rail Safety Research Steering Operation and Maintenance Federal Railroad Administration Canadian National Railways G. E. Reed Vice Chairman Director Committee W. J. Harris, Jr. Railroad Sales Vice President AMCAR Division Research and Test Department ACF Industries Association of American Railroads D. V. Sartore or the E. F. Lind Chief Engineer Design Project Director-Phase I Burlington Northern, Inc. Track Train Dynamics Southern Pacific Transportation Co. P. S. Settle Tack Tain President M. D. Armstrong Railway Maintenance Corporation Chairman Transportation Development Agency W. W. Simpson Dynamics Canadian Ministry of Transport Vice President Engineering W. S. Autrey Southern Railway System Chief Engineer Atchison, Topeka & Santa Fe Railway Co. W. S. Smith Vice President and M. W. Beilis Director of Transportation Manager General Mills, Inc. Locomotive Engineering General Electric Company J. B. Stauffer Director M. Ephraim Transportation Test Center Chief Engineer Federal Railroad Administration Electro Motive Division General Motors Corporation R. D. Spence (Chairman) J. G. German President Vice President ConRail Engineering Missouri Pacific Co. L. S. Crane (Chairman) President and Chief W. -
O-Steam-Price-List-Mar2017.Pdf
Part # Description Package Price ======== ================================================== ========= ========== O SCALE STEAM CATALOG PARTS LIST 2 Springs, driver leaf........................ Pkg. 2 $6.25 3 Floor, cab and wood grained deck............. Ea. $14.50 4 Beam, end, front pilot w/coupler pocket...... Ea. $8.00 5 Beam, end, rear pilot w/carry iron.......... Ea. $8.00 6 Bearings, valve rocker....................... Pkg.2 $6.50 8 Coupler pockets, 3-level, for link & pin..... Pkg. 2 $5.75 9 Backhead w/fire door base.................... Ea. $9.00 10 Fire door, working........................... Ea. $7.75 11 Journal, 3/32" bore.......................... Pkg. 4. $5.75 12 Coupler pockets, small, S.F. Street Railway.. Pkg.2 $5.25 13 Brakes, engine............................... Pkg.2 $7.00 14 Smokebox, 22"OD, w/working door.............. Ea. $13.00 15 Drawbar, rear link & pin..................... Ea. $5.00 16 Handles, firedoor............................ Pkg.2. $5.00 17 Shelf, oil can, backhead..................... Ea. $5.75 18 Gauge, backhead, steam pressure.............. Ea. $5.50 19 Lubricator, triple-feed, w/bracket, Seibert.. Ea. $7.50 20 Tri-cock drain w/3 valves, backhead.......... Ea. $5.75 21 Tri-cock valves, backhead, (pl. 48461)....... Pkg. 3 $5.50 23 Throttle, nonworking......................... Ea. $6.75 23.1 Throttle, non working, plastic............... Ea. $5.50 24 Pop-off, pressure, spring & arm.............. Ea. $6.00 25 Levers, reverse/brake, working............... Kit. $7.50 26 Tri-cock drain, less valves.................. Ea. $5.75 27 Seat boxes w/backs........................... Pkg.2 $7.50 28 Injector w/piping, Penberthy,................ Pkg.2 $6.75 29 Oiler, small hand, N/S....................... Pkg.2 $6.00 32 Retainers, journal........................... Pkg. -
Field and Analytical Investigation of a 3D Dynamic Train-Track Interaction Model at Critical Speeds
The Pennsylvania State University The Graduate School Department of Civil and Environmental Engineering FIELD AND ANALYTICAL INVESTIGATION OF A 3D DYNAMIC TRAIN-TRACK INTERACTION MODEL AT CRITICAL SPEEDS A Dissertation in Civil Engineering by Yin Gao 2016 Yin Gao Submitted in Partial Fulfillment of the Requirements for the Degree of Doctor of Philosophy August 2016 ii The dissertation of Yin Gao was reviewed and approved* by the following: Hai Huang Associate Professor of Rail Transportation Engineering Dissertation Adviser Co-chair of Committee Shelley Marie Stoffels Professor of Civil Engineering Co-chair of Committee Tong Qiu Associate Professor of Civil and Environmental Engineering Jamal Rostami Associate Professor of Energy and Mineral Engineering Patrick Fox Professor of Civil and Environmental Engineering Department Head of Civil and Environmental Engineering *Signatures are on file in the Graduate School iii ABSTRACT Railroad transportation, especially high-speed passenger rail, has been developing at sensational speed, creating the needs to evaluate the track safety and predict the potential hazards for railroad operation. As train speed increases, the responses of the train and track substructure present larger dynamic behavior, which raises problems in passenger comfort, operational safety and track structures. With the boom of modeling and computing techniques, numerical simulation becomes a more feasible, safe and effective tool to identify the problems in railroad engineering. In this dissertation, a self-developed three-dimensional train-track interaction model is formulated, validated and implemented to predict the potential risks and explore the mechanisms of rail track problems. The developed 3D dynamic track-subgrade interaction model includes a train model, 2D discrete support track model and 3D computation-efficient finite element (FE) soil subgrade model. -
Data Sheet Bogies-SF
SF 500 Bogies for high-speed trains The SF 500 bogies are a further Excellent ride quality is achieved in the Suspension is designed taking running development of the SGP 400 bogies, secondary suspension system by the stability and acoustic requirements 950 of which are in use on the ICE2 of high-tech air suspension system and into consideration. the Deutsche Bahn AG. They are the provision of large air volume. Redundant-type hydraulic yaw designed for electric railcar trains and The pivot, the yoke and the two dampers are used to stabilise running modern high-speed trains and provide traction rods are proven designs and behaviour at high speeds. optimum ride quality. similar to the con-cept of the ICE2. The trailer bogies are equipped with a Orders have been received from the Torque transmission from the lateral mechanical disc brake system with Deutsche Bahn AG, the Netherlands traction motor is achieved by a 2, 3 or 4 discs per axle and a non-wear Railways, the RENFE and many other partially suspended, low-noise gear eddy-current brake. On the motor operators for more than 6500 bogies. per axle together with spiral-toothed bogie, wheel disc brakes are used. The modular design means that the coupling. SF 500 bogie can be designed both as Bogie traction motors are flexibly motor bogies and as trailer bogies and suspended in the bogie by a motor can be fitted beneath carbodies with support structure and an innovative or without bolster. laminated spring damper system. Bogie weight is significantly lower than that of comparable bogies due to the use of light-weight components. -
How Bogies Work Isao Okamoto
T Technology echnolo Railway Technology Today 5 (Edited by Kanji Wako) How Bogies Work Isao Okamoto Role of Bogie Figure 1 Wheel and Axle Set Railcar bogies usually go unnoticed by rail passengers, but despite their obscurity, Wheel tread Flange they are very important in safe railway Tread operations and perform the following Wheel Axle gradient functions: • Support railcar body firmly Wheel • Run stably on both straight and curved diameter track • Ensure good ride comfort by absorbing vibration generated by track irregulari- Rail ties and minimizing impact of centri- fugal forces when train runs on curves at high speed Gauge • Minimize generation of track irregulari- ties and rail abrasion To help clarify the basic mechanism of gy bogies, this article explains bogies used affect the running performance and and some express trains of the Odakyu on conventional railcars. Bogies used on strength of the bogie frame, so none are Line in suburban Tokyo. Although the shinkansen will be discussed in more de- used for passenger railcars in Japan today. articulated bogie has some disadvantages, tail in the next article in this series. Non-articulated and articulated bogies such as a complex structure, increased Bogies can be classified into non-articu- axle load due to the support of one body lated and articulated types according to by one bogie, and difficult maintenance, Bogie Configurations the suspension. Two non-articulated it offers various advantages including a bogies usually support one railcar body lower centre of gravity, better ride com- Types (Fig. 3a), but one articulated bogie sup- fort because car ends do not overhang Bogies are classified into the various types ports the back end of the forward car and bogies, and less effect of running noise described below according to their con- the front end of the rear car (Fig. -
Basics of Vehicle Truck and Suspension Systems and Fundamentals of Vehicle Steering and Stability
Basics of Vehicle Truck and Suspension Systems and Fundamentals of Vehicle Steering and Stability Ralph Schorr, PE Senior Product Development Engineer Vehicle/Truck Dynamicist 1 Course Agenda • Truck Nomenclature • Wheel/rail influences • Truck Dynamics – Physics • Truck Types • AAR M‐976 • Truck Maintenance 2 Truck Nomenclature (Bogie) 3-piece truck Friction Wedge or Shoe Sideframe Wheel Adapter Spring Group Adapter Pad CCSB Bolster Control Springs Load Springs Axle Bearing 3 Truck Nomenclature Brake Beam Guide Pedestal Roof Column Wear Plate Thrust Lugs Center Bowl Side Bearing Pad Bolster/Friction Pocket Brake Rod Openings Gibs 4 Suspension Nomenclature Friction Wedge or Shoe Bolster Column Wear Plate Pocket Wear Plate Load Springs Side Frame Control Springs 5 North American Freight Car Systems Capacity GRL Bearing Wheel Diameter Tons Lbs. Size Inches 70 220,000 Class E33 100 263,000 Class F36 110 286,000 Class K36 125 315,000 Class G 38 6 Contact Patch area Comparison of Wheel/Rail contact area of AAR-1B-WF 200 180 160 140 120 loaded 286k (32.4mt) 100 80 loaded 263k (29.8mt) 60 40 empty 40k(6.8mt) 20 Area in mm^2 0 -50 0 50 Lateral position in mm 7 Dynamic Influences • Speed • Wheel to Rail Contact • Track Input • Mass/Inertias (Car Body, Truck Components) • Friction • Spring Suspension • Suspension Dampening 8 Multimode Dynamics Software 9 Critical Attributes of the Wheel/Rail 1. Wheel set back‐to‐back dimension 2. Wheel Profile of both wheels 3. Wheel tapeline of both wheels 4. Rail Gauge (I.E. gauge point) 5. Rail Profile of both rails 6. -
For Precise Evaluation of Wheel-Rail Contact Mechanics and Dynamics [Doctoral Thesis]", in Mechanical Engineering
Accurate Wheel-rail Dynamic Measurement using a Scaled Roller Rig Karan Kothari Thesis submitted to the faculty of the Virginia Polytechnic Institute and State University in partial fulfillment of the requirements for the degree of Masters of Science In Mechanical Engineering Mehdi Ahmadian, Chair Steve C Southward Reza Mirzaeifar June 19, 2018 Blacksburg, VA Keywords: scaled roller rig, dynamic measurements, wheel-rail contact, traction forces, angle of attack, third-body layer, wheel wear Accurate Wheel-rail Dynamic Measurement using a Scaled Roller Rig Karan Kothari Abstract (academic) The primary purpose of this study is to perform accurate dynamic measurements on a scaled roller rig designed and constructed by Virginia Tech and the Federal Railroad Administration (VT-FRA Roller Rig). The study also aims at determining the effect of naturally generated third-body layer deposits (because of the wear of the wheel and/or roller) on creep or traction forces. The wheel- rail contact forces, also referred to as traction forces, are critical for all aspects of rail dynamics. These forces are quite complex and they have been the subject of several decades of research, both in experiments and modeling. The primary intent of the VT-FRA Roller Rig is to provide an experimental environment for more accurate testing and evaluation of some of the models currently in existence, as well as evaluate new hypothesis and theories that cannot be verified on other roller rigs available worldwide. The Rig consists of a wheel and roller in a vertical configuration that allows for closely replicating the boundary conditions of railroad wheel-rail contact via actively controlling all the wheel-rail interface degrees of freedom: angle of attack, cant angle, normal load and lateral displacement, including flanging. -
Advance in Railway Vehicle Technology and Future Prospects Mainly in Relation to Bogie
NIPPON STEEL & SUMITOMO METAL TECHNICAL REPORT No. 105 DECEMBER 2013 Technical Review UDC 629 . 11 . 011 . 1 Advance in Railway Vehicle Technology and Future Prospects Mainly in Relation to Bogie Satoshi KOIZUMI* Abstract Since the world’s first public railway opened in Britain in 1825, high speed and safety have been the most important technical issues for the improvement of rolling stock perfor- mance. In particular, the trade-off problem between the curve negotiation and the high- speed running stability is a basic issue for bogie design technology. But today, by the use of simulation techniques, we can design the suitable rolling stock for the various applications. For the higher performance of rolling stocks, the following technical issues have been chal- lenged. The issues for high speed are the prevention of hunting, high speed curve negotia- tion by the use of tilting control, brake technology to slow down early from the high-speed range, and acceleration of lightweight. The issues for safety are the derailment prevention on the curve, the safety against the natural disasters. In addition, we are working on a ride comfort, an environmental protection such as noise and vibration, and the issues of main- tenance. 1. Introduction namely ride comfort and environmental protection, are dealt with. Ever since the first public railway of the world began its opera- What is required for maintenance of railway vehicles, an issue of in- tion in the U.K. in 1825, the most fundamental requirement for rail- creasing attention, is also considered, and finally, some prospects for way technology has been the pursuit for higher speeds and safety.