WHITE PAPER How Does Prism Technology Help to Achieve Superior Color Image Quality?
Total Page:16
File Type:pdf, Size:1020Kb
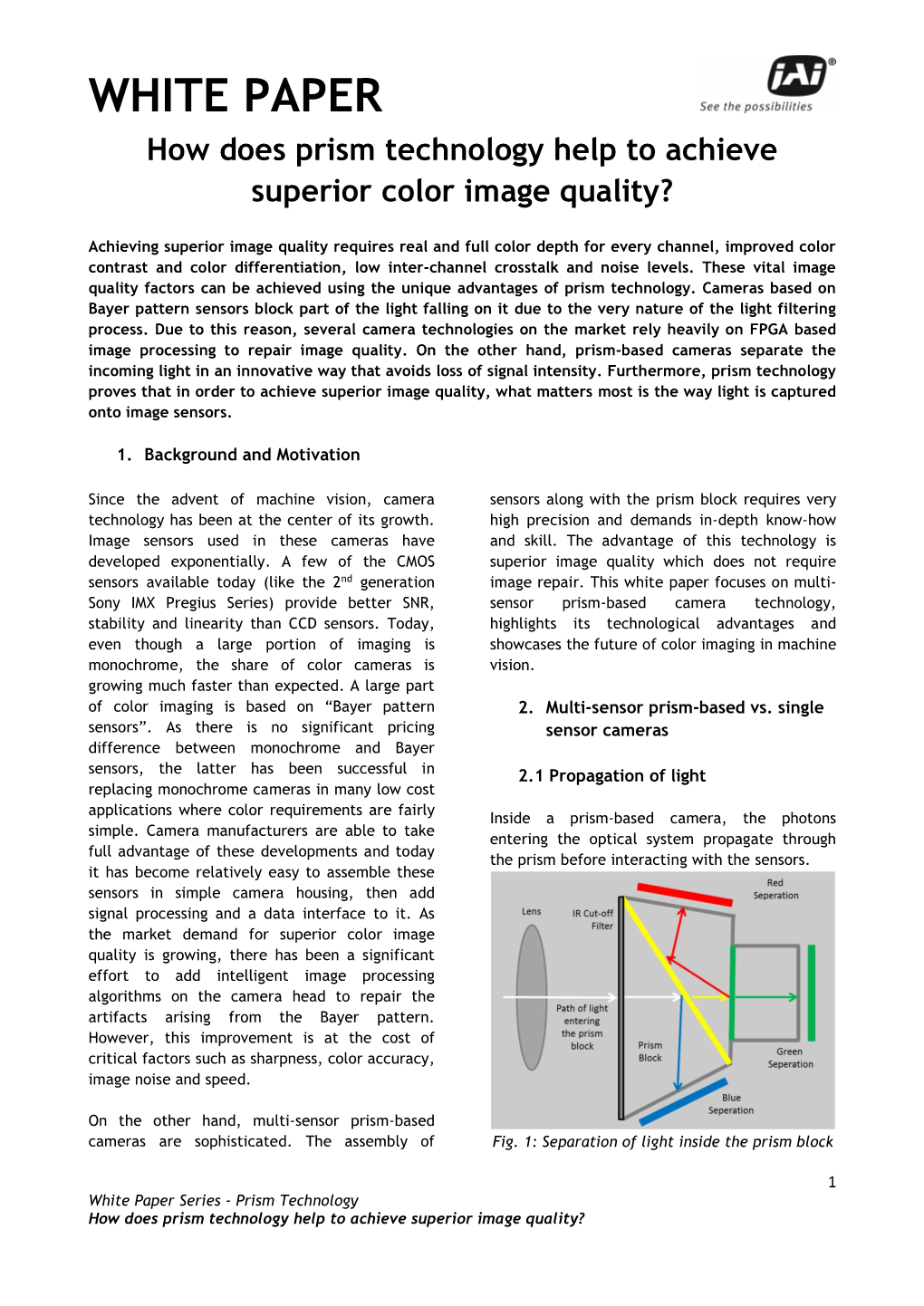
Load more
Recommended publications
-
Multispectral Imaging for Medical and Industrial Machine Vision Systems
1 | Tech Guide: Multispectral imaging for medical and industrial machine vision systems Tech Guide: Multispectral Imaging Multispectral imaging for medical and industrial machine vision systems 2 | Tech Guide: Multispectral imaging for medical and industrial machine vision systems Table of contents Introduction Chapter 1: What is multispectral imaging? Chapter 2: Multispectral imaging applications Chapter 3: Multispectral camera technologies Chapter 4: Key considerations when selecting camera technology for multispectral imaging Chapter 5: Hyperspectral and the future of multispectral imaging 3 | Tech Guide: Multispectral imaging for medical and industrial machine vision systems Introduction Just as machine vision systems have evolved from traditional monochrome cameras to many systems that now utilize full color imaging information, there has also been an evolution from systems that only captured broadband images in the visible spectrum, to those that can utilize targeted spectral bands in both visible and non- visible spectral regions to perform more sophisticated inspection and analysis. The color output of the cameras used in the machine vision industry today is largely based on Bayer-pattern or trilinear sensor technology. But imaging is moving well beyond conventional color where standard RGB is not enough to carry out inspection tasks. Some applications demand unconventional RGB wavelength bands while others demand a combination of visible and non-visible wavelengths. Others require exclusively non-visible wavelengths such as UV, NIR or SWIR, with no wavebands in the visible spectrum. Complex metrology and imaging applications are beginning to demand higher numbers of spectral channels or possibilities to select application-specific spectral filtering at high inspection throughputs. With the traditional machine vision industry merging with intricate measurement technologies, consistent, reliable, high-fidelity color and multispectral imaging are playing key roles in industrial quality control. -
United States Patent (19) 11 Patent Number: 6,072,635 Hashizume Et Al
US006072635A United States Patent (19) 11 Patent Number: 6,072,635 Hashizume et al. (45) Date of Patent: Jun. 6, 2000 54) DICHROIC PRISM AND PROJECTION FOREIGN PATENT DOCUMENTS DISPLAY APPARATUS 7-294.845 11/1995 Japan. 75 Inventors: Toshiaki Hashizume, Okaya; Akitaka Primary Examiner Ricky Mack Yajima, Tatsuno-machi, both of Japan Attorney, Agent, or Firm-Oliff & Berridge, PLC 73 Assignee: Seiko Epson Corporation, Tokyo, 57 ABSTRACT Japan The invention provides a dichroic prism capable of reducing displacements of projection pixels of colors caused by 21 Appl. No.: 09/112,132 chromatic aberration of magnification. A dichroic prism is formed in the shape of a quadrangular prism as a whole by 22 Filed: Jul. 9, 1998 joining four rectangular prisms together. A red reflecting 30 Foreign Application Priority Data dichroic plane and a blue reflecting dichroic plane intersect to form Substantially an X shape along junction Surfaces of Jul. 15, 1997 JP Japan .................................... 9-1900OS the prisms. The red reflecting dichroic plane is convex shaped by partly changing the thickness of an adhesive layer 51 Int. Cl." ............................ G02B 27/12: G02B 27/14 for connecting the rectangular prisms together. Accordingly, 52 U.S. Cl. ............................................. 359/640; 359/634 Since a red beam can be guided to a projection optical System 58 Field of Search ..................................... 359/634, 637, while being enlarged, it is possible to reduce a projection 359/640 image of the red beam to be projected onto a projection plane Via the projection optical System. This makes it 56) References Cited possible to reduce relative displacements of projection pix U.S. -
Characterization of Color Cross-Talk of CCD Detectors and Its Influence in Multispectral Quantitative Phase Imaging
Characterization of color cross-talk of CCD detectors and its influence in multispectral quantitative phase imaging 1,2,3 1 1,2 1 AZEEM AHMAD , ANAND KUMAR , VISHESH DUBEY , ANKIT BUTOLA , 2 1,4 BALPREET SINGH AHLUWALIA , DALIP SINGH MEHTA 1Department of Physics, Indian Institute of Technology Delhi, Hauz Khas, New Delhi 110016, India 2Department of Physics and Technology, UiT The Arctic University of Norway, Tromsø 9037, Norway [email protected] [email protected] Abstract: Multi-spectral quantitative phase imaging (QPI) is an emerging imaging modality for wavelength dependent studies of several biological and industrial specimens. Simultaneous multi-spectral QPI is generally performed with color CCD cameras. However, color CCD cameras are suffered from the color crosstalk issue, which needed to be explored. Here, we present a new approach for accurately measuring the color crosstalk of 2D area detectors, without needing prior information about camera specifications. Color crosstalk of two different cameras commonly used in QPI, single chip CCD (1-CCD) and three chip CCD (3-CCD), is systematically studied and compared using compact interference microscopy. The influence of color crosstalk on the fringe width and the visibility of the monochromatic constituents corresponding to three color channels of white light interferogram are studied both through simulations and experiments. It is observed that presence of color crosstalk changes the fringe width and visibility over the imaging field of view. This leads to an unwanted non-uniform background error in the multi-spectral phase imaging of the specimens. It is demonstrated that the color crosstalk of the detector is the key limiting factor for phase measurement accuracy of simultaneous multi-spectral QPI systems. -
Comparative Analysis of Color Architectures for Image Sensors
Comparative analysis of color architectures for image sensors Peter B. Catrysse*a, Brian A. Wande11', Abbas El Gamala aDept of Electrical Engineering, Stanford University, CA 94305, USA bDept ofPsychology, Stanford University, CA 94305,USA ABSTRACT We have developed a software simulator to create physical models of a scene, compute camera responses, render the camera images and to measure the perceptual color errors (CIELAB) between the scene and rendered images. The simulator can be used to measure color reproduction errors and analyze the contributions of different sources to the error. We compare three color architectures for digital cameras: (a) a sensor array containing three interleaved color mosaics, (b) an architecture using dichroic prisms to create three spatially separated copies of the image, (c) a single sensor array coupled with a time-varying color filter measuring three images sequentially in time. Here, we analyze the color accuracy of several exposure control methods applied to these architectures. The first exposure control algorithm (traditional) simply stops image acquisition when one channel reaches saturation. In a second scheme, we determine the optimal exposure time for each color channel separately, resulting in a longer total exposure time. In a third scheme we restrict the total exposure duration to that of the first scheme, but we preserve the optimum ratio between color channels. Simulator analyses measure the color reproduction quality of these different exposure control methods as a function of illumination taking into account photon and sensor noise, quantization and color conversion errors. Keywords: color, digital camera, image quality, CMOS image sensors 1. INTRODUCTION The use of CMOS sensors in digital cameras has created new opportunities for developing digital camera architectures. -
Can I Bring Dreams to Life with Quality & Versatility?
Can I bring dreams to life with quality & versatility? They've been dreaming about the wedding day for months. Positioning the green CCD out of line PROFESSIONAL FLUORITE LENS (pixel shift) sharpens image reproduction Canon has always led the way in optical Every detail has been planned. It goes perfectly. Bride and even if your subject moves. A new Super development. The first to equip a cam- Pixel Shift (horizontal + vertical) achieves corder with a fluorite lens – a lens that groom look radiant and the guests enjoy themselves. wider dynamic range for movies, reducing provides the quality of 35mm and vertical smear and gives 1.7 mega-pixel broadcast TV. The XM2 has a Professional You can bring back those special moments in a top-quality high resolution photos. L-Series fluorite lens. Combined with 20x optical zoom and 100x digital zoom, video recording. plus an optical image stabiliser, you can be sure of superior images. SUPERB QUALITY INSPIRATIONAL VERSATILITY The Canon XM2 Digital Camcorder No two video shoots are alike. What's combines the best of all worlds. Its happening, where it's happening, move- advanced technology delivers unri- ment, colour – it all demands a certain valled image quality in its class, while it amount of fine-tuning to capture the is still easy to operate. That makes it an special moments you want. The XM2 ideal choice for both serious camcorder features adjustments and enhancements enthusiasts, professional video- for sound and picture for your personal graphers and filmmakers. Whether creativity. Plus a LCD screen for easy you're regularly providing broadcast viewing. -
ELEC 7450 - Digital Image Processing Image Acquisition
I indirect imaging techniques, e.g., MRI (Fourier), CT (Backprojection) I physical quantities other than intensities are measured I computation leads to 2-D map displayed as intensity Image acquisition Digital images are acquired by I direct digital acquisition (digital still/video cameras), or I scanning material acquired as analog signals (slides, photographs, etc.). I In both cases, the digital sensing element is one of the following: Line array Area array Single sensor Stanley J. Reeves ELEC 7450 - Digital Image Processing Image acquisition Digital images are acquired by I direct digital acquisition (digital still/video cameras), or I scanning material acquired as analog signals (slides, photographs, etc.). I In both cases, the digital sensing element is one of the following: Line array Area array Single sensor I indirect imaging techniques, e.g., MRI (Fourier), CT (Backprojection) I physical quantities other than intensities are measured I computation leads to 2-D map displayed as intensity Stanley J. Reeves ELEC 7450 - Digital Image Processing Single sensor acquisition Stanley J. Reeves ELEC 7450 - Digital Image Processing Linear array acquisition Stanley J. Reeves ELEC 7450 - Digital Image Processing Two types of quantization: I spatial: limited number of pixels I gray-level: limited number of bits to represent intensity at a pixel Array sensor acquisition I Irradiance incident at each photo-site is integrated over time I Resulting array of intensities is moved out of sensor array and into a buffer I Quantized intensities are stored as a grayscale image Stanley J. Reeves ELEC 7450 - Digital Image Processing Array sensor acquisition I Irradiance incident at each photo-site is integrated over time I Resulting array of intensities is moved out of sensor array and into a buffer I Quantized Two types of quantization: intensities are stored as a I spatial: limited number of pixels grayscale image I gray-level: limited number of bits to represent intensity at a pixel Stanley J. -
Camera Sensors
Welcome Processing Digital Camera Images Camera Sensors Michael Thomas Overview Many image sensors: Infrared, gamma ray, x-rays etc. Focus on sensors for visible light (slightly into infrared and uv light) Michael Thomas, TU Berlin, 2010 Processing Digital Camera Images, WS 2010/2011, Alexa/Eitz 2 The beginnings First Video camera tube sensors in the 1930s Cathode Ray Tube (CRT) sensor Vidicon and Plumbicon for TV-Broadcasting in the 1950s – 1980s Vidicon sensors on Galileo-spacecraft to Jupiter in 1980s Michael Thomas, TU Berlin, 2010 Processing Digital Camera Images, WS 2010/2011, Alexa/Eitz 3 The Photoelectric-Effect How to convert light to electric charge? Inner photoelectric-effect at a photodiode: Photon excites electron creating a free electron and a hole The hole moves towards the anode, the electron towards the cathode Now we have our charge! Michael Thomas, TU Berlin, 2010 Processing Digital Camera Images, WS 2010/2011, Alexa/Eitz 4 Charge-Coupled Device (CCD) Integrated circuit Array of connected capacitors (Shift register) Charge of capacitor is transfered to neighbour capacitor At the end of chain, charge is converted into voltage by charge amplifier Transfer stepped by Clock-Signal Serial charge processing Michael Thomas, TU Berlin, 2010 Processing Digital Camera Images, WS 2010/2011, Alexa/Eitz 5 CCD-Sensor Each capacitor is coupled with a photodiode All capacitors are charged parallelly Charges are transferred serially Michael Thomas, TU Berlin, 2010 Processing Digital Camera Images, WS 2010/2011, Alexa/Eitz -
How Digital Cameras Capture Light
1 Open Your Shutters How Digital Cameras Capture Light Avery CirincioneLynch Eighth Grade Project Paper Hilltown Cooperative Charter School June 2014 2 Cover image courtesy of tumblr.com How Can I Develop This: Introduction Imagine you are walking into a dark room; at first you can't see anything, but as your pupils begin to dilate, you can start to see the details and colors of the room. Now imagine you are holding a film camera in a field of flowers on a sunny day; you focus on a beautiful flower and snap a picture. Once you develop it, it comes out just how you wanted it to so you hang it on your wall. Lastly, imagine you are standing over that same flower, but, this time after snapping the photograph, instead of having to developing it, you can just download it to a computer and print it out. All three of these scenarios are examples of capturing light. Our eyes use an optic nerve in the back of the eye that converts the image it senses into a set of electric signals and transmits it to the brain (Wikipedia, Eye). Film cameras use film; once the image is projected through the lens and on to the film, a chemical reaction occurs recording the light. Digital cameras use electronic sensors in the back of the camera to capture the light. Currently, there are two main types of sensors used for digital photography: the chargecoupled device (CCD) and complementary metaloxide semiconductor (CMOS) sensors. Both of these methods convert the intensity of the light at each pixel into binary form, so the picture can be displayed and saved as a digital file (Wikipedia, Image Sensor). -
Colors in Images Color Spaces, Perception, Mixing, Printing, Manipulating
Colors in images Color spaces, perception, mixing, printing, manipulating . Tom´aˇsSvoboda Czech Technical University, Faculty of Electrical Engineering Center for Machine Perception, Prague, Czech Republic [email protected] http://cmp.felk.cvut.cz/~svoboda Warning 2/31 rather an overview lecture pictorial, math kept on minimum knowing keywords you may dig deeper Thanks Wikipedia for many images. Color Spectrum 3/31 Color is a human interpretation of a mixture of light with different wavelength λ (projected into a retina or camera photoreceptors). Isaac Newton’s experiment (1666). Perception of Light 4/31 Human eye contains three types color receptor cells, or cones. Their sensitivity is a function of wavelength. Three peaks may be approximately identified in BLUE, GREEN, RED. Combination of the responses give us our color perception. tristimulus model of color vision. Marking according to wavelengths S — short M — medium L — long RGB color model 4/31 A color point is represented by three numbers [R, G, B] [R, G, B] have typically range 0. 255 for most common 8-bit images RG only, B zero 5/31 RB only, G zero 6/31 GB only, R zero 7/31 Additive mixing 8/31 computer screens, TV, projectors Primary colors: ones used to define other colors, [R,G,B] Secondary colors: pairwise combination of primaries, [C,M,Y] (Cyan, Magenta, Yellow) RG only, B zero 9/31 RB only, G zero 10/31 GB only, R zero 11/31 Subtractive mixing 12/31 it works through light absorption the colors that are seen are from the part of light that is not absorbed paintings, printing, . -
Appendix 1 HOW CCD IMAGERS ARE MADE
Appendix 1 HOW CCD IMAGERS ARE MADE This appendix gives an overview of a possible route which can be followed to make a CCD imager. The fabrication technology is purely an example and the vehicle used to describe the various steps is also a hypothetical device. CCD processes proceed from complicated, MOS-based technologies and processes. The complexity is a result of the relatively large number of technological steps and the consecutive relatively large throughput time in the production facilities. Fabrication involves several implantatron steps and the deposition of several layers of, for instance, silicon oxide, silicon nitride, polycrystalline silicon and at least one layer of metallization. If the imager has to be used in color applications, color filters layers have also to be added. Microlenses are another possible option. The minimum number of masks needed in the production trajectory is about 10 to 12, but, for very highly sophisticated devices (such as HDTV imagers with color filters), as many as 25 masking steps are no longer an exception. Throughput times for CCD imagers processes range from a fortnight to several weeks. In other words, there are probably as many different fabrication processes as there are CCD designs because the technology is quite often optimized with the main application and the device architecture in mind. The architecture on which this overview is based is that of a full-frame device highly suited to describing a minimal route. Figure A1 .1 shows a top view of the device under study. The full-frame imager has a light-sensitive part, a horizontal output register and an output amplifier connected to the floating diffusion. -
Multispectral Cameras
Multispectral Cameras Expanding Beyond the Visible Modern vision and imaging applications rely on interpretation of information acquired by an image sensor. Typically the sensor is designed to emulate human vision, resulting in a color or monochrome image of the field of view as seen by the eye. This is accomplished by sensing light at wavelengths in the visible spectrum (400-700 nm). However, additional information can be gained by creating an image based on the light that is outside the sensitivity of the human eye. The information available can be maximized by combining information found in multiple spectral bands. The photonic spectrum includes energy at wavelengths ranging from the ultraviolet through the visible, near infrared, far infrared, and finally, x-rays. The color image from a Charge Coupled Device (CCD) array is acquired by sensing the wavelengths corresponding to red, green, and blue light. CCD sensors are capable of detecting light beyond the visible wavelengths out to 1100 nm. The wavelengths from 700 nm to 1100 nm are known as the near infrared (NIR) and are not visible to the eye. In standard color video cameras the infrared light is usually blocked from the CCD sensor because it interferes with the quality of the visible image. GSI’s multispectral cameras give you access to the full power of the CCD’s capabilities by providing one imaging array that performs color imaging and two more that sense the invisible light from 700-1100 nm. The wavelengths detected by each array can be further limited by adding narrowband optical filters in the imaging path. -
Projection Type Video Image Display Device Videobildanzeigegerät Nach Dem Projektionsprinzip Dispositif D’Affichage D’Images Vidéo Du Type Projecteur
Europäisches Patentamt & (19) European Patent Office Office européen des brevets (11) EP 0 871 338 B1 (12) EUROPEAN PATENT SPECIFICATION (45) Date of publication and mention (51) Int Cl.: of the grant of the patent: H04N 9/31 (2006.01) 02.08.2006 Bulletin 2006/31 (21) Application number: 98302024.9 (22) Date of filing: 18.03.1998 (54) Projection type video image display device Videobildanzeigegerät nach dem Projektionsprinzip Dispositif d’affichage d’images vidéo du type projecteur (84) Designated Contracting States: • Yamagishi, Shigekazu DE FR GB Takatsuki-shi, Osaka 569-11 (JP) (30) Priority: 10.04.1997 JP 9191897 29.05.1997 JP 13948397 (74) Representative: Crawford, Andrew Birkby et al A.A. Thornton & Co., (43) Date of publication of application: 235 High Holborn 14.10.1998 Bulletin 1998/42 London WC1V 7LE (GB) (73) Proprietor: MATSUSHITA ELECTRIC INDUSTRIAL (56) References cited: CO., LTD. EP-A- 0 537 708 EP-A- 0 731 603 Kadoma-shi, Osaka 571-8501 (JP) EP-A- 0 752 608 US-A- 5 541 673 (72) Inventors: • Hatakeyama, Atsushi Ibaraki-shi, Osaka 567 (JP) Note: Within nine months from the publication of the mention of the grant of the European patent, any person may give notice to the European Patent Office of opposition to the European patent granted. Notice of opposition shall be filed in a written reasoned statement. It shall not be deemed to have been filed until the opposition fee has been paid. (Art. 99(1) European Patent Convention). EP 0 871 338 B1 Printed by Jouve, 75001 PARIS (FR) 1 EP 0 871 338 B1 2 Description same shape.