Sustainability Report 2017
Total Page:16
File Type:pdf, Size:1020Kb
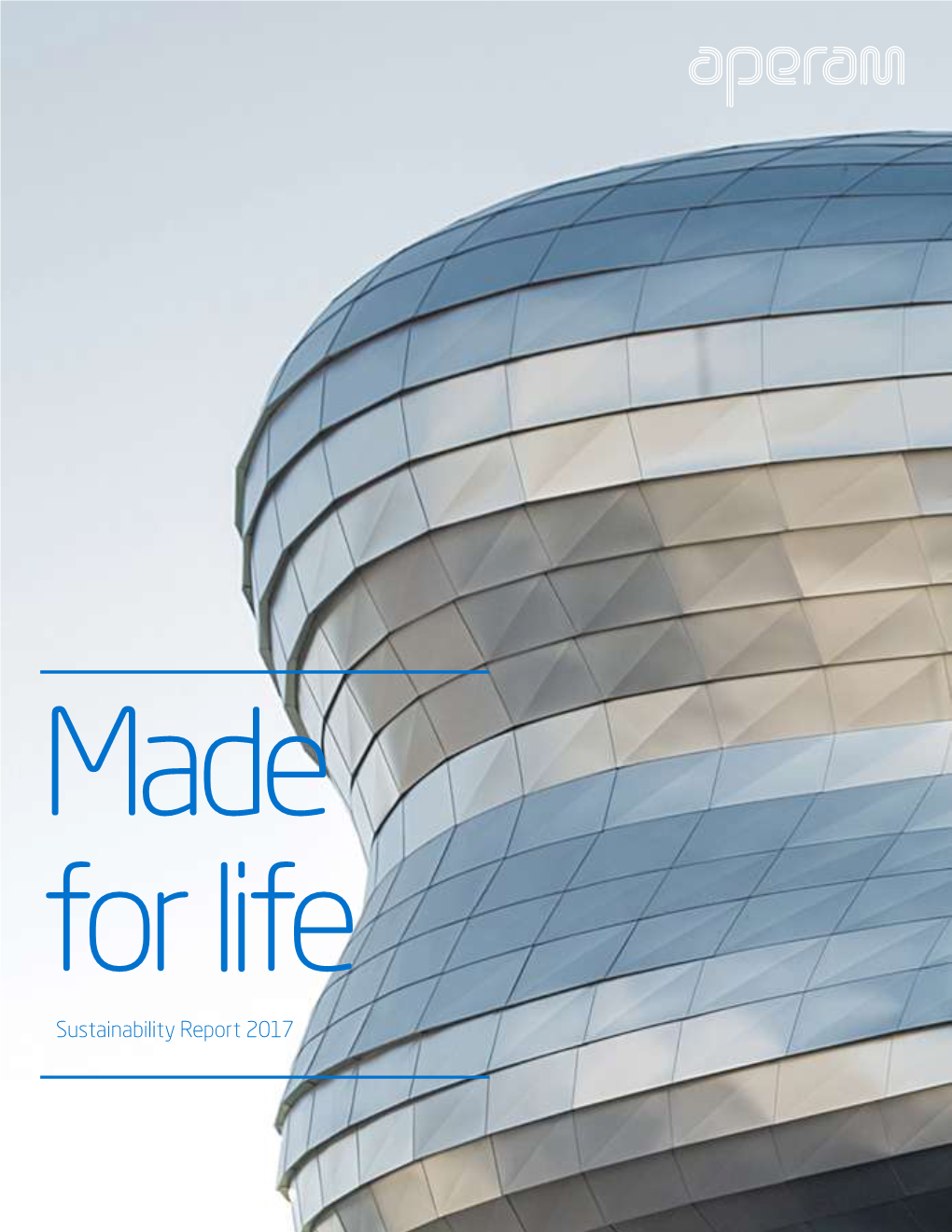
Load more
Recommended publications
-
Employees 18
This document has been translated from the original document in Japanese (”Yukashouken Houkokusho”), which is legally required for Recruit Holdings as a listed company in Japan to support investment decisions by providing certain information about the Company for the fiscal year ended March 31, 2021 (“FY2020”), under Article 24, Paragraph 1 of the Financial Instruments and Exchange Act of Japan. The Japanese original document was filed to the Director-General of the Kanto Local Finance Bureau in Japan on June 18, 2021. Please refer to “Note Regarding Reference Translation” below as a general warning for this translation document. Document Name Annual Report translated from Yukashouken Houkokusho Filing Date June 18, 2021 Fiscal Year FY2020 (From April 1, 2020 to March 31, 2021) Company Name in English Recruit Holdings Co., Ltd. Title and Name of Hisayuki Idekoba Representative President, CEO and Representative Director of the Board Address of Head Office 8-4-17 Ginza, Chuo-ku, Tokyo, Japan (The above address is a registered headquarters. Actual headquarters operation is conducted in the Contact Location below) Telephone Number +81-3-6835-1111 Contact Person Junichi Arai Corporate Executive Officer Contact Location 1-9-2 Marunouchi, Chiyoda-ku, Tokyo, Japan Definition of Abbreviations In this document, the terms the “Company,” “Recruit Group,” “we,” and “our” refer to Recruit Holdings Co., Ltd. and its consolidated subsidiaries unless the context indicates otherwise. The “Holding Company” refers to Recruit Holdings Co., Ltd. (“Recruit Holdings”) on a standalone basis. The Company’s fiscal year starts on April 1 and ends on March 31 of each year. Accordingly, “FY2020” refers to the period from April 1, 2020 to March 31, 2021. -
Our Business Evolution OUR BUSINESS EVOLUTION / PERFORMANCE HIGHLIGHTS / OUR GROUP STRUCTURE
AT A GLANCE Our Business Evolution OUR BUSINESS EVOLUTION / PERFORMANCE HIGHLIGHTS / OUR GROUP STRUCTURE The 59 Years of Our Corporate History FY2018 Consolidated Revenue 2,310.7bn yen Business fields expansion Digital transformation Globalization Recruit Group was founded in 1960 as a small Recruit Group began using computers at a time In the 2000s, Recruit Group entered the global advertising agency specializing in university when their use was still limited, putting digitization market with a bridal business in China. Although newspapers. Two years later, we published our into practice for increased efciency. Following the this ended as a withdrawal, the failure helped “Invitation to Companies,” a collection of job listings introduction of a supercomputer in the 1980s, we us to shape our mergers and acquisitions (M&A) for university students, through which we established transitioned from paper magazines to online media strategy, and we later succeeded in expanding our business model referred to as the “Ribbon in the 1990s, and then to mobile platforms. Not in the US, Europe, Australia and beyond. The 46% Model.” Since then, we have widened our range of only did this allow for faster and more convenient acquisitions of Indeed in 2012 and Glassdoor in Overseas HR business, while also expanding into the life events delivery of information, but it also transformed how 2018 have led to the successful establishment of feld, including education, housing, automobiles, individual users and enterprise clients interact, our HR Technology business, spearheading the bridal, and the lifestyle feld including travel, dining, through the development of groundbreaking tools growth of the Group as a whole and bringing the and beauty. -
Annual Report 2020 Annual Report 2020
Annual Report 2020 Annual Report 2020 Table of contents 10 Years Aperam Journey 4 Message from the Chairman of the Board of Directors 5 Message from the Chief Executive Officer 7 Glossary 9 Management Report 11 Group overview 11 Introduction 11 Business model: how we create value 12 Our history 13 Our operational organisation and facilities 13 Market analysis 17 Market environment 17 Competition 19 Developments regarding trade measures 20 Raw materials and energy 28 Impact of exchange rate movements 29 COVID-19: health and safety, business and accounting review 30 Operational review and liquidity 32 Operational Review 32 Liquidity 39 A strong focus on self-help measures 46 Principal strengths and risks 49 Principal strengths 49 Principal risks and uncertainties related to the Company and the stainless steel and specialty industry 53 Corporate responsibility and Governance 56 Social responsibility 56 Corporate Governance and stakeholder relationships 58 Corporate citizenship 59 Composition of the Board of Directors 61 Composition of the Leadership Team 66 Corporate governance practices 70 Luxembourg Takeover law disclosure 80 Articles of association 82 Compensation 83 Remuneration Policy 83 Remuneration Report 92 Business ethics 97 Environmental responsibility 100 Share capital 104 2 Annual Report 2020 Related Party Transactions 106 Shareholder information 108 Financial Statements 2020 111 Responsibility statement 113 Consolidated Financial statements as of and for the year ended December 31,2020 114 Annual Accounts of the Parent Company as of and for the year ending December 31, 2020 193 Proposed allocation of the 2020 results 215 Disclaimer - Forward Looking Statements In this Annual Report Aperam has made certain forward-looking statements with respect to, among other topics, its financial position, business strategy, projected costs, projected savings, and the plans and objectives of its management. -
"SOLIZE India Technologies Private Limited" 56553102 .FABRIC 34354648 @Fentures B.V
Erkende referenten / Recognised sponsors Arbeid Regulier en Kennismigranten / Regular labour and Highly skilled migrants Naam bedrijf/organisatie Inschrijfnummer KvK Name company/organisation Registration number Chamber of Commerce "@1" special projects payroll B.V. 70880565 "SOLIZE India Technologies Private Limited" 56553102 .FABRIC 34354648 @Fentures B.V. 82701695 01-10 Architecten B.V. 24257403 100 Grams B.V. 69299544 10X Genomics B.V. 68933223 12Connect B.V. 20122308 180 Amsterdam BV 34117849 1908 Acquisition B.V. 60844868 2 Getthere Holding B.V. 30225996 20Face B.V. 69220085 21 Markets B.V. 59575417 247TailorSteel B.V. 9163645 24sessions.com B.V. 64312100 2525 Ventures B.V. 63661438 2-B Energy Holding 8156456 2M Engineering Limited 17172882 30MHz B.V. 61677817 360KAS B.V. 66831148 365Werk Contracting B.V. 67524524 3D Hubs B.V. 57883424 3DUniversum B.V. 60891831 3esi Netherlands B.V. 71974210 3M Nederland B.V. 28020725 3P Project Services B.V. 20132450 4DotNet B.V. 4079637 4People Zuid B.V. 50131907 4PS Development B.V. 55280404 4WEB EU B.V. 59251778 50five B.V. 66605938 5CA B.V. 30277579 5Hands Metaal B.V. 56889143 72andSunny NL B.V. 34257945 83Design Inc. Europe Representative Office 66864844 A. Hak Drillcon B.V. 30276754 A.A.B. International B.V. 30148836 A.C.E. Ingenieurs en Adviesbureau, Werktuigbouw en Electrotechniek B.V. 17071306 A.M. Best (EU) Rating Services B.V. 71592717 A.M.P.C. Associated Medical Project Consultants B.V. 11023272 A.N.T. International B.V. 6089432 A.S. Watson (Health & Beauty Continental Europe) B.V. 31035585 A.T. Kearney B.V. -
Downloaded from Plans Are Developed by the Main on DEME’S Reputation
2 Message from the Chairman and the CEO 10 2018 highlights 14 Board of Directors 16 Operational chart 18 Report on non-financial indicators of the CFE Group SUMMARY OF THE 138TH CORPORATE FINANCIAL YEAR 38 DREDGING, ENVIRONMENTAL & MARINE ENGINEERING 50 CONTRACTING 52 Construction 60 Multitechnics 62 Rail & Utilies 66 REAL ESTATE DEVELOPMENT 75 FINANCIAL REPORT ANNUAL REPORT 2018 1 2018 DELIVERS GOOD PERFORMANCES IN THE THREE DIVISIONS 2018 was a good year for the CFE the vessels of GeoSea and Tideway. MESSAGE FROM group, and was characterized by a Revenue from traditional dredging also THE CHAIRMAN high level of activity. This is evidenced grew with the continuation of work AND by the consolidated revenue, which in Singapore, the start of deepening THE CEO increased by 18.7% to € 3,641 million, work in the port of Szczecin (Poland), and by the well-filled order book and maintenance dredging in Belgium, which at year-end amply topped Germany, Africa and India. Dimco € 5.3 billion. This high volume of also reported a substantial growth of business was also reflected in a very business with three major projects satisfactory profitability. The net profit in the Netherlands (the Rijnlandroute of € 171.5 million is barely 5% lower link, the Terneuzen lock, and the than the previous year, when windfall Blankenburg connection), illustrating profits were reported in the Real Estate the dynamic of the civil engineering Development division. branch that was transferred by CFE at the end of 2015. These strong consolidated results are the outcome of the excellent DEME recorded a slight increase in its performance of our three divisions. -
Annual Report 2020 Cfe Group
TOGETHER SHAPING TOMORROW’S WORLD ANNUAL REPORT 2020 CFE GROUP WHY AND WHO WE ARE HOW WE SHAPE THE WORLD ANNUAL REPORT STATEMENT OF NON-FINANCIAL INFORMATION FINANCIAL STATEMENTS ANNUAL REPORT 2020 CFE GROUP CFE 2020 REPORT ANNUAL ANNUAL REPORT 2020 Pursuant to the Belgian Royal Decree of Decree of 14 November 2007, Piet Dejonghe, 14 November 2007 on the obligations of issuers Managing Director, and MSQ SRL, represent- of financial instruments admitted to trading on ed by Fabien De Jonge, Chief Financial Officer, a regulated market, Compagnie d’Entreprises certify that, to their knowledge: SHAREHOLDER INFORMATION CFE is required to make its annual financial a. the financial statements, prepared in ac- report available to its shareholders. This report cordance with the applicable accounting ORDINARY GENERAL MEETING INVESTOR RELATIONS includes: standards, give a true and fair view of the The shareholders are invited to attend the Additional information is available on our web- • the combined statutory and consolidated assets, financial position and results of Ordinary General Meeting which shall take site (www.cfe.be), such as: annual report of the Board of Directors, Compagnie d’Entreprises CFE and of the place at the registered office of the company, • the annual and half-yearly reports, as well drawn up in accordance with Article 3:32§1, companies included in its scope of consol- Avenue Herrmann-Debroux 42, 1160 Brussels, as the quarterly trading updates; last paragraph, of the Code of Companies idation, on Thursday, 6 May 2021 at 3 pm. -
Recruit Holdings Announces Leadership Structure for FY2019
February 13, 2019 Recruit Holdings Announces Leadership Structure for FY2019 Recruit Holdings Co., Ltd. (TSE 6098) (“Recruit Holdings” or the “Company”) announced today its leadership structure for FY2019 effective April 1, 2019. New Executive Structure (as of April 1, 2019) 1. Recruit Holdings Corporate Executive Officers Name Position Responsibilities Masumi Minegishi President and CEO Internal Audit Shogo Ikeuchi Senior Managing Human Resource / General Affairs Division Corporate Executive Officer, CHRO Hisayuki Idekoba Senior Managing Corporate Planning Division Corporate Executive Administration Division Officer, COO, CSO, Business Operations Division CRO HR Technology Segment RGF OHR USA, Inc. CEO Keiichi Sagawa Senior Managing Finance Division Corporate Executive Officer, CFO Yoshihiro Kitamura Managing Corporate Media & Solutions Segment Executive Officer Recruit Co., Ltd. President and Representative Director Rob Zandbergen Managing Corporate Staffing Segment Executive Officer Recruit Global Staffing B.V. CEO Junichi Arai Corporate Executive Capital Market Strategies Officer Hiroaki Ogata Corporate Executive Business Development Officer Ayano Senaha Corporate Executive Corporate Planning Officer Sustainability/PR Human Resources Iwaaki Taniguchi Corporate Executive Finance / Accounting / Tax Officer Takahiro Noguchi Corporate Executive Work Style Innovation Officer General Affairs Mark Schultz Corporate Executive Legal / Compliance / Information Security Officer 2. Media & Solutions Segment: Recruit Co., Ltd. Corporate Executive -
Annual Report 2017__0.Pdf
Contents Message from the Chairman of the Board of Directors 03 Message from the Chief Executive Officer 04 Glossary 05 Management Report 06 Group overview 08 Introduction 08 The creation of Aperam 09 Our facilities 09 Our key competitive strengths 11 Our key strategic priorities 15 Our profit driving pillars 19 Market analysis 20 Board of Directors 27 Senior Management 32 Corporate responsibility 36 Operational review 40 Liquidity 46 Principal risks and uncertainties related to the company and the stainless and specialty Steel industry 55 Corporate Governance 58 Luxembourg Takeover Law disclosure 68 Share Capital 82 Related Party Transactions 83 Shareholder information 85 Financial statements 2017 89 Responsibility Statement 92 Consolidated Financial Statements as of and for the year ended December 31, 2017 93 Report of the Réviseur d’Entreprises Agréé on the Consolidated Financial Statements 164 Annual Accounts of the Parent Company as of and for the year ended December 31, 2017 169 Report of the Réviseur d’Entreprises Agréé on the Annual Accounts 186 Proposed allocation of the results for 2017 190 Disclaimer - Forward Looking Statements In this Annual Report Aperam has made certain forward-looking statements with respect to, among other topics, its financial position, business strategy, projected costs, projected savings, and the plans and objectives of its management. Such statements are identified by the use of forward-looking verbs such as 'anticipate', 'intend', 'expect', 'plan', 'believe', or 'estimate', or words or phrases with similar meanings. Aperam's actual results may differ materially from those implied by such forward-looking statements due to the known and unknown principal risks and uncertainties to which it is exposed, including, without limitation, the risks described in this Annual Report. -
Made for Life Sustainability Report 2019
Made for life Sustainability Report 2019 External Assurance We declare this report in accordance with GRI core level. Independent assurance statement Material aspects and indicators are shown on p. 8 of this report. Detailed Disclosures on Management Approach (DMA) are in the online supplement ‘C’. The scope of the information and data in this report Deloitte Audit Société à responsabilité limitée issued and covers global operations from January to December 2019. unmodified limited assurance report using ISEA 3000 limited assurance with respect to the Report on the following subject Aperam’s production capacity is focused on: > 6 production sites in Brazil (Timóteo), Belgium (Châtelet, Genk), and France (Gueugnon, Imphy, matters: adherence to the Global Reporting Initiative "GRI Isbergues/Recyco). Standard" guidelines with respect to the Principles of Materiality, > 14 Steel Service Centres (SSC) from our Service & Solutions segment. Stakeholders Inclusiveness, Sustainability context and > 12 transformation facilities: 5 in Service & Solutions segment; Pont de Roide and BioEnergia from Completeness, the adherence of the disclosure in the Report to Stainless & Electrical Steel segment; Rescal, Amilly, Imhua and ICS from Alloys & Specialties. > 16 sales offices: 10 for Service & Solutions segment and 6 from Alloys & Specialties. the GRI Standard "In Accordance Core" criteria and the > Registered office: 12C. rue Guillaume J. Kroll, L-1882 Luxembourg. appropriateness of the GRI Index on pages 68 and 69 of the Report and the fair presentation in all material aspects in Safety data cover Stainless & Electrical Steel, Services & Solutions and Alloys & Specialties divisions, accordance with GRI Standard Guidelines, of selected as well as on-site contractors. Human resources data exclude contractors. -
ANNUAL REPORT 2018 Results Strategy Operations Sustainability Governance & Risk Financial Statements
Results Strategy Operations Sustainability Governance & risk Financial Statements INTEGRATED ANNUAL REPORT 2018 Results Strategy Operations Sustainability Governance & risk Financial Statements RESULTS STRATEGY OPERATIONS Message from the CEO 5 Vision, mission and profile 14 Operations 22 Key performance indicators 7 Market, environmental and societal trends 16 Property portfolio The Netherlands 30 Key figures 2014-2018 8 Integrated strategic business model 18 Property portfolio Belgium 38 The share 10 Fully focused on convenience Property portfolio France 46 Financial Calendar 12 shopping centres 19 Staff & organisation 51 Highlights 2018 13 Strategic management agenda 2017-2019 20 Results 52 Equity and debt 54 EPRA tables 55 Direct & Indirect Result 60 SUSTAINABILITY GOVERNANCE & RISK FINANCIAL STATEMENTS Sustainability 61 Report from the Supervisory Board 81 Financial Statements 116 Stakeholder engagement and materiality 63 Composition of the Supervisory Board 88 Bricks: environmental performance 65 Remuneration report 90 People: our human capital 71 Corporate Governance 97 Partners: teaming up in Alternative Performance Measures 114 supply chain responsibility 75 Society: social performance 77 Achievements & commitments 80 AUDITOR'S REPORT Appendix 201 Material topics 205 Independent Auditor’s Report 185 Annual Report 2018 Wereldhave N.V. 2 Results Strategy Operations Sustainability Governance & risk Financial Statements OUR REPORTING FRAMEWORK This is the integrated annual report 2018 of About Wereldhave Feedback Wereldhave N.V., -
Global Employment Services Industry
Source: ReportLinker March 09, 2020 22:37 ET Global Employment Services Industry Employment Services market worldwide is projected to grow by US$269. 5 Billion, driven by a compounded growth of 5. 1%. Temporary Staffing/Agency Work, one of the segments analyzed and sized in this study, displays the potential to grow at over 4. New York, March 09, 2020 (GLOBE NEWSWIRE) -- Reportlinker.com announces the release of the report "Global Employment Services Industry" - https://www.reportlinker.com/p080458/?utm_source=GNW 9%. The shifting dynamics supporting this growth makes it critical for businesses in this space to keep abreast of the changing pulse of the market. Poised to reach over US$659 Billion by the year 2025, Temporary Staffing/Agency Work will bring in healthy gains adding significant momentum to global growth. - Representing the developed world, the United States will maintain a 5.8% growth momentum. Within Europe, which continues to remain an important element in the world economy, Germany will add over US$12.8 Billion to the region’s size and clout in the next 5 to 6 years. Over US$12.6 Billion worth of projected demand in the region will come from Rest of Europe markets. In Japan, Temporary Staffing/Agency Work will reach a market size of US$49.8 Billion by the close of the analysis period. As the world’s second largest economy and the new game changer in global markets, China exhibits the potential to grow at 5% over the next couple of years and add approximately US$47.4 Billion in terms of addressable opportunity for the picking by aspiring businesses and their astute leaders. -
Findings from the Global Comparative Study on the Definition of Recruitment Fees and Related Costs
MERFRC/2018 Findings from the global comparative study on the definition of recruitment fees and related costs Background paper for discussion at the Tripartite Meeting of Experts on Defining Recruitment Fees and Related Costs (Geneva, 14–16 November 2018) Conditions of Work and Equality Geneva, 2018 Department MERFRC/2018 INTERNATIONAL LABOUR ORGANIZATION Conditions of Work and Equality Department Findings from the global comparative study on the definition of recruitment fees and related costs Background paper for discussion at the Tripartite Meeting of Experts on Defining Recruitment Fees and Related Costs (Geneva, 14–16 November 2018) Geneva, 2018 INTERNATIONAL LABOUR OFFICE, GENEVA Copyright © International Labour Organization 2018 First edition 2018 Publications of the International Labour Office enjoy copyright under Protocol 2 of the Universal Copyright Convention. Nevertheless, short excerpts from them may be reproduced without authorization, on condition that the source is indicated. For rights of reproduction or translation, application should be made to ILO Publications (Rights and Licensing), International Labour Office, CH-1211 Geneva 22, Switzerland, or by email: [email protected]. The International Labour Office welcomes such applications. Libraries, institutions and other users registered with a reproduction rights organization may make copies in accordance with the licences issued to them for this purpose. Visit www.ifrro.org to find the reproduction rights organization in your country. Findings from the global comparative study on the definition of recruitment fees and related costs, Background paper for discussion at the Tripartite Meeting of Experts on Recruitment Fees and Related Costs (Geneva, 14–16 November 2018), International Labour Office, Conditions of Work and Equality Department, Geneva, ILO, 2018.