Hydrofluoric Acid Alkylation ABB and Conocophillips Develop a Critical New Process Analysis Tool Michael B
Total Page:16
File Type:pdf, Size:1020Kb
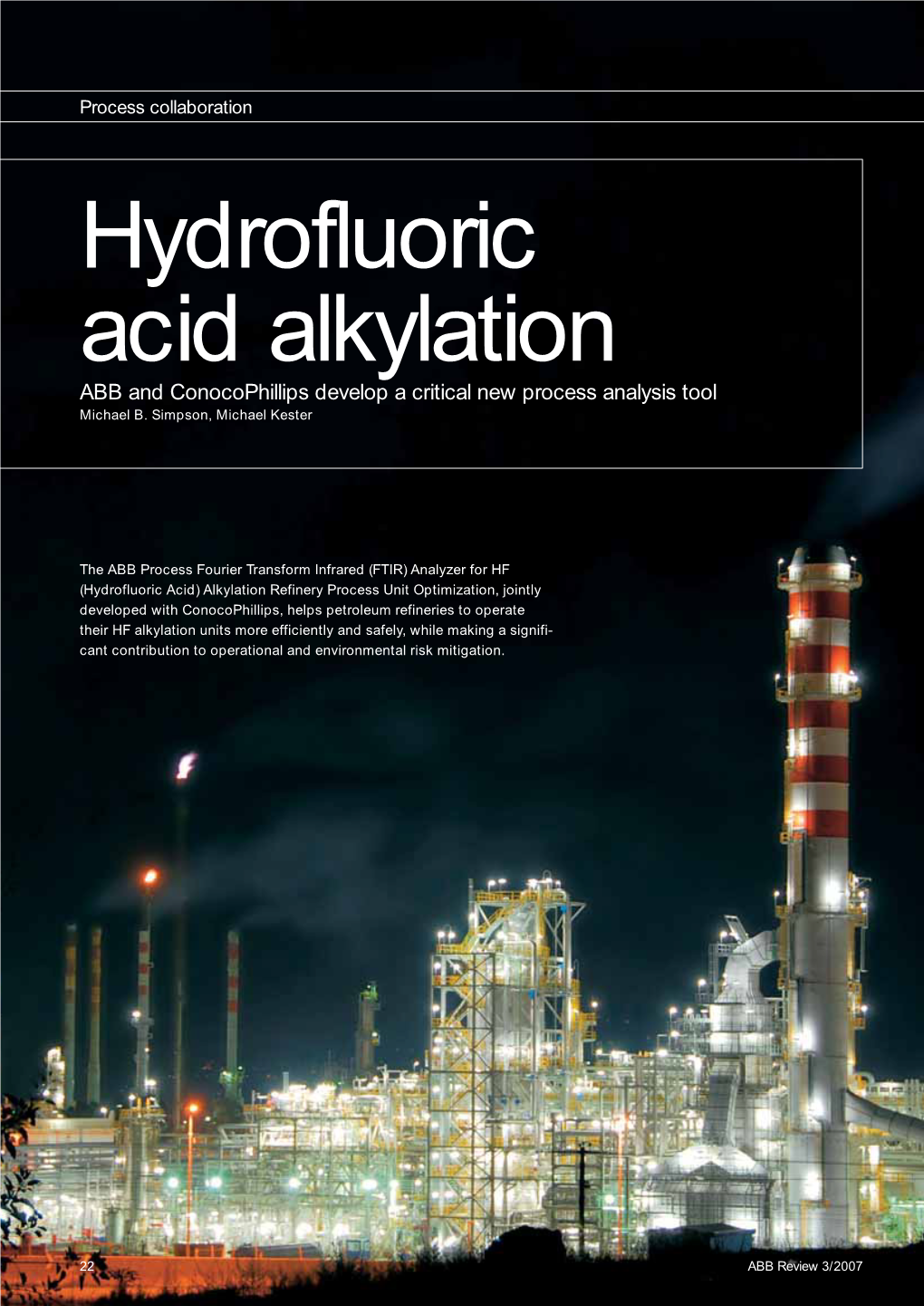
Load more
Recommended publications
-
APPENDIX M SUMMARY of MAJOR TYPES of Carfg2 REFINERY
APPENDIX M SUMMARY OF MAJOR TYPES OF CaRFG2 REFINERY MODIFICATIONS Appendix M: Summan/ of Major Types of CaRFG2 Refinery Modifications: Alkylation Units A process unit that combines small-molecule hydrocarbon gases produced in the FCCU with a branched chain hydrocarbon called isobutane, producing a material called alkylate, which is blended into gasoline to raise the octane rating. Alkylate is a high octane, low vapor pressure gasoline blending component that essentially contains no olefins, aromatics, or sulfur. This plant improves the ultimate gasoline-making ability of the FCC plant. Therefore, many California refineries built new or modified existing units to increase alkylate production to blend and to produce greater amounts of CaRFG2. Alkylate is produced by combining C3, C4, and C5 components with isobutane (nC4). The process of alkylation is the reverse of cracking. Olefins (such as butenes and propenes) and isobutane are used as feedstocks and combined to produce alkylate. This process enables refiners to utilize lighter components that otherwise could not be blended into gasoline due to their high vapor pressures. Feed to alkylation unit can include pentanes from light cracked gasoline treaters, isobutanes from butane isomerization unit, and C3/C4 streams from delayed coking units. Isomerization Units - C4/C5/C6 A refinery that has an alkylation plant is not likely to have exactly enough is-butane to match the proplylene and butylene (olefin) feeds. The refiner usually has two choices - buy iso-butane or make it in a butane isomerization (Bl) plant. Isomerization is the rearrangement of straight chain hydrocarbon molecules to form branched chain products or to convert normal paraffins to their isomer. -
Olefins Recovery CRYO–PLUS ™ TECHNOLOGY 02
Olefins Recovery CRYO–PLUS ™ TECHNOLOGY 02 Refining & petrochemical experience. Linde Engineering North America Inc. (LENA) has constructed more than twenty (20) CRYO-PLUS™ units since 1984. Proprietary technology. Higher recovery with less energy. Refinery configuration. Designed to be used in low-pressure hydrogen-bearing Some of the principal crude oil conversion processes are off-gas applications, the patented CRYO-PLUS™ process fluid catalytic cracking and catalytic reforming. Both recovers approximately 98% of the propylene and heavier processes convert crude products (naphtha and gas oils) components with less energy required than traditional into high-octane unleaded gasoline blending components liquid recovery processes. (reformate and FCC gasoline). Cracking and reforming processes produce large quantities of both saturated and Higher product yields. unsaturated gases. The resulting incremental recovery of the olefins such as propylene and butylene by the CRYO-PLUS™ process means Excess fuel gas in refineries. that more feedstock is available for alkylation and polym- The additional gas that is produced overloads refinery erization. The result is an overall increase in production of gas recovery processes. As a result, large quantities of high-octane, zero sulfur, gasoline. propylene and propane (C3’s), and butylenes and butanes (C4’s) are being lost to the fuel system. Many refineries Our advanced design for ethylene recovery. produce more fuel gas than they use and flaring of the ™ The CRYO-PLUS C2= technology was specifically excess gas is all too frequently the result. designed to recover ethylene and heavier hydrocarbons from low-pressure hydrogen-bearing refinery off-gas streams. Our patented design has eliminated many of the problems associated with technologies that predate the CRYO-PLUS C2=™ technology. -
Burton Introduces Thermal Cracking for Refining Petroleum John Alfred Heitmann University of Dayton, [email protected]
University of Dayton eCommons History Faculty Publications Department of History 1991 Burton Introduces Thermal Cracking for Refining Petroleum John Alfred Heitmann University of Dayton, [email protected] Follow this and additional works at: https://ecommons.udayton.edu/hst_fac_pub Part of the History Commons eCommons Citation Heitmann, John Alfred, "Burton Introduces Thermal Cracking for Refining Petroleum" (1991). History Faculty Publications. 92. https://ecommons.udayton.edu/hst_fac_pub/92 This Encyclopedia Entry is brought to you for free and open access by the Department of History at eCommons. It has been accepted for inclusion in History Faculty Publications by an authorized administrator of eCommons. For more information, please contact [email protected], [email protected]. 573 BURTON INTRODUCES THERMAL CRACKING FOR REFINING PETROLEUM Category of event: Chemistry Time: January, 1913 Locale: Whiting, Indiana Employing high temperatures and pressures, Burton developed a large-scale chem ical cracking process, thus pioneering a method that met the need for more fuel Principal personages: WILLIAM MERRIAM BURTON (1865-1954), a chemist who developed a commercial method to convert high boiling petroleum fractions to gas oline by "cracking" large organic molecules into more useful and marketable smaller units ROBERT E. HUMPHREYS, a chemist who collaborated with Burton WILLIAM F. RODGERS, a chemist who collaborated with Burton EUGENE HOUDRY, an industrial scientist who developed a procedure us ing catalysts to speed the conversion process, which resulted in high octane gasoline Summary of Event In January, 1913, William Merriam Burton saw the first battery of twelve stills used in the thermal cracking of petroleum products go into operation at Standard Oil of Indiana's Whiting refinery. -
Providing a Guide
Lydia Miller, Emerson Automation Solutions, USA, explores how guided wave radar instruments can help a refinery make accurate level measurements in a corrosive environment. he alkylation process has long been an important The first two product streams come out of the main technique for refiners to create economical fractionator and are sent on for additional refinement. The gasoline blending components capable of raising propane is part of a mixed stream coming out of the acid the octane rating. There are two main process settler, also containing unrecovered HF and unreacted Tapproaches that are distinguished from one another by isobutane. This stream is sent to a de-propanising stage, their catalyst, either sulfuric acid or hydrofluoric acid (HF). which is effectively a large trayed distillation column, Both approaches take lighter components – primarily where propane is separated from the liquid and sent on for isobutane and olefins (various low-molecular-weight purification. The liquid stream is recycled back to the alkenes) – and, using one of the acids as a catalyst, convert original reactor and mixed with fresh feedstocks. The them to alkylate, which can be added to gasoline. highest possible degree of separation is desirable because This octane booster can be used year-round as it does when the propane is sold as a product it must not have HF not cause vapour pressure problems that are common to residues, and returning propane to the reactor reduces its alternative additives. Both processes were developed efficiency. during World War II to help increase the supply of high-octane aviation fuel available to allied air forces, and The de-propanising tower both have been in use ever since. -
Optimization of Refining Alkylation Process Unit Using Response
Optimization of Refining Alkylation Process Unit using Response Surface Methods By Jose Bird, Darryl Seillier, Michael Teders, and Grant Jacobson - Valero Energy Corporation Abstract This paper illustrates a methodology to optimize the operations of an alkylation unit based on response surface methods. Trial based process optimization requires the unit to be operated across a wide range of conditions. This approach tends to be opposed by refinery operations as it can disrupt the normal operations of a process unit. Using the methods presented in this paper, the general direction of process improvement is first identified using a first order profit response surface built from available operating data. The performance of the unit is then evaluated at the refinery by making systematic changes to the key factors in the projected direction of process improvement. The operating results are then used to build a localized second order profit response surface to generate a revised set of optimum targets. Multiple linear regression models are used to predict alkylate yield, alkylate octane and Iso-stripper or De-Isobutanizer reboiler duty as a function of key process variables. These models are then used to generate a profit response surface for selection of an optimum target region for step testing at the refinery prior to implementation of the unit targets. 1. Introduction An alkylation unit takes a feed stream with a high olefin content, typically originating from a fluid catalytic cracking (FCC) unit, and adds isobutane (IC4) which reacts with the olefins to produce a high octane alkylate product. Either hydrofluoric or sulfuric acid is used as a catalyst for the alkylation reaction. -
Modeling the HF Alkylation Chemistry Contents
think simulation | getting the chemistry right Modeling the HF alkylation chemistry An OLI Joint Industry Project (JIP) beginning April 2019 Contents Corrosion in the HF alkylation process ............................................................................................................ 2 Current modeling challenge ............................................................................................................................ 2 OLI Systems framework .................................................................................................................................. 2 Proposed Joint Industry Project (JIP) ............................................................................................................... 3 Project approach ............................................................................................................................................ 3 Project feasibility ............................................................................................................................................ 4 Pricing and deliverables ................................................................................................................................. 4 JIP details ....................................................................................................................................................... 5 Why choose OLI? .......................................................................................................................................... -
Alkylation: a Key to Cleaner Fuels and Better Vehicle Mileage
Alkylation A Key to Cleaner Gasoline & Better Vehicle Mileage American Fuel & Petrochemical Manufacturers (AFPM) is the leading trade association representing the majority of U.S. refining and petrochemical manufacturing capacity. Our members produce the fuels that power the U.S. economy and the chemical building blocks integral to millions of products that make modern life possible. U.S. gasoline needs alkylate for (OSHA) Process Safety Management and projects to transition from HF to Refineries that are close to chemical facil- its octane and environmental program and the Environmental even newer alkylation technologies are ities may have the option of selling their properties Protection Agency’s (EPA) Risk still in early phases. Eliminating the use propylene and butylene as feedstocks America’s fuel refiners use a chemical Management Program. But refineries that of either HF or sulfuric acid technology to manufacture plastics and sanitizers. process called alkylation to produce use HF go even further. Because nothing would severely diminish U.S. capacity to For refineries without this option, HF Refinery alkylation alkylate, a component of the cleaner is more important to the refining industry manufacture cleaner gasoline in line with alkylation technology provides an answer Alkylation is a refinery gasoline required by today’s higher- than the safety of our people and consumer demand. where sulfuric acid technology does not. is subject to layers process essential to the efficiency automobiles. Nearly 90 U.S. communities, facilities with HF alkylation HF units can co-process both propylene of regulation and refineries — representing 90% of total U.S. units also adhere to exacting industry and butylene to make alkylate. -
Study of Selected Petroleum Refining Residuals
STUDY OF SELECTED PETROLEUM REFINING RESIDUALS INDUSTRY STUDY Part 1 August 1996 U.S. ENVIRONMENTAL PROTECTION AGENCY Office of Solid Waste Hazardous Waste Identification Division 401 M Street, SW Washington, DC 20460 TABLE OF CONTENTS Page Number 1.0 INTRODUCTION .................................................... 1 1.1 BACKGROUND ............................................... 1 1.2 OTHER EPA REGULATORY PROGRAMS IMPACTING THE PETROLEUM REFINING INDUSTRY ............................. 2 1.3 INDUSTRY STUDY FINDINGS .................................. 3 2.0 INDUSTRY DESCRIPTION ........................................... 8 2.1 PETROLEUM REFINING INDUSTRY PROFILE ..................... 8 2.2 INDUSTRY STUDY ........................................... 10 2.2.1 Site Selection ......................................... 11 2.2.2 Engineering Site Visits .................................. 13 2.2.3 RCRA §3007 Questionnaire .............................. 13 2.2.4 Familiarization Sampling ................................ 14 2.2.5 Record Sampling ....................................... 15 2.2.6 Split Samples Analyzed by API ........................... 20 2.2.7 Synthesis ............................................. 20 3.0 PROCESS AND WASTE DESCRIPTIONS ............................... 21 3.1 REFINERY PROCESS OVERVIEW .............................. 21 3.2 CRUDE OIL DESALTING ...................................... 25 3.2.1 Process Description ..................................... 25 3.2.2 Desalting Sludge ....................................... 26 3.3 HYDROCRACKING -
Invention and Innovation in the Petroleum Refining Industry
This PDF is a selection from an out-of-print volume from the National Bureau of Economic Research Volume Title: The Rate and Direction of Inventive Activity: Economic and Social Factors Volume Author/Editor: Universities-National Bureau Committee for Economic Research, Committee on Economic Growth of the Social Science Research Council Volume Publisher: Princeton University Press Volume ISBN: 0-87014-304-2 Volume URL: http://www.nber.org/books/univ62-1 Publication Date: 1962 Chapter Title: Invention and Innovation in the Petroleum Refining Industry Chapter Author: John L. Enos Chapter URL: http://www.nber.org/chapters/c2124 Chapter pages in book: (p. 299 - 322) Invention and Innovation in the Petroleum Refining Industry JOHN L. ENOS MASSACHUSETTS INSTITUTE OF TECHNOLOGY AN INNOVATION is the combination of many different activities. Gener- ally an invention is made and recognized, capital is obtained, plant is acquired, managers and workers are hired, markets are developed, and production and distribution take place. As the innovation proceeds the original conception may be altered to make it more amenable to commercial realities. Accomplishing these activities consumes re- sources. At any point in the sequence failure may occur, delaying or even frustrating the innovation. In studying the petroleum refining industry I observed several pro- cessing innovations following one another in time and generating technological progress.' I then sought their origins in terms of the original ideas and the men who conceived them. In this paper I shall discuss the relations between the inventions and the subsequent inno- vations, focusing on the intervals between them, the returns to the inventors and innovators, and the changes in the proportions in which the factors of production in petroleum processing were combined. -
In a Refinery, the Fluid Catalytic Cracking Unit (FCCU)
Bonnie Crossland, Emerson Automation To ensure optimum operation of the FCC and the VRU, real time compositional data to process control systems is Solutions, USA, considers how gas required and the process gas chromatograph (GC) is the chromatograph technology can be used analytical workhorse for online compositional measurement in refineries. While other technologies, such to optimise fluid catalytic cracking. as mass spectrometry or process gas analysers, can be considered in most refineries, GCs offer a balance of n a refinery, the fluid catalytic cracking unit (FCCU) is accuracy, process appropriate speed, ease of use, reliability one of the most important processes for converting low and cost-effectiveness. While most refinery personnel value heavy oils into valuable gasoline and lighter accept GC technology as an excellent measurement product. More than half of the refinery’s heavy solution for the FCCU and VRU, it bears an explanation of Ipetroleum goes through the FCCU for processing. how GC measurement points provide essential information Consequently, efficient operation of the FCCU directly for efficient refinery operation. impacts the refinery’s profitability. The valuable light gases produced by the catalytic process are sent to a vapour FCCU recovery unit (VRU). VRUs are an important source of As a review, it is important to know that the feed to the butane and pentane olefins, which are used as feed in FCCU in a refinery is the heavy gas oils from the crude unit refinery processes such as the alkylation unit. The alkylation as well as vacuum gas oils from the vacuum crude unit. The unit then converts the olefins to high octane products. -
Environmental, Health, and Safety Guidelines for Petroleum Refining
ENVIRONMENTAL, HEALTH, AND SAFETY GUIDELINES PETROLEUM REFINING November 17, 2016 ENVIRONMENTAL, HEALTH, AND SAFETY GUIDELINES FOR PETROLEUM REFINING INTRODUCTION 1. The Environmental, Health, and Safety (EHS) Guidelines are technical reference documents with general and industry-specific examples of Good International Industry Practice (GIIP).1 When one or more members of the World Bank Group are involved in a project, these EHS Guidelines are applied as required by their respective policies and standards. These industry sector EHS Guidelines are designed to be used together with the General EHS Guidelines document, which provides guidance to users on common EHS issues potentially applicable to all industry sectors. For complex projects, use of multiple industry sector guidelines may be necessary. A complete list of industry sector guidelines can be found at: www.ifc.org/ehsguidelines. 2. The EHS Guidelines contain the performance levels and measures that are generally considered to be achievable in new facilities by existing technology at reasonable costs. Application of the EHS Guidelines to existing facilities may involve the establishment of site-specific targets, with an appropriate timetable for achieving them. 3. The applicability of the EHS Guidelines should be tailored to the hazards and risks established for each project on the basis of the results of an environmental assessment in which site-specific variables— such as host country context, assimilative capacity of the environment, and other project factors—are taken into account. The applicability of specific technical recommendations should be based on the professional opinion of qualified and experienced persons. 4. When host country regulations differ from the levels and measures presented in the EHS Guidelines, projects are expected to achieve whichever is more stringent. -
Cracking (Chemistry)
Cracking (chemistry) In petrochemistry, petroleum geology and organic chemistry, cracking is the process whereby complex organic molecules such as kerogens or long-chain hydrocarbons are broken down into simpler molecules such as light hydrocarbons, by the breaking of carbon-carbon bonds in the precursors. The rate of cracking and the end products are strongly dependent on the temperature and presence of catalysts. Cracking is the breakdown of a large alkane into smaller, more useful alkenes. Simply put, hydrocarbon cracking is the process of breaking a long chain of hydrocarbons into short ones. This process requires high temperatures.[1] More loosely, outside the field of petroleum chemistry, the term "cracking" is used to describe any type of splitting of molecules under the influence of heat, catalysts and solvents, such as in processes of destructive distillation or pyrolysis. Fluid catalytic cracking produces a high yield of petrol and LPG, while hydrocracking is a major source of jet fuel, Diesel fuel, naphtha, and again yields LPG. Contents History and patents Cracking methodologies Thermal cracking Steam cracking Fluid Catalytic cracking Hydrocracking Fundamentals See also Refinery using the Shukhov cracking References process, Baku, Soviet Union, 1934. External links History and patents Among several variants of thermal cracking methods (variously known as the "Shukhov cracking process", "Burton cracking process", "Burton-Humphreys cracking process", and "Dubbs cracking process") Vladimir Shukhov, a Russian engineer, invented and patented the first in 1891 (Russian Empire, patent no. 12926, November 7, 1891).[2] One installation was used to a limited extent in Russia, but development was not followed up. In the first decade of the 20th century the American engineers William Merriam Burton and Robert E.