Appendix C Health and Safety Plan /Community Air Monitoring Plan
Total Page:16
File Type:pdf, Size:1020Kb
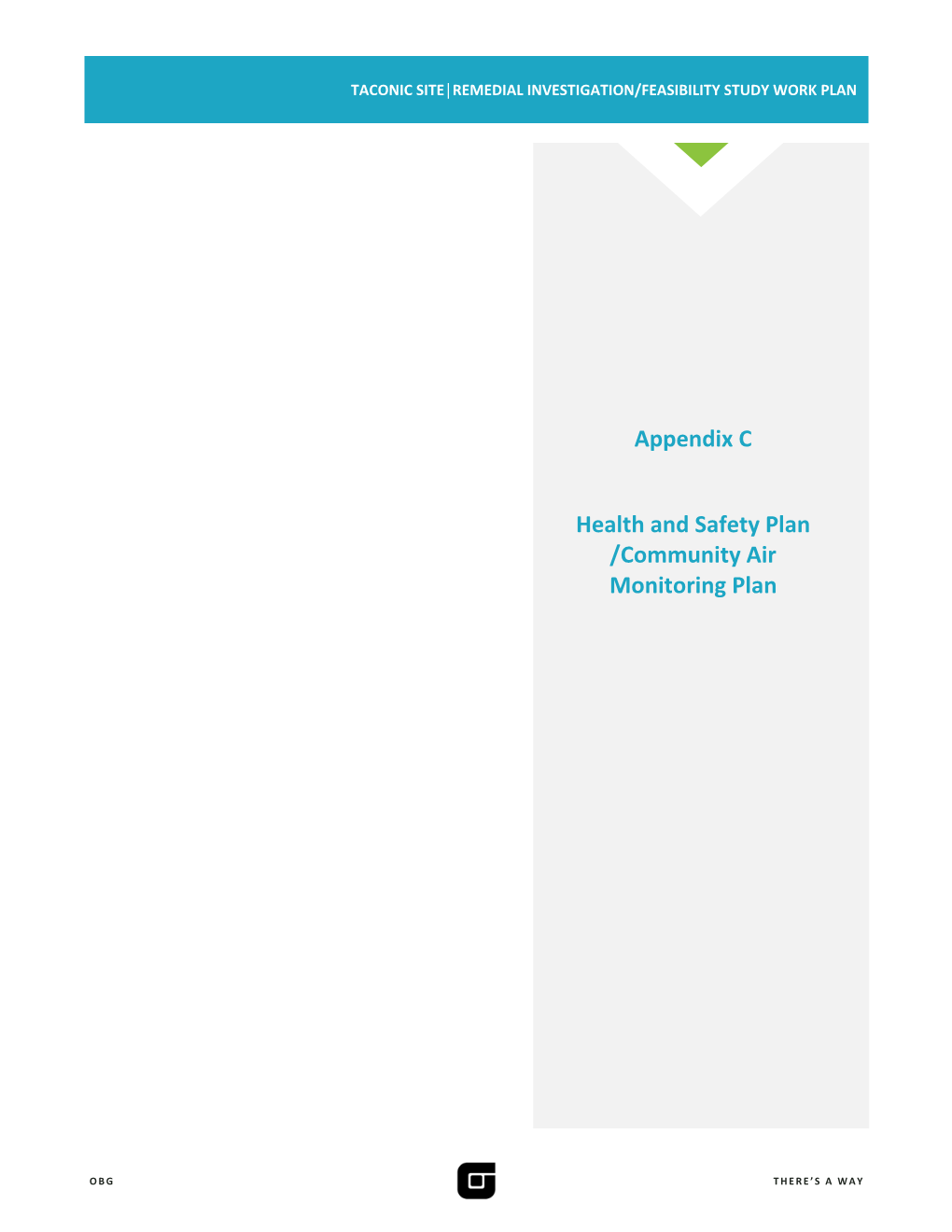
Load more
Recommended publications
-
Proposed Local Law # 1 of 2020
SCOZ Incorporation in the Town of Ancram Zoning Law of November 2014 LOCAL LAW NO. 1 OF THE'YEAR 2020 A Local Law amending Article V of the Town of Ancram Zoning Law to incorporate the supplementary regulations for the Town’s Scenic Corridor Overlay Zoning District from Local Law No. 1 of 2003 and repealing Local Law No. 1 of 2003. Be it enacted by the Town Board of the Town of Ancram, Columbia County, New York, as follows: SECTION I - TITLE OF LOCAL LAW This law shall be entitled “A Local Law proposing an amendment to Article V of the Town of Ancram Zoning Law to incorporate the supplementary regulations for the Town’s Scenic Corridor Overlay Zoning District from Local Law No. 1 of 2003, and then repeal Local Law No. 1 of 2003.” SECTION II - LEGISLATIVE PURPOSE Subsequent to the adoption of the 2010 Town of Ancram Comprehensive Plan, the Town Board of the Town of Ancram updated and adopted a new Zoning Law on November 20, 2014. The 2014 Zoning Law included establishment and definition of a zoning district called the Scenic Corridor Overlay Zone, which was previously established by Town of Ancram Local Law 1 of 2003. The purpose of the amendment proposed in this resolution is to incorporate into the Town’s Zoning Law adopted on November 20, 2014 the provisions of Local Law No. 1 of 2003 which Local Law established supplementary regulations for a zoning district called the Scenic Corridor Overlay Zone. Those supplementary regulations were not incorporated into the Town’s Zoning Law when it was adopted in 2014. -
2007 Traffic Data Report for New York State
2007 TRAFFIC DATA REPORT FOR NEW YORK STATE New York State Department of Transportation Table of Contents Page Chapter 1: Introduction.........................................................................................................1 Chapter 2: Traffic Data Collecting Program Overview........................................................2 Chapter 3: Accuracy of Traffic Data Section 3.1 Data Collection Equipment Requirements.............................................3 Section 3.2 Data Quality Control Checks.................................................................4 Chapter 4: Continuous Count Program Section 4.1 Introduction............................................................................................7 Section 4.2 Maps of Continuous Count Sites by Region..........................................8 Section 4.3 Map of High Speed Weigh-In-Motion Sites, Statewide .......................19 Section 4.4 Traffic Monitoring Site Details and Specifications ..............................20 Chapter 5: Coverage Count Program Section 5.1 Volume, Speed and Classification Counts............................................21 Section 5.2 Highway Performance Monitoring System ..........................................24 Section 5.3 Annual Traffic Monitoring Workshop..................................................24 Section 5.4 Mobile Traffic Monitoring Platforms ...................................................25 Section 5.5 County Counter Initiative .....................................................................26 -
Chapter 1: Background and Planning Context
Chapter 1: Background and Planning Context 1.1 INTRODUCTION Metro-North Commuter Railroad Company (“Metro-North” or the “Project Sponsor”) is proposing the construction of a new, expanded parking garage at 50 Haarlem Avenue (formerly referred to as 525 North Broadway) in White Plains, Westchester County, New York. The Project Sponsor is seeking a Congestion Mitigation and Air Quality (CMAQ) grant from the Federal Transit Administration for the design and construction of the proposed garage (the “Proposed Action”). The purpose of the Proposed Action is to accommodate the projected future demand for parking at the North White Plains railroad station, allowing Metro-North to better serve its existing customers and to accommodate future railroad customers. The provision of adequate parking at this location would encourage the use of mass transit at a station that has frequent service. 1.2 PROJECT LOCATION The Proposed Action is located on the site of the existing customer parking garage at 50 Haarlem Avenue between Glenn and Bond Streets in the City of White Plains. It would be sited to the east and across Haarlem Avenue from the existing North White Plains station (see Figure 1-1). 1.2.1 EXISTING STATION The North White Plains railroad station is located along Metro-North’s Harlem Line on Haarlem Avenue west of New York State Route 22 (Route 22) and east of the Bronx River Parkway, about ¼ mile north of Interstate 287 (I-287), in the northern section of the City of White Plains, Westchester County, New York (see Figure 1-2). The station is located near the municipal boundaries of the City of White Plains and the Towns of North Castle and Greenburgh. -
May 25, 2013 Karen Thornton, American Viticultural Area
May 25, 2013 Karen Thornton, American Viticultural Area Designations Regulations and Rulings Division Alcohol and Tobacco Tax and Trade Bureau 1310 G Street NW Washington DC, 20220 [email protected] Dear Ms. Thornton, Please find included here a revised petition for the declaration of a new American Viticultural Area, entitled the Champlain Valley AVA. This petition was created on behalf of the Lake Champlain Grape Growers Association. I previously included an endorsement from our local congressional representative, Bill Owens, whose interest is in the economic development of this region and through his participation as a member of the House Agricultural Committee. Finally, I include a set of USGS maps that define the trail. I believe I have addressed the items you have requested in this revise and resubmit. Most importantly, I provided extensive climatological data to show how this region is differentiated from the Adirondack and western foothills region to the west, the Hudson Valley to the south, and Vermont to the east. Each of these regions has a growing season averaging two weeks longer than we do, and hence can grow the Vitis vinifera grapes that cannot be grown in this proposed region. Hence, the characteristic of grapes in the proposed region is almost exclusively North American hybrid. It is this factor that most profoundly defines and differentiates our proposed region. Should you need any additional information, please do not hesitate to contact me. Best regards, Colin Read North Star Vineyard 1383 North Star Road, Mooers, NY, 12958 Telephone 518-561-3828 Email [email protected] Regulations and Rulings Division Alcohol and Tobacco Tax and Trade Bureau 1310 G Street NW Washington DC, 20220 A Petition to the Alcohol and Tobacco Tax and Trade Bureau of the Department of the Treasury to Establish the: Champlain Valley AVA (American Viticultural Area) Submitted by: An Association of Wineries in the Champlain Valley of New York State (1)Name Evidence [i] Name Usage The name of the viticultural area described is the Champlain Valley of New York. -
Pavement Preservation Program 2015-2016 Project Solicitation
Adirondack / Glens Falls Transportation Council Pavement Preservation Program 2015‐2016 Project Solicitation Introduction The Adirondack / Glens Falls Transportation Council is the Metropolitan Planning Organization (MPO) for the Planning and Programming Area that includes Warren County, Washington County, and the Town of Moreau and Village of South Glens Falls In Saratoga County. MPOs are responsible for administering a cooperative and continuing regional transportation planning process. A principal component of that process is capital programming for federally‐ funded transportation improvement projects. A/GFTC is seeking project candidates for its Pavement Preservation Program. This program consists of annual funding setasides dedicated for maintenance and preservation projects intended to prevent the deterioration of roadways that are presently in good to fair condition. The intent of the program is to encourage municipalities to actively engage in preventative maintenance strategies that reduce the need for more costly infrastructure replacement and major rehabilitation projects. Programming Levels A/GFTC has programmed $1,591,000 in matched federal Surface Transportation Program funds for pavement preservation projects that are to be obligated during Federal Fiscal Year (FFY) 2015‐2016. Additionally, $164,000 in matched funds has been programmed for FFY 2014‐2015 for any required design associated with the selected projects. A local match of 20% is required in order to access design and construction funds. The potential availability of Marchiselli funding, a State program that covers 75% of the required local match for federal aid transportation projects, could reduce the required local match to 5% of the overall project cost. Eligible Roadways All projects must be sponsored by a local municipality (Village, City, Town or County). -
Zoning Law, Amended 2020
TOWN OF ANCRAM Zoning Law Adopted November 20, 2014 Amended November 19, 2020 November 2020 Article I. Title and Scope ......................................................................................... 7 A. Title. ............................................................................................................................................... 7 B. Enactment and Authority. ............................................................................................................. 7 C. Scope. ............................................................................................................................................. 7 D. Purposes. ....................................................................................................................................... 7 E. Supersession of Inconsistent Laws. .............................................................................................. 8 F. Repeal and Replacement of Prior Zoning Law. ........................................................................... 8 Article II. Districts ................................................................................................. 8 A. Names of Zoning Districts. ........................................................................................................... 8 B. District Purposes. .......................................................................................................................... 9 C. Zoning Maps. .............................................................................................................................. -
Amending the Comprehensive Plan
New York State Department of State Local Law Filin; 41 State Street, Albany, NY 12231 (Use this form to file a local law with the Secretary of State.) Text of law should be given as amended. Do not include matter being eliminated and do not use italics or underlining to indicate new matter. County City of Hillsdale Town Village Local Law No. 1 of the year 2012 A local law Amenduig the Town of Hillsdale Comprehensive Plan. (Insert Title) Be it enacted by the Town Board of the County City of Hillsdale as follows: Town Village Section 1 Authorization. The Town of Hillsdale Comprehensive Plan is amended, in its entirety to read as follows: TOWN OF HILLSDALE COMPREHENSIVE PLAN INTRODUCTION The purpose of a town comprehensive plan is to provide a coherent vision of the future based upon the desires of the people of the town. The most important part of this vision is a statement of goals describing the t)'pes of development that are needed and the natural, scenic, and cultural resources that should be preserved. Under New York State law, zoning laws must be wTitten in a manner that is consistent with a comprehensive plan for the communit)'. A comprehensive plan does not commit the Town to any specific course of action. The goals expressed in the comprehensive plan may be implemented in many different ways. It is the comprehensive plan's purpose to oufline what the communit}' would like its future to be. The zoning law strikes the balance between these common goals and the rights and interests of individual property' owners. -
Wetland Permit Application
ARCADIS U.S., Inc. 2 Executive Drive Suite 303 Chelmsford Massachusetts 01824 New York State Department of Environmental Conservation Tel 978 937 9999 625 Broadway Fax 978 937 7555 Albany, NY 12233-4500 www.arcadis-us.com Attn: Stephen Tomasik United States Army Corps of Engineers New York District 26 Federal Plaza ENVIRONMENTAL New York, NY 10278-0090 Attn: Steve Ryba, Regulatory Branch, Room 1937 Subject: Date: Cricket Valley Energy Project, Dover, New York (Army Corps #2009-1043) April 7, 2011 Contact: Dear Mr. Tomasik and Mr. Ryba: Frederick M. Sellars On January 22, 2010, ARCADIS submitted a Joint Application Form and supporting Phone: information requesting authorization of wetland alteration associated with the Cricket 978-937-9999 Valley Energy (CVE) project in Dover, Dutchess County, New York. Since that time, Email: CVE has continued to refine project elements in response to NYSDEC and USACE [email protected] comments to further mitigate wetland impacts resulting from the CVE project. Our ref: This letter provides an update to the previously submitted information and highlights CO001447 those elements that have been changed since the January 22, 2010 submittal. The following includes a brief project description, a summary of wetland jurisdiction status, a review of alternatives considered to avoid and minimize wetland impacts (with revised graphics to better highlight the wetland areas avoided), and a discussion of proposed project activities, including a proposed wetland restoration/creation and adjacent area restoration plan. CVE previously submitted a copy of the Wetland Delineation report, which includes representative photographs and background, as well as a copy of the Environmental Assessment Form that was submitted on November 4, 2009. -
Minutes (Link Is External)
RESOLUTION LEWISBORO PLANNING BOARD NEGATIVE DECLARATION OF SIGNIFICANCE WILDER BALTER PARTNERS, INC. Sheet 5, Block 10766, Lots 19, 20 and 21 Cal. # 12-10 P.B. December 20, 2016 WHEREAS, \Xi'ilder Balter Partners, Inc. (''WBP'') proposes a 46-unit multifamily residential development comprised of five (5) buildings, a clubhouse, recreational facilities, an access road off of New York State Route 22, on-site parking for 92 vehicles and stormwater management (the "proposed action") on ±35.4 acres of land located on the east side of New York State Route 22 north of the 1-684 northbound exit (Exit 6A) ramp; and WHEREAS, the proposed action is to be sited on property consisting of three (3) tax parcels identified on the Tax Map of the Town of Lewisboro as Sheet 5, Block 10776, Lots 19,20 & 21 ("the subject property"), which is currend,' undeveloped and vacant; and WHEREAS, WBP has applied to the Planning Board for Site Development Plan Approval, and the issuance of a Wetland Activity Permit and Town Stormwater Permit, authorizing the proposed action on the subject property; and WHEREAS, the proposed action is an Unlisted Action under the State Environmental Review Act ("SEQRA"); and WHEREAS, a coordinated review of the propost J action is underway and the Planning Board is serving as SEQRA Lead Agency for purposes of this review; and WHEREAS, the Planning Board has received and reviewed application plans and materials, submissions, reports and verbal commentary from WBP and its consultants, submissions, comment letters and verbal commentary -
Environmental Impacts Associated with Preferred Alternatives
Champlain Hudson Power Express Project Assessment of Environmental Impacts Associated with Preferred Alternatives Appendix G TABLE OF CONTENTS 1.1 INTRODUCTION......................................................................................................... 1 1.1.1 Background ......................................................................................................... 1 1.1.2 Construction Methods ......................................................................................... 4 1.2 PUTNAM STATION PREFERRED ALTERNATIVE ............................................ 4 1.2.1 Land Use ............................................................................................................. 5 1.2.2 Vegetation and Natural Communities ................................................................. 9 1.2.3 Wetlands and Water Resources .......................................................................... 9 1.2.4 Historic and Archaeological Resources ............................................................ 10 1.2.5 Conclusions ....................................................................................................... 11 1.3 FORT ANN PREFERRED ALTERNATIVE .......................................................... 11 1.3.1 Land Use ........................................................................................................... 13 1.3.2 Vegetation and Natural Communities ............................................................... 15 1.3.3 Wetlands and Water Resources ....................................................................... -
Public Statement Hearing Notice
STATE OF NEW YORK PUBLIC SERVICE COMMISSION At a session of the Public Service Commission held in the City of Albany on February 13, 2013 COMMISSIONERS PRESENT: Garry A. Brown, Chairman Patricia L. Acampora Maureen F. Harris James L. Larocca Gregg C. Sayre CASE 11-E-0593 – Petition of Cricket Valley Energy Center, LLC for an Original Certificate of Public Convenience and Necessity and for an Order Providing for Lightened Regulation. ORDER GRANTING CERTIFICATE OF PUBLIC CONVENIENCE AND NECESSITY AND ESTABLISHING LIGHTENED RATEMAKING REGULATION (Issued and Effective February 14, 2013) BY THE COMMISSION: INTRODUCTION In this order, the Commission grants a Certificate of Public Convenience and Necessity (certificate or CPCN) to Cricket Valley Energy Center, LLC (Cricket Valley) for the construction of a combined cycle, natural gas-powered 1,000 megawatt (MW) electric generating facility on an inactive industrial site located in the Town of Dover, Dutchess County, New York (facility or project). The Commission also grants applicant’s motion for an expedited proceeding pursuant to 16 NYCRR 21.10 and approves a lightened regulatory regime for the new facility. The new facility is expected to provide cost effective electricity with lower emissions than many existing generation facilities. The facility may also act as a replacement for generation forced to retire due to environmental CASE 11-E-0593 or other regulatory factors. Further, the facility is expected to provide black-start services and to rehabilitate an inactive industrial site and provide economic growth for Dutchess County and the Town of Dover. NOTICE On November 9, 2011, Cricket Valley published notice of its petition and motion for an expedited proceeding in the Poughkeepsie Journal, a newspaper of general circulation in the vicinity of the project. -
Comp Plan Draft Chapter 2
2. REGIONAL CONTEXT 2.1 TOWN HISTORY apples) and dairy products. From 1850 to 1880, the Town was a center of shoemaking, which ultimately employed some 300 The area that is today the Town of North Castle was originally households in North Castle. In the latter part of the century, settled by the Native American tribe the Siwanoys, who were shoemaking was taken over by factories, and the Town shed part of the Wappinger Confederacy. Europeans began settling much of its population, decreasing from a high of 2,800 during the area around 1640 through a combination of British land the Civil War to 1,200 in 1910 – roughly the size at its founding. grants and the purchase of large parcels from the Native American chiefs. Settlers from the Massachusetts and In the early 20th century, wealthy New York City business people Connecticut areas moved into the eastern part of the area and discovered North Castle as an ideal location for country estates, Quakers from Long Island and nearby Rye, New York, inhabited with its rural setting and rail connection to Manhattan, and the area known today as Armonk. The name “North Castle” these estates provided jobs for local residents. stems from an old Indian fortification that was located on the hill where the IBM corporate headquarters now resides. During the American Revolution, George Washington established his headquarters in 1776, 1778 and 1781 at the Miller House – still located on Virginia Road in North White Plains – and the Battle of White Plains was fought in 1779 in that area. The hills of North Castle created a strategic advantage for the American troops, who would fire down at the British Army.