Catalysts for H2 Production
Total Page:16
File Type:pdf, Size:1020Kb
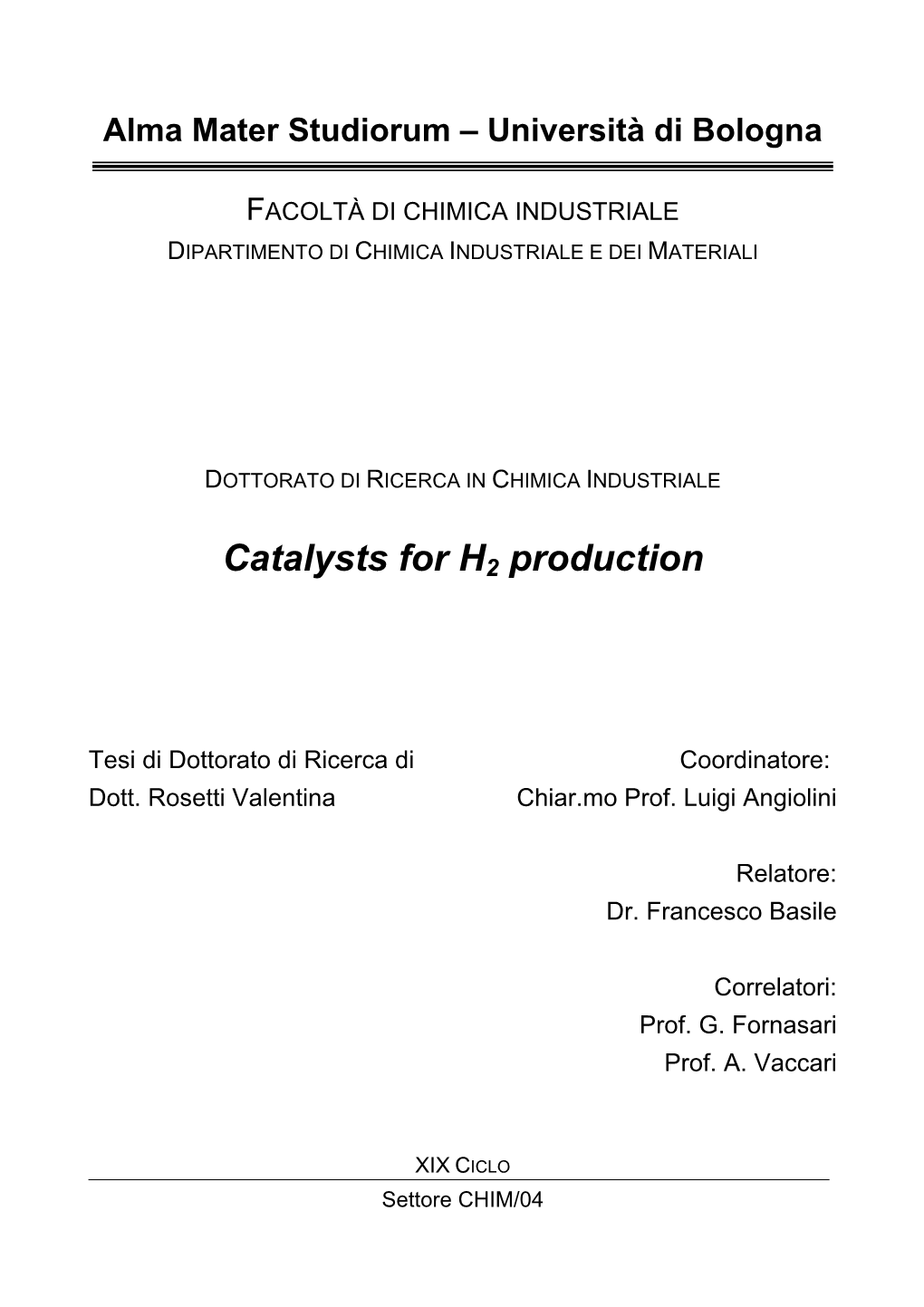
Load more
Recommended publications
-
Zn-Al Mixed Oxides Decorated with Potassium As Catalysts for HT-WGS: Preparation and Properties
catalysts Article Zn-Al Mixed Oxides Decorated with Potassium as Catalysts for HT-WGS: Preparation and Properties Katarzyna Antoniak-Jurak * , Paweł Kowalik, Kamila Michalska, Wiesław Próchniak and Robert Bicki Łukasiewicz Research Network—New Chemical Syntheses Institute, Al. Tysi ˛acleciaPa´nstwa Polskiego 13A, 24-110 Puławy, Poland; [email protected] (P.K.); [email protected] (K.M.); [email protected] (W.P.); [email protected] (R.B.) * Correspondence: [email protected]; Tel.: +48-8-1473-1754 Received: 8 September 2020; Accepted: 18 September 2020; Published: 21 September 2020 Abstract: A set of ex-ZnAl-LDHs catalysts with a molar ratio of Zn/Al in the range of 0.3–1.0 was prepared using co-precipitation and thermal treatment. The samples were characterized using various methods, including X-ray fluorescence spectroscopy (XRF), X-ray photoelectron spectroscopy (XPS), X-ray powder diffraction (XRD), Fourier transform infrared spectroscopy FT-IR, N2 adsorption, Temperature-programmed desorption of CO2 (TPD-CO2) as well as Scanning electron microscopy (SEM-EDS). Catalyst activity and long-term stability measurements were carried out in a high-temperature water–gas shift (HT-WGS) reaction. Mixed oxide catalysts with various Zn/Al molar ratios decorated with potassium showed high activity in the HT-WGS reaction within the temperature range of 330–400 ◦C. The highest activity was found for the Zn/Al molar ratio of 0.5 corresponding to spinel stoichiometry. However, the catalyst with a stoichiometric spinel molar ratio of Zn/Al (ZnAl_0.5_K) revealed a higher tendency for surface migration and/or vaporization of potassium during overheating at 450 ◦C. -
Opportunities for Catalysis in the 21St Century
Opportunities for Catalysis in The 21st Century A Report from the Basic Energy Sciences Advisory Committee BASIC ENERGY SCIENCES ADVISORY COMMITTEE SUBPANEL WORKSHOP REPORT Opportunities for Catalysis in the 21st Century May 14-16, 2002 Workshop Chair Professor J. M. White University of Texas Writing Group Chair Professor John Bercaw California Institute of Technology This page is intentionally left blank. Contents Executive Summary........................................................................................... v A Grand Challenge....................................................................................................... v The Present Opportunity .............................................................................................. v The Importance of Catalysis Science to DOE.............................................................. vi A Recommendation for Increased Federal Investment in Catalysis Research............. vi I. Introduction................................................................................................ 1 A. Background, Structure, and Organization of the Workshop .................................. 1 B. Recent Advances in Experimental and Theoretical Methods ................................ 1 C. The Grand Challenge ............................................................................................. 2 D. Enabling Approaches for Progress in Catalysis ..................................................... 3 E. Consensus Observations and Recommendations.................................................. -
'New Insights on the Selective Oxidation of Methanol to Formaldehyde on Femo Based Catalysts'
‘New Insights on the Selective Oxidation of Methanol to Formaldehyde on FeMo Based Catalysts' Catherine Brookes School of Chemistry Cardiff University Thesis for the degree of Doctor of Philosophy i This thesis was submitted for examination in August 2015. ii Abstract The selective oxidation of methanol has been studied in detail, with particular focus on gaining insights into the surface active sights responsible for directing the selectivity to formaldehyde. Various Fe and Mo containing oxides have been investigated for their reactivity with methanol, to gain an understanding of the different roles of these components in the industrial catalyst employed, which is a mixed phase comprised of MoO 3 and Fe 2(MoO 4)3. Catalysts have primarily been tested through using TPD (temperature programmed desorption) and TPPFR (temperature programmed pulsed flow reaction). The reactivity of Fe 2O3 is dominated by combustion products, with CO 2 and H 2 produced via a formate intermediate adsorbing at the catalyst surface. For MoO 3 however, the surface is populated by methoxy intermediates, so that the selectivity is almost 100 % directed to formaldehyde. When a mixture of isolated Fe and Mo sites co-exist, the surface methoxy becomes stabilised, resulting in a dehydrogenation reaction to CO and H 2. CO and CO 2 can also be observed on Mo rich surfaces, however here a consequence of the further oxidation of formaldehyde, through a linear pathway. TPD and DRIFTS identify these intermediates and products forming. Since the structure of the industrial catalyst is relatively complex, in that it contains both MoO 3 and Fe 2(MoO 4)3, it is difficult to identify the active site for the reaction with methanol. -
Direct Synthesis of Dimethyl Ether from Syngas on Bifunctional Hybrid
catalysts Article Direct Synthesis of Dimethyl Ether from Syngas on Bifunctional Hybrid Catalysts Based on Supported H3PW12O40 and Cu-ZnO(Al): Effect of Heteropolyacid Loading on Hybrid Structure and Catalytic Activity Elena Millán , Noelia Mota, Rut Guil-López, Bárbara Pawelec , José L. García Fierro and Rufino M. Navarro * Instituto de Catálisis y Petroleoquímica (CSIC), C/Marie Curie 2, Cantoblanco, 28049 Madrid, Spain; [email protected] (E.M.); [email protected] (N.M.); [email protected] (R.G.-L.); [email protected] (B.P.); jlgfi[email protected] (J.L.G.F.) * Correspondence: [email protected] Received: 27 August 2020; Accepted: 15 September 2020; Published: 17 September 2020 Abstract: The performance of bifunctional hybrid catalysts based on phosphotungstic acid (H3PW12O40, HPW) supported on TiO2 combined with Cu-ZnO(Al) catalyst in the direct synthesis of dimethyl ether (DME) from syngas has been investigated. We studied the effect of the HPW loading on TiO2 (from 1.4 to 2.7 monolayers) on the dispersion and acid characteristics of the HPW clusters. When the concentration of the heteropoliacid is slightly higher than the monolayer (1.4 monolayers) the acidity of the clusters is perturbed by the surface of titania, while for concentration higher than 1.7 monolayers results in the formation of three-dimensional HPW nanocrystals with acidity similar to the bulk heteropolyacid. Physical hybridization of supported heteropolyacids with the Cu-ZnO(Al) catalyst modifies both the acid characteristics of the supported heteropolyacids and the copper surface area of the Cu-ZnO(Al) catalyst. -
Platinum Metals Industrial Catalysts Catalysis of Organic Reactions EDITED by M
Platinum Metals Industrial Catalysts Catalysis of Organic Reactions EDITED BY M. G. SCAROS AND M. L. PRUNIER, Marcel Dekker, New York, 1995, 599 pages, ISBN 0-8247-9364-1, U.S. $195.00 This book comprises a set of papers presented reactant purity, agitation and poisons are at the 15th Conference on Catalysis of Organic considered. This is followed by a paper detail- Reactions, held in Phoenix, Arizona, in May ing noble metal recovery operations and the var- 1994. It covers a variety of topics, such as het- ious steps involved in the noble metal “loop”. erogeneous catalysis, asymmetric hydrogena- Heterogeneous catalysis in organic synthesis tion, hydrogenation, oxidation, hydroformyla- is discussed by R. L. Augustine and colleagues tion, catalyst design and catalyst characterisation. from Seton Hall University, New Jersey. This One topic which is emphasised is hydrogena- is illustrated by the platinum catalysed oxida- tion (alpha to omega), and this is intended to tion of alcohols, carbon-carbon bond forming allow a better understanding of the entire reactions of supported palladium catalysts for process, from choosing a catalyst to the noble the Heck type arylation of allylic groups, and metal “loop”. There are over 60 papers and 186 by enantioselective heterogeneous catalysis, contributors, with a healthy number of these which includes the hydrogenation of a-ketoesters being from industry. A large proportion of the to chiral a-hydroxyesters using chinchona alka- papers deal with reactions involving platinum loid modified platinum catalysts. group metal catalysts, reflecting their impor- A detailed study of the homogeneously pal- tance to both academia and industry. -
The Unique Interplay Between Copper and Zinc During Catalytic Carbon Dioxide Hydrogenation to Methanol ✉ Maxim Zabilskiy 1 , Vitaly L
ARTICLE https://doi.org/10.1038/s41467-020-16342-1 OPEN The unique interplay between copper and zinc during catalytic carbon dioxide hydrogenation to methanol ✉ Maxim Zabilskiy 1 , Vitaly L. Sushkevich1, Dennis Palagin 1, Mark A. Newton2, Frank Krumeich 2 & ✉ Jeroen A. van Bokhoven 1,2 fi 1234567890():,; In spite of numerous works in the eld of chemical valorization of carbon dioxide into methanol, the nature of high activity of Cu/ZnO catalysts, including the reaction mechanism and the structure of the catalyst active site, remains the subject of intensive debate. By using high-pressure operando techniques: steady-state isotope transient kinetic analysis coupled with infrared spectroscopy, together with time-resolved X-ray absorption spectroscopy and X-ray powder diffraction, and supported by electron microscopy and theoretical modeling, we present direct evidence that zinc formate is the principal observable reactive intermediate, which in the presence of hydrogen converts into methanol. Our results indicate that the copper–zinc alloy undergoes oxidation under reaction conditions into zinc formate, zinc oxide and metallic copper. The intimate contact between zinc and copper phases facilitates zinc formate formation and its hydrogenation by hydrogen to methanol. 1 Laboratory for Catalysis and Sustainable Chemistry, Paul Scherrer Institute, 5232 Villigen, Switzerland. 2 Institute for Chemistry and Bioengineering, ETH ✉ Zurich, Vladimir-Prelog-Weg 1, 8093 Zürich, Switzerland. email: [email protected]; [email protected] NATURE COMMUNICATIONS | (2020) 11:2409 | https://doi.org/10.1038/s41467-020-16342-1 | www.nature.com/naturecommunications 1 ARTICLE NATURE COMMUNICATIONS | https://doi.org/10.1038/s41467-020-16342-1 arbon dioxide is a principal anthropogenic pollutant, ris- catalyst for this highly important and industrially relevant Cing level of which has a detrimental effect on the envir- reaction. -
Heterogeneous Catalyst Deactivation and Regeneration: a Review
Catalysts 2015, 5, 145-269; doi:10.3390/catal5010145 OPEN ACCESS catalysts ISSN 2073-4344 www.mdpi.com/journal/catalysts Review Heterogeneous Catalyst Deactivation and Regeneration: A Review Morris D. Argyle and Calvin H. Bartholomew * Chemical Engineering Department, Brigham Young University, Provo, UT 84602, USA; E-Mail: [email protected] * Author to whom correspondence should be addressed; E-Mail: [email protected]; Tel: +1-801-422-4162, Fax: +1-801-422-0151. Academic Editor: Keith Hohn Received: 30 December 2013 / Accepted: 12 September 2014 / Published: 26 February 2015 Abstract: Deactivation of heterogeneous catalysts is a ubiquitous problem that causes loss of catalytic rate with time. This review on deactivation and regeneration of heterogeneous catalysts classifies deactivation by type (chemical, thermal, and mechanical) and by mechanism (poisoning, fouling, thermal degradation, vapor formation, vapor-solid and solid-solid reactions, and attrition/crushing). The key features and considerations for each of these deactivation types is reviewed in detail with reference to the latest literature reports in these areas. Two case studies on the deactivation mechanisms of catalysts used for cobalt Fischer-Tropsch and selective catalytic reduction are considered to provide additional depth in the topics of sintering, coking, poisoning, and fouling. Regeneration considerations and options are also briefly discussed for each deactivation mechanism. Keywords: heterogeneous catalysis; deactivation; regeneration 1. Introduction Catalyst deactivation, the loss over time of catalytic activity and/or selectivity, is a problem of great and continuing concern in the practice of industrial catalytic processes. Costs to industry for catalyst replacement and process shutdown total billions of dollars per year. Time scales for catalyst deactivation vary considerably; for example, in the case of cracking catalysts, catalyst mortality may be on the order of seconds, while in ammonia synthesis the iron catalyst may last for 5–10 years. -
High Temperature Water Gas Shift Catalysts: a Computer Modelling Study
High Temperature Water Gas Shift Catalysts: A Computer Modelling Study Sreelekha Benny Department of Chemistry University College London Johnson Matthey Technology Centre Thesis submitted for the degree of Doctor in Engineering March 2010 “It's our attitude at the beginning of a difficult undertaking which more than anything else will determine its successful outcome." William James (Father of American psychology) 2 Declaration ____________________________________________________________________ Declaration I, Sreelekha Benny confirm that the work presented in this thesis is the result of my own investigations and where information has been derived from other sources, this has been fully acknowledged. 3 Abstract ____________________________________________________________________ Abstract The high-temperature (HT) Water Gas Shift (WGS) reaction has considerable technological relevance for lowering CO content during the conversion of natural gas or liquid hydrocarbons to hydrogen. Conventional HT-WGS catalysts based on oxides of iron and chromium are well established industrially. However, it is crucial to remove any impurities present such as Cr6+, S or N during the catalytic process. In particular, Cr6+ is regarded as a Class I carcinogen and its presence is restricted by EU legislation. Even though Cr6+ is reduced during the catalytic process, caution must still be taken to eliminate any further impurities. Hence, it is desirable to identify alternative promoters and develop a Cr-free HT-WGS catalyst. This thesis presents results obtained using atomistic simulation techniques to investigate the effect of Cr3+ and possible alternative dopants in three important iron oxide materials, Hematite (α-Fe2O3), Maghemite (γ-Fe2O3) and Magnetite (Fe3O4). The starting point is to develop an understanding of the structural properties and distribution of Cr3+ on the bulk and surface material of hematite. -
Nanostructured Catalysts for Hydrogen Generation From
BESH2015 Sub-Nanometer Sized Clusters for Heterogeneous Catalysis Principal Investigator: Abhaya Datye Organization: University of New Mexico Program Scope Providing sustainable sources of energy, chemicals, and materials is one of the most important long-term issues facing society. Catalysis plays a central role in creating sustainable sources of energy through efficient transformations of hydrocarbon resources. Our quality of life depends on myriad products that involve a catalytic step at some point in their manufacture. It is widely accepted that chemical catalysis is a major economic driver in both the U.S. and world economies, with estimates as high as ~35% of the world’s gross domestic product arising via catalytic processes. Due to this significant commercial impact, there is a heavy demand for rare and expensive transition metals whose pricing and availability is at risk due to increasing geopolitical pressures. As our resource base shifts to alternate energy sources such as natural gas or biomass, there will be a need to develop new catalysts for converting these materials. Our project focuses on sub-nanometer (nm) clusters, of size <30 atoms, which provide unusual reactivity and selectivity for catalytic reactions. The objective of our project is to improve methods to tailor surfaces of high surface area supports to anchor platinum group metals (PGM). Heterogeneous catalysis using nanoparticles of PGMs is highly developed, but the science of using ionic forms of these metals as heterogeneous catalysts is still in its infancy. New methods only recently available allow us to study these atomically dispersed metals. Catalysis using single isolated atoms provides the highest atom efficiency for conducting catalytic reactions. -
1 Introduction
1 1 Introduction 1.1 The Phenomenon Catalysis Catalysis is the key to chemical transformations. Most industrial syntheses and nearly all biological reactions require catalysts. Furthermore, catalysis is the most important technology in environmental protection, i. e., the prevention of emissions. A well-known example is the catalytic converter for automobiles. Catalytic reactions were already used in antiquity, although the underlying principle of catalysis was not recognized at the time. For example, the fermentation of sugar to ethanol and the conversion of ethanol to acetic acid are catalyzed by enzymes (biocata- lysts). However, the systematic scientific development of catalysis only began about 200 years ago, and its importance has grown up to the present day [2]. The term “catalysis” was introduced as early as 1836 by Berzelius in order to ex- plain various decomposition and transformation reactions. He assumed that catalysts possess special powers that can influence the affinity of chemical substances. A definition that is still valid today is due to Ostwald (1895): “a catalyst acceler- ates a chemical reaction without affecting the position of the equilibrium.” Ostwald recognized catalysis as a ubiquitous phenomenon that was to be explained in terms of the laws of physical chemistry. While it was formerly assumed that the catalyst remained unchanged in the course of the reaction, it is now known that the catalyst is involved in chemical bonding with the reactants during the catalytic process. Thus catalysis is a cyclic process: the reactants are bound to one form of the catalyst, and the products are released from another, regenerating the initial state. -
CO2 Hydrogenation to Formate and Methanol As an Alternative to Photo
BNL-108316-2015-JA CO2 Hydrogenation to Formate and Methanol as an Alternative to Photo- and Electrochemical CO2 Reduction Wan-Hui Wang,a,* Yuichiro Himeda,b,c,* James T. Muckerman,d Gerald F. Manbeck,d and Etsuko Fujitad,* a School of Petroleum and Chemical Engineering, Dalian University of Technology, Panjin 124221, China. b National Institute of Advanced Industrial Science and Technology, Tsukuba Central 5-1, 1-1-1 Higashi, Tsukuba, Ibaraki 305-8565, Japan. c JST, ACT-C, 4-1-8 Honcho, Kawaguchi, Saitama, 332-0012, Japan. d Chemistry Department, Brookhaven National Laboratory, Upton, NY 11973-5000, USA. Email: [email protected], [email protected], [email protected] 1 Contents 1. Introduction 2. Recent developments in CO2 hydrogenation to formate 2.1. Catalysts with phosphine ligands 2.2. Catalysts with pincer ligands. 2.3. Catalysts with N-heterocyclic carbene ligands 2.4. Half-sandwich catalysts with/without proton-responsive ligands 2.4.1. Electronic effects 2.4.2. Second coordination sphere effects 2.4.3. Mechanistic investigations 2.4.4. pH-dependent solubility and catalyst recovery 3. Formic Acid Dehydrogenation with Various Metal Complexes 3.1. Catalysts with phosphine ligands 3.1.1. Organic solvent systems 3.1.2. Aqueous solvent systems 3.2. Catalysts with pincer-type ligands 3.3. Catalysts with bidentate C,N-/N,N-ligands 3.4. Half-sandwich catalysts with/without proton-responsive ligands 3.4.1. Electronic effects 3.4.2. Pendent-base effect changing RDS of formic acid dehydrogenation 3.4.3. Solution pH changing RDS of formic acid dehydrogenation 3.5. -
Sulfur Tolerant Supported Bimetallic Catalysts for Low
Sulfur Tolerant Supported Bimetallic Catalysts for Low Temperature Water Gas Shift Reaction A dissertation submitted to the Division of Graduate Studies and Research of the University of Cincinnati in partial fulfillment of the requirements of the degree of Doctor of Philosophy (Ph.D.) In the Department of Chemical & Environmental Engineering of the College of Engineering & Applied Science 2019 By SeongUk Yun Committee : Dr. Vadim Guliants (Chair) Dr. Anastasios Angelopoulos Dr. Junhang Dong Dr. Mingming Lu I Abstract A series of model CuPd nanoparticles, CoMo oxide nanoparticles, different metal oxide supported Mo sulfide catalysts, and sets of different composition ratio and surface coverage of CoMo sulfide catalysts were prepared and investigated as sulfur-tolerant WGS catalysts. For comparison, monometallic catalysts prepared by incipient wetness impregnation, as well as commercial CoMo catalysts, were also investigated. The model CoMo-S catalysts at the monolayer surface coverage employed in this research are highly promising as sulfur-tolerant WGS catalysts displaying desirable structural, morphological, and compositional properties. The CuPd-2 catalysts maximized the number of WGS-active Cu0 sites with the optimized ratio (2.37) of CuO/CuAl2O4, showing higher WGS activity, thermal stability, and sulfur tolerance at 250°C than any other tested Cu-based catalysts. Cu-Pd bimetallic alloy catalysts showed enhanced reducibility due to the Pd-promoting effect through hydrogen spillover and additional reducible CuO sites through Cu species diffusion from the CuO shell to Al2O3. The Mo and CoMo oxide nanoparticles were prepared by a metal colloid chemical co-reduction method by modifying the concentrations of the Mo and Co precursors during synthesis.