Application of Advanced Head End Reprocessing Concepts to a Fluoride Volatility Flowsheet
Total Page:16
File Type:pdf, Size:1020Kb
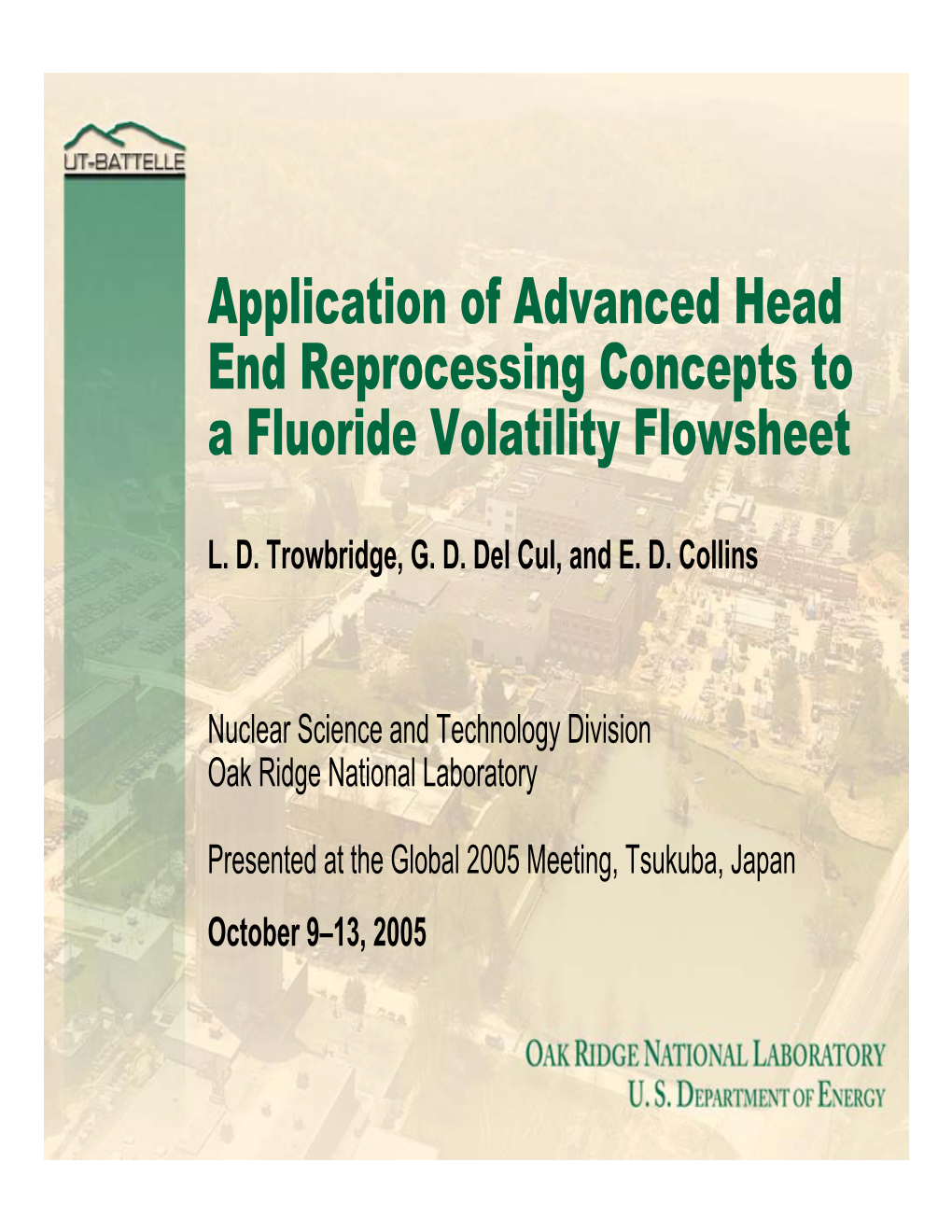
Load more
Recommended publications
-
Separation of Fluoride Residue Arising from Fluoride Volatility Recovery of Uranium from Spent Nuclear Fuel
University of Tennessee, Knoxville TRACE: Tennessee Research and Creative Exchange Masters Theses Graduate School 5-2004 Separation of Fluoride Residue Arising from Fluoride Volatility Recovery of Uranium from Spent Nuclear Fuel Jennifer L. Ladd-Lively University of Tennessee - Knoxville Follow this and additional works at: https://trace.tennessee.edu/utk_gradthes Part of the Chemical Engineering Commons Recommended Citation Ladd-Lively, Jennifer L., "Separation of Fluoride Residue Arising from Fluoride Volatility Recovery of Uranium from Spent Nuclear Fuel. " Master's Thesis, University of Tennessee, 2004. https://trace.tennessee.edu/utk_gradthes/2557 This Thesis is brought to you for free and open access by the Graduate School at TRACE: Tennessee Research and Creative Exchange. It has been accepted for inclusion in Masters Theses by an authorized administrator of TRACE: Tennessee Research and Creative Exchange. For more information, please contact [email protected]. To the Graduate Council: I am submitting herewith a thesis written by Jennifer L. Ladd-Lively entitled "Separation of Fluoride Residue Arising from Fluoride Volatility Recovery of Uranium from Spent Nuclear Fuel." I have examined the final electronic copy of this thesis for form and content and recommend that it be accepted in partial fulfillment of the equirr ements for the degree of Master of Science, with a major in Chemical Engineering. Robert M. Counce, Major Professor We have read this thesis and recommend its acceptance: Barry B. Spencer, Paul Bienkowski, Fred Weber Accepted for the Council: Carolyn R. Hodges Vice Provost and Dean of the Graduate School (Original signatures are on file with official studentecor r ds.) To the Graduate Council: I am submitting herewith a thesis written by Jennifer L. -
Properties of Selected Radioisotopes
CASE FILE COPY NASA SP-7031 Properties of Selected Radioisotopes A Bibliography PART I: UNCLASSIFIED LITERATURE NATIONAL AERONAUTICS AND SPACE ADMINISTRATION NASA SP-7031 PROPERTIES OF SELECTED RADIOISOTOPES A Bibliography Part I: Unclassified Literature A selection of annotated references to technical papers, journal articles, and books This bibliography was compiled and edited by DALE HARRIS and JOSEPH EPSTEIN Goddard Space Flight Center Greenbelt, Maryland Scientific and Technical Information Division / OFFICE OF TECHNOLOGY UTILIZATION 1968 USP. NATIONAL AERONAUTICS AND SPACE ADMINISTRATION Washington, D.C. PREFACE The increasing interest in the application of substantial quantities of radioisotopes for propulsion, energy conversion, and various other thermal concepts emphasizes a need for the most recent and most accurate information available describing the nuclear, chemical, and physical properties of these isotopes. A substantial amount of progress has been achieved in recent years in refining old and developing new techniques of measurement of the properties quoted, and isotope processing. This has resulted in a broad technological base from which both the material and information about the material is available. Un- fortunately, it has also resulted in a multiplicity of sources so that information and data are either untimely or present properties without adequately identifying the measurement techniques or describing the quality of material used. The purpose of this document is to make available, in a single reference, an annotated bibliography and sets of properties for nine of the more attractive isotopes available for use in power production. Part I contains all the unclassified information that was available in the literature surveyed. Part II is the classified counterpart to Part I. -
System Studies of Fission-Fusion Hybrid Molten Salt Reactors
University of Tennessee, Knoxville TRACE: Tennessee Research and Creative Exchange Doctoral Dissertations Graduate School 12-2013 SYSTEM STUDIES OF FISSION-FUSION HYBRID MOLTEN SALT REACTORS Robert D. Woolley University of Tennessee - Knoxville, [email protected] Follow this and additional works at: https://trace.tennessee.edu/utk_graddiss Part of the Nuclear Engineering Commons Recommended Citation Woolley, Robert D., "SYSTEM STUDIES OF FISSION-FUSION HYBRID MOLTEN SALT REACTORS. " PhD diss., University of Tennessee, 2013. https://trace.tennessee.edu/utk_graddiss/2628 This Dissertation is brought to you for free and open access by the Graduate School at TRACE: Tennessee Research and Creative Exchange. It has been accepted for inclusion in Doctoral Dissertations by an authorized administrator of TRACE: Tennessee Research and Creative Exchange. For more information, please contact [email protected]. To the Graduate Council: I am submitting herewith a dissertation written by Robert D. Woolley entitled "SYSTEM STUDIES OF FISSION-FUSION HYBRID MOLTEN SALT REACTORS." I have examined the final electronic copy of this dissertation for form and content and recommend that it be accepted in partial fulfillment of the equirr ements for the degree of Doctor of Philosophy, with a major in Nuclear Engineering. Laurence F. Miller, Major Professor We have read this dissertation and recommend its acceptance: Ronald E. Pevey, Arthur E. Ruggles, Robert M. Counce Accepted for the Council: Carolyn R. Hodges Vice Provost and Dean of the Graduate School (Original signatures are on file with official studentecor r ds.) SYSTEM STUDIES OF FISSION-FUSION HYBRID MOLTEN SALT REACTORS A Dissertation Presented for the Doctor of Philosophy Degree The University of Tennessee, Knoxville Robert D. -
RFI) DE-FOA-0002533 on Cleaning up Radioisotope Enventories (CURIE)
U.S. Department of Energy Advanced Research Projects Agency – Energy (ARPA-E) Request for Information (RFI) DE-FOA-0002533 on Cleaning Up RadioIsotope Enventories (CURIE) Introduction The purpose of this RFI is to solicit input for a potential future ARPA-E research program focused on the development of technologies that would enable the effective management of the Nation’s commercial used nuclear fuel (UNF). The goals of this RFI are to (1) solicit information about reactor fuel needs for both the current commercial light-water reactor (LWR) fleet and future advanced reactors, and (2) seek insights into technology gaps and/or cost drivers that may be hindering economical recycling of existing LWR UNF.1 This information is needed to help ARPA-E identify ways in which the Nation’s roughly 86,000 MTU2 inventory of UNF, which has been increasing by approximately 2,000 MTU per year, can best be recycled to support current and advanced reactor fuel needs. Such activities are consistent with ARPA-E’s statutory goals, which include supporting the development of transformative solutions for addressing UNF.3 ARPA-E is interested in information about technologies with the potential to make recycling UNF at least as economical, safe, and secure as the current once-through fuel cycle.4 Such technologies would enable a UNF treatment facility to be economically constructed, managed, and operated; yield an actinide product that is cost-competitive with natural uranium (U) obtained from traditional mining and milling; and generate significantly lower -
12.2% 130,000 155M Top 1% 154 5,300
We are IntechOpen, the world’s leading publisher of Open Access books Built by scientists, for scientists 5,300 130,000 155M Open access books available International authors and editors Downloads Our authors are among the 154 TOP 1% 12.2% Countries delivered to most cited scientists Contributors from top 500 universities Selection of our books indexed in the Book Citation Index in Web of Science™ Core Collection (BKCI) Interested in publishing with us? Contact [email protected] Numbers displayed above are based on latest data collected. For more information visit www.intechopen.com Chapter Fast-Spectrum Fluoride Molten Salt Reactor (FFMSR) with Ultimately Reduced Radiotoxicity of Nuclear Wastes Yasuo Hirose Abstract A mixture of NaF-KF-UF4 eutectic and NaF-KF-TRUF3 eutectic containing heavy elements as much as 2.8 g/cc makes a fast-spectrum molten salt reactor based upon the U-Pu cycle available without a blanket. It does not object breeding but a stable operation without fissile makeup under practical contingencies. It is highly integrated with online dry chemical processes based on “selective oxide precipita- tion” to create a U-Pu cycle to provide as low as 0.01% leakage of TRU and nominated as the FFMSR. This certifies that the radiotoxicity of HLW for 1500 effective full power days (EFPD) operation can be equivalent to 405 tons of depleted uranium after 500 years cooling without Partition and Transmutation (P&T). A certain amount of U-TRU mixture recovered from LWR spent fuel is loaded after the initial criticality until U-Pu equilibrium but the fixed amount of 238U only thereafter. -
Fuel Cycle Processes Directed Self-Study Course! This Is the Third of Nine Modules Available in This Directed Self-Study Course
MODULE 3.0: URANIUM CONVERSION Introduction Welcome to Module 3.0 of the Fuel Cycle Processes Directed Self-Study Course! This is the third of nine modules available in this directed self-study course. The purpose of this module is to be able to discuss the NRC regulations of and describe conversion facilities; identify the basic steps of the dry fluoride volatility conversion process and contrast with the wet acid digestion conversion process; identify sampling and measurement activities for the dry conversion process and the radiological and non-radiological hazards associated with the dry conversion process. This self-study module is designed to assist you in accomplishing the learning objectives listed at the beginning of the module. There are five learning objectives in this module. The module has self-check questions and activities to help you assess your understanding of the concepts presented in the module. Before you Begin It is recommended that you have access to the following materials: ◙ Trainee Guide ◙ Sequoyah Fuels Accident Slides (on CD accompanying course manual) ◙ “Release of UF6 from a Ruptured Model 48Y Cylinder at Sequoyah Fuels Corporation Facility: Lessons-Learned Report," U.S. Nuclear Regulatory Commission, NUREG-1198, June 1986. ◙ “Assessment of the Public Health Impact from the Accidental Release of UF6 at the Sequoyah Fuels Corporation Facility at Gore, Oklahoma," U.S. Nuclear Regulatory Commission, NUREG-1189, Vol. 1, March 1986. Complete the following prerequisites: ◙ Module 1.0: Overview of the Nuclear Fuel Cycle How to Complete this Module 1. Review the learning objectives. 2. Read each section within the module in sequential order. -
Estimation of Alkali Metal Mole Percent and Weight of Calcined Solids for ICPP Calcine
INEL-95/0184 Estimation of Alkali Metal Mole Percent and Weight of Calcined Solids for ICPP Calcine B. H. O'Brien Published March 1995 Idaho National Engineering Laboratory High-Levei Waste Engineering and Project Management Department Lockheed Idaho Technologies Company Idaho Falls, Idaho 83415 Prepared for the U.S. Department of Energy Assistant Secretary for Environmental Management Under DOE Idaho Operations Office Contract DE-AC07-94ID13223 DISTRIBUTION OF THIS DCCl-^T IS UNLIMITED (j$ I DISCLAIMER Portions of this document may be illegible eiectronic image products, images are produced from the best avaiiabie original document. ABSTRACT An updated method is given for estimation of the weight of calcined solids and volume reduction factor for calcine, and mole percent sodium plus potassium in calcine produced from radioactive waste in a fluidized-bed calciner at the Idaho Chemical Processing Plant (ICPP). It incorporates new information on a calcine chemistry from a study by K. N. Brewer and G. F. Kessinger in which they determined the compounds formed during calcination by both high temperature thermodynamic equilibrium calculations and by analyses of pilot-plant calcines. An explanation of the assumptions made in the calculations, along with several example calculations and comparisons with the previous calculation methods are included. This method allows calculation of the heat generation rate and sodium content of the calcine, which are used to determine the suitability of the calcine for storage in the ICPP bin sets. Although this method accurately predicts the weight of calcine and mole percent Na+K for its intended purpose, the compounds predicted should only be used as a first approximation for other purposes since the calculation does not incorporate all of the compounds, such as mixed-metal oxides, which may form during calcination. -
Actinide Separation Chemistry in Nuclear Waste Streams and Materials, December 1997
NEA/NSC/DOC(97)19 NEA NUCLEAR SCIENCE COMMITTEE ACTINIDE SEPARATION CHEMISTRY IN NUCLEAR WASTE STREAMS AND MATERIALS December 1997 NUCLEAR ENERGY AGENCY ORGANISATION FOR ECONOMIC CO-OPERATION AND DEVELOPMENT FOREWORD The separation of actinide elements from various waste materials is a significant problem facing developed countries. The issue arises primarily because of the potential long-term hazard of many of the actinides, but is also due to the regulatory requirements associated with actinide waste disposal, which are different from those associated with other radioactive wastes. The different regulations are in turn related to the different health hazards and generally longer half lives of the actinides. This issue is of continuing interest to the OECD/NEA Member countries primarily in relation to waste produced within power station fuel recycle. Similar problems exist for waste produced in the past as a result of nuclear weapons production programmes and wastes likely to be produced in the future emerging from operations required for waste disposal. The Nuclear Science Committee, representing the interests of the basic R&D in the OECD/NEA Member countries, has established a task force of experts in actinide chemistry to review the current and developing separation techniques and chemical processes of interest in separating actinides. This task force was commissioned with the preparation of a report on the subject. The task force members are listed in Annex 1. This report is intended to provide a timely and representative guide to technical journals and other sources of separation chemistry information on the actinide elements. An important objective is to provide information that may be used to conserve energy and protect humans and the environment. -
The Study of Alternate, Solid-Phase Fluorinating Agents for Use in Reactive Gas Recycle of Used Nuclear Fuel
University of South Carolina Scholar Commons Theses and Dissertations 2013 The tudS y of Alternate, Solid-Phase Fluorinating Agents for Use in Reactive Gas Recycle of Used Nuclear Fuel Dillon Inabinett University of South Carolina Follow this and additional works at: https://scholarcommons.sc.edu/etd Part of the Nuclear Engineering Commons Recommended Citation Inabinett, D.(2013). The Study of Alternate, Solid-Phase Fluorinating Agents for Use in Reactive Gas Recycle of Used Nuclear Fuel. (Master's thesis). Retrieved from https://scholarcommons.sc.edu/etd/3587 This Open Access Thesis is brought to you by Scholar Commons. It has been accepted for inclusion in Theses and Dissertations by an authorized administrator of Scholar Commons. For more information, please contact [email protected]. THE STUDY OF ALTERNATE, SOLID-PHASE FLUORINATING AGENTS FOR USE IN REACTIVE GAS RECYCLE OF USED NUCLEAR FUEL by Dillon Inabinett Bachelor of Science University of South Carolina, 2012 Submitted in Partial Fulfillment of the Requirements For the Degree of Master of Science in Nuclear Engineering College of Engineering and Computing University of South Carolina 2013 Accepted by: Travis W. Knight, Major Professor Joshua Gray, Second Reader Lacy Ford, Vice Provost and Dean of Graduate Studies © Copyright by Dillon Inabinett, 2013 All Rights Reserved. ii DEDICATION I would like to dedicate this work to my mother, for her endless support throughout all of my endeavors. Though life may not have always been perfect, the one thing that remains true is her love and affection. iii ACKNOWLEDGEMENTS I would like to thank my two advisors, Dr. Travis Knight and Dr. -
(Msrs): Coupling Spent Fuel Processing and Actinide Burning
Molten Salt Reactors (MSRs): Coupling Spent Fuel Processing and Actinide Burning Dr. Charles W. Forsberg* Oak Ridge National Laboratory P.O. Box 2008 Oak Ridge, Tennessee 37831-6179 Tel: (865) 574-6783 Fax: (865) 574-9512 E-mail: [email protected] Professor Ehud Greenspan University of California, Berkeley 4107 Etcheverry Berkeley, California 94720-1730 Tel: (510) 643-9983 E-mail: [email protected] Manuscript Date: July 25, 2003 File: MSR.HiltonHead.Combined.2003 Advances in Nuclear Fuel Management III American Nuclear Society Hilton Head, South Carolina October 5–7, 2003 The submitted manuscript has been authored by a contractor of the U.S. Government under contract DE-AC05-00OR22725. Accordingly, the U.S. Government retains a nonexclusive, royalty-free license to publish or reproduce the published form of this contribution, or allow others to do so, for U.S. Government purposes. _________________________ *Oak Ridge National Laboratory, managed by UT-Battelle, LLC, for the U.S. Department of Energy under contract DE-AC05-00OR22725. Advances in Nuclear Fuel Management III (ANFM 2003) Hilton Head Island, South Carolina, USA, October 5–8, 2003, on CD-ROM, American Nuclear Society, La Grange Park, IL (2003) MOLTEN SALT REACTORS (MSRs): COUPLING SPENT FUEL PROCESSING AND ACTINIDE BURNING Charles Forsberg Ehud Greenspan Oak Ridge National Laboratory University of California, Berkeley P.O. Box 2008 4107 Etcheverry Oak Ridge, Tennessee 37831 Berkeley, California 94720-1730 [email protected] [email protected] Keywords: Molten Salt Reactor, Transmutation, Actinide Burning ABSTRACT Molten salt reactors (MSRs) are liquid-fueled reactors that can be used for burning actinides, production of electricity, production of hydrogen, and production of fissile fuels (breeding). -
Identification of Potential Waste Processing and Waste Form Options for Molten Salt Reactors
Identification of Potential Waste Processing and Waste Form Options for Molten Salt Reactors Prepared for U.S. Department of Energy MSR Campaign B.J. Riley,(a) J. McFarlane,(b) G.D. DelCul,(b) J.D. Vienna,(a) C.I. Contescu,(b) L.M. Hay,(a) A.V. Savino,(a) H.E. Adkins,(a) (a)Pacific Northwest National Laboratory (b)Oak Ridge National Laboratory August 15, 2018 NTRD-MSR-2018-000379, PNNL-27723 Approved for public release. Distribution is unlimited. DISCLAIMER This information was prepared as an account of work sponsored by an agency of the U.S. Government. Neither the U.S. Government nor any agency thereof, nor any of their employees, makes any warranty, expressed or implied, or assumes any legal liability or responsibility for the accuracy, completeness, or usefulness, of any information, apparatus, product, or process disclosed, or represents that its use would not infringe privately owned rights. References herein to any specific commercial product, process, or service by trade name, trade mark, manufacturer, or otherwise, does not necessarily constitute or imply its endorsement, recommendation, or favoring by the U.S. Government or any agency thereof. The views and opinions of authors expressed herein do not necessarily state or reflect those of the U.S. Government or any agency thereof. Identification of Potential Waste Processing and Waste Form Options for Molten Salt Reactors iv August 15, 2018 SUMMARY The overall summary of the waste management envelope discussed in this report is represented by the diagram shown in Figure S1. The -
Nuclear Fuel Cycle Technologies for Future Low-Carbon Society 70 Nuclear Fuel Cycle Technologies for Future Low-Carbon Society
Nuclear Fuel Cycle Technologies for Future Low-carbon Society 70 Nuclear Fuel Cycle Technologies for Future Low-carbon Society Tetsuo Fukasawa, Dr. Eng. OVERVIEW: Establishing a nuclear fuel cycle that can recover usable fuel Shusaku Sawada material from spent nuclear fuel so that it can be reused in a nuclear reactor Kikuo Okada is essential to meet objectives such as securing the long-term availability of an energy source that emits almost no CO and improving Japan’s very low Masashi Shimizu 2 level of energy self-sufficiency. The Monju prototype fast breeder reactor was restarted on May 6, 2010 and this will be accompanied by the planned completion in the future of the Rokkasho Reprocessing Plant, an interim storage facility for spent fuel, and other associated facilities. Discussions regarding the construction of a second reprocessing plant are expected to start during the 2010 financial year. It is anticipated that a demonstration fast-breeder reactor will be completed around 2025 and the introduction of commercial fast-breeder reactors will take place around 2050 provided economic and other requirements have been satisfied. In addition to its involvement in reprocessing, Monju, interim storage, and other such projects, Hitachi is also working on the development of future technologies such as fast breeder reactors and advanced reprocessing with the aim of creating a low-carbon society in the future. INTRODUCTION energy sources such as photovoltaic and wind power RISING international concerns about climate change also emit no CO2 in the generation process, they are have led to a growing number of countries showing characterized by requiring a large area of land and an interest in nuclear power which can generate being dependent on weather conditions.