Ares® Retaining Wall Systems
Total Page:16
File Type:pdf, Size:1020Kb
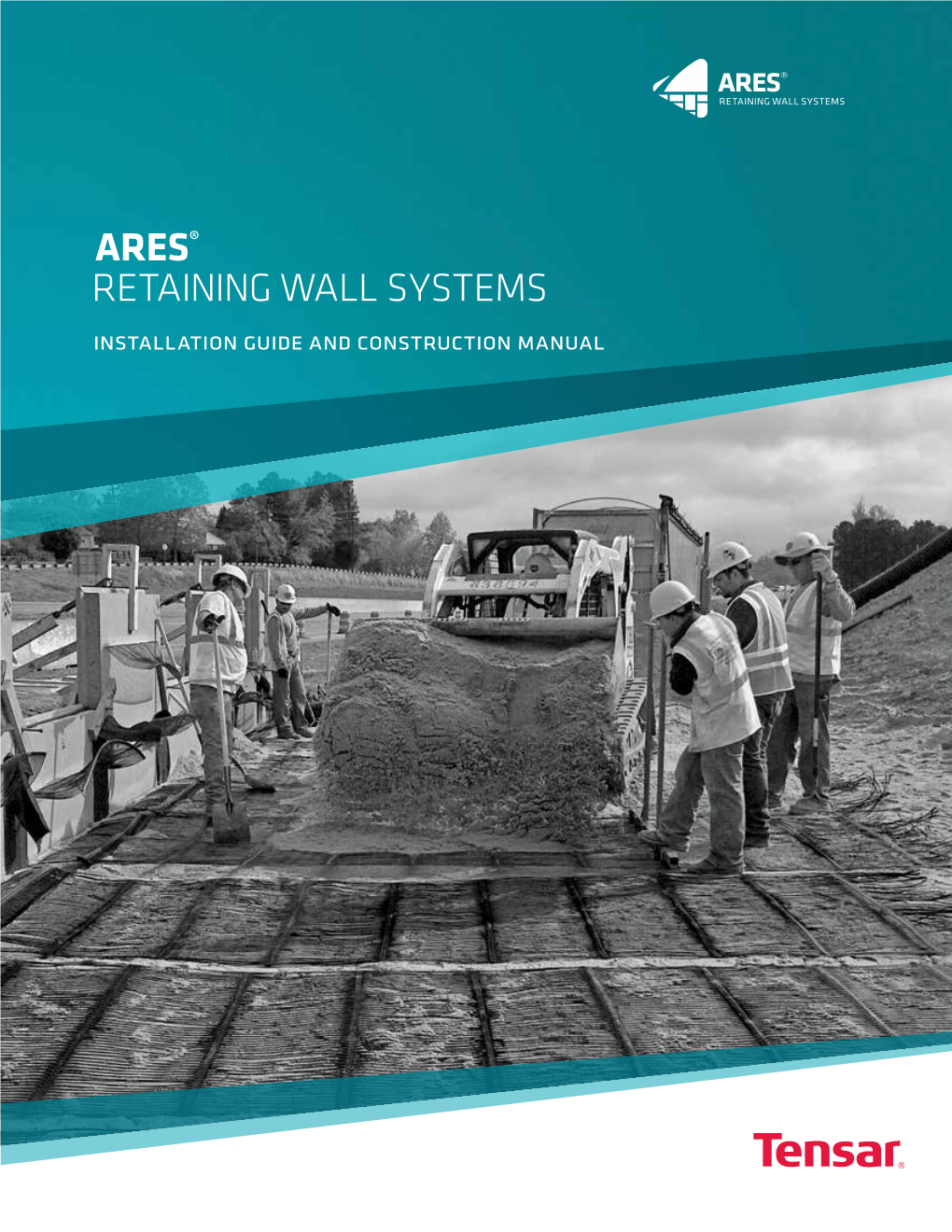
Load more
Recommended publications
-
The Oracle and Cult of Ares in Asia Minor Matthew Gonzales
The Oracle and Cult of Ares in Asia Minor Matthew Gonzales ERODOTUS never fails to fascinate with his rich and detailed descriptions of the varied peoples and nations H mustered against Greece by Xerxes;1 but one of his most tantalizing details, a brief notice of the existence of an oracle of Ares somewhere in Asia Minor, has received little comment. This is somewhat understandable, as the name of the proprietary people or nation has disappeared in a textual lacuna, and while restoring the name of the lost tribe has ab- sorbed the energies of some commentators, no moderns have commented upon the remarkable and unexpected oracle of Ares itself. As we shall see, more recent epigraphic finds can now be adduced to show that this oracle, far from being the fantastic product of logioi andres, was merely one manifestation of Ares’ unusual cultic prominence in south/southwestern Asia Minor from “Homeric” times to Late Antiquity. Herodotus and the Solymoi […] 1 The so-called Catalogue of Forces preserved in 7.61–99. In light of W. K. Pritcéhesttp’s¤ dtahwo rodu¢g h» mreofbuota˝tnioanws eo‰xf osunc hs mscihkorlãarws, aksa O‹ .p rAorbmÒalyoru, wD . FehdlÊinog ,l aunkdio Se.r Wg°eastw, ßwkhaos steoekw teo‰x dei,s c§rped‹ idt ¢th teª asuit hkoerfitay loªf sHie krordãontuesa o n thixs ãanldk eoath:e pr rpÚowin dts¢, tIo w›silli skimrãplnye rseif eŒr ttãhe t ree kadae‹r kto° rPerait cphreotts’s∞ tnw ob omÚawj or trexatãmleknetas ,o f t§hpe∞irs waonr k,d S¢t udkieas i‹n AlnÒcifenot i:G reetkå Two podg¢ra phkyn IÆVm (aBwe rk=eãleky e1s9i8 2) 23f4–o2in85ik a°nodi sTih ek Laiatre Silch¤xoola otf oH. -
2018-19 INSIDER Staff: Dayanna Perez, David Fender, Christian
Volume 7, Issue 1 October 2018 11880 Roswell Ave. Chino, CA I will survive!!! 2018-19 INSIDER Staff: Dayanna Perez, David Inside this issue: Fender, Christian Hartson, Toxic People/Trends 2-3 Duke Hernandez, Emma Trujillo, Reese Gonzales, Fortnite vs. H1Z1/Comic 4-5 Kelea Alicea Lara, Breann D.C. Comics vs. Marvel 6-7 Hill, Angel Cesma, Gavin Watch & Listen 8 Hrynezuk, Jackie Guerrero, Horoscopes 9 Annalisa Contreraz, Julia Zelaya, Alyah Tolentino Bullies/Masks/Urban Legends 10-11 T h e B r i g g s Scary Story 12 Page 2 Toxic People INSIDER Toxic People Cleanse By Emma Trujillo then you go ahead and have fun! Put yourself out there and meet new and better people Join school clubs they wouldn’t join. You can partner up with the new kid or ask someone you think would be nice to hangout. Do different sports and activities. Don’t list every single reason why they’re bad for you Again, this is only wasting your time. Plus, you don’t want to make them feel bad, or even worse it’ll aggra- vate them and they definitely won’t leave you alone. Don’t stoop to their level and focus on “revenge” Have a mindset that it will take time or “getting back at them.” Getting rid of a bad person in your life isn’t always Not only are you starting to act like this person but it’s easy. You can’t just say, “You’re not going to be in my completely stupid. I mean come on, just forgive and life anymore.” That’ll only make them want to bug you forget. -
Thesis Are Retained by the Author And/Or Other Copyright Owners
Canterbury Christ Church University’s repository of research outputs http://create.canterbury.ac.uk Copyright © and Moral Rights for this thesis are retained by the author and/or other copyright owners. A copy can be downloaded for personal non-commercial research or study, without prior permission or charge. This thesis cannot be reproduced or quoted extensively from without first obtaining permission in writing from the copyright holder/s. The content must not be changed in any way or sold commercially in any format or medium without the formal permission of the copyright holders. When referring to this work, full bibliographic details including the author, title, awarding institution and date of the thesis must be given e.g. Walsh, M. (2018) Comic books & myths: the evolution of the mythological narratives in comic books for a contemporary myth. M.A. thesis, Canterbury Christ Church University. Contact: [email protected] Comic Books & Myths: The Evolution of the Mythological Narratives in Comic Books for a Contemporary Myth by Michael Joseph Walsh Canterbury Christ Church University Thesis submitted for the Degree of MA by Research 2018 CONTENTS Abstract .................................................................................................................................................. iii Acknowledgements ................................................................................................................................ iv The Image of Myth: .............................................................................................................................. -
Marvel-Phile
by Steven E. Schend and Dale A. Donovan Lesser Lights II: Long-lost heroes This past summer has seen the reemer- 3-D MAN gence of some Marvel characters who Gestalt being havent been seen in action since the early 1980s. Of course, Im speaking of Adam POWERS: Warlock and Thanos, the major players in Alter ego: Hal Chandler owns a pair of the cosmic epic Infinity Gauntlet mini- special glasses that have identical red and series. Its great to see these old characters green images of a human figure on each back in their four-color glory, and Im sure lens. When Hal dons the glasses and focus- there are some great plans with these es on merging the two figures, he triggers characters forthcoming. a dimensional transfer that places him in a Nostalgia, the lowly terror of nigh- trancelike state. His mind and the two forgotten days, is alive still in The images from his glasses of his elder broth- MARVEL®-Phile in this, the second half of er, Chuck, merge into a gestalt being our quest to bring you characters from known as 3-D Man. the dusty pages of Marvel Comics past. As 3-D Man can remain active for only the aforementioned miniseries is showing three hours at a time, after which he must readers new and old, just because a char- split into his composite images and return acter hasnt been seen in a while certainly Hals mind to his body. While active, 3-D doesnt mean he lacks potential. This is the Mans brain is a composite of the minds of case with our two intrepid heroes for this both Hal and Chuck Chandler, with Chuck month, 3-D Man and the Blue Shield. -
Heroclix Bestand 16-10-2012
Heroclix Liste Infinity Challenge Infinity Gauntlet Figure Name Gelb Blau Rot Figure Name Gelb Blau Rot Silber und Bronze Adam Warlock 1 SHIELD Agent 1 2 3 Mr. Hyde 109 110 111 Vision 139 In-Betweener 2 SHIELD Medic 4 5 6 Klaw 112 113 114 Quasar 140 Champion 3 Hydra Operative 7 8 9 Controller 115 116 117 Thanos 141 Gardener 4 Hydra Medic 10 11 12 Hercules 118 119 120 Nightmare 142 Runner 5 Thug 13 14 15 Rogue 121 122 123 Wasp 143 Collector 6 Henchman 16 17 18 Dr. Strange 124 125 126 Elektra 144 Grandmaster 7 Skrull Agent 19 20 21 Magneto 127 128 129 Professor Xavier 145 Infinity Gauntlet 101 Skrull Warrior 22 23 24 Kang 130 131 132 Juggernaut 146 Soul Gem S101 Blade 25 26 27 Ultron 133 134 135 Cyclops 147 Power Gem S102 Wolfsbane 28 29 30 Firelord 136 137 138 Captain America 148 Time Gem S103 Elektra 31 32 33 Wolverine 149 Space Gem S104 Wasp 34 35 36 Spider-Man 150 Reality Gem S105 Constrictor 37 38 39 Marvel 2099 Gabriel Jones 151 Mind Gem S106 Boomerang 40 41 42 Tia Senyaka 152 Kingpin 43 44 45 Hulk 1 Operative 153 Vulture 46 47 48 Ravage 2 Medic 154 Jean Grey 49 50 51 Punisher 3 Knuckles 155 Hammer of Thor Hobgoblin 52 53 54 Ghost Rider 4 Joey the Snake 156 Fast Forces Sabretooth 55 56 57 Meanstreak 5 Nenora 157 Hulk 58 59 60 Junkpile 6 Raksor 158 Fandral 1 Puppet Master 61 62 63 Doom 7 Blade 159 Hogun 2 Annihilus 64 65 66 Rahne Sinclair 160 Volstagg 3 Captain America 67 68 69 Frank Schlichting 161 Asgardian Brawler 4 Spider-Man 70 71 72 Danger Room Fred Myers 162 Thor 5 Wolverine 73 74 75 Wilson Fisk 163 Loki 6 Professor Xavier 76 -
Dr. Anita K. Mcdaniel University of North Carolina Wilmington
Dr. Anita K. McDaniel University of North Carolina Wilmington [email protected] “On the topic of gender issues in superhero fiction, it seems that, in the action-adventure fantasy world parity between the sexes is a good thing. Whereas this is fantasy serving the forces of commerce, the forces of commerce in return serve the forces of fantasy. People would not pay to read and see the tales of these fictional heroes if the lessons–explicit and implicit–of the fictions did not feed their psyches and souls.... Each generation makes the fictional heroes it needs. What should inspire–or terrify–us are not the hero’s powers or gender, but what the heroes represent about our needs, our fears, and our attitudes.” Danny Fingeroth • Golden Age—male creators/writers/artists producing male oriented subject matter for male readers. • Post Golden Age—women as editors, writers and artists influencing well known titles of the Big Two and creator driven, independent works • Result—a new voice spoken by women is being heard in comic books and is helping to shape readers' perceptions of the superhero. Thesis • Often it has been stated that female superhero titles do not sell. Hence, superheroines (created by men) devolved into two dimensional stereotypes (Wonder Woman), plot devices for the stories of male superheroes (Batgirl), and industry jokes (She-Hulk). • Emphasis has been placed on the talented work of Karen Berger (editor), Barbara Kesel Randall (writer), and Jan Duursema (artist) because they exemplify attempts by women to restore dignity and “super” status to superheroines. “The [superhero] genre stuff that I did had to have strong elements of realism... -
X-Men, Dragon Age, and Religion: Representations of Religion and the Religious in Comic Books, Video Games, and Their Related Media Lyndsey E
Georgia Southern University Digital Commons@Georgia Southern University Honors Program Theses 2015 X-Men, Dragon Age, and Religion: Representations of Religion and the Religious in Comic Books, Video Games, and Their Related Media Lyndsey E. Shelton Georgia Southern University Follow this and additional works at: https://digitalcommons.georgiasouthern.edu/honors-theses Part of the American Popular Culture Commons, International and Area Studies Commons, and the Religion Commons Recommended Citation Shelton, Lyndsey E., "X-Men, Dragon Age, and Religion: Representations of Religion and the Religious in Comic Books, Video Games, and Their Related Media" (2015). University Honors Program Theses. 146. https://digitalcommons.georgiasouthern.edu/honors-theses/146 This thesis (open access) is brought to you for free and open access by Digital Commons@Georgia Southern. It has been accepted for inclusion in University Honors Program Theses by an authorized administrator of Digital Commons@Georgia Southern. For more information, please contact [email protected]. X-Men, Dragon Age, and Religion: Representations of Religion and the Religious in Comic Books, Video Games, and Their Related Media An Honors Thesis submitted in partial fulfillment of the requirements for Honors in International Studies. By Lyndsey Erin Shelton Under the mentorship of Dr. Darin H. Van Tassell ABSTRACT It is a widely accepted notion that a child can only be called stupid for so long before they believe it, can only be treated in a particular way for so long before that is the only way that they know. Why is that notion never applied to how we treat, address, and present religion and the religious to children and young adults? In recent years, questions have been continuously brought up about how we portray violence, sexuality, gender, race, and many other issues in popular media directed towards young people, particularly video games. -
ARES TARGETING SYSTEM English Manual
2021 ARES TARGETING SYSTEM English manual ares-alpha.com/shop Ver 3.00 Contents Specifications and models ...................................................................................................................... 2 Features .................................................................................................................................................. 4 Integrate the target in Ares Alpha games. ............................................................................................. 4 Configuration of the target .................................................................................................................... 5 Game settings ........................................................................................................................................ 8 Connection ........................................................................................................................................... 10 Info menu ............................................................................................................................................. 13 Fast reset .............................................................................................................................................. 13 Field Tests ............................................................................................................................................. 14 1 Specifications and models Ares Targeting System is the most advanced electronic airsoft target. It's fully integrated -
War and the Warrior: Functions of Ares in Literature and Cult1
War and the Warrior: Functions of Ares in Literature and Cult Alexander T. Millington UCL Dissertation submitted for the degree of PhD in History 2013 1 I, Alexander Millington, confirm that the work presented in this thesis is my own. Where information has been derived from other sources, I confirm that this has been indicated in the thesis. 2 Abstract This dissertation presents a new interpretative synthesis of the sources relating to the cults, identities, and functions of the god Ares, focusing on the Archaic and Classic periods. An apparent dichotomy is identified: in many respects, the evidence suggests that Ares must have been a very important god throughout much of the Greek world throughout the Archaic and Classic periods (and beyond), but in other respects the evidence suggests that he was not. I argue that this dichotomy does not derive from changes in the popularity, relevance, or nature of the god, as has been proposed. Instead, I argue that the elements of Ares’ cults and representations which suggest that Ares was unpopular or unimportant derive from those which made him important and continually relevant. I argue that because Ares was identified with war, attitudes towards the god directly reflect Greek attitudes towards war. War’s importance as an element of Greek life, and the god’s power as a causal force with it, led to deep respect for Ares, reflected by widespread cult, and a place among the great Olympians. But the wild, destructive, and unpredictable nature of war, which Ares represented, meant that he was not a regular recipient of large-scale celebratory cult. -
Marvel Comics Avengers Chronological Appearances by Bob Wolniak
Marvel Comics Avengers Chronological Appearances By Bob Wolniak ased initially on the Bob Fronczak list from Avengers Assemble and Avengers Forever websites. But unlike Mr. B Fronczak’s list (that stops about the time of Heroes Reborn) this is NOT an attempt at a Marvel continuity (harmony of Marvel titles in time within the fictional universe), but Avengers appearances in order in approx. real world release order . I define Avengers appearances as team appearances, not individual Avengers or even in some cases where several individual Avengers are together (but eventually a judgment call has to be made on some of those instances). I have included some non-Avengers appearances since they are important to a key storyline that does tie to the Avengers, but noted if they did not have a team appearance. Blue (purple for WCA & Ultimates) indicates an Avengers title , whether ongoing or limited series. I have decided that Force Works is not strictly an Avengers title, nor is Thunderbolts, Defenders or even Vision/Scarlet Witch mini- series, although each book correlates, crosses over and frequently contains guest appearances of the Avengers as a team. In those cases, the individual issues are listed. I have also decided that individual Avengers’ ongoing or limited series books are not Avengers team appearances, so I have no interest in the tedious tracking of every Captain America, Thor, Iron Man, or Hank Pym title unless they contain a team appearance or x-over . The same applies to Avengers Spotlight (largely a Hawkeye series, with other individual appearances), Captain Marvel, Ms. Marvel, Vision, Wonder Man, Hulk, She-Hulk, Black Panther, Quicksilver, Thunderstrike, War Machine, Black Widow, Sub-Mariner, Hercules, and other such books or limited series. -
Avengers Chronology by Bob Fronczak
Avengers Chronology By Bob Fronczak Avengers 1 Avengers 1.5 Avengers 2 Untold Tales of Spiderman 3 Tales of Suspense 49 (Iron Man vs. the Angel. Other Avengers appear in civilian identities (cameos), unable to answer IM's call for assistance) Avengers 3 Avengers 4 Sentry 1 (FB) Fantastic Four 25 Fantastic Four 26 Avengers 5 Avengers 6 Marvels 2 Thor: Godstorm 1 Journey into Mystery 101 Journey into Mystery 105 Tales of Suspense 56 (Iron Man vs. the Unicorn. The Avengers try to contact IM during his battle but he fails to answer their summons. 3 panels.) Avengers 7 Journey into Mystery 108 Tales to Astonish 59 Amazing Spider-Man Annual 1 Tales of Suspense 58 (Iron Man vs. Capt. America. The Chameleon impersonates Cap and tricks IM into attacking him. Giant-Man and Wasp capture the Chameleon and end the fight Avengers 8 Amazing Spider-Man 18 Avengers 9 Tales of Suspense 59 Fantastic Four 31 Unlimited Access 2 Unlimited Access 3 Unlimited Access 4 Untold Tales of Spider-Man Annual 2 (Avengers join in the battle vs. Sundown) Tales of Suspense 60 Avengers 10 X-Men 9 Avengers 11 Avengers 12 Avengers 13 Avengers 14 Fantastic Four 36 (Avengers attend Reed Richards and Sue Storm's engagement party. 2 panels) Captain America 221 / 2 nd Story Avengers 15 Avengers 16 Marvel Heroes & Legends 97 (Revised and expanded version of Avengers 16) Journey Into Mystery 116 Thunderbolts 9 Avengers 17 Journey into Mystery 120 (Thor vs. the Absorbing Man. Thor appears at the Mansion to ask the Avengers aid. -
Uncarded Figure Keyword List
Uncarded Figure Keyword List Infinity Challenge ............................................................................................................... 2 Hypertime ........................................................................................................................... 4 Clobberin' Time .................................................................................................................. 5 Xplosion ............................................................................................................................. 7 Indy..................................................................................................................................... 8 Cosmic Justice .................................................................................................................. 10 Critical Mass..................................................................................................................... 11 Universe ........................................................................................................................... 13 Unleashed ......................................................................................................................... 14 Ultimates .......................................................................................................................... 16 Mutant Mayhem ............................................................................................................... 17 City of Heroes .................................................................................................................