An Overview of Hydrodesulfurization and Hydrodenitrogenation
Total Page:16
File Type:pdf, Size:1020Kb
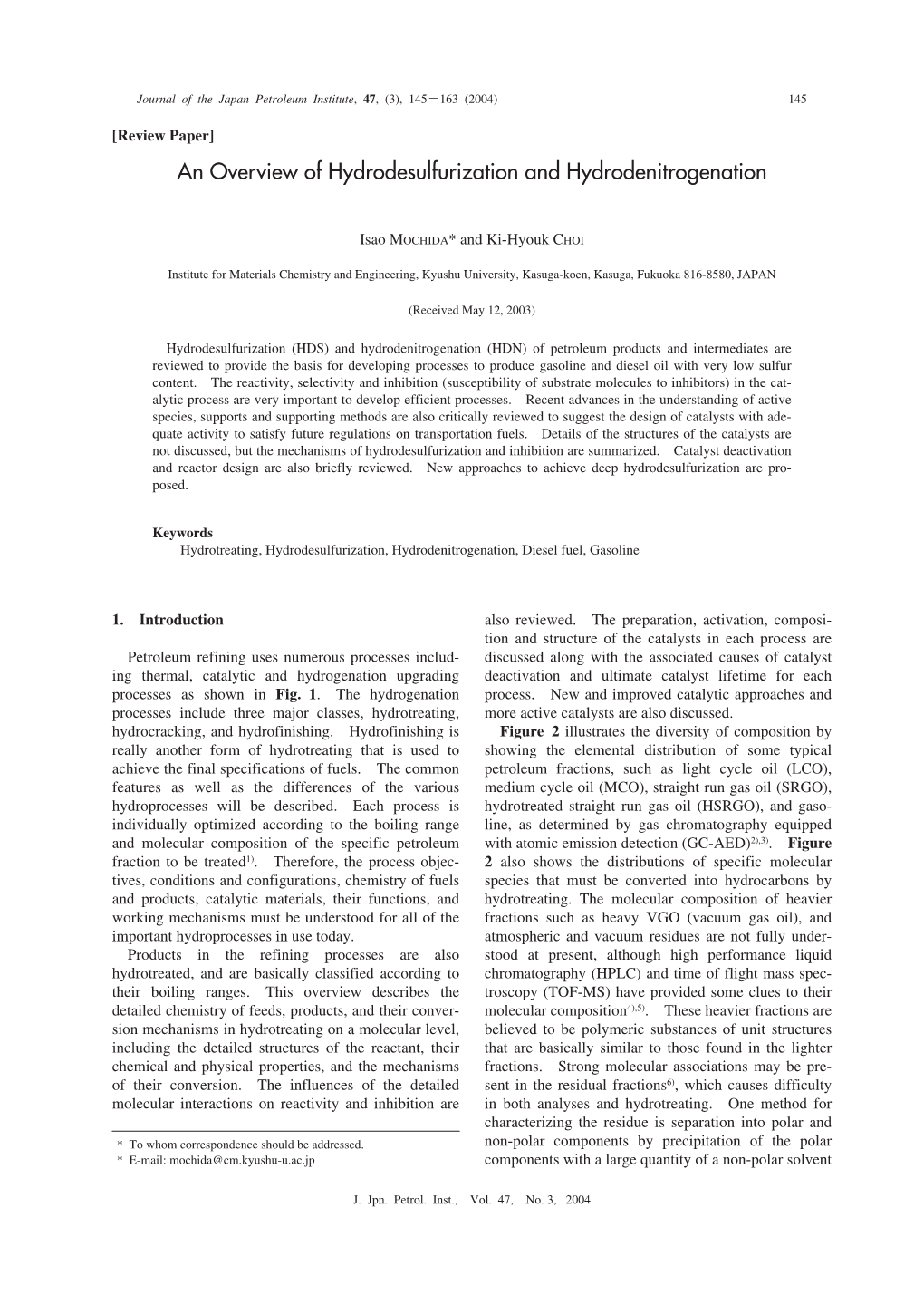
Load more
Recommended publications
-
Catalyst Precursors for Hydrodesulfurization Synthesized in Supercritical Fluids Manuel Théodet
New generation of ”bulk” catalyst precursors for hydrodesulfurization synthesized in supercritical fluids Manuel Théodet To cite this version: Manuel Théodet. New generation of ”bulk” catalyst precursors for hydrodesulfurization synthesized in supercritical fluids. Material chemistry. Université Sciences et Technologies - Bordeaux I,2010. English. NNT : 2010BOR14092. tel-00559113 HAL Id: tel-00559113 https://tel.archives-ouvertes.fr/tel-00559113 Submitted on 24 Jan 2011 HAL is a multi-disciplinary open access L’archive ouverte pluridisciplinaire HAL, est archive for the deposit and dissemination of sci- destinée au dépôt et à la diffusion de documents entific research documents, whether they are pub- scientifiques de niveau recherche, publiés ou non, lished or not. The documents may come from émanant des établissements d’enseignement et de teaching and research institutions in France or recherche français ou étrangers, des laboratoires abroad, or from public or private research centers. publics ou privés. Distributed under a Creative Commons Attribution - NonCommercial - NoDerivatives| 4.0 International License N° d’ordre : 4092 THÈSE présentée à L’UNIVERSITÉ BORDEAUX I ÉCOLE DOCTORALE DES SCIENCES CHIMIQUES Par Manuel THEODET Ingénieur ENSCPB POUR OBTENIR LE GRADE DE DOCTEUR SPÉCIALITÉ : Physico-Chimie de la Matière Condensée ___________________ NOUVELLE GENERATION DE PRECURSEURS « BULK » DE CATALYSEUR D’HYDRODESULFURATION SYNTHETISES EN MILIEU FLUIDE SUPERCRITIQUE ___________________ NEW GENERATION OF « BULK » CATALYST PRECURSORS FOR HYDRODESULFURIZATION SYNTHESIZED IN SUPERCRITICAL FLUIDS ___________________ Co-superviseurs de recherche : Cristina Martínez & Cyril Aymonier Soutenue le 03 Novembre 2010 Après avis favorable de : M. E. PALOMARES, Professor, UPV, Valencia, Spain Rapporteurs M. M. TÜRK, Professor, KIT, Karlsruhe, Germany Devant la commission d’examen formée de : M. -
Particle Size and Structural Effects in Platinum Electrocatalysis
JOURNAL OF APPLIED ELECTROCHEMISTRY 20 (1990) 537-548 REVIEWS OF APPLIED ELECTROCHEMISTRY 23 Particle size and structural effects in platinum electrocatalysis S. MUKERJEE Tata Energy Research Institute, 7 Jor Bagh, New Delhi-llO 003, India Received 4 January 1989; revised 18 October 1989 Of the several factors which influence electrocatalytic activity, particle size and structural effects are of crucial importance, but their effects and mechanism of interaction, vis-a-vis overall performance, have been, at best, vaguely understood. The situation is further aggravated by the use of a wide range of experimental conditions resulting in non-comparable data. This paper attempts systematically to present the developments to date in the understanding of these structural interactions and to point out areas for future investigation. The entire content of this review has been examined from the context of the highly dispersed Pt electrocatalyst, primarily because it has been examined in the greatest detail. In the first two sections a general idea on the correlations between surface microstructure and geometric model is presented. Subsequently, indicators of a direct correlation between particle size and catalyst support synergism are considered. The structural and particle size effect on electro- catalysis is examined from the point of view of anodic hydrogen oxidation and cathodic oxygen reduction reactions. The hydrogen and oxygen chemisorption effects, presented with the discussion on the anodic and cathodic electrocatalytic reactions, provide important clues toward resolving some of the controversial findings, especially on the dependence of particle size on the anodic hydrogen oxidation reaction. Finally, the effect of alloy formation on the cathodic oxygen reduction reaction is discussed, providing insights into the structural aspect. -
Burton Introduces Thermal Cracking for Refining Petroleum John Alfred Heitmann University of Dayton, [email protected]
University of Dayton eCommons History Faculty Publications Department of History 1991 Burton Introduces Thermal Cracking for Refining Petroleum John Alfred Heitmann University of Dayton, [email protected] Follow this and additional works at: https://ecommons.udayton.edu/hst_fac_pub Part of the History Commons eCommons Citation Heitmann, John Alfred, "Burton Introduces Thermal Cracking for Refining Petroleum" (1991). History Faculty Publications. 92. https://ecommons.udayton.edu/hst_fac_pub/92 This Encyclopedia Entry is brought to you for free and open access by the Department of History at eCommons. It has been accepted for inclusion in History Faculty Publications by an authorized administrator of eCommons. For more information, please contact [email protected], [email protected]. 573 BURTON INTRODUCES THERMAL CRACKING FOR REFINING PETROLEUM Category of event: Chemistry Time: January, 1913 Locale: Whiting, Indiana Employing high temperatures and pressures, Burton developed a large-scale chem ical cracking process, thus pioneering a method that met the need for more fuel Principal personages: WILLIAM MERRIAM BURTON (1865-1954), a chemist who developed a commercial method to convert high boiling petroleum fractions to gas oline by "cracking" large organic molecules into more useful and marketable smaller units ROBERT E. HUMPHREYS, a chemist who collaborated with Burton WILLIAM F. RODGERS, a chemist who collaborated with Burton EUGENE HOUDRY, an industrial scientist who developed a procedure us ing catalysts to speed the conversion process, which resulted in high octane gasoline Summary of Event In January, 1913, William Merriam Burton saw the first battery of twelve stills used in the thermal cracking of petroleum products go into operation at Standard Oil of Indiana's Whiting refinery. -
Monolithic Substrate Support Catalyst Design Considerations for Steam Methane Reforming Operation
Rev Chem Eng 2017; aop Luqmanulhakim Baharudin and Matthew James Watson* Monolithic substrate support catalyst design considerations for steam methane reforming operation DOI 10.1515/revce-2016-0048 as compared to other processes discussed by Baharudin Received October 16, 2016; accepted March 10, 2017 and Watson (2017). In this review paper, a monolithic structured packing for steam methane reforming (SMR) Abstract: This paper reviews the research undertaken to reactor will be studied. This novel reactor packing offers study the design criteria that address the monolithic sup- the benefits of overcoming the heat conduction limitation port structure requirements in steam reforming opera- in the current industrial-scale reformers, process intensi- tion for the effective mass transfer of process gases to the fication for an overall plant optimization, and materializ- active sites and effective conductive heat transfer through ing the concept of compact reformer. SMR is expressed by tube wall to the active catalytic areas, as well as low pres- (Saito et al. 2015). sure drop operation. Design considerations include selec- tion of substrate materials that possess good mechanical CH42+↔HO CO + 3 H2 (1) strength to withstand the severe reaction conditions and prevent catalyst crushing that would lead to carbon for- In a nutshell, a monolithic structure is a single structure mation and catalyst deactivation, and excessive heating consisting of thin-walled narrow channels that are paral- of the tube that results in hot spots which is fatal to tube lel to each other (Heck et al. 2001, Roy et al. 2004, Zamani- lifetime. The support’s mechanical properties are listed yan et al. -
THE H-OIL PROCESS: a Worldwxide LEADER in VACUUM RESIDUE HYDROPROCESSING” \ ^
—t&CR I'd, D 3 YJj TT-097 CONEXPO ARPEL '96 . i ' 1 "THE H-OIL PROCESS: A WORLDWXiDE LEADER IN VACUUM RESIDUE HYDROPROCESSING” \ ^ J.J. Colyar1 L.I. Wisdom2 A. Koskas3 SUMMARY With the uncertainty of market trends, refiners will need to hedge their investment strategies in the future by adding processing units that provide them with flexibility to meet the changing market. The various process configurations involving the H-Oil® Process described in this paper have been tested commercially and provide the refiner with the latest state of the art technology. ABSTRACT The H-Oil® Process is a catalytic hydrocracking process, invented by HRI, Inc., a division of IFP Enterprises, Inc. which is used to convert and upgrade petroleum residua and heavy oils. Today the H-Oil Process accounts for more than 50 percent of the worldwide vacuum residue hydroprocessing market due to its unique flexibility to handle a wide variety of heavy crudes 'while producing clean transportation fuels. The process is also flexible in terms of changes in yield selectivity and product quality. The unconverted vacuum residue from the process can be utilized for fuel oil production, blended into asphalt, routed to resid catalytic cracking, directly combusted or gasified to produce hydrogen. This paper will discuss additional background information on the H-Oil Process, some of the key advances made to the process and applications for the Latin America market. The paper will also discuss the status of recent commercial plants which are in operation or which are under design or construction and which utilize these new advances. -
Optimization of Refining Alkylation Process Unit Using Response
Optimization of Refining Alkylation Process Unit using Response Surface Methods By Jose Bird, Darryl Seillier, Michael Teders, and Grant Jacobson - Valero Energy Corporation Abstract This paper illustrates a methodology to optimize the operations of an alkylation unit based on response surface methods. Trial based process optimization requires the unit to be operated across a wide range of conditions. This approach tends to be opposed by refinery operations as it can disrupt the normal operations of a process unit. Using the methods presented in this paper, the general direction of process improvement is first identified using a first order profit response surface built from available operating data. The performance of the unit is then evaluated at the refinery by making systematic changes to the key factors in the projected direction of process improvement. The operating results are then used to build a localized second order profit response surface to generate a revised set of optimum targets. Multiple linear regression models are used to predict alkylate yield, alkylate octane and Iso-stripper or De-Isobutanizer reboiler duty as a function of key process variables. These models are then used to generate a profit response surface for selection of an optimum target region for step testing at the refinery prior to implementation of the unit targets. 1. Introduction An alkylation unit takes a feed stream with a high olefin content, typically originating from a fluid catalytic cracking (FCC) unit, and adds isobutane (IC4) which reacts with the olefins to produce a high octane alkylate product. Either hydrofluoric or sulfuric acid is used as a catalyst for the alkylation reaction. -
Thermal Stability Analysis of Hydroprocessing Unit A
THERMAL STABILITY ANALYSIS OF HYDROPROCESSING UNIT A Thesis by YONGCHUL CHO Submitted to the Office of Graduate and Professional Studies of Texas A&M University in partial fulfillment of the requirements for the degree of MASTER OF SCIENCE Chair of Committee, M. Sam Mannan Committee Members, Mahmoud M. El-Halwagi Maria A. Barrufet Head of Department, M. Nazmul Karim May 2018 Major Subject: Chemical Engineering Copyright 2018 Yongchul Cho ABSTRACT Thermal stability is one of the most critical safety issues in the hydroprocessing units. Runaway reactions in the units can lead to catastrophic consequences as the reactors are being operated at high temperature and pressure, and the reactor effluent is a highly explosive mixture which contains hydrogen and hydrocarbons. For example, a fire and explosion due to a runaway reaction in a hydrocracking unit caused one death and forty-six injuries in 1997, in California. While the temperature runaway is the topic which has been studied extensively, most of the studies worked on simple reactions and little focused on the complex reactions such as hydroprocessing reactions. Also, in the studies on the hydroprocessing reactions, a lumping kinetic model was used which is less accurate and requires experiments for each application. In this research, the thermal stability of a naphtha hydrotreater will be analyzed by using a commercial process simulator ProMax where a novel mechanistic kinetic model, Single Event Kinetics has been integrated. Also, a simplified model will be established by using the data provided by ProMax for further analysis. The continuity and energy equations and parametric sensitivity equations will be solved by Matlab based on the methodology presented by Morbidelli and Varma. -
Invention and Innovation in the Petroleum Refining Industry
This PDF is a selection from an out-of-print volume from the National Bureau of Economic Research Volume Title: The Rate and Direction of Inventive Activity: Economic and Social Factors Volume Author/Editor: Universities-National Bureau Committee for Economic Research, Committee on Economic Growth of the Social Science Research Council Volume Publisher: Princeton University Press Volume ISBN: 0-87014-304-2 Volume URL: http://www.nber.org/books/univ62-1 Publication Date: 1962 Chapter Title: Invention and Innovation in the Petroleum Refining Industry Chapter Author: John L. Enos Chapter URL: http://www.nber.org/chapters/c2124 Chapter pages in book: (p. 299 - 322) Invention and Innovation in the Petroleum Refining Industry JOHN L. ENOS MASSACHUSETTS INSTITUTE OF TECHNOLOGY AN INNOVATION is the combination of many different activities. Gener- ally an invention is made and recognized, capital is obtained, plant is acquired, managers and workers are hired, markets are developed, and production and distribution take place. As the innovation proceeds the original conception may be altered to make it more amenable to commercial realities. Accomplishing these activities consumes re- sources. At any point in the sequence failure may occur, delaying or even frustrating the innovation. In studying the petroleum refining industry I observed several pro- cessing innovations following one another in time and generating technological progress.' I then sought their origins in terms of the original ideas and the men who conceived them. In this paper I shall discuss the relations between the inventions and the subsequent inno- vations, focusing on the intervals between them, the returns to the inventors and innovators, and the changes in the proportions in which the factors of production in petroleum processing were combined. -
SILICA CATALYSTS High Performance Polyolefin Catalysts & Supports High Performance Polyolefin Catalysts & Supports
SILICA CATALYSTS High Performance Polyolefin Catalysts & Supports High Performance Polyolefin Catalysts & Supports World class PQ is a key global supplier of chrome-on-silica catalysts and modified chrome catalysts, widely used catalysts & supports in the polymerization of ethylene into polyethylene. designed to With a manufacturing history stretching back over give exceptional 200 years, PQ prides itself on being a manufacturer performance within that offers customers; the polyolefin • Consistent product quality market • Reliable product supply • Customised solutions • Expert technical service PQ silica supports are used in the production of • HDPE chrome, Ziegler-Natta and single site catalysts that are subsequently used to manufacture polyethylene, • LLDPE polypropylene and other polymers. These polymers • PP are used in a wide variety of applications including films and sheets, pipes and tubes, blow-moulded containers and automobile parts, and wire and • Gas Phase cable sheathings. • Slurry Phase PQ supports are used in both gas-phase and slurry- phase processes. High Performance Polyolefin Catalysts & Supports THE BENEFITS OF PQ PRODUCTS High Purity As a result of the strict control of raw materials and advanced process technologies, PQ produces silica supports that have low levels of impurities. PQ is the world leader in the production of sodium silicate, a key raw material in the production of silica supports, so the quality of this critical feedstock is directly managed. Uniform Products Through the careful control of critical process steps, PQ produces products that are highly uniform at both a macroscopic level (batch to batch consistency) and a microscopic level (particle to particle uniformity). Customizable Catalysts In addition to chrome-on-silica PQ also offers modified chromium catalysts containing aluminium, titanium and other elements to provide performance enhancements needed for certain end uses, such as reduced induction time and increased activity, melt flow index and ESCR. -
Hydrogen Sulfide Capture: from Absorption in Polar Liquids to Oxide
Review pubs.acs.org/CR Hydrogen Sulfide Capture: From Absorption in Polar Liquids to Oxide, Zeolite, and Metal−Organic Framework Adsorbents and Membranes Mansi S. Shah,† Michael Tsapatsis,† and J. Ilja Siepmann*,†,‡ † Department of Chemical Engineering and Materials Science, University of Minnesota, 421 Washington Avenue SE, Minneapolis, Minnesota 55455-0132, United States ‡ Department of Chemistry and Chemical Theory Center, University of Minnesota, 207 Pleasant Street SE, Minneapolis, Minnesota 55455-0431, United States ABSTRACT: Hydrogen sulfide removal is a long-standing economic and environ- mental challenge faced by the oil and gas industries. H2S separation processes using reactive and non-reactive absorption and adsorption, membranes, and cryogenic distillation are reviewed. A detailed discussion is presented on new developments in adsorbents, such as ionic liquids, metal oxides, metals, metal−organic frameworks, zeolites, carbon-based materials, and composite materials; and membrane technologies for H2S removal. This Review attempts to exhaustively compile the existing literature on sour gas sweetening and to identify promising areas for future developments in the field. CONTENTS 4.1. Polymeric Membranes 9785 4.2. Membranes for Gas−Liquid Contact 9786 1. Introduction 9755 4.3. Ceramic Membranes 9789 2. Absorption 9758 4.4. Carbon-Based Membranes 9789 2.1. Alkanolamines 9758 4.5. Composite Membranes 9790 2.2. Methanol 9758 N 5. Cryogenic Distillation 9790 2.3. -Methyl-2-pyrrolidone 9758 6. Outlook and Perspectives 9791 2.4. Poly(ethylene glycol) Dimethyl Ether 9759 Author Information 9792 2.5. Sulfolane and Diisopropanolamine 9759 Corresponding Author 9792 2.6. Ionic Liquids 9759 ORCID 9792 3. Adsorption 9762 Notes 9792 3.1. -
Heterogeneous Catalysis Using Supported Metal Nanoparticles for Environmental Applications
Heterogeneous catalysis using supported metal nanoparticles for environmental applications Thesis submitted in accordance with the regulations of the University of Cardiff for the degree of Doctor of Philosophy By Khaled Fadhi F. Alshammari School of Chemistry Cardiff University 2018 Declaration This work has not been submitted in substance for any other degree or award at ths or any other university or place of learning, nor is being submitted concurrently in candidature for any degree or other award. Signed………………………………………… (candidate) Date …………………..... Statement 1 This thesis is being submitted in partial fulfilment of the requirements for the degree of ……PhD……….. (insert MCh, MD, MPhil, PhD, etc, as appropriate). Signed………………………………………… (candidate) Date …………………..... Statement 2 This thesis is the result of my own independent work/investigation, except where otherwise stated, and the thesis has not been edited by a third party beyond what is permitted by Cardiff University’s Policy on the Use of Third-Party Editors by Research Degree Students. Other sources are acknowledged by explicit references. The views expressed are my own. Signed………………………………………… (candidate) Date …………………..... Statement 3 I hereby give consent for my thesis, if accepted, to be available online in the University’s Open Access repository and for inter-library loan, and for the title and summary to be made available to outside organisations. Signed………………………………………… (candidate) Date …………………..... Statement 4: Previously Approved Bar on Access. I hereby give consent for my thesis, if accepted, to be available online in the University’s Open Access repository and for inter-library loans after expiry of a bar on access previously approved by the Academic Standards and Quality Committee. -
Graphene As Catalyst Support: the Influences of Carbon Additives and Catalyst Preparation Methods on the Performance of PEM Fuel Cells
CARBON 58 (2013) 139– 150 Available at www.sciencedirect.com journal homepage: www.elsevier.com/locate/carbon Graphene as catalyst support: The influences of carbon additives and catalyst preparation methods on the performance of PEM fuel cells Angela Marinkas a, Francesco Arena a, Jens Mitzel a,Gu¨ nther M. Prinz b, Angelika Heinzel c, Volker Peinecke c, Harald Natter a,* a Saarland University, Physical Chemistry, Campus Geb. B2 2, D-66123 Saarbru¨ cken, Germany b University Duisburg-Essen, Experimental Physics and CENIDE, Lotharstraße 1, D-47057 Duisburg, Germany c ZBT Duisburg, The Fuel Cell Research Center GmbH, Carl-Benz-Str. 201, D-47057 Duisburg, Germany ARTICLE INFO ABSTRACT Article history: The reduction of the platinum amount for efficient PEM (polymer electrolyte membrane) Received 17 November 2012 fuel cells was achieved by the use of graphene/carbon composites as catalyst support. Accepted 19 February 2013 The influences of the carbon support type and also of the catalyst preparation method Available online 27 February 2013 on the fuel cell performance were investigated with electrochemical, spectroscopic and microscopic techniques. Using pure graphene supports the final catalyst layer consists of a dense and well orientated roof tile structure which causes strong mass transport limita- tions for fuels and products. Thus the catalysts efficiency and finally the fuel cell perfor- mance were reduced. The addition of different carbon additives like carbon black particles or multi-walled carbon nanotubes (MWCNT) destroys this structure and forms a porous layer which is very efficient for the mass transport. The network structure of the catalyst layer and therefore the performance depends on the amount and on the morphol- ogy of the carbon additives.