Presentation 80A Stranges Germany
Total Page:16
File Type:pdf, Size:1020Kb
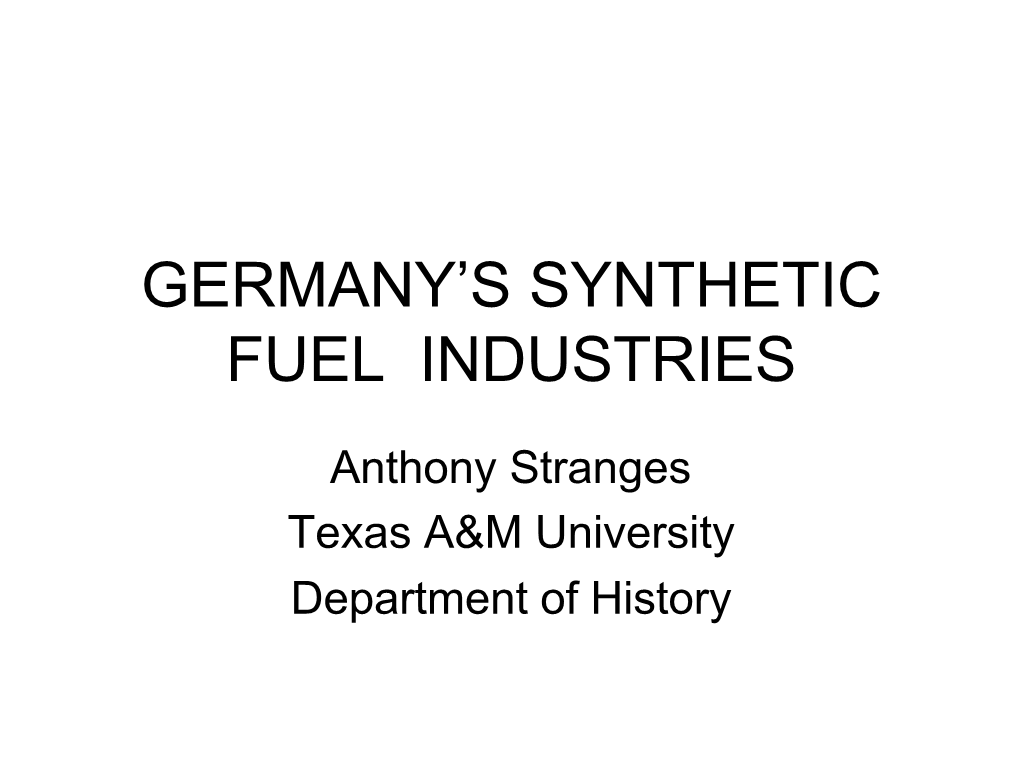
Load more
Recommended publications
-
Recent Advances in Direct Coal Liquefaction
Energies 2010, 3, 155-170; doi:10.3390/en3020155 OPEN ACCESS energies ISSN 1996-1073 www.mdpi.com/journal/energies Review Recent Advances in Direct Coal Liquefaction Hengfu Shui 1, Zhenyi Cai 1 and Chunbao (Charles) Xu 2,* 1 School of Chemistry and Chemical Engineering, Anhui University of Technology, Maanshan 243002, Anhui, China; E-Mails: [email protected] (H.S.); [email protected] (Z.C.) 2 Department of Chemical Engineering, Lakehead University, Thunder Bay, Ontario P7B 5E1, Canada * Author to whom correspondence should be addressed; E-Mail: [email protected]; Tel.: +1-807-343-8761; Fax: +1-807-343-8928. Received: 16 November 2009 / Accepted: 19 January 2010 / Published: 27 January 2010 Abstract: The growing demand for petroleum, accompanied by the declining petroleum reserves and the concerns over energy security, has intensified the interest in direct coal liquefaction (DCL), particularly in countries such as China which is rich in coal resources, but short of petroleum. In addition to a general introduction on the mechanisms and processes of DCL, this paper overviews some recent advances in DCL technology with respect to the influencing factors for DCL reactions (temperature, solvent, pressure, atmospheres, etc.), the effects of coal pre-treatments for DCL (swelling, thermal treatment, hydrothermal treatment, etc.), as well as recent development in multi-staged DCL processes, DCL catalysts and co-liquefaction of coal with biomass. Keywords: direct coal liquefaction (DCL); processes; influencing factors; coal pre-treatment; catalysts; co-liquefaction; biomass 1. Introduction Due to the rapid increase in demand for petroleum and its declining reserves, the concern over energy security has intensified the interest in coal liquefaction, especially for those countries which are short of oil resources but have abundant coal reserves, such as the United States and China, etc. -
Unit / Unidad 9
UNIT / UNIDAD 9 GRAMMAR PRACTICE / PRÁCTICA DE GRAMÁTICA Actividad 1 1. My name is Michael. I __was born__ in Liverpool but at the moment I __am living__ in London. Sometimes I __work__ inside and sometimes outside. I often __drive__ a car or a motorbike. I __wear__ a uniform. At the moment I __am walking__ down the street because there __was__ a phone call a quarter of an hour ago about some people who __were__ in a bar making a lot of trouble. I __don’t earn__ a lot of money but I __like__ my job. 2. What is his job? He is a policeman Actividad 2 Nefertiti / artist? Was Nefertiti an artist? No, she wasn’t. She was a queen Beethoven / Germany? Was Beethoven born in Germany? Yes, he was 1. Picasso/composer? Was Picasso a composer? No, he wasn’t. He was a painter 2. Paul Newman/writer? Was Paul Newman a writer? No, he wasn’t. He was an actor 3. Nelson Mandela/Gandhi/politicians? Were Nelson Mandela and Gandhi politicians? Yes, they were 4. The Beatles/actors? Were The Beatles actors? No, they weren’t. They were singers 5. Pele/Argentina? Was Pele from Argentina? No, he wasn’t. He was from brazil Actividad 3 1. Where were you born? I was born … in Lisbon 2. What is your job? I am a … teacher 3. How old were you on your last birthday? I was … forty-three 4. What would you like to do at the weekend? I would like to … go to the beach 1 5. -
Liquid Coal As a Green Energy: a Review
International Journal of Engineering and Technical Research (IJETR) ISSN: 2321-0869, Volume-2, Issue-3, March 2014 LIQUID COAL AS A GREEN ENERGY: A REVIEW Saurabh Prakash, Ghanshyam Paswan & Kumar Nikhil offers significant reductions in vehicle emissions such as Abstract— Fuel market is growing more rapidly than the oxides of nitrogen, volatile organic compounds and carbon fuel production of the world. Simultaneously coal to liquid fuel mono- oxide. technology is growing and covers some of the fuel demand of the world. A cost effective technology uses the coal with low carbon value, which is not much useful in its natural form and II. METHODOLOGY the manipulated form leads to the development of liquid coal. Most of process have not been industrialized. The raw gas is The process of liquid coal production is coal to liquid or converted into liquid is an idea along with removal of sulphur, gas to liquid conversion. There are mainly two methods of phosphorous impurities which does not pollutes air so, liquid coal production. ultimately environmentally safe. A. Direct coal liquefaction process. Index terms—Bergius process, fischer- tropsch reactor, B. Indirect coal liquefaction process. liquefaction, liquefied coal, syngas. A. Direct coal liquefaction process: I. INTRODUCTION The direct coal liquefaction processes are hydrogenation Liquid coal is a manipulated component used as a fuel by and carbonisation[3]. the process of liquefaction of coal. Liquid coal is used as an alternative to oil. Coal liquefaction is particularly suited to countries that rely heavily on oil imports and have large a) Hydrogenation: domestic reserve of coal [1]. The basic method of producing Bergius process developed by Friedrich bergius in 1913 , liquid coal is gasification of coal with little oxygen and water is a method for direct conversion of coal to liquid by vapour [2]. -
Friedrich Bergius – Chemist, Pioneering Researcher and Nobel Prize Laureate
Friedrich Bergius – chemist, pioneering researcher and Nobel Prize laureate Friedrich Bergius (born 1884 in Goldschmieden, Silesia; died 1949 in Buenos Aires) was a chemist and Nobel Prize laureate. He worked for one of the predecessor companies of Evonik from 1914 to 1918, including as a member of the executive board of Th. Goldschmidt AG from 1916 to 1918. In 1931, Friedrich Bergius received the Nobel Prize for Chemistry jointly with Carl Bosch "in recognition of their contributions to the invention and development of chemical high- Friedrich Bergius pressure methods." Thanks to his pioneering basic research, Friedrich Bergius is now considered one of the most important German chemists of the 20th century. His research continues to influence some of the chemicals produced at Evonik to this day. Bergius began his studies of chemistry in Breslau in 1903 and completed his doctoral studies in Leipzig in 1907. Reflecting the influence of Nobel laureate Fritz Haber, his professorial thesis was entitled "Application of high pressure in chemical processes and simulation of the genesis of coal." Written at the dawn of the automotive and aerospace age, Bergius’ work turned out to be prescient. He believed to have found a way to "liquidize" the rich coal deposits in Germany under high pressure to turn them into gasoline. Since Karl Goldschmidt, the chairman of the Th. Goldschmidt AG executive board, shared the conviction that gasoline would dominate the future, he provided Bergius with the means to implement his findings on an industrial scale. In 1913, Bergius therefore came to Essen, where he was appointed the head of research in a new, specially built laboratory and advanced to deputy member of the executive board of Th. -
Industrial Hydrocarbon Processes
Handbook of INDUSTRIAL HYDROCARBON PROCESSES JAMES G. SPEIGHT PhD, DSc AMSTERDAM • BOSTON • HEIDELBERG • LONDON NEW YORK • OXFORD • PARIS • SAN DIEGO SAN FRANCISCO • SINGAPORE • SYDNEY • TOKYO Gulf Professional Publishing is an imprint of Elsevier Gulf Professional Publishing is an imprint of Elsevier The Boulevard, Langford Lane, Kidlington, Oxford OX5 1GB, UK 30 Corporate Drive, Suite 400, Burlington, MA 01803, USA First edition 2011 Copyright Ó 2011 Elsevier Inc. All rights reserved No part of this publication may be reproduced, stored in a retrieval system or transmitted in any form or by any means electronic, mechanical, photocopying, recording or otherwise without the prior written permission of the publisher Permissions may be sought directly from Elsevier’s Science & Technology Rights Department in Oxford, UK: phone (+44) (0) 1865 843830; fax (+44) (0) 1865 853333; email: [email protected]. Alternatively you can submit your request online by visiting the Elsevier web site at http://elsevier.com/locate/ permissions, and selecting Obtaining permission to use Elsevier material Notice No responsibility is assumed by the publisher for any injury and/or damage to persons or property as a matter of products liability, negligence or otherwise, or from any use or operation of any methods, products, instructions or ideas contained in the material herein. Because of rapid advances in the medical sciences, in particular, independent verification of diagnoses and drug dosages should be made British Library Cataloguing in Publication Data -
Coal Liquefaction
http://uu.diva-portal.org This is an author produced version of a paper published in International journal of energy research. This paper has been peer-reviewed but does not include the final publisher proof-corrections or journal pagination. Citation for the published paper: Höök, M. & Aleklett, K. ”A review on coal-to-liquid fuels and its coal consumption” International journal of energy research, 2010, Vol. 34, Issue 10: 848-864 URL: http://dx.doi.org/10.1002/er.1596 Access to the published version may require subscription. Published in International Journal of Energy Research Volume 34, Issue 10, October 2010, Pages 848-864 http://dx.doi.org/10.1002/er.1596 A review on coal to liquid fuels and its coal consumption Mikael Höök*, Kjell Aleklett* Corresponding author: [email protected], phone: +46 18-471 7643, fax: +46 18-4713513 * Uppsala University, Global Energy Systems, Department of physics and astronomy, Box 535, SE-751 21, Lägerhyddsvägen 1, Sweden, http://www.fysast.uu.se/ges Abstract Continued reliance on oil is unsustainable and this has resulted in interest in alternative fuels. Coal-to-Liquids (CTL) can supply liquid fuels and have been successfully used in several cases, particularly in South Africa. This article reviews CTL theory and technology. Understanding the fundamental aspects of coal liquefaction technologies are vital for planning and policy-making, as future CTL systems will be integrated in a much larger global energy and fuel utilization system. Conversion ratios for CTL are generally estimated to be between 1-2 barrels/ton coal. This puts a strict limitation on future CTL capacity imposed by future coal production volumes, regardless of other factors such as economics, emissions or environmental concern. -
Principles of Selectivity in Fischer-Tropsch SYNTHESIS Hans Schulz Engler-Bunte-Institute, University of Karlsruhe Kaiserstrasse 12, 76128 Karlsruhe, Germany
DGMK/SCI-Conference „Synthesis Gas Chemistry", October 4-6, 2006, Dresden, Germany Principles of Selectivity in Fischer-Tropsch SYNTHESIS Hans Schulz Engler-Bunte-Institute, University of Karlsruhe Kaiserstrasse 12, 76128 Karlsruhe, Germany Abstract The detailed selectivity of Fischer-Tropsch synthesis with iron and cobalt as catalysts with high temporal resolution has been determined and used to derive the values of probability of chain growth, chain branching and olefin/paraffin molar ratio as a function of carbon number and time. Catalyst reassembling and self-organization of the Fischer-Tropsch regime are i nvestigated. The basic principle of Fischer-Tropsch synthesis, suppression of desorption of growing chains is disclosed. This frustration governs FT-synthesis of the otherwise different systems with iron and cobalt. The advanced characterization of sites and elementary reactions (specifically with cobalt) is thought to be a more realistic basis for future theoretical calculations. Diesel fuel through Fischer-Tropsch synthesis The present interest in Fischer-Tropsch synthesis focuses on the production of Diesel fuel. Competing in coal liquefaction with hydrogenation [1], the FT-route now is superior because the fuel is very clean and exhibits excellent performance in the combustion engine (TABLE 1). However, the maximum selectivity is only ~ 40% C, as shown in Fig. 1 on the basis of calculating the theoretical product composition, assuming ideal polymerization kinetics with carbon number independent growth probability [2]. The overall Diesel selectivity can be increased to ~ 60% by running the FT-synthesis at high paraffin-wax selectivity (high growth probability pg) and mildly converting the paraffin wax through ideal hydrocracking. TABLE 1 Gas oils from direct coal liquefaction and Fischer-Tropsch synthesis Gas oil from coal hydrogenation*): Highly aromatic, Atomic H/C-ratio: 1.3 Phenols: 16 wt-% Oxygen = 3 wt.-%. -
Fischer-Tropsch Fuels from Coal, Natural Gas, and Biomass: Background and Policy
Order Code RL34133 Fischer-Tropsch Fuels from Coal, Natural Gas, and Biomass: Background and Policy Updated March 27, 2008 Anthony Andrews Specialist in Energy and Energy Infrastructure Policy Resources, Science, and Industry Division Jeffrey Logan Specialist in Energy Policy Resources, Science, and Industry Division Fischer-Tropsch Fuels from Coal, Natural Gas, and Biomass: Background and Policy Summary As the price of crude oil sets a record high, liquid transportation fuels synthesized from coal, natural gas, and biomass are proposed as one solution to reducing dependency on imported petroleum and strained refinery capacity. The technology to do so developed from processes that directly and indirectly convert coal into liquid fuel. Congress now faces decisions on whether, and to what extent, it should support such a solution. Lacking domestic petroleum resources, but abundant in coal, Germany built synthetic fuel plants during World War II that employed the Bergius coal hydrogenation process (direct liquefaction), and Fischer-Tropsch synthesis (indirect). The United States attempted to capitalize on the German experience after World War II. Despite considerable investment in synthetic fuel research and development, the United States cut support for commercialization when crude oil prices dropped and supplies stabilized in the mid-1980s. Since then, several synthetic fuels plants have been constructed around the world that convert coal, natural gas, or biomass to liquid fuels using the Fischer-Tropsch process. Several private ventures in the United States are now studying the feasibility of constructing Fischer-Tropsch synthetic fuel plants based on coal, natural gas, and biomass. Proposals to expand the use of coal to synthesize transportation fuels have generated much opposition, particularly because the carbon dioxide (CO2) produced in the Fischer-Tropsch process is a greenhouse gas associated with global warming. -
List of Nobel Laureates 1
List of Nobel laureates 1 List of Nobel laureates The Nobel Prizes (Swedish: Nobelpriset, Norwegian: Nobelprisen) are awarded annually by the Royal Swedish Academy of Sciences, the Swedish Academy, the Karolinska Institute, and the Norwegian Nobel Committee to individuals and organizations who make outstanding contributions in the fields of chemistry, physics, literature, peace, and physiology or medicine.[1] They were established by the 1895 will of Alfred Nobel, which dictates that the awards should be administered by the Nobel Foundation. Another prize, the Nobel Memorial Prize in Economic Sciences, was established in 1968 by the Sveriges Riksbank, the central bank of Sweden, for contributors to the field of economics.[2] Each prize is awarded by a separate committee; the Royal Swedish Academy of Sciences awards the Prizes in Physics, Chemistry, and Economics, the Karolinska Institute awards the Prize in Physiology or Medicine, and the Norwegian Nobel Committee awards the Prize in Peace.[3] Each recipient receives a medal, a diploma and a monetary award that has varied throughout the years.[2] In 1901, the recipients of the first Nobel Prizes were given 150,782 SEK, which is equal to 7,731,004 SEK in December 2007. In 2008, the winners were awarded a prize amount of 10,000,000 SEK.[4] The awards are presented in Stockholm in an annual ceremony on December 10, the anniversary of Nobel's death.[5] As of 2011, 826 individuals and 20 organizations have been awarded a Nobel Prize, including 69 winners of the Nobel Memorial Prize in Economic Sciences.[6] Four Nobel laureates were not permitted by their governments to accept the Nobel Prize. -
Kinetic Modelling for Coal Liquefaction Process
International Journal of Engineering Research & Technology (IJERT) ISSN: 2278-0181 Vol. 3 Issue 5, May - 2014 Kinetic Modelling for Coal Liquefaction Process Rohitbabu .G. Nalwala[1]; Pravat Kumar Rana[2]; Deepak H. Shukla[3] Chemical Engineering Department, Gharda Institute of Technology, At/Po-Lavel, Tal-Khed, Dist.-Ratnagiri, Maharashtra (India) Abstract- In 1913 Bergius developed the coal hydro the principal products can be high molecular mass fuels, liquefaction. In 1917 there were clear indication of decline in distillate fuel Oils, gasoline, or chemical feedstocks. domestic oil production and possibility of international shortage The products of both indirect and direct liquefaction have was realized. Around to be 1970 the chevron started coal higher energy content than coal. Coal typically contains 60 liquefaction process. He had designed and executed the wt% of the heating value of the liquefied products. The production of synthetic fuel, but had not given any kinetic model for monitoring the reaction. Our main focus is on to development liquids produced by the two methods are very different in a kinetic model of reaction taking place and estimating the chemical composition. Synthesis gas conversion processes kinetic parameter like rate constant, order of the reaction using give saturated hydrocarbon liquids, whereas the products of optimization technique like regression, PSO (Particle Swamp direct liquefaction are highly aromatic. These chemical Optimization) validating it with experimental values. The differences affect the end use. Indirect liquefaction provides validating incorporate kinetic rate constant, conversion to cross high-quality diesel fuel and intermediates for olefin verify the result obtained through optimization. production; direct liquefaction yields high-octane gasoline and Scope of this work is to get a better insight of coal excellent feedstocks for aromatic chemicals. -
Heidelberg Nobel Prize Winners
Heidelberg Nobel Prize Winners Christoph Mager bert Bunsen in Heidelberg and Hermann thesising fuel from carbon liquefi ed at ᕡ The Nobel Prize von Helmholtz in Berlin. After spend- high temperatures and pressures. After ing time in Breslau (Wrocław) and Kiel, studying under the Nobel Prize winners The Nobel Prize is the world’s most fa- he was appointed professor at the De- Walter Nernst and Fritz Haber, in the mous and most coveted award. Founded by the Swedish industrialist Alfred Nobel partment of Physics and Radiology in 1920s Bergius set up a carbon chemistry (1833-1895), since 1901 the prizes have Heidelberg, where he remained until his laboratory in the vicinity of BASF in been awarded in the fi ve categories che- retirement in 1931 ᕢ. From around Ludwigshafen. The award winning mistry, physiology or medicine, physics, li- 1908, with his “Deutsche Physik” he work of Carl Bosch was the implemen- terature, and peace. According to Nobel’s openly opposed modern theoretical tation of the high pressure synthesis of testament wishes, the prize is to be awar- work, such as that of Albert Einstein, ammonia, which is used as the basis of ded annually to the person “who, during which he condemned as “Jewish”. After fertiliser and explosives. After his doc- the preceding year, shall have conferred the greatest benefi t on mankind.“ In World War II, his involvement in Na- torate in 1899 he moved to BASF awarding the Nobel Prizes “no considera- tional Socialism was not punished on where he gradually withdrew from ac- tion whatever shall be given to the natio- the grounds of his age. -
Friedrich Bergius and the Rise of the German Synthetic Fuel Industry
Friedrich Bergius and the Rise of the German Synthetic Fue nI ustry By Anthony N. Stranges* G ERMANY HAS VIRTUALLY NO petroleumdeposits. Prior to the twen- tieth century that lack of a liquid fuel was not a serious problem, because Germany possessed abundantcoal reserves. Coal provided for commercial and home heating; it also fulfilled the needs of industryand the military,particularly the navy. In the first decade of the twentieth century, Germany's energy requirements began to change. Two reasons were especially important. First, Germany be- came increasinglydependent on gasoline and diesel oil engines. The appearance of automobiles, trucks, and then airplanes made a plentiful supply of gasoline absolutely essential; moreover, ocean-going ships increasingly used diesel oil rather than coal as their energy source. Second, Germany's continuing indus- trialization and urbanizationmagnified the shortcomings of coal as an energy source. German scientists and engineers began to replace coal with smokeless liquid fuels, which not only were cleaner burningand more convenient to handle but also had a higher energy content. Petroleumwas clearly the fuel of the future, and to insure that Germanywould never be without it, her scientists and engineers created a domestic source of that fuel. From a plentiful natural substance, coal, they synthesized petroleum. Of the several processes the Germansused to convert coal into petroleum, high- pressure coal hydrogenationwas the most highly advanced. Its history falls into two broad periods: 1910-1925, duringwhich time its inventor, FriedrichBergius (1884-1949) developed the process through the first stages of industrialization, and 1925-1945, the period of its further commercial development by German industrialists.