Fatigue of Clamped Connections with Application to a Stem-Handlebar Assembly for Off-Road Bicycles
Total Page:16
File Type:pdf, Size:1020Kb
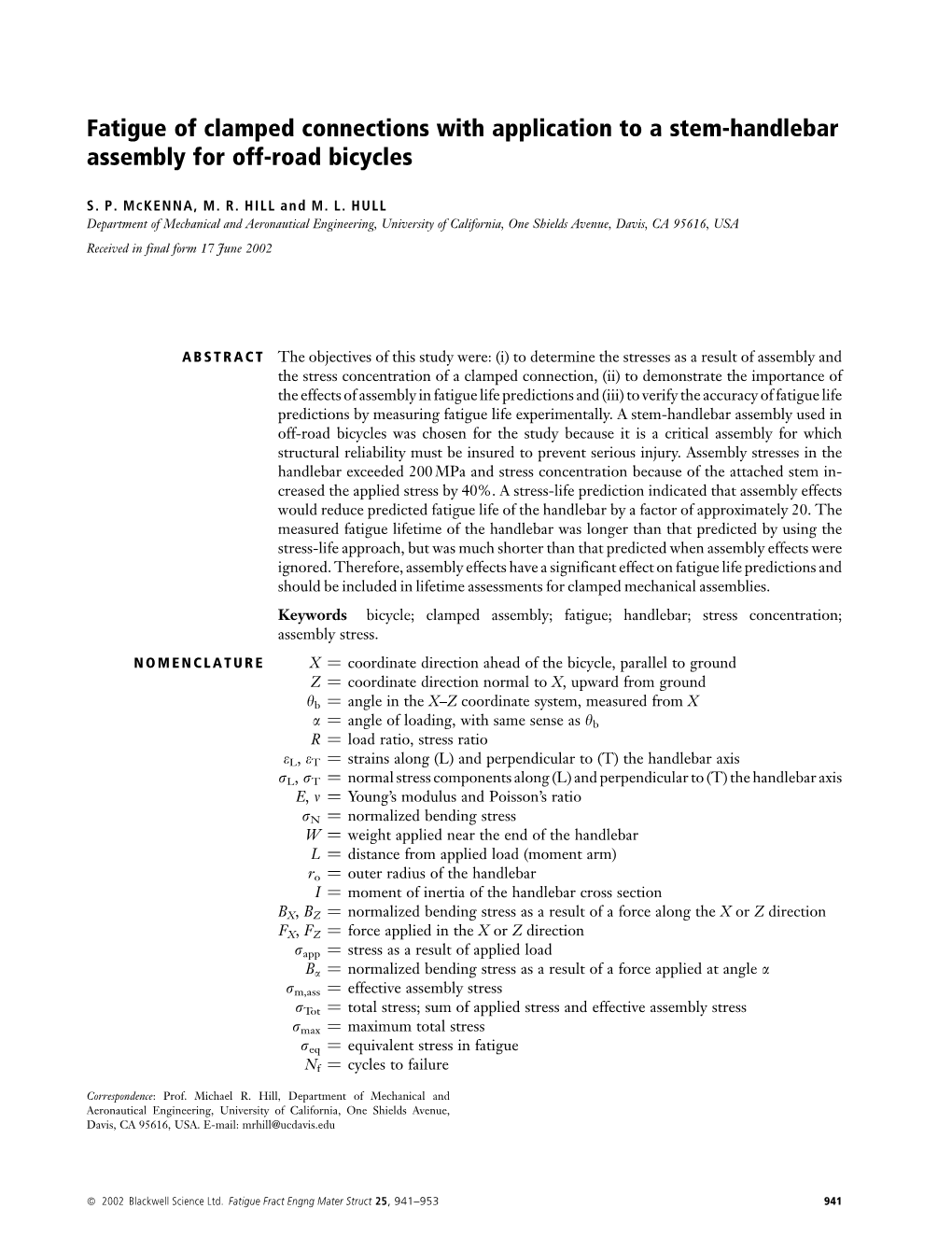
Load more
Recommended publications
-
Bike Tune Up
Bike Tune Up March 14, 2007 Contents What You Will Need For Tuning Your Bicycle: . 3 What if you get in over your head? . 3 Step 1: Adjust Headset . 4 Step 2: Bottom Bracket Adjustment . 6 Pedals . 7 Step 3: Adjust The Front Wheel Bike Hub . 9 Step 4: Adjust Rear Wheel Hubs . 11 Coaster Brake . 11 Three-Speed Wheels . 11 Derailleur-Equipped and BMX Bicycle Wheels . 11 Overhauling . 12 Freewheels - Overhaul, General Care and Troubleshooting . 12 Step 5: Wheel Truing . 14 Unbending A Bicycle Bent Wheel . 15 Flat Spots . 16 Kinks . 17 Broken Spokes . 17 Step 6: Bike Brake Adjustment . 19 If It Is A Sidepull Or Centerpull Brake: . 21 If It Is A Cantilever Bike Brake: . 21 Replacing A Cable . 22 The Brake Pads . 25 Diagnosing Brake Stickiness . 25 Hand Levers . 25 Step 7: Adjust The Rear Derailleur . 27 Replacing a Cable . 29 Step 8: Adjust The Front Derailleur . 31 Replacing a Cable . 33 Step 9: Finish The Tune-Up . 34 1 2 What You Will Need For Tuning Your Bicycle: • This Presentation • An adjustable wrench or set of wrenches • Tongue and groove pliers, sometimes called ”channellocks” • Bicycle bearing cone wrenches (approx. $8 at bike stores) Figure 1: cone wrench • Oil, grease, and non-flammable, non-toxic cleaning solvent • A couple of screwdrivers • A freewheel remover (maybe) Figure 2: Freewheel Remover • Patience - This is the most important ingredient What if you get in over your head? Ask a friend, or call the mechanic at the local bike shop for advice. In the worst case, you would have to take the bike into the shop and pay for professional help, which would still cost less than a complete tune-up anyway. -
2021 Product Catalog
2021 CATALOG BETTER PRODUCTS. BETTER WORLD. BETTER PRODUCTS. BETTER WORLD We love the balance the bicycle brings to the world and its power to make people, communities and the planet healthier. In addition to creating products that make cycling safer and more enjoyable, we pledge time, resources and profits to organizations working for sustainable transportation solutions. COME RIDE WITH US. PLANETBIKE.COM ADVOCACY IN ACTION We believe bicycles add vibrancy to our communities. When we’re out in the world pedaling around, we’re happier and healthier and more deeply connected to the people and places within our neighborhoods. We dream about the day when all towns and cities are more bicycle-friendly and that’s why we give time, resources and profits to organizations working for sustainable transportation solutions. PLANET BIKE IS A PROUD MEMBER OF THE FOLLOWING ORGANIZATIONS: PLANET BIKE IS PROUD TO SUPPORT THE FOLLOWING ORGANIZATIONS: This PDF is interactive. Click one of the links below CONTENTS to go to that product section. BIKE LIGHTS BIKE LOCKS + CABLES HANDLEBAR TAPE & GRIPS Headlights Tape Tail Lights Gel Pads Side Lights Grips Combo Sets BIKE FENDERS BIKE SEATS + BIKE BAGS BIKE BELLS Full Fenders Saddles Recumbent Saddle Covers Fat Tire Fenders Bike Bags Fast Mount Fenders BIKE COMPUTERS BIKE TIRE REPAIR KITS BIKE RACKS BIKE PUMPS + CO2 CYCLING GLOVES + WATER BOTTLE CAGES Floor Pumps Mini Pumps SHOE COVERS Suspension Pumps Tire Gauges CO2 Inflators + Replacement Cartridges BIKE HEADLIGHTS Planet Bike builds headlights that are durable, easy to use, versatile and bright! These lights give you the power to light up the night and even help keep you visible during the day. -
25 Annual Antique & Classic Bicycle Auction
CATALOG PRICE $4.00 Michael E. Fallon / Seth E. Fallon COPAKE AUCTION INC. 266 Rt. 7A/East Main Street - Box 47, Copake, N.Y. 12516 PHONE (518) 329-1142 FAX (518) 329-3369 Email: [email protected] - Website: www.copakeauction.com 25th Annual Antique & Classic Bicycle Auction Featuring the Jim Carpenter and Richard Roy Collections Auction: Saturday April 16, 2016 at 9:00 am Swap Meet: Friday April 15 (dawn ‘til dusk) Preview: Thur.-Fri. April 14-15, 11-5PM - Sat. April 16, 8-9AM TERMS: Everything sold “as is”. No condition reports in descriptions. Bidder must look over every lot to determine condition and authenticity. Cash or Travelers Checks - MasterCard, Visa and Discover Accepted * First time buyers cannot pay by check without a bank letter of credit * 17% buyer's premium, 20% buyer’s premium for LIVEAUCTIONEERS online purchases, 22% buyer’s premium for INVALUABLE & AUCTIONZIP online purchases. National Auctioneers Association - NYS Auctioneers Association CONDITIONS OF SALE 1. Some of the lots in this sale are offered subject to a reserve. This reserve is a confidential minimum price agreed upon by the consignor & COPAKE AUCTION below which the lot will not be sold. In any event when a lot is subject to a reserve, the auctioneer may reject any bid not adequate to the value of the lot. 2. All items are sold "as is" and neither the auctioneer nor the consignor makes any warranties or representations of any kind with respect to the items, and in no event shall they be responsible for the correctness of the catalogue or other description of the physical condition, size, quality, rarity, importance, medium, provenance, period, source, origin or historical relevance of the items and no statement anywhere, whether oral or written, shall be deemed such a warranty or representation. -
Manufacturing of Composite Bicycle Handlebar
Manufacturing of composite bicycle handlebar Peter Mörsky Degree Thesis Plastteknik 2016 EXAMENSARBETE Arcada Utbildningsprogram: Plastteknik Identifikationsnummer: 14616 Författare: Peter Mörsky Arbetets namn: Manufacturing of composite bicycle handlebar Handledare (Arcada): Rene Herrmann Uppdragsgivare: Arcada – Nylands svenska yrkeshögskola Sammandrag: Syftet med detta examensarbete var att undersöka hur det är möjligt att tillverka ett cy- kelstyre ut ur komposit material i Arcada – Nylands svenska yrkeshögskolas utrymmen. Vanligtvis tillverkas styre formade ihåliga sömlösa rör med industriella maskiner som är inte tillgängliga på Arcada. På grund av detta bestämde det att tillverka en expanderande laminerings form. Denna form fungerar på följande vis, ett flätat komposit material kom- binerat med harts i sock form lagas runt en expanderbar blåsa. Blåsan med material runt den lagas in i en form som har en kavitet form av ett styre. När blåsan uppfylls med hjälp av tryckluft så expanderar komposit materialet så att den får formen av formens kavitet. När hartset har härdat kan formen öppnas och färdiga styret kan tas bort. För detta jobb tillverkades två former, den första var en prototyp form var över 20 test lamineringar tillverkades. Baserat på den information som erhållits från test lamineringarna konstrue- rades och byggdes den andra och slutliga full storleks form för styret. En av de viktigaste informationen med testen lagade med prototyp formen var att slutliga formen måste vara ett sluten konstruktion. Med hjälp av ett sluten form konstruktion var det möjligt höja på trycket upp till 7 bar, med högre truck expanderar komposit materialet bättre inne i for- mens kavitet. Några problem uppkom med de första testen som lagades med full storleks form för styret. -
H6526470.Pdf
International OPEN ACCESS Journal Of Modern Engineering Research (IJMER) Design Of Single Fork Of Folding Bicycle 1 2 3 Ankush M. Hatwar , Sharad P. Bargat , Bhavesh A. Bohra 1(Mechanical Department, Abha Gaikwad Patil College Of Engineering Nagpur / Nagpur University, India) 2(Mechanical Department, DES’s College Of Engineering Dhamangaon Rly / Amravati University, India) 3(Mechanical Department, DES’s College Of Engineering Dhamangaon Rly / Amravati University, India) ABSTRACT:- In today’s life the bicycle can play the very important role for daily transportation purpose in human life. The reason behind increase in the importance is because of increased pollution due to automobiles and cost of fuel which is continuously increasing now a day. Also the transport has been one of the most important issues to be deal with in the present day situation as commuting from place to place within the city has become a tedious and an expensive task. It is very difficult to reach the nearest public transport facility and in many cases the destination will be very far from the main roads where the public transport might not be able to commute or it might be very expensive. To overcome a common problem faced by the society, an idea is conceptualized to design a single fork foldable bicycle. The aim of our paper is to design and analysis of single fork of foldable bicycle which fold in compact form which facilitating easy transport and easily park. We already have seen many foldable bicycles in the global market but the main idea of this paper is to provide only one side fork to a foldable bicycle which is light & safe, easy to handle, easy to fold and easy to maintain. -
2013 Holiday Consumer Protection Guide
2013 HOLIDAY CONSUMER PROTECTION GUIDE STATE OF FLORIDA PAM BONDI ATTORNEY GENERAL November 27, 2013 Dear Floridians, Happy Holidays! We are providing this holiday shopping guide to help you, Florida consumers, have a safer and more enjoyable shopping experience. We have included tips on purchasing items online, avoiding charity scams, and helping you stay on budget. We have also included a list of items recalled by the U.S. Consumer Products Safety Commission in the past year because of safety or health issues, including toys and other products that might cause safety issues for children. We urge you to review this list for unsafe items that need to be removed from your home. Please also keep this guide handy and review it as you purchase and receive gifts. If you have any questions on product recalls or any of the other issues discussed in this guide, feel free to contact my Citizen Services hotline at 1-866-966-7226, or visit our website at MyFloridaLegal.com. You can also find updated lists of recalled items at the U. S. Consumer Product Safety Commission’s website, cpsc.gov/en/Recalls/. Have a wonderful and safe holiday season! Sincerely, Pam Bondi Florida Attorney General PL-01, The Capitol, Tallahassee, Florida 32399-1050, Telephone (850) 414-3300 Fax (850) 487-2564 TABLE OF CONTENTS Section Page Number Holiday Shopping Tips 3 Charity Scams 4 RECALLS 5 Toys 6 Baby Items 17 Sporting Goods 41 Household Goods 65 OTHER RESOURCES 84 2 Holiday Shopping Tips The holidays are a time to be especially mindful of ways your purchases can cost you more than you expect. -
The Effect of Bicycle Geometry, Rider Posture and Rider Anthropometrics
The Effect of Bicycle Geometry, Rider Posture and Rider Anthropometrics on Pitch-Over Dynamics by Alex Moorhead B.S., University of Colorado at Colorado Springs, 2013 A thesis submitted to the Graduate Faculty of the University of Colorado at Colorado Springs in partial fulfillment of the requirements for the degree of Master of Science Department of Biology 2015 © Copyright by Alex Moorhead 2015 All Rights Reserved The thesis for the Master of Science degree by Alex Moorhead has been approved for the Department of Biology by Jeffrey Broker, Chair Jacqueline Berning Andrew Subudhi Jay Dawes 26 August, 2015 ii ABSTRACT Cycling is a popular activity that has been extensively studied. Unfortunately, within the research, there are sparse insights regarding pitch-over accidents. A pitch-over accident occurs when a bicycle is introduced to an abrupt deceleration, often from a front wheel impact or excessive front wheel braking. Pitch-overs due to front braking are avoided if deceleration levels do not exceed the longitudinal stability of the rider/bicycle system, which is defined by the location of the combined center of mass (COM) relative to the front tire contact point. The purpose of this study was to determine how bicycle designs and geometries, plus rider postures, effect rider/bicycle stability, and pitch-over propensity. This study began by presenting and validating the use of a new force plate method (FPM) for locating rider and bicycle COM locations, as an alternative to a traditional anthropometric method (AM) used by Winter et. al. (2009). COM location estimates developed from the FPM were then compared to estimates derived using the AM. -
Methods for Fatigue Testing Off-Road Bicycle Handlebars Based on Assembly Effects Using Two Different Stem Designs
UC Davis UC Davis Previously Published Works Title Methods for fatigue testing off-road bicycle handlebars based on assembly effects using two different stem designs Permalink https://escholarship.org/uc/item/1vk019pc Journal Journal of Testing and Evaluation, 31(2) ISSN 0090-3973 Authors McKenna, Sean P Hill, Michael R Hull, Maury L Publication Date 2003-03-01 Peer reviewed eScholarship.org Powered by the California Digital Library University of California Journal of Testing and Evaluation, Vol. 31, No. 2 Paper ID JTE10903_312 Available online at: www.astm.org Sean P. McKenna,1 Michael R. Hill,1 and Maury L. Hull1 Methods for Fatigue Testing Off-Road Bicycle Handlebars Based on Assembly Effects Using Two Different Stem Designs ABSTRACT: Assembly of off-road bicycle handlebars with a stem that clamps the handlebar around its circumference would be expected to affect fatigue performance by introducing both assembly stresses and stress concentration. Because the effect of clamping on fatigue performance is unknown and because of the need to insure structural reliability in the stem-handlebar assembly to prevent serious injury, the objectives of the work reported by the present article were fourfold. One was to determine the stresses due to assembly and the stress concentration induced in a handlebar for two different clamp designs (i.e. 1-bolt and 2-bolt), a second was to determine experimentally the high cycle constant amplitude load fatigue lives of the two stem-handlebar assemblies, a third was to determine experimentally the variable amplitude load fatigue lives, and the fourth was to predict the variable amplitude load fatigue life with constant amplitude load fatigue test results. -
Ergonomic Analysis Study and Its Use in Designing of Adjustable Bicycle Handlebars for Kids
Journal of Automation and Automobile Engineering e-ISSN: 2582-3159 Volume 4 Issue 3 Ergonomic Analysis Study and its Use in Designing of Adjustable Bicycle Handlebars for Kids Prashant V Thorat*, Dr. D.S.More ME Student, Professor Department of Mechanical Engineering, Dr. D.Y. Patil School of Engineering, Charoli Budurk, Pune, Maharashtra, India Email: [email protected] DOI: http://doi.org/ 10.5281/zenodo.3580577 Abstract Bicycle riders’ position is mostly depends on the position of the handlebars, type of handlebars. If the handlebars are at optimum height , then bicycle rider will get more comfort while riding the bicycle whereas if bicycle handlebars are at lower position compared to saddle position, bicycle rider will get more stresses and pain in his upper body parts like hands, neck and mostly in back. For manage discomfort and fatigue, the cyclist may stop to rest or sit erect without holding onto the handlebars while still riding. By not holding the handlebars, the rider has little control over steering and no control over braking or changing gears. A solution is to adjust the handlebars from the lower to higher position and still allow access to the hand controls. This project objective is to design new parts and extension for the handlebar which can be used to adjust the height of the handlebars as per the anthropometric size of the rider. This project mostly targets the age group of 6 to 9 years as those are the age in which spinal cord system is in development stage and kids mostly start using bicycle. -
Appended Table1 (Re: Article 7) Classification of Articles 1. Manufactured Foods and Nonessential Goods Manufactured Foods Sausa
Appended Table1 (Re: Article 7) Classification of Articles 1. Manufactured Foods Manufactured Sausage and Nonessential Goods Foods Ice cream Kamaboko *Kamaboko: steamed fish paste Kamaboko board *Kamaboko: steamed fish paste Nori *Nori: seaweed Sugar cube Udon *Udon: noodle Pastry Biscuit Cracker Senbei *Senbei: flat rice cracker Arare *Arare: small cubic rice cracker Bun with red bean paste filling Wafer with red bean paste filling Pie Cake Doughnut Caramel candy Candy Chocolate Confectionery stick Solid curry Sushi Nonessential Cigarette Goods Cigarette paper 2. Clothing Underwear Undershirt Short underpants Long underpants Panty Bloomers Tights Panty hose Chemise Slip Petticoat Brassiere Girdle Garter Diaper Diaper cover Sanitary shorts Nightwear Pajamas Negligee Dressing gown Nightwear Swaddling blanket Western-Style Sweater Clothes Cardigan Polo shirt T-shirt Jacket Wind jacket Vest Overcoat Raincoat Sports clothes Sports top Sports bottom Working clothes Workmen's top Overalls Business suit Suit jacket Trousers Shirt Swimming trunks One-piece dress Two-piece suit Skirt Culotte skirt Cloak Blouse Swimsuit Japanese-Style Kimono Clothes Tanzen *Tanzen: padded large-size kimono Haori *Haori: kimono jacket Hanten *Hanten: kimono short coat Hadajuban *Hadajuban: kimono underwear Hanjuban *Hanjuban: short kimono undergarment Nagajuban *Nagajuban: long kimono undergarment Japanese coat Aprons, etc. Apron Japanese-style coverall apron Makeup cape Bib 3. Clothing Accessories Socks, etc. Sock Sock cover Tabi *Tabi: Japanese sock Tabi cover -
Trade Mark Inter Partes Decision O/188/18
O-188-18 TRADE MARKS ACT 1994 IN THE MATTER OF: TRADE MARK APPLICATION 3195207 IN THE NAME OF DENNIS WARE FOR THE TRADE MARK: Ezibike AND OPPOSITION THERETO (UNDER No 408624) BY EASYGROUP LIMITED Background and pleadings 1. The details of the mark the subject of these proceedings are: Mark: Ezibike Filing date: 6 November 2016 Publication: 25 November 2016 Applicant: Mr Dennis Ware Goods: Class 12: Water bottle cages for bicycles; Water bottle holders for bicycles; Bottle cages for bicycles; Bicycle water bottle cages; Rims for wheels of bicycles, cycles; Bicycle rims; Rims for wheels of bicycles; Rims for bicycle wheels; Rims for bicycles; Wheel rims for bicycles; Bicycle wheel rims; Fittings for bicycles for carrying luggage; Racing bicycles; Road racing bicycles; Front fork joints [bicycle parts];Cranks for bicycles; Bicycle cranks; Stands for bicycles [parts of];Bicycle trailers (riyakah); Bicycle trailers; Chains [bicycle parts];Change-speed gears [bicycle parts];Pumps for bicycles, cycles; Bicycle pumps; Pumps for bicycle tyres; Pumps for bicycle tires; Brake shoes [bicycle parts];Shock absorbers for bicycles; Inner tubes for bicycles, cycles; Inner tubes for bicycles; Inner tubes for bicycle tires; Inner tubes for bicycle tyres; Dress guards for bicycles, cycles; Dress guards for bicycles; Brakes [bicycle parts];Metal bells for bicycles; Tyres for bicycles, cycles; Bicycle tires [tyres];Tires for bicycles, cycles; Bicycle tyres; Tires for bicycles; Bicycle tires; Brakes for bicycles, cycles; Bicycle brakes; Brakes for bicycles; -
Exhibit Profile (In Alphabetical Order)
Exhibit Profile (in alphabetical order) Product Name Code Product Name Code Product Name Code Sportswear Portable Speaker 646020 Bicycle Bell & Horn 706004 Cycling Wear 561040 Handheld Cable 641045 Bicycle Lock 706006 Garment Accessories GPS 681030 Bicycle Lighting Set & Dynamo 706008 Other Garment Accessories 562599 Satcom Equipment 682040 Bicycle Rear Mirror 706010 Sports Cap 564020 Microwave Communication Equipment 682045 Bicycle Pump 706022 Headband 567030 GPS Module 681035 Bicycle Speed Meter / Cycle Computer 706024 Gloves GPS Components 681040 Bicycle Decal 706046 Sport Gloves 565030 Geographic Information System (GIS) 681045 Bicycle Basket 706012 Towel 781050 RFID Tag 682050 Bicycle Children's Seat 706018 Hosiery RFID Printing Machine 614885 Bicycle Fender / Mudguard 706026 Sneakers 568010 Electric Vehicle 691090 Bicycle Reflector 706028 Cycling Shoes 568425 Bicycles Bicycle Water Bottle Cage 706020 Children's Shoes 569020 Complete Cycles Bicycle Repair Tool 706030 Sports Shoes Mini Bicycle 701010 Bicycle Helmet 706002 Handbag 571010 BMX (Bicycle Motocross) & Freestyle 701015 Bicycle Saddle Pad 706032 Duffle / Gym Bag 572030 Children's Bicycle 701040 Medical Monitor 742535 Bicycle Bag 572070 Road Bicycle 701020 Mobility Scooter 743550 Thermal Bag 573060 Tricycle 701050 Sunglasses 588005 Tool Sets Mountain Bicycle 701025 Sports Eyewear 588010 Industrial Automatic Equipment Cruiser Bicycle 701030 Sports Gear Robot 618005 Folding Bicycle 701005 Sports Accessories Robotic Arm 618010 Ladies Bicycle 701035 Exercise Bike & Pedal Exerciser