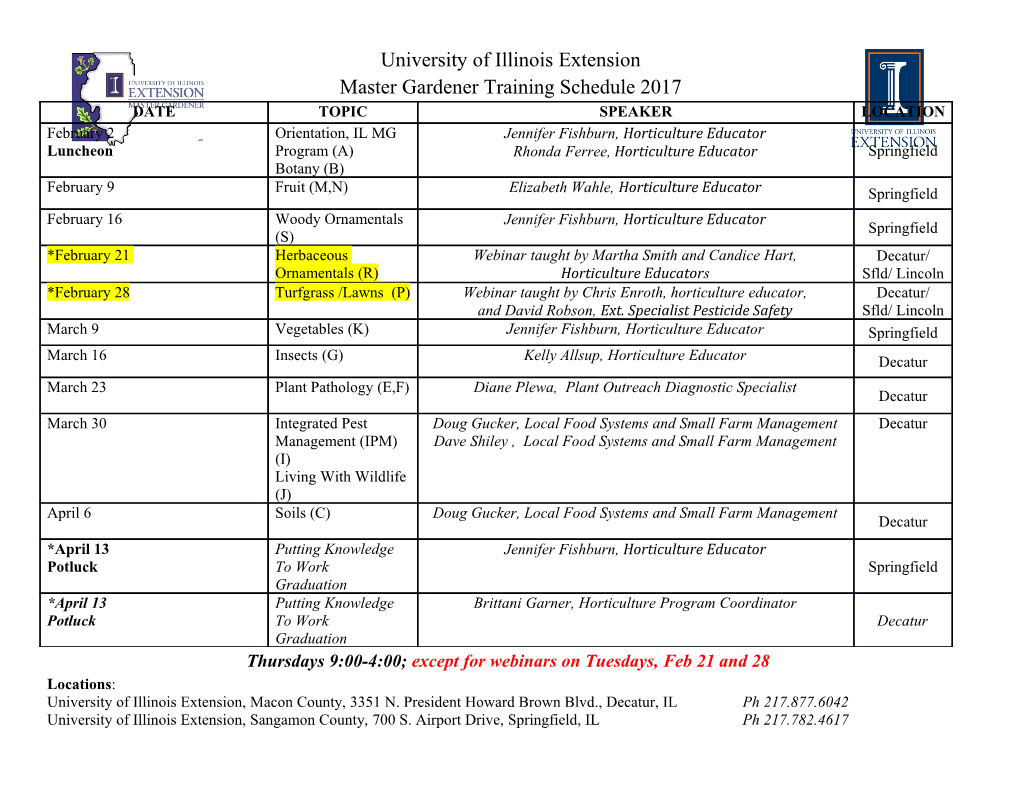
Fatigue of clamped connections with application to a stem-handlebar assembly for off-road bicycles S. P. MC KENNA,M.R.HILLandM.L.HULL Department of Mechanical and Aeronautical Engineering, University of California, One Shields Avenue, Davis, CA 95616, USA Received in final form 17 June 2002 ABSTRACT The objectives of this study were: (i) to determine the stresses as a result of assembly and the stress concentration of a clamped connection, (ii) to demonstrate the importance of the effects of assembly in fatigue life predictions and (iii) to verify the accuracy of fatigue life predictions by measuring fatigue life experimentally. A stem-handlebar assembly used in off-road bicycles was chosen for the study because it is a critical assembly for which structural reliability must be insured to prevent serious injury. Assembly stresses in the handlebar exceeded 200 MPa and stress concentration because of the attached stem in- creased the applied stress by 40%. A stress-life prediction indicated that assembly effects would reduce predicted fatigue life of the handlebar by a factor of approximately 20. The measured fatigue lifetime of the handlebar was longer than that predicted by using the stress-life approach, but was much shorter than that predicted when assembly effects were ignored. Therefore, assembly effects have a significant effect on fatigue life predictions and should be included in lifetime assessments for clamped mechanical assemblies. Keywords bicycle; clamped assembly; fatigue; handlebar; stress concentration; assembly stress. NOMENCLATURE X coordinate direction ahead of the bicycle, parallel to ground Z coordinate direction normal to X, upward from ground yb angle in the X±Z coordinate system, measured from X a angle of loading, with same sense as yb R load ratio, stress ratio eL, eT strains along (L) and perpendicular to (T) the handlebar axis sL, sT normal stress components along (L) and perpendicular to (T) the handlebar axis E, n Young's modulus and Poisson's ratio sN normalized bending stress W weight applied near the end of the handlebar L distance from applied load (moment arm) ro outer radius of the handlebar I moment of inertia of the handlebar cross section BX, BZ normalized bending stress as a result of a force along the X or Z direction FX, FZ force applied in the X or Z direction sapp stress as a result of applied load Ba normalized bending stress as a result of a force applied at angle a sm,ass effective assembly stress sTo t total stress; sum of applied stress and effective assembly stress smax maximum total stress seq equivalent stress in fatigue Nf cycles to failure Correspondence: Prof. Michael R. Hill, Department of Mechanical and Aeronautical Engineering, University of California, One Shields Avenue, Davis, CA 95616, USA. E-mail: [email protected] ß 2002 Blackwell Science Ltd. Fatigue Fract Engng Mater Struct 25,941±953 941 942 S. P. McKENNA et al. the stress concentration, so that no analytical prediction INTRODUCTION of the fatigue life of the assembled structural components One common type of mechanical connection used in was made. Because the analytical prediction of fatigue life order to assemble structural components is a clamped would be useful in the design of structural components connection, which can affect the fatigue performance assembled by clamping, the general goal of the present of the assembled structural components. Examples study was to develop and verify a method for predicting of clamped connections include the joining of a hub to high-cycle fatigue life of structural components in a shaft by using a set screw, the attachment of a hub to a clamped assemblies. In order to meet this general goal, shaft by using a clamp, the securing of piping by using the specific objectives were as follows: (i) to quantify the a yoke and the attachment of a bicycle handlebar to its effects of assembly in a fatigue-prone structural compon- stem via a pinch clamp (Fig. 1). In all the clamped ent for a particular clamped assembly, (ii) to include the connections shown in Fig. 1, the tightening of the assembly effects in an analytical prediction of fatigue life securing fastener(s) produces assembly stress in the as- for that structural component and (iii) to verify the ana- sembled structural components. Further, because these lytical fatigue life prediction with fatigue testing of that connections are also a point of support and/or a change structural component. in cross-section, stress concentration will also occur. In order to satisfy these specific objectives, a particular These two effects of clamped assembly affect both clamped assembly must be selected. In the off-road bi- the mean and amplitude values of cyclic stress and cycle, clamped components play a key role in rider sup- hence will influence fatigue performance of the assem- port and control of the bicycle. Critical clamped bled structural components. assemblies include the stem-handlebar, seatpost-frame Though many applications demand that the clamped and numerous similar assemblies. These clamped assem- structural components carry significant levels of cyclic blies are critical because the structural components may loading thus rendering the effects of assembly on fatigue experience high service loads and their failure can result performance of interest3 there have been few previous in either the loss of steering and braking control or the studies on the fatigue lives of structural components in loss of support for the rider's weight, thereby leading to clamped assemblies. To our knowledge, only a single serious injury. Such failures have occurred in service and clamp-specific, quantitative study of the effects of assem- have led to a number of product recalls for off-road bly on fatigue performance has been reported previ- bicycles (e.g. Refs [5, 6]). Accordingly, the handlebar in ously.4 This study investigated clamping a collar onto a the stem-handlebar assembly was selected in order to solid cylindrical shaft and found that assembly reduced satisfy the objectives above. the fatigue strength of the shaft by 55% at long lifetimes. While demonstrating that assembly has a profound effect on high-cycle fatigue life of a structural component, this METHODS study did not quantify either the assembly stress per se or Materials A stem and handlebar were selected from commonly T available, off-road bicycle components. The stem had a one-bolt clamp (1-bolt stem), where the clamp wrapped F d around the handlebar and bolted together on the under- d 2 r side of the stem (Fig. 2a). The 1-bolt stem was made of F steel and had the stem extension perpendicular to the quill. The handlebar was 580 mm long, with a cylindrical cross-section of nominal outer diameter of 25.4 mm and (a) (b) wall thickness of 2.2 mm. The bar had a bend of 68 (Fig. Yoke baam 2b) and was made of 6061-T6 aluminum (material prop- Load nut Handlebar erties given in Table 1). Clamp Load bar Table 1 Material properties for 6061-T6 aluminum7 Load distribution plate Stem E n Sy Su (c) (d) Fig. 1 Examples of mechanical assemblies: (a) hub connected to a 73.1 GPa 0.345 276 MPa 310 MPa shaft by a set screw,1 (b) split hub,2 (c) pipe yoke2 and (d) bicycle stem. ß 2002 Blackwell Science Ltd. Fatigue Fract Engng Mater Struct 25,941±953 FATIGUE OF CLAMPED CONNECTIONS 943 Experiments mented with strain gages. Bolt force was measured, rather than tightening torque, because friction does not Assembly stress allow consistent bolt force at a given measured torque.8 The stem clamp bolt was tightened until the bolt force In order to determine stress in the handlebar as a result transducer indicated a specific strain, corresponding to of assembly, strain gages were mounted on the outer an average tightening torque of 11.4 Nm (100 in-lb). surface of the handlebar and measured strain change during clamping. Four, two-element, 908 strain gage rosettes were placed at 908 intervals around the circum- Stress concentration ference, so that each rosette had an element orientated in both the longitudinal and transverse ± that is, circumfer- The instrumented handlebar was also used in order to ential ± directions of the handlebar. quantify the stress concentration in the handlebar when Assembly strain was measured at 108 increments around loaded in bending. Because the theoretical bending stress the stem±handlebar interface, with gage centers 1.6 mm is zero on the neutral axis, loads were applied along two away from the edge of the clamp. The assembly strain orthogonal directions in order to determine the stress was measured by repeatedly tightening the stem clamp concentration. For each loading direction, the instru- bolt with the handlebar rotated through 808,in108 mented handlebar was rotated incrementally by 108 increments, relative to the stem. In order to ensure con- with respect to the stem in order to map the bending sistency in the clamping force from tightening the stem strain around the entire stem±handlebar interface. The clamp bolt, the bolt force was measured with a bolt force two load directions were 2878 and 1978 with respect to transducer made from a cylindrical steel sleeve instru- the x-axis of the reference frame used in this study Z Њ (a) 17 Clamp qb Extension X 322Њ Load near end of handlebar, P/2 Quill (b) Applied load, P Center load fixture Clamp bolt Handlebar A 6 bend Fig. 2 Test articles and loading: (a) one- Support A bolt stem and (b) stem-handlebar assembly with handlebar cross-section. Here, (a) also P/2 L = 240 mm P/2 shows the X±Z coordinate frame and Stem typical 178 head-tube angle assumed, as well as the direction of applied load used in 520 mm fatigue testing (3228 from the x-axis); (b) also shows the three-point bending used for t = 2.2 mm fatigue testing, where roller supports were d = 25.4 mm placed where the hands would apply loads 0 and a centre load fixture was attached to the stem quill.
Details
-
File Typepdf
-
Upload Time-
-
Content LanguagesEnglish
-
Upload UserAnonymous/Not logged-in
-
File Pages14 Page
-
File Size-