Final Thesis
Total Page:16
File Type:pdf, Size:1020Kb
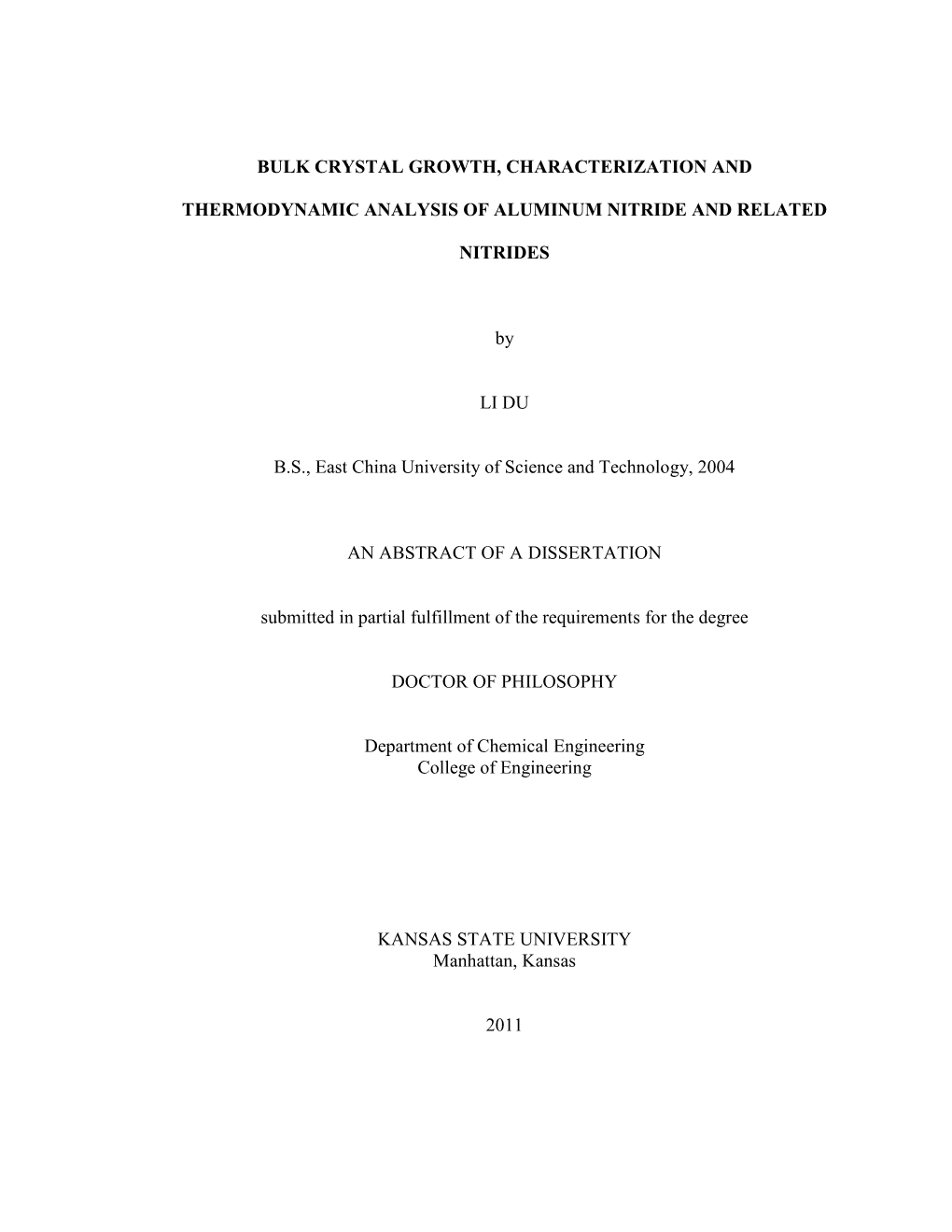
Load more
Recommended publications
-
Growth, Optimization, and Characterization of Transition Metal
GROWTH, OPTIMIZATION, AND CHARACTERIZATION OF TRANSITION METAL NITRIDES AND TRANSITION METAL OXIDES FOR ELECTRONIC AND OPTICAL APPLICATIONS Thesis Submitted to The School of Engineering of the UNIVERSITY OF DAYTON In Partial Fulfillment of the Requirements for The Degree of Master of Science in Electro-Optics By Zachary Biegler UNIVERSITY OF DAYTON Dayton, Ohio December 2019 GROWTH, OPTIMIZATION, AND CHARACTERIZATION OF TRANSITION METAL NITRIDES AND TRANSITION METAL OXIDES FOR ELECTRONIC AND OPTICAL APPLICATIONS Name: Biegler, Zachary Jay APPROVED BY: Andrew Sarangan, Ph.D., P.E. Amber Reed, Ph.D. Advisory Committee Chairman Committee Member Professor Materials Engineer Department of Electro-Optics and Photonics AFRL/RXAN Partha Banerjee, Ph.D. Committee Member Professor Department of Electro-Optics and Photonics Robert J. Wilkens, Ph.D., P.E. Eddy M. Rojas, Ph.D., M.A., P.E. Associate Dean for Research and Innovation Dean, School of Engineering Professor School of Engineering ii ABSTRACT GROWTH, OPTIMIZATION, AND CHARACTERIZATION OF TRANSITION METAL NITRIDES AND TRANSITION METAL OXIDES FOR ELECTRONIC AND OPTICAL APPLICATIONS Name: Biegler, Zachary J. University of Dayton Advisor: Dr. Andrew Sarangan The next generation of electronic and optical devices require high quality, crystalline materials in order to obtain relevant properties for novel devices. Two classes of materials offer unique material properties that can satisfy the requirements for next generation devices. These two classes of materials are the transition metal nitrides (TMNs) and transition metal oxides (TMOs). These materials offer electronic properties that range from conductive, metallic, materials to semiconducting and insulating materials. However, for many optical and electronic applications, the band structure and crystalline symmetries must be preserved. -
Design and Discovery of New Piezoelectric Materials Using Density Functional Theory
DESIGN AND DISCOVERY OF NEW PIEZOELECTRIC MATERIALS USING DENSITY FUNCTIONAL THEORY by Sukriti Manna © Copyright by Sukriti Manna, 2018 All Rights Reserved A thesis submitted to the Faculty and the Board of Trustees of the Colorado School of Mines in partial fulfillment of the requirements for the degree of Doctor of Philosophy (Mechanical Engineering). Golden, Colorado Date Signed: Sukriti Manna Signed: Dr. Cristian V. Ciobanu Thesis Advisor Signed: Dr. Vladan Stevanovi´c Thesis Advisor Golden, Colorado Date Signed: Dr. John Berger Professor and Head Department of Mechanical Engineering ii ABSTRACT Piezoelectric materials find applications in microelectromechanical systems (MEMS), such as surface acoustic wave (SAW) resonators, radio frequency (RF) filters, resonators, and energy harvesters. Using density functional theory calculations, the present study illus- trates the influence of alloying and co-alloying with different nitrides on piezoelectric and mechanical properties of an existing piezoelectric material such as aluminum nitride (AlN). Besides improving the performance of existing piezoelectric material, a high-throughput screening method is used to discover new piezoelectric materials. AlN has several beneficial properties such as high temperature stability, low dielectric permittivity, high hardness, large stiffness constant, high sound velocity, and complementary metal-oxide-semiconductor (CMOS) compatibility. This makes it widely accepted material in RF and resonant devices. However, it remains a challenge to enhance the piezoelectric modulus of AlN. The first part of this thesis establishes that the piezoelectric modulus of AlN could be improved by alloying with rocksalt transition metal nitrides such as scandium nitride (ScN), yttrium nitride (YN), and chromium nitride (CrN). As the content of the rocksalt end member in the alloy increases, the accompanying structural frustration enables a greater piezoelectric response. -
Metastable Scaln and Yaln Thin Films Grown by Reactive Magnetron Sputter Epitaxy
Linköping Studies in Science and Technology Dissertation No. 1566 Metastable ScAlN and YAlN Thin Films Grown by Reactive Magnetron Sputter Epitaxy Agnė Žukauskaitė Thin Film Physics Division Department of Physics, Chemistry, and Biologylogy (IFM)(IFM) Linköping University, Sweden 2014 The cover image The image on the cover is based on an elemental energy dispersive x-ray spectroscopy map of Sc0.2Al0.8N deposited at 400°C obtained in a transmission electron microscope. Each individual square represents an area of ~1x1 nm. Here, scandium was assigned the green color, and aluminum is mapped using purple. No tendencies to cluster into Sc-rich or Al-rich regions can be seen, indicating a solid solution. A special Thank You for recording this data goes to Dr. Justinas Pališaitis! © Agnė Žukauskaitė ISBN: 978-91-7519-434-9 ISSN: 0345-7524 Printed by LiU-Tryck Linköping, Sweden, 2014 Abstract Metastable ScxAl1-xN and YxAl1-xN thin films were deposited in an ultra high vacuum system using reactive magnetron sputter epitaxy from elemental Al, Sc, and Y targets in Ar/N2 gas mixture. Their structural, electrical, optical, mechanical, and piezoelectrical properties were investigated by using the transmission electron microscopy, x-ray diffraction, spectroscopic ellipsometry, I-V and C-V measurements, nanoindentation, and two different techniques for piezoelectric characterization: piezoresponse force microscopy and double beam interferometry. Compared to AlN, improved electromechanical coupling and increase in piezoelectric response was found in ScxAl1-xN/TiN/Al2O3 structures with Sc content up to x=0.2. Decreasing the growth temperature down to 400 °C improved the microstructure and crystalline quality of the material. -
Microstructure and Piezoelectric Response of Yxal1âˆ'xn Thin Films
Acta Materialia 100 (2015) 81–89 Contents lists available at ScienceDirect Acta Materialia journal homepage: www.elsevier.com/locate/actamat Microstructure and piezoelectric response of YxAl1ÀxN thin films ⇑ P.M. Mayrhofer a, , H. Riedl b, H. Euchner b, M. Stöger-Pollach c, P.H. Mayrhofer b, A. Bittner a, U. Schmid a a Institute of Sensor and Actuator Systems, TU Wien, Floragasse 7, 1040 Vienna, Austria b Institute of Materials Science and Technology, TU Wien, Getreidemarkt 9, 1060 Vienna, Austria c University Service Center for Transmission Electron Microscopy (USTEM), TU Wien, Wiedner Hauptstrasse 8-10/052, 1040 Vienna, Austria article info abstract Article history: Transition metal doping of aluminium nitride (AlN) type thin films was recently employed to increase the Received 6 July 2015 piezoelectric constants for application in micro electromechanical systems. YxAl1ÀxN thin films were Revised 7 August 2015 synthesized with varying x up to 11.6% by reactive co-sputtering from elemental Al and Y targets. Ab initio Accepted 11 August 2015 density functional theory studies up to x = 50% yttrium in YxAl1ÀxN suggest increasing piezoelectric constants d33 and d31 with increasing yttrium content. Experimental measurements of d33 yield increasing values for increasing yttrium content though, remaining below the prediction from ab initio Keywords: calculations. Detailed X-ray diffraction and transmission electron microscopy studies prove that, Yttrium aluminum nitride although the thin films are highly c-axis oriented, their nucleation at the Si (100) substrates leads to Piezoelectric the formation of an amorphous interface region with increasing Y. d33 PFM Ó 2015 Acta Materialia Inc. Published by Elsevier Ltd. -
Theoretical Study of Phase Stability, Crystal and Electronic Structure of Memgn2 (Me 5 Ti, Zr, Hf) Compounds
J Mater Sci (2018) 53:4294–4305 ElectronicELECTRONIC MATERIALS materials Theoretical study of phase stability, crystal and electronic structure of MeMgN2 (Me 5 Ti, Zr, Hf) compounds M. A. Gharavi1,* , R. Armiento2 , B. Alling2,3 , and P. Eklund1 1 Thin Film Physics Division, Department of Physics, Chemistry and Biology (IFM), Linköping University, 581 83 Linköping, Sweden 2 Theory and Modelling Division, Department of Physics, Chemistry and Biology (IFM), Linköping University, 581 83 Linköping, Sweden 3 Max-Planck-Institut für Eisenforschung GmbH, 40237 Düsseldorf, Germany Received: 6 July 2017 ABSTRACT Accepted: 21 November 2017 Scandium nitride has recently gained interest as a prospective compound for Published online: thermoelectric applications due to its high Seebeck coefficient. However, ScN 30 November 2017 also has a relatively high thermal conductivity, which limits its thermoelectric efficiency and figure of merit (zT). These properties motivate a search for other Ó The Author(s) 2017. This semiconductor materials that share the electronic structure features of ScN, but article is an open access which have a lower thermal conductivity. Thus, the focus of our study is to publication predict the existence and stability of such materials among inherently layered equivalent ternaries that incorporate heavier atoms for enhanced phonon scat- tering and to calculate their thermoelectric properties. Using density functional theory calculations, the phase stability of TiMgN2, ZrMgN2 and HfMgN2 compounds has been calculated. From the computationally predicted phase diagrams for these materials, we conclude that all three compounds are stable in these stoichiometries. The stable compounds may have one of two competing crystal structures: a monoclinic structure (LiUN2 prototype) or a trigonal superstructure (NaCrS2 prototype; R3mH). -
Ternary Nitride Semiconductors in the Rocksalt Crystal Structure
Ternary nitride semiconductors in the rocksalt crystal structure Sage R. Bauersa,1, Aaron Holdera,b, Wenhao Sunc, Celeste L. Melameda,d, Rachel Woods-Robinsona,c,e, John Mangumf, John Perkinsa, William Tumasa, Brian Gormanf, Adele Tambolia, Gerbrand Cederc,g, Stephan Lanya, and Andriy Zakutayeva,1 aMaterials Science Center, National Renewable Energy Laboratory, Golden, CO 80401; bDepartment of Chemical and Biological Engineering, University of Colorado, Boulder, Boulder, CO 80309; cMaterials Sciences Division, Lawrence Berkeley National Laboratory, Berkeley, CA 94720; dDepartment of Physics, Colorado School of Mines, Golden, CO 80401; eApplied Science and Technology Graduate Group, University of California, Berkeley, CA 94720; fDepartment of Metallurgical and Materials Engineering, Colorado School of Mines, Golden, CO 80401; and gDepartment of Materials Science and Engineering, University of California, Berkeley, CA 94720 Edited by Maw-Kuen Wu, Academia Sinica (Taiwan), Taipei, Taiwan, and approved June 7, 2019 (received for review March 21, 2019) Inorganic nitrides with wurtzite crystal structures are well-known TM nitrides with rocksalt structures. On one hand, the group IV semiconductors used in optical and electronic devices. In contrast, TMs usually exist in 3+ valence states in nitrides (e.g., TiN) (14). rocksalt-structured nitrides are known for their superconducting and On the other hand, introducing electropositive low-valence alkaline + refractory properties. Breaking this dichotomy, here we report ternary earth (AE)cations,suchasMg2 ,couldmoveTMsintohigher nitride semiconductors with rocksalt crystal structures, remarkable oxidation states, closing the d-shell and inducing semiconducting TM electronic properties, and the general chemical formula Mgx 1−xN behavior (15). Furthermore, TM nitride rocksalts are already known (TM = Ti, Zr, Hf, Nb). -
Develop and Characterization of Transparent Glass Matrix Composites
DEVELOPMENT AND CHARACTERIZATION OF TRANSPARENT GLASS MATRIX COMPOSITES Bo Pang A thesis submitted in fulfilment of the requirements of the degree of Doctor of Philosophy Imperial College London Department of Materials LONDON, 2011 Preface This thesis describes research carried out by the author in the Department of Materials of Imperial College during the period from January 2008 to January 2010, under the supervision of Dr. David McPhail and Prof. Aldo R. Boccaccini. No part of this work has been accepted or is being currently submitted for any other qualification in this college or elsewhere. Some of the results presented in this thesis have been published and presented in various journals and conferences. Journal publications B. Pang, D. McPhail, D.D. Jayaseelan, and A.R. Boccaccini, Development and Characterization of Transparent Glass Matrix Composites. Advances in Science and Technology, 2011. 71: p. 102-107. B. Pang, D. McPhail and A.R. Boccaccini, Glass Matrix Composites for Transparent Security Measures. Materials World, February 2011: p.20-22. Conference contributions Development and characterisation of transparent glass matrix composite. B. Pang, D. McPhail and A.R. Boccaccini. Oral presentation at the Annual Meeting of Society of Glass Technology, Murray Edwards College, Cambridge, UK. 6-10 September 2010. Development and characterisation of transparent glass matrix composite. B. Pang, D. McPhail and A.R. Boccaccini. Oral presentation at CIMTEC 2010 - 12th International Ceramics Congress, Montecatini Terme, Italy. 6-11 June 2010. 1 Abstract Glass matrix composites based on NextelTM alumina fibre reinforced borosilicate glass have been fabricated to improve their mechanical property and fracture toughness. In this work, a novel processing technique, which is called “sandwich” hot-pressing, has been used. -
First Principles Study on the Formation of Yttrium Nitride in Cubic and Hexagonal Phases
Manuscript including Title Page & Abstract First Principles Study on the Formation of Yttrium Nitride in Cubic and Hexagonal Phases G. Soto, M.G. Moreno-Armenta and A. Reyes-Serrato Centro de Ciencias de la Materia Condensada, Universidad Nacional Autónoma de México, Apartado Postal 356, Ensenada, Baja California. CP 22800, México. Abstract We have studied the formation of yttrium nitride in which the Y-atoms were arranged in two common close-packed stacking: The AB-stacking (hcp-symmetry) is the ground state of metallic yttrium; while the ABC-stacking (fcc-symmetry) is the ground state of yttrium nitride. Given the different symmetries between YN and Y, there must be a phase transition (hcp → fcc) as N is incorporated in the Y-lattice. By means of first principles calculations we have made a systematical investigation where N was gradually incorporated in octahedral interstices in AB and ABC stacking of Y. We report the heat of formation, bulk modulus, lattice parameter and electronic structure of the resultant nitrides. We found that both metal arrangements are physically achievable. Furthermore, for low nitrogen incorporation the two phases may coexist. However for high nitrogen concentration the cubic phases are favored by a 30 kJ mol-1 margi n. These results are important since fcc-YN is semiconducting and could be utilized as active layer in electronic devices. PACS: 71.15.Nc; 71.20.-b; 71.20.Be; 71.20.Lp; 71.20.Nr; 72.80.Ga Keywords: Yttrium nitride; Interstitial alloys; Transition metal nitrides; Ab initio; DFT; LAPW 1 Introduction The Transition (T) Metal (M) Nitrides (N) are valuable for several technological applications. -
Université Du Québec Thèse Présentée À L
UNIVERSITÉ DU QUÉBEC THÈSE PRÉSENTÉE À L'UNIVERSITÉ DU QUÉBEC À TROIS-RIVIÈRES COMME EXIGENCE PARTIELLE DU DOCTORAT EN GÉNIE ÉLECTRIQUE PAR ISSAM KERROUM CAPTEURS D'HYDROGÈNE POUR L'INDUSTRIE DE L'AUTOMOBILE ET DE LA SÉCURITÉ OCTOBRE 2016 Université du Québec à Trois-Rivières Service de la bibliothèque Avertissement L’auteur de ce mémoire ou de cette thèse a autorisé l’Université du Québec à Trois-Rivières à diffuser, à des fins non lucratives, une copie de son mémoire ou de sa thèse. Cette diffusion n’entraîne pas une renonciation de la part de l’auteur à ses droits de propriété intellectuelle, incluant le droit d’auteur, sur ce mémoire ou cette thèse. Notamment, la reproduction ou la publication de la totalité ou d’une partie importante de ce mémoire ou de cette thèse requiert son autorisation. ii UNIVERSITÉ DU QUÉBEC À TROIS-RIVIÈRES DOCTORAT EN GÉNIE ÉLECTRIQUE (PH.D.) Programme offert par l'Université du Québec à Trois-Rivières CAPTEURS D'HYDROGÈNE POUR L'INDUSTRIE DE L'AUTOMOBILE ET DE LA SÉCURITÉ PAR ISSAM KERROUM Frédéric Domingue, directeur de recherche Université du Québec à Trois-Rivières Alexandre Reinhardt, codirecteur de recherche CEA-LETI, Grenoble - France Adel-Omar Dahmane, président du jury Université du Québec à Trois-Rivières Adam Skorek, évaluateur interne Université du Québec à Trois-Rivières Charles Richard, évaluateur externe Teledyne DALSA Semiconducteur Thèse soutenue le 03 10 16 ili Résumé Dans le but de minimiser l'impact désastreux des gaz à effet de serre, la communauté scientifique s'est tournée vers l'exploitation de technologies à base d'énergies propres et renouvelables. -
Nitride Thin Films for Thermoelectric Applications: Synthesis, Characterization and Theoretical Predictions
Linköping Studies in Science and Technology Licentiate Thesis No. 1774 Nitride Thin Films for Thermoelectric Applications: Synthesis, Characterization and Theoretical Predictions Mohammad Amin Gharavi Thin Film Physics Division, Department of Physics, Chemistry and Biology (IFM) Linköping University, SE-581 83 Linköping, Sweden Linköping 2017 i Thin Film Physics Division, Department of Physics, Chemistry and Biology (IFM), Linköping University, SE-581 83 Linköping, Sweden © Mohammad Amin Gharavi, 2017 ISBN: 978-91-7685-539-3 ISSN: 0280-7971 Printed by LiU-Tryck, Linköping, Sweden, 2017 ii In the name of the lord of both wisdom and mind To nothing sublimer can thought be applied The lord of whatever is named or assigned A place, the sustainer of all and the guide The Persian epic “The Book of Kings” Abu ʾl-Qasim Ferdowsi Tusi 10th century A.D. iii iv Abstract Thermoelectrics is the reversible process which transforms a temperature gradient across a material into an external voltage through a phenomenon known as the Seebeck effect. This has resulted in niche applications such as solid-state cooling for electronic and optoelectronic devices which exclude the need for a coolant or any moving parts and long-lasting, maintenance-free radioisotope thermoelectric generators used for deep- space exploration. However, the high price and low efficiency of thermoelectric generators have prompted scientists to search for new materials and/or methods to improve the efficiency of the already existing ones. Thermoelectric efficiency is governed by the dimensionless figure of merit 푧푇, which depends on the electrical conductivity, thermal conductivity and Seebeck coefficient value of the material and has rarely surpassed unity. -
Tbiocas 2020 Final
Edinburgh Research Explorer Ultrasensitive Magnetoelectric Sensing Systemfor pico-Tesla MagnetoMyoGraphy Citation for published version: Zuo, S, Schmalz, J, Ozden , M-O, Özden, M-Ö, Gerken, M, Su, J, Niekiel, F, Lofink, F, Nazarpour, K & Heidari, H 2020, 'Ultrasensitive Magnetoelectric Sensing Systemfor pico-Tesla MagnetoMyoGraphy', IEEE Transactions on Biomedical Circuits and Systems, vol. 14, no. 5, pp. 971 - 984. https://doi.org/10.1109/TBCAS.2020.2998290 Digital Object Identifier (DOI): 10.1109/TBCAS.2020.2998290 Link: Link to publication record in Edinburgh Research Explorer Document Version: Peer reviewed version Published In: IEEE Transactions on Biomedical Circuits and Systems General rights Copyright for the publications made accessible via the Edinburgh Research Explorer is retained by the author(s) and / or other copyright owners and it is a condition of accessing these publications that users recognise and abide by the legal requirements associated with these rights. Take down policy The University of Edinburgh has made every reasonable effort to ensure that Edinburgh Research Explorer content complies with UK legislation. If you believe that the public display of this file breaches copyright please contact [email protected] providing details, and we will remove access to the work immediately and investigate your claim. Download date: 23. Sep. 2021 > REPLACE THIS LINE WITH YOUR PAPER IDENTIFICATION NUMBER (DOUBLE-CLICK HERE TO EDIT) < 1 Ultrasensitive Magnetoelectric Sensing System for pico-Tesla MagnetoMyoGraphy Siming Zuo, Student Member, IEEE, Julius Schmalz, Mesut-Ömür Özden, Martina Gerken, Member, IEEE, Jingxiang Su, Student Member, IEEE, Florian Niekiel, Fabian Lofink, Kianoush Nazarpour, Senior Member, IEEE and Hadi Heidari, Senior Member, IEEE Abstract—MagnetoMyoGraphy (MMG) with superconducting ThereFore, the corresPondence betWeen the MMG and EMG quantum interference devices (SQUIDs) enabled the measurement methods is governed by the MaxWell-AmPère law. -
LIME, MAGNESIA; SLAG; CEMENTS; COMPOSITIONS THEREOF, E.G. MORTARS, CONCRETE OR LIKE BUILDING MATERIALS; ARTIFICIAL STONE {(Roofi
CPC - C04B - 2021.08 C04B LIME, MAGNESIA; SLAG; CEMENTS; COMPOSITIONS THEREOF, e.g. MORTARS, CONCRETE OR LIKE BUILDING MATERIALS; ARTIFICIAL STONE {(roofing granules E04D 7/005)}; CERAMICS (devitrified glass-ceramics C03C 10/00); REFRACTORIES; TREATMENT OF NATURAL STONE Definition statement This place covers: Chemical aspects of the processing of lime, magnesia or dolomite and of molten slag. Compositional aspects of: • inorganic binders, such as hydraulic cements ; • mortars, concrete and artificial stone, e.g. the choice of fillers or active ingredients therefore; • shaped ceramic products, e.g. clay-wares, refractories , non-oxides. Physico-chemical aspects of methods for obtaining mortars, concrete, artificial stones or ceramics , e.g. for delaying the setting time of mortar compositions. Treatment including defibrillating of materials such as fillers , agglomerated or waste materials, or refuse to enhance their filling properties in mortars, concrete or artificial stone. Porous mortars, concrete, artificial stone or ceramic ware, and the preparation thereof. Methods and apparatus for: • burning or slaking lime; • obtaining mineral binders, e.g. Portland cement or hemihydrate plaster; • the expansion of mineral fillers , such as clay, perlite or vermiculite. After- treatment of artificial stones, mortars, concrete and ceramics , e.g. coating or impregnation of green concrete after primary shaping. Non-mechanical treatment of natural stone. Processing powders of inorganic compounds in preparation to the manufacturing of ceramic products . 1 C04B (continued) CPC - C04B - 2021.08 Definition statement The joining of burned ceramics with other articles by heating. References Limiting references This place does not cover: Granulating apparatus B01J 2/00 Mechanical features relating to the working of mortars, concrete, stone, B28 clay-wares or ceramics , e.g.