Mechanism and Assessment of Spin Transfer Torque (STT) Based Memory by Iong Ying Loh B.Sc. Applied Physics (2007) University Of
Total Page:16
File Type:pdf, Size:1020Kb
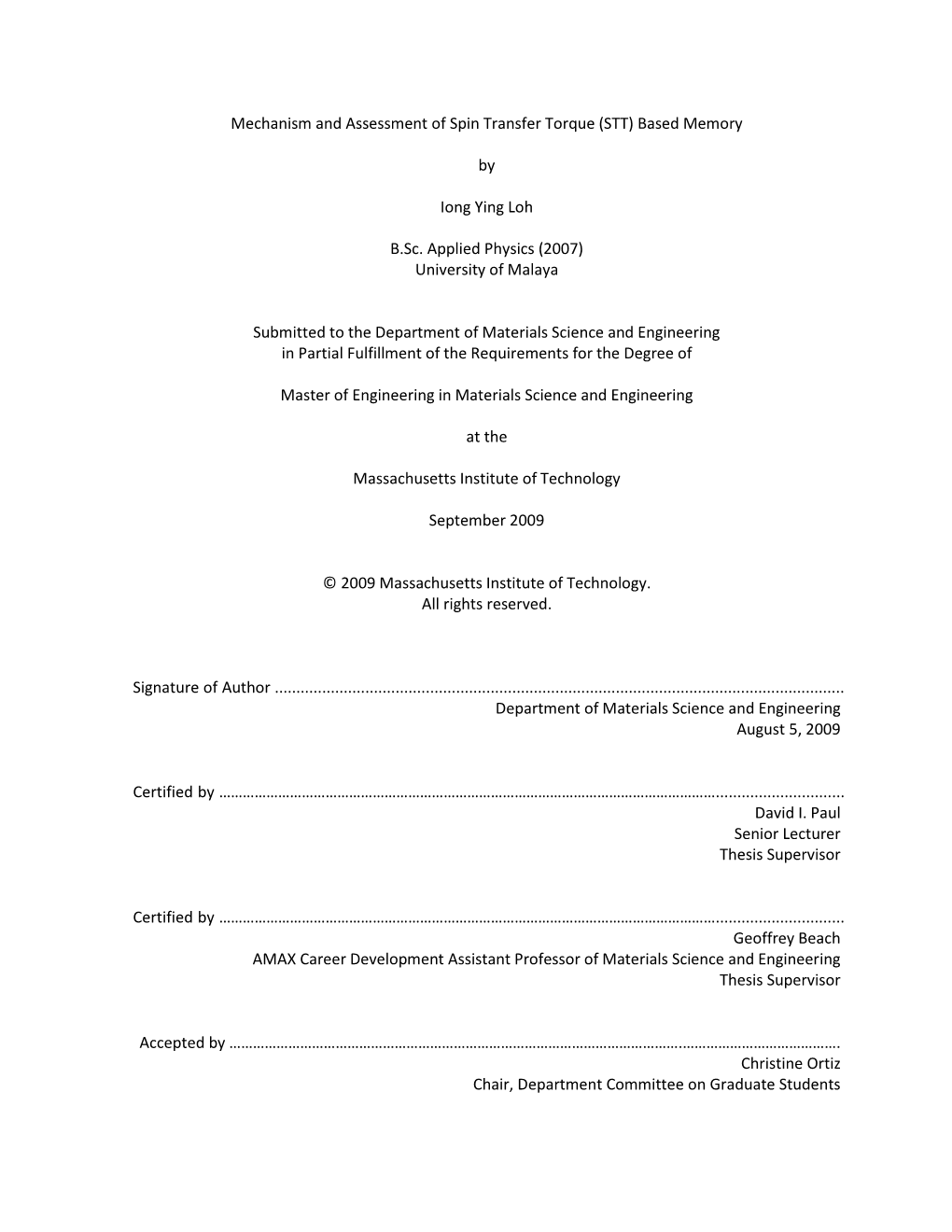
Load more
Recommended publications
-
Universal Memory
BRIEFING No.4 ICT UNIVERSAL MEMORY Memory is an integral part of information processing devices and is needed for short‐term stor‐ age such as when computer programs are being executed or text documents are processed. Currently, three main types of memory exist: SRAM offers very high speed at a high cost, DRAM is average in terms of speed and cost, and Flash memory is a low cost, low speed solution for applications that need to retain the data even when power is disconnected. A group of emerg‐ ing memory devices called universal memory aim to combine all these features in a single de‐ vice.1 Developments in universal memory devices may eventually lead to the introduction of novel October 2010 October memory architectures that offer increased performance, enable smaller mobile devices, and offer novel features in traditional products such as cars or domestic appliances. Nanotechnol‐ ogy is an integral part of emerging memory research as it is becoming increasingly difficult to enhance the performance of current devices by scaling the technology further. It is unlikely that a single technology will emerge as the universal memory technology; however, the develop‐ ments in this sector will enhance the energy efficiency and performance of memory devices. Currently, the Integrated Circuit (IC) market is dominated by US and Asia based companies. Uni‐ versal memory and nanotechnology based solutions could provide an opportunity for Europe to gain ground in the sector. Background volatility. Its disadvantage compared to SRAM and DRAM is speed. None of the existing memory technologies provide all of the required properties. -
Nanotechnology Trends in Nonvolatile Memory Devices
IBM Research Nanotechnology Trends in Nonvolatile Memory Devices Gian-Luca Bona [email protected] IBM Research, Almaden Research Center © 2008 IBM Corporation IBM Research The Elusive Universal Memory © 2008 IBM Corporation IBM Research Incumbent Semiconductor Memories SRAM Cost NOR FLASH DRAM NAND FLASH Attributes for universal memories: –Highest performance –Lowest active and standby power –Unlimited Read/Write endurance –Non-Volatility –Compatible to existing technologies –Continuously scalable –Lowest cost per bit Performance © 2008 IBM Corporation IBM Research Incumbent Semiconductor Memories SRAM Cost NOR FLASH DRAM NAND FLASH m+1 SLm SLm-1 WLn-1 WLn WLn+1 A new class of universal storage device : – a fast solid-state, nonvolatile RAM – enables compact, robust storage systems with solid state reliability and significantly improved cost- performance Performance © 2008 IBM Corporation IBM Research Non-volatile, universal semiconductor memory SL m+1 SL m SL m-1 WL n-1 WL n WL n+1 Everyone is looking for a dense (cheap) crosspoint memory. It is relatively easy to identify materials that show bistable hysteretic behavior (easily distinguishable, stable on/off states). IBM © 2006 IBM Corporation IBM Research The Memory Landscape © 2008 IBM Corporation IBM Research IBM Research Histogram of Memory Papers Papers presented at Symposium on VLSI Technology and IEDM; Ref.: G. Burr et al., IBM Journal of R&D, Vol.52, No.4/5, July 2008 © 2008 IBM Corporation IBM Research IBM Research Emerging Memory Technologies Memory technology remains an -
EVERSPIN TECHNOLOGIES INC Form 10-K Annual Report Filed
SECURITIES AND EXCHANGE COMMISSION FORM 10-K Annual report pursuant to section 13 and 15(d) Filing Date: 2021-03-04 | Period of Report: 2020-12-31 SEC Accession No. 0001558370-21-002369 (HTML Version on secdatabase.com) FILER EVERSPIN TECHNOLOGIES INC Mailing Address Business Address 5670 W. CHANDLER 5670 W. CHANDLER CIK:1438423| IRS No.: 262640654 | Fiscal Year End: 1231 BOULEVARD BOULEVARD Type: 10-K | Act: 34 | File No.: 001-37900 | Film No.: 21714089 SUITE 100 SUITE 100 SIC: 3674 Semiconductors & related devices CHANDLER AZ 85226 CHANDLER AZ 85226 480-347-1111 Copyright © 2021 www.secdatabase.com. All Rights Reserved. Please Consider the Environment Before Printing This Document Table of Contents UNITED STATES SECURITIES AND EXCHANGE COMMISSION Washington, D.C. 20549 FORM 10-K (Mark One) ☒ ANNUAL REPORT PURSUANT TO SECTION 13 OR 15(d) OF THE SECURITIES EXCHANGE ACT OF 1934 For the fiscal year ended December 31, 2020 OR ☐ TRANSITION REPORT PURSUANT TO SECTION 13 OR 15(d) OF THE SECURITIES EXCHANGE ACT OF 1934 FOR THE TRANSITION PERIOD FROM TO Commission File Number 001-37900 Everspin Technologies, Inc. (Exact name of Registrant as specified in its Charter) Delaware 26-2640654 (State or other jurisdiction (I.R.S. Employer of incorporation or organization) Identification No.) 5670 W. Chandler Boulevard, Suite 100 Chandler, Arizona 85226 (Address of principal executive offices including zip code) Registrant’s telephone number, including area code: (480) 347-1111 Securities registered pursuant to Section 12(b) of the Act: Title of each class Trading Symbol(s) Name of the exchange on which registered Common Stock, par value $0.0001 MRAM The Nasdaq Stock Market LLC Securities registered pursuant to Section 12(g) of the Act: None Indicate by check mark if the Registrant is a well-known seasoned issuer, as defined in Rule 405 of the Securities Act. -
Everspin Technologies, Inc. Annual Report 2018
Everspin Technologies, Inc. Annual Report 2018 Form 10-K (NASDAQ:MRAM) Published: March 15th, 2018 PDF generated by stocklight.com UNITED STATES SECURITIES AND EXCHANGE COMMISSION Washington, D.C. 20549 FORM 10‑K (Mark One) ☒ ANNUAL REPORT PURSUANT TO SECTION 13 OR 15(d) OF THE SECURITIES EXCHANGE ACT OF 1934 For the fiscal year ended December 31, 2017 OR ◻ TRANSITION REPORT PURSUANT TO SECTION 13 OR 15(d) OF THE SECURITIES EXCHANGE ACT OF 1934 FOR THE TRANSITION PERIOD FROM TO Commission File Number 001‑37900 Everspin Technologies, Inc. (Exact name of Registrant as specified in its Charter) Delaware 26‑2640654 (State or other jurisdiction (I.R.S. Employer of incorporation or organization) Identification No.) 5670 W. Chandler Boulevard, Suite 100 Chandler, Arizona 85226 (Address of principal executive offices including zip code) Registrant’s telephone number, including area code: (480) 347‑1111 Securities registered pursuant to Section 12(b) of the Act: Common Stock, Par Value $0.0001 Per Share; Common stock traded on the Nasdaq Stock Market Securities registered pursuant to Section 12(g) of the Act: None Indicate by check mark if the Registrant is a well-known seasoned issuer, as defined in Rule 405 of the Securities Act. YES ☐ NO ☒ Indicate by check mark if the Registrant is not required to file reports pursuant to Section 13 or 15(d) of the Act. YES ☐ NO ☒ Indicate by check mark whether the Registrant: (1) has filed all reports required to be filed by Section 13 or 15(d) of the Securities Exchange Act of 1934 during the preceding 12 months (or for such shorter period that the Registrant was required to file such reports), and (2) has been subject to such filing requirements for the past 90 days. -
October 31, 2013 RUSNANO Portfolio Company Crocus Nano Electronics
PRESS-RELEASE October 31, 2013 RUSNANO Portfolio Company Crocus Nano Electronics Launches First Production Line Open Innovations, an international forum devoted to emerging technologies and international collaboration, was the backdrop today for launching production of magnetoresistive random-access memory, or MRAM. The company that commissioned the factory line, Crocus Nano Electronics, is a joint venture between RUSNANO and Crocus Technology SA (France). Taking part in opening ceremonies by satellite link up were Moscow Mayor Sergei Sobyanin, RUSNANO CEO Anatoly Chubais, Crocus Technology VP for Worldwide Operations Jean-Luc Sentis, and Crocus Nano Electronics General Director Boris Omarov. Magnetoresistive random access memory, or MRAM, combines energy independence with rapid writing/reading speed and a virtually unlimited number of rewrite cycles. It is new generation memory. Crocus Nano Electronics will manufacture products based on Crocus Technology’s Magnetic Logic Unit™ (MLU), a disruptive CMOS-based rugged magnetic technology it is developing with IBM. MLU offers important advantages in high speed, security, and robust performance at lower cost for its broadening portfolio of embedded products and non-volatile memory blocks. The technology may be used in smart cards, network commutators, biometric authenticating devices, near field communications, and secure memory. The market for product applications manufactured by the portfolio company is forecasted to exceed $8 billion in 2014. The manufacturing facility for the company was built at TECHNOPOLIS Moscow in one of the partnership between RUSNANO and the Government of Moscow. The government is developing a new center for innovative high-tech industry on the site of the former Moskvich automobile factory. Crocus Nano Electronics is the first resident of the future microelectronic cluster. -
Final Program
1 General Information SCOPE OF THE CONFERENCE The 11th Joint MMM/Intermag Conference is sponsored jointly by the American Institute of Physics (PCI) and the Magnetics Society of the IEEE, in cooperation with The American Physical Society. Members of the inter- national scientific and engineering communities interested in recent devel- opments in fundamental and applied magnetism are invited to attend the Conference and contribute to its technical sessions. Sessions will include invited and contributed papers, oral and poster presentations and invited symposia. This Conference provides an outstanding opportunity for partici- pants to meet their colleagues and discuss new, advanced and controversial developments. WASHINGTON, DC The 2010 Joint Conference will be held in the nation’s capital. The city wel- comes 15 million visitors each year of which 1.2 million are international. There are more than 100 restaurants located in the downtown area alone, and the city has been called “one of the most exciting restaurant cities on the East Coast” by Travel & Leisure. To obtain an in-depth and current view of what to see and do while you are here, visit the official website at: http://www.washington.org. Here you will find information on how to trav- el to the Marriott Washington Wardman Park from any of the three local air- ports; you can check on the weather in mid-January, and can request a free Visitors Guide prior to making your trip. VISA REQUIREMENTS The US has updated its visa policies to increase security, so it may take you 3-6 months to apply for and receive your visa. -
Scalability and Reliability of Phase Change Memory
SCALABILITY AND RELIABILITY OF PHASE CHANGE MEMORY A DISSERTATION SUBMITTED TO THE DEPARTMENT OF ELECTRICAL ENGINEERING AND THE COMMITTEE ON GRADUATE STUDIES OF STANFORD UNIVERSITY IN PARTIAL FULFILLMENT OF THE REQUIREMENTS FOR THE DEGREE OF DOCTOR OF PHILOSOPHY SangBum Kim Aug 2010 © 2010 by SangBum Kim. All Rights Reserved. Re-distributed by Stanford University under license with the author. This work is licensed under a Creative Commons Attribution- Noncommercial 3.0 United States License. http://creativecommons.org/licenses/by-nc/3.0/us/ This dissertation is online at: http://purl.stanford.edu/kk866zc2173 ii I certify that I have read this dissertation and that, in my opinion, it is fully adequate in scope and quality as a dissertation for the degree of Doctor of Philosophy. Philip Wong, Primary Adviser I certify that I have read this dissertation and that, in my opinion, it is fully adequate in scope and quality as a dissertation for the degree of Doctor of Philosophy. Yi Cui I certify that I have read this dissertation and that, in my opinion, it is fully adequate in scope and quality as a dissertation for the degree of Doctor of Philosophy. Yoshio Nishi Approved for the Stanford University Committee on Graduate Studies. Patricia J. Gumport, Vice Provost Graduate Education This signature page was generated electronically upon submission of this dissertation in electronic format. An original signed hard copy of the signature page is on file in University Archives. iii Abstract Various memory devices are being widely used for a wide range of applications. There has not been any universal memory device so far because each memory device has a unique set of features. -
Architecting Racetrack Memory Preshift Through Pattern-Based Prediction Mechanisms
Architecting Racetrack Memory preshift through pattern-based prediction mechanisms Abstract— Racetrack Memories (RM) are a promising metalic racetrack, providing higher package density, lower spintronic technology able to provide multi-bit storage in a single energy and more robust data stability [5]. As seen in Fig. 1, each cell (tape-like) through a ferromagnetic nanowire with multiple RM cell is able to store multiple data bits in a single wire domains. This technology offers superior density, non-volatility programming domains to a certain direction (DWM) or by the and low static power compared to CMOS memories. These absence or presence of a skyrmion (SK-RM). Applying a current features have attracted great interest in the adoption of RM as a through the wire ends, domains or skyrmions can be shifted replacement of RAM technology, from Main memory (DRAM) to left/right at a constant velocity. With such a tape-like operation, maybe on-chip cache hierarchy (SRAM). One of the main every domain can be aligned with a read/write port, drawbacks of this technology is the serialized access to the bits implemented through a Magnetic Tunnel Junction (MTJ). The stored in each domain, resulting in unpredictable access time. An bit-cell structure required for shifting and read/write is shown in appropriate header management policy can potentially reduce the number of shift operations required to access the correct position. Fig. 1.down. Read/write operations are performed precharging Simple policies such as leaving read/write head on the last domain bitlines (BL and BLB) to the appropriate values and turning on accessed (or on the next) provide enough improvement in the the access transistors (TRW1 and TRW2). -
Racetrack Memory Based Logic Design for In‑Memory Computing
This document is downloaded from DR‑NTU (https://dr.ntu.edu.sg) Nanyang Technological University, Singapore. Racetrack memory based logic design for in‑memory computing Luo, Tao 2018 Luo, T. (2018). Racetrack memory based logic design for in‑memory computing. Doctoral thesis, Nanyang Technological University, Singapore. http://hdl.handle.net/10356/73359 https://doi.org/10.32657/10356/73359 Downloaded on 27 Sep 2021 05:57:42 SGT RACETRACK MEMORY BASED LOGIC DESIGN FOR IN-MEMORY COMPUTING School of Computer Science and Engineering A thesis submitted to the Nanyang Technological University in partial fulfilment of the requirement for the degree of Doctor of Philosophy LUO TAO August 2017 Abstract In-memory computing has been demonstrated to be an efficient computing in- frastructure in the big data era for many applications such as graph processing and encryption. The area and power overhead of CMOS technology based mem- ory design is growing rapidly because of the increasing data capacity and leak- age power along with the shrinking technology node. Thus, a newly introduced emerging memory technology, racetrack memory, is proposed to increase the data capacity and power efficiency of modern memory systems. As the design require- ments of the conventional logic are different from that of the emerging memory based logic for in-memory computing, the conventional well-developed CMOS technology based logic designs are less relevant to the emerging memory based in-memory computing. Therefore, novel logic designs for racetrack memory are required. Traditional logic design with separate chips is focusing on high speed, which causes large area and power consumption. -
Device-Aware Inference Operations in SONOS Non- Volatile Memory Arrays
Device-aware inference operations in SONOS non- volatile memory arrays Christopher H. Bennett1*, T. Patrick Xiao1*, Ryan Dellana1, Ben Feinberg1, Sapan Agarwal1, and Matthew J. Marinella1 1. Sandia National Laboratories, Albuquerque, NM 87185-1084, USA {cbennet,txiao,mmarine}@sandia.gov *These authors contributed equally Vineet Agrawal2, Venkatraman Prabhakar2, Krishnaswamy Ramkumar2, Long Hinh2, Swatilekha Saha2, Vijay Raghavan3, Ramesh Chettuvetty3 2. Cypress Semiconductor Corporation, 198 Champion Court, San Jose, CA, 95134, USA 3. Cypress Semiconductor Corporation, Ste #120, 536 Chapel Hills Drive, Colorado Springs, CO, 80920, USA [email protected] Abstract— Non-volatile memory arrays can deploy pre-trained noise, variability, and circuit non-idealities [6],[7]. We neural network models for edge inference. However, these additionally investigate the impact of retention loss as systems are affected by device-level noise and retention issues. measured in real devices and show that the same device-aware Here, we examine damage caused by these effects, introduce a training methods can be applied to mitigate the effects of mitigation strategy, and demonstrate its use in fabricated array weight drift. In the following sections, we demonstrate that the of SONOS (Silicon-Oxide-Nitride-Oxide-Silicon) devices. On following two approaches – in terms of software neural MNIST, fashion-MNIST, and CIFAR-10 tasks, our approach network and circuit architecture respectively – can mitigate increases resilience to synaptic noise and drift. We also show device non-idealities: strong performance can be realized with ADCs of 5-8 bits precision. The use of noise regularization during training which implicitly counteracts generic noise disturbance, device- Index Terms-- SONOS, CTM, neural networks, edge inference to-device variability, and charge decay phenomenon: The use of an appropriate 1T,1CTM cells in a dual array I. -
Data in the Fast Lanes of Racetrack Memory
INFOTECH Data in the Fast Lanes of RACETRACK MEMORY A device that slides magnetic bits back and forth along nanowire “racetracks” could pack data in a three-dimensional microchip and may replace nearly all forms of conventional data storage By Stuart S. P. Parkin he world today is very different from that when the computer powers down—or crashes. of just a decade ago, thanks to our ability A few computers use nonvolatile chips, which T to readily access enormous quantities of retain data when the power is off, as a solid-state information. Tools that we take for granted— drive in place of an HDD. The now ubiquitous social networks, Internet search engines, online smart cell phones and other handheld devices maps with point-to-point directions, and online also use nonvolatile memory, but there is a trade- libraries of songs, movies, books and photo- off between cost and performance. The cheapest KEY CONCEPTS graphs—were unavailable just a few years ago. nonvolatile memory is a kind called flash memo- ■ A radical new design for We owe the arrival of this information age to the ry, which, among other uses, is the basis of the computer data storage rapid development of remarkable technologies little flash drives that some people have hanging called racetrack memory in high-speed communications, data processing from their key rings. Flash memory, however, is (RM) moves magnetic and—perhaps most important of all but least ap- slow and unreliable in comparison with other bits along nanoscopic preciated—digital data storage. memory chips. Each time the high-voltage pulse “racetracks.” Each type of data storage has its Achilles’ heel, (the “flash” of the name) writes a memory cell, ■ RM would be nonvola- however, which is why computers use several the cell is damaged; it becomes unusable after tile—retaining its data types for different purposes. -
A Stacked Memory Device on Logic 3D Technology for Ultra-High-Density Data Storage
IOP PUBLISHING NANOTECHNOLOGY Nanotechnology 22 (2011) 254006 (7pp) doi:10.1088/0957-4484/22/25/254006 A stacked memory device on logic 3D technology for ultra-high-density data storage Jiyoung Kim1,2, Augustin J Hong1, Sung Min Kim1,2, Kyeong-Sik Shin1, Emil B Song1, Yongha Hwang1, Faxian Xiu1, Kosmas Galatsis1, Chi On Chui1, Rob N Candler1, Siyoung Choi2, Joo-Tae Moon2 and Kang L Wang1 1 Device Research Laboratory, Department of Electrical Engineering, University of California, Los Angeles, CA 90095, USA 2 Advanced Technology Development Team and Process Development Team, Memory R&D Center, Samsung Electronics Co. Ltd, Korea E-mail: [email protected] Received 22 June 2010, in final form 29 September 2010 Published 16 May 2011 Online at stacks.iop.org/Nano/22/254006 Abstract We have demonstrated, for the first time, a novel three-dimensional (3D) memory chip architecture of stacked-memory-devices-on-logic (SMOL) achieving up to 95% of cell-area efficiency by directly building up memory devices on top of front-end CMOS devices. In order to realize the SMOL, a unique 3D Flash memory device and vertical integration structure have been successfully developed. The SMOL architecture has great potential to achieve tera-bit level memory density by stacking memory devices vertically and maximizing cell-area efficiency. Furthermore, various emerging devices could replace the 3D memory device to develop new 3D chip architectures. S Online supplementary data available from stacks.iop.org/Nano/22/254006/mmedia (Some figures in this article are in colour only in the electronic version) 1. Introduction patterning resolution, transistor short-channel effects, and ever increasing interference between adjacent cells [3, 5–8].