Simulations and Modeling of Vehicle Dynamics and Aerodynamics Within a Teaching and Learning Environment
Total Page:16
File Type:pdf, Size:1020Kb
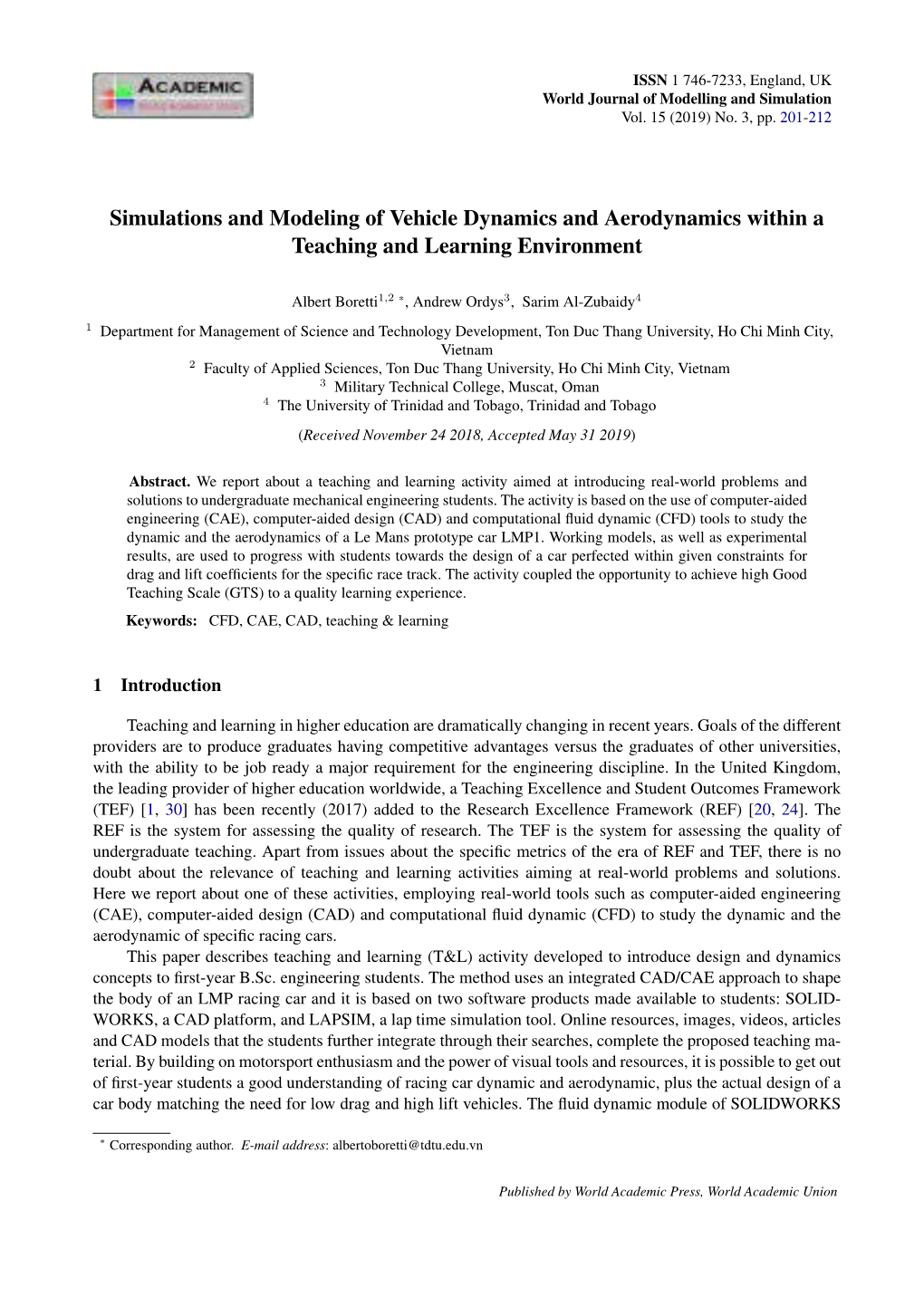
Load more
Recommended publications
-
Race 6 Hours of Sao Paulo FIA WEC Provisional
FIA WEC 6 Hours of Sao Paulo Race Provisional Classification Best Lap Nr. Team Drivers Car Class Ty Laps Total Time Gap Lap Time Kph 1 7 Toyota Racing Wurz / Lapierre Toyota TS030 - Hybrid LMP1 M 247 6:01'08.356 165 1'23.419 186.0 2 1 Audi Sport Team Joest Lotterer / Fässler / Tréluyer Audi R18 e-tron quattro LMP1 M 247 6:02'09.134 1'00.778 1'00.778 218 1'23.740 185.2 3 2 Audi Sport Team Joest Kristensen / McNish / Di Grassi Audi R18 ultra LMP1 M 247 6:02'23.035 1'14.679 13.901 213 1'23.070 186.7 4 12 Rebellion Racing Prost / Jani Lola B12/60 Coupé - Toyota LMP1 M 242 6:01'16.750 5 Laps 5 Laps 175 1'24.838 182.8 5 21 Strakka Racing Leventis / Watts / Kane HPD ARX 03a - Honda LMP1 M 240 6:01'48.032 7 Laps 2 Laps 230 1'24.915 182.7 6 13 Rebellion Racing Belicchi / Primat Lola B12/60 Coupé - Toyota LMP1 M 240 6:01'51.142 7 Laps 3.110 168 1'25.410 181.6 7 44 Starworks Motorsports Potolicchio / Dalziel / Sarrazin HPD ARX 03b - Honda LMP2 D 234 6:01'42.190 13 Laps 6 Laps 189 1'28.198 175.9 8 49 Pecom Racing Perez Companc / Minassian / Kaffer Oreca 03 - Nissan LMP2 D 231 6:02'28.457 16 Laps 3 Laps 187 1'28.586 175.1 9 22 JRM Brabham / Chandhok / Dumbreck HPD ARX 03a - Honda LMP1 M 230 6:01'24.825 17 Laps 1 Laps 175 1'25.257 181.9 10 24 Oak Racing Nicolet / Lahaye / Pla Morgan - Nissan LMP2 D 230 6:01'56.824 17 Laps 31.999 207 1'27.848 176.6 11 41 Greaves Motorsport Zugel / Gonzalez / Julian Zytek Z11SN - Nissan LMP2 D 229 6:02'01.666 18 Laps 1 Laps 192 1'29.057 174.2 12 25 ADR-Delta Martin / Charouz / Graves Oreca 03 - Nissan LMP2 D 228 6:01'39.572 -
Event Maximum Speed Free Practice 1 WEC 6 HOURS of SPA
FIA WEC WEC 6 HOURS OF SPA-FRANCORCHAMPS After Free Practice 1 Event maximum speed Team Car Class Driver Top Speed Lap Session 3 Audi Sport Team Joest Audi R18 e-tron quattro LMP1 Oliver JARVIS 304.2 42 Free Practice 1 7 Toyota Racing Toyota TS030 - Hybrid LMP1 Nicolas LAPIERRE 300.8 18 Free Practice 1 1 Audi Sport Team Joest Audi R18 e-tron quattro LMP1 Benoit TRÉLUYER 297.5 41 Free Practice 1 2 Audi Sport Team Joest Audi R18 e-tron quattro LMP1 Loïc DUVAL 295.9 46 Free Practice 1 8 Toyota Racing Toyota TS030 - Hybrid LMP1 Anthony DAVIDSON 291.9 31 Free Practice 1 12 Rebellion Racing Lola B12/60 Coupé - Toyota LMP1 Neel JANI 291.9 34 Free Practice 1 13 Rebellion Racing Lola B12/60 Coupé - Toyota LMP1 Andrea BELICCHI 288.0 22 Free Practice 1 21 Strakka Racing HPD ARX 03c - Honda LMP1 Jonny KANE 283.5 23 Free Practice 1 26 G-Drive Racing Oreca 03 - Nissan LMP2 Roman RUSINOV 274.1 35 Free Practice 1 49 Pecom Racing Oreca 03 - Nissan LMP2 Pierre KAFFER 272.7 30 Free Practice 1 35 OAK Racing Morgan - Nissan LMP2 Ricardo GONZALEZ 272.0 24 Free Practice 1 24 OAK Racing Morgan - Nissan LMP2 Olivier PLA 271.4 34 Free Practice 1 31 Lotus Lotus T128 LMP2 James ROSSITER 270.7 15 Free Practice 1 25 Delta-ADR Oreca 03 - Nissan LMP2 Antonio PIZZONIA 270.0 25 Free Practice 1 28 Gulf Racing Middle East Lola B12/80 Coupé - Nissan LMP2 Fabien GIROIX 270.0 32 Free Practice 1 32 Lotus Lotus T128 LMP2 Jan CHAROUZ 270.0 31 Free Practice 1 45 OAK Racing Morgan - Nissan LMP2 Jacques NICOLET 270.0 35 Free Practice 1 41 Greaves Motorsport Zytek Z11SN - Nissan -
WRC Rallye D'espagne
MEDIA INFORMATION November 2013 2013 FIA World Endurance Championship Round 7: 6 Hours of Shanghai Victory for the N°1 AUDI R18 e-tron quattro/MICHELIN, as Tom Kristensen/Loïc Duval/Allan McNish secure the 2013 WEC Drivers’ title After the torrential rain that forced the organisers to halt the recent 6 Hours of Fuji after just 16 laps, all spent behind the safety car, Audi Sport Team Joest and Toyota Motorsport GmbH were both eager to join battle once again this weekend in China. In contrast to the conditions encountered in Japan, the 6 Hours of Shanghai was marked by clear skies and warm weather (air temperature: approximately 25°C, and track temperatures up to 30°C) which enabled the teams to produce yet another thrilling show, with the outcome only settled with less than half-an-hour remaining. The pole-winning N°7 Toyota TS030-Hybrid of Wurz/Lapierre carved out an early lead, while the N°8 sister car – with Antony Davidson in command – engaged in a fight with André Lotterer in the N°1 Audi R18 e-tron quattro. On Lap 10, the British driver succeeded in finding a way past to ease into second place. The two Japanese prototypes then proceeded to dominate the top of the leaderboard until the eventful 143rd lap (190 laps completed in total). After 4½ hours of racing, the N°8 Toyota TS030-Hybrid was suddenly eliminated when its front- right suspension failed under barking for Turn 6. This promoted the N°1 Audi to second spot, approximately half-a-minute behind the N°7 Toyota, thanks to a strong stint from Benoît Tréluyer in the German car, as well as to a couple of time-consuming „moments‟ for the Japanese team‟s Nicolas Lapierre while overtaking slower competitors. -
WRC Rallye D'espagne
INFORMATION MEDIA Octobre 2013 Sixième manche : 6 Heures de Fuji 2013 La Toyota TS030-Hybrid de Kazuki NAKAJIMA s’impose à Fuji, Audi Sport Team Joest est Champion du Monde des Constructeurs Des victoires importantes, obtenues lors d’une course arrêtée à cause de la pluie battante Le ciel couvert par des nuages épais et la piste arrosée par une pluie battante n’ont cessé qu’à de rares moments. Voici les conditions dantesques dans lesquelles les concurrents des 6 Heures de Fuji 2013 ont pris le départ de la course à 11h00, derrière la safety car. Au bout de 8 tours, et une fois constaté que le manque de visibilité ne permettait pas de continuer à rouler en sécurité, le Directeur de course a imposé un premier drapeau rouge. Après plus de deux heures de parc fermé, les voitures ont recommencé à rouler, toujours sous la tutelle de la safety car. Encore 7 tours sont accomplis par les concurrents avant qu’un deuxième drapeau n’arrête à nouveau l’épreuve. L’attente dure jusqu’à 15h35 : les voitures reprennent la piste pour boucler un dernier tour avant la fin anticipée décrétée par les instances. Ainsi, les 6 Heures de Fuji 2013 se sont finalement achevées après 16 tours seulement, parcourus (à trois reprises) par les concurrents derrière la safety car. La Toyota TS030-Hybrid n°7 et le pilote japonais Kazuki NAKAJIMA (associé à Wurz/Lapierre) sont décrétés vainqueurs. Ils sont suivis sur le podium par le trio de pilotes officiels de l’Audi R18 e-tron quattro composé par Kristensen/Duval/McNish. -
2013 Fia World Endurance Championship - 6 Hours of Fuji - Provisionnal Entry List
2013 FIA WORLD ENDURANCE CHAMPIONSHIP - 6 HOURS OF FUJI - PROVISIONNAL ENTRY LIST N° LMP1 NAT T CARS HYBRID DRIVER 1 DRIVER 2 DRIVER 3 5 1 AUDI SPORT TEAM JOEST DEU M Audi R18 e-tron quattro Hybrid André Lotterer (DEU) P Benoit Tréluyer (FRA) P Marcel Fässler (CHE) P 2 AUDI SPORT TEAM JOEST DEU M Audi R18 e-tron quattro Hybrid Tom Kristensen (DNK) P Loïc Duval (FRA) P Allan McNish (GBR) P 7 TOYOTA RACING JPN M Toyota TS030 - Hybrid Hybrid Alexander Wurz (AUT) P Nicolas Lapierre (FRA) P Kazuki Nakajima (JPN) P 8 TOYOTA RACING JPN M Toyota TS030 - Hybrid Hybrid Anthony Davidson (GBR) P Sébastien Buemi (CHE) P Stéphane Sarrazin (FRA) P 12 REBELLION RACING CHE M Lola B12/60 Coupé - Toyota Andrea Belicchi (ITA) P Mathias Beche (CHE) P - N° LMP2 NAT T CARS DRIVER 1 DRIVER 2 DRIVER 3 10 24 OAK RACING FRA D Morgan - Nissan Olivier Pla (FRA) P David Heinemeier Hansson (DNK) S Alex Brundle (GBR) G 25 DELTA-ADR GBR D Oreca 03 - Nissan Tor Graves (GBR) S James Walker (GBR) G Shinji Nakano (JPN)° P 26 G-DRIVE RACING RUS D Oreca 03 - Nissan Roman Rusinov (RUS) S John Martin (AUS) P Mike Conway (GBR) P 27 GAINER INTERNATIONAL JPN D Zytek Z11SN - Nissan Katsuyuki Hiranaka (JPN) G Masayuki Ueda (JPN) S Björn Wirdheim (SWE) P 31 LOTUS CZE D Lotus T128 Kevin Weeda (USA) B James Rossiter (GBR) P Vitantonio Liuzzi (ITA) P 32 LOTUS* CZE D Lotus T128 Thomas Holzer (DEU) S Dominik Kraihamer (AUT) G Jan Charouz (CZE) G 35 OAK RACING FRA D Morgan - Nissan Bertrand Baguette (BEL) P Ricardo Gonzalez (MEX) S Martin Plowman (GBR) G 45 OAK RACING FRA D Morgan - Nissan -
Driver Fastest Lap
FIA WEC WEC 6 HOURS OF SPA-FRANCORCHAMPS Free Practice 2 Provisional Classification by Driver Fastest Lap Nr Team Car Class Driver Time Lap Total Gap Kph 1 1 Audi Sport Team Joest Audi R18 e-tron quattro LMP1 André LOTTERER 2:01.276 20 22 207.9 2 3 Audi Sport Team Joest Audi R18 e-tron quattro LMP1 Lucas DI GRASSI 2:01.377 2 20 0.101 0.101 207.7 3 2 Audi Sport Team Joest Audi R18 e-tron quattro LMP1 Tom KRISTENSEN 2:01.690 16 20 0.414 0.313 207.2 4 1 Audi Sport Team Joest Audi R18 e-tron quattro LMP1 Marcel FÄSSLER 2:01.850 19 21 0.574 0.160 206.9 5 12 Rebellion Racing Lola B12/60 Coupé - Toyota LMP1 Nick HEIDFELD 2:02.305 2 4 1.029 0.455 206.2 6 7 Toyota Racing Toyota TS030 - Hybrid LMP1 Alexander WURZ 2:02.332 13 15 1.056 0.027 206.1 7 8 Toyota Racing Toyota TS030 - Hybrid LMP1 Stéphane SARRAZIN 2:02.524 17 18 1.248 0.192 205.8 8 2 Audi Sport Team Joest Audi R18 e-tron quattro LMP1 Loïc DUVAL 2:02.723 10 15 1.447 0.199 205.5 9 12 Rebellion Racing Lola B12/60 Coupé - Toyota LMP1 Neel JANI 2:02.727 10 19 1.451 0.004 205.4 10 7 Toyota Racing Toyota TS030 - Hybrid LMP1 Nicolas LAPIERRE 2:02.928 17 22 1.652 0.201 205.1 11 8 Toyota Racing Toyota TS030 - Hybrid LMP1 Sébastien BUEMI 2:02.987 13 21 1.711 0.059 205.0 12 3 Audi Sport Team Joest Audi R18 e-tron quattro LMP1 Marc GENÉ 2:03.045 3 14 1.769 0.058 204.9 13 2 Audi Sport Team Joest Audi R18 e-tron quattro LMP1 Allan MCNISH 2:03.124 6 14 1.848 0.079 204.8 14 7 Toyota Racing Toyota TS030 - Hybrid LMP1 Kazuki NAKAJIMA 2:03.396 3 12 2.120 0.272 204.3 15 3 Audi Sport Team Joest Audi R18 e-tron -
Yaris Hybrid Na Celom Svete Revolution a Sedan)
Všetko o hybridnom pohone spoločnosti Toyota 0 ROČNÁ 1 Z R Á O R T U Á K L A U N M A U H K Y A B Ý R N I D * Záruka platí len v prípade pravidelného servisu akumulátora v autorizovanej sieti Toyota. Podrobnosti získate od predajcu. COMPACT HYBRID REVOLUTION Už viac ako 20 rokov ponúka spoločnosť Toyota automobily vybavené revolučnou hybridnou technológiou, ktoré získavajú uznanie medzi našimi zákazníkmi, ako aj v prestížnych rebríčkoch. Hybridné automobily značky Toyota sú dôkazom toho, že technický vývoj môže ísť ruka v ruke so starostlivosťou o životné prostredie. Naším cieľom je ponúkať inovatívne riešenia, vďaka ktorým si vodiči môžu užívať úspornejšiu a zároveň pohodlnú a bezporuchovú jazdu. Hybridná technológia je dôležitým míľnikom v oblasti vývoja automobilov, ktorý mení tvár trhu a vytyčuje trendy do budúcnosti. Budúcnosti, ktorú môžete spoznať už dnes. Rozšírte si vedomosti o hybridnom pohone v automobiloch Toyota. HistoriaCesta hybridných vozidiel Toyota 1997 2002 prvý sériovo hybrid 1937 vyrábaný s vodíkovými 2005 vzniká hybrid na svete: palivovými prvý hybridný 2009 2011 Toyota Motor Toyota Prius článkami: model Lexus: Toyota Prius premiéra modelu Corporation I. generácie Toyota FCHV RX 400h III. generácie Lexus CT 200h 1977 2001 2003 2007 2010 2012 prvý prototyp premiéra modelu Toyota Prius premiéra prvý hybridný prvý hybrid s hybridným Toyota Estima II. generácie modelov kompakt: zo segmentu B: pohonom: Hybrid Lexus LS 600h Toyota Auris Toyota Yaris Toyota Sports 800 v Japonsku a LS 600h L Hybrid Hybrid 4 2013 v apríli presiahol 2015 2016 2019 predaj hybridných viac ako 8 mil. premiéra premierá modelov 2012 modelov Toyota 2014 predaných nového modelu Corolla Hybrid prvý hybrid na celom svete premiéra hybridných Toyota C‑HR – (Hatchback, zo segmentu MPV: (od uvedenia na trh) nového modelu vozidiel Toyota Compact Hybrid Touring Sports Prius+ hranicu 5 mil. -
Newsletter | Your Update on What’S New from DENSO Aftermarket Sales
Newsletter | Your update on what’s new from DENSO Aftermarket Sales Issue number 42 | March 2015 Menu > Follow the links below! Inside this issue… > Auto Professioneel & Schadeherstel Tradeshow, Netherlands > Spotlight on Spark Plugs > 2014 FIA WEC Toyota Racing win > Third quarter financial results > May we introduce – Mark Robertson > Toyota TS030 Hybrid Le Mans racing car on stand, featuring a rear hybrid motor system specifically developed by DENSO. Gorinchem tradeshow a sparkling success DENSO exhibited at the Auto Professioneel answer questions on all DENSO products continue strengthening interest in the & Schadeherstel Tradeshow which took available to retailers and garages. DENSO brand in the Netherlands,” place in Gorinchem, The Netherlands explained Dominic. on February 3rd – 5th. The three day Another big draw on the stand was the event attracted around 16,000 visitors, DENSO sponsored Toyota TS030 Hybrid The next Auto Professioneel & and featured 250 exhibitors from the Le Mans racing car, featuring a rear Schadeherstel Tradeshow will take automotive industry. hybrid motor system specifically place in early 2016. developed by DENSO. DENSO took the opportunity to showcase a selection of products and parts from Stand visitors also had the opportunity its world-leading aftermarket programme to register with Automotive Diamonds, on three display areas which have been the popular, web-based customer loyalty tailor-made for exhibitions. Interest from scheme enabling garages and installers workshop and wholesaler visitors to the to maximise the benefits and reap the stand was also very high, with particular rewards of purchasing products from emphasis on A/C Compressors thanks to a DENSO and its programme partners. -
In Touch the Official Magazine of Dunlop Motorsport [ ] Le Mans Race Edition
IN TOUCH THE OFFICIAL MAGAZINE OF DUNLOP MOTORSPORT [ www.injection.tv ] LE MANS RACE EDITION Dunlop came away from the Le Mans 24 hours delighted with the performance of its dry and light wet tyres after a difficult race in which the changing condi- tions contributed to the overall result. “We were pretty competitive in all conditions other than full wet conditions,” says Dunlop’s chief tyre technician Matthew Simpson of the LMP2 tyres. “On the slick tyres and the light wet tyres, we had a performance advantage, but in full wet conditions we struggled to get temperature into our compounds. The Essex car had engine trouble so we were never going to do better than we did, but we have to look at the tyre perform- ance in wet conditions and make it better. “The Virgo Ferrari team were very strong and our development construction at the rear allowed us to double stint safely. There was no sign of difficulty in doing so, and there was zero deterioration from the first lap to the last in a double stint, according to the drivers. Le Mans podiums for Essex Perhaps we could have triple stinted, but we didn’t test that before the race and during the race was not the time to try. Porsche and Farnbacher Ferrari “The Creation team had four punctures and three of them were caused by debris. There was not enough left of the tyre to establish the cause of the fourth.” The 2008 edition of the Le Mans 24 hours produced was difficult to drive because sometimes the power was everything from a record breaking qualifying and race there, other times it wasn’t and we couldn’t know what to John Nielsen, Casper Elgaard and Sascha Maassen pace, a record crowd of 258,500 turning out in eager expect. -
Kinetic Energy Recovery System - Wikipedia 1 of 8
Kinetic energy recovery system - Wikipedia 1 of 8 Kinetic energy recovery system A kinetic energy recovery system (KERS) is an automotive system for recovering a moving vehicle's kinetic energy under braking. The recovered energy is stored in a reservoir (for example a flywheel or high voltage batteries) for later use under acceleration. Examples include complex high end systems such as the Zytek, Flybrid,[1] Torotrak[2][3] and Xtrac used in Formula One racing and simple, easily manufactured and integrated differential based systems such as the Cambridge Passenger/Commercial Vehicle Kinetic Energy Recovery A Flybrid Systems kinetic energy System (CPC-KERS). recovery system. Xtrac and Flybrid are both licensees of Torotrak's technologies, which employ a small and sophisticated ancillary gearbox incorporating a continuously variable transmission (CVT). The CPC-KERS is similar as it also forms part of the driveline assembly. However, the whole mechanism including the flywheel sits entirely in the vehicle's hub (looking like a drum brake). In the CPC-KERS, a differential replaces the CVT and transfers torque between the flywheel, drive wheel and road wheel. Contents Use in motor sport History Formula One Working diagram for KERS Autopart makers Carmakers Motorcycles Bicycles Races Use in public transport London buses See also References Use in motor sport https://en.wikipedia.org/wiki/Kinetic_energy_recovery_system Kinetic energy recovery system - Wikipedia 2 of 8 History The first of these systems to be revealed was the Flybrid.[4] This system weighs 24 kg (53 lbs) and has an energy capacity of 400 kJ after allowing for internal losses. A maximum power boost of 60 kW (81.6 PS, 80.4 HP) for 6.67 seconds is available. -
Programme Peugeot Sport 2008
PROGRAMME PEUGEOT SPORT 2008 - Press release - Peugeot 908 HDi FAP - Technical Data - Calendar - Drivers - The team - Press officer - Motor Sport Promotional Activities 2008 PROGRAMME A YEAR OF MANY CHALLENGES The 2007 season turned out to be one of the most rewarding ever for Peugeot Sport which launched four different new cars on the world motor sport scene, from the factory programme with the 908 HDi FAP to its package of promotional formulae with the 207 LW THP, 207 Super 2000 and Spider THP. The lessons learned by the team while finding its marks last year will be implemented in 2008 and all its energy will be devoted to building on that experience to achieve its objectives. This time last year, under the leadership of Michel Barge, Peugeot Sport organised a dynamic presentation of the new 908 HDi FAP to announce its modest objectives for the season ahead. Following the car's initial gestation, which was rapid to say the least, Team Peugeot Total enjoyed a memorable season which brought its fair share of surprises, satisfactions and passion, not to mention the unrelenting toil which enabled it to secure results well beyond its expectations and targets. Indeed, never in Peugeot's history had a competition car won out of the box, yet the 908 HDi FAP claimed victory in its debut race at Monza before going on to clinch the 2007 Le Mans Series. Team Peugeot Total won all six rounds, started from pole position each time and posted every fastest race lap, not to mention its unhoped-for performance at Le Mans where it started from pole position before taking second place at the end of the 24-hour race. -
Motor Sports
Motor Sports Hiromasa Tanaka1) Hiromi Hayashi2) Satoru Terada3) Shinichi Yamashita3) 1)Honda R&D 2)Toyota Motor 3)Suzuki Motor 4)Bridgestone 2. 1. 1. Super GT (Fig. 1) 1 Introduction The racing distances of the second round (Fuji Speed- Even as countries around the world face up to eco- way) and fifth round (Suzuka), which were shortened in nomic and environmental issues, activities are being pur- 2009 to reduce participation costs, were returned to the sued to ensure the continued future of motor sports. original distances of 500 and 1,000 km, respectively, in Major regulatory changes in motor sports in 2012 2012. Four official tests are now held each year, increas- included the introduction of different standard engine ing the amount of vehicle and tire development testing displacements for the motorcycle Road Racing World in conjunction with the tire manufacturer tests. Championship Grand Prix. However, as car racing is on In the GT300 class, participating cars must be based the verge of substantial changes to power plant regula- on production vehicles. Cars are now divided into two tions, no major changes to regulations occurred in 2012. main categories: FIA GT3 cars and JAF-GT300 cars that However, steady progress was made in specific technical are based on authorized or registered vehicles (other studies in anticipation of the future modifications. cars were limited to participants in the 2011 series that In Japan, Suzuka Circuit celebrated the 50th anniver- were allowed to continue racing in 2012). The regula- sary of its construction as the country's first full-scale tions for performance adjustment of FIA GT3 cars have racing circuit in September 1962.