Technical University of Crete Department of Mineral Resources Engineering Master Thesis in Petroleum Engineering
Total Page:16
File Type:pdf, Size:1020Kb
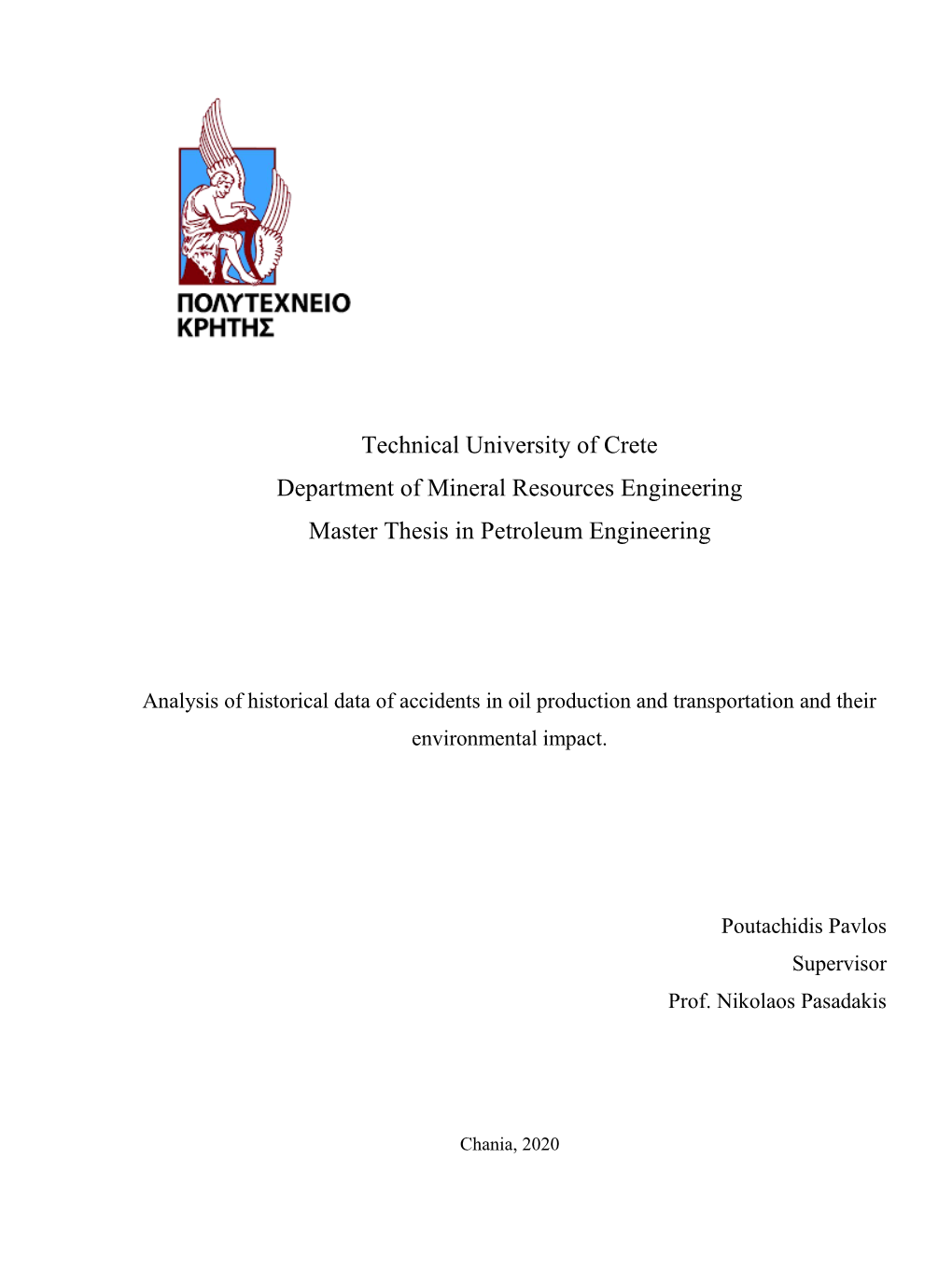
Load more
Recommended publications
-
Crisis-Induced Learning and Issue Politicization in the Eu: the Braer, Sea Empress, Erika,Andprestige Oil Spill Disasters
doi: 10.1111/padm.12170 CRISIS-INDUCED LEARNING AND ISSUE POLITICIZATION IN THE EU: THE BRAER, SEA EMPRESS, ERIKA,ANDPRESTIGE OIL SPILL DISASTERS WOUT BROEKEMA This article explores the relation between issue politicization and crisis-induced learning by the EU. We performed a political claims analysis on the political response to the four major oil spill disasters that have occurred in European waters since 1993. Political claims that we observed in three arenas (mass media, national parliaments, and the European Parliament) were compared with recommen- dations in post-crisis evaluation reports and the EU’s legislative responses. For all three political arenas our findings indicate that politicization of issues either promotes or impedes crisis-induced EU learning, which points to the existence of determining intervening factors. EU legislation that is adopted in response to oil spill disasters appears to a large extent grounded in crisis evaluation reports. Characteristics of crisis evaluation reports, especially the degree of international focus, seem to offer a more plausible explanation for variance in crisis-induced learning outcomes than politi- cization. INTRODUCTION On 15 January 1996, the Liberian-registered oil tanker Sea Empress ran aground on the rocks at the entrance to Milford Haven, releasing 72,000 tonnes of oil into the sea in the following days. Only three years later, on 12 December 1999, a very similar accident occurred in the European Atlantic when the Maltese-registered tanker Erika sank due to rough weather conditions off the Brittany coast, causing an oil spill of 20,000 tonnes. Both accidents had a dramatic long-term environmental, social, and economical transboundary impact (EMSA 2004; Wene 2005). -
An Empirical Profile of South African Cadets and Implications for Career Awareness
1 TABLE OF CONTENTS NO. TOPIC PAGE NO. 1 Ten Lessons in providing MET remotely by Quentin N. Cox 1 2. SAMTRA’s road to e-Learning in the South African Maritime industry by Gregory Moss 15 3. Using multimedia to understand ship design by Ashok Mulloth 29 4. Innovative manoeuvring support by simulation augmented methods – on-board and from the shore methods - on board and from shore by Knud Benedict, Michael Gluch, Sandro Fischer and Michele Schaub 36 5. The 3-D simulation of collision detection and response between ships in navigational simulator by Guan Ke-ping, Ying Shijun, Jia Dongxing and Jiang Jingnan 52 6 Application of marine simulators to bridge the gap between theory and practice in BRM teaching by Chen Jin-biao, Guan Ke-ping, Jia Dong-Xing and Zhuang Xinqing 63 7. Developing maritime theoretical education tools for a lack of seagoing exposure on the part of marine engineering students at CPUT by Derek Lambert 75 8. Looking at human factors in cases of accidents- nurturing inner-motivation and solidarity by Hitosh Sekiya, Takash Shirozu and Katsuya Matsui 82 9. Moving from training to practice- a comparison of the maritime and aviation industry crew resource management education programs by Greg Hanchrow 90 10. The conditional effect of maritime student’s demographic characteristics on career commitment at different levels of career motivation by Shaun Ruggunan and Herbert Kanengoni 99 11. Towards a career capital approach in explaining career development patterns amongst female seafarers in Durban by Slindile Mgaga 109 12. Wellness at sea: a new conceptual framework for seafarer training by Johan Smit 117 13. -
An Environmental Restoration Programme 12 Years After: the HAVEN Wreck
Les journées d’information du CEDRE – 6 octobre 2003 Le Traitement des Epaves Potentiellement Polluantes An Environmental Restoration Programme 12 Years After: the HAVEN Wreck E. Amato ICRAM–Central institute for marine applied research Via di Casalotti 300, 00166 Rome, Italy [email protected] Synopsis The VLCC “HAVEN” accident is the major case of oil spill ever occurred in the Mediterranean Sea. On April 11th 1991, while the “HAVEN” was anchored in front of the port of Genoa, two violent explosions started a fire within the ship that was extinguished only 70 hours later when the Very Large Crude Carrier sunk. At the moment of the accident the ship was carrying 144.000 tons of “heavy Iranian crude oil”. A large quantity of burnt oil rapidly sank in form of bitumen, while the rest of the cargo was dispersed by the Ligurian-Provençal current and by the winds. 1 Les journées d’information du CEDRE – 6 octobre 2003 Le Traitement des Epaves Potentiellement Polluantes During the emergency phase operations began in order to contain the pollution. Two important decisions were taken: to tug the ship coastward and to allow the burning of the greatest part of the oil spilled at sea. The operations concerned the containment of the spilled oil, the collection of the oil both at sea and on shore and the performing of an environmental control and monitoring plan. Twelve years later a restoration programme is on the way mainly dealing with the tar residues laying on the seabed and with the oil products still contained in the wreck. -
Study on Effective Methods Foroil Products Cleaning
1 Plant Archives Vol. 19, Supplement 2, 2019 pp. 483-489 e-ISSN:2581-6063 (online), ISSN:0972-5210 STUDY ON EFFECTIVE METHODS FOR OIL PRODUCTS CLEANING Danehpash Shaghayegh 1, Farshchi Parvin 2*, Roayaei Emad 3, Ghoddousi Jamal 4 and Hassani Amir Hesam 5 1Department of Environmental Science, Faculty of Environment and Energy, Science and Research Branch, Islamic Azad University, Tehran, Iran. 2Department of Environmental Science, Faculty of Environment and Energy, Science and Research Branch, Islamic Azad UniversityTehran, Iran. *corresponding author 3Iranian National Oil Company,Tehran,Iran. 4Department of Environmental Management, Faculty of Environment and Energy, Science and Research Branch, Islamic Azad University, Tehran, Iran. 5Department of Environmental Engineering, Faculty of Environment and Energy, Science and Research Branch, Islamic Azad University, Tehran, Iran. *Corresponding Author Department of Environmental Science, Faculty of Environment and Energy, Science and Research Branch, Islamic Azad University, Tehran, Iran Abstract The hydrocarbon compounds which are discharged in to the environment are affected by various physical, chemical and biological alterations. Oil spill are a global concern due to the environmental impacts. The main concern of the environmental experts is the pollution from the production and transfer of oil products in different ecosystems. Among the consequences of releases of various types of crude oil, it is possible to mention the adverse environmental effects, the death of marine organisms, the inappropriateness of seafood for human consumption and the reduction of the power of flying sea birds due to the impregnation of feathers into petroleum products. The cost of oil remediation depends on relatively large parameters such as the type of oil products that leads to pollution, the amount and severity of the contamination, the time of the accident, the location of the incident, the geographical, political, economical, physical and biological location of the accident. -
Prepared by Supervised By
Prepared By 4th Student of Special Geology Supervised By Prof. Dr. of Economic Geology Tanta University Faculty of Science Geology Department 2016 1 Abstract An oil spill is a release of a liquid petroleum hydrocarbon into the environment due to human activity, and is a form of pollution. The term often refers to marine oil spills, where oil is released into the ocean or coastal waters. Oil spills include releases of crude oil from tankers, offshore platforms, drilling rigs and wells, as well as spills of refined petroleum products (such as gasoline, diesel) and their by-products, and heavier fuels used by large ships such as bunker fuel, or the spill of any oily refuse or waste oil. Spills may take months or even years to clean up. During that era, the simple drilling techniques such as cable-tool drilling and the lack of blowout preventers meant that drillers could not control high-pressure reservoirs. When these high pressure zones were breached the hydrocarbon fluids would travel up the well at a high rate, forcing out the drill string and creating a gusher. A well which began as a gusher was said to have "blown in": for instance, the Lakeview Gusher blew in in 1910. These uncapped wells could produce large amounts of oil, often shooting 200 feet (60 m) or higher into the air. A blowout primarily composed of natural gas was known as a gas gusher. Releases of crude oil from offshore platforms and/or drilling rigs and wells can be observed: i) Surface blowouts and ii)Subsea blowouts. -
Conclusions for Part II: National Case Studies
This is a repository copy of Conclusions for Part II: National Case Studies. White Rose Research Online URL for this paper: http://eprints.whiterose.ac.uk/141836/ Version: Accepted Version Book Section: Carpenter, A orcid.org/0000-0002-1030-5866 and Kostianoy, AG (2018) Conclusions for Part II: National Case Studies. In: Carpenter, A and Kostianoy, AG, (eds.) Oil Pollution in the Mediterranean Sea: Part II. The Handbook of Environmental Chemistry, 84 . Springer International Publishing , Cham, Switzerland , pp. 263-285. ISBN 978-3-030-11137-3 https://doi.org/10.1007/698_2018_362 © 2018, Springer Nature Switzerland AG. This is a post-peer-review, pre-copyedit version of a chapter published in Oil Pollution in the Mediterranean Sea: Part II. The final authenticated version is available online at: https://doi.org/10.1007/698_2018_362. Uploaded in accordance with the publisher's self-archiving policy. Reuse Items deposited in White Rose Research Online are protected by copyright, with all rights reserved unless indicated otherwise. They may be downloaded and/or printed for private study, or other acts as permitted by national copyright laws. The publisher or other rights holders may allow further reproduction and re-use of the full text version. This is indicated by the licence information on the White Rose Research Online record for the item. Takedown If you consider content in White Rose Research Online to be in breach of UK law, please notify us by emailing [email protected] including the URL of the record and the reason for the withdrawal request. [email protected] https://eprints.whiterose.ac.uk/ Conclusions for Part II: National Case Studies Angela Carpenter1 and Andrey Kostianoy2 Abstract This book (Part 2 of a volume on “Oil Pollution in the Mediterranean Sea”) has presented a review of knowledge on oil pollution in the Mediterranean Sea, through a series of National and Regional Case Studies. -
Marine Environment Protection and Biodiversity Conservation: the Application and Future Development of the IMO’S Particularly Sensitive Sea Area Concept
University of Wollongong Thesis Collections University of Wollongong Thesis Collection University of Wollongong Year Marine environment protection and biodiversity conservation: the application and future development of the IMO’s particularly sensitive sea area concept Julian Peter Roberts University of Wollongong Roberts, Julian Peter, Marine environment protection and biodiversity conservation the appli- cation and future development of the IMO’s particularly sensitive sea area concept, PhD thesis, Centre for Maritime Policy, University of Wollongong, 2006. http://ro.uow.edu.au/theses/547 This paper is posted at Research Online. http://ro.uow.edu.au/theses/547 NOTE This online version of the thesis may have different page formatting and pagination from the paper copy held in the University of Wollongong Library. UNIVERSITY OF WOLLONGONG COPYRIGHT WARNING You may print or download ONE copy of this document for the purpose of your own research or study. The University does not authorise you to copy, communicate or otherwise make available electronically to any other person any copyright material contained on this site. You are reminded of the following: Copyright owners are entitled to take legal action against persons who infringe their copyright. A reproduction of material that is protected by copyright may be a copyright infringement. A court may impose penalties and award damages in relation to offences and infringements relating to copyright material. Higher penalties may apply, and higher damages may be awarded, for offences and -
Analysis of Oil Pollution at Sea by Means of Sea Craft in Spain
Analysis of oil pollution at sea by means of sea craft in Spain. Department of Nautical Engineering and Science Technical University of Catalonia Author: Dr. F. Xavier Martínez de Osés Lecturer Secretary for academics Department of Nautic al Science and Engineering Contents 1. Introduction................................................................................................................... 4 2. Contacting with the main department of controlling and following sea pollution in Spain ................................................................................................................................. 6 2.1. Introduction............................................................................................................ 6 1.2. Which department follows sea pollution............................................................... 6 1.3. Equipment and manning of the dedicated establishment ...................................... 8 1.4. What methods are used to control and follow pollution? ...................................... 8 1.4.1. Synthetic Aperture Radar (SAR) .................................................................... 8 1.4.2. Coastal spills................................................................................................... 9 1.5. The available budget for the pollution fighting agency....................................... 10 2. Penalties and fines and their effect on the affected companies .................................. 11 2.1. Main legislation bodies....................................................................................... -
Chapter 2 Hazardous and Noxious Substances
CHAPTER 2 HAZARDOUS AND NOXIOUS SUBSTANCES Introduction sea.”14 HNS encompasses thousands of products that are transported by ship around the world. Hazardous and Noxious Substances in Canada The marine transportation of HNS generally poses very little threat; hundreds of products are Hazardous and noxious substances (HNS) are safely transported, either as bulk liquids or solids moved in and out of Canadian ports every day. in specialized vessels or packaged and carried The International Maritime Organization defines among general cargo on container vessels HNS as “any substance other than oil which, if every day. A risk assessment commissioned by introduced into the marine environment, is likely Transport Canada also found that the risk posed to create hazards to human health, to harm living by select bulk HNS movements in Canadian resources and marine life, to damage amenities waters was relatively low. Notwithstanding or to interfere with other legitimate uses of the this result, and the fact that Canadian and 14 Protocol on Preparedness, Response and Co-operation to Pollution Incidents by Hazardous and Noxious Substances, 2000. International Maritime Organization, 2000. 53 international statistics generally point to a In the decades that followed the publication of low historical frequency of HNS incidents, the the Brander-Smith Panel’s report, a number of potential impacts of a release, should one occur, attempts were made to establish a Canadian could be harmful to human health (particularly in HNS preparedness and response program. populated areas) and the environment. However, these attempts have not been brought to a satisfactory conclusion. In the mid-1990s, Canada’s Ship-source Oil Spill Preparedness HNS Risk Assessment and Response Regime was implemented and, thereafter, the Canadian Coast Guard began In addition to other sources of information working on a Marine Chemical Emergency that informed our review, the results of a risk Response system for HNS releases. -
Recommendations for Maritime Transport Contents Executive Summary 3 Introduction 4
PHAROS4MPAS SAFEGUARDING MARINE PROTECTED AREAS IN THE GROWING MEDITERRANEAN BLUE ECONOMY RECOMMENDATIONS FOR MARITIME TRANSPORT CONTENTS EXECUTIVE SUMMARY 3 INTRODUCTION 4 PART ONE MARITIME TRANSPORT SECTOR: BACKGROUND INFORMATION 7 Front cover: Bottlenose dolphins (Tursiops truncatus) in the Strait of Gibraltar © Sylvain Cordier / Biosphoto PART TWO MARITIME TRANSPORT SECTOR: Publication We would like to warmly thank all the people and organizations who were part of the advisory group of this Published in May 2019 by PHAROS4MPAs. INTERACTIONS WITH MPAS 17 publication or kindly contributed in some other way: © PHAROS4MPAs. All rights reserved Robert Turk and Tina Centrih Genov (Institute of the Republic 2.1. How commercial transport activities affect MPAs 18 Reproduction of this publication for educational or other of Slovenia for Nature Conservation), Catherine Piante non-commercial purposes is authorized without prior written (WWF-France), Amalia Alberini (WWF-Greece), Panagiota 2.2. Impacts of maritime transport sector on marine ecosystems 26 permission from the copyright holder provided the source is Maragou (WWF-Greece), Julien Le Tellier (UN Environment/ fully acknowledged. Reproduction of this publication for resale MAP), Sylvain Petit (PAP/RAC), Oscar Esparza (WWF-Spain), 2.3. Shipping and ferries in MPAs: where are they permitted? 31 or other commercial purposes is prohibited without prior Theodora Papatheochari and Spyros Niavis (University of written permission of the copyright holder. Thessaly), Atef Ouerghi (RAC/SPA), Wissem Seddik (MedPAN), Eric Charbonnel (Parc Marin de la Côte Bleue), PART THREE Citation of this report: Randone, M., Bocci, M., Castellani, C., Anthony Mastitski (WWF Mediterranean). Laurent, C. (2019). Safeguarding Marine Protected Areas in the RECOMMENDATIONS FOR MEDITERRANEAN STAKEHOLDERS: growing Mediterranean Blue Economy. -
UNILATERAL PORT STATE JURISDICTION Detention, Expulsion Or Request of Any Type of Information Prior to the to Attend the Public Defence Entry Into the Port
U The capacity to act as a port state in international law is best described NILATERAL INVITATION by the specific powers exercised over foreign ships, namely inspection, UNILATERAL PORT STATE JURISDICTION detention, expulsion or request of any type of information prior to the To attend the public defence entry into the port. Many of these powers are explicitly attributed to the of my PhD thesis entitled: state in multilateral instruments, whereby the flag state consents to having its ships subject to the jurisdiction of the port state. Notwithstanding the P THE QUEST FOR UNIVERSALITY IN THE PREVENTION, consensus around the complementary nature of port state jurisdiction ORT with respect to certain obligations of the flag state, the port state is not REDUCTION AND CONTROL OF SHIP-SOURCE POLLUTION UNILATERAL PORT STATE limited to fulfil a secondary role. This is especially visible in the prevention, S JURISDICTION reduction and control of ship-source pollution, where some port states TATE have not hesitated in acting regardless of an expressed consent by the flag state to the rule or standard being applied with the support of port J By Nelson F. Coelho powers. Not only do port states use more stringent enforcement powers URISDICTION to ensure that international treaties are effective, but they also prescribe novel rules and standards upon any foreign ship that approaches the Tuesday 12 February 2019 port, often as a means of breaking an international negotiation deadlock. at 12:45 hours This study discusses the international legal basis for such unilateral jurisdiction by analysing the principles of state jurisdiction under the dichotomy parochial/cosmopolitan. -
Written by Zechariah Von Den Burg
A Thesis of Angels Written by Zechariah Von Den Burg Version 2.0 Index (All chapters start at Page 1 for easier navigation) 1. Foreword 2. Thesis of Angels 3. Science of Angels -1. Ancient Evidence (Pages 1-21) -1.1: Ancient artifacts and writings (Pages 2-5) -1.2: Egypt (Pages 5-6) -1.3: Indus Valley (Pages 6-10) -1.4: Biblical evidence (Pages 10-15) -1.5: Gnostic Gospels (Pages 15-16) -1.6: Americas (Pages 16-17) -1.7: Wikiana collection (Pages 17-21) -2. Modern day Evidence (Pages 21-27) -Conclusion (Pages 27-28) 4. Precession of faith -Hypothesis (Pages 1-2) -20,000-10,000 B.C. (Pages 2-10) -Shamanism (Pages 6-9) -6000-4500 B.C. (Pages 11-12) -5000 B.C. (Pages 12-14) -4500-1000 B.C. (Pages 14-23) -Sumeria (Pages 14-16) -Egypt (Pages 16-20) -Indus Valley (Pages 20-23) -Creation myths (Pages 23-43) -Mesopotamian Creation (Pages 25-34) -Egyptian Creation myth (Pages 34-36) -Indus valley Creation myth (Pages 36-39) -Greek Creation myth (Pages 39-40) -Roman Creation myth (Pages 40-41) -Norse Creation myth (Pages 42-43) -Flood myth (Pages 44-52) -Sumerian (Pages 44-47) -Egyptian (Page 47) -Indus Valley (Pages 48-49) -Ancient Greece (Pages 49-51) -Ancient China (Page 51) -Native Americans (Pages 51-52) -Conclusion (Pages 53-54) 5. Precession of Culture -Hypothesis (Pages 1-2) -Vincan (Pages 2-4) -Sumerian (Pages 4-12) -Egyptian (Pages 12-23) -Indus Valley (Pages 23-31) -Minoan Civilization (Pages 32-36) -Greece (Pages 37-44) -Conclusion (Pages 44-45) 6.