Rats Studies in Molecular Distillation a Thesis
Total Page:16
File Type:pdf, Size:1020Kb
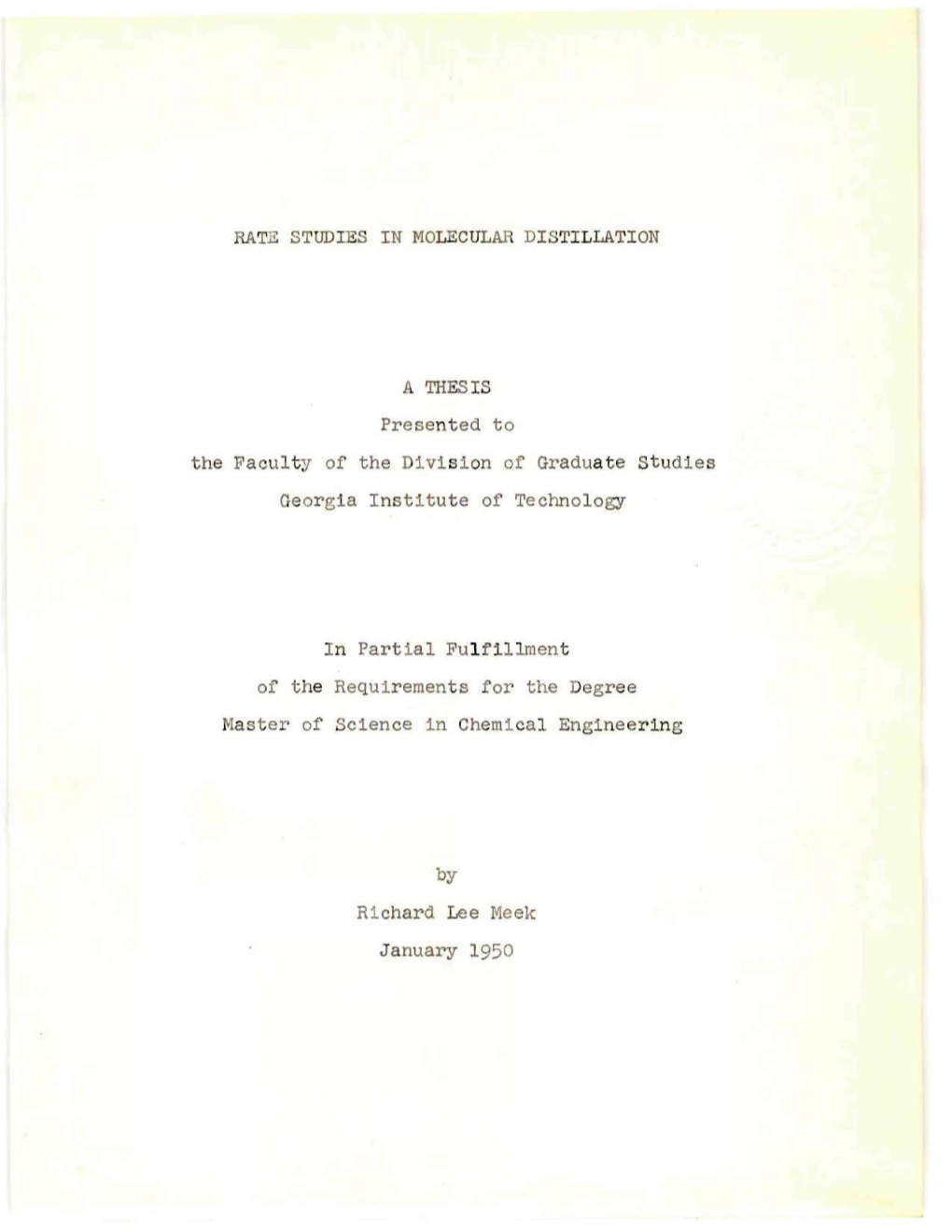
Load more
Recommended publications
-
CHEMISTRY ASSIGNMENT CLASS VII CHAP 3, Part – II Elements , Compounds and Mixture ( Separation Techniques of Mixtures )
CHEMISTRY ASSIGNMENT CLASS VII CHAP 3, Part – II Elements , compounds and Mixture ( Separation Techniques of Mixtures ) Mixture can be separated into its constituent by various method. Seperation technique totally depend upon the nature of the constituent. Q1. Describe a method to separate solid to solid mixture . Ans . We can separate solid to solid mixture by using Solvent Method , when one of the component is soluble. In this method we use a appropriate solvent to dissolve one of the component of the mixture .After that we filter the solute .The soluble solute get filtered from the insoluble solid. The filtered solution can be further separated from the solvent by heating or keeping in the sun.In this way we can separate out the two mixture. Q2. Differentiate between Solute and Solvent. Ans Solute Solvent The solid that is dissolved or spread evenly in the The liquid in which solute is dissolved is called solvent is called Solute . solvent. e.g. In sugar syrup sugar is the solute. e.g. In sugar syrup water is the solvent Q3. Name the various method used to separate solid to liquid mixture. Ans. The solid to liquid mixtures can be separated by various method – i. Evaporation ii. Filtration iii. Distillation Q4. What do you mean by filtration ? Draw a well labelled diagram to show filtration. Give one example too. Ans. Filtration is the simplest method to separate mixture when it contain one insoluble solid component and a liquid component by using a filter paper. The clear liquid that passes through the filterpaper is called Filtrate . -
Experiment 2 — Distillation and Gas Chromatography
Chem 21 Fall 2009 Experiment 2 — Distillation and Gas Chromatography _____________________________________________________________________________ Pre-lab preparation (1) Read the supplemental material on distillation theory and techniques from Zubrick, The Organic Chem Lab Survival Manual, and the section on Gas Chromatography from Fessenden, Fessenden, and Feist, Organic Laboratory Techniques, then read this handout carefully. (2) In your notebook, write a short paragraph summarizing what you will be doing in this experiment and what you hope to learn about the efficiencies of the distillation techniques. (3) Sketch the apparatus for the simple and fractional distillations. Your set-up will look much like that shown on p 198 of Zubrick, except that yours will have a simple drip tip in place of the more standard vacuum adaptor. (4) Look up the structures and relevant physical data for the two compounds you will be using. What data are relevant? Read the procedure, think about the data analysis, and decide what you need. (5) Since you have the necessary data, calculate the log of the volatility factor (log α) that you will need for the theoretical plate calculation. Distillation has been used since antiquity to separate the components of mixtures. In one form or another, distillation is used in the manufacture of perfumes, flavorings, liquors, and a variety of other organic chemicals. One of its most important modern applications is in refining crude oil to make fuels, lubricants, and other petrochemicals. The first step in the refining process is separation of crude petroleum into various hydrocarbon fractions by distillation through huge fractionating columns, called distillation towers, that are hundreds of feet high. -
Tailoring Diesel Bioblendstock from Integrated Catalytic Upgrading of Carboxylic Acids: a “Fuel Property First” Approach Xiangchen Huoa,B, Nabila A
Electronic Supplementary Material (ESI) for Green Chemistry. This journal is © The Royal Society of Chemistry 2019 Tailoring Diesel Bioblendstock from Integrated Catalytic Upgrading of Carboxylic Acids: A “Fuel Property First” Approach Xiangchen Huoa,b, Nabila A. Huqa, Jim Stunkela, Nicholas S. Clevelanda, Anne K. Staracea, Amy E. Settlea,b, Allyson M. Yorka,b, Robert S. Nelsona, David G. Brandnera, Lisa Foutsa, Peter C. St. Johna, Earl D. Christensena, Jon Lueckea, J. Hunter Mackc, Charles S. McEnallyd, Patrick A. Cherryd, Lisa D. Pfefferled, Timothy J. Strathmannb, Davinia Salvachúaa, Seonah Kima, Robert L. McCormicka, Gregg T. Beckhama, Derek R. Vardona* aNational Renewable Energy Laboratory, 15013 Denver West Parkway, Golden, CO, United States bColorado School of Mines, 1500 Illinois St., Golden, CO, United States cUniversity of Massachusetts Lowell, 220 Pawtucket St., Lowell, MA, United States dYale University, 9 Hillhouse Avenue, New Haven, CT, United States *[email protected] Section S1: Experimental Methods Catalyst synthesis and characterization Pt/Al2O3 catalyst was prepared by strong electrostatic adsorption method with chloroplatinic acid hexahydrate as Pt precursor. Al2O3 of 30-50 mesh and Pt precursor were added to deionized water, and solution pH was adjusted to 3 by adding HCl. After stirring overnight, the catalyst particles were recovered by filtration extensively washed with -1 deionized water. The catalyst was dried in the air and reduced in flowing H2 (200 mL min ) at 300°C for 4 h. BET surface area was determined by nitrogen physisorption using a Quadrasorb SI™ surface area analyzer from Quantachrome Instruments. Samples of ~80–120 mg were measured using a 55-point nitrogen adsorption/desorption curve at -196°C. -
Laboratory Rectifying Stills of Glass 2
» LABORATORY RECTIFYING STILLS OF GLASS 2 By Johannes H. Bruun 3 and Sylvester T. Schicktanz 3 ABSTRACT A complete description is given of a set of all-glass rectifying stills, suitable for distillation at pressures ranging from atmospheric down to about 50 mm. The stills are provided with efficient bubbling-cap columns containing 30 to 60 plates. Adiabatic conditions around the column are maintained by surrounding it with a jacket provided with a series of independent electrical heating units. Suitable means are provided for adjusting or maintaining the reflux ratio at the top of the column. For the purpose of conveniently obtaining an accurate value of the true boiling points of the distillates a continuous boiling-point apparatus is incor- porated in the receiving system. An efficient still of the packed-column type for distillations under pressures less than 50 mm is also described. Methods of operation and efficiency tests are given for the stills. CONTENTS Page I. Introduction 852 II. General features of the still assembly 852 III. Still pot 853 IV. Filling tube and heater for the still pot 853 V. Rectifying column 856 1. General features 856 2. Large-size column 856 3. Medium-size column 858 4. Small-size column 858 VI. Column jacket 861 VII. Reflux regulator 861 1. With variable reflux ratio 861 2. With constant reflux ratio 863 VIII. The continuous boiling-point apparatus 863 IX. Condensers and receiver 867 X. The mounting of the still 867 XI. Manufacture and transportation of the bubbling-cap still 870 XII. Operation of the bubbling-cap still 870 XIII. -
Heterogeneous Azeotropic Distillation
PROSIMPLUS APPLICATION EXAMPLE HETEROGENEOUS AZEOTROPIC DISTILLATION EXAMPLE PURPOSE This example illustrates a high purity separation process of an azeotropic mixture (ethanol-water) through heterogeneous azeotropic distillation. This process includes distillation columns. Additionally these rigorous multi- stage separation modules are part of a recycling stream, demonstrating the efficiency of ProSimPlus convergence methods. Specifications are set on output streams in order to insure the required purity. This example illustrates the way to set "non-standard" specifications in the multi-stage separation modules. Three phase calculations (vapor-liquid- liquid) are done with the taken into account of possible liquid phase splitting. ACCESS Free-Internet Restricted to ProSim clients Restricted Confidential CORRESPONDING PROSIMPLUS FILE PSPS_EX_EN-Heterogeneous-Azeotropic-Distillation.pmp3 . Reader is reminded that this use case is only an example and should not be used for other purposes. Although this example is based on actual case it may not be considered as typical nor are the data used always the most accurate available. ProSim shall have no responsibility or liability for damages arising out of or related to the use of the results of calculations based on this example. Copyright © 2009 ProSim, Labège, France - All rights reserved www.prosim.net Heterogeneous azeotropic distillation Version: March, 2009 Page: 2 / 12 TABLE OF CONTENTS 1. PROCESS MODELING 3 1.1. Process description 3 1.2. Process flowsheet 5 1.3. Specifications 6 1.4. Components 6 1.5. Thermodynamic model 7 1.6. Operating conditions 7 1.7. "Hints and Tips" 9 2. RESULTS 9 2.1. Comments on results 9 2.2. Mass and energy balances 10 2.3. -
Distillation Accessscience from McgrawHill Education
6/19/2017 Distillation AccessScience from McGrawHill Education (http://www.accessscience.com/) Distillation Article by: King, C. Judson University of California, Berkeley, California. Last updated: 2014 DOI: https://doi.org/10.1036/10978542.201100 (https://doi.org/10.1036/10978542.201100) Content Hide Simple distillations Fractional distillation Vaporliquid equilibria Distillation pressure Molecular distillation Extractive and azeotropic distillation Enhancing energy efficiency Computational methods Stage efficiency Links to Primary Literature Additional Readings A method for separating homogeneous mixtures based upon equilibration of liquid and vapor phases. Substances that differ in volatility appear in different proportions in vapor and liquid phases at equilibrium with one another. Thus, vaporizing part of a volatile liquid produces vapor and liquid products that differ in composition. This outcome constitutes a separation among the components in the original liquid. Through appropriate configurations of repeated vaporliquid contactings, the degree of separation among components differing in volatility can be increased manyfold. See also: Phase equilibrium (/content/phaseequilibrium/505500) Distillation is by far the most common method of separation in the petroleum, natural gas, and petrochemical industries. Its many applications in other industries include air fractionation, solvent recovery and recycling, separation of light isotopes such as hydrogen and deuterium, and production of alcoholic beverages, flavors, fatty acids, and food oils. Simple distillations The two most elementary forms of distillation are a continuous equilibrium distillation and a simple batch distillation (Fig. 1). http://www.accessscience.com/content/distillation/201100 1/10 6/19/2017 Distillation AccessScience from McGrawHill Education Fig. 1 Simple distillations. (a) Continuous equilibrium distillation. -
Building a Home Distillation Apparatus
BUILDING A HOME DISTILLATION APPARATUS A Step by Step Guide Building a Home Distillation Apparatus i BUILDING A HOME DISTILLATION APPARATUS Foreword The pages that follow contain a step-by-step guide to building a relatively sophisticated distillation apparatus from commonly available materials, using simple tools, and at a cost of under $100 USD. The information contained on this site is directed at anyone who may want to know more about the subject: students, hobbyists, tinkers, pure water enthusiasts, survivors, the curious, and perhaps even amateur wine and beer makers. Designing and building this apparatus is the only subject of this manual. You will find that it confines itself solely to those areas. It does not enter into the domains of fermentation, recipes for making mash, beer, wine or any other spirits. These areas are covered in detail in other readily available books and numerous web sites. The site contains two separate design plans for the stills. And while both can be used for a number of distillation tasks, it should be recognized that their designs have been optimized for the task of separating ethyl alcohol from a water-based mixture. Having said that, remember that the real purpose of this site is to educate and inform those of you who are interested in this subject. It is not to be construed in any fashion as an encouragement to break the law. If you believe the law is incorrect, please take the time to contact your representatives in government, cast your vote at the polls, write newsletters to the media, and in general, try to make the changes in a legal and democratic manner. -
Drinking Water Treatment: Distillation Bruce I
® ® University of Nebraska–Lincoln Extension, Institute of Agriculture and Natural Resources Know how. Know now. G1493 (Revised December 2013) Drinking Water Treatment: Distillation Bruce I. Dvorak, Extension Environmental Engineering Specialist Sharon O. Skipton, Extension Water Quality Educator water as it is boiled in the distiller. Such compounds will not Homeowners are increasingly concerned about be completely removed unless another process is used prior contaminants in their water supply that may affect to condensation. See the section in this NebGuide on treat- health or cause taste, odor, or nuisance problems. Dis- ment principles for further discussion of ways distillers may tillation, one of the oldest methods of water treatment, remove VOCs. is an effective method for reducing many impurities The boiling process during distillation generally inacti- found in water. This NebGuide discusses the process vates microorganisms. However, if the distiller is idle for an and related equipment used for household drinking extended period, bacteria can be reintroduced from the outlet water treatment by distillation. spigot and may recontaminate the water. Water Testing Contaminants Removed from Water by Distillation Regardless of which water treatment system is con- Distillation can remove nearly all impurities from sidered, the water first should be tested to determine what water. Compounds removed include sodium, hardness substances are present. Public water systems routinely test compounds such as calcium and magnesium, other dis- for contaminants. Water utilities are required to publish solved solids (including iron and manganese), fluoride, Consumer Confidence Reports (CCRs), which inform con- and nitrate. Operated properly, it effectively inactivates sumers on the source of the water, contaminants present, microorganisms such as bacteria, viruses, and protozoan potential health effects of those contaminants, and methods cysts (though protozoan cysts are not likely to be found in of treatment used by the utility. -
It's Just a Phase!
Bay Area Scientists in School Presentation Plan Lesson Name It’s just a phase!______________ Presenter(s) Kevin Metcalf, David Ojala, Melanie Drake, Carly Anderson, Hilda Buss, Lin Louie, Chris Jakobson California Standards Connection(s): 3rd Grade – Physical Science 3-PS-Matter has three states which can change when energy is added or removed. Next Generation Science Standards: 2nd Grade – Physical Science 2-PS1-1. Plan and conduct an investigation to describe and classify different kinds of materials by their observable properties. 2-PS1-4. Construct an argument with evidence that some changes caused by heating or cooling can be reversed and some cannot. Science & Engineering Practices Disciplinary Core Ideas Crosscutting Concepts Planning and carrying out PS1.A: Structure and Properties Patterns investigations to answer of Matter ・Patterns in the natural and questions or test solutions to ・Different kinds of matter exist human designed world can be problems in K–2 builds on prior and many of them can be observed. (2-PS1-1) experiences and progresses to either solid or liquid, simple investigations, based on depending on temperature. Cause and Effect fair tests, which provide data to Matter can be described and ・Events have causes that support explanations or design classified by its observable generate observable patterns. solutions. properties. (2-PS1-1) (2-PS1-4) ・Plan and conduct an ・Different properties are suited ・Simple tests can be designed to investigation collaboratively to to different purposes. (2-PS1- gather evidence to support or produce data to serve as the 2), (2-PS1-3) refute student ideas about basis for evidence to answer a ・A great variety of objects can causes. -
Chem Tech Pro 2F/20, Jaljyoti Appartment, New Sama Road, Chhani Jakat Naka, Vadodara-390002 Website: Email: [email protected]
Suppliers of all types of Equipments, Instruments and Chemicals Hub for all types Equipments, Instruments and Chemicals for various industries Registered Marketing Office: Chem Tech Pro 2F/20, Jaljyoti Appartment, New Sama Road, Chhani Jakat Naka, Vadodara-390002 Website: www.chemtechpro.in Email: [email protected] 1 About Chem Tech Pro Chem Tech Pro is global leading suppliers of various scientific equipments, chemical equipments, educational equipments, pilot plants for chemicals and pharmaceuticals products, analytical instruments, automation systems, labo- ratory chemicals, industrial chemicals and varieties of technical services pro- vider. Chem Tech Pro’s Products and Services 1. Absorption Columns 2. Adsorption Columns 3. Agitators 4. Analytical Equipments 5. Boilers and Steam Generators 6. Catalysts 7. Centrifuges 8. Chemicals 9. Cooling Towers 10. Crystallizers 11. Decanters 12. Distillation Columns 13. Dryers 14. Educational Equipments for Engineering Colleges 15. Environmental Equipments 16. Evaporators 17. Extraction Units 18. Fans, Blowers and Compressors 19. Fermenters and Bioreactors 20. Furnaces 21. Glass Equipments 22. Heat Exchangers 23. Humidifiers 24. Ion Exchange Equipments 25. Liquid Handling Equipments 26. Material Handling Equipments 27. Mechanical Seals and Stuffing Boxes 28. Membrane and Filtration Equipments 29. Mixing and Blending Units 30. Packing for columns 31. Personal Protective Equipments 32. Pilot Plants Specialists 33. Polymers 34. Pressure Vessels 35. Process Controllers and Instruments 36. Pumps 37. Reactors 38. Re-boilers 39. Safety and Fire fighting Equipments 40. Sewage Treatment Plants 41. Sight Glass and Flow Indicators 42. Solar Equipments 43. Sonicators and Homogenizers 44. Storage Tanks 45. Surface Treatment Equipments 46. Technical Services for various industries 47. Thickeners and Clarifiers 48. -
Distillation1
Distillation1 Distillation is a commonly used method for purifying liquids and separating mixtures of liquids into their individual components. Familiar examples include the distillation of crude fermentation broths into alcoholic spirits such as gin and vodka, and the fractionation of crude oil into useful products such as gasoline and heating oil. In the organic lab, distillation is used for purifying solvents and liquid reaction products. In analyzing a distillation, how do we know the real composition of each collected component? In this lab, we will introduce gas chromatography (GC), which will tell us how pure each fraction we collected is. After the distillation of your unknown is complete, you will analyze both components via GC. See page 11 and 12 for a light discussion on GC. To understand distillation, first consider what happens upon heating a liquid. At any temperature, some molecules of a liquid possess enough kinetic energy to escape into the vapor phase (evaporation) and some of the molecules in the vapor phase return to the liquid (condensation). An equilibrium is set up, with molecules going back and forth between liquid and vapor. At higher temperatures, more molecules possess enough kinetic energy to escape, which results in a greater number of molecules being present in the vapor phase. If the liquid is placed into a closed container with a pressure gauge attached, one can obtain a quantitative measure of the degree of vaporization. This pressure is defined as the vapor pressure of the compound, which can be measured at different temperatures. Consider heating cyclohexane, a liquid hydrocarbon, and measuring its vapor pressure at different temperatures. -
Simulation of the Open Sky Seawater Distillation
Green and Sustainable Chemistry, 2013, 3, 68-88 http://dx.doi.org/10.4236/gsc.2013.32012 Published Online May 2013 (http://www.scirp.org/journal/gsc) The Best Available Technology of Water/Wastewater Treatment and Seawater Desalination: Simulation of the Open Sky Seawater Distillation Djamel Ghernaout Chemical Engineering Department, Saad Dahlab University of Blida, Blida, Algeria Email: [email protected] Received March 16, 2013; revised April 18, 2013; accepted April 26, 2013 Copyright © 2013 Djamel Ghernaout. This is an open access article distributed under the Creative Commons Attribution License, which permits unrestricted use, distribution, and reproduction in any medium, provided the original work is properly cited. ABSTRACT This review suggests the concept of the best available technology of water/wastewater treatment and seawater desalina- tion which is in fact a simulation of the seawater distillation at the open sky: coagulation in salty water aerated basin/ coagulation using seawater as coagulant solution with distillation using stored solar energy followed by waterfall on a natural mountain. This natural, green, and technico-economical technology is composed of three steps: the first one is coagulation which may be achieved: 1) in salty water aerated basin (air stripping, AS; dissolved air flotation, DAF) where the raw water is “diluted” in seawater; or 2) in “conventional” coagulation using seawater as coagulant solution instead of alum/ferric salts. The first option seems to be more natural as it simulates river water dilution in seawater and the second one is more practical for “rapid” water consummation. For colloids and microorganisms’ removal, double- layer compression and charge neutralisation, as main coagulation and disinfection mechanisms, would be involved in the first and second options, respectively.