2011 Human Powered Vehicle: Mjölnir
Total Page:16
File Type:pdf, Size:1020Kb
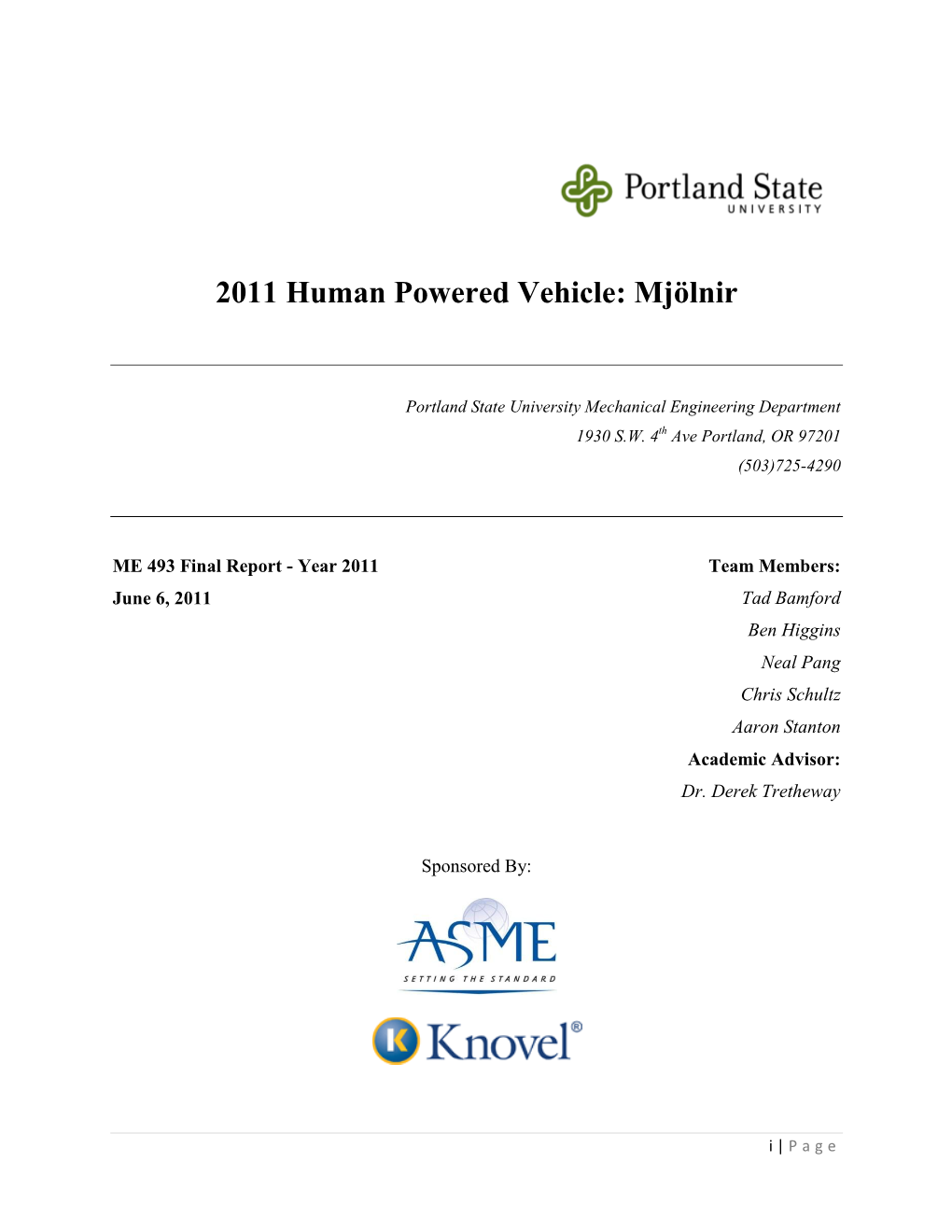
Load more
Recommended publications
-
Sp057 Leaf Spring Installation
SP057 LEAF SPRING INSTALLATION Also covering Part #RH015 1967-1969 CAMARO AND FIREBIRD NOTE: This part number is designed to use the original mounting hardware from a factory multi-leaf rear end setup. If you have a factory mono-leaf rear end or wish to upgrade the hardware for your multi-leaf setup, you can purchase the BMR leaf spring installation kit (Part #RH015). This kit includes new front mounting hardware, polyurethane leaf spring pads, larger U-bolts, and a heavy duty rear shackle kit with polyurethane frame bushings. INSTALLATION: 1. Lift vehicle and support with jack stands under the frame rails. 2. Remove the lower shock bolts. 3. Loosen the (4) nuts on the shock mounting plates then remove the plates. 4. Place a hydraulic jack under the axle. Lift the axle off the springs. 5. Loosen the nut on the rear lower shackle plates but do not remove the bolt. 6. Loosen the (3) bolts on the front leaf spring pocket and also remove the rear leaf spring bolt then remove the leaf spring from the vehicle. 7. If the vehicle was originally equipped with mono-leaf springs, knock out the factory bolts from the leaf spring axle mount (4 per side). Using a ½” drill bit, drill out the 4 holes in the leaf spring axle mounts. Also drill out the holes in the shock mounts to allow the use of ½” U-bolts. (IMAGE 1) 8. If you also purchased the leaf spring installation kit (RH015), replace the nut clips in the frame at this time. 9. If you purchased the leaf spring installation kit, knock out the upper bushings in the frame and install the supplied polyurethane bushings and inner steel sleeves. -
What You Need to Know About Mounting Radial Tires on Classic Vehicle Rims
What You Need to Know About Mounting Radial Tires on Classic Vehicle Rims Over the past 100 years, tires, and the wheels that support them, have gone through significant changes as a result of technical innovations in design, technology and materials. No single factor affects the handling and safety of a car’s ride more than the tire and the wheel it is mounted on and how the two work together as a unit. One nagging question that has been the subject of a lot of anecdotal evidence, speculation, and even more widespread rumor is whether rims designed for Bias ply tires can handle the stresses placed on them by Radial ply tires. And the answer is - it depends. It depends on how the rim was originally designed and built as well as whether the rim has few enough cycles on it, and how it has been driven. But most importantly it depends upon the construction of the tire and how it transmits the vehicle's load to where the rubber meets the road. In this paper, we want to educate you on the facts - not the wives tales or just plain bad information - about how Bias and Radial tires differ in working with the rim to provide a safe ride. Why is there a possible rim concern between Radial and Bias Tires? The fitting of radial tires, to wheels and rims originally designed for bias tires, is an application that may result in rim durability issues. Even same-sized bias and radial tires stress a rim differently, despite their nearly identical dimensions. -
Adaption and Evaluation of Transversal Leaf Spring Suspension Design for a Lightweight Vehicle Using Adams /C Ar
ADAPTION AND EVALUATION OF TRANSVERSAL LEAF SPRING SUSPENSION DESIGN FOR A LIGHTWEIGHT VEHICLE USING ADAMS /C AR FLORIAN CHRIST Master Thesis in Vehicle Engineering Vehicle Dynamics Aeronautical and Vehicle Engineering Royal Institute of Technology TRITA-AVE 2015:09 ISSN 1651-7660 Adaption and Evaluation of Transversal Leaf Spring Suspension Design for a Lightweight Vehicle using Adams/Car FLORIAN CHRIST © Florian Christ, 2015. Vehicle Dynamics Department of Aeronautical and Vehicle Engineering Kungliga Tekniska Högskolan SE-100 44 Stockholm Sweden ii Abstract This investigation deals with the suspension of a lightweight medium-class vehicle for four passengers with a curb weight of 1000 kg. The suspension layout consists of a transversal leaf spring and is supported by an active air spring which is included in the damper. The lower control arms are replaced by the leaf spring ends. Active ride height control is introduced to compensate for different vehicle load states. Active steering is applied using electric linear actuators with steer-by wire design. Besides intense use of light material the inquiry should investigate whether elimination of suspension parts or a lighter component is concordant with the stability demands of the vehicle. The investigation is based on simulations obtained with MSC Software ADAMS/Car and Matlab. The suspension is modeled in Adams/Car and has to proof it's compliance in normal driving conditions and under extreme forces. Evaluation criteria are suspension kinematics and compliance such as camber, caster and toe change during wheel travel in different load states. Also the leaf spring deflection, anti-dive and anti-squat measures and brake force distribution are investigated. -
Mini-Tub Leaf-Spring Rear Suspension for 1964-70 Mustangs
CLICK for More Info Online Mini-Tub Leaf-Spring Rear Suspension for 1964-70 Mustangs • Additional 2-3/4” tire clearance • Stronger offset frame rail inserts • Adjustable suspension geometry • Choose spring rate and ride height Mini-Tub Leaf-Spring Rear Suspension The mini-tub leaf-spring suspension from Total Control Products Applications allows substantially greater clearance for extremely large tire and wheel Mustang 64-70 combinations. Relocated shocks and springs combined with the additional mini-tub clearance allow 2-3/4” more tire clearance on each side of the vehicle. Systems include all mounts, offset frame rail inserts, leaf springs, spring plates and shock absorbers. A panhard bar version of the suspension is also offered for sharper and more predictable handling. Optional components include a narrow- width, adjustable-rate anti-roll bar and fabricated Ford 9” housing (FAB9™). Currently available for all styles of 1964-70 Mustangs. NOTE: ‘65-66 GT rear valance is not compatible with suspension. 1 Rear Spring Mounts Offset Frame Rail Insert Front Spring Mounts Relocated mount with 2-3/4” additional tire Welds inboard of OEM supporting crossmember clearance per side frame rail Panhard Bar System Upper Shock Mounts Lateral locating device Relocates stem-mount for rear end housing style shock inboard of OEM position Anti-Roll Bar FAB9 Rear End Houisng Splined arms with Fabricated Ford 9” adjustable end-link housing, structurally positions to alter rate superior to OEM 2 Mini-Tub Leaf-Spring Suspension Shown with optional Anti-Roll -
The Effect of Rollover Protection Systems and Trailers on Quad Bike Stability
International Journal of Forest Engineering ISSN: (Print) (Online) Journal homepage: https://www.tandfonline.com/loi/tife20 The effect of rollover protection systems and trailers on quad bike stability Björn Edlund , Ola Lindroos & Tomas Nordfjell To cite this article: Björn Edlund , Ola Lindroos & Tomas Nordfjell (2020) The effect of rollover protection systems and trailers on quad bike stability, International Journal of Forest Engineering, 31:2, 95-105, DOI: 10.1080/14942119.2020.1708067 To link to this article: https://doi.org/10.1080/14942119.2020.1708067 © 2020 The Author(s). Published by Informa UK Limited, trading as Taylor & Francis Group. Published online: 06 Jan 2020. Submit your article to this journal Article views: 369 View related articles View Crossmark data Full Terms & Conditions of access and use can be found at https://www.tandfonline.com/action/journalInformation?journalCode=tife20 INTERNATIONAL JOURNAL OF FOREST ENGINEERING 2020, VOL. 31, NO. 2, 95–105 https://doi.org/10.1080/14942119.2020.1708067 The effect of rollover protection systems and trailers on quad bike stability Björn Edlund , Ola Lindroos and Tomas Nordfjell Department of Forest Biomaterials and Technology, Swedish University of Agricultural, Sciences, Umeå, Sweden ABSTRACT ARTICLE HISTORY Quad bikes are light-weight vehicles which are used for transportation of personnel, equipment, and Received 26 June 2019 material in forestry operations such as planning, logging, planting, and fire-fighting. With increased Accepted 17 December 2019 quad bike usage, serious injuries have become an increasing concern. The most common forms of KEYWORDS severe incidents occur when a quad bike loses stability, causing injuries as it rolls over the rider trapped ATV; All-terrain vehicle; beneath. -
Design \&Amp\; Weight Optimization of a Wheel Rim for Sport Utility Vehicle
MATEC Web of Conferences 172, 03006 (2018) https://doi.org/10.1051/matecconf/201817203006 ICDAMS 2018 Design & Weight Optimization of a Wheel Rim for Sport Utility Vehicle. Harish Panjagala1, *, Balakrishna M2, Shasikant Kushnoore1 and E L N Rohit Madhukar3 1Faculty of Mechanical Engineering, Koneru Lakshmaiah Educational Foundation, Vaddeswaram, Guntur, Andhra Pradesh, India – 522502. 2Faculty of Mechanical Engineering, G.I.E.T, Rajahmundry, Andhra Pradesh, India. 3Department of Mechanical Engineering, Koneru Lakshmaiah Educational Foundation, Vaddeswaram, Guntur, Andhra Pradesh, India – 522502. ABSTRACT. Automobile have various parts which are important for good running of the vehicle. The most important safety components from a structural point of view are the road wheels. They are required to be lighter and more fascinating to the buyer all the time. This implies that it's important to perform a lot of accurate strength assessment on wheel styles. The wheel rim plays a major role in vehicle dynamics. This paper deals with the design and model of different wheel rims based on weight optimization and also structural analysis has been carried out. It has been compared with standard values by varying two different materials. In addition, from the obtained outputs of simulations and the weight optimization, we suggested Aluminium alloys as most suitable material for SUV. Model is created by using SOLIDWORKS software 2015 and structural analysis & weight optimization is done by using ANSYS WORKBENCH 16.0. 1 INTRODUCTION by considered two different materials namely Aluminum and forged steel and their relative performances have A sport or suburban utility vehicle (SUV) is similar to a been observed respectively. -
A Comparative Study of the Suspension for an Off-Road Vehicle
International Research Journal of Engineering and Technology (IRJET) e-ISSN: 2395-0056 Volume: 07 Issue: 05 | May 2020 www.irjet.net p-ISSN: 2395-0072 A Comparative study of the Suspension for an Off-Road Vehicle Sivadanus.S Department of Manufacturing Engineering, College of Engineering – Guindy, Chennai ---------------------------------------------------------------------***--------------------------------------------------------------------- Abstract - Humans use different vehicles to travel in is set nothing can be adjusted or moved. This type of different terrains for comfort and ease of travel. An off-terrain suspension will not be considered in the scope of this project vehicle is generally used for rugged terrain and needs a largely due to its lack of adjustability. completely different dynamics in suspension comparison to an on-road vehicle. The aim of this project is to identify and Independent suspension systems provide more effective determine the parameters of vehicle dynamics with a proper functionality in traction and stability for off-roading study of suspension and to initiate a comparative study for an applications. Independent suspension systems provide flex off-road vehicle using different models. (the ability for one wheel to move vertically while still Key Words: Suspension, Vehicle Dynamics, Off-road allowing the other wheels to stay in contact with the Vehicle, Control arms, Camber surface). 1.INTRODUCTION There are many different versions and variations of independent suspensions, which include swing axle Suspension suspensions, transverse leaf spring suspensions, trailing and The role of a suspension system within a vehicle is to ensure semi-trailing suspensions, Macpherson strut suspensions, that contact between the tires and driving surface is and double wishbone suspensions. Control arms are used for continuously maintained. -
Specifiers & Installers Guide to TORSION BAR APPLICATIONS
Specifiers & Installers Guide To TORSION BAR APPLICATIONS WELCOME Thank you for specifying Sauber Torsion Bars. By choosing us as your stability partner, you derive the following benefits: * Improved Stability * Stability is safety, and safety is our first concern. A Sauber Torsion Bar can eliminate unwanted counterweight, offering your users an extra safety margin. Because Sauber bars don't rigidize the chassis frame, they always provide a smooth, quiet ride. * Long Life * Premium bronze and galvanized components. Bushings guaranteed and replaced as/if needed for 10 years. 10 Year parts coverage when inspected at no greater than four month intervals. * Excellent Documentation * Our comprehensive applications charts, installation instructions and detailed drawings provide the vital information you and your installers need in an organized format. * Superior Support * Toll-free phone and fax service from anywhere in North America provides easy access to the resources of our organization through your personal company representative. * Lower Life Cycle Costs * Since it takes less time to mount our bar, its installed cost can actually be less than other alternatives. Sauber Torsion Bars are designed and built to last as long as your chassis. * Extensive Inventory * Our inventory power puts our bar on the floor just when you want it. Your production schedule can't wait on your suppliers, and with us as your partner, it won't. * More Choices * Underframe or overframe, nobody provides more installation options than we do. More choices mean a better -
Modelling Commercial Vehicle Handling and Rolling Stability
357 CORE Metadata, citation and similar papers at core.ac.uk Provided by Bradford Scholars Modelling commercial vehicle handling and rolling stability K HussainÃ, W Stein, and A J Day School of Engineering, Design, and Technology, University of Bradford, Bradford, UK The manuscript was received on 3 September 2004 and was accepted after revision for publication on 28 April 2005. DOI: 10.1243/146441905X48707 Abstract: This paper presents a multi-degrees-of-freedom non-linear multibody dynamic model of a three-axle heavy commercial vehicle tractor unit, comprising a subchassis, front and rear leaf spring suspensions, steering system, and ten wheels/tyres, with a semi-trailer comprising two axles and eight wheels/tyres. The investigation is mainly concerned with the rollover stability of the articulated vehicle. The models incorporate all sources of compliance, stiffness, and damping, all with non-linear characteristics, and are constructed and simulated using automatic dynamic analysis of mechanical systems formulation. A constant radius turn test and a single lane change test (according to the ISO Standard) are simulated. The constant radius turn test shows the understeer behaviour of the vehicle, and the single lane change manoeuvre was conducted to show the transient behaviour of the vehicle. Non-stable roll and yaw behaviour of the vehicle is predicted at test speeds .90 km/h. Rollover stability of the vehicle is also investigated using a constant radius turn test with increasing speed. The articulated laden vehicle model predicted increased understeer behaviour, due to higher load acting on the wheels of the middle and rear axles of the tractor and the influence of the semi-trailer, as shown by the reduced yaw rate and the steering angle variation during the con- stant radius turn. -
Roadmaster, Experts in Dinghy Towing, Introduces the Comfort Ride Slipper Leaf Spring and Shock Absorber Systems to Road-Weary Trailer and Fifth-Wheel Owners
article and photos by Bob Livingston SUSPENSION NIRVANA Roadmaster, experts in dinghy towing, introduces the Comfort Ride Slipper Leaf Spring and Shock Absorber systems to road-weary trailer and fifth-wheel owners railers and fifth-wheels take a lot of punishment a company immersed in the tow-bar business, catering on the road. Suspensions, designed to counter this to owners towing vehicles behind their motorhomes, has Tabuse, have not changed much over the years, and expanded its offerings in the towable arena with the intro- in most cases are the same ones found on chassis that date duction of the Comfort Ride Slipper Leaf Spring Suspension back a very long time. (The old line “This isn’t your grand- and Shock Absorber systems. father’s vehicle” does not apply.) While stock suspensions The concept is simple, and the result is a game changer hold the chassis off the ground, controlling the ride is not in the way trailers and fifth-wheels handle all road conditions. a strong attribute. One might ask, “Why worry about ride quality inside Leaf springs tied to shackles and a center-mounted a trailer when towing since no one is back there to feel equalizer are supposed to counter the bumps in the road the shakes, rattles and rolls? That’s a valid question, but but, with few exceptions, are not very effective. Roadmaster, subjecting a trailer to a constant 4.0-magnitude earthquake 74 TRAILER LIFE July 2018 Roadmaster’s Comfort Ride Slipper Leaf Spring and Shock Absorber systems bolt on to the frame with only minor drilling needed to mount the center box. -
Ride Control Defined
RIDE CONTROL DEFINED According to Newton's First Law, a moving body will continue moving in a straight line until it is acted upon by another force. Newton's Second Law states that for each action there is an equal and opposite reaction. In the case of the automobile, whether the disturbing force is in the form of a wind-gust, an incline in the roadway, or the cornering forces produced by tires, the force causing the action and the force resisting the action will always be in balance. Many things affect vehicles in motion. Weight distribution, speed, road conditions and wind are some factors that affect how vehicles travel down the highway. Under all these variables however, the vehicle suspension system including the shocks, struts and springs must be in good condition. Worn suspension components may reduce the stability of the vehicle and reduce driver control. They may also accelerate wear on other suspension components. Replacing worn or inadequate shocks and struts will help maintain good ride control as they: Control spring and suspension movement Provide consistent handling and braking Prevent premature tire wear Help keep the tires in contact with the road Maintain dynamic wheel alignment Control vehicle bounce, roll, sway, dive and acceleration squat Reduce wear on other vehicle systems Promote even and balanced tire and brake wear Reduce driver fatigue Suspension concepts and components have changed and will continue to change dramatically, but the basic objective remains the same: 1. Provide steering stability with good handling characteristics 2. Maximize passenger comfort Achieving these objectives under all variables of a vehicle in motion is called ride control 1 BASIC TERMINOLOGY To begin this training program, you need to possess some very basic information. -
Part 72. Automotive Service Operations
MIOSHA-STD-1149 (05/13) For further information 8 Pages Ph: 517-284-7740 www.michigan.gov/mioshastandards DEPARTMENT OF LICENSING OF REGULATORY AFFAIRS DIRECTOR'S OFFICE GENERAL INDUSTRY SAFETY STANDARDS Filed with the Secretary of State on December 12, 1974 (as amended September 30, 1977) (as amended May 31, 1990) (as amended August 2, 1993) (as amended May 29, 2013) These rules become effective immediately upon filing with the Secretary of State unless adopted under section 33, 44, or 45a(6) of 1969 PA 306. Rules adopted under these sections become effective 7 days after filing with the Secretary of State. (By authority conferred on the director of the department of licensing and regulatory affairs by sections 16 and 21 of 1974 PA 154, and Executive Reorganization Order Nos. 1996-2, 2003-1, 2008-4, and 2011-4, MCL 445.2001, 445.2011, 445.2025, and 445.2030) R 408.17211, R 408.17212, R 408.17213, R 408.17222, R 408.17225, R 408.17236, and R 408.17251 of the Michigan Administrative Code are amended and R 408.17227 of the Code is rescinded as follows: GENERAL INDUSTRY SAFETY AND HEALTH STANDARD PART 72. AUTOMOTIVE SERVICE OPERATIONS Table of Contents SPECIFICS ................................................................... 4 GENERAL PROVISIONS ............................................ 1 R 408.17232. Cranes and winches, hoists R 408.17201. Scope. ................................................... 1 and chain falls. ....................................................... 4 R 408.17204. Definitions; A to E. ................................. 1 R 408.17233. Wreckers. ............................................... 4 R 408.17205. Definitions; F to L. ................................. 2 R 408.17234. Jacking and blocking. ............................ 4 R 408.17206. Definitions; P to S. ................................. 2 R 408.17235.