1 Fast Liquid Metal Program for Fusion Reactor Divertor E
Total Page:16
File Type:pdf, Size:1020Kb
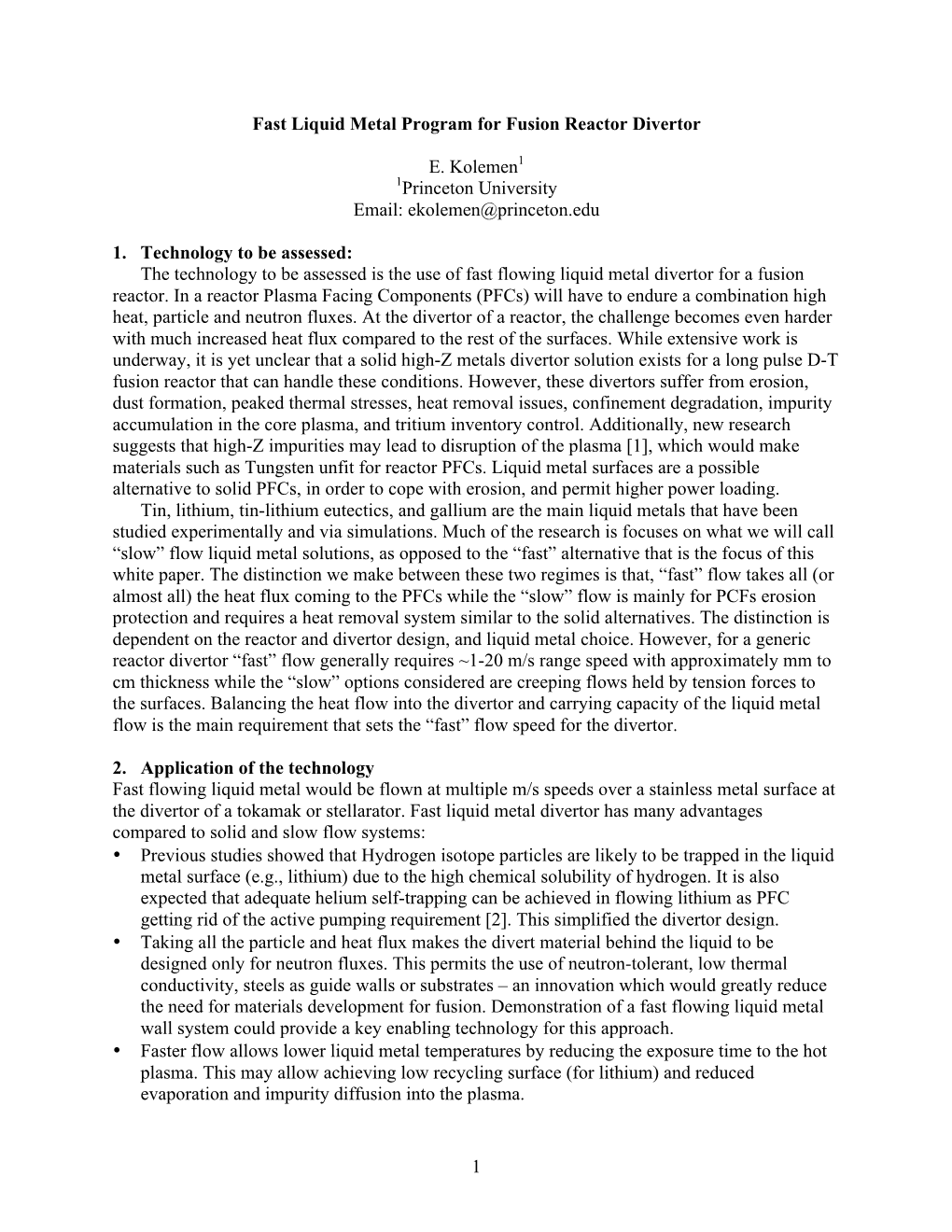
Load more
Recommended publications
-
Liquid Metal Cooled Reactors: Experience in Design and Operation
IAEA-TECDOC-1569 Liquid Metal Cooled Reactors: Experience in Design and Operation December 2007 IAEA-TECDOC-1569 Liquid Metal Cooled Reactors: Experience in Design and Operation December 2007 The originating Sections of this publication in the IAEA were: INIS and Nuclear Knowledge Management and Nuclear Power Technology Development Sections International Atomic Energy Agency Wagramer Strasse 5 P.O. Box 100 A-1400 Vienna, Austria LIQUID METAL COOLED REACTORS: EXPERIENCE IN DESIGN AND OPERATION IAEA, VIENNA, 2007 IAEA-TECDOC-1569 ISBN 978–92–0–107907–7 ISSN 1011–4289 © IAEA, 2007 Printed by the IAEA in Austria December 2007 FOREWORD In 2002, within the framework of the Department of Nuclear Energy’s Technical Working Group on Fast Reactors (TWG-FR), and according to the expressed needs of the TWG-FR Member States to maintain and increase the present knowledge and expertise in fast reactor science and technology, the IAEA established its initiative seeking to establish a comprehensive, international inventory of fast reactor data and knowledge. More generally, at the IAEA meeting of senior officials convened to address issues of nuclear knowledge management underlying the safe and economic use of nuclear science and technology (Vienna, 17–19 June 2002), there was widespread agreement that, for sustainability reasons for fissile sources and waste management, long-term development of nuclear power as a part of the world’s future energy mix will require the fast reactor technology. Furthermore, given the decline in fast reactor development projects, data retrieval and knowledge preservation efforts in this area are of particular importance. This consensus concluded from the recognition of immediate need gave support to the IAEA initiative for fast reactor data and knowledge presevation. -
Plasma-Materials and Divertor Options for Fusion
Plasma-Materials and Divertor Options for Fusion Presented to: National Academy of Sciences Panel A Strategic Plan for U.S. Burning Plasma Research J. Rapp ORNL is managed by UT-Battelle for the US Department of Energy Lifetime of divertor will deterimine fusion reactor availability TF coils Coolant manifold (permanent) Upper ports (modules and coolant) Blanket Cost of modules electricity is 5-6 yrs lifetime proportional 0.6 to (1/A) Central ports (modules) Vacuum vessel 70cm Cool shield (permanent) 30cm Divertor plates (permanent) Lower ports 2 yrs lifetime goal (divertor) Main driver of scheduled maintenance: divertor (and blanket) 2 Juergen Rapp Outline • Plasma-Material Interaction (PMI) challenges • Potential Plasma-Facing Materials (PFMs) and Components (PFCs) • Current status of U.S. PMI research • Facilities needed for the development of PFCs • Strategic elements to accelerate U.S. burning plasma research • A proposed high-level R&D program and roadmap for PMI 3 Juergen Rapp Outline • Plasma-Material Interaction (PMI) challenges • Potential Plasma-Facing Materials (PFMs) and Components (PFCs) • Current status of U.S. PMI research • Facilities needed for the development of PFCs • Strategic elements to accelerate U.S. burning plasma research • A proposed high-level R&D program and roadmap for PMI 4 Juergen Rapp Challenges for materials: fluxes and fluence, temperatures JET ITER FNSF Fusion Reactor 50 x divertor ion fluxes 5000 x divertor ion fluence up to 5 x ion fluence 106 x neutron fluence (1dpa) up to 100 x neutron fluence (150dpa) -
A European Success Story the Joint European Torus
EFDA JET JETJETJET LEAD ING DEVICE FOR FUSION STUDIES HOLDER OF THE WORLD RECORD OF FUSION POWER PRODUCTION EXPERIMENTS STRONGLY FOCUSSED ON THE PREPARATION FOR ITER EXPERIMENTAL DEVICE USED UNDER THE EUROPEAN FUSION DEVELOPEMENT AGREEMENT THE JOINT EUROPEAN TORUS A EUROPEAN SUCCESS STORY EFDA Fusion: the Energy of the Sun If the temperature of a gas is raised above 10,000 °C virtually all of the atoms become ionised and electrons separate from their nuclei. The result is a complete mix of electrons and ions with the sum of all charges being very close to zero as only small charge imbalance is allowed. Thus, the ionised gas remains almost neutral throughout. This constitutes a fourth state of matter called plasma, with a wide range of unique features. D Deuterium 3He Helium 3 The sun, and similar stars, are sphe- Fusion D T Tritium res of plasma composed mainly of Li Lithium hydrogen. The high temperature, 4He Helium 4 3He Energy U Uranium around 15 million °C, is necessary released for the pressure of the plasma to in Fusion T balance the inward gravitational for- ces. Under these conditions it is pos- Li Fission sible for hydrogen nuclei to fuse together and release energy. Nuclear binding energy In a terrestrial system the aim is to 4He U produce the ‘easiest’ fusion reaction Energy released using deuterium and tritium. Even in fission then the rate of fusion reactions becomes large enough only at high JG97.362/4c Atomic mass particle energy. Therefore, when the Dn required nuclear reactions result from the thermal motions of the nuclei, so-called thermonuclear fusion, it is necessary to achieve u • extremely high temperatures, of at least 100 million °C. -
(12) Patent Application Publication (10) Pub. No.: US 2006/0090474 A1 Sauciuc Et Al
US 20060090474A1 (19) United States (12) Patent Application Publication (10) Pub. No.: US 2006/0090474 A1 Sauciuc et al. (43) Pub. Date: May 4, 2006 (54) METHOD AND APPARATUS FOR Publication Classification REMOVING HEAT (51) Int. Cl. F2SB 2L/02 (2006.01) (76) Inventors: Ioan Sauciuc, Phoeniz, AZ (US); Jim F28D 5/00 (2006.01) D. Williams, Banks, OR (US) F25D 23/12 (2006.01) (52) U.S. Cl. ....................... 62/3.2: 62/259.2; 165/104.22 Correspondence Address: BLAKELY SOKOLOFFTAYLOR & ZAFMAN (57) ABSTRACT 124OO WILSHIRE BOULEVARD SEVENTH FLOOR A device includes a liquid metal and a ferrofluid contained LOS ANGELES, CA 90025-1030 (US) in a closed tube. Many electrode groups are connected to the closed tube. A feedback device is connected to the electrode (21) Appl. No.: 10/976,406 groups. The feedback device switches power to each elec trode group in series to circulate the liquid metal and move (22) Filed: Oct. 29, 2004 the ferrofluid in the closed tube. 200 210 -4220 Automatic feedback system and StartUp Circuit (2) (25 260 250 Patent Application Publication May 4, 2006 Sheet 1 of 7 US 2006/0090474 A1 20 FIG. 1A F.G. 1B (Prior Art) (Pr O Art) Patent Application Publication May 4, 2006 Sheet 2 of 7 US 2006/0090474 A1 200 - Automatic feedback system and StartUp Circuit 25 (25 240 E.iSE S3 ES 230 250 FIG. 2 Patent Application Publication May 4, 2006 Sheet 3 of 7 US 2006/0090474 A1 FIG. 3 Patent Application Publication May 4, 2006 Sheet 4 of 7 US 2006/0090474 A1 400 Determine Temperature Alternate power to electrode groups to move ferrofluid 420 Circulate liquid metal Dissipate heat within the liquid metal FIG. -
Steady State and Transient Power Handling in JET G.F.Matthews* on Behalf of the JET EFDA Exhaust Physics Task Force and JET EFDA Contributors+ +See Annex of J
Steady State and Transient Power Handling in JET G.F.Matthews* on behalf of the JET EFDA Exhaust Physics Task Force and JET EFDA Contributors+ +See annex of J. Pamela et al, "Overview of JET Results", Fusion Energy 2002 (Proc. 19th Int. Conf. Lyon, 2002),IAEA, Vienna. *Euratom/UKAEA Fusion Association, Culham Science Centre, Abingdon, Oxon. OX14 3DB,UK. E-mail: [email protected] Abstract. Steady state and transient power deposition profiles have been measured in the JET MIIGB divertor using improved diagnostics techniques involving the use of fast infra-red, thermocouples and Langmuir probe arrays. In unfuelled type I ELMy H-modes a very narrow power profile is observed at the outer target which we associate with the ion channel. Systematic parameter scans have been carried out and our analysis shows that the average power width scaling is consistent with a classical dependence of perpendicular transport in the SOL. Using the fast IR capability the factors such as rise time, broadening, variability and in/out asymmetry have been studied and lead to the conclusion that type I ELMs in ITER may fall just below the material ablation limits. JET disruptions are very different from type I ELMs in that only a small fraction of the thermal energy reaches the divertor and what does arrive is distributed uniformly over the divertor area. This is very different from the current ITER assumption which puts most of the energy from the thermal quench onto the divertor strike points. 1. Introduction The actively cooled divertor target for ITER has been tested up to a surface power loading of 25MWm-2 but the planned operating point is around 10MWm-2 to allow for excursions. -
The Pumped Divertor the NEW PHASE of JET B.E
The Pumped Divertor THE NEW PHASE OF JET B.E. Keen and M.L. Watkins and the JET Team JET Joint Undertaking, Abingdon, Oxford, UK Associate Member of EPS The pumped divertor experiment, in demonstrating before full deuterium-tritium operation an effective method of impurity control, aims to provide essential design data for a Next Step tokamak fusion device. The basic principle of the fusion pro Switzerland and Sweden. By mid-1983, by careful design of the targets and speci cess is the fusing of light nuclei to form the construction of JET, its power supplies fic operational techniques, but is limited, heavier ones and the accompanying re and buildings were completed on sche ultimately, by an unacceptably high influx lease of substantial energy. For a fusion dule and broadly to budget and the prog of impurities. The fourth area of work had reactor, there are several possible fusion ramme started. been started by earlier studies of energetic reactions, but the one that is easiest to JET is the largest project in the coordi particles produced as fusion products or achieve is that between the deuterium and nated programme of EURATOM, whose by ion cyclotron resonance heating tritium isotopes of hydrogen. This D-T fusion programme is designed to lead ulti (ICRH). It has now been addressed further reaction is : mately to the construction of an energy by the first tokamak plasma experiments D + T → 4He + neutrons + 17.6 MeV. producing reactor. Its strategy is based on in D-T mixtures. These results are presen At the temperatures needed for this reac the sequential construction of major ap ted briefly in the following sections. -
Liquid-Based Reconfigurable Antenna Technology
sensors Review Liquid-Based Reconfigurable Antenna Technology: Recent Developments, Challenges and Future Habshah Abu Bakar 1, Rosemizi Abd Rahim 2,* , Ping Jack Soh 2,3 and Prayoot Akkaraekthalin 4,* 1 Department of Electrical Engineering, Politeknik Sultan Abdul Halim Muadzam Shah, Jitra 06000, Kedah, Malaysia; [email protected] 2 Faculty of Electronic Engineering Technology, Pauh Putra Campus, Universiti Malaysia Perlis, Pauh 02600, Perlis, Malaysia; [email protected] 3 Advanced Communication Engineering (ACE) Centre of Excellence, Universiti Malaysia Perlis, Kangar 01000, Perlis, Malaysia 4 Department of Electrical and Computer Engineering, Faculty of Engineering, King Mongkut’s University of Technology North Bangkok (KMUTNB), 1518 Pracharat 1 Rd., Wongsawang, Bangsue, Bangkok 10800, Thailand * Correspondence: [email protected] (R.A.R.); [email protected] (P.A.) Abstract: Advances in reconfigurable liquid-based reconfigurable antennas are enabling new pos- sibilities to fulfil the requirements of more advanced wireless communication systems. In this review, a comparative analysis of various state-of-the-art concepts and techniques for designing reconfigurable antennas using liquid is presented. First, the electrical properties of different liquids at room temperature commonly used in reconfigurable antennas are identified. This is followed by a discussion of various liquid actuation techniques in enabling high frequency reconfigurability. Next, the liquid-based reconfigurable antennas in literature used to achieve -
Lyra' Divertor
ENERGY AND PARTICLE CONTROL CHARACTERISTICS OF THE ASDEX UPGRADE `LYRA' DIVERTOR M. Kaufmann, H-S. Bosch, A. Herrmann, A. Kallenbach, K. Borrass, A. Carlson, D. Coster, J.C. Fuchs, J. Gafert, K. Lackner, J. Neuhauser, R. Schneider, J. Schweinzer, W. Suttrop, W. Ullrich, U. Wenzel, and ASDEX Upgrade team Max-Planck-Institut fÈurPlasmaphysik, EURATOM-IPP Association, Garching und Berlin, Germany Abstract In 1997 the new `LYRA' divertor went into operation at ASDEX Upgrade and the neutral beam heating power was increased to 20 MW by installation of a second injector. This leads to the relatively high value of P/R of 12 MW/m. It has been shown that the ASDEX Upgrade LYRA divertor is capable of handling such high heating powers. Mea- surements presented in this paper reveal a reduction of the maximum heat ¯ux in the LYRA divertor by more than a factor of two compared to the open Divertor I. This reduction is caused by radiative losses inside the divertor region. Carbon radiation cools the divertor plasma down to a few eV where hydrogen radiation losses become signi®cant. They are increased due to an effective re¯ection of neutrals into the hot separatrix region. B2-Eirene modelling of the performed experiments supports the experimental ®ndings and re®nes the understanding of loss processes in the divertor region. 1. INTRODUCTION The width of the scrape-off layer (SOL) does not necessarily increase in proportion to the size of the device. This poses severe problems for the power exhaust in a fusion reactor. If we take ITER as described in the ®nal design report (FDR) [1], a power ¯ow across the separatrix in the order of 100 to 150 MW might be needed to stay in the H-mode [2]. -
A Complete Interfacial System Solution for Liquid Metal Electronics
A Complete Interfacial System Solution for Liquid Metal Electronics A dissertation submitted to the Graduate School of the University of Cincinnati in partial fulfillment of the requirements for the degree of Doctor of Philosophy in the Department of Materials Science & Engineering of the College of Engineering & Applied Science by Sarah E. Holcomb B.S., Rensselaer Polytechnic Institute, 2013 Committee Chair: Jason C. Heikenfeld, Ph.D. Abstract Liquid metal electronic devices have numerous advantages over traditional solid devices such as the ability to be flexed and stretched or reconfigured. Examples of such devices are wires, switches, polarizers, and antennas. Previously, mercury has been used as the room temperature liquid metal of choice but has been recently replaced by gallium liquid metal alloys (GaLMAs) which are non-toxic, have extremely low vapor pressures, and can remain liquid at temperatures as low as -19°C. A key difference in the performance of GaLMAs vs. mercury is the mechanically stabilizing, passivating oxide which forms instantly on the surface of GaLMAs in as little as 1 ppm oxygen environments. This oxide presents a significant challenge for reconfigurable device applications because it “sticks” to most surfaces, preventing reversible shape change, which alters the desired electrical performance. Proposed here are two novel methods of overcoming this challenge. These methods enable new capabilities for reconfigurable electronic devices. The first approach involves removing the oxide in situ as it is continuously formed in all practically achievable device environments. Oxide removal is commonly done through the use of hydrochloric acid (aqueous or vapor), which reacts with the gallium oxide to produce gallium chloride, which is not mechanically stabilizing, and water. -
Study of Electrochemical Properties of Liquid Gallium
University of Wollongong Research Online University of Wollongong Thesis Collection 2017+ University of Wollongong Thesis Collections 2017 Study of electrochemical properties of liquid gallium Yuchen Chen University of Wollongong Follow this and additional works at: https://ro.uow.edu.au/theses1 University of Wollongong Copyright Warning You may print or download ONE copy of this document for the purpose of your own research or study. The University does not authorise you to copy, communicate or otherwise make available electronically to any other person any copyright material contained on this site. You are reminded of the following: This work is copyright. Apart from any use permitted under the Copyright Act 1968, no part of this work may be reproduced by any process, nor may any other exclusive right be exercised, without the permission of the author. Copyright owners are entitled to take legal action against persons who infringe their copyright. A reproduction of material that is protected by copyright may be a copyright infringement. A court may impose penalties and award damages in relation to offences and infringements relating to copyright material. Higher penalties may apply, and higher damages may be awarded, for offences and infringements involving the conversion of material into digital or electronic form. Unless otherwise indicated, the views expressed in this thesis are those of the author and do not necessarily represent the views of the University of Wollongong. Recommended Citation Chen, Yuchen, Study of electrochemical properties of liquid gallium, Master of Philosophy thesis, Institute for Superconducting and Electronic Materials, University of Wollongong, 2017. https://ro.uow.edu.au/ theses1/14 Research Online is the open access institutional repository for the University of Wollongong. -
Tuning Surface Texture of Liquid Metal Particles by Exploiting Material Metastability Joel Cutinho Iowa State University
Iowa State University Capstones, Theses and Graduate Theses and Dissertations Dissertations 2017 Tuning surface texture of liquid metal particles by exploiting material metastability Joel Cutinho Iowa State University Follow this and additional works at: https://lib.dr.iastate.edu/etd Part of the Materials Science and Engineering Commons, and the Mechanics of Materials Commons Recommended Citation Cutinho, Joel, "Tuning surface texture of liquid metal particles by exploiting material metastability" (2017). Graduate Theses and Dissertations. 16118. https://lib.dr.iastate.edu/etd/16118 This Thesis is brought to you for free and open access by the Iowa State University Capstones, Theses and Dissertations at Iowa State University Digital Repository. It has been accepted for inclusion in Graduate Theses and Dissertations by an authorized administrator of Iowa State University Digital Repository. For more information, please contact [email protected]. Tuning surface texture of liquid metal particles by exploiting material metastability by Joel Cutinho A thesis submitted to the graduate faculty in partial fulfillment of the requirements for the degree of MASTER OF SCIENCE Major: Materials Science and Engineering Program of Study Committee: Martin Thuo, Major Professor Shan Jiang Jaime Juarez The student author, whose presentation of the scholarship herein was approved by the program of study committee, is solely responsible for the content of this thesis. The Graduate College will ensure this thesis is globally accessible and will not permit alterations after a degree is conferred Iowa State University Ames, Iowa 2017 Copyright © Joel Cutinho, 2017. All rights reserved. ii DEDICATION I dedicate this work primarily to my family, who have taught me to believe in God, myself and follow my desires. -
Coupling Optimization Experiment on HL-2A Based on Passive-Active Multijunction Antenna for 3.7Ghz Lower Hybrid System
42nd EPS Conference on Plasma Physics P5.137 Coupling optimization experiment on HL-2A based on Passive-Active Multijunction antenna for 3.7GHz Lower Hybrid system Xingyu Bai, Hao Zeng, Bo Lu, Xiaolan Zou1, Roland Magne1, Annika Ekedahl1, Julien Hillairet1, Chao Wang, Jun Liang, He Wang, Yali Chen, Junwei He, Jieqiong Wang, Kun Feng and Jun Rao Southwestern Institute of Physics, Chengdu, China 1 CEA, IRFM, 13108 Saint Paul-lez-Durance, France System Introduction. A new Lower Hybrid Wave (LHW) system (3.7GHz/2MW/2s) has been built on HL-2A tokamak. A Passive-Active-Multijunction (PAM) concept antenna [1], [2] was designed and built, fed by 500kW × 4 TH2103A Klystrons, delivering ITER-relevant power density, i.e. 25MW/m2 at f = 3.7GHz [3],[4]. The antenna is designed to launch a peak parallel refractive index of N||=2.75 with a low theoretical Reflection Coefficient (RC), i.e. less than 1% [5], [6]. A specific gas puffing system for improving the antenna coupling and a set of Langmuir probes for antenna mouth density measurements are separately located on one side of the antenna each. An auxiliary vacuum system is installed at the rear of the antenna to improve the pumping efficiency. Vacuum leak tests and low power microwave scattering parameter measurements were done before the PAM antenna was installed on HL-2A, allowing the antenna to be conditioned at RF power of 100kW/100ms before starting plasma operation. Fig. 1: New LHW system(3.7GHz/2MW/2s)of HL- Fig. 2: PAM launcher was developed and installed, facing 2A.