Processing of Fiber Flax in Oregon
Total Page:16
File Type:pdf, Size:1020Kb
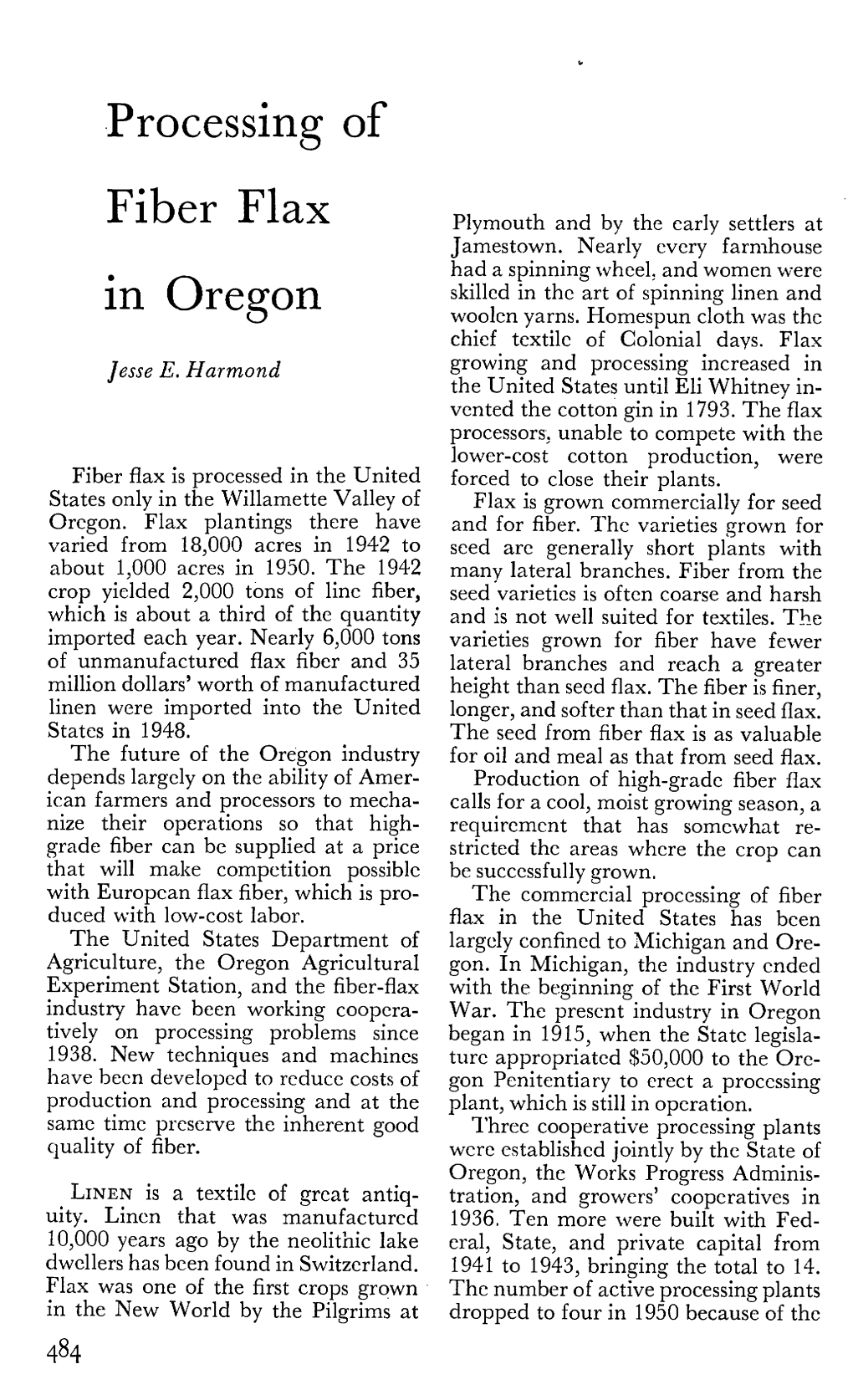
Load more
Recommended publications
-
Mechanical Properties of Unidirectional Epoxy Matrix Composites Reinforced with Scutched Flax and Tow By-Product
ECCM16 - 16TH EUROPEAN CONFERENCE ON COMPOSITE MATERIALS, Seville, Spain, 22-26 June 2014 MECHANICAL PROPERTIES OF UNIDIRECTIONAL EPOXY MATRIX COMPOSITES REINFORCED WITH SCUTCHED FLAX AND TOW BY-PRODUCT N. Martina*,c, P. Daviesb, C. Baleya aLIMATB, EA 4250, Univ. Bretagne-Sud, 56100 Lorient, France bMarine Structures Laboratory, IFREMER, 29280 Plouzané, France cVan Robaeys Frères, 83 rue Saint-Michel, 59122 Killem, France *[email protected] Keywords: Flax fibers, Scutching, Flax by-products, Composite materials Abstract The decortication of flax by scutching yields scutched flax and tows. In this study, we have compared the properties of composite materials made of scutched flax and flax tows from the same batch. A series of unidirectional epoxy composites were manufactured by wet moulding. Mechanical properties of single fibers and composite materials were measured by tensile tests. The tensile properties of single fibers were in the same range. The tensile properties of the unidirectional composites show a similar evolution of properties versus fiber volume fraction. The results show that tows could be used to reinforce high performance composite materials. 1. Introduction A wide range of plant fibers have been studied for composite reinforcement including hemp, jute, sisal and flax [1]. Among them, flax fibers have excellent specific mechanical properties and are being evaluated as a replacement for E-glass fibers [2,3]. Flax (Linum usitatissimum) is the major plant fiber cultivated in northern Europe, mainly for the textile sector. The structure and composition of flax plants is complex [4,5]. The stems contain fiber bundles embedded in cortex tissues at the periphery. In these bundles, single fibers are grouped together by middle lamellae. -
Spinning and Winding Taro Nishimura
The_Textile_Machinery_Society_of_Japan_Textile_College_2-Day_Course_on_Cloth_Making_Introduction_to_Spinning_2014_05_22 Spinning and Winding Taro Nishimura 1. Introduction Since several thousand years ago, humans have been manufacturing linen, wool, cotton, and silk to be used as fibrous materials for clothing. In 繊維 (sen’i ), which is the word for “fiber,” the Chinese character 繊 (sen ) is a unit for decimal fractions of one ten-millionth (equal to approximately 30 Ǻ), while 維 (i) means “long and thin.” Usually, fibers are several dozen µ thick, and can range from around one centimeter long to nigh infinite length. All natural materials, with the exception of raw silk, are between several to several dozen centimeters long and are categorized as staple fibers. Most synthetic fibers are spun into filaments. Figure 1 shows how a variety of textile product forms are interrelated. Short fibers are spun into cotton (spun) yarns, whereas filaments are used just as they are, or as textured yarns by being twisted or stretched. Fabric cloths that are processed into two-dimensional forms using cotton (spun) yarns and filament yarns include woven fabrics, knit fabrics, nets, and laces. Non-woven fabrics are another type of two-dimensional form, in which staple fibers and filaments are directly processed into cloths without being twisted into yarns. Yet another two-dimensional form is that of films, which are not fiber products and are made from synthetic materials. Three-dimensional fabrics and braids are categorized as three-dimensional forms. This paper discusses spinning, or the process of making staple fibers into yarns, and winding, which prepares fibers for weaving. One-dimensional Two-dimensional Three-dimensional Natural Staple fibers Spun yarns Woven fabrics Three-dimensional materials Filaments Filament yarns Knit fabrics fabrics Synthetic Nets Braids materials Laces Non-woven fabrics Films Fig. -
And Interdisciplinary Nature of Textile Design Research of Linseed Fibres
Multi- and interdisciplinary nature of textile design research of linseed fibres Tiina Härkäsalmi* and Ilpo Koskinen** Aalto-University, School of Art and Design, Department of Design Hämeentie 135 C, 00560 Helsinki, Finland *e-mail: [email protected] **e-mail: [email protected] Abstract: In the future there will be an increasing need for renewable, recyclable and environmentally safety fibres, which are compatible with existing, cotton-based textile manufacturing technologies and are competitive on price and quality. In this study as a raw material the linseed fibres are used, which is almost an unexploited resource for high value end uses. This paper describes a multidisciplinary design study that consisted of three parts, a microbiological study that devel- oped a Fusart®-method for cottonizing linseed fibres, a production model study aimed at showing how the fibres could be processed in an industrial scale, and a fibre quality evaluation study. In practise it means that lustrous and soft fibres, light coloured can be produced cost-efficiently and environmentally-consciously for textiles and potential for producing high-quality bio-based mate- rial with tailored properties. Keywords: design research, material research, fungus, textile design 1. Introduction The objective of this study is to explore the suitability of linseed elementary fibres in new textile and technical applications and creating prerequisites for product design and productization. The study is based on a multidisciplinary approach to the use of flax elementary fibres where, rather than tradi- tional long-linen textile processing technology, short-fibre methods are employed. Special attention was paid to the quality requirements of rotor spinning. -
Basic of Textiles
BASIC OF TEXTILES BFA(F) 202 CC 5 Directorate of Distance Education SWAMI VIVEKANAND SUBHARTI UNIVERSITY MEERUT 250005 UTTAR PRADESH SIM MOUDLE DEVELOPED BY: Reviewed by the study Material Assessment Committed Comprising: 1. Dr. N.K.Ahuja, Vice Chancellor Copyright © Publishers Grid No part of this publication which is material protected by this copyright notice may be reproduce or transmitted or utilized or store in any form or by any means now know or here in after invented, electronic, digital or mechanical. Including, photocopying, scanning, recording or by any informa- tion storage or retrieval system, without prior permission from the publisher. Information contained in this book has been published by Publishers Grid and Publishers. and has been obtained by its author from sources believed to be reliable and are correct to the best of their knowledge. However, the publisher and author shall in no event be liable for any errors, omission or damages arising out of this information and specially disclaim and implied warranties or merchantability or fitness for any particular use. Published by: Publishers Grid 4857/24, Ansari Road, Darya ganj, New Delhi-110002. Tel: 9899459633, 7982859204 E-mail: [email protected], [email protected] Printed by: A3 Digital Press Edition : 2021 CONTENTS 1. Fiber Study 5-64 2. Fiber and its Classification 65-175 3. Yarn and its Types 176-213 4. Fabric Manufacturing Techniques 214-260 5. Knitted 261-302 UNIT Fiber Study 1 NOTES FIBER STUDY STRUCTURE 1.1 Learning Objective 1.2 Introduction 1.3 Monomer, Polymer, Degree of polymerization 1.4 Student Activity 1.5 Properties of Fiber: Primary & Secondary 1.6 Summary 1.7 Glossary 1.8 Review Questions 1.1 LEARNING OBJECTIVE After studying this unit you should be able to: ● Describe the Natural Fiber. -
PRELIMINARY TREATMENT of FIBRES, E.G. for SPINNING (Winding Or Unwinding, Conducting Or Guiding Laps, Webs, Slivers Or Roving
D01G CPC COOPERATIVE PATENT CLASSIFICATION D TEXTILES; PAPER TEXTILES OR FLEXIBLE MATERIALS NOT OTHERWISE PROVIDED FOR D01 NATURAL OR MAN-MADE THREADS OR FIBRES; SPINNING (NOTE omitted) D01G PRELIMINARY TREATMENT OF FIBRES, e.g. FOR SPINNING (winding or unwinding, conducting or guiding laps, webs, slivers or rovings in general, sliver or roving cans, depositing in sliver or roving cabs B65H; preparation of fibres for paper-making D21) NOTE Attention is drawn to the note following the title of Class D01. WARNING In this subclass non-limiting references (in the sense of paragraph 39 of the Guide to the IPC) may still be displayed in the scheme. 1/00 Severing continuous filaments or long fibres, e.g. 9/08 . by means of air draught arrangements stapling 9/10 . using foraminous cylinders (foraminous suction 1/02 . to form staple fibres not delivered in strand form cylinders for lap-forming D01G 25/00) 1/022 . {by solvents} 9/12 . Combinations of opening or cleaning machines 1/025 . {by thermic means, e.g. laser} 9/14 . Details of machines or apparatus 1/027 . {by freezing} 9/16 . Feeding arrangements (fibre-feeding apparatus 1/04 . by cutting of general application in fibre-treating machines 1/06 . Converting tows to slivers or yarns, e.g. in D01G 23/00) direct spinning (drafting arrangements, twisting 9/18 . Arrangements for discharging fibres arrangements D01H) 9/20 . Framework; Casings; Coverings; Grids 1/08 . by stretching or abrading 9/22 . Driving arrangements 1/081 . {with preferential breaking zones} 11/00 Disintegrating fibre-containing articles to obtain 1/083 . {obtained by mechanical means, e.g. -
(A) Machinery, Plant, Vehicles ; (B) Construction of Buildings ; Basic Data on the Essential Characteristics of Industry Were Co
Official Journal of the European Communities 201 13.8.64 OFFICIAL JOURNAL OF THE EUROPEAN COMMUNITIES 2193/64 COUNCIL DIRECTIVE of 30 July 1964 concerning co-ordinated annual surveys of investment in industry ( 64/475/EEC ) THE COUNCIL OF THE EUROPEAN ECONOMIC Article 2 COMMUNITY, For the purposes of this Directive, an industry shall Having regard to the Treaty establishing the Euro be defined by reference to the 'Nomenclature of Indus pean Economic Community, and in particular Article tries in the European Communities' ( NICE). 1 In the 213 thereof ; case of small undertakings the survey may be carried out by random sampling. Having regard to the draft submitted by the Com Article 3 Whereas in order to carry out the tasks entrusted to it under the Treaty the Commission must have at its The figures to be recorded shall be those in respect disposal annual statistics on the trend of investment of annual investment expenditure ( including plant in the industries of the Community ; constructed by the undertakings themselves), broken Whereas in the industrial survey for 1962 comparable down as follows : basic data on the essential characteristics of industry ( a ) Machinery, plant, vehicles ; were collected for the first time ; whereas such a ( b) Construction of buildings ; census cannot be carried out frequently ; whereas annual statistics concerning certain basic matters ( c) Purchase of existing buildings and of land . cannot however be dispensed with for the intervening Investments of a social nature shall , where possible, be years -
Reference for Spinning, Dyeing and Finishing of Milk Fiber
Swicofil AG Textile Services Gerliswilstr. 23 CH-6021 Emmenbrücke Reference for Spinning, Dyeing and Finishing of milk fiber 1. Spinning technological process (example of yarn with 163tex) Scutching A002D---A006B---A036C (card wire) Carding A186D Drawing FA302 (two lines) Roving A454G Spinning FA502 Winding 2. Main technical measure for each process 1). Pretreatment As seen in Table 1, the mass specific resistance of milk protein fiber is larger, so the pretreatment before scutching is more important. After opening bales, the milk protein fiber needs some water and antistatic agent. Based on the tests of fiber property and the choice of antistatic agents, the moisture regain of pure spinning with milk protein fiber is controlled about 16%, and the add-on of chosen composite antistatic agent is about 1%. Meanwhile, the relative humidity in the workshop is controlled within 68~70% to reduce the electrostatic influence. 2). Process of opening and picking With good uniformity and less impurity, the milk protein fiber is bulky and it is easy to open, and the friction coefficient between fibers is low, and the cohesion force is relatively weaker. Thus, the process of opening and picking should adopt the process of precise picking, less beating and low speed. During production, the height of the beater in the grab machine stretched rib is 2.5mm, and the picking should be precise and the blending should be uniform. In the opening machine model A036C, the card beater is adopted to reduce fiber damage and the constant volume of laps should be smaller to avoid neps during opening and picking so the lap quality can be stable. -
Agricultural Products FLAX Linum Usitatissimum from Which Comes
Agricultural Products FLAX Linum usitatissimum from which comes our words “linen”, “linseed oil”, “linoleum”. Flax seed is sewn as early in the springtime as the ground will permit; as soon as the frost leaves it, in other words. The seed was distributed rather densely so that the plants would be forced to grow straight upward to get enough sunlight, rather than to put out branches, which was not desirable. When ready for harvesting, the plants would be about two feet high. When the mature plants were ready for harvesting along about mid-summer, they were pulled up out of the ground rather than cut, and allowed to dry on the surface for a day or two. Cutting caused the plant’s sap to flow out, and this would stain the fibers, after which no amount of bleaching would produce white cloth. After drying, the flax was pulled through a ripple comb made with coarse wooden or heavy wire teeth. This broke off the pods and the seeds, which were saved for next year’s planting, or for barter or cash sale. The stalks were then tied by the top end in bundles called “beats”, or “bates” (depending on what part of the country you came from) and the base of the stalks were spread out to form a tent-shaped stack called a “stook” for drying. Next came soaking in water for fermentation, the length of time depending on the temperature and whether the water was moving. One method was to put the stalks in a stream. This was a smelly and slow process. -
Spinning Daily Presents Alternative Fibers: the Spinner's Guide To
presents Alternative Fibers: The Spinner’s Guide to Vegan, Natural, and Wool-Free Yarns ©F+W Media, Inc. ■ All rights reserved ■ F+W Media grants permission for any or all pages in this issue to be copied for personal use Spin.Off ■ spinningdaily.com ■ 1 pinners have worked with wool for thousands of years, and with good reason: it dyes easily, wears well, and Scomes from cute sheep. But it’s not the only option available nowadays. We can spin fiber produced from other animals, from plants, or from manufacturing processes. Bam- boo, soy, and corn can all be made into yarn. So can wood pulp and seaweed: if you’ve never heard of Seacell, Modal, or Lyocell, read on. Do all of these spinnable fibers qualify as natural? Are they vegan (i.e., animal-friendly) or at least animal- neutral? How sustainable are the different production methods? It depends on your personal definitions and choices. Some people might see rayon, extruded from wood pulp, as too far removed from Nature, while others might prefer rayon to water-intensive hemp retting. You’ll read about protein and cellulose fibers in the first article, then find others on plant-based fibers, either directly from the plant or processed in some way. If you want to spin something other than wool, you can find the perfect substitute here. Happy spinning, Anne Merrow [email protected] ©F+W Media, Inc. ■ All rights reserved ■ F+W Media grants permission for any or all pages in this issue to be copied for personal use Spin.Off ■ spinningdaily.com ■ 2 What are natural fi bers? BY A MY C LARKE M OORE atural fi bers occur naturally in na- not usually included in the natural fi ber catego- a Nture, naturally. -
GLOSSARY of SPINNING TERMS Batts - Carded Hunks of Fiber As It Comes Off of a Drumcarder Bench – Also Called the Table
GLOSSARY OF SPINNING TERMS batts - carded hunks of fiber as it comes off of a drumcarder bench – also called the table. The table of the spinning wheel on which the wheel and spinning mechanism are mounted bobbin – the shaft of the spool onto which the spun yarn is wound on a spinning wheel carders – (or cards) a pair of brushes used to smooth and straighten fibers for spinning comb - used to process long stapled wool for worsted spinning crimp - amount of curl in a lock of fleece; fine wool is very crimpy distaff – a staff that holds the flax or wool fibers which are drawn from as the spinner needs them when spinning. A distaff can be attached to a belt, mounted on the bench of a spinning wheel, or free-standing. draft - the pulling out of fibers to allow only a certain amount of the fiber to twist into thread drafting triangle – the space between the spun yarn and the fibers being drawn out drive band – the cord carrying the power from the large wheel to the spindle or bobbin/pulley drop spindle – (handspindle) a stick with a weighted whorl that is used to twist fibers into thread ewe – a mature female sheep fiber – the unspun hair/wool/plant material (as opposed to the thread, which is already spun) fleece – the entire coat of wool off of a sheep flyer – the u-shaped device on a treadle spinning wheel that twists the yarn footman – the straight piece of wood or wire that connects the treadle to the axle/crank of a spinning wheel grease wool – (or “wool in the grease”) the unwashed wool as it comes off of a sheep hank – a 560-yard long skein of wool, usually wound on a niddy-noddy or reel knot – a 40-yard strand skein of yarn wound on a reel or a niddy-noddy that measures 2 yards in circumference= 80 yards maidens – (or sisters) two upright pieces of wood that hold the spinning apparatus in a horizontal position. -
Notes from the Flax Presentation by Bruce Engebertson April 29, 2017
notes from the Flax Presentation by Bruce Engebertson April 29, 2017 Bruce began spinning wool at age 10, despite the fact that no one in his immediate family had any background in spinning. A chance referral led him to Ester Kromaki about 25 years ago, and she taught him the traditional Finnish techniques for growing, processing, spinning, and weaving flax. He says his linen knowledge is firmly based in the Finnish traditions and that "he doesn't know a variety of methods but the ones he knows, he knows well." The flax plant is an annual that dies in the winter. It is a "greedy" plant which will take lots of nutrients, so it's best not to plant it in soil that has been exhausted by other crops like corn. Flax is best in full sun and protected from the wind. It is relatively free from insect pests and will even keep potato bugs away (so plant near potatoes!). Prepare the seed bed by spading up the area to be seeded (in our case, approximately 3 ft by 3 ft) and adding in some cow manure or other fertilizer. Make sure the area is free of weeds when you seed. Seed flax when the lilacs just begin blooming. The seed should be spread thickly -- about 5 to 7 seeds for a thumbprint (of course, this depends on the size of your -- hopefully green -- thumb). Do not plant in rows. Divide the seeds in half and sow half in one direction and the other half if the other direction. If the soil is the same color as the seeds, you can add sand to the mix so you'll have an idea of how the seeds are being spread out. -
Hemp for Textiles: Plant Size Matters
Hemp for textiles: plant size matters Willem Westerhuis Thesis committee Promotor Prof. Dr P.C. Struik Professor of Crop Physiology Wageningen University Co-promotors Dr T.J. Stomph Associate professor, Centre for Crop Systems Analysis Wageningen University Dr J.E.G. van Dam Senior scientist, Food & Biobased Research Wageningen University and Research Centre Other members Prof. Dr J.H. Bitter, Wageningen University Dr B. Chabbert, UMR FARE, INRA, Reims, France Prof. Dr M.K. van Ittersum, Wageningen University Dr F.J. Sterck, Wageningen University This research was conducted under the auspices of the C.T. De Wit Graduate School of Production Ecology and Resource Conservation. Hemp for textiles: plant size matters Willem Westerhuis Thesis submitted in fulfilment of the requirements for the degree of doctor at Wageningen University by the authority of the Rector Magnificus Prof. Dr A.P.J. Mol, in the presence of the Thesis Committee appointed by the Academic Board to be defended in public on Friday 20 May 2016 at 11 a.m. in the Aula. Willem Westerhuis Hemp for textiles: plant size matters 234 pages. PhD thesis, Wageningen University, Wageningen, NL (2016) With references, with summaries in Dutch and English ISBN: 978-94-6257-787-9 DOI: http://dx.doi.org/10.18174/378698 Abstract Westerhuis, W. (2016) Hemp for textiles: plant size matters, PhD thesis. Wageningen University, Wageningen, The Netherlands, 234 pp. With English and Dutch summaries. Fibre hemp (Cannabis sativa L.) may be an alternative to cotton and synthetic fibres as a raw material for textile yarn production in the European Union. The agronomic options to manipulate plant development and crop growth with the aim to optimise hemp long fibre production were investigated.