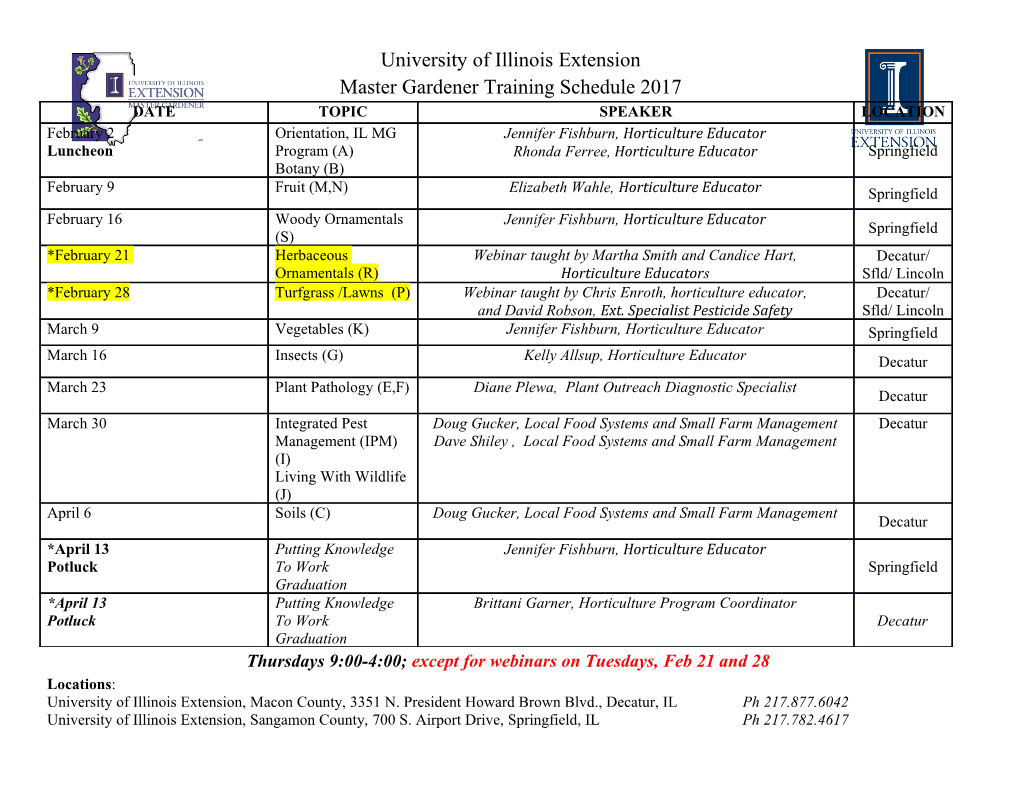
Processing of Fiber Flax Plymouth and by the early settlers at Jamestown. Nearly every farmhouse had a spinning wheel and women were skilled in the art of spinning linen and in Oregon woolen yarns. Homespun cloth was the chief textile of Colonial days. Flax Jesse E. Harmond growing and processing increased in the United States until Eli Whitney in- vented the cotton gin in 1793. The flax processors, unable to compete with the lower-cost cotton production, were Fiber flax is processed in the United forced to close their plants. States only in the Willamette Valley of Flax is grown commercially for seed Oregon. Flax plantings there have and for fiber. The varieties grown for varied from 18,000 acres in 1942 to seed are generally short plants with about 1,000 acres in 1950. The 1942 many lateral branches. Fiber from the crop yielded 2,000 tons of line fiber, seed varieties is often coarse and harsh which is about a third of the quantity and is not well suited for textiles. The imported each year. Nearly 6,000 tons varieties grown for fiber have fewer of unmanufactured flax fiber and 35 lateral branches and reach a greater million dollars' worth of manufactured height than seed flax. The fiber is finer, linen were imported into the United longer, and softer than that in seed flax. States in 1948. The seed from fiber flax is as valuable The future of the Oregon industry for oil and meal as that from seed flax. depends largely on the ability of Amer- Production of high-grade fiber flax ican farmers and processors to mecha- calls for a cool, moist growing season, a nize their operations so that high- requirement that has somewhat re- grade fiber can be supplied at a price stricted the areas where the crop can that will make competition possible be successfully grown. with European flax fiber, which is pro- The commercial processing of fiber duced with low-cost labor. flax in the United States has been The United States Department of largely confined to Michigan and Ore- Agriculture, the Oregon Agricultural gon. In Michigan, the industry ended Experiment Station, and the fiber-flax with the beginning of the First World industry have been working coopera- War. The present industry in Oregon tively on processing problems since began in 1915, when the State legisla- 1938. New techniques and machines ture appropriated $50,000 to the Ore- have been developed to reduce costs of gon Penitentiary to erect a processing production and processing and at the plant, which is still in operation. same time preserve the inherent good I'hrec cooperative processing plants quality of fiber. were established jointly by the State of Oregon, the Works Progress Adminis- LINEN is a textile of great antiq- tration, and growers' cooperatives in uity. Linen that was manufactured 1936. Ten more were built with Fed- 10,000 years ago by the neolithic lake eral, State, and private capital from dwellers has been found in Swdtzerland. 1941 to 1943, bringing the total to 14. Flax was one of the first crops grown The number of active processing plants in the New World by the Pilgrims at dropped to four in 1950 because of the 484 PROCESSING OF FIBER FLAX IN OREGON 485 decline in prices of domestic fiben lower yield of line fiber ; it increases the competition from cheaper imported proportion of tangled fiber, w^hich is European fiber, failure of the industry called flax tow, and causes the dis- to establish grade standards, lack of charge of fiber with uneven ends from orderly marketing procedures, and the scutching machine. high prices paid for competitive crops. Many patents have been granted on flax pullers, but only four or five have FLAX PROCESSING comprises six ma- been developed to the stage where they jor steps: Pulling, or harvesting; de- are used commercially. The slowness seeding, or separation of seed from in adapting mechanical pullers has straw; retting,, or partial rotting, to been attributed to an abundance of loosen the fiber from the rest of the cheap labor in the flax areas and the plant ; drying, or removal of the retting small plantings of flax on each farm. water from the straw; scutching, or The shortage of labor after the First separation of the long line fiber from World War stimulated the develop- the rest of the plant; and hackling, or ment and use of flax pullers. combing, to make the long fibers paral- lel and remove the short tangled fibers. A MAJOR PROBLEM Confronting the Fiber flax is usually planted from industry at the beginning of the proj- February 15 to April 15. It is pulled ect was how to ri^move the seed from and delivered to the processing plants the flax stems without damaging the in July and August. A small part of the straw. straw is deseeded as it is delivered; Devices for deseeding fiber flax al- the rest is deseeded by January. Retting ready patented include a hand-oper- and drying arc ordinarily done from ated ripple, one of the earliest devices. June to October of the following year. Ripple deseeding is still practiced to Scutching and hackling arc done from some extent in Egypt. The bundle of October to May. The processing opera- flax is spread and the seed ends are tions cover from 18 months to 2 years drawn manually through stationary from the time the straw is pulled until metal combs. The seed balls are pulled the fiber is ready for the market. off and collected on a sheet. This an- cic^nt method requires 18 to 20 man- FLAX PLANTS grown for fiber are hours per ton of pulled flax. pulled by hand or by machine. Reapers, In 1938, when the research project sometimes used, cut the flax straw from was bi^gun, the Oregon industry used 3 to 7 inches above the ground. As the the whipper deseeder, which consists line fiber runs the full length of the of two smooth rollers revolving inward straw, a good deal of valuable fiber is and pressed together by springs. The left in the field to rot when the crop seed-bearing part of the straw is passed is harvested by cutting. three or four times between the rollers, A skilled workman can hand pull an which crush the seed balls and liberate acre of flax in 68 hours. The tractor- the seed. A crew of 10 men can deseed drawn Willamette puller wdth two men a ton of flax in an hour with the can do it in far less time. w^hipper machine. Mechanical pullers thus far devel- An automatic rotary-comb des<îcder, oped often scuff, or crush, the straw which facilitates straight-line opera- where it is gripped in the pulling tion, was developed by specialists on mechanism and cause the fiber to over- the research project. It has been widely ret and weaken at the damaged points adopted in Oregon. during retting. One of the new desecders, wdth Uneven bundles produced in pulling auxiliary automatic conveying, but- cause seed losses in the deseeding and ting^ and tying apparatus, w^as installed straw losses in the processing opera- at the Mount Angel flax plant in 1948. tions. The unevcnness results in a Four men can operate it. One unloads 486 1950-1951 YEARBOOK OF AGRICULTURE from the wagon to the deseeder table; A mechanical device now makes it one cuts the string and places the possible to fasten the many tank-cover bundles on the straw conveyor; one re- parts together and handle them as a ceives the bundles from an elevator single unit. The operation takes 3 to 5 and stacks them on the wagon; and minutes. the fourth operates the threshing ma- Under the existing methods of flax chine and sacks the seed. handling, retted flax straw is dried only The capacity of the improved ma- in the summer. The wet straw from the chine has been limited to the ability of large concrete retting tanks is trans- the operators to feed it. Four men can ferred to the field by truck. The strings deseed 3 tons of pulled straw an hour. are cut, and each bundle of retted flax is set up in the form of a wigwam to FLAX FIBERS are in the cambium field-dry. The flax is manually removed layer of the plant, where they are ce- from the field after drying and fed to a mented together and to the other parts small mobile binder, which ties the of the stem by pectins. To prepare it bundle again and leaves it on the dry- for fiber separation, the straw is sub- ing field. The bundles are loaded on a jected to a retting, or rotting, process. truck with pitchforks and transported Retting is a bacteriological fermenta- to a storage shed. tion; micro-organisms decompose the A self-propelled machine, developed pectins and loosen the bond between on the project, mechanically removes the fiber and other parts of the plant, the dried wigwams from the field, so that the woody portions can be binds them into bundles with one tie broken and the fiber removed. string, and conveys them to a trailing There are two methods of retting— wagon. Three men operate the ma- dew retting and water retting. In dew chine—one, a ground man, sets up wig- retting, the flax is spread on the wams that have been blown over; one ground, where it is exposed repeatedly operates the machine and guides the to heavy dew. The pectins are slowly bundle; the third receives the bundles broken down by the action of mold from the elevator and stacks them on fungus, so that the fiber is loosened the wagon.
Details
-
File Typepdf
-
Upload Time-
-
Content LanguagesEnglish
-
Upload UserAnonymous/Not logged-in
-
File Pages5 Page
-
File Size-