Analysis of Propellant Weight Under Re-Entry Conditions for a Reusable Launch Vehicle Using Retropropulsion
Total Page:16
File Type:pdf, Size:1020Kb
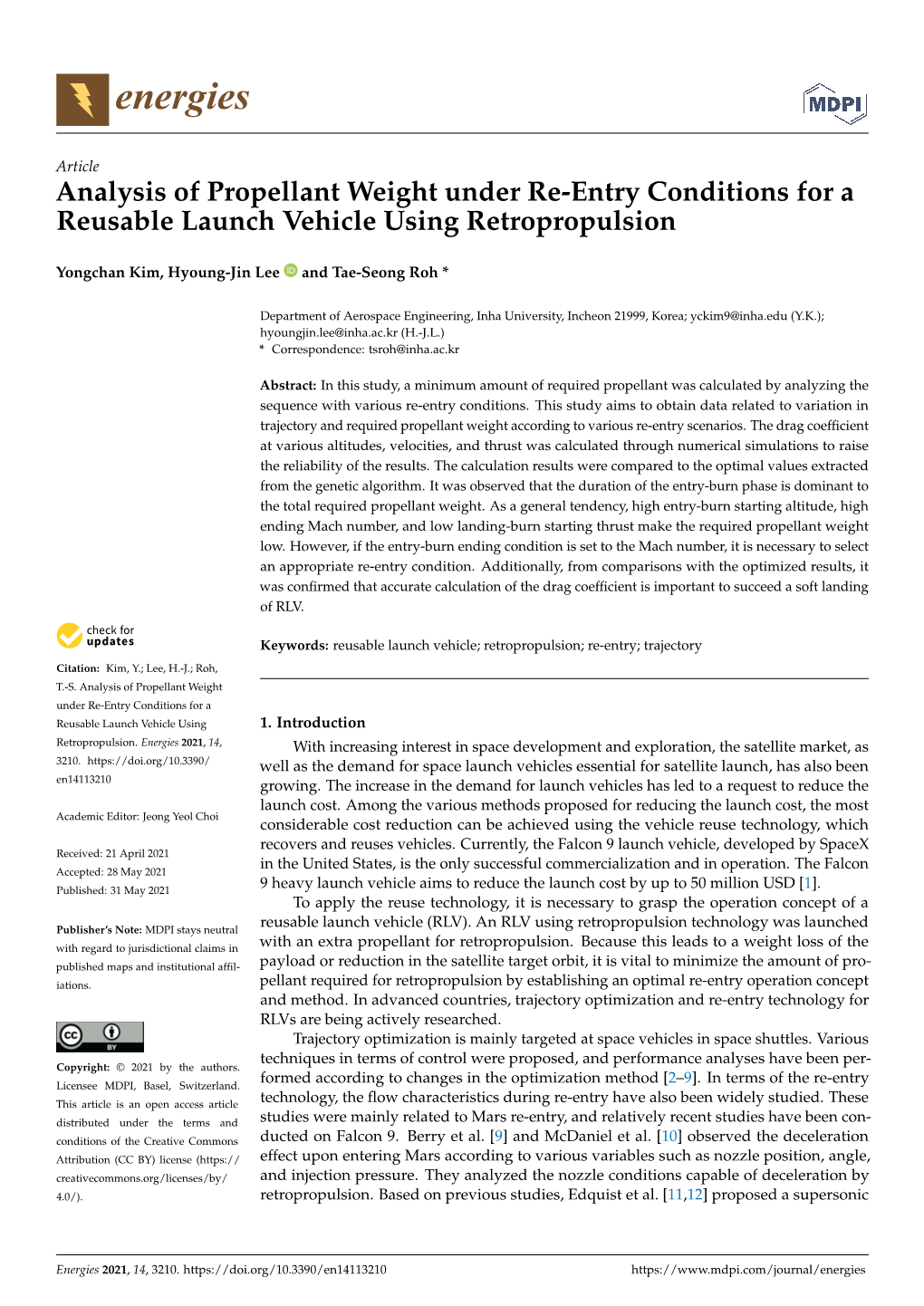
Load more
Recommended publications
-
APSCC Monthly E-Newsletter NOVEMBER 2017
APSCC Monthly e-Newsletter NOVEMBER 2017 The Asia-Pacific Satellite Communications Council (APSCC) e-Newsletter is produced on a monthly basis as part of APSCC’s information services for members and professionals in the satellite industry. Subscribe to the APSCC monthly newsletter and be updated with the latest satellite industry news as well as APSCC activities! To renew your subscription, please visit www.apscc.or.kr/sub4_5.asp. To unsubscribe, send an email to [email protected] with a title “Unsubscribe.” News in this issue has been collected from October 1 to October 31. INSIDE APSCC The APSCC 2017 Conference & Exhibition Marks Another Great Success! The APSCC 2017 Satellite Conference & Exhibition successfully ended on 12 October 2017 in Tokyo after 3 days of in-depth conference sessions, state-of-the-art technology displayed exhibition, and diverse networking events with more than 400 delegates attending the event. At APSCC 2017, thought leaders covered major issues impacting the Asia-Pacific satellite industry, including market insight on the latest trends, new applications, and innovative technical solutions throughout the three-day roundtable discussions and presentation sessions. The APSCC 2018 Satellite Conference & Exhibition will be held on 9-11 October in Jakarta, Indonesia. The APSCC-ISU Youth Development Workshop The second APSCC-ISU Youth Development Workshop was successfully held concurrently with the APSCC 2017 event on October 12. The workshop provided a platform for the brightest up-and-coming engineering students and young professionals in Japan to connect with leading satellite and space industry experts and learn more about the opportunities in the sector. -
Orbital Debris Quarterly News 22-1
National Aeronautics and Space Administration Orbital Debris Quarterly News Volume 22, Issue 1 February 2018 Inside... Two Anomalous Events in GEO Summer 2017 was marred by two apparently platform. Spacecraft dry mass is estimated to be on Space Debris Sensor anomalous events in the geosynchronous orbit the order of 2000 kg. On-board stored energy sources Launches Aboard (GEO) belt. Both incidents have been observed by include fuel and pressurized components, as well as the commercial space situation awareness providers, but as battery subsystem. SpaceX-13 2 of 26 December 2017 no debris from either event have The Indonesian GEO communications spacecraft entered the public catalog. TELKOM-1 (1999-042A, SSN catalog number 25880) SEM Analysis The GEO communications spacecraft AMC-9 experienced an energetic event on or about 25 August Results of (International Designator 2003-024A, U.S. Strategic 2017, after over 18.1 years on-orbit—3 years past Returned ISS Command [USSTRATCOM] Space Surveillance its nominal operational lifetime. An examination of Network [SSN] catalog number 27820), formerly known the Two Line Element data indicates an observable PMA-2 Cover 4 as GE-12, experienced an energetic event estimated to change in spacecraft orbit between 26 and 29 August. have occurred at approximately 07:10 GMT on 17 June At the beginning of this time interval, approximately CubeSat Study 2017, after approximately 14 years on-orbit. Fig. 1 Project Review 6 depicts the orbital evolution of the spacecraft in 2017. continued on page 2 SES, the spacecraft owner- operator, described this AMC‐9 (SSN 27820, 2003‐024A) 360 36300 Space Debris Sensor event as a “serious anomaly.” Installation 8 Following this event, the 36200 spacecraft began a westward 300 Monthly Object Type drift in the GEO belt. -
Validation of Wind Tunnel Test and Cfd Techniques for Retro-Propulsion (Retpro): Overview on a Project Within the Future Launchers Preparatory Programme (Flpp)
VALIDATION OF WIND TUNNEL TEST AND CFD TECHNIQUES FOR RETRO-PROPULSION (RETPRO): OVERVIEW ON A PROJECT WITHIN THE FUTURE LAUNCHERS PREPARATORY PROGRAMME (FLPP) D. Kirchheck, A. Marwege, J. Klevanski, J. Riehmer, A. Gulhan¨ German Aerospace Center (DLR) Supersonic and Hypersonic Technologies Department Cologne, Germany S. Karl O. Gloth German Aerospace Center (DLR) enGits GmbH Spacecraft Department Todtnau, Germany Gottingen,¨ Germany ABSTRACT and landing (VTVL) spacecraft, assisted by retro-propulsion. Up to now, in Europe, knowledge and expertise in that field, The RETPRO project is a 2-years activity, led by the Ger- though constantly growing, is still limited. Systematic stud- man Aerospace Center (DLR) in the frame of ESA’s Future ies were conducted to compare concepts for possible future Launchers Preparatory Program (FLPP), to close the gap of European launchers [2, 3], and activities on detailed inves- knowledge on aerodynamics and aero-thermodynamics of tigations of system components of VTVL re-usable launch retro-propulsion assisted landings for future concepts in Eu- vehicles (RLV) recently started in the RETALT project [4, 5]. rope. The paper gives an overview on the goals, strategy, and Nevertheless, validated knowledge on the aerodynamic current status of the project, aiming for the validation of inno- and aerothermal characteristics of such vehicles is still lim- vative WTT and CFD tools for retro-propulsion applications. ited to a small amount of experimental and numerical inves- Index Terms— RETPRO, retro-propulsion, launcher tigations mostly on lower altitude VTVL trajectories, e. g. aero-thermodynamics, wind tunnel testing, CFD validation within the CALLISTO project [6, 7, 8]. Other studies were conducted to analyze the aerothermodynamics of a simplified generic Falcon 9 geometry during its re-entry and landing 1. -
Reusable Launch Vehicle Technology Program{
Acta Astronautica Vol. 41, No. 11, pp. 777±790, 1997 # 1998 Published by Elsevier Science Ltd. All rights reserved Printed in Great Britain PII: S0094-5765(97)00197-5 0094-5765/98 $19.00 + 0.00 REUSABLE LAUNCH VEHICLE TECHNOLOGY PROGRAM{ DELMA C. FREEMAN{ JR. and THEODORE A. TALAY} NASA Langley Research Center, Hampton, Virginia 23681-0001, USA R. EUGENE AUSTIN} NASA Marshall Space Flight Center, Marshall Space Flight Center, Alabama 35812-1000, USA (Received 25 April 1997) AbstractÐIndustry/NASA reusable launch vehicle (RLV) technology program eorts are underway to design, test, and develop technologies and concepts for viable commercial launch systems that also satisfy national needs at acceptable recurring costs. Signi®cant progress has been made in understanding the technical challenges of fully reusable launch systems and the accompanying management and oper- ational approaches for achieving a low-cost program. This paper reviews the current status of the RLV technology program including the DC-XA, X-33 and X-34 ¯ight systems and associated technology programs. It addresses the speci®c technologies being tested that address the technical and operability challenges of reusable launch systems including reusable cryogenic propellant tanks, composite structures, thermal protection systems, improved propul- sion, and subsystem operability enhancements. The recently concluded DC-XA test program demon- strated some of these technologies in ground and ¯ight tests. Contracts were awarded recently for both the X-33 and X-34 ¯ight demonstrator systems. The Orbital Sciences Corporation X-34 ¯ight test ve- hicle will demonstrate an air-launched reusable vehicle capable of ¯ight to speeds of Mach 8. -
A Review of Current Research in Subscale Flight Testing and Analysis of Its Main Practical Challenges
aerospace Article A Review of Current Research in Subscale Flight Testing and Analysis of Its Main Practical Challenges Alejandro Sobron * , David Lundström and Petter Krus Department of Management and Engineering, Division of Fluid and Mechatronic Systems, Linköping University, SE-58183 Linköping, Sweden; [email protected] (D.L.); [email protected] (P.K.) * Correspondence: [email protected]; Tel.: +46-1328-1893 Abstract: Testing of untethered subscale models, often referred to as subscale flight testing, has traditionally had a relatively minor, yet relevant use in aeronautical research and development. As recent advances in electronics, rapid prototyping and unmanned-vehicle technologies expand its capabilities and lower its cost, this experimental method is seeing growing interest across academia and the industry. However, subscale models cannot meet all similarity conditions required for simulating full-scale flight. This leads to a variety of approaches to scaling and to other alternative applications. Through a literature review and analysis of different scaling strategies, this study presents an overall picture of how subscale flight testing has been used in recent years and synthesises its main issues and practical limitations. Results show that, while the estimation of full-scale characteristics is still an interesting application within certain flight conditions, subscale models are progressively taking a broader role as low-cost technology-testing platforms with relaxed similarity constraints. Different approaches to tackle the identified practical challenges, implemented both by the authors and by other organisations, are discussed and evaluated through flight experiments. Citation: Sobron, A.; Lundström, D.; Keywords: subscale flight testing; similarity; scale model; remotely piloted aircraft; demonstration; Krus, P. -
+ Part 10: Test and Evaluation
10. Test and Evaluation 10.1 Approach Architecture Design, Development, Test, and Evaluation (DDT&E) schedule, costs, and risk are highly dependent on the integrated test and evaluation approach for each of the major elements. As a part of the Exploration Systems Architecture Study (ESAS), a top-level test and evaluation plan, including individual flight test objectives, was developed and is summarized in this section. The test and evaluation plan described here is derived from the Apollo Flight Test Program of the 1960s. A more detailed test and evaluation plan will be based on detailed verification requirements and objectives documented in specifications and verification plans. In order to support schedule, cost, and risk assessments for the reference ESAS architecture, an integrated test and evaluation plan was developed to identify the number and type of major test articles (flight and ground) and the timing and objectives of each major flight test, including facilities and equipment required to support those tests. This initial plan is based on the Apollo Program and the ESAS Ground Rules and Assumptions (GR&As)—including the human- rating requirements from NASA Procedural Requirements (NPR) 8705.2A, Human-Rating Requirements for Space Systems. 10. Test and Evaluation 645 10.2 Ground Rules and Assumptions ESAS GR&As establish the initial set of key constraints to testing. Although all ESAS GR&As are considered, the specific ones listed below are particularly significant, as they deal with schedule and testing/qualification assumptions. • The crew launch system shall facilitate crew survival using abort and escape. There will be three all-up tests of the Launch Abort System (LAS). -
Flight Engineer Knowledge Test Guide
AC 63-1 FLIGHT ENGINEER KNOWLEDGE TEST GUIDE U.S. Department of Transportation Federal Aviation Administration 1 FLIGHT ENGINEER KNOWLEDGE TEST GUIDE 1995 U.S. DEPARTMENT OF TRANSPORTATION FEDERAL AVIATION ADMINISTRATION Flight Standards Service 2 PREFACE The Flight Standards Service of the Federal Aviation Administration (FAA) has developed this guide to help applicants meet the knowledge requirements for the computer administered tests for flight engineer turbojet, turboprop, and reciprocating class certification. This guide contains information about the knowledge test eligibility requirements, test descriptions, testing and retesting procedures, and sample test questions with answers. As a convenience to the applicant, the eligibility requirements for the oral and flight tests are included. Appendix 1 provides a list of reference materials and subject matter knowledge codes, and computer testing designees. Changes to the subject matter knowledge code list will be published as a separate advisory circular. The sample questions and answers in this guide are predicated on Federal Aviation Regulations (FAR's) and references that were current at the time of publication. Questions and answers in the computer administered knowledge tests are updated when changes are made to these reference materials. The flight engineer test question bank and subject matter knowledge code list for all airmen certificates and ratings, with changes, may be obtained by computer access from FedWorld at (703) 321-3339. This bulletin board service is provided by the U.S. Department of Commerce, 24 hours a day, 7 days per week. For technical assistance regarding computer requirements for this service, contact the FedWorld help desk at (703) 487-4608 from 7:30 a.m. -
Spacex Rocket Data Satisfies Elementary Hohmann Transfer Formula E-Mail: [email protected] and [email protected]
IOP Physics Education Phys. Educ. 55 P A P ER Phys. Educ. 55 (2020) 025011 (9pp) iopscience.org/ped 2020 SpaceX rocket data satisfies © 2020 IOP Publishing Ltd elementary Hohmann transfer PHEDA7 formula 025011 Michael J Ruiz and James Perkins M J Ruiz and J Perkins Department of Physics and Astronomy, University of North Carolina at Asheville, Asheville, NC 28804, United States of America SpaceX rocket data satisfies elementary Hohmann transfer formula E-mail: [email protected] and [email protected] Printed in the UK Abstract The private company SpaceX regularly launches satellites into geostationary PED orbits. SpaceX posts videos of these flights with telemetry data displaying the time from launch, altitude, and rocket speed in real time. In this paper 10.1088/1361-6552/ab5f4c this telemetry information is used to determine the velocity boost of the rocket as it leaves its circular parking orbit around the Earth to enter a Hohmann transfer orbit, an elliptical orbit on which the spacecraft reaches 1361-6552 a high altitude. A simple derivation is given for the Hohmann transfer velocity boost that introductory students can derive on their own with a little teacher guidance. They can then use the SpaceX telemetry data to verify the Published theoretical results, finding the discrepancy between observation and theory to be 3% or less. The students will love the rocket videos as the launches and 3 transfer burns are very exciting to watch. 2 Introduction Complex 39A at the NASA Kennedy Space Center in Cape Canaveral, Florida. This launch SpaceX is a company that ‘designs, manufactures and launches advanced rockets and spacecraft. -
PRFP-11) & Interconnectivity Workshop 26-30 November 2019, Apia, SAMOA
11th APT Policy and Regulation Forum for Pacific (PRFP-11) & Interconnectivity Workshop 26-30 November 2019, Apia, SAMOA Workshop Topic ENABLERS FOR A BETTER CONNECTED PACIFIC - New Satellite Technologies and Services (MSS, ESIM and LEOs) Dr Bob Horton Consultant Satellite Industry ENABLERS FOR A BETTER CONNECTED PACIFIC - New Satellite Technologies and Services (MSS and LEOs) CONTENTS • Examples of progress : MSS, ESIM – Inmarsat LEOs – OneWeb • Pacific Needs - understanding and participating in the regional/global environment - the Pacific : a “Collection of Islands” or an “Island Collective”? - opportunities overdue in APAC Inmarsat use of spectrum L band Ka band User links: 1626.5-1660.5 MHz ↑, 1525-1559 Feeder link ↑ : 27.5 – 30.0 GHz MHz↓ Feeder link↓ : 17.7 – 20.2 GHz Extended L-band: User link ↑ : 29.0 – 30.0 GHz User link↓ : 19.2 – 20.2 GHz User links: 1668-1675 MHz ↑, 1518 MHz-1525 MHz ↓ Used by Inmarsat Global Express satellites S band Used by Inmarsat-4 satellites and Alphasat Feeder link ↑ : 27.5 – 29.5 GHz Feeder link↓ : 17.7 – 19.7 GHz User link ↑ 1980-2010MHz Q/V band User link↓ : 2170-2200MHz C band 37.5-42.5 GHz ↓ Used by Europasat Feeder links for L-band satellites operate in 47.2-50.2 GHz + 50.4-51.4 GHz ↑ the bands 3550 – 3700 MHz and 6425 – - Planned for future satellites to free 6575 MHz through more than 20 Land Earth Stations up Ka-band for user terminals TT&C operated in standard C-band on most - Developmental payload on Alphasat Inmarsat satellites Inmarsat and Extended L-band Extended L-band will be available -
The Annual Compendium of Commercial Space Transportation: 2017
Federal Aviation Administration The Annual Compendium of Commercial Space Transportation: 2017 January 2017 Annual Compendium of Commercial Space Transportation: 2017 i Contents About the FAA Office of Commercial Space Transportation The Federal Aviation Administration’s Office of Commercial Space Transportation (FAA AST) licenses and regulates U.S. commercial space launch and reentry activity, as well as the operation of non-federal launch and reentry sites, as authorized by Executive Order 12465 and Title 51 United States Code, Subtitle V, Chapter 509 (formerly the Commercial Space Launch Act). FAA AST’s mission is to ensure public health and safety and the safety of property while protecting the national security and foreign policy interests of the United States during commercial launch and reentry operations. In addition, FAA AST is directed to encourage, facilitate, and promote commercial space launches and reentries. Additional information concerning commercial space transportation can be found on FAA AST’s website: http://www.faa.gov/go/ast Cover art: Phil Smith, The Tauri Group (2017) Publication produced for FAA AST by The Tauri Group under contract. NOTICE Use of trade names or names of manufacturers in this document does not constitute an official endorsement of such products or manufacturers, either expressed or implied, by the Federal Aviation Administration. ii Annual Compendium of Commercial Space Transportation: 2017 GENERAL CONTENTS Executive Summary 1 Introduction 5 Launch Vehicles 9 Launch and Reentry Sites 21 Payloads 35 2016 Launch Events 39 2017 Annual Commercial Space Transportation Forecast 45 Space Transportation Law and Policy 83 Appendices 89 Orbital Launch Vehicle Fact Sheets 100 iii Contents DETAILED CONTENTS EXECUTIVE SUMMARY . -
UAS FLIGHT TEST for SAFETY and for EFFICIENCY Seamus M
UAS FLIGHT TEST FOR SAFETY AND FOR EFFICIENCY Seamus M. McGovern, U.S. DOT National Transportation Systems Center, Cambridge, Massachusetts Abstract (e.g., SAE International technical standards and recommended practices) but also takes advantage of Manned aircraft that operate in the National competitive racing in order to evaluate new Airspace System (NAS) typically undergo technologies and materials (as it turns out, this may certification flight test to ensure they meet a have applicability to UASs as well with the advent of prescribed level of safety—dependent on their several organizations and sanctioning bodies category—before they are able to enter service [for including the European Rotor Sports Association and example, Federal Aviation Administration (FAA) the Drone Racing League). Other aviation-related advisory circular (AC) 25-7C is the flight-test guide tests and test formats not discussed here include the for certification of transport-category airplanes]. typically Department of Defense-focused With the integration of unmanned aircraft systems developmental test and evaluation; operational test (UAS) into the NAS, in the future some type of and evaluation; and research, development, test, and certification flight test may ultimately be required, evaluation structures. however, even lacking such a requirement UAS manufacturers can find value in flight testing UASs In terms of flight test, the military services have using familiar experimental and certification flight- their own criteria for evaluating their various aircraft. test procedures, the results of which can enhance the These requirements are often bound by contractual safety of the design, the safety of the operation, agreements between the service and the vendor, and/or the efficiency of the operation. -
General Flight Test Theory Applied to Aircraft Modifications
General Flight Test TheoryTUTORIAL Applied to Aircraft Modifications GENERAL FLIGHT TEST THEORY APPLIED TO AIRCRAFT MODIFICATIONS Lt Col Lionel D. Alford, Jr., USAF and Robert C. Knarr Any external aircraft modification has potentially far-reaching effects on the capability of the aircraft to succeed or fail in its mission. The authors take a systematic look at the effects that small changes can have upon the whole, with a series of examples that demonstrate why careful review of data or testing is often vital in the assessment of system modifications. new design aircraft program always external aircraft modification. The aircraft includes an instrumented test to design problems covered here represent Avalidate the analyses. But a modifi- the fundamental characteristics by which cation program may rely instead on pre- aircraft capability is judged. These design viously collected data for model valida- problems, when not properly analyzed and tion. Such a program must adequately tested (if required), have historically address the effects of the modification on resulted in significant degradation of air the aircraft and its mission. The user must worthiness. We define the subject area and judge these effects for their desirability— explain the importance of each problem especially when they degrade mission by discussing the rationale behind stan- capability. But, to be judged, they must dard design practices and air worthiness be fully understood. Reviewing historical and operational considerations for the fleet data or conducting a test are two ways to aircraft. Concrete examples illustrate each validate the data by which these effects case. Although only effects to the C–130 on aircraft capability are judged.