Ink Composition Tintenzusammensetzung Composition D’Encre
Total Page:16
File Type:pdf, Size:1020Kb
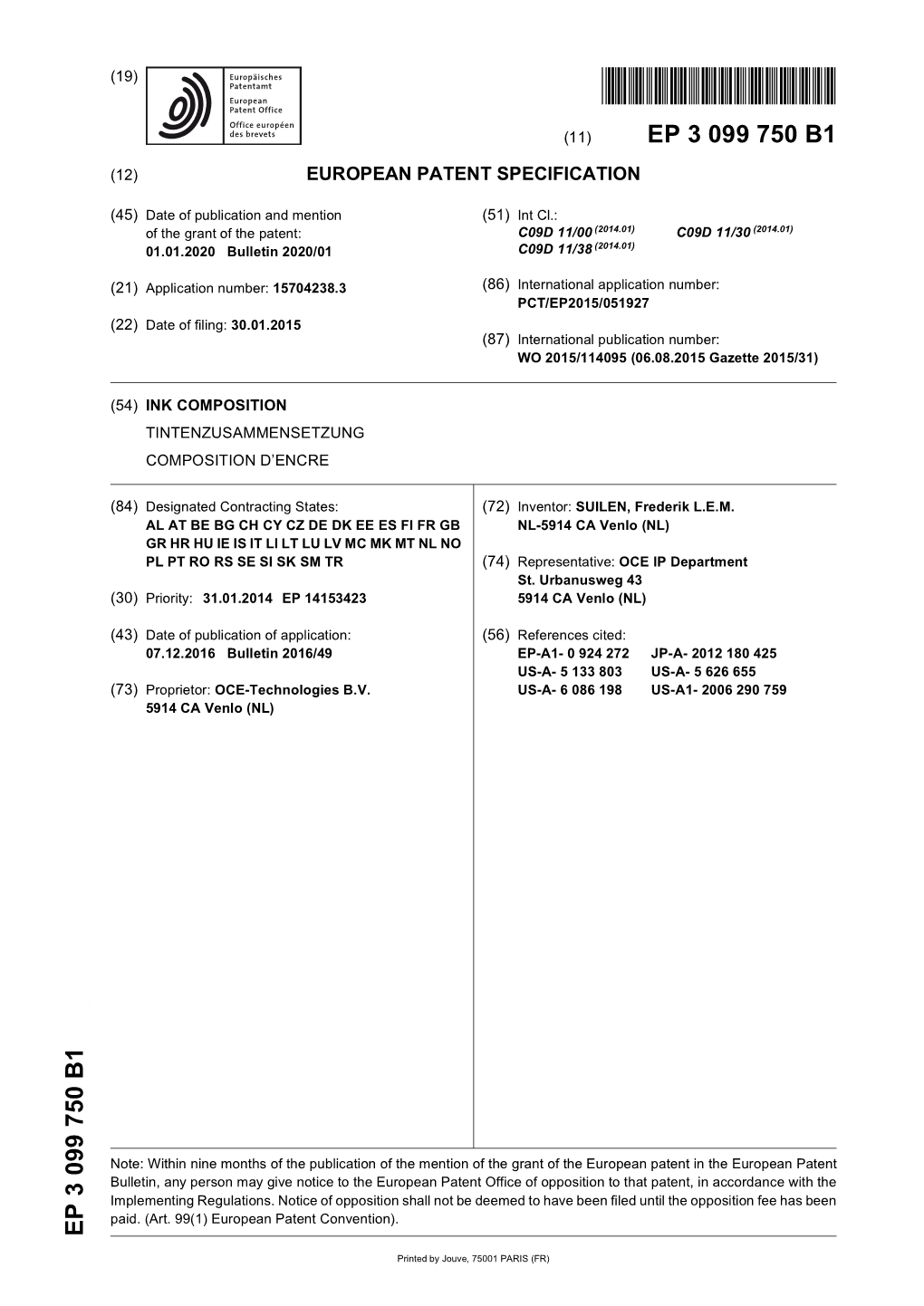
Load more
Recommended publications
-
(12) United States Patent (10) Patent No.: US 7,819,967 B2 Kyota Et Al
US007819967B2 (12) United States Patent (10) Patent No.: US 7,819,967 B2 Kyota et al. (45) Date of Patent: Oct. 26, 2010 (54) METHOD OF PRODUCING AN ORGANIC 7,160,380 B2 * 1/2007 Maeta et al. ................ 106,493 FINE PARTICLE DISPERSION, ORGANIC 7,503.972 B2 * 3/2009 Nagasawa et al. ........... 106,493 FNE PARTICLE DISPERSION OBTANED BY 2004/O138349 A1 7, 2004 Babler THE SAME, AND INK-JET RECORDING INK 2006/0057485 A1 3/2006 Teshima et al. AND PAINT USING THE DISPERSION 2006/0090697 A1 5, 2006 Teshima et al. 2007/0012221 A1 1/2007 Maeta et al. (75) Inventors: Hirokazu Kyota, Kanagawa (JP); Hideki Maeta, Minami-ashigara (JP) FOREIGN PATENT DOCUMENTS EP 1364997 A2 11/2003 (73) Assignee: Fujifilm Corporation, Minato-Ku, EP 1516 896 A1 3, 2005 Tokyo (JP) EP 1693 423 8, 2006 JP 2002-03O230 A 1, 2002 (*) Notice: Subject to any disclaimer, the term of this JP 2002-282678 A 10, 2002 patent is extended or adjusted under 35 JP 2002-282679. A 10, 2002 U.S.C. 154(b) by 55 days. JP 2003-026972 A 1, 2003 JP 2004-043776. A 2, 2004 (21) Appl. No.: 12/265,426 JP 2006-104448 A 4/2006 JP 2006-124556 A 5, 2006 (22) Filed: Nov. 5, 2008 JP 2007-039643 A 2, 2007 WO WO2007/091712 A1 * 8, 2007 (65) Prior Publication Data US 2009/O120325 A1 May 14, 2009 OTHER PUBLICATIONS Yuki Ganryo Handbook (Handbook of Organic Pigments), edited by (30) Foreign Application Priority Data Color Office, p. 45, with Concise Explanation of Document. -
Portrait Drawing
LILLSTREET ART CENTER 10-Week Classes Begin September 14. 5-Week Classes Begin September 14 & October 19. FALL CATALOGUE save ly and ear up n- ig Pay in full by S August 31 and receive $20 off your 10-week class and $10 off your 5-week class. CONTENTS First-Time Artist 3 Ceramics 4 Metalsmithing 6 & Jewelry Painting & Drawing 8 Kidstreet Special Section 11 Policies & Procedures 14 Glass 15 Printmaking 16 Textiles 18 Full Schedule 22 REGISTER TODAY! Gallery Information 24 VISIT WWW.LILLSTREET.COM OR CALL 773.769.4226 THIS IS YOUR ART CENTER When you take a class as Lillstreet Art Center, you'll enjoy professional instruction from our outstanding faculty. But being a student here means so much more. Many of your materials are included in your class fee, you'll have access to our facilities during generous open studio hours, and you'll be part of a unique community of artists sharing experiences and techniques with one another. You won't find a better value! Pay in full by August 31 and receive $20 off your 10-week class and $10 off your 5-week class. Book Your Holiday Party Here! Create a memorable event at Lillstreet. Choose from casual cocktail hours in the gallery, to hands-on workshops with projects to take home. Bring in your own caterer or select from First Slice's delicious options. Evenings and weekends available. Call 773-769-4226 for details. FIRST SLICE PIE CAFE‘ Stop by First Slice Pie Cafe before or after your class! Enjoy a cup of coffee with your friends, a quick snack, or a complete meal, and support this great nonprofit organization that helps fight hunger while satisfying yours. -
Obiko Art Wear Archive Project
TEXTILE ARTS COUNCIL FINE ARTS MUSEUMS OF SAN FRANCISCO OBIKO ART WEAR ARCHIVE PROJECT Feather collar by K.Lee Manuel “Electra” 1988. Photo: David Reese The Obiko ArtWear Archive documents and celebrates the work of Bay Area clothing and jewelry designers whose work was showcased at Sandra Sakata’s renowned boutique, Obiko. In the 1970s- through the 1990s, one-of-a-kind Art Wear blossomed in a culture that embraced global design. The influence of Asian and African ethnic costume and textile techniques is particularly evident in the aesthetic of this remarkable era. The archive includes a collection of designers’ work, four fashion shows, oral histories, photos and memories. The Textile Art Council hopes that the archive will be a great discovery and resource for future generations. © 2014 Textile Arts Council Fine Arts Museums of San Francisco, all rights reserved | Design: Nancy Rosenblum, Frisco Graphics OBIKO ART WEAR ARCHIVE PROJECT TABLE OF CONTENTS 1. Acknowledgements 2. History 3. Designers 4. Audio Interviews 5. Videos OBIKO ART WEAR ARCHIVE PROJECT ACKNOWLEDGEMENTS Jean Cacicedo Ana Lisa Hedstrom Thank Yous OBIKO ART WEAR ARCHIVE PROJECT | ACKNOWLEDGE- MENTS JEAN CACICEDO The hand-crafted garments and accessories that emerged in late 1960s and 1970s America played a significant role in our cultural identity. One-of-a-kind wearables emerged on both the east and west coasts, drawing on an anti-fashion street style approach. Two seminal galleries, Julie:Artisans in New York City and Obiko in San Francisco, provided a showcase for this work. I began my career on the east coast in the late 60s during an extraordinary time consumed by nationwide political protests and self expression. -
(12) United States Patent (10) Patent No.: US 7.442,731 B2 Tittmann (45) Date of Patent: Oct
USOO7442731B2 (12) United States Patent (10) Patent No.: US 7.442,731 B2 Tittmann (45) Date of Patent: Oct. 28, 2008 (54) OPAQUE, COLOUR-PIGMENTED COATING (56) References Cited (75) Inventor: Rolf Tittmann, Kandern (DE) U.S. PATENT DOCUMENTS 4.415,685 A 1 1/1983 Iqbal et al. .................... 524.92 (73) Assignee: Ciba Specialty Chemicals Corp., 5,200,528 A 4/1993 Wooden et al. ....... ... 548/453 Tarrytown, NY (US) 5,476,949 A 12/1995 Wallguist et al. ...... ... 548/453 5.492.564 A 2f1996 Wooden et al. ....... ... 106,493 (*) Notice: Subject to any disclaimer, the term of this 5,618,343 A 4/1997 Hendi et al. ...... ... 106,498 patent is extended or adjusted under 35 5,821,373 A 10/1998 Hao et al. ................... 548/453 U.S.C. 154(b) by 578 days. 5.997,627 A 12/1999 Balbler ........................ 106,493 (21) Appl. No.: 10/529,408 FOREIGN PATENT DOCUMENTS (22) PCT Filed: Sep. 30, 2003 EP O43O875 6, 1991 (86). PCT No.: PCT/EPO3/10835 EP O719842 T 1996 EP O842989 5, 1998 S371 (c)(1), (2), (4) Date: Mar. 29, 2005 Primary Examiner Kriellion A Sanders (74) Attorney, Agent, or Firm Joseph Suhadolnik (87) PCT Pub. No.: WO2004/031280 (57) ABSTRACT PCT Pub. Date: Apr. 15, 2004 (65) Prior Publication Data The invention relates to a coating having a thickness of from 5 to 25 um, comprising a high-molecular-weight organic US 2006/OO41037A1 Feb. 23, 2006 material and from 5 to 9 g/m colored pigments, wherein, based on the total amount of colored pigments, (a) from 30 to (30) Foreign Application Priority Data 90% by weight of 3,6-di(4'-biphenyl)-2,5-dihydro-pyrrolo3. -
Natural Dyes Are Friendly and Satisfying Some Notes Before Beginning
$1 the MAIWA guide to N atural dyes 603216 what they are and how to use them MAIWA atural Dyes handprints N what they are and how to use them People have added colour to cloth for thousands of years. It is only recently (the first artificial dye was invented in 1857) that the textile industry has turned to synthetic dyes. Today, many are rediscovering the joy of achieving colour through the use of renewable, non-toxic, natural sources. Natural dyes are friendly and satisfying some notes before beginning ... to use. They are familiar substances that can spark creative ideas and widen your 9 Learning to use natural dyes is like cooking with colour. view of the world. Try experimenting And just like cooking, it takes practice and care. Don’t rush the with them. Colour can be coaxed from process. Attention to detail will give results you are proud to all kinds of natural sources. Once the call your own. cloth or fibre is prepared for dyeing it Always use clean non-reactive vessels: stainless steel, will soak up the colour, yielding a range of shades from vibrant 9 unchipped enamel, glass, or plastic. Iron or copper vessels can jewel tones to dusky heathers and pastels. Variations are easily also be used but the metal will react with the dyebath. Iron will achieved by changing dyestuff, recipes, and methods. dull or “sadden” colours. Copper will tend to brighten them. Not all natural dye recipes are safe and non-toxic. Some books 9 Even dyeing is much more difficult with piece goods than still call for the use of heavy metal mordants such as chrome and with yarns. -
Industrial Chemicals, Ashfords Dictionary, Chemical Name Index
2 Chemical name index A A ACA 4-AA ACA AA ACAC AA acamprosate calcium AAA acarbose AABA ACB AADMC 7-ACCA AAEM ACE AAMX acebutolol AAOA aceclidine AAOC aceclofenac AAOT acemetacin AAPP acenaphthene AAPT acenocoumarol 4-ABA acephate ABA acepromazine abacavir acequinocyl ABAH acesulfame-K abamectin acetaldehyde ABFA acetaldehyde ethyl phenethyl diacetal ABL acetaldehyde oxime ABPA acetaldehyde n-propyl phenethyl diacetal ABS acetaldoxime ABS acetal resins O-ABTF acetal resins P-ABTF acetamide ACN acetamidine hydrochloride 7-ACA 5-acetamido-2-aminobenzenesulfonic acid 7-ANCA 6-acetamido-2-aminophenol-4-sulfonic acid Name Index: Ashford’s Dictionary of Industrial Chemicals 3-acetamidoaniline 3-acetamidoaniline acetic acid, s-butyl ester 4-acetamidoaniline acetic acid, calcium salt p-acetamidoanisole acetic acid, chromium salt 4-acetamidobenzenesulfonyl chloride acetic acid, cinnamyl ester 2-acetamidocinnamic acid acetic acid, citronellyl ester 3-acetamido-2-hydroxyaniline-5-sulfonic acid acetic acid, cobalt salt 1-acetamido-7-hydroxynaphthalene acetic acid, decahydro-β-naphthyl ester 8-acetamido-1-hydroxynaphthalene-3,6-disulfonic acid acetic acid, dicyclopentenyl ester 1-acetamido-7-naphthol acetic acid, diethylene glycol monobutyl ether ester 4-acetamidonitrobenzene acetic acid, 2-ethoxyethyl ester p-acetamidophenol acetic acid, ethoxypropyl ester 3-acetamidopropylsulfonic acid, calcium salt acetic acid, ethyl diglycol ester 5-acetamido-2,4,6-triiodo-N-methylisophthalamic acid acetic acid, ethylene glycol diester 4-acetamido-2-ethoxybenzoic -
Apr 9 – Oct 9 2016
APR 9 – OCT 9 2016 PRESS Press Contact Rachel Eggers Manager of Public Relations [email protected] RELEASE 206.654.3151 MARCH 17, 2016 MOOD INDIGO: TEXTILES FROM AROUND THE WORLD OPENS AT ASIAN ART MUSEUM SAT APR 9 SAM’s global textile collection—and a contemporary immersive installation with sound—tells the story of a color that surrounds us April 9–October 9, 2016 SEATTLE, WA – The Asian Art Museum presents Mood Indigo: Textiles From Around the World, honoring the unique ability of the color blue to create many moods in cloth. The exhibition of over 100 works is drawn primarily from SAM’s global textile collection, including a set of tapestries from Belgium, a silk court robe from China, a vast array of kimonos from Japan, resist-dyed cloths from Indonesia and Africa, and ancient fragments from Peru and Egypt. These historical pieces are accompanied by an immersive installation by contemporary artist Rowland Ricketts that includes interactive sounds of indigo by artist Norbert Herber. Indigo is a familiar thread throughout textile history, making it a natural focus for this, the first exhibition of textiles from the SAM collection since Patterns of Fiber in 1980. The galleries will take the viewer on a journey through the historic scope and multiple meanings of indigo. A quilt-like stuffed kimono and futonji (bedding covers), along with two contemporary American quilts, will explore the art of sleeping. The museum’s magnificent set of Belgian tapestries that depict three continents will be unveiled after recent conservation, showcasing the anchor role that indigo has in igniting their unusual subject matter. -
Dyes, Colors & Pigements
Copyright © Tarek Kakhia. All rights reserved. http://tarek.kakhia.org DYES , COLORS & PIGMENTS Writing By TAREK ISMAIL KAKHIA 0 Copyright © Tarek Kakhia. All rights reserved. http://tarek.kakhia.org Natural dye Skeins of wool colored with natural plant dyes. Contents : 1 Origins 2 Processes 3 Common dyestuffs o 3.1 Reds and pinks o 3.2 Oranges o 3.3 Yellows o 3.4 Greens o 3.5 Blues o 3.6 Purples o 3.7 Browns o 3.8 Greys and blacks o 3.9 Lichen o 3.10 Fungi 4 Luxury dyestuffs o 4.1 Royal purple o 4.2 Crimson and scarlet o 4.3 The rise of formal black 5 Decline and rediscovery 6 Notes 7 References 1 Copyright © Tarek Kakhia. All rights reserved. http://tarek.kakhia.org - Introduction : Natural dyes are dyes or colorants derived from plants, invertebrates, or minerals. The majority of natural dyes are vegetable dyes from plant sources – roots, berries, bark, leaves, and wood — and other organic sources such as fungi and lichens. Archaeologists have found evidence of textile dyeing dating back to the Neolithic period. In China, dyeing with plants, barks and insects has been traced back more than 5,000 years. The essential process of dyeing changed little over time. Typically, the dye material is put in a pot of water and then the textiles to be dyed are added to the pot, which is heated and stirred until the color is transferred. Textile fiber may be dyed before spinning (dyed in the wool), but most textiles are yarn- dyed or piece-dyed after weaving. -
( 12 ) Patent Application Publication ( 10 ) Pub . No .: US 2020/0325342 A1 LIANG (43 ) Pub
US 20200325342A1 IN ( 19 ) United States ( 12 ) Patent Application Publication ( 10 ) Pub . No .: US 2020/0325342 A1 LIANG ( 43 ) Pub . Date : Oct. 15 , 2020 ( 54 ) METHOD FOR MANUFACTURING A C08K 5/14 ( 2006.01 ) SPECIAL EFFECT PIGMENT USING AN C08K 5/23 ( 2006.01 ) EMULSION C08K 3/30 ( 2006.01 ) ( 52 ) U.S. CI . ( 71 ) Applicant: VIAVI SOLUTIONS INC . , San Jose , CPC C09C 1/0021 ( 2013.01 ) ; C08K 2003/3045 CA (US ) ( 2013.01 ) ; B05D 5/068 ( 2013.01 ) ; B05D 1/38 ( 2013.01 ) ; B05D 3/067 ( 2013.01 ) ; B05D ( 72 ) Inventor: Kangning LIANG , San Jose , CA (US ) 3/0254 ( 2013.01 ) ; C08K 5/06 ( 2013.01 ) ; C08K 5/07 ( 2013.01 ) ; C08K 5/45 ( 2013.01 ) ; C08K ( 73 ) Assignee : VIAVI SOLUTIONS INC . , San Jose , 5/14 ( 2013.01 ) ; C08K 5/23 ( 2013.01 ) ; C08K CA ( US ) 3/30 ( 2013.01 ) ; B05D 2202/25 ( 2013.01 ) ; B05D 2202/45 ( 2013.01 ) ; B05D 2202/30 ( 21 ) Appl . No .: 16 / 383,056 ( 2013.01 ) ; B05D 2401/30 ( 2013.01 ) ; B05D Apr. 12 , 2019 2502/00 ( 2013.01 ) ; B05D 2503/00 ( 2013.01 ) ; ( 22 ) Filed : B05D 2518/10 ( 2013.01 ) ; B05D 2504/00 Publication Classification ( 2013.01 ) ; B05D 2506/00 ( 2013.01 ) ; B05D ( 51 ) Int . CI . 2401/10 ( 2013.01 ) ; C09C 3/10 ( 2013.01 ) C09C 1/00 ( 2006.01 ) ( 57 ) ABSTRACT C09C 3/10 ( 2006.01 ) B05D 5/06 ( 2006.01 ) A method of making pigments, such as special effect pig B05D 1/38 ( 2006.01 ) ment includes forming a first slurry including a substrate, a B05D 3/06 ( 2006.01 ) polymer precursor , and a radical initiator; forming a solution B05D 3/02 ( 2006.01 ) including an emulsifier; and combining the first slurry and C08K 5/06 ( 2006.01 ) the solution so that the substrate is encapsulated by a first C08K 5/07 ( 2006.01 ) coating. -
(12) United States Patent (10) Patent No.: US 6,562,121 B2 Nickel Et Al
USOO6562121B2 (12) United States Patent (10) Patent No.: US 6,562,121 B2 Nickel et al. (45) Date of Patent: *May 13, 2003 (54) CONDITIONING OF ORGANIC PIGMENTS 5,110,931 A 5/1992 Dietz et al. ................... 546/37 5,492,564 A 2/1996 Wooden et al. ............. 106/493 (75) Inventors: UWe Nickel, Bad Homburg (DE); 5,534,328 A 7/1996 Ashmead et al. ........... 428/166 Klaus Kund, Langenscheid (DE); 5,591.258 A 1/1997 Urban et al. ................ 106/497 5,755,874. A 5/1998 Urban et al. ................ 106/497 ESSE SPE Maim 5,811,062 A 9/1998 Wegeng et al. ............. 422/129 (DE); Olaf Schupp,s Frankfurt am Main 5,910,577 A 6/1999 Metz et al. ................. 534/742 (DE) FOREIGN PATENT DOCUMENTS (73) Assignee: Clariant Finance (BVI) Limited, DE 1261 106 9/1968 Tortola (VG) DE 39 26 466 2/1991 EP O O77 O25 4/1983 (*) Notice: Subject to any disclaimer, the term of this EP O 318 O22 5/1989 patent is extended or adjusted under 35 EP O 655 485 5/1995 EP O 672 729 9/1995 U.S.C. 154(b) by 0 days. EP O 799 863 10/1997 EP O894 831 2/1999 This patent is Subject to a terminal dis EP 1162 240 * 12/2001 claimer. EP 1 167461 * 1/2002 (21) Appl. No.: 09/892,588 OTHER PUBLICATIONS (22) Filed: Jun. 27, 2001 Derwent Abstract of DE 3926466 (Feb./1991). (65) Prior Publication Data Derwent Abstract of EP 0 077 025 (Apr./8193). -
Fashion,Costume,And Culture
FCC_TP_V1_919 3/5/04 3:50 PM Page 1 Fashion, Costume, and Culture Clothing, Headwear, Body Decorations, and Footwear through the Ages FCC_TP_V1_919 3/5/04 3:50 PM Page 3 Fashion, Costume, and Culture Clothing, Headwear, Body Decorations, and Footwear through the Ages Volume 1: The Ancient1 World SARA PENDERGAST AND TOM PENDERGAST SARAH HERMSEN, Project Editor Fashion, Costume, and Culture: Clothing, Headwear, Body Decorations, and Footwear through the Ages Sara Pendergast and Tom Pendergast Project Editor Imaging and Multimedia Composition Sarah Hermsen Dean Dauphinais, Dave Oblender Evi Seoud Editorial Product Design Manufacturing Lawrence W. Baker Kate Scheible Rita Wimberley Permissions Shalice Shah-Caldwell, Ann Taylor ©2004 by U•X•L. U•X•L is an imprint of For permission to use material from Picture Archive/CORBIS, the Library of The Gale Group, Inc., a division of this product, submit your request via Congress, AP/Wide World Photos; large Thomson Learning, Inc. the Web at http://www.gale-edit.com/ photo, Public Domain. Volume 4, from permissions, or you may download our top to bottom, © Austrian Archives/ U•X•L® is a registered trademark used Permissions Request form and submit CORBIS, AP/Wide World Photos, © Kelly herein under license. Thomson your request by fax or mail to: A. Quin; large photo, AP/Wide World Learning™ is a trademark used herein Permissions Department Photos. Volume 5, from top to bottom, under license. The Gale Group, Inc. Susan D. Rock, AP/Wide World Photos, 27500 Drake Rd. © Ken Settle; large photo, AP/Wide For more information, contact: Farmington Hills, MI 48331-3535 World Photos. -
Inkjet Compositions Tintenstrahlzusammensetzungen Compositions D’Encre Pour Impression Par Jet D’Encre
(19) TZZ___T (11) EP 1 819 784 B1 (12) EUROPEAN PATENT SPECIFICATION (45) Date of publication and mention (51) Int Cl.: of the grant of the patent: C09D 11/40 (2014.01) C09D 11/54 (2014.01) 10.08.2016 Bulletin 2016/32 C09D 11/32 (2014.01) (21) Application number: 05810191.6 (86) International application number: PCT/US2005/036632 (22) Date of filing: 12.10.2005 (87) International publication number: WO 2006/052372 (18.05.2006 Gazette 2006/20) (54) INKJET COMPOSITIONS TINTENSTRAHLZUSAMMENSETZUNGEN COMPOSITIONS D’ENCRE POUR IMPRESSION PAR JET D’ENCRE (84) Designated Contracting States: • SARKISIAN, George M. AT BE BG CH CY CZ DE DK EE ES FI FR GB GR San Diego, California 92127-1899 (US) HU IE IS IT LI LT LU LV MC NL PL PT RO SE SI • TSAO, Yu-Hua SK TR San Diego, California 92127-1899 (US) • ANDERSON, Richard (30) Priority: 04.11.2004 US 982006 San Diego, California 92127-1899 (US) (43) Date of publication of application: (74) Representative: HGF Limited 22.08.2007 Bulletin 2007/34 Fountain Precinct Balm Green (73) Proprietor: HEWLETT-PACKARD DEVELOPMENT Sheffield S1 2JA (GB) COMPANY, L.P. Houston TX 77070 (US) (56) References cited: EP-A- 0 913 438 EP-A- 0 945 496 (72) Inventors: EP-A- 0 962 324 • PRASAD, Keshava A. San Diego, California 92127-1899 (US) Note: Within nine months of the publication of the mention of the grant of the European patent in the European Patent Bulletin, any person may give notice to the European Patent Office of opposition to that patent, in accordance with the Implementing Regulations.